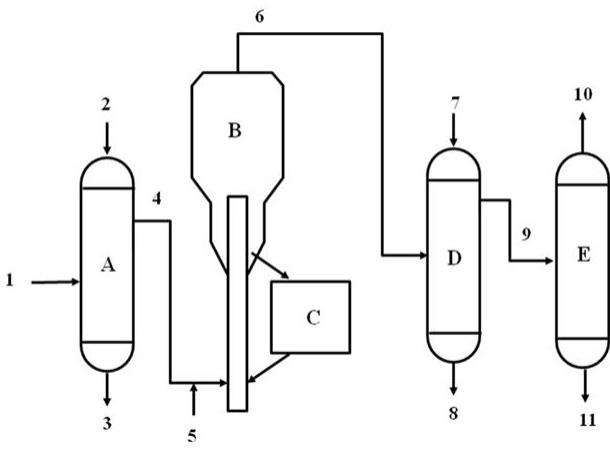
1.本发明涉及一种液化石油气脱硫生产聚丙烯原料的方法,具体地说,本发明涉及一种液化石油气临氢脱硫并抽提出满足聚丙烯原料要求的丙烯的工艺方法。
背景技术:2.液化石油气是目前重要的石油加工产品之一,据统计2018年中国石化的催化裂化液化气处理量高达1430万吨/年。液化石油气一方面可直接作为清洁燃料使用,另一方面在经分离纯化抽提后可用作丙烯、合成汽油抗爆剂的甲基叔丁基醚(mtbe)等生产高附加值产品的化工原料。液化石油气中含有大量含硫化合物,主要是硫化氢和有机硫,硫化氢在硫化物中的占比约为85%左右,其中有机硫中主要以硫醇为主,其它少量的硫化物包括羰基硫(cos)与硫醚等。含硫液化石油气在燃烧过程中会产生有害的 sox排放,并且在作为化工原料使用时易造成下游加工工艺中催化剂的中毒失活,因此液化石油气在进一步加工利用前要进行脱硫处理。
3.目前,对于液化石油气脱硫工业化方法是以merox 脱硫工艺为代表的醇胺抽提硫化氢和碱液抽提硫醇的两步脱硫法。但在脱硫过程中需使用大量碱液,存在碱渣排放问题,给环保带来了巨大的压力,且脱硫的精度并不能满足下游产品的需求。聚丙烯(pp)是以丙烯单体聚合而成的聚合物,是通用塑料中的一个重要品种。由于聚合催化剂对硫特别敏感,以液化石油气为原料抽提丙烯原料时,原料中微量的硫即可导致催化剂中毒失活。因此作为聚丙烯原料的丙烯,在反应前要进行深度脱硫处理,其含硫量要控制在不大于1μg/g,同时羰基硫要小于0.1μg/g。因此,由液化石油气抽提的丙烯原料在进行聚合反应前,还需进一步深度脱除有机硫尤其是羰基硫以满足聚丙烯生产要求。
4.cn104194833a介绍了一种液化气深度脱硫工艺,其特点是液化气先通过胺液抽提脱h2s,并进行水洗脱除携带的胺液;然后在硫化态mo-ni/γ-al2o3催化剂上加氢转化将液化气中的硫化物转化为高沸点的硫化物;加氢产物进入稳定塔,采用低硫碳五以上馏分进行精馏分离,得到超低硫液化气产物,可以作为生产mtbe或烷基化低硫原料。
5.cn107201254a公开了一种包括混合液化石油气脱硫精制方法。该方法将焦化液化石油气通入催化裂化装置的提升管反应器与催化裂化原料一起发生裂化反应,将分馏出的混合液化石油气送入硫化氢抽提单元和硫醇抽提单元脱除硫化氢和硫醇,脱硫后液化石油气产品硫含量不大于10μg/g。 精制后的混合液化石油气能够分馏出满足硫含量要求的丙烯产品,并且可以作为生产低硫的mtbe原料使用。但该方法在脱硫化氢和硫醇的过程中,仍使用常规的碱液抽提的方法,会产生大量的碱渣排放,对环保不利。
6.cn110628476a公开了一种液化气的预处理脱硫方法,该方法在液化气脱硫前采用净化剂进行净化预处理,对炼厂富气中的硫化氢及硫醇等轻质硫化物实施催化氧化,再经过随后的吸收、解吸、精馏工艺,将高沸点的硫化物转移出去,得到硫化氢浓度显著降低、硫醇硫几乎彻底被脱除的粗液化气,粗液化气再经常规的醇胺脱硫和碱液脱硫得到低硫液化气产品。该方法工艺流程长,仍会产生一定量的碱渣。
7.在目前的液化石油气脱硫工艺中,均存在碱渣带来的环保问题以及脱硫深度不够的问题,加氢脱硫技术在催化裂化汽油脱硫方面都取得了良好的成果,但加氢脱硫技术于液化气脱硫方面的工业应用相对较少,因此为弥补目前液化气脱硫过程的不足,完善液化气精制过程,因此急需开发一种深度脱硫且环保的液化石油气脱硫工艺。
技术实现要素:8.针对现有技术中的不足,本发明提供了一种液化石油气脱硫生产聚丙烯原料的方法。该方法在液化石油气深度脱硫的过程中不使用液碱,因此不会产生液碱废渣以及夹带碱液对后续工艺带来的不利影响,且该方法可以达到深度脱硫,经脱硫后液化石油气抽提后的丙烯中总硫和有机硫含量可满足聚丙烯原料的要求。
9.本发明的液化石油气脱硫生产聚丙烯原料的方法,包括如下内容:粗液化石油气经醇胺抽提塔脱除硫化氢后,送入流态化反应器中,在临氢条件下,与加氢脱硫催化剂发生深度脱硫反应,得到的脱硫产物再经醇胺抽提塔脱除硫化氢后,得到精制脱硫液化石油气产品,再经抽提得到硫含量小于1μg/g丙烯产品。
10.本发明方法中,所述的粗液化石油气来自催化裂化装置,其中丙烯含量为20.0v%~40.0v%、丁烯含量为10.0v%~30.0v%,总硫含量为100~10000mg/m3,有机硫含量为50~300mg/m3。所述的粗液化石油气中有机硫化物为硫醇硫、羰基硫或硫醚等。
11.本发明方法中,所述醇胺抽提塔中所用醇胺液为一乙醇胺、二乙醇胺、二异丙醇胺中的一种或多种。
12.本发明方法中,所述醇胺抽提塔操作温度30~40℃,反应压力0.1~0.5mpa。
13.本发明方法中,所述的流态化反应器为提升管反应器或流化床反应器。
14.本发明方法中,流态化反应器中的操作条件如下:反应压力为0.1~2.0mpa、反应温度50~150℃、液化石油气进料体积空速10.0~30.0h-1
,氢气与液化石油气体积比5:1~100:1;优选的操作条件如下:反应压力为0.5~1.0mpa、反应温度60~100℃、液化石油气进料体积空速15.0~25.0h-1
,氢气与液化石油气体积比5:1~20:1。
15.本发明方法中,所述的脱硫产物中有机硫化物含量≯0.5μg/g;单烯饱和率≯1.0%。
16.本发明方法中,所述的加氢脱硫催化剂的再生过程:待再生的加氢脱硫催化剂从反应器下部排出,经气提后输送到再生器中,在空气气氛下烧炭再生,所得的再生催化剂返回流化床反应器循环使用。所述的再生器中进行烧炭再生的条件如下:压力为0.5mpa~1.5mpa,气剂体积比100:1~500:1,在400℃~550℃下恒温0.5~2.0小时。
17.本发明中所述加氢脱硫催化剂包括载体和活性金属组分;所述的载体为氧化锌和氧化铝复合载体,以载体质量为基准,氧化锌为10.0wt%~50.0wt%,优选为20.0wt%~40.0wt%;所述的活性金属组分为第viii族金属,优选ni;以催化剂的重量为基准,活性金属组分以氧化物计的含量为1.0wt%~10.0wt%,优选为3.0wt%~10.0wt%。
18.本发明的加氢脱硫催化剂的制备方法,包括如下内容:a)将氧化锌、拟薄水铝石及成型助剂均匀混合后,经混捏、挤条、干燥、焙烧后,得到条形载体a;b)将条形载体a在行星式球磨机中进行球磨、过筛,得到物料b;
c)将步骤b)得到的物料b在含活性金属组分的溶液中混合打浆,得到固含量为10wt%~60wt%的浆液c;d)将步骤c)得到的浆液c进行喷雾干燥,再经焙烧,制备出加氢脱硫催化剂。
19.本发明方法中,步骤a)所述的成型助剂,包括胶溶剂、助挤剂中的一种或多种。所述的胶溶剂为盐酸、硝酸、硫酸、乙酸、草酸等中的一种或几种,所述的助挤剂是指有利于挤压成型的物质,如田菁粉、炭黑、石墨粉、柠檬酸等中的一种或几种,成型助剂的用量为步骤a)总物料干基的1.0wt%~10.0wt%。
20.本发明方法中,步骤a)所述的干燥条件为100~150℃下干燥2~10小时,焙烧为400~600℃下焙烧3~10小时。
21.本发明方法中,步骤b)所述的球磨时间一般为30~60min,过筛的目数为150~250目。
22.本发明方法中,步骤c)中优选加入分散剂,所述的分散剂为中聚乙烯醇、聚乙烯吡咯烷酮、聚乙二醇中的一种或几种,优选聚乙烯醇,分散剂的用量为总物料干基的1.0wt%~10.0wt%。在搅拌条件下加入分散剂,升温至45~80℃恒温30~90min后,冷却至室温,得到浆液。
23.步骤d)所述喷雾干燥的喷雾压力4~10mpa,入口温度优选范围为150~380℃,出口温度优选范围为100~230℃,焙烧为400~600℃下焙烧3~10小时。
24.本发明方法制备的加氢脱硫催化剂的颗粒尺寸60~100μm。
25.上述方法通过挤条、干燥、焙烧的方式将载体组分结合使载体获得一定的载体孔道、较高的机械强度和抗磨性能;其次对载体进行球磨、过筛得到若干保留原来孔道和比表面性质的微米级反应单元颗粒,相当于多个微反应单元前体;再次通过将多个微米级反应单元颗粒浸渍于含分散剂的活性金属溶液中,使活性金属在微米级反应单元颗粒上充分分散,并通过喷雾成型,获得粒径均匀的高脱硫活性和低烯烃加氢饱和活性的催化剂,可在流态化反应器中实现长周期运转。
26.本发明方法中,所述的精制脱硫液化石油气产品中总硫含量小于1μg/g,有机硫含量小于0.5μg/g。
27.与现有技术相比,本发明具有以下优点:1、本发明方法中,液化石油气进流态化反应前,经醇胺吸收所含的硫化氢,有效的降低了液化石油气在临氢脱硫反应前的总硫含量,减少了流态化反应器中硫化氢与有机硫化物在催化剂上发生临氢脱硫的竞争反应,降低了反应中的硫化氢分压,更有利于硫醇、羰基硫、硫醚类有机硫化物在本发明的催化剂上的众多微米级反应单元颗粒上发生深度脱硫反应,实现低温、高空速下有机硫化物深度脱除。
28.2、本发明方法的在整个脱硫工艺流程中,不使用碱液,不使用二次碱吸收,不产生碱渣,工艺过程对环境友好。
附图说明
29.图1是本发明方法的流程示意图,其中:a-醇胺抽提塔,b-流态化反应器,c-催化剂再生系统,d-醇胺抽提塔,e-丙烯抽提塔,1-液化石油气,2-贫胺液i,3-富胺液i,4-脱硫化氢液化石油气,5-氢气,6-加氢脱硫产
物,7-贫胺液ii,8-富胺液ii,9-精制液化石油气产品,10-丙烯,11-液化石油气抽余产物。
具体实施方式
30.下面结合附图和实施例进一步本发明方法过程及效果。物流及各单元操作沿箭头方向按顺序进行。
31.下面结合图1对本发明方法进行详细说明。
32.根据图1中的流程示意图:液化石油气1进入醇胺抽提脱塔a除硫化氢,贫胺液i 2从醇胺抽提塔a塔顶进入,与液化石油气1逆流接触后得到富胺液i 3从胺液吸收塔底流出,得到脱硫化氢液化石油气4;脱硫化氢液化石油气4与氢气5从底部进入流态化反应器b中,在一定条件下进行加氢脱硫反应;待再生催化剂进入催化剂再生系统c中,经空气活化再生后返回流态化反应器b中循环使用;加氢脱硫产物6进入醇胺抽提脱塔d进一步脱去反应中产生的硫化氢,贫胺液ii 7从醇胺抽提塔d塔顶进入,与加氢脱硫产物6逆流接触后得到富胺液ii 8从胺液吸收塔底流出;精制液化石油气产品9经丙烯抽提塔e,分别得到丙烯10和液化石油气抽余产物11。
33.特别是,流态化反应器主要发生的硫醇、硫醚、二硫醚和羰基硫等在催化剂加氢脱硫,如下:特别是,催化剂再生系统主要发生的烧碳、烧硫反应如下:下面通过实施例进一步说明本发明的方案和效果,但并不因此限制本发明。
34.实施例1本实施例制备加氢脱硫催化剂s-1,该催化剂含8.0wt%nio,载体由40.0wt%zno-60.0wt%al2o3构成。
35.s-1催化剂的制备方法如下:40.0g zno、83.3g拟薄水铝石(al2o3干基含量为72wt%)、3g田菁粉研钵混合均匀后,加入100g/l硝酸溶液25ml,混合并碾压混合成可塑粉体。用挤条机将可塑粉体挤出直径为1.5mm的圆柱条,在120℃下干燥5小时,500℃下焙烧5小时,制备出条型载体;将条形载体放入到行星式球磨机中球磨30min,将载体过150~250目筛;取30g过150~250目筛粉体,加入到100ml含硝酸镍溶液中混合打浆,将总物料干基2.0wt%聚乙烯醇加入到混合浆液中,升温
至60℃恒温60min,冷却至室温后,将所得浆液进行喷雾干燥,喷雾干燥压力为6.0mpa,入口温度220℃,出口温度约为120℃,再经450℃焙烧4h得到加氢脱硫催化剂s-1。s-1催化剂的物化性质见表1。
36.实施例2本实施例制备加氢脱硫催化剂s-2,该催化剂含10.0wt%nio,载体由30.0wt%zno-70.0wt%al2o3构成,s-2催化剂的制备方法同实施例1,s-2催化剂的物化性质见表1。
37.实施例3本实施例制备加氢脱硫催化剂s-3,该催化剂含8.0wt%nio,载体由10.0wt%zno-90.0wt%al2o3构成,s-3催化剂的制备方法同实施例1,s-3催化剂的物化性质见表1。
38.实施例4本实施例制备加氢脱硫催化剂s-4,该催化剂含5.0wt%nio,载体由25.0wt%zno-75.0wt%al2o3构成。
39.称取25.0g zno、104.2g拟薄水铝石(al2o3干基含量为72wt%),并研磨混合均匀,加入25ml浓度为100g/l的稀硝酸溶液,再加入250ml去离子水配制成浆液。将上述浆液进行喷雾干燥,喷雾干燥压力为6.0mpa,入口温度220℃,出口温度约为120℃,再经450℃焙烧4h,得到微球载体。
40.称取上述微球载体30g放入喷浸罐中,开动旋转泵。在30分钟内将硝酸镍溶液喷淋到催化剂载体中。室温下晾干后,在120℃下干燥5小时,500℃下焙烧5小时,得到加氢脱硫催化剂s-4。s-4催化剂的物化性质见表1。
41.对比例1本实施例制备加氢脱硫催化剂d-1,该催化剂含5.0 wt%nio
ꢀ‑
95.0 wt%al2o3构成。
42.称取138.9g拟薄水铝石(al2o3干基含量为72wt%),加入25ml浓度为100g/l的稀硝酸溶液,再加入250ml去离子水配制成浆液。将上述浆液进行喷雾干燥,喷雾干燥压力为6.0mpa,入口温度220℃,出口温度约为120℃,再经450℃焙烧4h,得到微球载体。
43.称取上述微球载体30g放入喷浸罐中,开动旋转泵。在30分钟内将硝酸镍溶液喷淋到催化剂载体中。室温下晾干后,在120℃下干燥5小时,500℃下焙烧5小时,得到加氢脱硫催化剂d-1。d-1催化剂的物化性质见表1。
44.实施例5本实施例为利用催化裂化液化石油气生产丙烯工艺方法,具体步骤如下:(1)催化裂化液化石油气原料经醇胺抽提塔脱除硫化氢,采用二乙醇胺为吸收溶剂,二乙醇胺:反应产物体积比为4:1,抽提塔操作温度40℃,反应压力0.5mpa。
45.(2)将s-1催化剂40ml装入小型连续流化床反应器内,在反应前对s-1催化剂用氢气进行还原,在反应压力1.0 mpa、温度350℃、氢剂体积比50:1下的条件下还原2h;通入脱硫化氢的液化石油气在流化床内进行加氢脱硫反应,反应工艺条件:反应压力为1.0mpa,反应温度为100℃,液时体积空速为20.0h-1
,氢剂体积比为10:1;将液化石油气加氢脱硫产物再经醇胺抽提塔脱除反应中产生硫化氢后,得到的精制液化石油气产品的性质如表2所示。
46.(3)再经抽提得到丙烯产品,丙烯中总硫含量为0.4
µ
g/g,有机硫含量﹤0.1
µ
g/g,可满足聚丙烯原料对硫含量的要求。
47.实施例6
本实施例与实施例5的不同之处在于使用加氢脱硫催化剂s-2,得到的精制液化石油气产品的性质如表2所示,再经抽提得到丙烯产品,丙烯中总硫含量为0.3
µ
g/g,有机硫含量﹤0.1
µ
g/g,可满足聚丙烯原料对硫含量的要求。
48.实施例7本实施例与实施例5的不同之处在于使用加氢脱硫催化剂s-3,得到的精制液化石油气产品的性质如表2所示,再经抽提得到丙烯产品,丙烯中总硫含量为0.6
µ
g/g,有机硫含量﹤0.1
µ
g/g,可满足聚丙烯原料对硫含量的要求。
49.实施例8本实施例与实施例5的不同之处在于使用加氢脱硫催化剂s-4,得到的精制液化石油气产品的性质如表2所示,再经抽提得到丙烯产品,丙烯中总硫含量为0.8
µ
g/g,有机硫含量﹤0.1
µ
g/g,可满足聚丙烯原料对硫含量的要求。
50.对比例2本对比例与实施例5的不同之处在于使用加氢脱硫催化剂d-1,得到的精制液化石油气产品的性质如表2所示,再经抽提得到丙烯产品,丙烯中总硫含量为1.6
µ
g/g,有机硫含量1.0
µ
g/g,不能满足聚丙烯原料对硫含量的要求。
51.实施例9本实施例与实施例5的不同之处在于s-1催化剂在流化床中反应条件不同,具体反应条件:反应压力为1.0mpa,反应温度为100℃,液时体积空速为20.0h-1
,氢剂体积比为10:1;得到的精制液化石油气产品的性质如表2所示,再经抽提得到丙烯产品,丙烯中总硫含量为0.5
µ
g/g,有机硫含量﹤0.1
µ
g/g,可满足聚丙烯原料对硫含量的要求。
52.实施例10本实施例与实施例5的不同之处在于s-1催化剂在流化床中反应条件不同,具体反应条件:反应压力为1.0mpa,反应温度为100℃,液时体积空速为10.0h-1
,氢剂体积比为10:1;得到的精制液化石油气产品的性质如表2所示,再经抽提得到丙烯产品,丙烯中总硫含量为0.5
µ
g/g,有机硫含量﹤0.1
µ
g/g,可满足聚丙烯原料对硫含量的要求。
53.实施例11本实施例与实施例5的不同之处在于s-1催化剂在流化床中反应条件不同,具体反应条件:反应压力为1.0mpa,反应温度为80℃,液时体积空速为25.0h-1
,氢剂体积比为10:1;失活催化剂的烧炭活化的条件如下:压力为1.0mpa,气剂体积比500:1,在500℃下恒温1h,活化气为空气,活化后的催化剂用氢气还原再生,再生后返回反应器内循环使用。运转500h后,得到的精制液化石油气产品的性质如表2所示,再经抽提得到丙烯产品,丙烯中总硫含量为0.5
µ
g/g,有机硫含量﹤0.1
µ
g/g,可满足聚丙烯原料对硫含量的要求。
54.表1 催化剂性质
项目实施例1实施例2实施例3实施例4对比例1催化剂编号s-1催化剂s-2催化剂s-3催化剂s-4催化剂d-1催化剂形状微球微球微球微球微球直径,
µ
m60.0~100.060.0~100.060.0~100.010.0~60.010.0~60.0孔容,ml
·
g-1
0.510.500.490.500.49比表面积,m2·
g-1
241238239230232
堆积密度,g
·
cm-3
0.920.950.910.880.86
表2 液化石油气原料和精制液化石油气产品性质 总硫含量,
µ
g/g有机硫含量,
µ
g/g丙烯,v%丁烯,v%原料液化气204518435.123.0实施例50.80.335.022.9实施例60.70.334.822.8实施例71.50.534.822.7实施例82.00.534.722.7实施例90.90.434.822.9实施例100.70.234.222.5实施例110.90.434.922.9对比例25.02.734.121.9