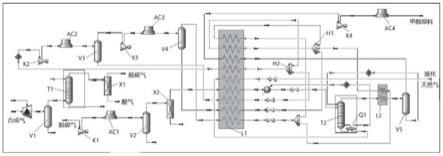
1.本发明属于地下煤合成气处理工艺技术领域,具体涉及一种高效地下煤合成气地面处理工艺。
背景技术:2.煤炭地下气化技术是将处于地下的煤炭进行有控制的燃烧,通过对煤层的热作用及化学作用而产生可燃气体(主要成分为h2、co、co2、ch4等)的过程,该过程集建井、采煤、地面气化三大工艺为一体,变传统的物理采煤为化学采煤。煤炭地下气化技术不仅可以回收矿井遗弃煤炭资源,而且还可以用于开采井工难以开采或开采经济性、安全性较差的薄煤层、深部煤层、“三下”压煤和高硫、高灰、高瓦斯煤层;地下气化灰渣留在气化区,减少了地表下沉,无固体物质排放,煤气可以集中净化,大大减少了煤炭开采和使用过程中对环境的破坏,因具有安全性好、投资少、效益高、污染少等优点,深受世界各国的重视,是煤炭开采利用技术的重要补充。
3.地下煤合成气主要特点:井口来气温度高(>200℃),饱和含水量大(50%以上)需要污水回收再利用,组分复杂(高含co2、高含h2、含煤焦油、含粉尘杂质等),其中co2含量超过50%,脱碳难度大;目前的地下煤合成气处理工艺不完善,装置能耗高,资源整体利用率低,经济效益不佳。
技术实现要素:4.本发明的目的是克服现有技术的不足而提供一种高效地下煤合成气地面处理工艺
5.本发明的技术方案如下:
6.一种高效地下煤合成气地面处理工艺,包括以下步骤:
7.步骤一,除尘除油:从产品井出来的合成气通入重力式旋风分离器,将合成气中的固体杂质和煤焦油分离出来,而后通入水洗塔中通过塔顶喷淋水洗将煤焦油和粉尘进行洗涤得到原料气,水洗后控制塔底的液相温度为105℃,塔顶的原料气温度为45℃,原料气饱和含水量降至0.3%;
8.步骤二,mdea脱碳:采用mdea脱碳装置吸收原料气中的co2,将co2含量脱除至50ppm以下,得到脱碳气;
9.步骤三,co2回收液化:步骤二中的mdea脱碳装置吸收原料气中的co2后产生酸气,采用co2深度处理装置将酸气中的硫脱除并回收,将co2液化成液态二氧化碳;
10.步骤四,增压:步骤二中得到的脱碳气通过增压压缩机增压至5.4mpa,得到增压气;
11.步骤五,脱水:采用两塔等压分子筛脱水工艺对增压气脱水处理,增压气通入干燥塔顶部,通过分子筛吸附脱水后从干燥塔底部流出,将增压气中的水含量脱除至0.1ppm以下,得到脱水气;
12.步骤六,液化脱氢:脱水气通入主冷箱并向下流动,脱水气冷却至
‑
136℃时被引出主冷箱,进入脱氢塔分离出含有氢气的混合气,得到天然气,天然气从脱氢塔的底部流出后进入主冷箱底部冷却至
‑
162℃得到过冷的液化天然气,过冷的液化天然气经过节流膨胀后进入储罐;脱氢塔的顶部的混合气进入脱氢塔冷箱后通入脱氢塔回流罐,脱氢塔回流罐底部连通至脱氢塔进行回流,脱氢塔回流罐的顶部的氢组分气进入主冷箱加热至20℃,得到甲醇原料;
13.进一步地,步骤一中水洗塔过滤后产生的污水通入三相分离器,被三相分离器分离后的污水经过污水冷却器冷却后被抽料泵输送回水洗塔的上部。
14.进一步地,步骤二中的mdea溶液由重量份31.48%的mdea、59.86%的水、8.66%的哌嗪组成,将原料气通入co2吸收塔的底部,mdea溶液自塔顶流向塔底吸收原料气中的co2,吸收co2后的mdea溶液通过胺再生塔吸收co2对mdea再生。
15.进一步地,步骤二中的胺再生塔对mdea再生后产生酸气,将酸气通入co2深度处理装置中依次经过多级增压、脱硫、脱水脱汞、分馏回收后收集液态二氧化碳;酸气经过多个压缩机增压至3.6mpa,而后经过预热并与被加热约200℃的空气在反应器内反应得到反应气,将反应气冷凝后通入硫分离器,冷凝后的液态硫经硫分离器分离出进入硫磺成型、包装设备得到硫产品,反应气则经过硫磺聚集器和除雾器后硫分离器的顶部排出,而后依次通入分子筛干燥塔、脱汞塔内脱水脱汞,经过脱水脱汞后通入脱甲烷塔进行分馏,位于脱甲烷塔塔顶的塔顶气经过二氧化碳冷箱冷凝后再回流至脱甲烷塔内,回流后经脱甲烷塔塔底的重沸器重沸,而后经二氧化碳冷箱液化后进入产品储存单元。
16.进一步地,步骤六中主冷箱的制冷单元采用闭式制冷循环,冷剂是由氮气30%、甲烷24%、丙烷12%、乙烯19%、异戊烷15%组成的混合物,制冷单元的制冷温度范围是
‑
149℃~
‑
177℃;来自主冷箱顶部的低压冷剂,经第一冷剂压缩机的第一段压缩后,进入冷剂压缩机段间冷却器,冷却后的冷剂进入段间罐进行气液分离,得到第一段气相冷剂和第一段液相冷剂,第一段气相冷剂经过第二冷剂压缩机增压至3.63mpa后在冷剂冷凝器冷却,进入冷剂出口分离器进行气液分离,得到第二段气相冷剂和第二段液相冷剂,分别进入主冷箱,经主冷箱内的第一混合器混合后在第二混合器内和第一段液相冷剂混合,而后从主冷箱顶部通入第一冷剂压缩机形成循环。
17.与现有技术相比,本发明的有益效果是:
18.1.本发明采用mdea脱碳技术,co2脱除效率高,结合co2回收液化,更利于将合成气中的co2回收完全,在co2回收的过程中,脱硫并将合成气中的硫回收再利用,脱氢后得到液化天然气,合成气中的氢气等组分回流冷凝后得到甲醇原料,将产品井出来的合成气中的有用成分进行分离回收,得到相关的产品,有效提高整体资源利用率,经济效益显著;
19.2.本发明采用水洗塔水洗工艺,可以有效将合成气中剩余的固体杂质、煤焦油、高温饱和含水等再次洗涤,可回收循环用水量600t/h,同时解决了煤焦油可能堵塞塔底、污水难回收和复用的问题,进而达到合成气后续处理工艺流程要求;
20.3.本发明的工艺充分考虑到合成气的压力、组成、产品收率以及经济效益,有效降低能耗,将装置的综合能耗由4814.04kw
·
h/104nm3降低至1378.86kw
·
h/104nm3,综合能耗下降了71.36%,整体资源利用率高,经济效益显著,通过资源有效利用,可以得到lng(液化天然气)、液态co2、氢气、工业硫磺、煤焦油等产品,通过经济效益分析,每年净利润达(税
后)3.61亿元;该技术不仅可将大量地层深部闲置煤炭资源进行清洁化利用,缓解天然气供应紧张局面,还能有效解决由煤炭燃烧排放co2引起的环境问题。
附图说明
21.图1为本发明的简易流程框图;
22.图2为本发明的整体流程图;
23.图3为本发明中的除尘除油流程图;
24.图4为本发明中的mdea脱碳流程图;
25.图5为本发明中的co2回收液化流程图;
26.图6为本发明中的co2回收液化中脱硫流程图;
27.图7为本发明中的co2回收液化中脱水流程图。
28.图中,重力式旋风分离器(v1),水洗塔(t1),脱碳单元(x1),增压压缩机(k1),增压冷却器(ac1),增压分离器(v2),脱水单元(x2),主冷箱(l1),脱氢塔(t2),重沸器(q1),脱氢塔冷箱(l2),脱氢塔回流罐(v3),氢组分压缩机(k4),氢组分冷却器(ac4),第一冷剂压缩机(k2),段间冷却器(ac2),段间罐,第二冷剂压缩机(k3),冷剂冷却器(ac3),冷剂出口分离器(v4),第一混合器(h1),第二混合器(h2);
29.三相分离器(v6),污水冷却器(ac5);
30.过滤器(v7),co2吸收塔(t3),富胺闪蒸罐(v8),脱碳气分离器(v9),半贫液冷却器(ac6),胺再生塔(t4),再生塔冷却器(ac7),再生塔分离器(v11),闪蒸气分离器(v10);
31.一级压缩机(k5),一级冷却器(ac8),一级分离器(v12),二级压缩机(k6),二级冷却器(ac9),二级分离器(v13),三级压缩机(k7),三级冷却器(ac10),三级分离器(v14),四级压缩机(k8),四级冷却器(ac11),四级分离器(v15),脱硫系统(y1),脱水系统(y2),脱甲烷塔(t5),二氧化碳冷箱(l3),脱甲烷塔回流罐(v16);
32.酸气预热器(s1),空气预热器(s2),反应器(tl1),硫冷凝器(s3),硫分离器(tl2),汽包(b1);
33.分子筛干燥塔(tw1),脱汞塔(tw2),粉尘过滤器(f1),碳粉过滤器(f2)。
具体实施方式
34.下面将结合本发明实施例中的附图,对本发明实施例中的技术方案进行清楚、完整地描述,显然,所描述的实施例仅仅是本发明一部分实施例,而不是全部的实施例。基于本发明中的实施例,本领域普通技术人员在没有做出创造性劳动前提下所获得的所有其他实施例,都属于本发明保护的范围。
35.如图1
‑
2所示,一种高效地下煤合成气地面处理工艺,包括以下步骤:
36.步骤一,除尘除油:从产品井出来的合成气通入重力式旋风分离器v1,将合成气中的固体杂质和煤焦油分离出来,而后通入水洗塔t1中通过塔顶喷淋水洗将煤焦油和粉尘进行洗涤得到原料气,水洗后控制塔底的液相温度为105℃,塔顶的原料气温度为45℃,原料气饱和含水量降至0.3%;利用重力沉降分离原理和旋风分离原理,根据不同组分的密度差,将合成气中的固体杂质、煤焦油等较重组分分离出来,本工艺分离效率高,可将合成气中的固体杂质、煤焦油等较重组分分离至10mg/l左右;
37.步骤二,mdea脱碳:采用mdea脱碳装置吸收原料气中的co2,将co2含量脱除至50ppm以下,得到脱碳气;
38.步骤三,co2回收液化:步骤二中的mdea脱碳装置吸收原料气中的co2后产生酸气,采用co2深度处理装置将酸气中的硫脱除并回收,将co2液化成液态二氧化碳;
39.步骤四,增压:步骤二中得到的脱碳气通过增压压缩机k1增压至5.4mpa,脱碳气的操作压力为3.2mpa,为满足轻烃回收对冷凝压力的要求,将脱碳气增压至5.4mpa左右,得到增压气;
40.步骤五,脱水:采用两塔等压分子筛脱水工艺对增压气脱水处理,增压气通入干燥塔顶部,通过分子筛吸附脱水后从干燥塔底部流出,经干燥器出口过滤器v7过滤后进入下一步骤,将增压气中的水含量脱除至0.1ppm以下,得到脱水气;
41.两塔等压分子筛脱水工艺采用两台干燥塔,分别为第一干燥塔和第二干燥塔,当第一干燥塔用于吸附脱水时,第二干燥塔进行再生,再生气采用粉尘过滤器过滤并节流后的天然气和lng(液化天然气)储罐闪蒸气的混合气;lng储罐出来的闪蒸气经闪蒸气压缩机增压后,与一部分经过第一干燥塔脱水并调压后的干气混合,通过再生气加热器加热至再生温度260~280℃,然后从第二干燥器底部进入,将分子筛吸附的水分脱除掉,再生气从第二干燥器顶部出来,经再生气空冷器冷却后,进入再生气分离器分液,分液后的气体从再生气分液罐顶部出来,从第一干燥塔的入口分离器前进入系统,液体从再生气分液罐底部流出去排污汇管;其中,操作温度为40℃,操作压力3.5mpa,吸附周期8小时,再生气用量约为原料气量的7~11%,再生温度260℃,再生气出床层温度220℃;
42.具体的,为保证天然气脱水部分的正常运行,分子筛干燥器应采用dcs系统分散控制,系统可自动切换吸附、再生;为保证再生温度的要求,再生加热器设温度控制;分子筛干燥器床层温度远传至集中控制室显示;为了确保冷却分离系统不冻堵,脱水后干气管线设置在线露点分析仪,显示脱水后露点并报警;再生气分离器设置液位显示、控制,压力显示、控制。
43.步骤六,液化脱氢:脱水气通入主冷箱l1并向下流动,脱水气冷却至
‑
136℃时被引出主冷箱l1,进入脱氢塔t2分离出含有氢气的混合气,得到天然气,其中混合气中含有72%左右的氢气和18%左右的一氧化碳,天然气从脱氢塔t2的底部流出后进入主冷箱l1底部冷却至
‑
162℃得到过冷的液化天然气,过冷的液化天然气经过节流膨胀后进入储罐,由于天然气在冷箱内被冷却过程始终处于过冷状态,所以在储罐内只会产生较少的闪蒸气;脱氢塔t2的顶部的混合气进入脱氢塔冷箱l2后通入脱氢塔回流罐v3,脱氢塔回流罐v3底部连通至脱氢塔t2进行回流,脱氢塔回流罐v3的顶部的氢组分气进入主冷箱l1加热至20℃,得到甲醇原料;
44.本实施例中,步骤一中水洗塔t1过滤后产生的污水通入三相分离器v6,被三相分离器v6分离后的污水经过污水冷却器ac5冷却后被抽料泵输送回水洗塔t1的上部,可以有效将合成气中剩余的固体杂质、煤焦油、高温饱和含水等再次洗涤,可回收循环用水量600t/h,同时解决了煤焦油可能堵塞塔底、污水难回收和复用的问题,进而是合成气达到后续处理工艺流程要求。
45.本实施例中,步骤二中的mdea溶液由重量份31.48%的mdea、59.86%的水、8.66%的哌嗪组成,将原料气通入co2吸收塔t3的底部,mdea溶液自塔顶流向塔底吸收原料气中的
co2,mdea溶液简称胺液,该工艺具有酸气负荷大、二氧化碳脱除效率高的优点,可将原料气中二氧化碳含量脱除至50ppm以下。
46.步骤一中得到的原料气通入过滤器v7内将将粒径大于10μm的液体及杂质除去,将过滤后压力为3.35mpa、温度为42℃的原料气通入co2吸收塔t3下部,将压力为3.5mpa、温度为40℃的mdea溶液通入co2吸收塔t3的上部,mdea溶液与原料气逆向接触后将原料天然气中的co2吸收形成脱碳气,co2吸收塔t3的顶部设置有脱碳气冷却器将脱碳气冷却,脱碳气冷却器连通有脱碳气分离器v9将脱碳气分离后通入干燥塔顶部进行脱水处理;
47.mdea溶液吸收co2后形成富胺液,富胺液从co2吸收塔t3的塔底流出后通入富胺闪蒸罐v8内,闪蒸后的半贫液通入胺再生塔t4内将脱除co2,胺再生塔t4塔顶的压力为0.005mpa、温度为97.6℃,胺再生塔t4塔底的压力为0.01mpa、温度为113.5℃,胺再生塔t4的塔顶设置有塔顶冷却器和塔顶回流罐,胺再生塔t4内产生的酸气通入co2深度处理装置中进行回收硫和二氧化碳,而胺再生塔t4内冷却后形成的液体经由塔顶回流罐回流至胺再生塔t4内,胺再生塔t4塔底的胺液经重沸器通入贫胺缓冲罐内,贫胺缓冲罐内的胺液通入co2吸收塔t3顶部开始新的循环;
48.其中,富胺闪蒸罐v8下端连通有三通阀将半贫液分成两股,其中一股通入胺再生塔t4内,另一股通过增压泵通入co2吸收塔t3的中部,增压泵和co2吸收塔t3之间设置有半贫液冷却器ac6,将半贫液冷却后通入co2吸收塔t3的中部后,半贫液对原料天然气进行预吸收,由于原料天然气从co2吸收塔t3的下部通入,位于co2吸收塔t3下半段的原料天然气的酸性组分浓度较高,co2吸收塔t3下半段的原料天然气进行预吸收,经过预吸收后的原料天然气再与再生后的贫胺液在co2吸收塔t3上半段接触,从而使原料天然气中的酸性组分达到处理指标要求,增加预吸收后可有效提升除碳效果,有效降低胺溶液的循环量和再生塔的再生负荷,从而有效降低胺溶液的再生能耗,使再生能耗由240mw降低至80mw左右,装置能耗下降70%以上。
49.具体的,所述胺再生塔t4上设置有压力调节阀和液位报警器,用以方便补充胺再生塔t4内的胺溶液量,从而利于调节脱碳工艺系统中的胺溶液量的调节,在胺溶液含量不足时能够及时补充,为防止mdea溶液发泡,系统中需增加消泡剂罐、胺过滤器以及新鲜mdea补充装置,只有当mdea溶液发泡时才向系统内通入少量消泡剂。
50.本实施例中,步骤二中的胺再生塔t4对mdea再生后产生酸气,将酸气通入co2深度处理装置中依次经过多级增压、脱硫、脱水脱汞、分馏回收后收集液态二氧化碳;酸气经过多个压缩机增压至3.6mpa,而后经过预热并与被加热约200℃的空气一起通入管道混合器,充分混合后通入在反应器tl1内在反应器tl1上部的绝热段发生反应得到反应气,反应热用于加热反应气体,加快反应速度,以获得最大的转化率,将反应气冷凝后通入硫分离器tl2,冷凝后的液态硫经硫分离器tl2分离出进入硫磺成型、包装设备得到硫产品,充分反应后的反应气进入温度在硫的露点温度以上的等温反应段,通过与冷却盘管内水的冷却作用将温度控制在硫露点温度以上,防止硫在催化剂床层中冷凝,反应气离开反应器tl1后进入硫冷凝器s3冷却成液态硫,然后进入硫分离器tl2,最后进入硫磺成型、包装设备得到硫产品,反应气则经过硫磺聚集器和除雾器后硫分离器tl2的顶部排出,而后依次通入分子筛干燥塔tw1、脱汞塔tw2内脱水脱汞,经过脱水脱汞后通入脱甲烷塔t5进行分馏,位于脱甲烷塔t5塔顶的温度为
‑
27℃、压力为1.45mpa的塔顶气进入二氧化碳冷箱l3冷凝至
‑
32℃,冷凝后进入
脱甲烷塔回流罐v16,然后经过脱甲烷塔t5回流泵增压后回流至脱甲烷塔t5顶充分脱烃,回流后经脱甲烷塔t5塔底的重沸器重沸至
‑
26℃,重沸后通入二氧化碳冷箱l3内冷却至
‑
26.4℃并进行液化,液化后的二氧化碳浓度为99%,而后进入产品储存单元;
51.其中,多级增压采用四级增压,将原酸气通入一级压缩机k5中,一级压缩机k5经一级冷却器ac8连通有一级分离器v12,一级分离器v12连通有二级压缩机k6,二级压缩机k6经二级冷却器ac9连通有二级分离器v13,二级分离器v13连通有三级压缩机k7,三级压缩机k7经三级冷却器ac10连通有三级分离器v14,三级分离器v14连通有四级压缩机k8,四级压缩机k8经四级冷却器ac11连通有四级分离器v15,四级分离器v15连通至步骤二中的干燥塔,经过多级的压缩、冷却和分离能够有效提高增压除杂的效果。
52.本实施例中,步骤六中主冷箱l1的制冷单元采用闭式制冷循环,冷剂是由氮气、甲烷、丙烷、乙烯、异戊烷组成的混合物,其中氮气的质量分数为30%、甲烷的质量分数为24%、丙烷的质量分数为12%、乙烯的质量分数为19%、异戊烷的质量分数为15%,制冷单元的制冷温度范围是
‑
149℃~
‑
177℃;来自主冷箱l1顶部的低压冷剂,经第一冷剂压缩机k2的第一段压缩后,进入冷剂压缩机段间冷却器ac2,冷却后的冷剂进入段间罐进行气液分离,得到第一段气相冷剂和第一段液相冷剂,第一段气相冷剂经过第二冷剂压缩机k3增压至3.63mpa后在冷剂冷凝器冷却,进入冷剂出口分离器v4进行气液分离,得到第二段气相冷剂和第二段液相冷剂,分别进入主冷箱l1,第二段气相冷剂以其自身的压力流动,第二段液相冷剂则有冷剂泵送入,第二段气相冷剂进入主冷箱l1时的温度为40℃,自上向下流出主冷箱l1时的温度为
‑
159.4℃,第二段液相冷剂进入主冷箱l1时的温度为40℃,自上向下流出主冷箱l1时的温度为
‑
151.5℃,第一段液相冷剂进入主冷箱l1时的温度为40℃,自上向下流出主冷箱l1时的温度为
‑
60.3℃,高压冷剂自上向下流出后,经节流阀膨胀至0.36mpa,第二段气相冷剂和第二段液相冷剂膨胀后经主冷箱l1内的第一混合器h1混合,而后在第二混合器h2内和第一段液相冷剂混合,混合后的低压冷剂的温度为
‑
59.7℃,低压冷剂自下而上流动,吸收高压冷剂和从脱氢塔t2底部流出的天然气的热量后温度升至26.7℃,低压冷剂从主冷箱l1顶部流出后通入第一冷剂压缩机k2形成循环;
53.其中,对于该制冷工艺,由于为闭式循环,当制冷系统首次填装冷剂后,不存在大的泄漏,只需要较少的冷剂补充,首次填装的冷剂原料均需外购和配比,装置正常运行后,甲烷的补充来生产的液化天然气产品;氮气是由液氮气化而来,低温液氮进入液氮储罐后,利用低温液氮泵将液氮输至液氮气化器,液氮气化器利用空气加热,将液氮升温气化达到系统压力要求,气化后氮气进入氮气缓冲罐,后经调压计量进入氮气管网,氮气主要用来作为混合冷剂组分的同时兼顾填充气功能,如主冷箱l1隔层之间填充珠光砂,为避免珠光砂吸收水分从而冻裂冷箱,需要保持冷箱隔层氮气维持微正压。
54.尽管参照前述实施例对本发明进行了详细的说明,对于本领域的技术人员来说,其依然可以对前述各实施例所记载的技术方案进行修改,或者对其中部分技术特征进行等同替换,凡在本发明的精神和原则之内,所作的任何修改、等同替换、改进等,均应包含在本发明的保护范围。