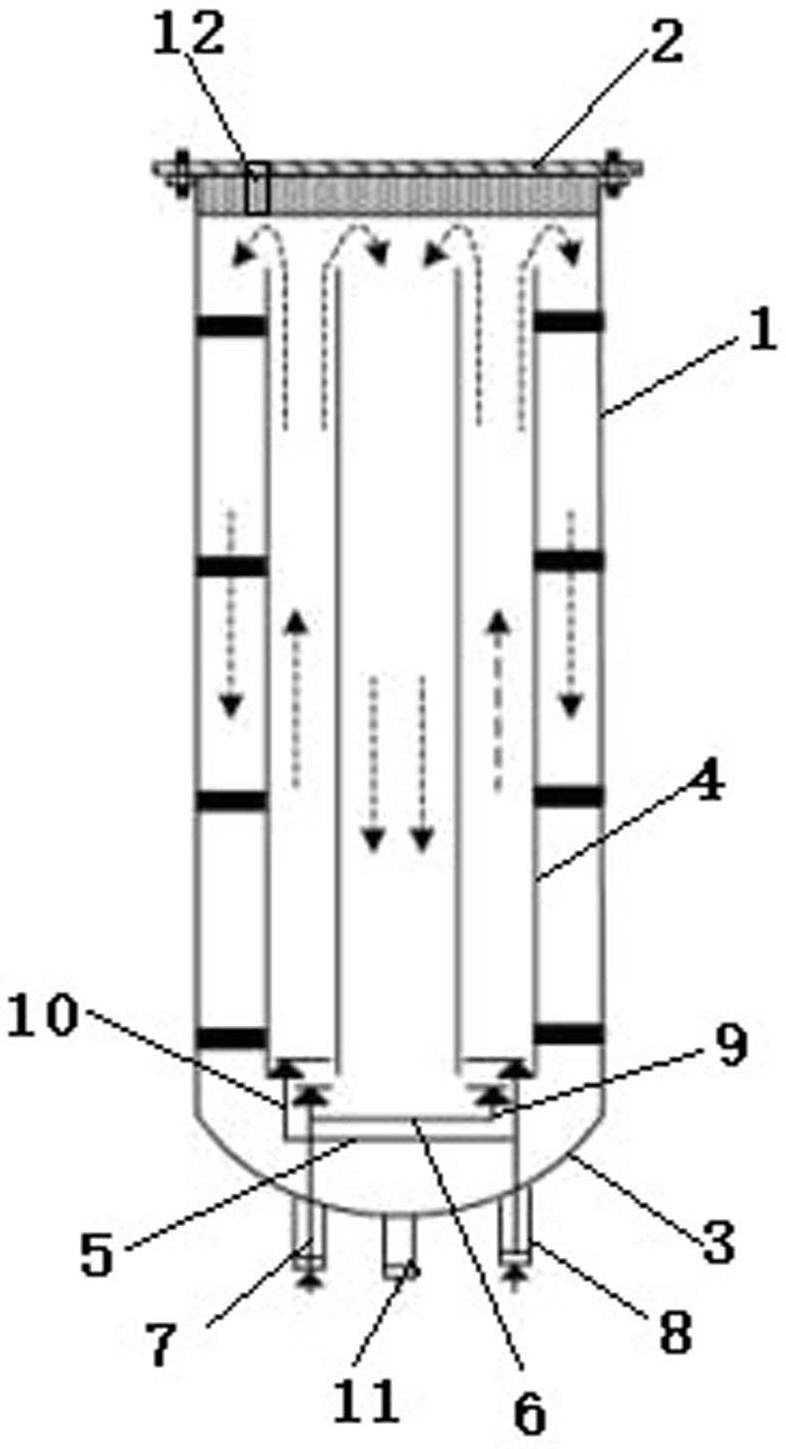
一种用于乙烯齐聚生产
α-烯烃的环流反应器、反应装置及生产工艺
1.技术领域:本发明涉及一种用于乙烯齐聚生产α-烯烃的环流反应器、反应装置及生产工艺。
2.
背景技术:α-烯烃是高附加值化工原料,可用作高端聚乙烯共聚单体、高档合成润滑油基础油生产原料,也是生产添加剂、粘合剂、密封剂、高档增塑剂和洗涤剂等精细化工品的基本原料;在α-烯烃产品中,尤其是1-己烯与1-辛烯作为聚乙烯共聚单体,能够显著增加聚乙烯的机械性能、光学性能、抗撕强度和抗冲击强度。
3.对于目前使用较多的乙烯选择性齐聚技术的开发来说,一方面是提高催化体系的催化活性和目的产物的选择性,以期降低生产成本;另一方面是乙烯选择性齐聚技术的工程放大和过程开发,目前乙烯三聚工艺反应器使用最广泛的有釜式反应器和管式反应器;国际上,phillips使用的是环管反应器,国内主要的1-己烯技术拥有者为中石化和中石油,中石化燕山石化使用环管反应器,中石油大庆石化和独山子石化后采用釜式反应釜;釜式反应器传热面积少,传热能力差,反应温度不易控制,需在外部加夹套、内部装冷凝盘管进行撤热,长期运行聚合物容易在盘管结垢,影响传热效率,且难以清洗;与釜式反应器相比使用连续管式反应器时,虽然环管工艺不需要使用搅拌桨,减少了聚合物附着的面积,且提高了传热效率,但长时间运行同样存在问题,随着管式反应器的管道的位置远离乙烯引入口,乙烯浓度急剧减少,难以有效地调节转化率和选择性。
4.可以说乙烯齐聚反应装置的工程和工艺技术开发是保证该技术大规模工业化应用的前提,因此研究人员和工程技术人员需在反应装置方面做大量的研究和技术开发工作。
5.cn 105085132a公布了一种优化乙烯齐聚工艺的方法及装置,该方法对乙烯齐聚反应结束闪蒸后得到的富含乙烯单体的烯烃类产物分离除去c6~c8烯烃产物,得到气体物流,再将所述气体物流与新鲜乙烯一起引入反应器中发生聚合反应,该方法有效降低了分离单元的设备投资,大大降低了分离过程的能耗。
6.cn105693448a公开了一种乙烯齐聚的多釜串联工艺。将反应介质、催化剂以及聚乙烯蜡抑制剂引入第一反应器,在较低温度下进行预反应,待活性开始下降引入第2反应器;升高反应温度,使反应能在长时间内维持在较高的活性;依此将反应物料引入第n个反应器。采用多釜串联反应工艺可以避免在反应前期高反应活性引起的飞温造成催化剂失活,有效地提高了催化剂的催化效率,显著提高液相α-烯烃的产量。但该技术存在工艺流程复杂、反应单元设备投资大,且后续反应器因乙烯浓度降低而存在催化活性和产物选择性降低的问题等问题。
7.cn 107151195a公开了一种乙烯齐聚生产α-烯烃工艺中去除催化剂和聚乙烯的方法,将闪蒸得到的液相物流通入含碱液的碱洗装置进行碱洗操作,得到混合物,将混合物分层,方可析出聚乙烯,去除催化剂。该方法可有效去除催化剂和聚合物,防止聚乙烯堵塞管线和影响装置长期稳定运行。但该技术存在工艺流程复杂,引入碱液的过程中很大程度上
增加了后续分离过程的成本和能耗。
8.cn 108026200a 公开了一种用于乙烯的选择性低聚反应的工业化反应工艺,通过循环反应器中的液体混合物、借助用于从循环流中分离未反应的乙烯的装置来从循环流中分离未反应的乙烯、然后冷却剩余混合物并将其重新引入反应器,由此,有效地移除反应中产生的反应热并灵活调节反应器温度。但该技术将一部分反应液循环至反应器中,大大降低了乙烯的转化率,很大程度上影响了催化剂的活性和选择性。
9.cn 107746365 a公布了一种选择性乙烯齐聚生产α-烯烃的工艺方法及系统,该方法在一个高压反应釜外接物料循环管线相连,在物料循环管线中引入换热器,及时撤走反应生成热量,实现反应温度的平稳控制,提高催化剂活性与选择性。同时在循环管线的过滤器可以及时清除反应产生聚合物,避免聚合物挂壁和装置停车,降低维护成本,提高装置效益。但该技术将一部分反应液循环至反应器中,大大降低了乙烯的转化率,且在循环管线上引入换热器,很大程度上增大了投资成本和能耗。
10.cn 110639459 a公布了一种连续化乙烯选择性齐聚制备1-辛烯的装置和方法。该流程采用釜式反应器与管式反应器串联的工艺:乙烯低温液相输送至釜式反应器,在反应器内被加热气化,一部分乙烯气体通过分布器喷射进入反应体系内参与反应,另一部分乙烯作为移热介质气化吸收反应热并循环利用,主催化剂a/配体b及助催化剂c分别与溶剂混合后加入釜式反应器,调节剂d直接气相进料至反应釜;反应后的物料经输送泵送入管式反应器,与淬灭剂在管式反应器内高温反应,淬灭后的物料进入分离系统;该方法进行制备1-辛烯,具有高催化活性,高1-辛烯选择性,高淬灭效率,长运转周期等优势。
11.虽然公开的乙烯齐聚生产α-烯烃工艺技术较多,但是反应器只局限在了传统的釜式反应器和管式反应器,釜式反应器存在传热能力差,长期运行聚合物结垢,易堵塞管路,聚合物难以清洗等问题,而管式反应器存在制造、安装复杂,占地面积大,且传质能力弱等缺点;乙烯齐聚生产α-烯烃整体工艺仍存在工艺流程复杂,连续反应容易挂壁、传热效率低、聚合物容易挂壁、堵换热器等问题,不利于工程放大等缺点。
12.综上所述,无论是釜式工艺还是环管工艺,由于齐聚过程中总是有少量的乙烯低聚物或乙烯聚合物产生,极大地影响了生产装置的长周期稳定运行,需要不定期停车处理固体聚合物,这对连续法生产装置的安全运行及高效益运行均带来了不小的挑战,因此,针对乙烯选择性齐聚反应体系的特点及存在的问题,寻求一种新的反应器及工艺方法保证装置的连续稳定运行具有重要的工业应用价值。
13.
技术实现要素:鉴于现有技术的上述不足,本发明的目的在于提供一种用于乙烯齐聚生产α-烯烃的环流反应器、反应装置及生产工艺,该环流反应器、反应装置及生产工艺有利于解决反应器容易挂壁、传热效率低等缺点。
14.本发明用于乙烯齐聚生产α-烯烃的环流反应器,其特征在于:包括柱形外筒、分别设在柱形外筒上开口、下开口上的上封头和下封头,所述柱形外筒内设有多根内置导流筒,各根内置导流筒的轴心线与柱形外筒的轴心线平行,所述柱形外筒的内底部设有气体分布器和液体分布器,所述气体分布器和液体分布器上分别设有伸进柱形外筒外的进气管和进液管,所述气体分布器和液体分布器上还分别设有多根出气支管和出液支管,各根出气支管和出液支管分别连接内置导流筒的内底部,各内置导流筒的上端口低于柱形外筒的上开
口,以使气液两相体系从各内置导流筒的上端口溢出后下沉至柱形外筒底部,所述柱形外筒底部设有反应产物排出管。
15.进一步的,上述柱形外筒内具有换热系统,其中柱形外筒采用外壁夹套式冷却,在内置导流筒中设有冷却管,所述冷却管伸出柱形外筒外以与外置的冷却系统进行连接。
16.进一步的,上述上封头设有顶部测量口,用于监测反应釜内温度和压力;所述上封头为平板形,所述上封头与柱形外筒的上开口采用平面法兰连接,所述上封头和柱形外筒相接触的密封面采用o型密封圈。
17.进一步的,上述下封头为椭圆形,所述下封头与外壳采用焊接连接,椭圆型设计光滑,无死角,以解决聚合物极易挂壁的问题。
18.进一步的,上述内置导流筒具有2-8个,且每个导流筒下方均设置气相进料口和液相进料口,所述出气支管和出液支管分别连接气相进料口和液相进料口。
19.进一步的,上述气体分布器和液体分布器均为封闭的容器,气体分布器设在液体分布器的下方,气体分布器与液体分布器之间通过出气支管连通,所述气体分布器和液体分布器上分别设有所述进气管和进液管,仅仅各根出液支管分别连接内置导流筒的内底部。
20.本发明用于乙烯齐聚生产α-烯烃的环流反应器的反应装置,其特征在于:包括原料预处理单元、反应单元和分离单元;所述原料预处理单元包括原料精制系统,所述原料精制系统包括乙烯、氢气和环乙烷的精制系统或溶剂纯化装置;所述气体精制系统、溶剂纯化装置用于脱水和脱氧,使水氧含量小于5ppm;所述反应单元包括所述环流反应器和溢流罐;所述环流反应器的进气管和进液管分别与各原料精制系统的出端连接;所述分离单元包括闪蒸罐和若干个精馏塔,所述闪蒸罐的进料端与溢流罐的液相出料端相连,闪蒸罐的出料端与精馏塔的进料端相连。
21.进一步的,上述催化剂配制单元包括催化剂预混罐和催化剂储罐;所述催化剂预混罐为带有搅拌桨的釜式储罐,且催化剂预混罐内用高纯氮气密封保护。
22.进一步的,上述分离单元的精馏塔包括依次串联的脱轻塔(c2塔)、癸烯回收塔(c10塔)和溶剂回收塔(c6塔),溶剂回收塔(c6塔)还另连接有1-己烯纯化塔(c4)。
23.本发明乙烯选择性齐聚生产线性α-烯烃的生产工艺,其特征在于:包括如下步骤:来自界区的乙烯,经过脱氧、脱水处理,使水氧含量小于5ppm,并同循环乙烯混合,经过乙烯压缩机压缩至5mpa后进入反应装置,采用的溶剂为环己烷,新鲜的环己烷水含量较高,需经过溶剂纯化装置干燥脱水,经脱水处理合格后进入反应装置,催化剂各组分在高纯氮气的保护下使环己烷稀释到一定浓度,然后一次性打入环流反应器内;将溶剂、催化剂从底部液体进样口注入环流反应器内,通过液体分布器的喷射孔进入内置导流筒;将乙烯和氢气从底部通过气体进样口注入反应器,通过气体分布器进入内置导流筒,由底部布气造成液相的密度差从而推动气液相体系由高密度区向低密度区自下而上流动,可实现原料的充分混合,原料在流动过程中在催化剂的作用下,乙烯发生聚合反应,到达内置导流筒顶部后外溢至内置导流筒外,再利用重力作用向下流动,反应产物和部分溶剂从环流反应器
底部流出进入溢流罐;将反应产物在溢流罐内进行淬灭后,进入分离单元;反应物料进入闪蒸罐,经过闪蒸后,在闪蒸罐顶部闪蒸出循环乙烯,循环乙烯并入新鲜乙烯重新参与反应,闪蒸罐的液相进入精馏塔,经过多次精馏得到1-辛烯产品、环己烷、少量烯烃混合物以及残液。
24.本发明优点是:气体流体和液体流体进入内置导流筒底部,由底部布气造成液相的密度差从而推动气液相体系由高密度区向低密度区自下而上流动,而后外溢至内置导流筒外,再利用重力作用向下流动,从可以实现气体、液体流体的定向流动,流动损失少,混合均匀,环流液速较快,气液接触时间较长,气液接触良好,极大提高了体系传质效率,因此该反应器的转化效率较高,能耗低;该反应器无运动密封件,结构简单,设备费用低,并且由于环流反应器内流体的循环流动,强化了反应物之间的混合、传热和传质等过程,因此,它适合较大处理量的气液反应的顺利进行,该装置具有,工艺简单,设备费用低等特点,可适用于高温高压的反应过程,传质能力较强,可促进催化剂活性和选择性的提高,从而降低聚乙烯蜡以及高聚物的生成,减少聚合物挂壁的情况,有利于长周期连续运行。
25.附图说明:下面结合附图对本发明专利进一步说明;图1是本发明环流反应器的构造示意图;图2是本发明反应装置的原理框图;图3是气体分布器与液体分布器一种实施例的原理框图;图4是气体分布器与液体分布器另一种实施例的原理框图。
26.具体实施方式:下面结合附图和具体实施方式对本发明进一步说明。
27.本发明用于乙烯齐聚生产α-烯烃的环流反应器,包括柱形外筒1、分别设在柱形外筒1上开口、下开口上的上封头2和下封头3,所述柱形外筒内设有2-8根内置导流筒4,各根内置导流筒4的轴心线与柱形外筒的轴心线平行,所述柱形外筒的内底部设有气体分布器5和液体分布器6,所述气体分布器5和液体分布器6上分别设有伸进柱形外筒外的进气管7和进液管8,所述气体分布器和液体分布器上还分别设有多根出气支管9和出液支管10,各根出气支管9和出液支管10分别连接内置导流筒4的内底部,各内置导流筒的上端口低于柱形外筒的上开口,以使气液两相体系从各内置导流筒的上端口溢出后下沉至柱形外筒底部,所述柱形外筒底部设有反应产物排出管11。
28.每个内置导流筒4下部均设置气相进料口和液相进料口,所述出气支管9和出液支管10分别连接气相进料口和液相进料口。
29.上述柱形外筒内具有换热系统,其中一种方式是柱形外筒采用外壁夹套式冷却,即在柱形外筒的外周具有夹层,夹层内设有冷却管,冷水管与柱形外筒外的冷却系统连接,或者在内置导流筒中设有冷却管,所述冷却管伸出柱形外筒外以与外置的冷却系统进行连接,上述冷却系统可以水冷却系统,或者空调冷却系统等;冷却器设定温度可以在0~5℃,经冷却器冷却后的循环冷却液与柱形外筒内温度形成连锁,根据柱形外筒内的温度高低调节循环冷却液进料速率。
30.为了便于检测柱形外筒内的参数,上述上封头设有顶部测量口12,用于监测反应釜内温度和压力;所述上封头2为平板形,所述上封头2与柱形外筒的上开口采用平面法兰
连接,所述上封头2和柱形外筒相接触的密封面采用o型密封圈,通过o型密封圈和平面法兰连接,从而便于柱形外筒的上封头2的拆装。
31.为了设计合理,上述下封头为椭圆形,所述下封头与外壳采用焊接连接,椭圆型设计光滑,无死角,从而可以较少聚合物极易挂壁的问题。
32.如图4所示,其中一种实施例是气体分布器5和液体分布器6均为封闭的容器,气体分布器5设在液体分布器6的下方,气体分布器与液体分布器之间通过出气支管9连通,所述气体分布器和液体分布器上分别设有所述进气管7和进液管8,仅仅各根出液支管10分别连接内置导流筒4的内底部。
33.如图3所示,其中一种实施例是气体分布器5和液体分布器6均为封闭的容器,气体分布器5设在液体分布器6的上方或下方,气体分布器与液体分布器之间没有管路连通,所述气体分布器和液体分布器上分别设有所述进气管7和进液管8,各根出液支管10和出气支管9分别连接内置导流筒的内底部。
34.本发明环流反应器无需机械搅拌,可降低设备投资和能耗消耗,利用内置导流筒的导流作用较好实现反应物之间的接触,从而更好的促进反应,具有更好的传质效果以及更低的传质成本。
35.本发明用于乙烯齐聚生产α-烯烃的环流反应器的反应装置,包括原料预处理单元a1、反应单元a2和分离单元a3;其中原料预处理单元a1包括原料精制系统,所述原料精制系统包括乙烯、氢气和环乙烷的精制系统或溶剂纯化装置a4;所述气体精制系统、溶剂纯化装置用于脱水和脱氧,使水氧含量小于5ppm;其中反应单元a2包括所述环流反应器a5和溢流罐a6;所述环流反应器的进气管7和进液管8分别与各原料精制系统a1的出端连接;其中分离单元a3包括闪蒸罐a8和若干个精馏塔,所述闪蒸罐的进料端与溢流罐a6的液相出料端相连,闪蒸罐的出料端与精馏塔的进料端相连,分离单元的精馏塔包括依次串联的脱轻塔c2、癸烯回收塔c10和溶剂回收塔c6,溶剂回收塔c6还另连接有1-己烯纯化塔c4;工作时,反应液经闪蒸罐分离出部分乙烯,绝大部分液相进入脱轻塔(c2塔),塔顶分离得少部分乙烯,塔釜液进入癸烯回收塔(c10塔),塔釜液为重组分副产物(1-辛烯和1-癸烯),塔顶馏出液继续进入溶剂回收塔(c6塔),此时塔釜为环己烷溶剂,经换热器后返回反应器中参与反应,最终塔顶馏出液进入1-己烯纯化塔(c4)分离,塔釜得到1-己烯,塔顶得到轻组分副产物(1-丁烯)。
36.进一步的,上述催化剂配制单元包括催化剂预混罐a7和催化剂储罐(为现有技术,图中未示出);所述催化剂预混罐为带有搅拌桨的釜式储罐,且催化剂预混罐内用高纯氮气密封保护。
37.在环流反应器和分离单元中间还可以设有一终止反应段,设备自动注射终止剂使反应终止,且该终止反应段外部与冷凝器相连,冷凝器设定温度低于5℃,使反应产物温度降低至15℃以下,反应所得产物随后通过闪蒸釜分离后,通过若干精馏塔分离处理,最终获得纯度达标的目标产物线性α-烯烃和可循环使用的溶剂。
38.本发明乙烯选择性齐聚生产线性α-烯烃的生产工艺,包括如下步骤:来自界区的乙烯,经过脱氧、脱水处理,使水氧含量小于5ppm,并同循环乙烯混合,
经过乙烯压缩机压缩至5mpa后进入反应装置,采用的溶剂为环己烷,新鲜的环己烷水含量较高,需经过溶剂纯化装置干燥脱水,经脱水处理合格后进入反应装置,催化剂各组分在高纯氮气的保护下使环己烷稀释到一定浓度,然后一次性打入环流反应器内;将溶剂、催化剂从底部液体进样口注入环流反应器内,通过液体分布器的喷射孔进入内置导流筒;将乙烯和氢气从底部通过气体进样口注入反应器,通过气体分布器进入内置导流筒,由底部布气造成液相的密度差从而推动气液相体系由高密度区向低密度区自下而上流动,可实现原料的充分混合,原料在流动过程中在催化剂的作用下,乙烯发生聚合反应,到达内置导流筒顶部后外溢至内置导流筒外,再利用重力作用向下流动,反应产物和部分溶剂从环流反应器底部流出进入溢流罐;将反应产物在溢流罐内进行淬灭后,进入分离单元;反应物料进入闪蒸罐,经过闪蒸后,在闪蒸罐顶部闪蒸出循环乙烯,循环乙烯并入新鲜乙烯重新参与反应,闪蒸罐的液相进入精馏塔,经过多次精馏得到1-辛烯产品、环己烷、少量烯烃混合物以及残液。
39.下面列举实施例:实施例1 乙烯选择性三聚连续反应如图1所示,来自界区的乙烯,经过脱氧、脱水处理,使水氧含量小于5ppm,并同循环乙烯混合,经过乙烯压缩机压缩至5mpa后进入反应装置,其中乙烯进料量为200kg/h,循环乙烯的量为50kgh,采用的溶剂为环己烷,新鲜的环己烷水含氧量较高,需经过溶剂纯化装置干燥脱水,经脱水处理至水氧含量小于5ppm后进入反应装置;催化剂各组分在高纯氮气的保护下使环己烷稀释到一定浓度,然后一次性打入反应器内,其中溶剂进料量240kg/h,将溶剂、催化剂从底部液体进样口注入反应器内,通过分流导管由液体分布器的喷射孔进入导流筒;催化剂选择中国发明专利cn202211158189.8应用例1所述的铬配合物及其配比,用溶剂环己烷将催化剂稀释成25mol/l的溶液后直接进料至反应器,催化剂溶液进料量10.0kg/h。调节剂以气体形式与乙烯混合后进入至反应器内,进料量0 .2kg/h,在125℃,5.0mpa的乙烯压力下进行反应,乙烯选择性齐聚生成1-己烯、1-辛烯、1-癸烯等等,同时副产少量1-丁烯、2-己烯和3-己烯等c6副产物、其它c12+低聚物。
40.该装置在上述流程下连续运行400h未发生反应器挂胶、管道堵塞等影响装置长周期运行的问题,通过反应釜内气液相定向流动,通过导流筒由底部布气造成液相的密度差从而推动气液相体系由高密度区向低密度区自下而上流动,可实现原料的充分混合,该方式可强化传质,进而提高催化活性、提高目的产物的选择性;并且,规避了传统釜式反应器内搅拌桨上易壁挂胶及盘管粘结低聚物等问题。
41.催化性能见表1。
42.由此可见,本发明实施例采用环流反应器,内置导流筒使气液相定向高速流动的方式进行传质,达到传质传热的目的,相对于搅拌桨,该传质方式传质效果好,设备成本低和能耗低。相对于夹套+釜内盘管撤热,采用气液相定向流动+导流筒撤热具有操作简单,易清洗且能耗低等优势。
43.对比例1乙烯选择性三聚连续反应乙烯齐聚反应器采用反应釜,通过夹套+釜内盘管通循环水撤除反应热;乙烯经脱氧脱水处理后氧含量小于5ppm、水含量小于5ppm,通过分布器进料至反
应釜内液面以下,乙烯进料量200kg/h,循环乙烯的量为60kgh;溶剂环己烷经脱氧脱水预处理后氧含量小于5ppm、水含量小于5ppm,饱和乙烯后进料至反应釜,溶剂进料量240kg/h。
44.催化剂选择中国发明专利cn202211158189.8应用例1所述的铬配合物及其配比,用溶剂环己烷配制成25mol/l的溶液后直接进料至反应器,催化剂溶液进料量10.0kg/h;调节剂以气体形式混入乙烯循环气后进料至反应器内,进料量0 .2kg/h,在125℃,5 .0mpa的乙烯压力下进行反应,乙烯选择性齐聚生成1-己烯、1-辛烯、1-癸烯等等,同时副产少量1-丁烯、2-己烯和3-己烯等c6副产物、其他c12+低聚物。
45.该装置在上述流程下连续运行180h时发现反应器存在堵塞现象,停止反应,取样分析,清理反应釜,计算各组分的选择性和催化活性。
46.催化性能见表1。
47.由此可见,由于长周期反应时,反应釜气相分布不均,导致反应器内温度梯度较大,温度较低的地方出现聚合物粘釜,导致撤热困难,1-己烯选择性稍有降低、1-辛烯选择性稍有增加、低聚物pe选择性稍有增加,装置连续运行周期明显变短,另外,由于乙烯在液相中的传质受限,使催化剂活性稍降低。
48.实施例2 乙烯选择性四聚连续反应如图1所示,来自界区的乙烯,经过脱氧、脱水处理,使水氧含量小于5ppm,并同循环乙烯混合,经过乙烯压缩机压缩至5mpa后进入反应装置,其中乙烯进料量为200kg/h,循环乙烯的量为70kgh。采用的溶剂为环己烷,新鲜的环己烷水含氧量较高,需经过溶剂纯化装置干燥脱水,经脱水处理至水氧含量小于5ppm后进入反应装置;催化剂各组分在高纯氮气的保护下用环己烷稀释到一定浓度,然后一次性打入反应器内;其中溶剂进料量240kg/h。将溶剂、催化剂从底部液体进样口注入反应器内,通过分流导管由液体分布器的喷射孔进入导流筒。
49.催化剂选择中国发明专利cn202211158189.8应用例1所述的铬配合物及其配比,用溶剂环己烷将催化剂稀释成1mol/l的溶液后直接进料至反应釜,催化剂溶液进料量10 .0kg/h,调节剂以气体形式与乙烯混合后进入至反应器内,进料量5kg/h,在55℃,5 .5mpa的乙烯压力下进行反应,乙烯选择性齐聚生成1-辛烯、1-己烯、1-癸烯等等,同时副产少量1-丁烯、甲基环戊烷和亚甲基环戊烷等c6副产物、其他c14+低聚物。
50.该装置在上述流程下连续运行140h,未发生反应器挂胶、管道堵塞等影响装置长周期运行的问题,通过反应釜内气液相定向流动,通过导流筒由底部布气造成液相的密度差从而推动气液相体系由高密度区向低密度区自下而上流动,可实现原料的充分混合;该方式可强化传质,进而提高催化活性、提高目的产物的选择性。并且,规避了传统釜式反应器内搅拌桨上易壁挂胶及盘管粘结低聚物等问题。
51.催化性能见表1。
52.对比例2乙烯选择性四聚连续反应乙烯齐聚反应器采用反应釜,通过夹套+釜内盘管通循环水撤除反应热。
53.乙烯经脱氧脱水处理后氧含量小于5ppm、水含量小于5ppm,通过分布器进料至反应釜内液面以下,乙烯进料量200kg/h,循环乙烯的量为80kgh。溶剂环己烷经脱氧脱水预处理后氧含量小于5ppm、水含量小于5ppm,饱和乙烯后进料至反应釜,溶剂进料量240kg/h。
54.催化剂选择中国发明专利cn202211158189.8应用例1所述的铬配合物及其配比,
用溶剂环己烷配制成1mol/l的溶液后直接进料至反应釜,主催化剂溶液进料量2 .0kg/h。调节剂以气体形式混入乙烯循环气后进料至反应釜内,进料量0.5kg/h,在55℃,5 .5mpa的乙烯压力下进行反应,乙烯选择性齐聚生成1 辛烯、1 己烯、1 癸烯等等,同时副产少量1 丁烯、甲基环戊烷和亚甲基环戊烷等c6副产物、其他c14+低聚物。
55.该装置在上述流程下连续运行80h时发现反应器存在堵塞现象。停止反应,取样分析,清理反应釜,计算各组分的选择性和催化活性,相关结果见表1,催化性能见表1。
56.由此可见,如同乙烯三聚一样由于长周期反应时,反应釜气相分布不均,导致反应器内温度梯度较大,温度较低的地方出现聚合物黏釜,导致撤热困难,1-辛烯选择性稍有降低、1-己烯选择性稍有增加、低聚物pe选择性明显增加,装置连续运行周期明显变短。另外,由于乙烯在液相中的传质受限,使催化剂活性稍降低。
57.表1 实施例和对比例性能结果本发明优点是:(1) 首次提出环流反应器用于乙烯齐聚反应,具有结构简单、传质传热性能好、能耗低等优点;(2) 环流反应器中设置2~8根导流筒,设置导流筒可实现环流反应器内流体的循环流动,强化了反应物之间的混合、传热和传质等过程;(3)导流筒内设置循环冷却液,实现反应器撤热功能,相比于冷凝盘管,该技术避免了长期运行聚合物容易在盘管结垢,影响传热效率,且难以清洗等问题。
58.上列较佳实施例,对本发明的目的、技术方案和优点进行了进一步详细说明,所应理解的是,以上所述仅为本发明的较佳实施例而已,并不用以限制本发明,凡在本发明的精神和原则之内,所作的任何修改、等同替换、改进等,均应包含在本发明的保护范围之内。