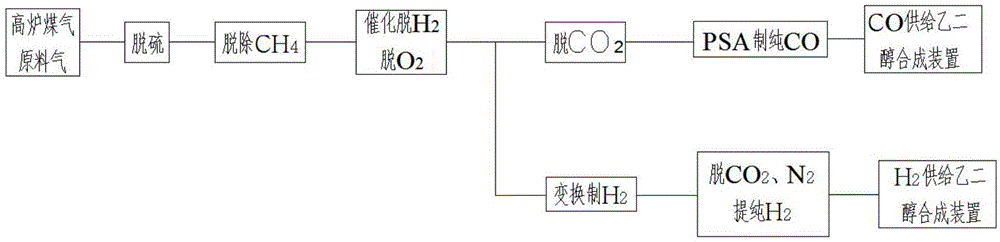
本发明属于化工
技术领域:
,涉及一种煤气生产h2/co原料气的方法及装置。
背景技术:
:近年来,我国工业持续迅速发展,钢铁焦化行业产量逐年增高,根据国家统计局2014年统计结果显示,2013年,我国生铁产量已达7.08亿吨,焦炭产量达4.79亿吨,粗钢产量达7.78亿吨。在这些工业生产过程中,会伴随产生大量的焦炉煤气(炼焦)、高炉煤气(炼铁)及转炉煤气(炼钢),简称“三气”。这些副产煤气总量每年可达上万亿立方米,并呈逐年增加的趋势。同时,其它的黑色金属和有色金属的冶炼过程中也会产生高炉煤气、转炉煤气以及气体组分类似于高炉煤气、转炉煤气的尾气。在钢厂“三气”中,高炉煤气虽然有效气体含量最低,但其排放量最大。高炉煤气主要成分为:co,co2,n2,h2,ch4等,其中co含量约占25%左右,co2和n2的含量分别占15%、55%左右,h2、ch4的含量很少。高炉煤气热值低,仅为3300~3800kj/nm3。由于高炉煤气中的co2,n2既不参与燃烧产生热量,也不能助燃,相反,还吸收大量的燃烧过程中产生的热量,导致高炉煤气的理论燃烧温度偏低,只有1300℃左右,甚至有些只有900℃左右。高炉煤气常温下燃烧不稳定,一般工业炉不能单一以高炉煤气为燃料,需与焦炉煤气或转炉煤气等高热值煤气参混使用,但是高炉煤气与焦炉煤气或与转炉煤气混合使用热值波动大,不但对燃烧装置提出了更高要求,而且对产品质量亦有不同程度的影响。由于大部分企业高炉煤气富余,高热值煤气紧缺,因此存在着不同程度的高炉煤气放散现象,这不仅污染环境,而且浪费能源。如何有效利用这些热值低、杂质含量高、产量巨大、净化困难、环境污染严重的高炉煤气,是国内外都需要解决的难题。现在高炉煤气普遍是用来燃烧,但由于其热值低,不燃组分含量高,燃烧效率和利用率差,并且浪费了含有的大量的宝贵的可以用来做高附加价值的化工原料的co。现在转炉煤气普遍是用来燃烧或发电,但由于其热值低,燃烧效率和利用率差,并且发电所产生的收益要远低于用其处理后作为化工原料生产高附加价值的化工产品的收益。另外,变压吸附(pressureswingadsorption,psa)的基本原理是利用气体组份在固体材料上吸附特性的差异,通过周期性的压力变换过程来实现气体的分离或提纯。任何一种吸附对于同一被吸附气体(吸附质)来说,在吸附平衡情况下,温度越低,压力越高,吸附量越大。反之,温度越高,压力越低,则吸附量越小。如果温度基本不变,在加压的情况下吸附,用减压(抽真空)、用弱吸附气体吹扫或低压解吸的方法,称为变压吸附。变压吸附一般包括吸附、解吸(抽真空、吹扫或抽真空加吹扫)以及可能存在的均压、充压、顺放、逆放、置换等。可见,变压吸附是通过改变压力来吸附和解吸的。有压力变化就存在着能量的损失,而现在的变压吸附的方法是没有对这部分的能量进行回收的,造成了能量的白白损失,降低了变压吸附的经济效益,从而造成了在压力过高的情况下应该变压吸附方法,成本过高的情况。随着工业的发展,出现了很多高压条件下的气体分离的情况,操作压力越高,越导致过高的运行能耗。另一方面,由于在变压吸附的工业操作过程中,众多设备之间的加压、降压之间的变换非常频繁,导致了很难将其能量较好地回收。技术实现要素:发明目的:本发明的目的是提供工艺流程简单、设备投资少和功耗小的由高炉煤气和/或转炉煤气为主成分的原料气经过多种处理步骤制备符合高标准要求的合成乙二醇的原料气的工艺,该工艺不但能够缓解国内的能源短缺及高炉煤气浪费严重的现状,且能进一步增大煤气特别是高炉煤气的经济和环境效益;本发明的另一目的是提供其装置。技术方案:本发明所述的一种煤气生产h2/co原料气的方法,包括如下步骤:第1步,将煤气在源头或第一预处理流程中分为两部分,其中第一部分气体经第一预处理流程后通过变压吸附方法分离co和n2,得到co;第二部分气体通过变换反应将气体中的co变换为h2,得到含co2、h2和n2的反应气,再从反应气中分离得到h2;第2步,将第1步得到的co和h2作为h2/co原料气。所述的h2/co原料气用于醇。所述的煤气主要包括高炉煤气或转炉煤气;煤气中可能还含有其他的尾气或者驰放气中的一种或几种的混合。第一部分气体所占的体积分数为15~70%,第二部分气体所占的体积分数为30~85%。第二部分气体与第一部分气体变压吸附方法分离co和n2得到co过程中产生的置换尾气或/和顺放气体进行混合后进行变换反应。所述的第一预处理流程包括除尘、除磷、除砷、脱水、脱氢脱氧、脱硫、脱co2、除ch4、脱重组分中的一步或几步的组合。进一步,所述的第一预处理流程包括脱硫和脱co2,脱co2与脱硫同步进行或者脱co2处于脱硫步骤后。进一步,所述的第一预处理流程还包括除ch4或/和脱氢脱氧;除ch4处于脱硫步骤之后;脱氢脱氧处于除ch4步骤之后;将所述煤气在脱硫、脱甲烷或脱氢脱氧后分为两部分。第二部分气体在变换反应之前经第二预处理流程,所述第二预处理流程包括与第一部分气体处于混合态时所经的第一预处理步骤以及单独的预处理步骤,所述第二预处理流程包括除尘、除磷、除砷、脱水、脱氢脱氧、脱硫、脱co2、除ch4、脱重组分中的一步或几步的组合。第一预处理流程和第二预处理流程中,所述除ch4是通过催化燃烧反应脱除ch4;脱氢脱氧是通过催化反应方法进行脱除。从所述含co2、h2和n2的反应气中分离得到h2时,经过脱co2和n2,其中,脱n2通过变压吸附分离方法,脱co2通过变压吸附分离方法或吸收法。第一预处理流程中的脱co2通过变压吸附分离方法或吸收法,采用吸收法时,第一预处理流程中的吸收剂脱co2后用于第二部分气体制h2过程中的co2脱除。一种煤气生产h2/co原料气的装置,包括:第一预处理装置,用于对煤气原料气进行预处理;分流装置,连接于第一预处理装置或煤气原料气输出口,并且设有第一部分气体出口和第二部分气体出口,用于将气体分成两股;与第一预处理装置或第一部分气体出口相连的变压吸附装置,用于对第一部分气体通过变压吸附方法分离co和n2;变换反应器,连接于分流装置的第二部分气体出口,用于对第二部分气体进行变换反应将气体中的co变换为h2,得到含co2、h2和n2的反应气;h2分离装置,连接于变换反应器,用于从含co2、h2和n2的反应气中分离得到h2。所述的煤气生产h2/co原料气的装置,还包括生产醇的装置,连接于变压吸附装置的co出口和h2分离装置的h2出口,用于反应合成碳原子数≥2的醇。所述的第一预处理装置连接于主要含有高炉煤气或者转炉煤气的原料气输出口。主要含有高炉煤气或者转炉煤气的原料气输出口还连接有焦炉煤气、其他的尾气或者驰放气的接入口。变压吸附装置通过管路与变换反应器相连,用于将第一部分气体变压吸附方法分离co和n2得到co过程中产生的置换气体或/和顺放气体与第二部分气体进行混合后进行变换反应。所述的第一预处理装置包括除尘装置、除磷装置、除砷装置、脱水装置、脱氢脱氧装置、脱硫装置、脱co2装置、脱co装置或者除ch4装置中的一个或几个的组合。相应的作用为除尘、除磷、除砷、脱水、脱氢脱氧、脱硫、脱co2、脱co或者除ch4中的一个或几个的组合。第二预处理装置同理。进一步,所述的第一预处理装置包括脱硫装置和脱co2装置,脱co2装置与脱硫装置集成或者脱co2装置处于脱硫装置下游侧。进一步,所述的第一预处理装置还包括除ch4装置或/和脱氢脱氧装置;除ch4装置处于脱硫装置下游侧;脱氢脱氧装置处于除ch4装置下游侧;分流装置与除ch4装置气体出口、脱硫装置气体出口或脱氢脱氧装置气体出口相连。即当含除ch4装置时,除ch4装置处于脱硫装置下游侧,脱硫装置和脱co2装置分开时,除ch4装置处于脱硫装置下游侧,脱co2装置上游侧;当含脱氢脱氧装置时,脱氢脱氧装置处于脱硫装置下游侧,脱硫装置和脱co2装置分开时,脱氢脱氧装置处于脱硫装置下游侧,脱co2装置上游侧,如果还含除ch4装置,脱氢脱氧装置处于除ch4装置下游。对于不同的组合,显然的,变压吸附装置连接于第一预处理装置的尾部(即最后第一预处理装置的最后一个单元结束后),或者连接于分流装置第一部分气体出口。分流装置处于第一预处理装置的前端、中间单元或尾部。变换反应器的气体进口与第二预处理装置相连,所述第二预处理装置包括两部分气体处于混合态时所经的第一预处理装置以及通过分流装置与其相连的单独的预处理装置,所述第二预处理装置包括除尘装置、除磷装置、除砷装置、脱水装置、脱氢脱氧装置、脱硫装置、脱co2装置、除ch4装置、脱重组分装置中的一个或几个的组合。单独的预处理装置也可以不设置,此时,变换反应器与分流装置的第二部分气体出口直接相连。h2分离装置为第二变压吸附装置,或者h2分离装置为串联的吸收法脱co2装置和第三变压吸附装置。h2提取时,可通过第二变压吸附装置直接将含co2、h2和n2的反应气中的co2和n2脱除,分离得到h2,或者先通过吸收法脱co2装置反应气中的co2脱除,再通过第三变压吸附装置将h2和n2分离得到h2。上述的变压吸附装置、第二、第三变压吸附装置仅为表述清楚对装置进行编号命名,并无结构上的限定,除此之外,本发明中对涉及的变压吸附装置的命名还有一些功能上的命名如变压吸附提氢装置、变压吸附分离co和n2装置、变压吸附脱碳装置等,均是为了清楚表述本发明,而非对结构进行主要限定。第一预处理装置中的脱co2装置为变压吸附法脱co2装置或吸收法脱co2装置,采用吸收法脱co2装置时,第一预处理装置中的吸收法脱co2装置的吸收液出口连接于h2分离装置中的吸收法脱co2装置。另外,在上述的分离过程中,需要使用了较多的变压吸附除杂的单元操作,变压吸附过程中操作压力高导致的能耗大、升降压的操作变换频繁,当压差波动和能量波动都很大、冲击载荷很大时,超过了常规的能量回收设备的允许的波动范围,会导致机器设备寿命变短、会引起安全等多种隐患甚至是机器设备无法正常工作,以至于导致的能量难以回收利用的问题。本发明把正常的吸附分离过程和能量回收过程以及某种气体或液体加压过程耦合在一起,回收了能量,能量利用率高,工艺过程简单,降低了变压吸附的运营成本,从成本的角度拓展了变压吸附的生存空间。主要是通过由膨胀机、电动机、压缩机或泵组成同轴驱动的能量回收系统进行能量回收操作,该设备还具有结构紧凑,整机效率高、整机设备费用和运行费用都比较低,具有较好的经济效益。在上述的变压吸附过程中,还可以使用如下所示的方法:一种用变压吸附的能量回收方法,包括如下步骤:对变压吸附工作中的压力降低过程中的气体采用膨胀机回收其能量;在膨胀机的气体入口和/或气体出口处通过流体缓冲装置平抑气压的波动;或者,通过膨胀机转轴上的转动阻力装置抑制其转速的波动。所述的流体缓冲装置选自调节阀或者缓冲罐中的一种或者几种的组合;所述的转动阻力装置是指飞轮。所述的压力降低过程是指均压、充压、置换、带压冲洗、顺放或逆放等存在压力变化的过程。在一个实施例中,膨胀机带动发电机发电,发电机所产生的电能用于其它需要电力的设备,或者发电机所产生的电能通过压缩机对变压吸附过程中需要升压的气体或液体进行压缩。通过控制与压缩机相连的电动机的输入电流以补充其需要的电能;可以通过电池组或者电容组来平抑输入至电动机的电能的波动。在一个实施例中,发电机所产生的电能并入电网,电网的作用是利用容纳能力平抑膨胀机所产生的电能的波动;电网中所获得的电能用于其它需要电力的设备,或者通过压缩机对变压吸附过程中需要升压的气体进行压缩。在一个实施例中,膨胀机的转轴与电动机的转轴为同轴连接,由膨胀机和电动机共同带动压缩机工作。基于上述的方法,还可以采用如下的装置:一种变压吸附装置,包括有:1)、至少一个高压吸附塔;2)、至少一个能量回收装置,所述的能量回收装置中包括有膨胀机,用于回收高压吸附塔中排出的高压气体的能量;膨胀机的气体入口和/或气体出口处连接有流体缓冲装置;或者,在膨胀机的转轴上设置转动阻力装置。所述的流体缓冲装置选自调节阀或者缓冲罐中的一种或者几种的组合;所述的转动阻力装置是指飞轮。在一个实施例中,高压吸附塔通过能量回收装置与低压吸附塔之间连接。在一个实施例中,变压吸附装置中还包括有发电机,膨胀机与发电机连接。发电机与其它需要使用电力的设备连接,或者发电机带动压缩机对变压吸附过程中需要升压的气体或液体进行压缩。发电机与电网连接,电网的作用是利用容纳能力平抑发电机所产生的电能的波动。在一个实施例中,变压吸附装置中还包括有压缩机和电动机,并且膨胀机的转轴与电动机的转轴为同轴连接,由膨胀机和电动机共同带动压缩机工作。电动机上还安装电池组或者电容组。在压缩机的气体入口和/或气体出口还设置有缓冲罐。与一般的变压吸附方法相比,本发明的方法和装置在的变压吸附方法增加了能量回收的过程,把正常的吸附分离过程和能量回收过程以及某种气体或液体加压过程耦合在一起,回收了能量,提高了系统的能量利用率,降低了变压吸附的运营成本,从成本的角度拓展了变压吸附的生存空间,工艺过程简单,安全系数高,机组自动化程度高,操作简便,设备占地面积少,保证了产品纯度,保证了回收率,操作灵活,降低塔设备数量与尺寸。有益效果:本发明提出了一种高炉煤气和/或转炉煤气等原料气经多种处理步骤制备合成乙二醇的原料气的思路,不但为煤气特别是高炉煤气的综合利用提供了一条新的技术路线,而且进一步提高了煤气特别是高炉煤气的经济价值;本发明公开的由高炉煤气、转炉煤气等原料气制备h2/co原料气工艺,氮气浓度可达工业级要求并能够回收再利用;本发明公开的由高炉煤气、转炉煤气等原料气制备合成乙二醇的原料气的整体式工艺通过大量实验、模拟计算、炼钢厂实地调研和多年的工程设计经验得出,物料匹配和热量利用均从整体的工艺考虑,优化了工艺流程。附图说明图1是高炉煤气制备h2/co原料气的工艺方法流程图;图2是实施例1中h2/co原料气制备方法工艺流程图;图3是实施例2中h2/co原料气制备方法工艺流程图;图4是实施例3中h2/co原料气制备方法工艺流程图;图5是对照例1中h2/co原料气制备方法工艺流程图;图6是一种应用于变压吸附过程的能量回收装置的结构图;图7是另外一种应用于变压吸附过程的能量回收装置的结构图;图8是集成了能量回收装置的两塔变压吸附净化h2装置;图9是集成了能量回收装置的三塔变压吸附净化h2装置;图10为高炉煤气制备h2/co原料气的装置图;其中1是吸附塔,2是透平膨胀机的一级,3是压缩机,4是电动机,5是抽空气缓冲罐,6是真空泵,7是逆放气缓冲罐,8是逆放气压缩机,9是飞轮,10是电容组,11是被压缩气体进口缓冲罐,12是被压缩气体出口缓冲罐,13是透平进口高压缓冲罐,14是透平出口高压缓冲罐,15是透平进口低压缓冲罐,16是透平出口低压缓冲罐,17是透平膨胀机的二级,18是来料气缓冲罐,19是塔顶产品气缓冲罐,20是一级透平出口换热器,21是二级透平出口换热器。具体实施方式本发明所提供的h2/co原料气的生产方法,主要是利用了高炉煤气、转炉煤气等作为原料或主要原料(如主要原料占比在80%、90%以上)。煤气中可能还含有焦炉煤气、其他的尾气或者驰放气中的一种或几种的混合。上述的煤气的气体组成中主要包括了:n2、h2、co、co2、o2、ch4、h2s、cos等,在一些典型的高炉煤气中,其组成包括按体积百分比计的:n240~65%、h20.5~5%、o20.2~5%、co210~30%、co10~30%、ch40.1~2.0%、h2s5~400ppm、cos0.1~100ppm。以上的例如煤气等原料在进入本专利中的工艺和设备前,也可以通过常规的方法进行相应的除杂等预处理过程;这些前处理没有特别的限制。本发明中所述的“h2/co原料气”主要是指co和h2,它们是单独存在,h2/co原料气的用途可以用于在不同的催化剂上合成不同的化工原料。本发明中,在得到了含有h2和co的h2/co原料气之后,其主要是应用于生产乙二醇。由于本方法制得h2/co原料气的高质量,还可以用来制其他碳原子数≥2的醇等过程,如由甲醇制乙醇,以及其他通过加入co实现增链反应从而实现增加一个或多个碳原子(羰基化反应),之后需要调节产品种类可以在需要时再进行加氢h2而得到的产品。一种煤气生产h2/co原料气的方法,包括如下步骤:第1步,将煤气在源头或第一预处理流程中分为两部分,其中第一部分气体经第一预处理流程后通过变压吸附方法分离co和n2,得到co;第二部分气体通过变换反应将气体中的co变换为h2,得到含co2、h2和n2的反应气,再从反应气中分离得到h2;第2步,将第1步得到的co和h2作为h2/co原料气。在第1步中,通过采用变压吸附分离法(或称变压吸附方法)分离co和氮气,可采用本领域常规的吸附剂,如采用载铜基或载银基的吸附剂或金属有机骨架型吸附剂(mofs、zifs)、金属有机多面体(mops);吸附剂的载体可为活性炭、氧化铝、硅胶、分子筛、蜂窝陶瓷、独居石、蜂窝金属、金属板、波纹填料、波纹板、纤维(布)材料和结构、编织物、金属发泡体、陶瓷发泡体、石墨基发泡体等。采用变压吸附分离法分离co和氮气,变压吸附的吸附压力为0.02~10mpa左右,操作温度0~150℃,在一些实施方式中,变压吸附的吸附压力为0.2~0.8mpa,操作温度为20~80℃,经变压吸附提取工业级氮气的体积分数≥99.2%,符合工业氮气标准gb3864-2008及其更新版本,可直接作为产品进行使用或出售。采用变压吸附分离法分离co和氮气时,需要在变压吸附的单元前面加入变温吸附方法,脱除水和重组分,因为水分和重组分会影响后续变压吸附步骤的效果,会对吸附剂产生不利的影响,会减少吸附剂的变压吸附的分离能力,甚至会对吸附剂造成不可逆的损害,使吸附剂劣化,甚至是致其失活、缩短其使用寿命,尤其是对于co和氮气分离的吸附剂损伤更为严重,迅速使得吸附剂劣化、致其失活、无法使用。当采用大于一套变压吸附装置串联时,变温吸附分离单元加在第一套变压吸附法的分离单元的前面,在变压吸附分离法分离co和氮气,得到不满足工业标准的氮气,当氮气压力大于0.15mpa时可以进入余压回收系统,回收氮气所带有压能,当采用变压吸附法时,可以在变压吸附装置内加入能量回收装置,在完成变压吸附分离过程同时回收变压吸附过程中浪费的压能。将来料煤气在源头或第一预处理流程中(包括第一预处理的任一中间环节或第一预处理结束后)进行分流,其中第一部分气体(其体积分数为15~70%)经过第一预处理流程后采用变压吸附分离法分离co和氮气,得到的纯co送入中间储气罐后,作为合成醇如乙二醇的原料气供下一步合成醇如乙二醇装置使用,co可调节其压力为0.15~10mpa再送入中间储气罐,以直接用于后续乙二醇的合成。而第二部分气体(其体积分数为30~85%)进行变换反应制取氢气,其反应压力0.3~20mpa,反应温度160~550℃,在一些实施方式中,反应压力0.3~4mpa,所得气体经除杂提纯氢气步骤得到纯氢气送入中间储气罐后,作为合成乙二醇的原料气供下一步合成乙二醇装置使用,同理的,氢气可调节其压力为1.5~20mpa再送入中间储气罐,以直接用于后续乙二醇的合成。由于此时的co含量较低,变换反应放热较少,不反应的气体较多,总的载热热容较大,以至于温升较少,减少其反应的苛刻度,有利于催化剂的寿命。将来料煤气分为两部分的比例,由后续的工艺需求和作为补充的外接气源的来料气的co和/或h2的数量和比例来决定的,对于仅利用来料气提纯所需气体,为充分利用来料气并达到合适的乙二醇生产碳氢比,第一部分气体所占的体积分数为30~35%,第二部分气体所占的体积分数为65~70%。co变换的基本原理是:这是一个可逆放热等体积的化学反应,从化学反应平衡角度来讲,提高压力对化学平衡没影响,但是降低反应温度和增加反应物中水蒸气量均有利于反应向生成co2和h2的方向进行。其反应器采用等温变换反应器。变换反应可采用本领域常规的催化剂,如采用铜基和/或铁基和/或钴钼系催化剂,催化剂包含铜和/或铁和/或锌和/或铝和/或锰和/或钴和/或钼和/或铈和/或镁和/或铬和/或钾和/或钒和/或镍和/或钛和/或钯和/或铂和/或钌和/或铑和/或钠和/或铷和/或铯和/或铌和/或锆和/或稀土元素和/或碱金属的氧化物和/或它们的硫化物和/或它们的可溶性盐和/或它们之间形成的复合金属氧化物。载体为活性炭、氧化铝、氧化硅、氧化镁、氧化钛、硅胶、分子筛、水滑石、尖晶石、蜂窝陶瓷、独居石、蜂窝金属、金属板、波纹填料、波纹板、纤维(布)材料和结构、编织物、金属发泡体、陶瓷发泡体、石墨基发泡体,铜和/或铁和/或锌和/或铝和/或锰和/或钴和/或钼和/或铈和/或镁和/或铬和/或钾和/或钒和/或镍和/或钛和/或钯和/或铂和/或钌和/或铑和/或钠和/或铷和/或铯和/或铌和/或锆和/或稀土元素和/或碱金属的氧化物和/或它们的硫化物和/或它们的可溶性盐和/或它们之间形成的复合金属氧化物等。经变换反应后的气体主要含氢气、氮气和二氧化碳以及一些其它的微量杂质,还可能存在没有反应的水蒸汽。先降温脱除水分,再脱除co2和氮气。在一个实施方式中,所述的第一预处理流程包括除尘、除磷、除砷、脱水、脱氢脱氧、脱硫、脱co2、除ch4、脱重组分中的一步或几步的组合,第一部分气体经第一预处理流程净化后有害杂质含量控制在硫化物≤1.15ppm,nh3≤200ppm,h2≤1000ppm,o2≤1000ppm,h2o≤100ppm,cl+≤0.03ppm,砷化物≤0.1ppm,焦油+尘≤1mg/nm3,萘≤1mg/nm3。更进一步有害杂质含量控制在硫化物≤0.1ppm,cl+≤0.01ppm,h2≤100ppm。在一个实施方式中,所述的第一预处理流程包括脱硫和脱co2,脱co2与脱硫同步进行或者脱co2处于脱硫步骤后。由于高炉煤气和/或转炉煤气含有微量的硫,会对后续的步骤中的多种催化剂(脱氢脱氧、变换、产品气要求、甚至是脱甲烷催化剂)和吸附剂(co和氮气分离)产生不利的影响,甚至是致其失活、缩短其使用寿命,并且其含量硫又低于一些耐硫催化剂所要求的最低的硫含量,所以要最先对其脱除。并且由于来料的高炉煤气和/或转炉煤气在开始温度会较高,这有利于采用金属氧化物类的脱硫剂的反应速度和脱硫效果。脱除硫或含的硫的各种杂质可以采用本领域常用方法如吸附法、膜分离方法、含有铁或锰或锌或铜或镍或钙或锡的氧化物或氢氧化物或它们之间形成的复合金属氧化物的固体脱硫剂、低温甲醇洗法、碳酸丙烯酯法、n-甲基吡咯烷酮法、聚乙二醇二甲醚法、聚乙二醇甲基丙醚法、磷酸三丁酯法、热钾碱法、活化热钾碱法、mea法、dea法、mdea法、dipa法、碳酸丙烯酯法+dipa、碳酸丙烯酯法+甘醇胺、环丁砜法、环丁砜+dipa法、环丁砜+mdea法、甲醇+仲胺法、烷基醇胺溶液法以及加入活性剂的mea法、dea法、mdea法、氨水洗涤法、烧碱法、ada法(stretford法)、栲胶法、lo-cat法、sulferox法、sulfint法、konox法、bio-sr法、萘醌法(takahax法)、金属酞菁法(pds法)、g-v(改良砷碱法)、砷碱法、msq法、sulfolin法、edta法、湿式氧化法、碱液吸收法、石灰石-石膏法、氨法、镁法、磷铵肥法、有机酸钠-石膏法、石灰-镁法、钙法、干式循环流化床法、氧化锌法、尿素法、络合吸收法、荷电干式吸收剂喷射法、等离子体法、电子束法、双碱法、硫化碱法,以及它们的组合。较好的采用固体脱硫剂、吸收液如活性dea/mdea的吸收法,脱硫效果好且成本低。其中脱除的硫送往硫回收系统,原料气经脱硫后气体中的硫脱除至0.01~0.1ppm。当采用吸收法时,吸收剂如dea/mdea同时对硫和二氧化碳具有吸收能力,则可以同时脱除硫和二氧化碳。脱硫在0.2~10mpa、20~700℃,在一些实施方式中(0.2~1.6mpa、20~400℃,如一些金属氧化物的固体脱硫剂280~400℃,吸收液20~70℃)下进行。采用吸收法可以实现脱co2与脱硫同步进行,最好再设置一步采用固体脱硫剂的精脱硫。当来料气含有硫中有机硫的含量过高,可以通过催化加氢反应或催化水解反应,使有机硫转化为h2s,再进行脱硫,使得经过处理后的气体的硫含量能够满足要求,当来料气含有硫中主要为so2且含量过高,可以通过催化加氢反应使so2转化为h2s,再进行脱硫,使得经过处理后的气体的硫含量能够满足要求。这里的催化加氢反应的催化剂以含有的铁和/或铜和/或钴和/或锰和/或钼和/或锌和/或铝和/或镍和/或钛和/或锆和/或钨和/或铈的金属和/或它们的氧化物和/或它们的硫化物和/或它们的可溶性盐和/或它们之间形成的复合金属氧化物为活性组分,以钛、锆、锰、铁、镍、钴、铜、钼、钨、锌、钴、铈的金属和/或它们的氧化物以及硅、稀土、碱金属、碱土金属、过渡金属的氧化物和/或它们的硫化物中的一种或几种为助剂。载体为活性炭、氧化铝、氧化硅、氧化镁、氧化钛、硅胶、分子筛、蜂窝陶瓷、独居石、蜂窝金属、金属板、波纹填料、波纹板、纤维(布)材料和结构、编织物、金属发泡体、陶瓷发泡体、石墨基发泡体等。这里的催化水解反应的催化剂以含有的镁和/或镧和/或钡和/或铝和/或钛和/或锆和/或铈和/或钾和/或钙和/或钴和/或钼和/或铁和/或铜和/或锰和/或锌和/或镍和/或钨的金属和/或它们的氧化物和/或它们的硫化物和/或它们之间形成的复合金属氧化物为活性组分,以钛、锆、镍、钴、钼、钴、铈的金属和/或它们的氧化物以及硅、稀土、碱金属、碱土金属、过渡金属的氧化物和/或它们的硫化物中的一种或几种为助剂。载体为活性炭、氧化铝、氧化硅、氧化镁、氧化钛、硅胶、分子筛、蜂窝陶瓷、独居石、蜂窝金属、金属板、波纹填料、波纹板、纤维(布)材料和结构、编织物、金属发泡体、陶瓷发泡体、石墨基发泡体等。co2会影响变压吸附分离co和氮气步骤的分离效果,由于co2在co和氮气分离步骤所用的吸附剂上有一定的吸附量,导致co2和co、co2和氮气分离系数都不高,co2的存在会导致co和氮气分离步骤不能够得到高纯度的co和氮气,会使得分离出的co和氮气气体中含有比较多的co2,所以要先行除去co2,脱除co2的步骤需要在co和氮气分离步骤之前,脱除co2的步骤是为了co和氮气分离步骤能使得co和氮气分别得到高纯度的co和氮气,同时这种先后顺序也符合吸附能力的逐级原则以及尽量吸附低含量组分、降低脱附能耗原则,减少了吸附压力、中间级加压步骤以及脱附步骤的损耗。对煤气中进行除co2的步骤,可以采用变压吸附法、吸收法以及它们的组合。其中吸收法包括:水洗法、低温甲醇洗法、碳酸丙烯酯法、n-甲基吡咯烷酮法、聚乙二醇二甲醚法、聚乙二醇甲基丙醚法、catacarb法(催化热碱法)、热钾碱法、活化热钾碱法、改良热碱法、热碳酸盐法、氨基酸盐法、氨水洗涤法、联尿(碱)法、g-v(改良砷碱法)、mea法、dea法、mdea法、dipa法、tea法、环丁砜法、环丁砜+dipa法、环丁砜+mdea法、甲醇+仲胺法、烷基醇胺溶液法以及加入活性剂的mea法、dea法、mdea法、tea法等,经脱碳后原料气中的co2脱除至0.01~0.8vol%,脱除的二氧化碳可以作为二氧化碳产品销售或作为其它过程的原料气或达到放空标准后放空,脱除co2在0.2~20mpa、20~150℃条件下进行,在一些实施方式中(0.2~1.6mpa、20~80℃),当采用吸收法作为脱碳的分离的单元时,通常会在气体中带出微量的吸收液,需要在其单元的后面加入变温吸附分离单元以脱除水和一些气体里含有的重组分等成分。变温吸附法脱除水分及重组分等成分;吸附剂为分子筛、活性炭、氧化铝、硅胶或它们的复合床层,其中脱除的含大量二氧化碳尾气当压力大于0.15mpa时可以进入余压回收装置回收能量。在一个实施方式中,除了包括上述的脱硫和脱co2后,所述的第一预处理流程还包括除ch4或/和脱氢脱氧;通过除ch4可获得满足标准的工业氮气(gb3864-2008及其更新版本)进行利用。经脱ch4后原料气中的ch4脱除至≤0.2vol%。由于除ch4反应所需的温度较高,使除ch4处于脱硫步骤之后,先行脱除,如果脱硫和脱co2步骤分开,使除ch4处于脱硫后脱co2前,有利于节省能量和换热设备,减少设备投资和运行费用。在一个实施方式中,除ch4主要是通过在一定的温度和压力下进行甲烷的催化燃烧反应脱除甲烷,控制反应温度及压力分别为200~1000℃(可进一步为250~350℃)和0.1~10mpa(可进一步为0.2~1.6mpa),防止催化剂失去活性。所用催化剂可以为本领域常规催化剂,例如为含有铁和/或铜和/或钴和/或锰和/或钼和/或锌和/或铝和/或镍和/或铬和/或铋和/或镁和/或钛和/或钡和/或钌和/或锆和/或铈和/或镧系和/或铂和/或钯和/或金和/或铑和/或钙的金属和/或它们的氧化物和/或它们的可溶性盐和/或它们之间形成的复合金属氧化物为活性组分。以钛、锆、锰、铁、镍、钴、铜、钼、钨、锌、钴、铈、铝、铬、铋、镁、钛、钡、钌、锆、铈、镧、铂、钯、金、铑、钙的金属和/或它们的氧化物和/或它们的可溶性盐和/或它们之间形成的复合金属氧化物以及硅、稀土、碱金属、碱土金属、过渡金属的氧化物中的一种或几种为助剂。载体为活性炭、氧化铝、氧化硅、氧化镁、氧化钛、硅胶、分子筛、蜂窝陶瓷、独居石、蜂窝金属、金属板、波纹填料、波纹板、纤维(布)材料和结构、编织物、金属发泡体、陶瓷发泡体、石墨基发泡体等。除ch4后原料气中的含量≤0.5%,进一步ch4≤0.1%。如果不需要满足标准的工业氮气,则可以不采用脱除甲烷的步骤。如果高炉煤气和/或转炉煤气等原料气中含有的氧的含量较高(大约>0.1%,典型气体中均大于该数值)时,会对后续的变换催化剂、co和氮气分离吸附剂产生不利的影响,甚至是致其失活、缩短其使用寿命,需要先行脱氧,并且产品气要求较低的氢含量和氧含量;由于在后面纯co中进行催化脱h2和o2,会使得更多的co和o2反应,造成co的浪费,并且由于催化反应脱氢脱氧后的反应产物作为杂质需要再除去,同时由于反应后会产生h2o以及co2,作为杂质为了不影响后面的反应的催化剂需要除去,需要增加相应除杂的步骤和装置除去经过催化反应所产生的杂质。并且由于氧气含量的过高使得变换催化剂剂劣化,经过变换反应器的变换效果越来越差,变换后氢气的纯度越来越低,所产生的净化尾气中co的含量越来越高,造成原料不必要的浪费,并且不利于环保;并且由于氧气含量的过高使得吸附剂劣化,并且随着时间的推移经达不到分离的要求,而且由于反应产生的杂质,co的纯度满足不了预先设定的要求,无法作为合成乙二醇的原料气供下一步合成乙二醇装置使用。除此之外,合成乙二醇的原料气中所需高浓度co气体中需要满足h2≤1000ppm和o2≤1000ppm的浓度需求。所以在第一预处理流程在脱硫后先行一次脱氢脱氧(补入微量氧,调节氢氧比脱氧时同时脱除氢),是在0.1~10mpa和50~1000℃(在一些实施方式中为0.2~1.6mpa和80~250℃)温度条件下采用选择性脱氢脱氧催化剂脱除煤气中的h2和o2。如果脱硫和脱co2步骤分开,使脱氢脱氧处于脱硫后脱co2前,如果含有除ch4步骤,则使脱氢脱氧处于除ch4后,从而一步达成目标,会有保护后续步骤的吸附剂、催化剂,减少co浪费,减少催化脱氢脱氧后所产生杂质的除杂步骤,缩短了流程,减少投资和运行费用,同时由于在前面气体的温度较高能够满足催化脱氢脱氧的反应温度,从而避免了放在后面需要升温而造成的需要换热设备所需的投资和运行费用,同时这种先后顺序也符合反应温度高低的逐级原则,减少了换热设备的投资和运行费用,脱氢脱氧也有利于增大氮气的纯度,得到满足标准的工业氮气。当然如果来料气中含氧量较低(≤0.1%)的话在第一预处理流程也可以不进行脱氢脱氧,将催化脱氢脱氧步骤放到变压吸附分离co和n2后面,这样不会对造成吸附剂、催化剂快速失活、快速缩短其使用寿命,但其会造成co浪费,增加除杂设备和换热设备,增长了流程,增加投资和运行费用。脱氢脱氧的催化剂以含有的钯和/或铂和/或钴和/或锰和/或铜的金属和/或它们的氧化物和/或硫化物为活性组分,以钠、钾、镁、钛、锆、钒、锰、铁、镍、钴、铜、钼、钨、镧、锌、银、钯、钴、或铈的金属和/或它们的氧化物和/或硫化物和/或它们形成的络合物中的一种或几种为助剂。载体为活性炭、氧化铝、氧化硅、氧化镁、氧化钛、硅胶、分子筛、蜂窝陶瓷、独居石、蜂窝金属、金属板、波纹填料、波纹板、纤维(布)材料和结构、编织物、金属发泡体、陶瓷发泡体、石墨基发泡体等。第二部分气体在变换反应之前经第二预处理流程,所述第二预处理流程包括与第一部分气体处于混合态时所经的第一预处理步骤以及单独的预处理步骤,所述第二预处理流程包括除尘、除磷、除砷、脱水、脱氢脱氧、脱硫、脱co2、除ch4、脱重组分中的一步或几步的组合。第二部分气体经第二预处理流程净化后有害杂质含量控制在净化后气体中有害杂质含量控制在硫化物≤1.15ppm,o2≤1%,h2o≤100ppm,cl+≤0.03ppm,砷化物≤0.1ppm,焦油+尘≤1mg/nm3,萘≤1mg/nm3。更进一步有害杂质含量控制在硫化物≤0.1ppm,cl+≤0.01ppm,o2≤0.2%。由于所需生产产品的需要,需要将来料气体分成两部分,其中一部分用来制得符合预设要求的高纯co气体,另一部分用来制得符合预设要求的高纯h2气体。但在流程中分开点的位置可以有多种选择,比如:来料气体直接分开或者在第一预处理流程中分开,其中在第一预处理流程中分开可以使是在第一预处理流程的任一中间环节或者第一预处理流程结束后分开,可选择的,在脱硫后分开、在脱ch4后分开、在脱氢脱氧后分开、在脱除co2后分开等。但是由于有些处理和除杂过程是两部分气体都需要的,如脱硫、脱氧(氧含量比较高时)、脱ch4(需要工业氮气或环保需要时),所以一些过程是可以共有的,可以在一套装置里共同实现的,就导致在流程中分开点的位置的不同,并且导致第二部分气体后续单独的预处理过程略有不同。其分开点的位置是受来料气体组成的不同和产品需求的不同影响。例如,两部分气体都需要脱硫,可在脱硫后分开,如果来料气体中氧含量比较低,制高纯h2气体的分支气体可以直接进行变换反应。如果因需要工业氮气或环保需要时,两部分气体都需要脱ch4,可在脱ch4后分开,如果来料气体中氧含量比较低,制高纯h2气体的第二部分气体可以直接进行变换反应;如果来料气体中氧含量比较高,制高纯h2气体的第二部分气体可以再单独脱氧后进行变换反应,这样的脱氧步骤中只考虑氧含量,尽管在脱氧过程中会消耗一定量的氢,但不用考虑氢含量、不需补入微量氧、不需调节氢氧比,可以减少和氧反应的氢气的量,有利于增加氢气的产量。如果来料气体中氧含量比较高,两部分气体都需要脱氧,可在脱氢脱氧后分开,虽然一步进行脱氢脱氧会略微增加氢气的损耗量,但是会减少装置的数量、减少占地面积、减少投资和运行费用。在脱除co2后分开,可以使得气体中含量很高却不需要的co2分离出去,使得有用气体含量增加,便于后续加压操作、减少加压能耗,但是后续变换反应还会生成co2,还需要再次进行脱除co2。第二部分气体变换后在所述含co2、h2和n2的反应气中分离得到h2时,经过脱co2和n2,其中,脱n2通过变压吸附分离方法,脱co2通过变压吸附分离方法或吸收法。。具体的,变换反应之后经降温分液罐粗脱水和重组分,再经过变温吸附法精脱水和重组分,然后再经过变压吸附方法,脱除气体中含有的co2、氮气以及微量的co,得到满足要求预先设定的要求的高纯h2。如果采用吸收法先脱除co2,变换之后先经降温分液罐粗脱水和重组分,再通过吸收法脱碳,经过吸收法脱除co2的气体再经过变温吸附法精脱水和重组分,然后再经过变压吸附方法,脱除气体中含有的氮气以及微量的co2、co,得到满足要求预先设定的要求的高纯h2(≥99.9%)。高纯h2再经加压(此时气体体积最小,加压成本最低)作为合成醇如乙二醇的原料气。在一个实施方式中,第一预处理流程和第二预处理流程中都包括除co2,且除co2采用吸收法,且第一除杂预处理中除co2所用的吸收液送入第二除杂预处理中除co2作为吸收液。两次脱除co2的方法都采用吸收法,并且两次脱除co2采用同一种吸收剂。图1示出了一种较好的工艺流程,煤气如高炉煤气依次经脱硫、脱甲烷、脱氢脱氧后分成两部分,第一部分气体经脱co2后再通过变压吸附方法分离co和n2,得到co;第二部分气体通过变换反应将气体中的co变换为h2,得到含co2、h2和n2的反应气,再通过变压吸附的方法从反应气中脱除co2和n2,分离得到h2。相应提供的煤气生产h2/co原料气的装置,如图10,包括:第一预处理装置,用于对煤气原料气进行预处理,该第一预处理装置包括依次相连的脱硫装置、除ch4装置脱氢脱氧装置和脱co2装置;其中分流装置的一端与脱氢脱氧装置的出口连接,另一端设有第一部分气体出口和第二部分气体出口,用于将气体分成两股,第一部分气体出口与脱co2装置相连。变压吸附装置,与脱co2装置相连,用于对第一部分气体通过变压吸附方法分离co和n2,得到的co;脱co2装置与变压吸附装置之间的管路最好设有变温吸附装置,用于脱除水和重组分。变压吸附装置的co出口还连接co储罐,co储罐与乙二醇合成装置相连。变换反应器,连接于分流装置的第二部分气体出口,用于对第二部分气体进行变换反应将气体中的co变换为h2,得到含co2、h2和n2的反应气。h2分离装置,与变换反应器相连,该h2分离装置为第二变压吸附装置,直接将co2、n2脱除,得到h2。变换反应器与第二变压吸附装置之间的管路最好也设有一个变温吸附装置。h2分离装置的h2出口还连接氢气储罐,氢气储罐与乙二醇合成装置相连。在上述的方法中,一些分离步骤中需要使用到变压吸附分离操作;本发明的目的是针对来料气体压力比较高或者需要加压到比较高的情况才能实现符合需求的分离效果的常温变压吸附和非常温变压吸附领域中存在的比较大的压力变化过程,在频繁升降压操作过程中,由设备排出的高压气体中所带有较高压能,此过程存在大量的能量损失,所以在这些压力变化比较大的过程中加入能量回收装置,回收能量,把回收的能量用于提供机械能,用于给气体或液体提供压力。这里所指的排出高压气体的设备在工业化的变压吸附设备中有多种,最为常见的是吸附塔,也可以是其它的稳压罐、缓冲罐,这些设备中具有高压气体,降压过程可能是和另一台处于低压状态的吸附塔或稳压罐、缓冲罐进行均压、充压、顺放或逆放等过程,在这些过程中,处于吸附饱和吸附塔中的高压气体经能量回收装置回收能够回收的气体能量再流到处于低压状态的吸附塔或稳压罐、缓冲罐,同时完成了能量的回收和正常的变压吸附的降压过程,这里的能量回收装置当采用膨胀机时,可以将高压气体所具有的压能转化为机械能,这些机械能可以应用于带动压缩机旋转、发动机发电、补充电动机旋转出力等多种用途。在变压吸附流程中,对于接入能量回收装置的降压气体流量、压力和压降都不稳定,具有周期性和比较大的波动性,通常会导致能量回收装置几乎无法正常稳定工作,因此需要对能量回收装置进行相应的改进。本发明的主要设计构思是:通过平抑由高压装置排出的气体的周期性的快速波动来使膨胀机可以正常工作,主要是通过在膨胀机的气体入口和/或气体出口处通过流体缓冲装置平抑气压的波动;另外一个解决思路是:通过抑制膨胀机的转轴在转速上的波动,也可以实现使其平稳运行,可以通过在其转轴上安装转动阻力装置来实现。基于上述构思,有以下的几种实施方式:在需能量回收的气体在进入能量回收装置中的透平膨胀机之前或者离开能量回收装置后加入一定容积的缓冲罐,缓冲罐可以用来平抑被加压的气体的压力和流量的波动,使其基本稳定,可以实现先由膨胀机来回收变压吸附的中气体的能量,转化为轴的机械能。在另一个实施方式中,在能量回收装置中的气体管路上安装有调节阀,通过在压力变化的过程中,根据压力变化频率和大小,相应地对调节阀的开度进行调节,对进入膨胀机的高压气体的压力和流量波动进行抑制。对于需要增大膨胀机的转轴转动阻力的设计,在另一个实施方式中,在膨胀机的转轴上安装一定尺寸和一定质量分布的飞轮来增加轴的转动惯量,飞轮的安装位置可以是在膨胀机的上游侧或者下游侧的转轴上。以上可以看出,当使用了缓冲装置或者阻力装置之后,当膨胀机将气体压能转为机械能的过程中,可以更好地平抑压能的变化波动,使膨胀机可以正常平稳工作,也就适合于将机械能应用于其它的各个需要消耗能量的过程中。为了能更好地利用膨胀机所产生的机械能,可以将机械能带动其它设备转动工作,也可以将机械能转化为电能后再利用。在一个实施方式中,在膨胀机带动电动机进行发电,由于膨胀机的转动具有一定的周期性波动变化,因此将产生的电能并入电网中,电网需要具有较大的电负载容量,利用大的电网对周期性快速变化的电流的容纳能力,可以将具有周期性波动变化的电能平抑以实现利用;电网中的电能可以输送至其它的用电设备,也可以再带动变压吸附装置中的压缩机进而压缩的气体或液体,使电能得到回用。在变压吸附过程中,存在着对气体进行周期性加压的过程。因此,在另外一个实施方式中,膨胀机带动电动机所产生的电能可以通过电动机带动压缩机进行工作,完成对气体或液体的加压操作,以使电能能够回收利用。由于与压缩机相连接的电动机的运行时,过载会对设备妥善率、稳定性、寿命、安全性有不利影响,因此,在一个实施方式中,电动机可以和电容组或者电池组相连接,当电流波动比较大的时,电容组或者电池组可以快速的平抑电流快速变化,能够加强电动机系统对快速变化转轴所需转动能的响应。以上描述的是利用膨胀机产生的机械能转化为电能的实施方式,也可以直接利用膨胀机所产生的机械能。在这种实施方式中,膨胀机、电动机、压缩机或泵组成能量回收装置可以组成同轴驱动系统、也可以为不同轴驱动系统。组成同轴驱动系统就是将膨胀机转化过来的机械能直接补充在压缩机或泵的轴系上,同时不足的部分由电动机提供能量进行补充,例如将电动机连接于较大的电网中,一方面通过电能带动电动机运行,同时电动机的转轴也与膨胀机的转轴连动,实现膨胀机同时将机械能补充在电动机上的效果,这种方式可以直接利用膨胀机获得的机械能,也能通过膨胀机与电动机的共同作用,使机械能的波动被平抑。同轴驱动系统具有结构紧凑,整机效率高、整机设备费用和运行费用都比较低,具有较好的经济效益。对于变压吸附的过程来说,一般会存在着高压装置(例如:较高压力的吸附塔)向低压装置(例如:较低压力的吸附塔)输送高压气体,以使高压塔的压力降低,而低压塔的压力升高,也可以是两个气体缓冲罐之间的压力相互变化或吸附塔与缓冲罐之间的压力相互变化。当采用本发明中的流体缓冲装置和膨胀机作为主体的能量回收装置时,可以实现气体从由高压侧向低压侧流动时,经过膨胀机后出现气体温度下降的现象,这是由于能量回收过程为降压对外输出功的膨胀过程,膨胀机出口的气体的温度会下降,当低温气体进入至另外的需要加压的塔中时,吸附温度会降低,会使得吸附塔的吸附温度低于脱附再生的温度,吸附时的温度低有利于增大单位吸附剂的吸附量,脱附再生时的温度高有利于使得吸附剂的脱附的更彻底,增大了吸附剂的动态吸附量。也可以采用膨胀机出口的气体经换热器对外输出一定温度的冷量供其它装置使用。另外,通过在膨胀机的前后加上流体缓冲装置,还可以有效地防止较快地气体压力周期性快速变动;由于过大并且频繁的冲击荷载会使吸附剂的容易粉化,减少吸附剂的寿命,同时也对吸附塔的安全性、疲劳使用寿命产生不利影响,所以使用了在变压吸附装置中使用了带有控制阀、缓冲罐等设备可以抑制高压气体的快速波动,能够使得吸附剂的使用寿命延长,同时也有利于吸附塔的安全性和疲劳使用寿命。基于上述的能量回收装置的操作,本发明中一个典型的变压吸附过程如下所示:一个比较常见的变压吸附工业过程如下所述:第1步、由上游来料的混合气进行入处于吸附阶段的吸附塔,大部分易吸附组分被吸附塔中吸附剂吸附,大部分不宜易吸附组分穿过吸附塔床层,为吸附阶段。第2步、将第1步得到的处于吸附饱和的吸附塔进行降压,降压过程可能是和另一台处于低压状态的吸附塔或稳压罐、缓冲罐进行均压、顺放或逆放等过程。在这些过程中,处于吸附饱和吸附塔中的高压气体经能量回收装置回收能够回收的能量再流到处于低压状态的吸附塔或稳压罐、缓冲罐。同时完成了能量的回收和正常的变压吸附的降压过程。第3步、可能存在需要将第2步所得的处于吸附塔或稳压罐、缓冲罐等中的降压后的气体进行再次降压或者将降压后的气体经过某些处理(如:置换或再次吸附、带压冲洗、充压等)后再进行再次降压。同样这个过程可能是需要采取和第2步类似的处理方法。这个过程可能是和另一台处于低压状态的吸附塔或稳压罐、缓冲罐进行均压、顺放或逆放等过程。在这些过程中,处于吸附饱和吸附塔中的高压气体经能量回收装置回收能够回收的能量再流到处于低压状态的吸附塔或稳压罐、缓冲罐。同时完成了能量的回收和正常的变压吸附的降压过程。第4步、可能存在是将第2步或第3步的类似过程重复进行直到吸附塔降到足够低的压力。第5步、将第4步中降到低压状态的吸附塔进行在低压状态下的脱附再生过程,在这一过程中可能采取抽真空、吹扫或抽真空加吹扫或低压解吸等方法。第6步、可能存在需要将经过低压解吸的吸附塔由其它的处于第3步的吸附塔或稳压罐、缓冲罐进行均压升压过程,在这个过程中可能承接第2步或第3步中的经过能量回收后降压的高压气体。第7步、可能存在需要将第6步所得的处于吸附塔或稳压罐、缓冲罐等中的升压后的气体进行再次升压或者将升压后的气体经过某些处理(如:置换或再次吸附、带压冲洗、充压等)后再进行再次升压,在这些可能的升压过程中可能承接第2步或第3步中的经过能量回收后降压的高压气体。第8步、可能存在需要将第7步中的经过升压过后的吸附塔用原料气或经过吸附塔吸附过后的不吸附气体来再次升压至接近于吸附步骤的压力。第9步、前8部的过程对于单塔进行循环往复不断的连续运行,对于塔与塔之间相互配合、交替进行循环往复不断的连续运行。其高压吸附、降压能量回收、降压、低压解吸等过程对于单塔进行循环往复不断的连续运行,对于塔与塔之间相互配合、交错进行循环往复不断的连续运行。将变压吸附分离的过程中的周期性快速变化压能回收,转化成常规可利用的机械能供给对气体加压过程,节省了对气体加压所消耗的电能。对比于没有加入能量回收装置的变压吸附系统,其可回收常规变压吸附系统中由于压差引起的能量损耗的50%。另外,吸附过程中经过吸附塔吸附后的不吸附气体可能压力比较高,或为放空气或在需求端不需要这么高的压力的气体也可以把高的压力的气体接入量回收和加压耦合的装置进行能量回收,回收能量后的压力降低的气体再接入需求端或再放空。本发明中,吸附过程中所采用的吸附剂可以为任何类型的起吸附作用的吸附剂,没有特别限制,可以为分子筛、活性炭、碳分子筛、活性氧化铝、碳纤维等,以及他们的混合填装和分层填装。本发明提供了一种效果较好的脱氧催化剂(或称脱氢脱氧催化剂),制备方法包括:(1)将摩尔比为10~20:1的总摩尔量为0.9~1.1mmol的九水硝酸铝和六水硝酸铈共溶于25~30ml去离子水,得到蓝色澄清的硝酸铝-硝酸铈混合液;(2)在步骤(1)所得混合液中加入0.6~0.8mmol的对苯二甲酸溶解,再将市售13x型分子筛加入其中,13x型分子筛与硝酸铝-硝酸铈的摩尔比为1:40~50;在室温溶液混合搅拌20~30min后,以100~150w超声10~12min后,以升温速率为0.5~5℃/min,升温至200~220℃,保温25~30h,然后,以2~5℃/min降温速率冷却到室温,生成沉淀,离心分离,过滤;用体积比1:1~2的乙醇和去离子水混合溶液以及n,n-二甲基甲酰胺各洗涤得到的晶体3次,80℃干燥15h;(3)配制二氧化硅质量含量为10%的硅溶液(溶剂为水),加入凹凸棒土粉末,二氧化硅同凹凸棒土的质量比为2~3:1,并以0.05g/l的量加入上述步骤(3)的晶体、lg/l的量加入十二烷基磺酸钠,再加入硝酸钼和硝酸锌,硝酸钼和硝酸锌同凹凸棒土的质量比均为1:10~20,机械搅拌20~30min;以300~350w的超声波照射溶液100~120min,得悬浮液;(4)将上述的悬浮液与质量分数为20~25%的硫酸溶液按1:1~2的重量比接触反应生成硅凝胶,在20~40℃反应10~12h,反应结束后用水洗涤,固形物在质量浓度为0.1~0.2%的氨水中浸泡10~12h后,在100~120℃下干燥8~10h,得固体粉末;(5)将上述固体粉末在300~330℃条件下焙烧60~70h(去除骨架里的多余物质,得到高比表面积的载体),将其加入质量分数为3~5%的硝酸钯和硝酸铂的水溶液中,硝酸钯和硝酸铂的质量比为3:1,通过等体积浸渍得到混合溶液,经过8~10h后过滤;之后经过400~430℃焙烧10~15h;(6)将步骤(5)所得物质在含氢10%体积的h2/ar混合气气氛下于400~430℃还原8~10h,升温速率为每分钟2~3℃,得粉末材料。(7)称取一定量的上述步骤(6)粉末材料、甲基纤维素和柠檬酸水溶液,置于混捏机中搅拌均匀后,将混合物放置在离心抛丸机内进行成型,成型产物于200~220℃下干燥,即可得到直径约2~4mm的圆形颗粒,即负载型脱氧催化剂成型体。该脱氧剂的思路是:由al和稀土元素(铈)共同制成金属有机骨材料(mil53-al/ce),稀土元素(铈)和钼、锌起稳定结构的作用,同时起抗硫的作用。由于通常制成的金属有机骨材料(mofs)的方法的不成熟,都存在一定的缺陷,之后采取加入市售13x型分子筛来增大吸附量。金属有机骨材料(mil53-al/ce)粉末与二氧化硅、凹凸棒土共同制得粉末,使得三者之间形成不同层次的分布,促进结构分布,有利于负载,兼顾性能以及成本。之后再对粉末负载钯和/或铂,得到脱氧催化剂,钯和/或铂为贵金属材料,此种催化剂兼顾性能以及成本。采用加入二氧化硅和凹凸棒土是为了减少不必要的气体吸附量,避免副反应发生,提高选择性,因为同时金属有机骨材料比较贵,采用加入二氧化硅和凹凸棒土的方法起到减少成本的作用。下面结合具体的实施例进一步阐释本发明,如无特殊说明,实施例中所采用的方法、吸附剂或催化剂等均可采用本领域常规手段。实施例1高炉煤气来料先经过除尘后,再在380℃、0.36mpa下经过铁、锰的氧化物和zno组成的脱硫剂脱硫后,随着温度的降低,再在300℃、0.36mpa下经甲烷催化燃烧反应,除掉其中微量的甲烷后,进一步在温度降低为220℃和压力保持不变依然为0.36mpa的条件下进行催化反应,脱除高炉煤气中微量的氢气和氧气。将所得气体主要分为两部分。第一部分约1/3体积的所得气体进一步在温度降低为32℃和压力保持不变依然为0.36mpa的条件下进入变温吸附装置脱除气体所含的微量的水分和重组分等成分后进入变压吸附脱碳装置(0.36mpa,32℃)脱除二氧化碳,脱除的二氧化碳经处理后达到排放标准后放空。此时气体组分主要含有co和氮气。将此部分气体送入变压吸附co和氮气分离装置(或称变压吸附装置)中进行co和氮气的分离,在吸附压力为0.35mpa,操作温度为32℃的条件下提取出工业级氮气(体积组成≥99.2%),且将其作为产品送往氮气回收系统。变压吸附塔底抽真空脱附出的高纯度的co产品送入压缩机组中增压,至0.35mpa进入中间储气罐后,作为合成乙二醇的原料气供下一步合成乙二醇装置使用。另一部分约2/3体积的所得气体在0.36mpa的压力条件下与饱和水蒸气混合后进入多段绝热变换反应器进行变换反应,采用中间级水激冷移除反应放热,反应温度180~350℃,冷却水被加热后去往废热锅炉。经变换反应后的气体再经气液分离罐降温至低于100℃,使水蒸气液化后气液分离脱除液态水,再降温至32℃后经变温吸附法脱除微量的水分及重组分等成分;然后通入变压吸附提氢装置,其主要还是脱除变换反应生成的二氧化碳和氮气。最后,提纯得到的氢气经增压至3.0mpa后进入中间储气罐后,作为合成乙二醇的原料气供下一步合成乙二醇装置使用。在本实施例的工艺和反应流程下不仅得到了合成乙二醇的原料气,还回收了工业级氮气,而且在高炉煤气的高温工段将含有的少量甲烷进行催化燃烧反应处理,环保指标更有保障。实施例1具体工艺流程详见图2,各步骤过程中的气体组分见表1。表1实施例2转炉煤气来料(0.12mpa,380℃)先经过除尘后,再经催化加氢转化使气体中的硫转化为易脱除的硫化氢(0.12mpa,300℃),将所得气体主要分为两部分。第一部分约1/3体积的所得气体增压至0.4mpa,进一步在温度降低至40℃后进入二氧化碳吸收塔,此二氧化碳吸收塔采用dea吸收法,此二氧化碳吸收塔采用dea溶液为吸收剂在吸收塔内脱除二氧化碳和大部分的微量硫,吸收饱和后的dea溶液再在再生塔中升温释放出二氧化碳和微量硫活化以及其它杂质再生,脱除的二氧化碳经处理后达到标准后供其他装置回收使用。经过脱除二氧化碳后的气体送入变温吸附装置中,在吸附压力为0.2mpa,操作温度为32℃的条件下进行变温吸附分离进而脱除水和其他重组分成分后,再经过活性炭、分子筛和铁、锰、锌等的金属氧化物等组成的精脱硫吸附塔进行精脱硫后,此时气体组分主要含有co和氮气。将此部分气体送入变压吸附co和氮气分离装置中进行co和氮气的分离,在相近的吸附压力和吸附温度条件(0.2mpa,32℃)下,通过变压吸附分离的方法提纯co气体,得到的co气体的纯度≥99%,在变压吸附塔顶分离出的含有大量氮气的气体经过余压回收装置回收所含的压能后,经处理后达到排放标准后放空。变压吸附塔底抽真空脱附出的高纯度的co产品送入压缩机组中增压,至0.35mpa后在温度为140℃的条件下进行催化反应,脱除其中的微量的氢气和氧气后进入中间储气罐后,作为合成乙二醇的原料气供下一步合成乙二醇装置使用。另一部分约2/3体积的所得气体,再在320℃下经过铁、锰的氧化物和zno组成的脱硫剂脱硫后,进一步在温度降低为200℃和增压至0.4mpa的条件下与饱和水蒸气以及增压后的变压吸附co和氮气分离装置中进行co和氮气的分离过程中产生的置换尾气和部分顺放气体进行混合后进入多段绝热变换反应器进行变换反应,采用中间级水激冷移除反应放热,反应温度180~500℃,冷却水被加热后去往废热锅炉。经变换反应后的气体再经气液分离罐降温至低于100℃,使水蒸气液化后气液分离脱除液态水,再降温至32℃后经变温吸附法脱除微量的水分及重组分等成分;然后通入变压吸附提氢装置(0.39mpa,32℃),其主要还是脱除变换反应生成的二氧化碳和氮气以及其它杂质组分。最后,提纯得到的氢气经增压至3.5mpa后进入中间储气罐后,作为合成乙二醇的原料气供下一步合成乙二醇装置使用。此方法通过引入变压吸附co和氮气分离装置中的置换尾气和部分顺放气体等的过程气体即回收和气体中所含的co,又使有用气体得以充分利用,减少了有效气体的浪费;同时由于置换尾气和部分顺放气体等过程气体的引入,降低了气体中co的浓度,使变换深度变低,使得反应放热温升减小,降低了催化剂的最高使用温度,减少变换的条件的苛刻度,增加变换催化剂的使用寿命。在本实施例的工艺和反应流程下制备合成乙二醇的原料气主要考虑用dea吸收法代替实施例1中提到的变压吸附法脱除co2,同时对不需要回收工业级氮气而做了部分净化工艺上的简化和调整,简化了步骤,缩短了流程,节约了成本,同时用余压回收系统对放空的气体回收所含的压能。该方法综合平衡了变换催化剂的寿命,同时联系和回收利用了另一套装置的置换尾气和部分顺放气体等的过程气体,使有用气体得以充分利用,减少了有效气体的浪费。实施例2具体工艺流程详见图3,各步骤过程中的气体组分见表2。表2实施例3高炉煤气来料(350℃,0.2mpa)先经过除尘后,再在350℃、0.2mpa下经过锰的氧化物和zno组成的脱硫剂脱硫后,将所得气体主要分为两部分。第一部分约1/3体积的所得气体随着温度的降低,再在290℃、0.2mpa下经甲烷催化燃烧反应,除掉其中微量的甲烷后,进一步在温度降低为200℃和压力保持不变依然为0.2mpa的条件下进行催化反应,脱除高炉煤气中微量的氢气和氧气。经处理后的气体进入气体压缩机组增压至0.45mpa,温度降低至40℃后进入二氧化碳吸收塔,此二氧化碳吸收塔采用活性mdea吸收法,此二氧化碳吸收塔采用活性mdea溶液为吸收剂在吸收塔内脱除二氧化碳和极其微量硫,经过吸收后的活性mdea溶液出塔经增压去往第二部分的脱碳装置的吸收塔,作为吸收液再次进行吸收脱碳。脱除的二氧化碳经处理后达到标准后供其他装置回收使用。将此部分气体送入变温吸附装置中,在吸附压力为0.35mpa,操作温度为32℃的条件下进行变温吸附分离进而脱除水和其他重组分成分后,此时气体组分主要含有co和氮气。将此部分气体送入变压吸附co和氮气分离装置中进行co和氮气的分离,在吸附压力为0.35mpa,操作温度为32℃的条件下提取出工业级氮气(体积组成≥99.2%),且将其作为产品送往氮气回收系统。变压吸附塔底抽真空脱附出的高纯度的co产品送入压缩机组中增压,至0.35mpa后进入中间储气罐后,作为合成乙二醇的原料气供下一步合成乙二醇装置使用。第二部分约2/3体积的所得气体进一步在温度降低为200℃和压力保持不变依然为0.2mpa的条件下进行催化反应,脱除高炉煤气中微量的氧气后,经增压至0.45mpa与水蒸气混合后进入多段绝热变换反应器进行变换反应,采用中间级水激冷移除反应放热,反应温度180~450℃,冷却水被加热后去往废热锅炉。经变换反应后的气体再经气液分离罐降温至低于100℃,使水蒸气液化后气液分离脱除液态水,再降温至40℃后进入二氧化碳吸收塔,此二氧化碳吸收塔采用活性mdea吸收法,此二氧化碳吸收塔采用活性mdea溶液为吸收剂在吸收塔内脱除二氧化碳,此二氧化碳吸收塔采用活性mdea溶液主要来自于第一部分的脱碳(脱除二氧化碳)装置的吸收塔,作为吸收液再次进行吸收脱碳;吸收塔还有部分吸收液来自经过热再生的贫液和经过减压再生的半贫液。吸收饱和后的活性mdea溶液经过减压再生释放出所含的部分二氧化碳,部分经过减压活化再生的活性mdea溶液作为半贫液去往吸收塔脱除二氧化碳;余下部分的活性mdea溶液在热再生塔中升温再生释放出所含余下的部分二氧化碳后活化再生,最终完全活化再生为贫液;脱除的二氧化碳经处理后达到排放标准后放空。然后经过活性mdea溶液脱碳后的气体再在吸附压力为0.35mpa,操作温度为32℃的条件下通过变温吸附装置脱除气体在经过活性mdea溶液脱碳装置时气体中带出微量的吸收液中所含的微量的水分和重组分,此时气体组分主要含有氢气和氮气;然后通入变压吸附提氢装置(0.35mpa,32℃),其主要还是脱除所含有的氮气。最后,提纯得到的氢气经增压至2.8mpa后进入中间储气罐后,作为合成乙二醇的原料气供下一步合成乙二醇装置使用。在本实施例的工艺和反应流程下制备h2/co原料气主要考虑用加入活化剂的mdea吸收法分两次分别在高、低两种不同的co2的浓度下脱除co2,两次脱除co2的方法都采用吸收法,并且两次脱除co2采用同一种吸收剂。吸收剂在第一次脱除co2的过程中在较低的co2浓度下的吸收塔吸收一定量的co2后,经加压后进入第二次脱除co2的过程中在较高的co2浓度下的吸收塔继续吸收co2后,待吸收完成后,再进入再生塔完成活化再生过程。由于第一次除co2的操作在较低的co2浓度条件下进行吸收液的吸收,吸收液一般未实现饱和吸附,而经过co变换后得到的co2浓度较高,上述的吸收液可以进一步地对co2进行吸收,从而达到饱和,此方法有利于减小吸收液的循环量从而减小再生液的循环量,从而有利于减小再生流程,节约再生能量;具有类似效果的情况,还包括用同一种吸收液先后进入的不少于两个的塔的压力由一定的差距或压力与浓度同时都具有一定的差距;本方法同时还回收工业级氮气,而且在高炉煤气的高温工段将含有的少量甲烷进行催化燃烧反应处理,环保指标更有保障。实施例3具体工艺流程详见图4,各步骤过程中的气体组分见表3。表3对比例1与实施例1的区别是:将脱氢脱氧放在工艺后段,第一部分气体先psa分离co和氮气后得到纯的co再进行催化脱h2和o2。第二部分气体不进行脱氢脱氧。具体流程如下:高炉煤气来料先经过除尘后,再在380℃、0.36mpa下经过铁、锰的氧化物和zno组成的脱硫剂脱硫后,随着温度的降低,再在300℃、0.36mpa下经甲烷催化燃烧反应,除掉其中微量的甲烷后。将所得气体主要分为两部分。第一部分约1/3体积的所得气体进一步在温度降低为32℃和压力保持不变依然为0.36mpa的条件下进入变温吸附装置脱除气体所含的微量的水分和重组分等成分后进入变压吸附脱碳装置脱除二氧化碳,脱除的二氧化碳经处理后达到排放标准后放空。此时气体组分主要含有co和氮气。将此部分气体送入变压吸附co和氮气分离装置中进行co和氮气的分离,在吸附压力为0.35mpa,操作温度为32℃的条件下提取的氮气的体积组成≤99.2%,无法满足工业级氮气的需求,只能将其送往能量回收系统,回收氮气压能后放空。并且co的体积组成≤99%,满足不了预先设定的要求,无法作为合成乙二醇的原料气供下一步合成乙二醇装置使用。并且随着时间的推移,吸附剂开始劣化,经过一个月的时间吸附剂已经达不到分离的要求。变压吸附塔底抽真空脱附出的co产品送入压缩机组中增压,至0.35mpa进入中间储气罐后,然后再升温至140℃后,压力保持不变依然为0.35mpa的条件下进行催化反应,脱除co气体中所含有的微量的氢气和氧气。经过催化脱h2和o2的纯co作为合成乙二醇的原料气供下一步合成乙二醇装置使用,由于在纯co中进行催化脱h2,由于co含量极高要使得脱h2和o2至h2≤100ppm,o2≤1000ppm,由于co的浓度很高会使得更多的co和o2反应,造成co的浪费,同时由于反应后会产生h2o以及co2,作为杂质为了不影响后面的反应的催化剂需要除去,需另增加一套变温吸附净化装置除去经过催化脱h2和o2反应所产生的杂质。另一部分约2/3体积的所得气体在0.36mpa的压力条件下与水蒸气混合后进入多段绝热变换反应器进行变换反应,采用中间级水激冷移除反应放热,反应温度180~350℃,冷却水被加热后去往废热锅炉。经变换反应后的气体再经气液分离罐降温至低于100℃,使水蒸气液化后气液分离脱除液态水,再降温至32℃后经变温吸附法脱除微量的水分及重组分等成分;然后通入变压吸附提氢装置,其主要还是脱除变换反应生成的二氧化碳和氮气。最后,提纯得到的氢气经增压至3.0mpa后进入中间储气罐后,作为合成乙二醇的原料气供下一步合成乙二醇装置使用。并且随着时间的推移,变换催化剂开始劣化,经过6个月的时间经过拟等温变换反应器的变换效果越来越差,采用不同方案变换反应器出口中的co浓度随工作时间见表5,可见采取对比例方案后变换后氢气的纯度随时间越来越低,经过变压吸附脱碳提氢装置,所产生的净化尾气中co的含量越来越高,造成原料不必要的浪费,并且不利于环保。在本实施例的工艺和反应流程下得到了合成乙二醇的原料气的含量满足不了预先设定的要求,并且还无法满足工业级氮气,还能使吸附剂中毒而随着时间的推移,吸附剂开始劣化直至无法使用。由于在纯co中进行催化脱h2和o2,会使得更多的co和o2反应,造成co的浪费,并且由于催化反应脱氢脱氧后的反应产物作为杂质需要再除去,需要增加相应除杂的步骤和装置。并且由于氧气含量的过高使得变换催化剂剂劣化,经过变换反应器的变换效果越来越差,变换后氢气的纯度越来越低,所产生的净化尾气中co的含量越来越高,造成原料不必要的浪费,并且不利于环保。对比例1具体工艺流程详见图5,各步骤过程中的气体组分见表4。表4表5从表5中可以看出,采用先脱氢脱氧再除co2的方法,气体里的co浓度较低,有利于催化氧化脱氢的选择性提高、有利于减少co同氧气的反应,从而减少co浪费,使得反应条件没有那么苛刻,有利于催化剂的选择。同时减少了气体中的氧气的含量,有利于保护co和氮气步骤的吸附剂以及变换反应的催化剂,以及减少脱氢脱氧后再除去作为杂质的反应产物的步骤和装置。实施例4本实施例用于说明两塔变压吸附中的能量回收过程某尾气气体中还含有微量n2、co、co2、ch4、ar等杂质,为达到产品氢气要求需设置氢气分离单元进行分离提纯。由于上游装置的运行压力较高,造成h2的变压吸附分离装置进入的原料气压力较高,同时需要完成分离后的h2需要增压至4.2mpa(g)。原料气条件:组份(干基)coh2co2n2arch4h2s+cosvol,%11.17968.2810.00410.2270.0030.3080.1ppm流量:2000nm3/h(干基)压力:2.2mpa(g)温度:≈32℃总h2o、o2、nh3、ch3oh、氯、磷、砷、氟、hcn:≤0.1ppm经装有h2分离专用吸附剂的变压吸附提纯装置进行分离净化,分离步骤包括:吸附、均压降压、逆向放压、抽真空、均压升压、最终充压。在包括了压力变化的步骤:均压、逆向放压、最终升压中采用了能量回收和加压耦合的装置回收了能量,同时完成了h2的专分离净化。能量回收和加压耦合的装置为螺杆膨胀机、压缩机、电动机组成的系统,以及其辅助作用的电容组、调节阀组、飞轮、多个缓冲罐,还包括变速机构以及控制系统等复杂系统。在被加压的h2在进入能量回收装置中前和离开能量回收装置后加入一定容积的缓冲罐,来平抑被加压的h2的压力和流量的波动,使其基本稳定。本实施例中提供的装置如图6和图7、图8所示,其中,吸附塔1a的排气管连接至膨胀机的一级2,膨胀机的一级2的排气方向再与吸附塔1b相连接,在膨胀机的一级2的进口和出口侧的管路上,分别连接有缓冲罐13、14,膨胀机的一级2的转轴再与电动机4相连接,电动机4再与压缩机3相连接,用于对气体加压,压缩机3的进出口上分别也设置有被压缩气体进口缓冲罐11和被压缩气体出口缓冲罐12,在电动机2上还连接有电容组10。以下结合该装置的操作过程对其运行作进一步地说明:在(0~3min)的时间段里吸附塔1a(以下简称a塔)进行吸附的过程,阀门a5a1打开,原料气通过原料气稳压罐(18)和调节阀e4进入待吸附状态的吸附塔a塔;塔顶未吸附的气体经过产品气稳压罐(19)和调节阀e3作为产品气供其它装置使用。吸附塔1b(以下简称b塔)进行抽真空的过程,阀门b6打开,由往复泵(6)经抽空气缓冲罐(5)对b塔进行抽真空。能量回收装置没有气体通过,没有回收能量供给压缩机(3)进行气体压缩。在(3~4min)的时间段里进行a塔和b塔进行均压的过程,阀门a2b3e2打开,利用a塔中的高压气体给b塔进行升压,首先,在阀门a2b3e2打开的瞬间,管道中压力、膨胀机(3)进出口的压差、流量变化都很大,所以会造成比较大的冲击载荷,过大的冲击载荷会影响设备的平稳、安全的运行、会影响设备的寿命。所以通过调节阀e5e10,来调节膨胀机3进出口的压差、流量,在阀门a2b3e2打开的瞬间,减小调节阀e5e10的开度,对相应的吸附塔进行憋压,来减少冲击荷载对膨胀机的影响。还通过膨胀机进出口管线相连的缓冲罐(13)(14)来进行缓冲,当与缓冲罐相连的管道中压力高于阀门e6e7设定的压力时,阀门e6e7打开,缓冲罐与管线相连通,使气体分流进入缓冲罐,减少进入膨胀机的气体的量减少冲击荷载的影响,为膨胀机调节机构的动作争取所需的时间,使得调节控制机构动作螺杆膨胀机的滑阀,调节通过膨胀机的流量、内压比、内容积比能适于开阀后的膨胀机进出口的外压比和流量。同时作用在膨胀机上的压能带动轴转动,转化为轴的机械能,由于开阀时形成的冲击荷载易使轴转速超过设定的需要转速,轴转速改变不利于同电动机形成合力共同驱动压缩机完成对另一气体的压缩过程,通过在转轴上增加一定尺寸和一定质量分布的飞轮来增加轴的转动惯量,使得在相同转矩下,转轴说获得的加速度减小,有利于转轴的转速的稳定在定的需要转速。膨胀机的转轴与电动机(4)相连接,可以带动电动机转动,但是由于膨胀机所输出的机械能转速会由于变压吸附的频繁变化过程导致周期性变化,因此会导致电动机的运行不稳定,因此,电动机所需的电流需要接入整体电网,利用大的电网对周期性快速变化的电流的容纳能力,应用控制装置来完成电动机平稳的驱动。在冲击荷载作用下,电网对电动机输入的电流的流量可能快速减小,甚至引起电流的输送方向的改变,所以通过电动机和电容组(10)相接,来平抑在冲击荷载作用下引起的电流的流量的快速变化,能够加强电动机系统对快速变化转轴所需转动能的响应能力,减小对电网的冲击。随着运行时间的加长,由于a塔中的气体逐渐流向b塔,a塔压力逐渐降低,b塔压力逐渐升高,两塔之间的压差逐渐减小,膨胀机进出口之间气体的压差逐渐减小,流量也逐渐减小,这一过程逐渐变化的。调大调节阀e5e10的开度,减小阀门处的阻力损失。随着膨胀机进出口处管线压力逐渐变化,气体由流入缓冲罐逐渐变化到流出缓冲罐,当与缓冲罐相连的管道中压力低于阀门e6e7设定的压力时,阀门e6e7关闭,缓冲罐与管线不再连通。由于被压缩的气体需要基本稳定的压力和流量,这意味着压缩的气体所需的轴功率需要基本稳定,所以被压缩的气体在压缩机进出口都接入了缓冲罐来应对可能的压力和流量的波动,随着时间的变化,膨胀机进出口之间气体的压差逐渐减小,流量也逐渐减小,所以膨胀机所输出的轴功率也在逐渐变小,则需要电动机所输出的轴功率逐渐变大,则电网输入的电流需要通过控制系统调节逐渐变大来补全被压缩的气体所需的轴功率。电动机所需的电流需要接入整体电网,利用大的电网对周期性快速变化的电流的容纳能力,应用控制装置来完成电动机平稳的驱动。同时通过调节控制机构调节螺杆膨胀机的滑阀,调节通过膨胀机的流量、内压比、内容积比使得膨胀机的保持较高的效率。由于能量回收过程为降压对外输出功的膨胀过程,膨胀机出口的气体的温度会下降,降温幅度由膨胀机进、出口的压差决定,膨胀机出口的气体经换热器(20)(21)对外输出一定温度的冷量供其它装置使用。膨胀机出口的气体进入b塔,对b塔进行均压升压的过程,经换热回收一定冷量后的气体温度低于膨胀机入口端的气体温度,低温气体的进入使得b塔的温度降低。对b塔来说,在下一步的充压过程中同样存在着类似的低温气体的进入使得b塔的温度降低的过程,会使得b塔在下一步进行吸附的步骤中,b塔的吸附温度会降低,会使得吸附塔的吸附温度低于脱附再生的温度,吸附时的温度低有利于增大单位吸附剂的吸附量,脱附再生时的温度高有利于使得吸附剂的脱附的更彻底增大了吸附剂的动态吸附量。同时由于气体通过膨胀机进行了能量回收,会使得吸附塔的升压或降压过程趋于缓慢,相较于没有采用能量回收的变压吸附装置,减少了均压过程中的气体对吸附塔的冲击荷载。过大并且频繁的冲击荷载会使吸附剂的容易粉化,减少吸附剂的寿命,同时也对吸附塔的安全性、疲劳使用寿命产生不利影响。所以使用了在变压吸附装置中使用了能量回收装置会使得吸附剂的使用寿命延长,同时也有利于吸附塔的安全性和疲劳使用寿命。在(4~5min)的时间段里a塔进行逆放,b塔进行充压过程。阀门a4e13打开,a塔中的高压气体经过能量回收系统回收了压能和冷量后经逆放气缓冲罐(7)和逆放气压缩机(8)后去往其他燃烧装置。和均压过程中能量回收系统的运作情况类似,在开阀的瞬间形成的冲击荷载,由调节阀组e6e8e9、缓冲罐(13)(15)(16)、飞轮、电容组(10)起缓冲作用进行缓解,以及大的电网的接入、膨胀机滑阀的调节也可以对冲击荷载起到一定的缓冲作用。同样和均压过程中能量回收系统的运作情况类似,随着运行时间的加长,a塔中气体的压力逐渐降低,膨胀机进出口之间气体的压差逐渐减小,流量也逐渐减小,所以膨胀机所输出的轴功率也在逐渐变小,则需要电动机所输出的轴功率逐渐变大,则电网输入的电流需要通过控制系统调节逐渐变大来补全被压缩的气体所需的轴功率。电动机所需的电流需要接入整体电网,利用大的电网对周期性快速变化的电流的容纳能力,应用控制装置来完成电动机平稳的驱动,电容组通过电流的输入和输出对电动机平稳的驱动也有贡献。同时通过调节控制机构调节螺杆膨胀机的滑阀,使得膨胀机的流量、内压比、内容积比使能适于开阀后的膨胀机进出口的外压比和流量,使膨胀机保持较高的效率。同样通过膨胀机出口处的换热器对外输出一定温度的冷量供其它装置使用。同样和均压过程中能量回收系统的运作情况类似,因为在压力变化过大的过程中加入了能量回收系统,使得吸附剂的使用寿命延长,同时也有利于吸附塔的安全性和疲劳使用寿命。阀门e1e2b3打开,产品气稳压罐(19)中的高压气体经过能量回收系统回收了压能和冷量后对b塔进行充压,使b塔压力升高到接近吸附步骤的压力。在这一过程中能量回收系统对开阀的冲击载荷的应对方式、电网中输入电流的变化对平稳的驱动、通过换热器对外提供冷量、滑阀对膨胀机流量、内压比、内容积比的调节和a塔的顺放过程相类似。经换热回收一定冷量后的气体温度低于膨胀机入口端的气体温度,低温气体的进入使得b塔的温度降低。在(5~8min)的时间段里b塔进行抽真空的过程,阀门a6打开,由往复泵(6)对a塔进行抽真空。b塔处于吸附状态,原料气通过原料气稳压罐(18)和调节阀e4进入待吸附状态的吸附塔b塔;塔顶未吸附的气体经过产品气稳压罐(19)和调节阀e3作为产品气供其它装置使用。b塔由于在之前的均压升压和充压过程中,接受的经过能量回收后的气体的温度低于膨胀机入口端的气体温度。会使得b塔的吸附温度会降低,在b吸附的步骤中,会使得吸附塔的吸附温度低于抽真空脱附再生的温度,吸附时的温度低有利于增大单位吸附剂的吸附量,脱附再生时的温度高有利于使得吸附剂的脱附的更彻底,增大了吸附剂的动态吸附量。在这段时间中能量回收装置没有气体通过,没有回收能量供给压缩机(3)进行气体压缩。在(8~9min)的时间段里进行b塔和a塔进行均压的过程,阀门b2a3打开,利用b塔中的高压气体给a塔进行升压。其过程和(3~4min)段的均压的过程相类似,a塔与b塔之间相互配合、交替进行循环往复不断的连续运行。在(9~10min)的时间段里a塔进行充压过程,b塔进行逆放过程。阀门e1e2b3,产品气稳压罐(19)中的高压气体经过能量回收系统回收了压能和冷量后对a塔进行充压,使a塔压力升高到接近吸附步骤的压力。阀门b4e13打开,a塔中的高压气体经过能量回收系统回收了压能和冷量后经逆放气缓冲罐(7)和逆放气压缩机(8)后去往其它燃烧装置。其过程和(4~5min)段的里a塔进行逆放,b塔进行充压过程相类似,a塔与b塔之间相互配合、交替进行循环往复不断的连续运行。至此,吸附塔完成了一个完整的吸附-再生循环过程,并为下一个循环过程做好了准备。b塔的操作过程和塔a相同,每个吸附塔交替进行各个步骤的操作,对于单塔进行循环往复不断的连续运行,对于塔与塔之间相互配合、交替进行循环往复不断的连续运行。通过变压吸附将变压吸附分离h2的过程中的周期性快速变化压能回收,转化成常规可利用的机械能供给对h2加压过程和对外输出的冷量,节省了对h2加压所消耗的电能。对比于没有加入能量回收装置的变压吸附系统,其可回收常规变压吸附系统中由于压差引起的能量损耗的46%。表6两塔变压吸附净化h2循环操作步骤时序表实施例5本实施例用于说明三塔变压吸附中的能量回收过程某尾气气体中还含有微量n2、co、co2、ch4、ar等杂质,为达到产品氢气要求需设置氢气分离单元进行分离提纯。由于上游装置的运行压力较高,造成h2的变压吸附分离装置进入的原料气压力较高,同时需要完成分离后的h2需要增压至4.2mpa(g)。原料气条件:组份(干基)coh2co2n2arch4h2s+cosvol,%11.17968.2810.00410.2270.0030.3080.1ppm流量:2000nm3/h(干基)压力:2.2mpa(g)温度:≈32℃总h2o、o2、nh3、ch3oh、氯、磷、砷、氟、hcn:≤0.1ppm经装有h2分离专用吸附剂的变压吸附提纯装置进行分离净化,分离步骤包括:吸附、均压降压、逆向放压、抽真空、均压升压、最终升压。在包括了压力变化的步骤:均压、逆向放压、最终升压中采用了能量回收和加压耦合的装置回收了能量,同时完成了h2的专分离净化。能量回收和加压耦合的装置为透平膨胀机、压缩机、电动压缩机组成的系统,以及其辅助作用的电容组、调节阀组、飞轮、多个缓冲罐,还包括变速箱以及控制系统等复杂系统。在被加压的h2在进入能量回收装置中压缩机的前面和离开能量回收装置后加入一定容积的缓冲罐,来平抑被加压的h2的压力和流量的波动,使其基本稳定。如图9所示。在这一变压吸附和能量回收和加压耦合的装置的各个操作步骤中的能量回收过程有着相似的过程。对于操作过程中操作步骤转换过程中开阀的瞬间管道中压力、调节膨胀机进出口端的压差变化都很大,所以会造成比较大的冲击载荷,过大的冲击载荷会影响设备的平稳、安全的运行、会影响设备的寿命。所以通过调节阀e2e5,来调节膨胀机进出口的压差、流量,在阀门打开的瞬间,减小调节阀e2e5的开度,对相应的吸附塔进行憋压,来减少冲击荷载对膨胀机的影响。还通过膨胀机进出口管线相连的缓冲罐(13)(14)(15)(16)来进行缓冲,当与缓冲罐相连的管道中压力高于阀门e6e7e8e9设定的压力时,阀门e6e7e8e9打开,缓冲罐与管线相连通,使气体分流进入缓冲罐,减少进入膨胀机的气体的量减少冲击荷载的影响,为膨胀机调节机构的动作争取所需的时间,使得调节控制机构动作透平膨胀机的入口导叶片的偏转角度或可调喷嘴的开度,调节通过膨胀机的流量、压差能适于开阀后的膨胀机进出口处的压差和流量。同时作用在膨胀机上的压能带动轴转动,转化为轴的机械能,由于开阀时形成的冲击荷载易带动轴转速加速,轴转速改变不利于同电动机形成合力共同驱动压缩机完成另一气体的压缩过程,通过在转轴上增加一定尺寸和一定质量分布的飞轮来增加轴的转动惯量,使得在相同转矩下,转轴说获得的加速度减小。电动机所需的电流需要接入整体电网,利用大的电网对周期性快速变化的电流的容纳能力,应用控制装置来完成电动机平稳的驱动。在冲击荷载作用下,电网对电动机输入的电流的流量可能快速减小,甚至引起电流的输送方向的改变,所以通过电动机和电容组相接,来平抑在冲击荷载作用下引起的电流的流量的快速变化,能够加强电动机系统对快速变化转轴所需转动能的响应能力,减小对电网的冲击。随着运行时间的加长,由于高压塔中的气体逐渐流向低压塔或稳压罐,高压塔压力逐渐降低,低压塔压力逐渐升高,两塔之间的压差逐渐减小,膨胀机进出口之间气体的压差逐渐减小,流量也逐渐减小,这一过程逐渐变化的。调大调节阀e2e5的开度,减小阀门处的阻力损失。随着膨胀机进出口处管线压力逐渐变化,气体由流入缓冲罐逐渐变化到流出缓冲罐,当与缓冲罐相连的管道中压力低于阀门e6e7e8e9所设定的压力时,阀门e6e7e8e9关闭,缓冲罐与管线不再连通。由于被压缩的气体需要基本稳定的压力和流量,这意味着压缩的气体所需的轴功率需要基本稳定,所以被压缩的气体在压缩机进出口都接入了缓冲罐来应对可能的压力和流量的波动,随着时间的变化,膨胀机进出口之间气体的压差逐渐减小,流量也逐渐减小,所以膨胀机所输出的轴功率也在逐渐变小,则需要电动机所输出的轴功率逐渐变大,则电网输入的电流需要通过控制系统调节逐渐变大来补全被压缩的气体所需的轴功率。电动机所需的电流需要接入整体电网,利用大的电网对周期性快速变化的电流的容纳能力,应用控制装置来完成电动机平稳的驱动。同时通过调节控制机构调节透平膨胀机的入口导叶片的偏转角度或可调喷嘴的开度,调节通过膨胀机的流量、压差使得膨胀机的保持较高的效率。由于能量回收过程为降压对外输出功的膨胀过程,膨胀机出口的气体的温度会下降,降温幅度由膨胀机进出口的压差决定,膨胀机出口的气体经换热器对外输出一定温度的冷量供其它装置使用。膨胀机出口的气体进入低压塔,对低压塔进行升压的过程,经换热回收一定冷量后的气体温度低于膨胀机入口端的气体温度,低温气体的进入使得低压塔的温度降低。对低压塔来说,在接下来步骤中的升压过程同样存在着类似的低温气体的进入使得低压塔的温度降低的过程,会使得低压塔在升压结束后进行吸附的步骤中,低压塔的吸附温度会降低,会使得吸附塔的吸附温度低于脱附再生的温度,吸附时的温度低有利于增大单位吸附剂的吸附量,脱附再生时的温度高有利于使得吸附剂的脱附的更彻底增大了吸附剂的动态吸附量。同时由于气体通过膨胀机进行了能量回收,会使得吸附塔的升压或降压过程趋于缓慢,相较于没有采用能量回收的变压吸附装置,减少了均压过程中的气体对吸附塔的冲击荷载。过大并且频繁的冲击荷载会使吸附剂的容易粉化,减少吸附剂的寿命,同时也对吸附塔的安全性、疲劳使用寿命产生不利影响。所以使用了在变压吸附装置中使用了能量回收装置会使得吸附剂的使用寿命延长,同时也有利于吸附塔的安全性和疲劳使用寿命。简单来说,通过在变压吸附和能量回收和加压耦合的装置中加入一定容积的缓冲罐和调节阀组来平抑管道内气体的压力或流量的波动,先由透平膨胀机来回收变压吸附的中气体的能量,转化为轴的机械能。在能量回收装置中加入一定尺寸和一定质量分布的飞轮来增加轴的转动惯量,来平抑周期性快速变化转轴的转动能。然后再控制系统根据系统需要的总能量,确定由电动压缩机需要的出力,控制电机出力,再由电动压缩机或电动泵提供能量来补充所需的剩余的能量对h2完成增压过程。电动机的和电容组相连接,当电流波动比较大的时,电池组可以快速的平抑电流快速变化,能够加强电动机系统对快速变化转轴所需转动能的响应。电动机所需的电流需要接入整体电网,利用大的电网对周期性快速变化的电流的容纳能力,应用控制装置来完成电动机平稳的驱动。从而将变压吸附分离h2的过程中的周期性快速变化压能回收,转化成常规可利用的机械能供给对h2加压过程,节省了对h2加压所消耗的电能。对比于没有加入能量回收装置的变压吸附系统,其可回收常规变压吸附系统中由于压差引起的能量损耗的46%。而对于变压吸附过程,根据三塔变压吸附净化h2循环操作步骤时序表(表7),每个吸附塔交替进行以上各个步骤的操作,对于单塔进行循环往复不断的连续运行,对于塔与塔之间相互配合、交替进行循环往复不断的连续运行。逆放气和抽空气作为废气通往厂区的废气火炬管网,通过h2吸附分离装置得到纯度≥99.9%的h2为1300nm3/h,其余的co约为0.03%、co2约为0.03%、n2约为0.03%、ar+ch4约为0.01%;逆放气和抽空气700nm3/h,其中co约为31.94%、、co2约为28.59%、n2约为29.22%、、h2约为9.37%、ch4约为0.88%。变压吸附分离h2的过程,以a塔为例说明这个变压吸附流程:(a)吸附(0~2min):在2.2mpa压力下,阀门a4打开原料气进入固定床层进行吸附,吸附前沿未到达床层出口一端以前便停止吸附,使吸附前沿和床层出口之间保留一段新鲜的床层,塔顶所得的h2作为产品气由塔顶的打开的阀门a1排出。吸附压力接近于原料气来料压力。(b)吸附(2~3min):a塔在吸附的同时将a塔塔顶出口与处于均升后的b塔相连,用塔顶得到的部分h2对b塔进行充压步骤,这步需经过能量回收和加压耦合的装置回收了能量,阀门a1a4打开,a塔塔顶阀门a2、b塔塔底阀门b3、e3e6e7阀门打开,当e6所连罐中气体的压力低于1.9mpa时e6关闭,当e7所连罐中气体的压力低于1.4mpa时e7关闭。调节阀组e2、e5是为了调节管路中的压力和气体流量逐渐变大或变小,能够减小使得透平膨胀机(2)运行的波动。e6e7阀门所连缓冲罐和调节阀组e2、e5在阀门刚打开的瞬间能够缓冲通过透平透平膨胀机的气体的流量和压差,能够减小透平膨胀机的瞬时出力。(c)均降(3~4min):将a塔与处于真空状态的c塔相连进行均压步骤,在这步需经过能量回收和加压耦合的装置回收了能量,a塔塔顶阀门a2、c塔塔底阀门c3、e3e6e9阀门打开,当e6所连罐中气体的压力低于1.9mpa时e6关闭,当e9所连罐中气体的压力低于0.4mpa时e7关闭。调节阀组e2、e5是为了调节管路中的压力和气体流量逐渐变大或变小,能够减小使得透平膨胀机运行的波动。e6e9阀门所连缓冲罐和调节阀组e2、e5在阀门刚打开的瞬间能够缓冲通过透平透平膨胀机的气体的流量和压差,能够减小透平膨胀机的瞬时出力。对塔a来说是一段降压过程,对塔c来说是一段升压过程。均压后a塔的压力略高于原始压力的一半(1.1mpa),均压气体的纯度和从塔顶流出的产品气的纯度基本相同。(d)逆放(4~5min):将a塔与处于接近常压状态的逆放气缓冲罐相连进行逆放步骤,逆放回路同时在这步需经过能量回收和加压耦合的装置回收了能量,a塔塔底阀门a3、e1e4e8e9阀门打开,当e8所连罐中气体的压力低于0.9mpa时e8关闭,当e9所连罐中气体的压力低于0.4mpa时e9关闭。调节阀组e2、e5是为了调节管路中的压力和气体流量逐渐变大或变小,能够减小使得透平膨胀机运行的波动。e8e9阀门所连缓冲罐和调节阀组e2、e5在阀门刚打开的瞬间能够缓冲通过透平透平膨胀机的气体的流量和压差,能够减小透平膨胀机的瞬时出力。在均压降压过程结束后,吸附床中的杂质前沿已经达到吸附塔的出口位置。这时,逆着吸附方向将吸附塔压力降至接近常压(0.11mpa)。在此过程中,吸附塔中被吸附的杂质开始从吸附剂上大量解吸下来。逆向放压气经逆放气缓冲罐(7)和逆放气压缩机(8)后去往其它燃烧装置。(e)抽真空(5~6min):逆放步骤结束后,为使吸附剂得到较为彻底地再生,对吸附塔抽空,使吸附剂彻底解吸。打开a塔底部的a5号阀门,用真空泵(6)对床层逆向抽真空,塔内压力至-0.09mpa。(f)均升(6~7min):将处于真空状态的a塔与处于吸附状态结束的b塔相连进行均压步骤。对塔a来说是一段充压过程,对塔b来说是一段降压过程。a塔塔底阀门a3、b塔塔顶阀门b2、e3e6e9阀门打开,这步需经过能量回收和加压耦合的装置回收了能量,其过程类同于(c)均降的过程,只是a塔变成了接收气体的的被均压升压的低压塔。均压后a塔的压力略低于吸附步骤压力的一半(0.9mpa),均压气体的纯度和从b塔塔顶流出的产品气的纯度基本相同。(g)空置(7~8min):a塔塔顶、塔底阀门都关闭,a塔中没有气体进出,a塔处于等待状态。(h)充压(8~9min):将处于均升后的a塔与c塔塔顶出口的相连用部分h2对a塔进行充压步骤,使a塔内部压力升高,接近于吸附压力(2.1mpa)。a塔塔底阀门a3、c塔塔顶阀门c2、e3e6e7阀门打开,这步需经过能量回收和加压耦合的装置回收了能量的过程类同于(b)吸附的过程,只是a塔变成了接收气体的被充压的低压塔。至此,吸附塔完成了一个完整的吸附-再生循环过程,并为下一个循环过程做好了准备。其它三个塔的操作过程和塔a相同,每个吸附塔交替进行以上各个步骤的操作,对于单塔进行循环往复不断的连续运行,对于塔与塔之间相互配合、交替进行循环往复不断的连续运行。其具体环操作步骤和操作时间及时序参见表1,其间各塔各个阀门开启状态的控制和操作参见表7。根据时序表(表7)和阀门开启控制表(表8)可以知道能量回收系统处于连续工作状态,为均压、逆放、充压过程交替出现,交替进行循环往复不断的连续运行,能量回收系统连续不断的运行,回收这3个操作步骤中的能量,使得能量回收系统避免了空载,有利于机器安全稳定的运行,避免了对机器的不利影响和能量的损失。表7三塔变压吸附净化h2循环操作步骤时序表表8各塔阀门开启控制表实施例6一种脱氧催化剂的制备方法如下:(1)将摩尔比为19:1的总摩尔量为0.9mmol的九水硝酸铝和六水硝酸铈共溶于25ml去离子水,得到蓝色澄清的硝酸铝-硝酸铈混合液;(2)在步骤(1)所得混合液中加入0.6mmol的对苯二甲酸(h2bdc)溶解,再将市售13x型分子筛加入其中,13x型分子筛与硝酸铝-硝酸铈的摩尔比为1:50;在室温溶液混合搅拌30min后,以150w超声12min后,以升温速率为0.5~5℃/min,升温至220℃,保温30h,然后,以2℃/min降温速率冷却到室温,生成沉淀,离心分离,过滤;用1:1的乙醇和去离子水混合溶液以及n,n-二甲基甲酰胺各洗涤得到的晶体3次,80℃干燥15h;(3)配制二氧化硅质量含量为10%的硅溶液(溶剂为水),加入凹凸棒土粉末,二氧化硅同凹凸棒土的质量比为2:1,并以0.05g/l的量加入上述步骤(3)的晶体、lg/l的量加入十二烷基磺酸钠,再加入硝酸钼和硝酸锌,硝酸钼和硝酸锌同凹凸棒土的质量比均为1:20,机械搅拌30min;以350w的超声波照射溶液120min,得悬浮液;(4)将上述的悬浮液与质量分数为25%的硫酸溶液按1:1的重量比接触反应生成硅凝胶,在20℃反应10h,反应结束后用水洗涤,固形物在质量浓度为0.1%的氨水中浸泡10h后,在100℃下干燥10h,得固体粉末;(5)将上述固体粉末在330℃条件下焙烧70h(去除骨架里的多余物质,得到高比表面积的载体),将其加入质量分数为3%的硝酸钯和硝酸铂的水溶液中,硝酸钯和硝酸铂的质量比为3:1,通过等体积浸渍得到混合溶液,经过10h后过滤;之后经过430℃焙烧15h;(6)将步骤(5)所得物质在含氢10%体积的h2/ar混合气气氛下于430℃还原10h,升温速率为每分钟2~3℃,得粉末材料;(7)称取一定量的上述步骤(6)粉末材料、甲基纤维素和浓度为5%的柠檬酸水溶液(除水外三者的添加的质量比是10:0.3:0.2),置于混捏机中搅拌均匀后,将混合物放置在离心抛丸机内进行成型,成型产物于200℃下干燥,即可得到直径约2mm的圆形颗粒,即负载型脱氧催化剂成型体。对比例6-1无步骤(1),其他同实施例1。对比例6-2溶液不含硝酸铈和硝酸钼、硝酸锌,其他同实施例1。对比例6-3采用市售506ht型脱氧催化剂。催化剂的性能表征1、脱氧率:采用的气源是实施例1中高炉气经甲烷催化燃烧反应,除掉其中微量的甲烷后的气体,其组成是:n2h2o2co2coch4h2scos组成%54.272.170.7020.9121.850.10.1ppm---实验量取20~40目催化剂100ml装入反应管,连接好系统。对催化剂活化后降温至110℃进行活性评价,以脱氧率或出口氧含量表示脱氧催化剂的活性。空速3000h-1,气体压力0.3mpa,试验时间为480h。脱氧率(%)如下表所示:实施例6对比例6-1对比例6-3脱氧率%99.085.690.32、耐硫性能当硫化物累计至吸附剂重量0.1%的硫时,其中实施例6的脱氧率下降6%,对比例6-2的脱氧率分别下降29%,实施例6的催化剂具有良好的耐硫性能。当前第1页12