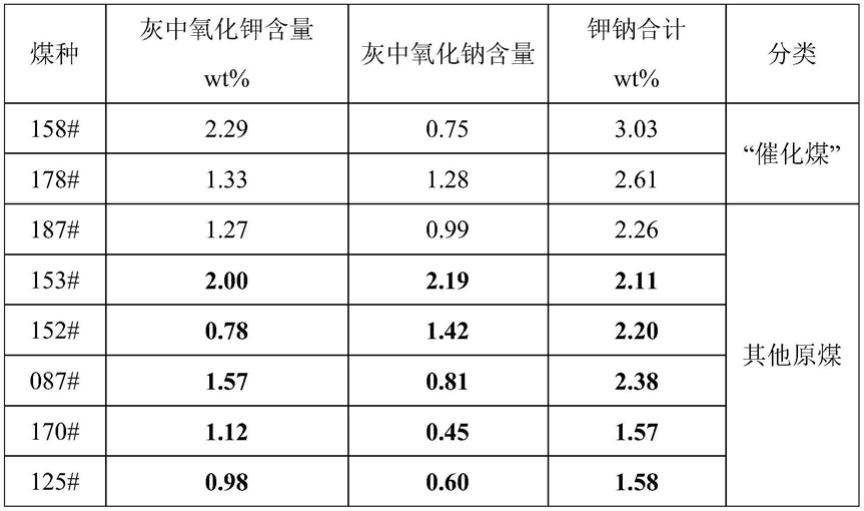
1.本发明涉及一种煤催化气化的方法,特别涉及利用煤中天然钾钠元素进行催化气化的方法,属于煤炭气化技术领域。
背景技术:2.目前,气流床加压气化工艺是大规模工业化煤制粗合成气的主流工艺。气流床加压气化工艺采用原煤和纯氧反应,两者同时加压进入气流床气化炉内发生无催化气化反应,反应温度在1300℃~1700℃之间,生成以一氧化碳和氢气为主要产物的粗合成气。
3.煤气化反应为无催化反应,根据阿累尼乌斯方程和气体化学反应动力学理论,煤气化反应速度与反应温度、反应活化能、反应压力和反应物浓度有关。反应活化能与入炉煤反应活性(挥发分)有关,当入炉煤挥发分在一段时间保持稳定时,可以忽略其对煤气化反应速度的影响。反应压力在气化炉内保持相对稳定,可以忽略其对煤气化反应速度的影响。反应物浓度与气化反应负荷有关,当气化炉保持一定的负荷稳定运行,可以忽略其对煤气化反应速度的影响。因此,气化反应温度对煤气化反应速度有较大影响。
4.实践证明,反应温度每升高10℃,反应速度一般增大到原来速度的2~4倍。在煤气化反应的温度区间1300~1700℃,反应温度下降或升高10℃对碳转化率有明显影响,具体可以体现在渣中碳含量的变化。一般来说气化反应温度上升则渣中碳含量下降。
5.目前气流床煤气化工艺的气化反应温度很高,大约在1300℃~1700℃之间,灰渣中未完全转化为co和co2的残碳质量含量一般在5%~25%,总体碳转化率低于98%。使用煤催化气化工艺可以降低气化反应温度,提高碳转化率,降低能耗。
6.但是较高的气化反应温度对耐火砖、碳化硅耐火材料、水冷壁寿命有不利影响。因此,气流床煤气化行业一直在研究如何利用合适的催化剂降低煤气化反应活化能,进而降低气化反应温度,但又确保碳转化率不下降。目前,煤催化气化生产粗合成气的工艺尚在研究中,无工业应用的报导。
7.大量文献和研究表明,钾钠等碱金属元素对煤气化反应具有催化气化作用。
8.目前煤催化气化技术研发普遍使用外加催化剂,依照一定比例负载在原料煤中,或者使用流化床技术将催化剂与原煤同时加入进行催化反应。这种外加催化剂的方法使用成本高、工艺复杂,催化剂回收或者处理技术难度大或者成本高。
9.中国专利cn110628465a介绍:将煤颗粒、水蒸气以及负载有催化剂的热活性半焦在流化床气化反应器中发生催化气化反应,生成富含甲烷的产品气及固体颗粒,固体颗粒包括活性半焦颗粒、飞灰、残碳颗粒和灰渣。
10.中国专利cn108927189a涉及煤气化技术领域,尤其涉及一种煤催化气化催化剂回收方法、回收系统以及煤催化气化系统,该专利介绍采用激冷水对煤催化气化灰渣进行激冷处理,利用所述煤催化气化灰渣中的余热,通过所述激冷水对所述煤催化气化灰渣进行水洗处理,并向激冷处理后的渣水混合物中加入消解剂,对所述煤催化气化灰渣进行消解处理,将消解处理后的产物进行固液分离,获得催化剂回收液与残渣。
11.中国专利cn109652152a介绍了一种煤催化气化制甲烷的装置及方法,解决了现有技术中存在的碳转化率低、甲烷产率低、能耗高、结构复杂的问题,该发明通过采用上下空间变径的鼓泡湍动床气化炉,包括以下步骤:原煤和催化剂在下层空间与气化剂进行催化气化反应,气化反应产生的合成气在上层空间与部分循环合成气、催化剂混合,进一步强化甲烷化反应,从而产生富含甲烷的合成气的技术方案,而整个系统反应所产生的灰渣及co、h2、ch4均循环返回至气化炉的不同位置,强化系统的整体碳转化率和甲烷产率,可应用于煤制天然气领域。
12.对于煤催化气化工艺,上述技术不管是催化剂负载还是催化剂回收处理,都存在催化剂添加成本高、回收处理难度大的缺点,消耗能源较多,以及产生新的危险废弃物等问题。
技术实现要素:13.为了解决现有技术中煤催化气化工艺生产粗合成气的催化剂添加成本高、催化剂回收处理难度大的缺陷,本发明的目的是在于提供一种利用本身富含有天然钾钠元素生物特定原煤中钾钠元素作为催化活性成分进行催化气化的方法;该方法是将含有较多钾钠元素的特定原煤与其他原煤混合或者单独送入气化炉气化,特定原煤中的钾钠元素起到催化作用,无需额外添加催化剂,煤中有机成分在相对较低的气化温度下发生催化气化反应生成粗合成气,且具有催化作用的钾钠元素与煤中灰分发生造渣反应,以渣的形式从渣系统排出,作为建筑材料使用,无需回收或处理催化剂,以达到在相对较低的气化温度下、提升混配煤碳转化率、降低原煤消耗、保护气化炉的目的。
14.为了实现上述技术目的,本发明提供了一种利用煤中天然钾钠元素进行催化气化的方法,该方法是将富含钾钠的原煤添与普通原料煤混配成混配煤,将混配煤输送至气化炉中在钾钠催化作用下进行气化反应,得到粗合成气,钾钠富集在渣中随渣排出。
15.本发明涉及的普通原料煤为现有技术中气化工艺中常规的煤原料,其钾钠总含量一般低于2.5%,主要在0.5~2%范围内,在该范围内钾钠对煤的催化气化效果并不明显。
16.作为一个优选的方案,所述富含钾钠的原煤中钾钠总含量以其灰分中氧化钾和氧化钠总质量含量为2.5%~10.0%计量。富含钾钠的原煤的灰分中氧化钾和氧化钠总质量含量高于2.5%,其表现出较好的催化气化活性,如低于2.5%时,催化活性较低,会导致碳气化转化率较低。
17.作为一个优选的方案,所述富含钾钠的原煤的灰分组成中硅铝比为1.8~3.8,硅铝比以sio2和al2o3的质量比计量。
18.作为一个优选的方案,所述混配煤中钾钠总含量以其灰分中氧化钾和氧化钠总质量含量2.5~8.0%计量。如果混配煤的灰分中氧化钾和氧化钠总质量含量低于2.5%,会出现碳转化率偏低,后续换热器出现积灰结垢问题,而灰分中氧化钾和氧化钠总质量含量大于8.0%,会导致后续换热器出现积灰堵塞问题。因此,在优选的比例范围内,可以获得较好煤催化气化效果。一般来说,气化过程中,可以仅仅采用富含钾钠的原煤,也可以将富含钾钠的原煤搭配其他普通原煤使用,其他普通原煤的质量比例最好不要高于75%。通过控制混配煤中钾钠总含量能够保证气化反应的碳转化效率高,合成其中的有效成分比例高。
19.作为一个优选的方案,所述混配煤的灰分组成中硅铝比为1.8~2.8,硅铝比以
sio2和al2o3的质量比计量,灰分熔点为1200~1440℃。控制合适的硅铝比有利于混配煤中钾钠催化活性的造渣。
20.作为一个优选的方案,所述气化反应的温度为1400~1700℃,压力为2.5~5.0mpa,混配煤中碳转化率不低于98.0%。
21.作为一个优选的方案,所述粗合成气的co和h2总体积百分比大于80%。
22.本发明技术方案采用的气化炉为加压气流床气化炉。
23.作为一个优选的方案,混配煤中通过添加石灰石来降低灰熔点,降低气化炉反应温度,一般石灰石的添加量为混配煤的0.5~3.5%。
24.本发明技术方案将富含钾钠的原煤与其他普通原煤混配后送入气流床气化炉中进行催化气化,催化煤中的钾钠元素起催化气化作用,反应产生粗合成气,钾钠元素随灰渣排出气化炉用作建筑材料,无需额外催化剂加入,不需要设置催化剂回收及处理流程。
25.相对现有技术,本发明技术方案带来的有益技术效果:
26.1、本发明技术方案利用天然负载在原煤中的钾钠元素作为催化剂,直接将富含钾钠的原煤作为催化剂及原料使用,无需额外添加催化剂,且催化气化反应完成后直接造渣,钾钠富集在渣相中排出,作为建筑材料得到利用,无需设置催化剂回收和处理工艺,简化了工艺步骤。
27.2、本发明技术方案采用的富含钾钠的原煤利用原煤本身作为钾钠载体,钾钠分散性好,能更好地发挥钾钠元素的催化作用,煤催化气化产生的粗合成气含量高,碳转化率提高明显;
28.3、本发明技术方案通过调节富含钾钠的原煤与其他普通原煤的混配比例,改变混配煤灰组成,使混配后的原料煤适应煤气化装置要求,因此,煤气化用煤选择范围更广。
具体实施方式
29.下面结合具体实施例作进一步说明,但本发明并不因此而受到任何限制。
30.实施例1
31.使用xrf荧光光谱法分析下列煤种的灰组成,如187#、158#、153#、152#、087#、170#、125#、178#,见表1;
32.表1单煤灰中钾钠含量
[0033][0034]
上表中158#、178#原煤灰中钾钠含量较高,符合“催化煤”的定义。将表1中2种“催化煤”与1种其他原煤组合,形成187#+158#+178#(1:1:1)三元混配煤配方,根据187#+158#+178#(1:1:1)三元混配煤的煤质分析数据,输入粘温特性模型软件计算需要添加的石灰石比例为1.5%,一起混合后加入到ap粉煤气化炉进行气化反应,进行连续72小时性能测试,测定碳转化率为98.5%,气化反应温度1575℃,气化反应压力4.0mpa g;该三元煤的钾钠含量以及气化生产数据见表2。
[0035]
表2
[0036][0037][0038]
(3)“催化煤”中钾钠元素与其他灰组成发生造渣反应后,从渣系统排出,用于生产
水泥。
[0039]
(4)在“催化煤”的作用下煤碳转化率>98%,气化反应温度为1575℃。
[0040]
实施例2
[0041]
(1)将表1中2种其他原煤组合,形成170#+125#(1:2)二元混配煤配方。
[0042]
(2)根据170#+125#(1:2)二元混配煤的煤质分析数据,输入粘温特性模型软件计算需要添加的石灰石比例为1.5%,一起混合后加入到ap粉煤气化炉进行气化反应,进行连续72小时性能测试,测定碳转化率为95.4%,气化反应温度1636℃,气化反应压力4.0mpa g;该二元煤的钾钠含量以及气化生产数据见表2。
[0043]
(3)由于该配方中缺乏高钾钠的“催化煤”,因此实际运行中煤碳转化率仅95.4%,低于实施例1,气化反应温度为1636℃,高于实施例1约60℃。
[0044]
实施例3
[0045]
(1)将表1中2种其他原煤组合,形成170#+125#(1:1)二元混配煤配方。
[0046]
(2)根据170#+125#(1:1)二元混配煤的煤质分析数据,输入粘温特性模型软件计算需要添加的石灰石比例为2.3%,一起混合后加入到ap粉煤气化炉进行气化反应,进行连续72小时性能测试,测定碳转化率为95.0%,气化反应温度1676℃,气化反应压力4.0mpa(g);该二元煤的钾钠含量为1.58%,混配煤中催化物质钾钠元素含量低,转化率偏低。