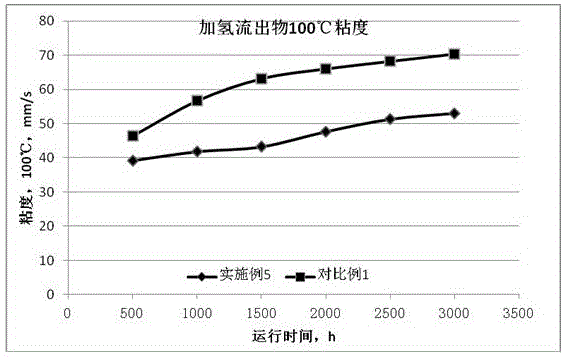
本发明涉及一种烃类加氢处理技术,具体地说是一种加氢脱除渣油中金属杂质的方法。
背景技术:
:渣油加氢技术是在高温、高压和催化剂存在的条件下,使渣油和氢气进行催化反应,脱除渣油分子中硫、氮和金属等有害杂质,同时,渣油中部分较大的分子裂解并加氢,变成分子较小的理想组分。相比于其它渣油加工技术,固定床加氢处理技术的投资和操作费用低,运行安全简单,是迄今为止工业应用最多和技术最成熟的渣油加工技术。固定床渣油加氢装置可为催化裂化装置提供合格进料,同时生成部分汽、柴油等轻质产品。由于渣油原料密度大、粘度大,不利于渣油原料在渣油加氢处理催化剂孔道中扩散,特别是原料中的胶质、沥青质等大分子物质无法进入催化剂微孔也就无法反应转化为小分子物质,这样不但影响了渣油加氢反应中的杂质脱除率及脱残炭率,还影响催化剂使用寿命、操作稳定性。原料粘度越大,系统压降及物流波动就越大,操作稳定性就越差。再者,由于渣油中金属含量高、残炭值高,在转化率较低时就会出现沥青质聚沉现象,导致催化剂积炭而快速失活,缩短装置操作周期。目前,渣油加氢装置原料为了控制适当原料粘度等指标,通过掺炼低密度、低粘度、低残炭的轻质油品(例如焦化蜡油、催化裂化柴油和循环油、瓦斯油等)来调整原料粘度、残炭等加工指标,达到装置加工要求。cn106367113a公开了一种渣油加氢处理方法。该方法使用渣油固定床加氢装置,渣油原料掺入劣质轻质油品,依次通过加氢保护剂、加氢脱金属催化剂、加氢脱硫催化剂、加氢脱氮催化剂和加氢脱残炭催化剂,产物经分馏得到汽油、煤油、柴油馏分以及加氢尾油。所述劣质轻质油品可以为催化裂化柴油及一中油、裂解柴油或碳十重芳烃。该方法可以降低渣油固定床加氢装置进料体系粘度的同时改善体系反应性能和产品品质。cn1488719a公开了一种重烃加氢处理方法,渣油原料依次通过保护剂床层、加氢脱金属催化剂床层、加氢脱硫催化剂床层、加氢脱氮催化剂床层,并且在保护剂床层后及加氢脱硫催化剂床层之前引入脱沥青油和/或焦化蜡油,其引入位置在部分加氢脱金属催化剂床层之后。该方法用于渣油和脱沥青油、焦化蜡油共同加氢处理,为下游催化裂化或加氢裂化等轻质化装置提供优质进料。乙烯焦油是乙烯生产中的副产品,占乙烯产量的15%左右,其由各种烷烃、c8~c15的芳烃、芳烯烃及含n、s、o等元素的杂环化合物等组成,主要是双环以上稠环芳烃的混合物,芳烃含量达90%以上,密度(20℃)1.0g/cm3以上,硫和氮等杂质含量低,基本不含金属杂质(含有微量的铁等金属杂质主要是设备腐蚀原因带入),粘度(100℃)达到200mm/s以上,远远高于常规的渣油加氢处理原料,不适宜用于渣油加氢的降低粘度组份,同时由于基本不含金属杂质,一般也不需要进行加氢脱金属反应。乙烯焦油中350℃以前的馏分约占30%~40%,为轻质油;350℃以后的馏分是重质油,常温下是黑色固体,约占60%~70%。近几年,随着乙烯工业的迅猛发展,乙烯焦油产量也飞速增加,因此,合理利用乙烯焦油使其产生较高的经济效益,对乙烯装置整体效益及乙烯副产资源深加工都有着重大影响,这也是当前乙烯后加工行业亟待解决的重要课题之一。关于乙烯焦油综合利用的研究主要包括以下几个方面:(1)从乙烯焦油中提取萘、甲基萘及其系列物;(2)利用乙烯焦油制备碳石油树脂、纤维沥青、碳纤维等;(3)将乙烯焦油的轻馏分掺炼到其他装置中进一步加工;(4)将乙烯焦油制备为芳烃溶剂油、针状焦、炭黑。由于乙烯焦油成分的复杂性,上述研究未得到工业上大规模应用,目前,乙烯焦油主要用作锅炉或窑炉的燃料油使用,只有很少部分乙烯焦油加工生产炭黑,整体利用率不高,经济价值低,且由于乙烯焦油中含有重烯基芳烃等,燃烧时易产生黑烟及结焦,造成环境污染,导致上述对乙烯焦油的处理工艺存在着工艺条件苛刻、成本高,乙烯焦油转化率低、产品收率低、综合利用率不高、产品附加值低等缺点。cn1970688a公开了一种乙烯焦油综合加工工艺。该工艺先将乙烯焦油切出沸点小于260~280℃的轻馏分,再用加氢精制的方法除去轻馏分中的不饱和烃类,然后再从中提取萘及甲基萘产品,同时副产少量溶剂油产品。该方法只利用了乙烯焦油中所占比例很少的轻馏分,尚有约80%以上的乙烯焦油馏分没有得到有效处理;同时其所提供的加氢精制条件无法处理沸点高于280℃的乙烯焦油馏分。cn102234538a公开了一种乙烯焦油的加氢处理方法。该方法将乙烯焦油分馏成轻馏分和重馏分,切割点为400~450℃,轻馏分依次经过加氢保护催化剂、加氢精制催化剂、加氢脱残炭催化剂和加氢裂化催化剂,所得产物分离得到汽油和柴油馏分;重馏分依次经加氢保护催化剂、加氢脱残炭催化剂和加氢转化催化剂,所得的加氢转化生成油循环去重馏分加氢反应区,剩余部分经分离得到汽油和柴油馏分。该方法单独加工乙烯焦油,由于重馏分的密度大、粘度高,对加氢装置以及配套设备的要求增高,还需另设分馏塔用于切割乙烯焦油,而且重馏分的加工需要大量的加氢转化生成油循环,工艺过程复杂,较难实现工业化。技术实现要素:针对现有技术的不足,本发明提供了一种加氢脱除渣油中金属杂质的方法。本发明发明人意外发现,采用乙烯焦油作为物料粘度调节助剂加到渣油原料中,能够在加氢脱金属反应条件下,通过各组分的协同作用,有效降低了反应条件下的体系粘度,促进了渣油加氢脱金属的进行,并也有利于后续脱硫、脱残炭等反应性能的提升。对于渣油加氢来说,原料的性质和催化剂失活状况是影响渣油加氢的两个重要因素。渣油加氢是扩散控制的反应,而原料油的粘度和反应物分子的大小都对扩散有很大的影响,因此,在本领域中通常是降低原料油的粘度,减小反应物分子的尺寸,进而改善原料油的扩散性能,促进渣油加氢反应的进行。特别是在渣油加氢脱金属反应区,由于比后续加氢脱硫及加氢转化反应区的反应温度相对低、渣油转化率相对低(生成低分子量低粘度的组分少),该阶段物料的粘度较高,粘度对该阶段反应的影响更为突出。催化剂会由于金属沉积或积炭等原因,影响催化剂的孔道结构和表面性能,进而影响催化剂的扩散及反应性能。而乙烯焦油中稠环芳烃含量高,粘度高,若将乙烯焦油作为渣油加氢处理原料,从原料性质和对催化剂失活影响来看,对渣油加氢均不利。发明人意外发现,虽然对于本领域技术人员来说,从乙烯焦油的组成和性质上均不符合常规改善渣油加氢性能的要求,特别是对渣油加氢脱金属反应区的不利影响将会更为突出,但发明人出乎意料地,将乙烯焦油作为物料粘度调节助剂加到渣油原料中,在加氢脱金属反应条件下,反应体系脱金属性能不但没有降低,反而有促进作用,该阶段反应流出物的粘度、金属脱除率等指标有明显的提升,可以判断该反应体系在加氢脱金属反应条件下扩散性能更有利于脱金属反应,各组分的协同作用有效降低了反应条件下的体系粘度,促进了渣油加氢脱金属的进行,并也有利于后续脱硫、脱残炭等反应性能的提升。本发明提供的加氢脱除金属杂质的方法,进料包括渣油原料、氢气和物料粘度调节助剂,其中,物料粘度调节助剂包括乙烯焦油,进料经过加氢脱金属反应区进行加氢处理反应,得到加氢流出物;所述加氢脱金属反应区至少装填有第一加氢脱金属催化剂,所述第一加氢脱金属催化剂包括载体组分和加氢活性金属组分,其中载体组分包括炭和氧化铝。所述第一加氢脱金属催化剂中,以第一加氢脱金属催化剂的重量为基准,所述载体组分的含量为82%~93%。所述载体组分中,炭含量为5wt%~40wt%,进一步优选为10wt%~40wt%,氧化铝含量为60wt%~95wt%,进一步优选为60wt%~90wt%。所述第一加氢脱金属催化剂中,以第vib族金属和/或第viii族金属为加氢活性金属组分,加氢活性金属的选择和用量可以按常规加氢脱金属催化剂进行选用,比如:以第一加氢脱金属催化剂的重量为基准,加氢活性金属以氧化物计的质量含量为7%~18%,其中优选为第vib族金属以氧化物计的质量含量为5%~17%,第viii族金属以氧化物计的质量含量为0.5%~6.0%。所述第一加氢脱金属催化剂的性质如下:比表面积为120~175m2/g,孔容为0.80~1.25ml/g,可几孔直径12~35nm,优选为15~25nm,孔直径小于15nm所占的孔容为总孔容的10%以下,孔直径15-100nm所占的孔容为总孔容的50%~80%,优选为50%~70%,孔直径100-1000nm所占的孔容为总孔容的10%~30%,优选为18%~30%,孔直径大于1000nm所占的孔容为总孔容的3%~15%,优选为5%~15%。所述加氢脱金属反应区中,第一加氢脱金属催化剂优选装填在加氢脱金属反应区的最上游。第一加氢脱金属催化剂的装填体积占加氢脱金属反应区催化剂总体积的10%~70%,优选为15%~40%。所述加氢脱金属反应区中,除了第一加氢脱金属催化剂外,在第一加氢脱金属催化剂的下游装填第二加氢脱金属催化剂,第二加氢脱金属催化剂可以采用常规加氢脱金属催化剂。所述加氢脱金属反应区中,第一加氢脱金属催化剂可以采用一种,也可以采用多种级配装填,第二加氢脱金属催化剂可以采用一种,也可以采用多种级配装填。所述加氢脱金属反应区中,在第一加氢脱金属催化剂中间和/或第二加氢脱金属催化剂中间装填加氢保护剂,即按液相物流方向,依次装填第一加氢脱金属催化剂、第一加氢保护剂、第一加氢脱金属催化剂、第二加氢脱金属催化剂、第二加氢保护剂、第二加氢脱金属催化剂。一般来说,加氢脱金属反应区主要是进行加氢脱金属反应,同时也进行加氢脱硫、加氢脱残炭等反应。所述加氢脱金属反应区中,第二加氢脱金属催化剂中活性金属的含量比第一加氢脱金属催化剂中活性金属含量多,优选多1.0~10.0个百分点,以质量分数计。第二加氢脱金属催化剂的平均孔直径小于第一加氢脱金属催化剂的平均孔直径,优选小2.0~15.0nm。所述加氢脱金属反应区中,第二加氢脱金属催化剂采用多种加氢脱金属催化剂时,一般地,按活性逐渐增加,孔径逐渐减小的常规催化剂级配原则来选择和装填。下游加氢脱金属催化剂中活性金属的含量比上游相邻加氢脱金属催化剂中活性金属含量多,优选多1.0~10.0个百分点,以质量分数计。下游加氢脱金属催化剂的平均孔直径小于上游相邻加氢脱金属催化剂的平均孔直径,优选小0.5~6.0nm。进一步地,所述加氢脱金属反应区中,各种加氢保护剂可以采用相同的加氢保护剂,也可以按常规的级配原则来装填。进一步地,所述加氢脱金属反应区中,加氢保护剂的装填体积占加氢脱金属反应区中催化剂总装填体积的1%~12%,优选为2%~10%。进一步地,第一加氢保护剂的装填体积是第一加氢脱金属催化剂装填体积的1%~16%,优选为2%~15%。进一步地,第一加氢保护剂上游第一加氢脱金属催化剂占第一加氢脱金属催化剂总体积的25%~80%,优选为25%~75%。进一步地,第二加氢保护剂的装填体积是第二加氢脱金属催化剂装填体积的1%~16%,优选为2%~15%。进一步地,第二加氢保护剂上游第二加氢脱金属催化剂占第二加氢脱金属催化剂总体积的25%~80%,优选为25%~75%。所述乙烯焦油的用量占渣油原料质量的0.1%~30%,优选为5%~20%,进一步优选为8%~20%。所述乙烯焦油的性质如下:密度(20℃)为1.000g/cm3以上,一般为1.000~1.200g/cm3,残炭含量为10wt%~30wt%,凝点为30~40℃,100℃粘度为200~500mm/s。所述乙烯焦油中,硫和氮的含量较低,基本不含金属杂质,其中,硫含量为0.05wt%以下,一般为0.03wt%~0.05wt%,氮含量为80μg/g以下,一般为10~80μg/g,ni和v的含量在5μg/g以下,进一步为3μg/g以下。所述的渣油原料为渣油加氢处理装置常用的原料,渣油原料可以包括常压渣油和/或减压渣油。任选地,所述的渣油原料还可以包括用于改善渣油性质、便于加工等方面的常规辅助原料,比如为了控制适当原料粘度等指标而加入低密度、低粘度的轻质油品,所述的轻质油品可以为来自直馏、减压或二次加工而得的轻质油品,可以为蜡油、柴油、瓦斯油等中的至少一种,其中二次加工可以为焦化、催化裂化、减粘等中的至少一种。比如蜡油可以为直馏蜡油、减压蜡油、焦化蜡油中的一种或几种,由催化裂化而得的轻质油品可以为催化裂化柴油、催化裂化回炼油、催化裂化循环油等中的至少一种。所述常规辅助原料的加入量,本领域技术人员可以根据原料性质等来调整。所述渣油原料的性质如下:密度(20℃)为0.955~0.996g/cm3,残炭含量为9wt%~14wt%,金属杂质含量以ni和v计为10~110μg/g,凝点为27~38℃,100℃粘度为60~120mm/s。所述渣油原料中硫、氮含量较高,硫含量一般为0.8wt%~3.5wt%,氮含量一般为1500~5000μg/g。本发明渣油加氢脱金属方法中,加氢脱金属反应区的操作条件如下:反应温度为300~410℃,氢分压为10~20mpa,液时体积空速为0.1~2.0h-1,氢油体积比为500~2000,优选的操作条件如下:反应温度为350~395℃,氢分压为13~18mpa,液时体积空速为0.1~1.5h-1,氢油体积比为500~2000。本发明渣油加氢脱金属方法中,优选采用固定床加氢工艺,其中含加氢脱金属反应区的反应器可以采用上流式进料方式,也可以采用下流式进料方式。本发明渣油加氢脱金属方法中,还可以设置有加氢保护反应区,这是本领域技术人员根据原料的性质能够确定的。在加氢脱金属反应区之前设置加氢保护反应区。加氢保护反应区至少装填一个加氢保护剂床层,优选为2~4个加氢保护剂床层。本发明渣油加氢脱金属方法中,所述的加氢保护剂、第二加氢脱金属催化剂可以选自本领域常规的商业催化剂或采用现有技术的常规方法制备。上述催化剂包括载体和活性金属组分,其中载体可以为氧化铝基载体,可以加入硼、硅、锆、磷、氟、钛等中的至少一种,活性金属组分一般选自第vib族和∕或第viii族金属中的一种或多种,第viii族金属优选为ni和∕或co,第vib族金属优选为mo和∕或w。本发明催化剂可以采用挤出成型物或球形。例如可以采用中国石化抚顺石油化工研究院开发的fzc系列商业催化剂,比如加氢保护剂fzc-100b、fzc-12b、fzc-103d、fzc-13b等,第二加氢脱金属催化剂fzc-28a、fzc-204a等。本发明渣油加氢脱金属方法中,加氢保护剂中加氢活性金属以氧化物计的质量含量为3%~12%,其中第vib族金属以氧化物计的质量含量为2.0%~11.5%,第viii族金属以氧化物计的质量含量为0.2%~5.0%。本发明渣油加氢脱金属方法中,第二加氢脱金属催化剂中加氢活性金属以氧化物计的质量含量为4%~22%,其中第vib族金属以氧化物计的质量含量为3%~21%,第viii族金属以氧化物计的质量含量为0.5%~6.0%。本发明渣油加氢脱金属方法所得的加氢流出物的粘度小于独立以渣油原料为液相进料时所得加氢流出物的粘度。其中粘度是指100℃粘度,单位mm/s。本发明渣油加氢脱金属方法所得的加氢流出物中金属ni和v的脱除率高于独立以渣油原料为液相进料时所得加氢流出物中金属ni和v的脱除率。本发明渣油加氢脱金属方法所得的加氢流出物中硫的脱除率高于独立以渣油原料为液相进料时所得加氢流出物中硫的脱除率。其中,本发明渣油加氢脱金属方法所得的加氢流出物与独立以渣油原料为液相进料时所得加氢流出物,两者仅在进料不同的情况下,分别得到加氢流出物,其中独立以渣油原料为液相进料,是指与本发明渣油加氢脱金属方法相比,仅用等质量的相同渣油原料替换乙烯焦油,其他均与本发明的渣油加氢脱金属方法相同。本发明还提供了一种渣油加氢处理方法,其中,所述的加氢流出物经加氢脱硫反应区和加氢脱氮和/或加氢转化反应区进行加氢反应,得到加氢产物。所述的加氢产物进入分离系统,分离出汽油、柴油和加氢重油,加氢重油优选作为催化裂化装置的进料。所述的加氢脱硫反应区主要进行加氢脱硫反应,一般至少设置一个加氢脱硫催化剂床层,所述的加氢脱氮和/或加氢转化反应区主要进行加氢脱氮和加氢转化反应,一般至少设置一个加氢脱氮和/或加氢转化催化剂床层。本发明渣油加氢处理方法中,所述的加氢脱硫催化剂、加氢脱氮和/或转化催化剂可以选自本领域常规的商业催化剂或采用现有技术的常规方法制备。上述催化剂包括载体和活性金属组分,其中载体可以为氧化铝基载体,可以加入硼、硅、锆、磷、氟、钛等中的至少一种,活性金属组分一般选自第vib族和∕或第viii族金属中的一种或多种,第viii族金属优选为ni和∕或co,第vib族金属优选为mo和∕或w。本发明催化剂可以采用挤出成型物或球形。例如可以采用中国石化抚顺石油化工研究院开发的fzc系列商业催化剂,比如加氢脱硫催化剂fzc-33b,加氢脱氮催化剂fzc-41c等。本发明渣油加氢处理方法中,各催化剂的装填种类和用量,本领域技术人员可以根据实际需要进行调整。与现有技术相比,本发明的有益技术效果如下:(1)本发明方法是发明人意外发现的,采用乙烯焦油作为物料粘度调节助剂加到渣油原料中,能够在加氢脱金属反应条件下,反应体系脱金属性能不但没有降低,反而有促进作用,该阶段反应流出物的粘度、金属脱除率等指标有明显的提升,可以判断该反应体系在加氢脱金属反应条件下扩散性能更有利于脱金属反应,各组分的协同作用有效降低了反应条件下的体系粘度,促进了渣油加氢脱金属的进行,并也有利于后续脱硫、脱残炭等反应性能的提升。(2)本发明采用的第一加氢脱金属催化剂是采用含炭氧化铝为载体,特别是具有适宜的孔结构,将其用于加氢处理渣油时,具有较高的催化活性和良好的稳定性,其加氢脱金属、脱沥青质的效率均较高,活性和稳定性均较好。(3)常规的加氢脱金属反应区中,一般装填加氢脱金属催化剂,其装填原则一般是沿液相物流方向,活性逐步增加,粒度逐渐减小,孔径逐步减小等,但本发明发明人经进一步研究发现,在加氢脱金属催化剂中间的部分替换成加氢保护剂,反而进一步促进加氢脱金属条件下反应体系粘度的降低,以及促进加氢脱金属的进行。(4)本发明方法可以在常规渣油加氢处理装置上进行,易于工业化。附图说明图1为实施例5和对比例1在不同运转时间下所得加氢流出物的粘度对比图;图2为实施例5和对比例1在不同运转时间下所得加氢流出物的金属ni和v的脱除率的对比图;图3为实施例5和对比例1在不同运转时间下所得加氢流出物的硫的脱除率的对比图。具体实施方式下面结合具体实施方式对本发明作进一步的详细说明。本发明中,wt%为质量分数。本发明渣油加氢脱金属方法中,按液相物流方向,所述加氢脱金属反应区装填第一加氢脱金属催化剂和第二加氢脱金属催化剂,优选地,在加氢脱金属催化剂中间装填有加氢保护剂,即按液相物流方向,依次装填第一加氢脱金属催化剂、第一加氢保护剂、第一加氢脱金属催化剂、第二加氢脱金属催化剂、第二加氢保护剂、第二加氢脱金属催化剂,其中第一加氢保护剂和第二加氢保护剂可以装填其一,也可以两者同时装填。进一步地,第二加氢保护剂中活性金属的含量比第一加氢保护剂中活性金属含量多,优选多0.2~7.0个百分点,以质量分数计。进一步地,第一加氢保护剂中加氢活性金属以氧化物计的质量含量为3%~8%,其中第vib族金属以氧化物计的质量含量为2.0%~7.5%,第viii族金属以氧化物计的质量含量为0.2%~4.0%;第二加氢保护剂中加氢活性金属以氧化物计的质量含量为4%~12%,其中第vib族金属以氧化物计的质量含量为3.0%~11.5%,第viii族金属以氧化物计的质量含量为0.5%~5.0%。进一步地,第二加氢保护剂的平均孔直径小于第一加氢保护剂的平均孔直径,优选小0.5~6.0nm。进一步地,第一加氢保护剂的平均孔直径为18~200nm,第二加氢保护剂的平均孔直径为16~180nm,第一加氢保护剂的粒径为3~50mm,第二加氢保护剂的粒径为3~50mm。进一步地,第二加氢脱金属催化剂中活性金属的含量比第一加氢脱金属催化剂中活性金属含量多,优选多1.0~10.0个百分点,以质量分数计。进一步地,第一加氢脱金属催化剂中加氢活性金属以氧化物计的质量含量为7%~18%,其中第vib族金属以氧化物计的质量含量为5%~17%,第viii族金属以氧化物计的质量含量为0.5%~6.0%;第二加氢脱金属催化剂中加氢活性金属以氧化物计的质量含量为8%~22%,其中第vib族金属以氧化物计的质量含量为7%~21%,第viii族金属以氧化物计的质量含量为0.5%~6.0%。进一步地,第二加氢脱金属催化剂的平均孔直径小于第一加氢脱金属催化剂的平均孔直径,优选小0.5~6.0nm。进一步地,第一加氢脱金属催化剂的平均孔直径为10~30nm,第二加氢脱金属催化剂的平均孔直径为8~28nm,第一加氢脱金属催化剂的粒径为0.8~3mm,第二加氢脱金属催化剂的粒径为0.8~3mm。本发明渣油加氢处理方法中,所述的加氢脱硫催化剂和加氢脱氮和/或转化催化剂可以采用常规催化剂,比如加氢脱硫催化剂中加氢活性金属以氧化物计的质量含量为8%~25%,其中第vib族金属以氧化物计的质量含量为5%~24%,第viii族金属以氧化物计的质量含量为1%~8%;加氢脱氮和/或转化催化剂中加氢活性金属以氧化物计的质量含量为8%~30%,其中第vib族金属以氧化物计的质量含量为5%~28%,第viii族金属以氧化物计的质量含量为1%~8%。进一步地,加氢脱硫催化剂的平均孔直径为8~15nm,加氢脱氮和/或转化催化剂的平均孔直径为7~15nm。进一步地,加氢脱硫催化剂的粒径为0.6~2mm,加氢脱氮和/或转化催化剂的粒径为0.6~2mm。本发明加氢脱除渣油中金属杂质的方法中,所述的第一加氢脱金属催化剂的制备方法可以采用常规方法制备,优选采用下述方法制备,具体包括:(1)将木质原料进行干燥,粉碎成木屑;(2)将步骤(1)所得的木屑与拟薄水铝石,选择性地加入加氢活性金属组分,进行混捏,挤出成型;(3)将步骤(2)所得成型物在200~350℃下进行微波预处理,预处理时间为0.5~5.0h,微波功率为1~6kw;然后在惰性保护气体氛围下进行炭化处理,炭化温度为400~600℃,炭化时间0.5~8.0h;(4)将步骤(3)炭化后的物料在500~800℃下进行1~5h高温活化,活化氛围为碱性气体氛围,活化之后选择性地引入加氢活性金属组分,制得加氢处理催化剂;其中,步骤(2)和步骤(4)至少之一引入加氢活性金属。步骤(1)中,木质原料可以为木材、锯木屑、果壳、树皮、竹材中的一种或多种,干燥条件为:在100~150℃下干燥3~8h。所述木屑的粒度为100~300目,优选200~250目。步骤(2)中,木屑和拟薄水铝石以al2o3计的质量比为2~7:3~8,优选3~5:5~7。所述拟薄水铝石的晶粒为40~200μm,优选为100~150μm。步骤(2)在成型过程中,可以根据需要加入常规的成型助剂,比如胶溶剂、助挤剂等,所述胶溶剂包括盐酸、硝酸、醋酸、柠檬酸等中的一种或多种,助挤剂包括田菁粉、水中的一种或两种。步骤(3)预处理温度优选为250~320℃,预处理时间优选为1~3h;所述的惰性保护气体为氮气和/或惰性气体,其中惰性气体为氩气、氦气中的一种或两种混合,炭化温度优选为450~500℃,炭化时间优选为2~8h。步骤(4)高温活化温度优选为600~700℃;活化时间优选为2~4h。所述的碱性气体氛围为含氨的水蒸气,其中含氨的水蒸气中氨的体积分数为5%~20%;含氨的水蒸气中也可以加入惰性气体、二氧化碳和氮气等保护气中一种或几种,所述保护气的体积与含氨的水蒸气的体积之比为10以下,优选为5以下,所述的惰性气体为氩气、氦气中的一种或两种混合。步骤(4)引入活性金属组分时,一般采用浸渍法,可以采用喷浸法、饱和浸渍法、过饱和浸渍法中的任意一种,然后经干燥和焙烧得到加氢处理催化剂;其中干燥和焙烧采用常规的操作条件,所述的干燥条件为:在100~200℃下干燥2~5h,焙烧条件为:300~600℃下焙烧2~5h。所述的焙烧使催化剂中炭含量满足要求即可。本发明在第一加氢脱金属催化剂的制备过程中,采用木屑作为炭化物,与拟薄水铝石进行混捏成型后,先经微波预处理,再经炭化,在碱性气氛下进行适宜的高温活化后得到第一加氢脱金属催化剂。因为木屑中含有大量半纤维素和纤维素,在微波预处理之后再炭化,可以控制半纤维素和纤维素等高分子的分解和聚合炭化程度,第一,有利于形成一定比例的适宜大孔的活性炭,在改善催化剂孔结构的同时提高催化剂的机械强度,第二,还有利于其分解产物与拟薄水铝石作用形成一定量的覆炭氧化铝,并调节氧化铝与活性炭之间的作用关系,同时减弱活性金属与氧化铝之间的作用力,更易于硫化,有利于催化剂活性的提高。在之后的碱性气氛条件下活化,有利于减少载体表面羟基的损失,改善催化剂表面的酸性。此外,本发明中选择大晶粒拟薄水铝石,不但有利于调节催化剂的孔结构,而且还能促进木屑在较低的温度下炭化和活化,同时达到避免活性金属的聚集以及活性金属的活化,使木屑炭化和活性金属分布均达到很好效果,并提高活性金属的有效利用率。由本发明方法制得的催化剂具有微孔、介孔、大孔的孔道,使其孔道结构更有利于处理渣油,促进大分子的反应和扩散,同时又增加容杂质的能力,而且活性金属有效利用率高,更易于硫化,有利于催化剂活性和稳定性的提高。下面结合实施例对本发明作进一步的详细说明,但本发明的保护范围不受实施例的限制。实施例1将锯木屑在140℃下干燥5小时,粉碎成200目的木屑;将木屑与粒径为110μm的拟薄水铝石以al2o3计按照质量比3:7进行混合,并加入5wt%醋酸、3wt%田菁粉和含有活性金属组分钼、镍的溶液,混捏,然后挤出成型;将挤出物在250℃下进行微波预处理1h,微波功率为2kw,然后在惰性气体氛围下进行3h炭化处理,炭化温度为450℃;将炭化后的载体在700℃下进行高温活化,活化氛围含体积分数5%的氨的水蒸气,活化时间3h,制备成本发明第一加氢脱金属催化剂a,催化剂性质见表1。实施例2与实施例1相比较,区别在于锯木屑在110℃下干燥7小时,粉碎成250目的木屑,微波预处理温度为300℃,微波功率为4kw,活化氛围含体积分数15%的氨的水蒸气,活化时间为2h,其它与实施例1相同,制备成本发明第一加氢脱金属催化剂b,催化剂性质见表1。实施例3与实施例1相比较,区别在于拟薄水铝石的晶粒为140μm,木屑与拟薄水铝石以al2o3计的混合质量比4:6,微波预处理时间2h,其它与实施例1相同,制备成本发明第一加氢脱金属催化剂c,催化剂性质见表1。实施例4选择现成的粒度为200目,比表面积为960m2/g的活性炭,采用浓度为25wt%的盐酸进行酸洗,然后用去离子水清洗,再利用30wt%硝酸氧化处理10h。然后与拟薄水铝石(原料同实施例1)以al2o3计按照重量比为3:7进行混合,再加入5wt%醋酸和3wt%的田菁粉以及含有活性金属组分钼、镍的溶液,挤条成型,130℃干燥3h,在氮气氛围下900℃焙烧3h,制得第一加氢脱金属催化剂d,催化剂性质见表1。表1实施例所得第一加氢脱金属催化剂的性质实施例1实施例2实施例3实施例4催化剂编号abcd比表面积,m2/g165168164168孔容,ml/g1.131.161.180.90可几孔直径,nm15151713孔分布,%<15nm768715-100nm65625579100-1000nm22242711>1000nm68103催化剂组成nio,wt%2.82.72.72.7moo3,wt%11.211.311.511.1对比例1本对比例采用一个固定床反应器r1,其中设置有加氢保护反应区和加氢脱金属反应区,各反应区装填的催化剂和级配方案见表1、表3和表4。将渣油原料a预热混合,然后与氢气一起,采用上进料方式进入反应器,在加氢脱金属条件下依次与表4级配的催化剂接触并进行加氢反应,得到加氢流出物,其性质见表6。在不同运转时间下,加氢流出物的粘度、金属ni和v的脱除率以及硫的脱除率分别见图1-3。其中,渣油原料a和乙烯焦油a的性质见表2,催化剂种类和级配见表1、表3和表4,其中加氢保护剂为a系列,第二加氢脱金属催化剂为b系列,均采用氧化铝载体,以mo和ni为加氢活性组分。工艺条件见表5,固定床加氢结果见表6。实施例5本实施例的方法与对比例1基本相同,不同点在于:采用乙烯焦油a替代部分渣油原料a(见表5)以及采用第一加氢脱金属催化剂替代加氢脱金属催化剂b1(见表4)。其中,工艺条件见表5,固定床加氢结果见表6。在不同运转时间下,加氢流出物的粘度、金属ni和v的脱除率以及硫的脱除率分别见图1-3。实施例6本实施例与实施例5基本相同,不同点在于:本实施例的进料采用渣油原料b、乙烯焦油b和重循环油以及不同催化剂级配方式,工艺条件见表5,催化剂级配见表4,固定床加氢结果见表6。实施例7本实施例与实施例5基本相同,不同点在于,本实施例的进料采用渣油原料a和乙烯焦油b以及不同催化剂级配方式,工艺条件见表5,催化剂级配见表4,固定床加氢结果见表6。实施例8本实施例与实施例5基本相同,不同点在于:调节不同催化剂级配方式,催化剂级配见表4,工艺条件见表5,固定床加氢结果见表6。实施例9本实施例与实施例5基本相同,不同点在于:调节乙烯焦油a的用量和工艺条件,催化剂级配见表4,工艺条件见表5,固定床加氢结果见表6。实施例10本实施例与实施例5基本相同,不同点在于:采用加氢保护剂替代部分第一加氢脱金属催化剂和第二加氢脱金属催化剂,催化剂级配见表4,工艺条件见表5,固定床加氢结果见表6。实施例11在实施例5一个反应器r1的基础上,增加一个反应器r2,反应器r2设置加氢脱硫反应区和加氢脱氮反应区,各反应区装填的催化剂见表7。将渣油原料a与乙烯焦油a预热混合,然后与氢气一起,采用上进料方式依次进入串联设置的反应器r1和r2,在加氢处理条件下依次与表7级配的催化剂接触并进行加氢反应,得到加氢产物,所得产物由反应器r2底部排出进入分离系统,分离出少量汽油和柴油馏分,其它馏分(350℃以上馏分)即加氢重油进入催化裂化装置。其中,渣油原料a和乙烯焦油a的性质见表2,催化剂种类和级配见表7,其中加氢保护剂为a系列,第二加氢脱金属催化剂为b系列,加氢脱硫催化剂为c系列,加氢脱氮催化剂为d系列,均采用氧化铝载体,以mo和ni为加氢活性组分。两个固定床反应器的工艺条件见表7,固定床加氢结果见表8。对比例2本对比例的方法与实施例5基本相同,不同点在于:采用含多芳烃油(催化裂化回炼油,性质见表1)的渣油原料a代替含乙烯焦油a的渣油原料a。其中,工艺条件见表5,固定床加氢结果见表6。对比例3本对比例的方法与实施例5基本相同,不同点在于:采用含催化裂化重循环油(性质见表1)的渣油原料a代替含乙烯焦油a的渣油原料a。其中,工艺条件见表5,固定床加氢结果见表6。对比例4本对比例的方法与实施例5基本相同,不同点在于:采用将乙烯焦油a作为原料代替含乙烯焦油a的渣油原料a。其中,工艺条件见表5,固定床加氢结果见表6。对比例5本对比例的方法与实施例10基本相同,不同点在于:在对比例1一个反应器r1的基础上,增加一个反应器r2,进料采用渣油原料a。其中,工艺条件见表8,加氢结果见表9。对比例6本对比例的方法与实施例10基本相同,不同点在于:在对比例2一个反应器r1的基础上,增加一个反应器r2,进料采用含多芳烃油(催化裂化回炼油,性质见表2)的渣油原料a。其中,工艺条件见表8,加氢结果见表9。表2渣油原料、乙烯焦油和轻质油品的性质分析项目渣油原料a渣油原料b乙烯焦油a乙烯焦油b多芳烃油重循环油分析方法硫含量,μg/g3060028400494351190015600sh/t0689-2000氮含量,μg/g30024831271714002100sh/t0704-2001残炭,wt%13.6511.2120.1612.410.230.65gb/t17144-1997重金属含量ni,μg/g22.3219.360.160.261-3.45astmd5708-2005v,μg/g68.4565.422.800.008-5.26astmd5708-2005凝点,℃32253432--gb/t510-1983粘度,100℃,mm/s93.6692.17317.8285.0-8.90gb/t11137密度(20℃),g/cm30.98750.98281.11971.0430.9571.056gb/t13377-1992模拟蒸馏,%astmd7169-2005ibp/10,℃228/455243/472165/238156/224186/228222/36330/50,℃545/586547/605358.6/478.4343/462256/293387/40270/90,℃621/679643/695558.2/676541/658318/359419/44595.3,℃694714750730375470表3催化剂组成和性质催化剂编号a1a2a3a4a5b1b2c1d1金属含量,wt%moo32.02.73.34.75.212.015.216.518.3nio0.50.70.81.01.12.22.54.25.0催化剂性质孔容,ml/g0.920.890.870.850.820.680.640.590.57比表面积,m2/g102109120142155167172210230平均孔直径,nm353026232015131110粒径,mm6.23.32.82.22.01.31.31.21.1表4催化剂级配方案(以体积份计)实施例5实施例6实施例7实施例8实施例9实施例10第一反应器加氢保护反应区加氢保护剂a1777777加氢保护剂a2888888加氢保护剂a3888888加氢保护剂a4888888加氢脱金属反应区第一加氢脱金属催化剂,编号/体积份数a/24b/24c/24d/24a/34a/16第一加氢保护剂a4-----2第一加氢脱金属催化剂,编号/体积份数-----a/6第二加氢脱金属催化剂b2959595958528第二加氢保护剂a5-----3第二加氢脱金属催化剂b2-----64续表4催化剂级配方案(以体积份计)对比例1对比例2对比例3对比例4第一反应器加氢保护反应区加氢保护剂a17777加氢保护剂a28888加氢保护剂a38888加氢保护剂a48888加氢脱金属反应区加氢脱金属催化剂b1/24a/24a/24a/24第二加氢脱金属催化剂b295959595表5各例工艺条件实施例5实施例6实施例7实施例8实施例9实施例10原料渣油原料a+乙烯焦油a渣油原料b+乙烯焦油b+重循环油渣油原料a+乙烯焦油b渣油原料a+乙烯焦油a渣油原料a+乙烯焦油a渣油原料a+乙烯焦油a乙烯焦油与渣油原料的重量比1:101:101.5:101:100.6:101:10重循环油与渣油原料的重量比-0.5:10----反应器(r1)氢分压,mpa15.216.316.815.216.315.2反应温度,℃384379382384386384液时体积空速,h-10.420.400.430.420.470.42氢油体积比600650700600750600续表5对比例1对比例2对比例3对比例4原料渣油原料a渣油原料a+多芳烃油渣油原料a+重循环油乙烯焦油a掺炼油品与渣油原料的重量比-1(多芳烃油):101:10-反应器(r1)氢分压,mpa15.215.215.215.2反应温度,℃384384384384液时体积空速,h-10.420.420.420.42氢油体积比600600600600表6各例反应结果分析项目实施例5实施例6实施例7实施例8实施例9实施例10运转时间,h150015001500150015001500加氢流出物性质硫含量,μg/g109931074611236116631112310652氮含量,μg/g220730852124234723152110残炭,wt%8.136.908.198.248.208.01重金属含量ni,μg/g5.074.514.795.985.474.59v,μg/g15.4414.4914.5215.9415.7614.71凝点,℃161617161715粘度,100℃,mm/s43.2547.8251.2752.8949.841.26密度(20℃),g/cm30.9650.9630.9680.9650.9620.963续表6分析项目对比例1对比例2对比例3对比例4运转时间,h150015001500500加氢流出物性质硫含量,μg/g126781210511732258氮含量,μg/g20782116208714残炭,wt%8.107.838.0114.97重金属含量ni,μg/g6.496.156.19--v,μg/g18.9218.0118.07--凝点,℃18181826粘度,100℃,mm/s63.1263.2860.11181.54密度(20℃),g/cm30.9580.9560.9621.049由表6中实施例5和对比例1的结果对比可知,本发明方法加入的乙烯焦油虽然其残炭含量高于渣油原料,但由加氢流出物的残炭含量推得,本发明方法的脱残炭率要高于对比例1。表7催化剂级配方案(以体积分计)r1-加氢保护反应区r1-加氢脱金属反应区r2实施例11a1:a2:a3:a4=7:8:8:8a:b2=24:95c1:d1=53:134表8各例工艺条件实施例11对比例5对比例6原料渣油原料a+乙烯焦油a渣油原料a渣油原料a+多芳烃油乙烯焦油与渣油原料的重量比1:10--多芳烃油与渣油原料的重量比--1:10反应器(r1)氢分压,mpa15.215.215.2反应温度,℃384384384液时体积空速,h-10.420.420.42氢油体积比600600600反应器(r2)氢分压,mpa14.914.914.9反应温度,℃389389389液时体积空速,h-10.340.340.34氢油体积比600600600表9各例加氢结果分析项目实施例11对比例5对比例6运转时间,h150015001500加氢重油性质硫含量,μg/g386249854804氮含量,μg/g155415821486残炭,wt%5.325.435.27重金属含量ni,μg/g2.983.783.59v,μg/g8.4112.1611.78凝点,℃111312粘度,100℃,mm/s22.9732.8427.98密度(20℃),g/cm30.9420.9350.931为了进一步考察本发明方法对活性、稳定性的影响,对实施例11和对比例5进行催化剂稳定性试验,一反氢分压为15.2mpa,二反氢分压为14.9mpa,一反液时体积空速0.42h-1,二反液时体积空速0.34h-1,一反平均反应温度384℃,二反平均反应温度389℃,一反氢油比体积(v/v)600,二反氢油比体积(v/v)600的工艺条件下,进行加氢反应,反应结果见表10。表10渣油加氢稳定性试验结果固定床反应器1500h2000h2500h3000h加氢重油s,wt%实施例113862408742164393加氢重油s,wt%对比例54985520653455462加氢重油ccr,wt%实施例115.325.756.106.38加氢重油ccr,wt%对比例55.435.626.046.36加氢重油ni+v,µg/g实施例1111.3912.1713.0214.38加氢重油ni+v,µg/g对比例515.9417.1618.4119.68由表10中实施例11和对比例5的结果对比可知,本发明方法加入的乙烯焦油虽然其残炭含量高于渣油原料,但由加氢重油的残炭含量推得,在不同运转时间下,本发明方法的脱残炭率高于对比例5。由表10长时间运转周期的考察可见,采用实施例11的渣油加氢处理方法得到了预料不到的反应效果,经过3000小时稳定运行,加氢重油中硫含量为4393µg/g,残炭小于6.5%,金属小于15µg/g,比采用对比例5现有方法进行反应得到的生成油性质有了明显改善,有利于延长装置的运转周期。当前第1页12