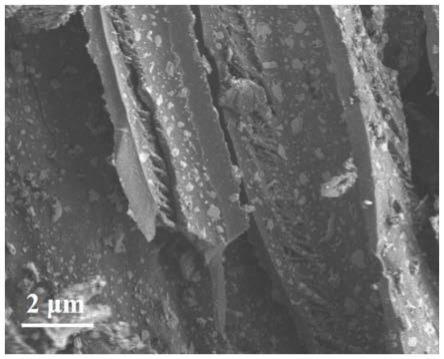
一种co与mo2c共掺杂的生物炭基复合材料及其制备方法与应用
技术领域
1.本发明属于碳材料制备领域,特别涉及一种吸附和高级氧化技术协同来催化降解常见染料亚甲基蓝的应用。
背景技术:2.我国是全球最大的染料生产和消费国,目前我国各种染料产量已达90万吨,占世界70%左右。在环境治理领域,根据染料分子在水溶液中解离出来的离子态可分为阳离子染料、阴离子染料、非离子型染料。亚甲基蓝(mb)是一种典型的阳离子染料——碱性染料,这类染料色泽非常鲜艳,即使浓度很低,水体的色度也会很高,进而影响光线射入,从而影响水底植物的光合作用和水生动物的生长,其“三致”效应也会对人体造成潜在的危害,若不合理处置,将造成严重的环境和健康问题。
3.传统的污水处理系统对染料的去除效果很差,这大大刺激了相关水处理技术的创新。高级氧化处理(aops)在此展现出巨大的应用潜力,其通过产生具有强氧化能力的自由基,使大分子难降解有机物氧化成低毒或无毒的小分子物质。近年来,基于硫酸根自由基的高级氧化技术(sr-aops)引起了广泛的关注。
4.过氧单硫酸盐(pms)是一种具有不对称结构(ho-so
4-)的代表性过硫酸盐,可产生强氧化性so
4-·
,广泛应用于sr-aops中,其分子中o-o键的裂解是产生so
4-·
和
·
oh的必要条件。紫外光、高温是很好的产生so
4-·
的方法,但需要很高的设备投资和运行成本;过渡金属(如co、fe、mn等)及其氧化物、硫化物、碳化物也均具有一定的pms活化能力,但其存在着金属离子浸出、稳定性有限等一系列问题。因此,急需开发更高性能、更低成本且环境友好的pms活化剂。
5.与其他过渡金属相比,mo毒性较低,对人类健康和环境保护相对有利。其硫化物mos2已广泛应用于活化pms降解污染物的研究,而其碳化物mo2c的相关报道却微乎其微。但mo2c在结构上相较于mos2具有更多暴露的mo位点,且研究表明mo
2+
活性位点可能具有更高的有效激活pms的潜力。为了减少金属离子浸出、提高材料在实际应用中的稳定性,将其负载于较高比表面积、高机械强度、良好化学稳定性的固体载体上是一种很好的解决策略。常见的载体主要包括mgo、zno、tio2等金属氧化物载体,碳纳米管、石墨烯、g-c3n4等碳基载体,以及金属-有机框架、沸石、分子筛等其他载体。其中,生物炭(bc)作为新型碳质载体,成本低廉、来源广泛且环境友好。因此,探索由其组成的非均相催化剂用于pms的活化将是非常有意义的。
技术实现要素:6.本发明提供了一种co与mo2c共掺杂的生物炭基复合材料的制备方法,旨在同时满足对pms活化剂高性能和环境友好的要求,并拓宽mo2c的应用领域。
7.本发明为解决技术问题,采用如下技术方案:
8.一种co与mo2c共掺杂的生物炭基复合材料的制备方法,包括如下步骤:
9.步骤1、将蒲草生物质烘干后,用粉碎机进行粉碎,获得原始生物质材料;
10.步骤2、称取co(ch3coo)2·
4h2o、(nh4)6mo7o
24
·
4h2o,并在磁搅拌下溶于去离子水,得到混合溶液;将步骤1所得原始生物质材料置于所述混合溶液中浸渍,再通过旋转蒸发和真空干燥脱水,获得前体材料;
11.步骤3、将步骤2所得前体材料置于瓷舟中,放入管式热解炉,在n2氛围下慢速热解,然后研磨,即获得掺杂co与mo2c的生物炭基复合材料。
12.优选地,步骤1中,所述原始生物质材料粒径为100目以下(《0.15mm)。
13.优选地,步骤2中,所述co(ch3coo)2·
4h2o、(nh4)6mo7o
24
·
4h2o的总质量为原始生物质材料质量的30%-30.5%。
14.优选地,步骤2中,所述co(ch3coo)2·
4h2o、(nh4)6mo7o
24
·
4h2o的质量比满足n(co):n(mo)=1:4.95-5.05(即co元素与mo元素的摩尔比满足1:4.95-5.05)。
15.优选地,步骤2中,所述浸渍的时间为24h,旋转蒸发及真空干燥的温度均设置为60℃。
16.优选地,步骤3中,所得前体材料在n2氛围下慢速热解的条件为:以2℃/min的升温速率、60ml/min的n2流速,先升温至400℃保温2h,再继续升温至800-900℃保温退火2h,最后自然冷却至室温。
17.本发明所获得的co与mo2c共掺杂的生物炭基复合材料可用于活化过氧单硫酸盐(pms),以提高pms对亚甲基蓝(mb)的氧化速率。基于此,本发明提供了一种提高pms氧化mb效率的方法,包括以下步骤:
18.在待处理的mb溶液中加入所述co与mo2c共掺杂的生物炭基复合材料,并充分吸附,使反应达到吸附/解吸平衡;吸附结束后加入pms氧化。
19.优选地,所述co与mo2c共掺杂的生物炭基复合材料的投加量与mb的质量比为5:1,pms的用量与mb的质量比为1:100。
20.优选地,吸附时间为30min,氧化时间为15min。
21.本发明的有益效果体现在:
22.本发明提供了一种co与mo2c共掺杂的生物炭基复合材料的制备方法,可以高效活化pms降解污染物。mo具有较多未被占满的d轨道,而co具有丰富的外层电子,该方法掺杂微量co与mo2c进行组合,可以形成良好的异质界面,增加活性位点,再利用蒲草热解得到的bc作为载体和电子传输介质,不仅能实现对废弃生物质的资源化利用,还能防止金属纳米粒子团聚,保护co、mo2c不受工作环境的腐蚀,减少金属离子浸出,加快得失电子循环和自由电子的转移,促进pms的活化和污染物的降解。
附图说明
23.图1为本发明实施例1所得co与mo2c共掺杂的生物炭基复合材料的sem图。
24.图2为本发明实施例1-4所得复合材料的xrd图,退火温度分别为600℃、700℃、800℃、900℃。
25.图3为本发明实施例1-4所得复合材料的mb降解实验图。
26.图4为本发明实施例1、对比例1-3所得材料的mb降解实验图。
具体实施方式
27.下面结合具体实施例对本发明进行详细说明。以下实施例将有助于本领域的技术人员进一步理解本发明,但不以任何形式限制本发明。应当指出的是,对本领域的技术人员来说,在不脱离本发明构思的前提下,还可以做出若干变形和改进,这些都属于本发明的保护范围。
28.实施例1
29.1、制备co与mo2c共掺杂的生物炭基复合材料:
30.将蒲草生物质烘干后,用粉碎机进行粉碎,获得粒径在100目以下的原始生物质材料。
31.称取0.2667gco(ch3coo)2·
4h2o、0.9451g(nh4)6mo7o
24
·
4h2o,并在磁搅拌下溶于200ml去离子水中,得到混合溶液;将4g原始生物质材料置于混合溶液中,在磁搅拌下浸渍24h,再通过60℃旋转蒸发和真空干燥脱水,获得前体材料。
32.将步骤2所得前体材料置于瓷舟中,放入管式热解炉,以2℃/min的升温速率、60ml/min的n2流速,先升温至400℃保温2h,再继续升温至800℃保温退火2h,最后自然冷却至室温,用玛瑙研钵进行研磨,即获得co与mo2c共掺杂的生物炭基复合材料(co,mo2c@bc)。
33.2、mb的氧化降解
34.取5mg制得的co,mo2c@bc加入50ml浓度为20mg/l的mb溶液中,吸附30min使反应达到吸附/解吸平衡。吸附结束后加入1ml浓度为10g/l的过氧单硫酸盐(pms)并开始计时,每隔一段时间取出1ml反应液,稀释一倍后用0.22μm有机系滤头过滤,用紫外分光光度计检测反应液中剩余mb浓度。
35.本实施例所制得的co,mo2c@bc的sem图参见图1。从图1可见,与典型的热解生物炭类似,材料主体由粗糙的碳片组成,且存在非连续的锯齿状缝隙,金属纳米颗粒均匀分布在表面。
36.实施例2
37.1、制备co与mo2c共掺杂的生物炭基复合材料:
38.将蒲草生物质烘干后,用粉碎机进行粉碎,获得粒径在100目以下的原始生物质材料。
39.称取0.2667gco(ch3coo)2·
4h2o、0.9451g(nh4)6mo7o
24
·
4h2o,并在磁搅拌下溶于200ml去离子水中,得到混合溶液;将4g原始生物质材料置于混合溶液中,在磁搅拌下浸渍24h,再通过60℃旋转蒸发和真空干燥脱水,获得前体材料。
40.将步骤2所得前体材料置于瓷舟中,放入管式热解炉,以2℃/min的升温速率、60ml/min的n2流速,先升温至400℃保温2h,再继续升温至900℃保温退火2h,最后自然冷却至室温,用玛瑙研钵进行研磨,即获得co与mo2c共掺杂的生物炭基复合材料(co,mo@bc-900)。
41.2、mb的氧化降解
42.取5mg制得的co,mo@bc-900加入50ml浓度为20mg/l的mb溶液中,吸附30min使反应达到吸附/解吸平衡。吸附结束后加入1ml浓度为10g/l的过氧单硫酸盐(pms)并开始计时,每隔一段时间取出1ml反应液,稀释一倍后用0.22μm有机系滤头过滤,用紫外分光光度计检测反应液中剩余mb浓度。
43.实施例3
44.1、制备co与mo2c共掺杂的生物炭基复合材料:
45.将蒲草生物质烘干后,用粉碎机进行粉碎,获得粒径在100目以下的原始生物质材料。
46.称取0.2667gco(ch3coo)2·
4h2o、0.9451g(nh4)6mo7o
24
·
4h2o,并在磁搅拌下溶于200ml去离子水中,得到混合溶液;将4g原始生物质材料置于混合溶液中,在磁搅拌下浸渍24h,再通过60℃旋转蒸发和真空干燥脱水,获得前体材料。
47.将步骤2所得前体材料置于瓷舟中,放入管式热解炉,以2℃/min的升温速率、60ml/min的n2流速,先升温至400℃保温2h,再继续升温至700℃保温退火2h,最后自然冷却至室温,用玛瑙研钵进行研磨,即获得co与mo2c共掺杂的生物炭基复合材料(co,mo@bc-700)。
48.2、mb的氧化降解
49.取5mg制得的co,mo@bc-700加入50ml浓度为20mg/l的mb溶液中,吸附30min使反应达到吸附/解吸平衡。吸附结束后加入1ml浓度为10g/l的过氧单硫酸盐(pms)并开始计时,每隔一段时间取出1ml反应液,稀释一倍后用0.22μm有机系滤头过滤,用紫外分光光度计检测反应液中剩余mb浓度。
50.实施例4
51.1、制备co与mo2c共掺杂的生物炭基复合材料:
52.将蒲草生物质烘干后,用粉碎机进行粉碎,获得粒径在100目以下的原始生物质材料。
53.称取0.2667gco(ch3coo)2·
4h2o、0.9451g(nh4)6mo7o
24
·
4h2o,并在磁搅拌下溶于200ml去离子水中,得到混合溶液;将4g原始生物质材料置于混合溶液中,在磁搅拌下浸渍24h,再通过60℃旋转蒸发和真空干燥脱水,获得前体材料。
54.将步骤2所得前体材料置于瓷舟中,放入管式热解炉,以2℃/min的升温速率、60ml/min的n2流速,先升温至400℃保温2h,再继续升温至600℃保温退火2h,最后自然冷却至室温,用玛瑙研钵进行研磨,即获得co与mo2c共掺杂的生物炭基复合材料(co,mo@bc-600)。
55.2、mb的氧化降解
56.取5mg制得的co,mo@bc-600加入50ml浓度为20mg/l的mb溶液中,吸附30min使反应达到吸附/解吸平衡。吸附结束后加入1ml浓度为10g/l的过氧单硫酸盐(pms)并开始计时,每隔一段时间取出1ml反应液,稀释一倍后用0.22μm有机系滤头过滤,用紫外分光光度计检测反应液中剩余mb浓度。
57.实施例1-4所制得复合材料的xrd图参见图2。从图2可知,实施例1-4的样品均在44.3
°
出现了衍射峰,对应于co纳米颗粒(111)晶面(jcpds15-0806),表明co被成功掺入。实施例1、2的样品在34.47
°
、38.06
°
、39.54
°
、52.31
°
、61.76
°
、74.98
°
、75.41
°
出现了衍射峰,对应于mo2c的标准衍射峰(jcpds35-0787),实施例3、4的样品所出现的衍射峰主要对应于moo
x
和moc,这表明随着退火温度逐渐升高,moo
x
逐渐被生物炭热解所产生的还原性气体还原为mo2c,mo的价态逐渐降低,当退火温度≥800℃时,即可形成mo2c。
58.实施例1-4所制得材料的mb降解效果图参见图3。从图3可知,以上实施例1-4的样
品通过活化pms在15min内对mb的去除率分别为:97.52%、97.12%、86.13%、70.78%,其中实施例1(co,mo2c@bc)和实施例2(co,mo@bc-900)的效果接近一致,这表明随着退火温度的升高,材料对mb的去除率越高。
59.对比例1
60.1、制备co掺杂的生物炭基复合材料:
61.将蒲草生物质烘干后,用粉碎机进行粉碎,获得粒径在100目以下的原始生物质材料。
62.称取0.2667gco(ch3coo)2·
4h2,并在磁搅拌下溶于200ml去离子水中,得到乙酸钴溶液;将4g原始生物质材料置于乙酸钴溶液中,在磁搅拌下浸渍24h,再通过60℃旋转蒸发和真空干燥脱水,获得前体材料。
63.将步骤2所得前体材料置于瓷舟中,放入管式热解炉,以2℃/min的升温速率、60ml/min的n2流速,先升温至400℃保温2h,再继续升温至800℃保温退火2h,最后自然冷却至室温,用玛瑙研钵进行研磨,即获得co掺杂的生物炭基复合材料(co@bc)。
64.2、mb的氧化降解
65.取5mg制得的co@bc加入50ml浓度为20mg/l的mb溶液中,吸附30min使反应达到吸附/解吸平衡。吸附结束后加入1ml浓度为10g/l的过氧单硫酸盐(pms)并开始计时,每隔一段时间取出1ml反应液,稀释一倍后用0.22μm有机系滤头过滤,用紫外分光光度计检测反应液中剩余mb浓度。
66.对比例2
67.1、制备mo2c掺杂的生物炭基复合材料:
68.将蒲草生物质烘干后,用粉碎机进行粉碎,获得粒径在100目以下的原始生物质材料。
69.称取0.9451g(nh4)6mo7o
24
·
4h2o,,并在磁搅拌下溶于200ml去离子水中,得到钼酸铵溶液;将4g原始生物质材料置于钼酸铵溶液中,在磁搅拌下浸渍24h,再通过60℃旋转蒸发和真空干燥脱水,获得前体材料。
70.将步骤2所得前体材料置于瓷舟中,放入管式热解炉,以2℃/min的升温速率、60ml/min的n2流速,先升温至400℃保温2h,再继续升温至800℃保温退火2h,最后自然冷却至室温,用玛瑙研钵进行研磨,即获得mo2c掺杂的生物炭基复合材料(mo2c@bc)。
71.2、mb的氧化降解
72.取5mg制得的mo2c@bc加入50ml浓度为20mg/l的mb溶液中,吸附30min使反应达到吸附/解吸平衡。吸附结束后加入1ml浓度为10g/l的过氧单硫酸盐(pms)并开始计时,每隔一段时间取出1ml反应液,稀释一倍后用0.22μm有机系滤头过滤,用紫外分光光度计检测反应液中剩余mb浓度。
73.对比例3
74.1、制备生物炭材料:
75.称取4g蒲草生物质置于瓷舟中,放入管式热解炉,以2℃/min的升温速率、60ml/min的n2流速,先升温至400℃保温2h,再继续升温至800℃保温退火2h,最后自然冷却至室温,用玛瑙研钵进行研磨,即获得生物炭材料(bc)。
76.2、mb的氧化降解
77.取5mg制得的bc加入50ml浓度为20mg/l的mb溶液中,吸附30min使反应达到吸附/解吸平衡。吸附结束后加入1ml浓度为10g/l的过氧单硫酸盐(pms)并开始计时,每隔一段时间取出1ml反应液,稀释一倍后用0.22μm有机系滤头过滤,用紫外分光光度计检测反应液中剩余mb浓度。
78.实施例1、对比例1-3所制得材料的mb降解效果图参见图4。从图4可知,以上实施例1、对比例1-3的样品通过活化pms在15min内对mb的去除率分别为:97.52%、65.43%、32.56%、9.3%,这表明co与mo2c共掺杂的生物炭基复合材料(实施例1)对pms的活化能力优于仅掺杂co(对比例1)、仅掺杂mo2c(对比例2)和不掺杂的生物炭(对比例3)。说明实施例1制备的材料效果突出,co、mo2c、bc之间存在良好的协同作用,有助于得失电子循环和自由电子转移,从而有效激活pms。
79.以上所述仅是本发明的优选实施方式,应当指出,对于本技术领域的普通技术人员来说,在不脱离本发明原理的前提下,还可以做出若干改进和润饰,这些改进和润饰也应视为本发明的保护范围。