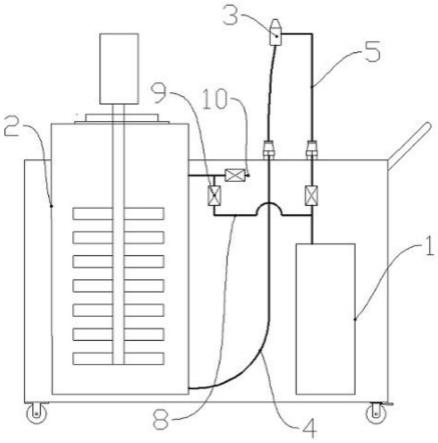
1.本发明涉及喷雾设备技术领域,尤其是气体辅助液体分散的喷雾设备,具体为一种脱模剂喷雾装置及其使用方法。
背景技术:2.模具是生产产品的模型,利用模具生产产品可以确保产品规格相同而且程序相对简单,是目前规模化生产的常用手段。模具生产过程中,为了便于成型产品完整地从模具中取出,往往在模具本体中喷洒脱模剂,脱模剂作为一种位于模具表面的界面涂层,可以使模具中与成型材料接触的表面光滑、洁净,降低模具与成型材料之间的粘附作用,便于成型产品脱落。脱模剂一般是多种物质组成的混合物,具有较高的粘度,其使用前都需要搅拌均匀,甚至部分脱模剂还需要加入水或油等进行一定程度的稀释,而且为了更为均匀地将脱模剂分布在模具表面,脱模剂的喷涂装置通常还配套有雾化气体来分散脱模剂。通常而言,脱模剂的搅拌操作在罐体中进行,搅拌均匀后再经管线送至喷头,喷头处配设雾化气体将脱模剂均匀喷射到模具表面,罐体与喷头之间的管线可以是伸缩管、软管等,以便于移动喷头对模具的不同部位进行喷涂。连续喷涂作业时,罐体中脱模剂搅拌后在管线中停留时间短、不存在静置分层的问题,然而较长时间中断作业后,比如中午午休、夜晚停工休息,脱模剂如果留存在管线中则会沉降分层,导致管段内的脱模剂喷洒后不能在模具表面均匀分布,影响脱模效果,目前常见的方式就是中断后再次投用时利用罐体中的脱模剂冲洗置换管线内的脱模剂,置换出来的脱模剂再投入罐体中搅拌回用,此方式耗时较长,而且置换时长往往根据个人经验确定,当置换时间不足时存在脱模剂喷洒不均匀的问题,当置换时间过长时则浪费了有效工作时间。
技术实现要素:3.鉴于上述问题,本发明的一个目的是提供一种脱模剂喷雾装置,其在喷头与脱模剂罐的连接管线中内置带中通孔的活塞,利用雾化气的压力来开关活塞的通孔,使用完成后关闭活塞通孔并利用雾化气将连接管线中的脱模剂全部驱入脱模剂罐中,解决了脱模剂在连接管线中静置分层的问题。
4.本发明的具体方案如下:
5.一种脱模剂喷雾装置,包括雾化气源、内部设有搅拌器的脱模剂罐、喷头、活塞组件、加压结构、弹性结构和限位结构;脱模剂罐体底部经第一管道与喷头连通;喷头包括中心管、外壳和盖体,中心管侧壁设置有贯穿本体的通气孔,外壳套设在中心管外,且外壳的一端与中心管密封连接、另一端与中心管出口连通,外壳、中心管之间形成夹套结构,外壳上设有雾化气接口,用于将雾化气源中的雾化气引入夹套结构中,夹套结构与通气孔连通;盖体以可拆卸方式与喷头出口密封连接;活塞组件包括活塞本体和风压开关,其中,活塞本体整体呈筒状,其中部的中空部位为流体通道,活塞本体的两端均设有与第一管道内壁和中心管内壁滑动密封连接的密封部,活塞本体中部设有沿其径向延伸的盲孔,盲孔的出口
端位于两个密封部之间,风压开关则安装在盲孔中,用于启闭流体通道,当盲孔与通气孔连通时,雾化气能够触发风压开关动作以开关流体通道;加压结构用于调节脱模剂罐中脱模剂的压力;弹性结构用于推动活塞组件沿喷头向脱模剂罐方向移动至盲孔与通气孔隔离;限位结构用于限制活塞组件从第一管道中脱落并掉入脱模剂罐中。
6.作为本发明的一种具体实施方式,所述加压结构由第二活塞和伸缩机构提供,第二活塞位于脱模剂罐中并与脱模剂罐内壁滑动密封连接,伸缩机构用于推动第二活塞在脱模剂罐中移动,从而调整脱模剂的压力。作为一种替换手段,脱模剂罐中脱模剂的压力由气体控制,加压结构为包括第二气源的压力控制机构,用于控制脱模剂罐内的压力,此具体实施方式有很多,比如将脱模剂罐布置成密闭容器,将雾化气源的气体引入脱模剂罐中,脱模剂罐设置排气管,通过控制脱模剂罐进入、排放的气量来调节脱模剂的压力。
7.作为本发明的一种具体实施方式,所述弹性结构可以是由沿中心管中心线方向伸缩的第一弹性元件,此弹性元件可以与活塞本体一体成型,也可以与喷头一体成型,比如弹性元件的一端与喷头固定连接。
8.作为本发明的一种具体实施方式,所述风压开关包括内置于盲孔中的第二弹性元件、阀芯,阀芯中设有贯穿本体的阀芯通道,阀芯与盲孔滑动密封连接,阀芯通道与活塞本体的流体通道连通后流体能够从流体通道流通,此时活塞本体的流体通道为打开状态;阀芯通道与活塞本体的流体通道错位隔离后流体通道被截断,流体不能够从流体通道流通,此时活塞本体的流体通道为关闭状态,第二弹性元件用于推动阀芯向盲孔出口方向移动以使得流体通道与阀芯通道错位;当喷头出口打开时,通气孔处的风压能够推动阀芯向盲孔的盲端移动使得阀芯通道与流体通道联通。
9.进一步,风压开关还包括固定于盲孔处的限位环,用于限制阀芯与中心管内壁接触。
10.本发明的又一目的是提供上述脱模剂喷雾装置的使用方法,其包括投用过程和停工时将第一管道中的液体回收至脱模剂罐中的过程。
11.投用过程包括如下步骤:
12.a1、通过加压结构调整脱模剂罐中脱模剂压力,推动流体通道关闭的活塞组件从脱模剂罐向喷头方向移动至盲孔与通气孔连通;
13.a2、调节夹套结构中雾化气压力触发风压开关动作打开流体通道,打开后脱模剂喷出,雾化气对脱模剂进行分散。
14.停工时将第一管道中的液体回收至脱模剂罐中的过程包括如下步骤:
15.b1、调节夹套结构中雾化气压力触发风压开关动作关闭流体通道;
16.b2、通过加压结构降低脱模剂罐中脱模剂压力,使得活塞组件在弹性结构作用下沿喷头向脱模剂罐方向移动至盲孔与通气孔隔离;
17.b3、通过盖体密封喷头出口,调整夹套结构中雾化气压力推动活塞组件沿喷头向脱模剂罐方向移动。
18.与现有技术相比,具有以下优点:
19.本发明在喷头与脱模剂之间的管线中设置活塞组件,活塞组件设置风压开关,利用雾化气来控制活塞组件开关,能够确保活塞组件打开后喷雾操作的正常运行,同时,活塞组件关闭后,本发明还利用雾化气体的压力推动活塞向脱模剂罐方向移动从而在停工时将
管道中的脱模剂完全驱入脱模剂罐中,脱模剂不残留在管道中,不存在脱模剂在缺少搅拌作用的管道中静置分层的问题,不需要开工时对管道进行冲洗置换,节省了置换操作时间,提高了工作效率。
附图说明
20.图1是本发明实施例1中脱模剂喷雾装置的整体结构示意图;
21.图2是本发明实施例1中喷头、活塞组件组合体的立体半剖视图;
22.图3是本发明实施例1中处于喷射状态的喷头、活塞组件组合体的平面剖视图;
23.图4是本发明实施例1中处于停工反推排液状态的喷头、活塞组件组合体的平面剖视图;
24.图5是本发明实施例1中中心管、弹性结构组合体的立体半剖视图;
25.图6是本发明实施例1中活塞组件的立体半剖视图;
26.图7是本发明实施例1中限位结构的示意图;
27.图中,雾化气源1;脱模剂罐2;喷头3;第一管道4;第二管道5;弹性结构6;第三管道8;阀门9;排气管道10;限位结构11;
28.中心管31;外壳32;盖体33;压紧螺母34;夹套结构35;活塞本体71;风压开关72;密封部73;
29.螺纹连接部311;第一凸台312;通气孔313;雾化气接口321;流体通道711;盲孔712;第二弹性元件721;阀芯722;限位环723;
30.阀芯通道7221。
具体实施方式
31.下面结合实施例及附图,对本发明作进一步地的详细说明,但本发明的实施方式不限于此。
32.实施例1
33.请参考图1,图1是本实施例脱模剂喷雾装置的整体结构示意图。本脱模剂喷雾装置包括雾化气源1、脱模剂罐2、喷头3、加压结构、活塞组件、弹性结构6和限位结构11。脱模剂罐2底部经第一管道4与喷头3连通,用于将脱模剂引至喷头3,第一管道4可以采用钢丝缠绕管等可以弯曲一定幅度的管道,以便于移动喷头3对模具的不同位置进行喷雾作业;雾化气源1为储存有高压空气的空气罐,雾化气源1经第二管道5与喷头3连通,用于将雾化气引至喷头3处,辅助脱模剂分散,第二管道5上设有阀门9以控制雾化气量。本实施例将整个脱模剂喷雾装置置于小推车上,以便于其移动对多个模具进行喷雾作业。
34.请结合图2~图4,图2是喷头、活塞组件组合体的立体半剖视图;图3是处于喷射状态的喷头、活塞组件组合体的平面剖视图,图4是处于停工反推排液状态的喷头、活塞组件组合体的平面剖视图。喷头3包括中心管31、外壳32、盖体33和压紧螺母34,其中,中心管31如图5所示,其一端设置有螺纹连接部311,用于与第一管道4密封连接,其另一端的外壁为圆锥状、内壁设有第一凸台312,用于支撑弹性结构6,中心管31的侧壁设有贯穿本体的通气孔313;如图2、3、4所示,外壳32的一端与中心管31外壁密封连接、另一端与中心管31出口连通,中心管31外壁、外壳32内壁之间形成一端开口的夹套结构35,外壳32上设有雾化气接口
321,用于将雾化气源1中的雾化气引入夹套结构35中,夹套结构35与通气孔313连通,具体而言,外壳32与中心管1侧壁螺纹连接,因此,可以通过旋转外壳32来改变外壳32出口端与中心管31出口端之间的间隙,从而也能够调整雾化气流量和夹套结构35中的雾化气压力,压紧螺母34也与中心管31侧壁螺纹连接,其与外壳32压紧接触,起到固定外壳32的作用;盖体33与外壳32的出口端螺纹连接,用于临时封堵喷头3出口。
35.请结合图6,图6是活塞组件的结构示意图。活塞组件包括活塞本体71和风压开关72,其中,活塞本体71整体呈筒状,其中部的中空部位为流体通道711,活塞本体71的两端均设有与第一管道4内壁和中心管31内壁滑动密封连接的密封部73,在外力作用下,活塞本体71能够沿第一管道4内壁和中心管31内壁滑动,活塞本体71中部设有沿其径向延伸的盲孔712,盲孔712的出口位于两个密封部73之间,风压开关72安装在盲孔712中,用于启闭流体通道711,因此,当盲孔712与通气孔313连通时,可以利用夹套结构35中的雾化气来触发风压开关72动作,以开、闭关流体通道711,如图3所示,此时在夹套结构35与第一管道4之间存在一个密封部313,因此,脱模剂不会窜入夹套结构35中,风压开关72完全受夹套结构35中的风压控制,当盲孔712与通气孔313隔离时,如图4所示,此时盲孔712中的气压不再受夹套结构35中的气压控制。
36.风压开关72包括内置于盲孔712中的第二弹性元件721、阀芯722和限位环723,阀芯722中设有贯穿本体的阀芯通道7221,阀芯722与盲孔712滑动密封连接,第二弹性元件721位于盲孔712的盲端,用于推动阀芯722向盲孔712出口方向移动以使得流体通道711与阀芯通道7211错位隔离、关闭流体通道711;当阀芯722向盲孔712的盲端滑动至极限位置(不能继续向盲端滑动)时,阀芯通道7221与活塞本体71的流体通道711连通,此时活塞本体71的流体通道711为打开状态,脱模剂可以顺利通过;当阀芯722向盲孔712的开口端滑动至极限位置(不能继续向开口端滑动)时,阀芯通道7221与活塞本体71的流体通道711错位后流体通道被截断,流体不能从流体通道711流通,此时活塞本体71的流体通道711为关闭状态。
37.弹性结构6用于推动活塞组件沿喷头3向脱模剂罐2方向移动至盲孔712与通气孔313隔离,如图4所示,弹性结构6可以是弹簧可以是弹性块等弹性元件,本实施例中弹性元件沿中心管31中心线方向伸缩,且其一端与第一凸台312固定连接。
38.加压结构用于调节脱模剂罐2中脱模剂的压力,具体而言,本实施例采用控制脱模剂罐2气相压力的方式来调整脱模剂压力,如图1所示,加压结构包括将雾化气源1与脱模剂罐2连通的第三管道8,第三管道上设有阀门9以控制向脱模剂罐2中输入的气体量,同时脱模剂罐2还设有带有阀门9的排气管道10,用于控制脱模剂罐2的排放气量,通过向脱模剂罐2中加、排气体可以调节脱模剂罐2中脱模剂压力。
39.限位结构11用于限制活塞组件72从第一管道4中脱落并掉入脱模剂罐2中,限位结构11的具体形状有很多,可以采用目前常见的限位结构,比如十字架,将其置于第一管道4的入口端即可,如图7所示。
40.上述装置的一种使用方法包括投用过程和停工时将第一管道中的液体回收至脱模剂罐中的过程。
41.其投用过程包括如下步骤:
42.a1、通过加压结构调整脱模剂罐中脱模剂压力,推动流体通道关闭的活塞组件从
脱模剂罐向喷头方向移动至盲孔与通气孔连通,具体而言,拆掉喷头处的盖体,打开第三管道8上的阀门、关闭排气管道10上的阀门,利用雾化气源1对脱模剂罐2充压,推动位于第一管道入口处的活塞组件向喷头方向移动至盲孔与通气孔连通,此过程中活塞组件为关闭状态,脱模剂不会喷出。
43.a2、调节夹套结构中雾化气压力触发风压开关动作打开流体通道,进而脱模剂喷出,雾化气对脱模剂进行分散,具体而言,打开第二管道5上的阀门将雾化气引入喷头,此时雾化气从喷头喷出且喷头处的夹套结构35承压,雾化气通过通气孔挤压阀芯,使得流体通道被打开,脱模剂喷出并被夹套结构35出口处的雾化气雾化分散。
44.使用过程中,可以通过调整外壳与中心管之间的间隙来进一步控制雾化气量和夹套结构终中的气体压力。
45.停工时将第一管道中的液体回收至脱模剂罐中的过程包括如下步骤:
46.b1、调节夹套结构中雾化气压力触发风压开关动作关闭流体通道,比如直接关闭第二管道5上的阀门使得喷头处的夹套结构35的压力恢复至常压,此时,阀芯在第二弹性元件作用下移动截断流体通道,脱模剂不再喷射。
47.b2、通过加压结构降低脱模剂罐中脱模剂压力,使得活塞组件在弹性结构作用下沿喷头向脱模剂罐方向移动至盲孔与通气孔隔离,具体而言,关闭第三管道8上的阀门、打开排气管道10上的阀门,使得脱模剂罐恢复至常压,此时活塞组件在弹性结构作用下沿喷头向脱模剂罐方向移动至盲孔与通气孔隔离,如图4所示。
48.b3、通过盖体密封喷头出口,调整夹套结构中雾化气压力以推动活塞组件沿喷头向脱模剂罐方向移动,即将盖体安装在外壳出口处,然后打开第二管道上的阀门,利用雾化气将活塞组件推动到第一管道的末端(液体入口处),活塞移动过程中将推动第一管道中的流体反排至脱模剂罐体中,利用罐体中的搅拌器搅拌避免脱模剂分层。
49.本装置在停工时将喷头与脱模剂罐之间的脱模剂完全驱入脱模剂罐中,管道中不残存脱模剂、不存在静置分层问题,因而再次投用时只需启动搅拌机搅拌脱模剂罐中的脱模剂就行,无须对管道进行脱模剂置换,节约了操作时间,提高了效率。
50.以上所述,仅为本发明较佳的具体实施方式,但本发明的保护范围并不局限于此,任何熟悉本技术领域的技术人员在本发明实施例揭露的技术范围内,可轻易想到的变化或替换,都应涵盖在本发明的保护范围之内。