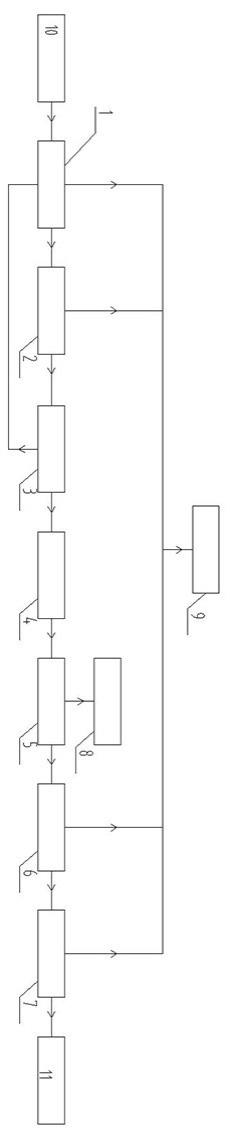
1.本技术属于化工机械设备技术领域,具体涉及一种己二酸生产液回收利用系统。
背景技术:2.己二酸是一种重要的化工生产原料,在有机合成工业、医药、润滑剂制造、尼龙66和工程塑料等工业生产制备领域均具有广泛的用途。
3.己二酸的工业化生产制备,最早是以环己醇作为原料,然后通过硝酸氧化(苯酚加氢)制备获得。60年代后,随着其他化工行业发展,工业生产中逐步改用以环己烷为原料的生产工艺。即,先由环己烷制成中间产物环己酮和环己醇混合物(即酮醇油,又称ka油),然后再进行氧化制备成己二酸。在对ka油氧化过程中,一种工艺路线是以过量硝酸作为氧化剂,然后在催化剂和适当反应条件下来实现氧化反应的,由于这种工艺路线制备获得的己二酸收率较高、纯度较高,因此工业生产中应以较为广泛。
4.实际产业化生产中,由于生产液中含有大量硝酸,故无论从降低生产成本还是从环保角度出发,都需对生产液中硝酸进行重新回收利用。因此,实际的己二酸连续化生产制备中,反应所用硝酸为新添加硝酸和所回收硝酸的混合物。
5.对生产液(即,母液酸)中硝酸进行回收时,硝酸经蒸馏后即可回收重新进入己二酸制备工艺,但由于制备己二酸过程中会生产含有大量dba(己二酸、丁二酸、戊二酸混合物,母液酸中含量大约为15~25%),而从己二酸制备生产角度,反应中硝酸混合物(添加硝酸和所回收硝酸的混合物)中的dba含量必须保持在合理的范围内(一般要求为9%~13%),因此,对生产液(即,母液酸)中dba必须进行回收去除,才能确保己二酸的稳定化生产。同时,回收所得dba也可进一步提高产业价值。而另一方面,由于生产液(即,母液酸)还含有大量催化剂(主要为铜、钒),因此,对于催化剂的有效回收,也有助于降低己二酸的生产制备成本。
技术实现要素:6.本技术目的在于提供一种己二酸生产液回收利用系统,从而为降低己二酸生产成本、提高己二酸生产的总体生产值奠定一定技术基础。
7.本技术所采取的技术方案详述如下。
8.一种己二酸生产液回收利用系统,包括:通过管路依次连接的第一蒸发器、第一催化剂回收装置、第二蒸发器、ada回收结晶器、固液分离装置、第二催化剂回收装置、结片装置;
9.其中:
10.第一蒸发器、第一催化剂回收装置、第二催化剂回收装置和结片装置分别通过管路与己二酸生产系统中的己二酸浓缩塔连接;进一步而言:
11.第一蒸发器(负压条件下)把母液酸中的部分硝酸通过蒸发气化送回己二酸浓缩塔内进行回收;
12.优选设计中,第一蒸发器和第二蒸发器之间设有连接管路,以第二蒸发器蒸发硝酸过程中所产蒸汽作为热源;
13.第一催化剂回收装置,一般为连续性离子交换树脂装置,通过离子交换方式,将dba溶液中约97%的铜和约70%的钒通过吸附交换方式进行回收后,再返回到己二酸浓缩塔回收;
14.第二蒸发器,采用高压蒸汽(2.8~3.5mpa,温度420~445℃)作为热源,以对经第一催化剂回收装置处理后液相中硝酸进行较为彻底的蒸发处理;蒸发所得硝酸可送回己二酸浓缩塔内进行回收,或者返回用于第一催化剂回收装置内离子交换树脂的再生。
15.所述固液分离装置,具体例如为螺旋沉降式离心机;所述固液分离装置可进一步连接有己二酸反应完成罐,以将分离所得ada进一步返回己二酸反应完成罐内。
16.所述第二催化剂回收装置,与第一催化剂回收装置类似,同样采用连续性离子交换树脂装置,以对回收ada后回收液中催化剂进行较为彻底回收。
17.所述结片装置,用于将dba回收溶液中二元酸(dba)进行结片,以制备成含水在2%左右的二元酸成品。
18.实际设计中,所述结片装置,可进一步连接有蒸发系统,以对dba回收溶液中硝酸进行进一步回收。
19.根据工艺设计需要,第一蒸发器和第一催化剂回收装置之间的连接管路上,还连接有稀释水管路,以对第一蒸发器处理后回收液进行稀释。类似的,第二蒸发器和ada(己二酸)回收结晶器之间的连接管路上连接有稀释水管路,以对dba溶液进行稀释。
20.具体生产中,以现有己二酸生产中的母液酸(ma)为原料(主要成分为:硝酸25%~35%,二元酸5%~15%,铜0.4%~0.6%,钒0.04%~0.06%)。采用本技术所提供回收利用系统后,结合相关工艺参数调整,初步应用效果表明,该回收系统可有效分离回收己二酸生产液中硝酸,并可有效回收二元酸(dba),99%的催化剂也可被有效回收。基于这一初步应用结果,对于降低己二酸生产成本、确保己二酸的连续稳定化生产、和提高己二酸生产的总体生产值具有较好的实用价值。
附图说明
21.图1为本技术所提供己二酸生产液回收利用系统结构示意图。
具体实施方式
22.如图1所示,本技术所提供己二酸生产液回收利用系统,包括:通过管路依次连接的第一蒸发器1、第一催化剂回收装置2、第二蒸发器3、ada(己二酸)回收结晶器4、固液分离装置5、第二催化剂回收装置6、结片装置7;
23.其中:
24.第一蒸发器1、第一催化剂回收装置2、第二催化剂回收装置6和结片装置7分别通过管路与现有己二酸生产系统中的己二酸浓缩塔9连接;进一步而言:
25.第一蒸发器1(负压条件下)把母液酸(ma)10中的部分硝酸通过蒸发气化送回己二酸浓缩塔9内进行回收;
26.优选设计中,第一蒸发器1和第二蒸发器3之间设有连接管路,以第二蒸发器3蒸发
硝酸过程中所产蒸汽作为热源;
27.第一催化剂回收装置2,一般为连续性离子交换树脂装置,通过离子交换方式,将dba溶液中约97%的铜和约70%的钒通过吸附交换方式进行回收后,再返回到己二酸浓缩塔9回收;
28.第二蒸发器3,采用高压蒸汽(2.8~3.5mpa,温度420~445℃)作为热源,以对经第一催化剂回收装置2处理后液相中硝酸进行较为彻底的蒸发处理,蒸发硝酸剩余所得为温度150℃左右、浓度90wt%的dba溶液,进入后续处理工艺;蒸发所得硝酸可送回己二酸浓缩塔9内进行回收,或者返回用于第一催化剂回收装置2内离子交换树脂的再生。
29.实际设计中,由于dba溶液中还含有部分己二酸(ada),因此,为最大程度回收ada,提高系统收率,因此,在第二蒸发器3处理后管路上设计有ada回收结晶器,以对第二蒸发器3处理后dba溶液进行冷却结晶,随后通过固液分离装置5(具体例如为螺旋沉降式离心机)以将ada进行分离,并可将分离所得ada进一步返回己二酸反应完成罐8。
30.所述第二催化剂回收装置6,与第一催化剂回收装置2类似,同样采用连续性离子交换树脂装置,以对回收ada后回收液中催化剂进行较为彻底回收,所回收的催化剂进一步返回己二酸浓缩塔9内以备重新用于己二酸的生产制备;同时,用于再生第二催化剂回收装置6内离子交换树脂的硝酸也可回收后返回己二酸浓缩塔9内以重新用于生产制备己二酸。经第二催化剂回收装置6处理后回收液,具体工艺设计要求参考为:硝酸≤5%,dba13%~25%,铜≤25ppm,钒≤25ppm。
31.所述结片装置7,用于将dba回收溶液中二元酸(dba)进行结片,以制备成含水在2%左右的二元酸成品11,并用于外售制备其他化工产品;
32.实际设计中,所述结片装置7,可进一步连接有蒸发系统,以对dba回收溶液中硝酸进行进一步回收(所回收的硝酸可进一步返回己二酸浓缩塔9内),同时可将dba回收溶液中水份蒸发出来,以便于结片机的连续化作业生产。
33.具体工艺生产中,第一蒸发器1蒸发回收硝酸过程中之所以采用第二蒸发器3所产蒸汽作为热源(具体而言,热源为第二蒸发器3所产硝酸蒸汽,此硝酸蒸汽在第一蒸发器1壳表冷凝过程中用于加热蒸发进入第一蒸发器1母液酸,而冷凝后硝酸可根据工艺设计送到第一和/或第二催化剂回收装置以用于树脂再生),而不采用第二蒸发器类似的高温蒸汽作为热源(以在起始回收阶段即最大化回收硝酸),其主要原因在于,在金属催化剂(cu、v)尚未充分回收情况下,高温蒸发操作会形成大量的金属沉渣(金属络合物),从而使得蒸发器的作业无法正常进行,因此以第二蒸发器3所产蒸汽作为热源是兼顾硝酸蒸发、节约能耗和连续化作业的最为合理设计。
34.具体生产中,本技术以现有己二酸生产中的母液酸(ma)10为原料(主要成分为:硝酸25%~35%,二元酸5%~15%,铜0.4%~0.6%,钒0.04%~0.06%),通过第一蒸发器1处理后,出口所得为浓度为70wt%的dba溶液。由于dba浓度过高情况下会影响第一催化剂回收装置2对于催化剂的离子交换效果,因此,实际设计中,第一蒸发器1和第一催化剂回收装置2之间的连接管路上,还连接有稀释水管路(图中未示出,根据本领域技术常识,实际施工设计中,具体添加即可),以对第一蒸发器1处理后回收液进行稀释(稀释后要求参考为:硝酸≤18%,dba 17%~35%)。类似的,第二蒸发器3和ada(己二酸)回收结晶器4之间的连接管路上连接有稀释水管路,以对dba溶液进行稀释(稀释后要求参考为:硝酸≤9%,dba30%~45%),从而
便于后续的结晶处理。
35.采用上述回收利用系统后,结合相关工艺参数调整,初步应用效果表明,该回收系统可有效分离回收己二酸生产液中硝酸,并可有效回收二元酸(dba),99%的催化剂也可被有效回收。基于这一初步应用结果,对于降低己二酸生产成本、确保己二酸的连续稳定化生产、和提高己二酸生产的总体生产值具有较好的实用价值。