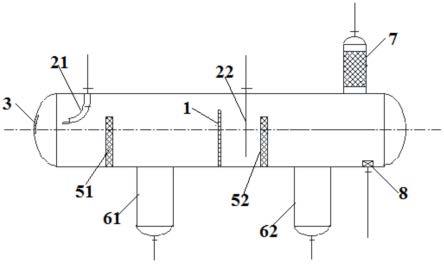
1.本实用新型属于多相分离技术领域,涉及一种低分油脱气脱水的分离装置。
背景技术:2.在石油炼制过程中,石油被加工为各种石油产品和化工产品,其中加氢工艺是各类燃料油和化工产品生产的重要步骤,后续还包括一系列的分离、分馏操作,即加氢反应产物需要先经过多级分离流程,以实现油水气三相产物的分离,通常包括高压、低压两级分离或者高压、中压、低压三级分离形式,经过前期分离,到达低压分离器时通常是低分油与酸性水的混合物,需要进一步进行油水气三相分离。
3.低压分离器的工作原理属于蒸馏操作中的平衡汽化,即进料经过减压后,在一定温度、压力下,汽、液两相迅速分离,得到相应的气相和液相产物;低压分离器作用一是将冷高压分离器来料中的气液相组分进行分离,闪蒸出部分气相组分,降低分馏系统的气相负荷;二是因为气相组分中含有较多的硫化氢,在低压分离器中脱除一部分硫化氢后,会减少分馏系统的设备腐蚀;上述过程对于油水相的分离效果往往较差,且来自冷高压分离器和中压分离器的两股馏分含水、含气量差异较大,通常需要分开处理,若是混合处理,会增加分水难度,油水分离不充分,影响产品油的品质。
4.cn 104667579a公开了一种强化冷低压分离器中油水分离和耦合除盐的方法,该方法先将含水低分油在入口段与脱盐水逆流混合后进入t型液气分离器进行脱气处理,将低分油中因降压闪蒸出的气相快速分离,油水混合物在低压分离器下部自左封头向右流动至整流分布器实现在径向截面的均布;油水依次通过粗粒化及cpi模块快速分离后一部分水外排,油及微量水通过隔板后进入深度分离段,油通过纤维组合模块将深度脱水后外排,拦截下的水进一步通过组合纤维模块深度除油后外排。该方法着重强调对含水低分油的油水分离,并实现脱盐处理,但并未涉及到含水、含气量不同的多种类低分油的处理,对于此种情况并未明确如何处理。
5.cn 214654064u公开了一种低压油、气、水三相分离装置,该装置包括卧式三相分离器,所述卧式三相分离器的壳体上具有液体进口、水出口、低分油出口及气出口,所述液体进口上连接混合产物输入管,混合产物输入管另一端连接至萘加氢生产十氢萘装置,所述水出口上安装有分水包,所述分水包的出水端连接水输出管,所述低分油出口上连接有油输出管,所述气出口上连接有气输出管,所述气输出管上串联有脱硫罐组。该装置可用于分离油水气三相混合物,但同样未涉及低分油的含水、含气量不同时,是分开处理还是混合处理,对于其存在的困难及解决方式均未明确。
6.综上所述,对于低分油脱气脱水装置的选择,尤其是涉及到含水量和含气量不同的两种低分油时,需要根据低分油特性进行装置的结构设计,使之能够实现两类低分油同时脱气脱水分离,同时降低设备成本。
技术实现要素:7.针对现有技术存在的问题,本实用新型的目的在于提供一种低分油脱气脱水的分离装置,所述分离装置针对两股含水量、含气量不同的低分油,通过纵向挡板的设置将低压分离器划分为两部分,同时将聚结器和水包设置两组,使其能够进行两段脱水过程,以实现含水量、含气量不同的两股低分油同时脱气脱水分离的目的,既能够满足分离效率,又能够降低设备成本。
8.为达此目的,本实用新型采用以下技术方案:
9.本实用新型提供了一种低分油脱气脱水的分离装置,所述分离装置包括低压分离器,所述低压分离器横向放置,中部设有纵向挡板,将低压分离器内部空间划分为两部分;
10.所述纵向挡板两侧的低压分离器顶部均设有进料管,所述进料管延伸到低压分离器内部,所述纵向挡板两侧的低压分离器中均设有聚结器,所述纵向挡板两侧的低压分离器的下部外侧均设有水包,所述纵向挡板的一侧距离纵向挡板由远及近依次为进料管、聚结器和水包,所述纵向挡板的另一侧距离纵向挡板由近及远依次为进料管、聚结器和水包;所述纵向挡板的另一侧的低压分离器底部还设有油相出口,顶部设有气包,所述油相出口和气包与纵向挡板的距离大于这一侧的水包与纵向挡板的距离。
11.本实用新型中,待处理的低分油为石油炼制过程中的加氢产物,例如煤焦油加氢反应后的产物,需要经过多级分离过程实现油水气三相分离,分离压力逐步降低,经过高压、中压分离后得到低分油进行低压分离,根据低分油的来源,会有不同气、水含量的低分油介质,因而本实用新型中将低压分离器通过纵向挡板划分为两部分,纵向挡板两侧均设置聚结器和水包,使得其中一股低分油能够进行两段脱水过程,从而实现含水量、含气量均不同的两种低分油同时脱水脱气分离的目的,既能够保证良好的分离效果,将水气油三相充分分离,又能够降低设备成本,简化装置结构,适用范围更广。
12.其中,所述低压分离器的操作压力通常为1.0~3.5mpa,例如1.0mpa、2.0mpa、3.0mpa或3.5mpa等,该压力条件下低分油可闪蒸产生气相,进一步分离出气相组分。
13.以下作为本实用新型优选的技术方案,但不作为本实用新型提供的技术方案的限制,通过以下技术方案,可以更好地达到和实现本实用新型的技术目的和有益效果。
14.作为本实用新型优选的技术方案,所述纵向挡板与低压分离器的顶部之间留有空隙;
15.所述纵向挡板的顶部与低压分离器的顶部之间的距离为200~400mm,例如200mm、250mm、300mm、350mm或400mm等,但并不仅限于所列举的数值,该数值范围内其他未列举的数值同样适用。
16.本实用新型中,所述纵向挡板上方留有空隙,可保障气体空间相同,也可使得经过一段脱水的低分油进入挡板另一侧进一步分离,该空隙大小的选择与低压分离器的直径尺寸以及待分离低分油的组成有关。
17.作为本实用新型优选的技术方案,所述纵向挡板两侧的进料管分别为第一进料管和第二进料管,所述第一进料管为内伸弯管,靠近封头一端,远离纵向挡板,所述第二进料管为内伸直管,紧邻纵向挡板。
18.作为本实用新型优选的技术方案,经第一进料管进入的低分油为第一低分油,来自中压分离器,经第二进料管进入的低分油为第二低分油,来自高压分离器。
19.本实用新型中,根据低压分离器前的分离装置,低分油的来源包括高压分离器的高分油,以及中压分离器分离的气体经冷却后得到的气液混合物,两者性质相近,分离后的去向相同,但是含水量、含气量差异较大,因而需要采用本实用新型中的低压分离器;其中高压分离器的分离压力为10~22mpa,例如10mpa、14mpa、18mpa或22mpa等,中压分离器的分离压力为4~8mpa,例如4mpa、5mpa、6mpa、7mpa或8mpa等。
20.本实用新型中,若未特意说明,所述压力通常是指表压。
21.作为本实用新型优选的技术方案,所述内伸弯管的出口段呈水平方向,朝向低压分离器的封头,所述封头内壁上与内伸弯管出口对应的位置设有防冲挡板。
22.本实用新型中,所述第一进料管为内伸弯管,其进料为水、气含量相对较高的低分油,通过内伸弯管的水平出口段将进料引至设备的封头,避免对分离器内的油水静置分离产生干扰,同时为避免进料流速较大对封头的损坏,在正对出口的位置设置防冲挡板,而且将内伸弯管水平段中临近出口的一段上半部分的管壁挖空,使得进料的压力能够先行降低,避免对封头造成较大的冲击作用。
23.作为本实用新型优选的技术方案,所述第二进料管的末端延伸到低压分离器的下部,其末端横截面由盲板封口,在第二进料管的侧面对称设有矩形开口槽。
24.本实用新型中,第二进料管同样设置内伸管,以防止发生虹吸现象,同时为了避免进料对分离器底部的冲击作用较大,将进料管末端水平截面采用盲板封口,盲板的厚度为5~8mm,例如5mm、6mm、7mm或8mm等,而在侧面对称设置两个开口槽,使得低分油向两侧喷出,同时矩形开口槽的面积较大,至少要大于第二进料管的横截面积,以保证低分油能够快速流出,其宽度的选择与第二进料管自身的直径有关。
25.作为本实用新型优选的技术方案,与第一进料管位于同一侧的聚结器和水包分别为第一聚结器和第一水包,所述第一聚结器的高度为低压分离器高度的75~80%,例如75%、76%、77%、78%、79%或80%等,但并不仅限于所列举的数值,该数值范围内其他未列举的数值同样适用,所述第一水包的底部设有第一水相出口。
26.本实用新型中,所述第一低分油进入低压分离器后,先通过第一聚结器,聚结器的表面具有亲水性,油中的水会被聚结器吸附,然后形成更大的水滴,再利用水和油的密度差,在重力作用下沉降而与油液分离,水相密度大,进入第一水包,通过第一水相出口排出;油相密度小,通过纵向挡板上方进入挡板另一侧继续处理。
27.作为本实用新型优选的技术方案,与第二进料管位于同一侧的聚结器和水包分别为第二聚结器和第二水包,所述第二聚结器的高度为低压分离器高度的75~80%,例如75%、76%、77%、78%、79%或80%等,但并不仅限于所列举的数值,该数值范围内其他未列举的数值同样适用,所述第二水包的底部设有第二水相出口。
28.本实用新型中,所述第二低分油进入低压分离器后,先通过第二聚结器,同理形成水滴,在重力作用下沉降与油液分离,水相密度大,进入第二水包,通过第二水相出口排出。
29.作为本实用新型优选的技术方案,所述油相出口和气包均位于第二进料管一侧,所述油相出口处设有防涡流器。
30.本实用新型中,经过第二聚结器和第二水包的分离,通过低分分离器的底部的油相出口排出,送至下游的分馏系统,进一步切割成不同馏分段的轻质油品,为了防止低分油排出速度过快,形成涡流,在油相出口处设置了防涡流器。
31.作为本实用新型优选的技术方案,所述气包内装填有填料柱,所述气包的顶部设有气相出口。
32.本实用新型中,所述低压分离器顶部设有气包,气包内装填一段规整填料柱,主要作用是分离气体夹带的液滴,保证气液分离的效率,气包顶部设气相出口,把两种低分油降压闪蒸产生的气体统一排出。
33.与现有技术相比,本实用新型具有以下有益效果:
34.(1)本实用新型所述分离装置针对两股含水量、含气量不同的低分油,通过纵向挡板的设置将低压分离器划分为两部分,并在两侧均设置聚结器和水包,使得其中一股低分油能够进行两段脱水过程,从而实现含水量、含气量均不同的两种低分油同时脱水脱气分离的目的,保证良好的分离效果,与两种低分油混合后一起脱气脱水的方式相比,气体含液率降低5~20%,水相含油率降低10~25%;
35.(2)本实用新型所述分离装置能够将设备成本降低30%~50%,简化装置结构,适用范围更广。
附图说明
36.图1是本实用新型实施例1提供的低分油脱气脱水的分离装置的结构示意图;
37.图2是本实用新型实施例1提供的第一进料管的结构示意图;
38.图3是本实用新型实施例1提供的第二进料管的结构示意图;
39.其中,1-纵向挡板,21-第一进料管,22-第二进料管,3-防冲挡板,4-盲板,51-第一聚结器,52-第二聚结器,61-第一水包,62-第二水包,7-气包,8-防涡流器。
具体实施方式
40.为更好地说明本实用新型,便于理解本实用新型的技术方案,下面对本实用新型进一步详细说明,但下述的实施例仅是本实用新型的简易例子,并不代表或限制本实用新型的权利保护范围,本实用新型保护范围以权利要求书为准。
41.本实用新型具体实施方式部分提供了一种低分油脱气脱水的分离装置,所述分离装置包括低压分离器,所述低压分离器横向放置,中部设有纵向挡板1,将低压分离器内部空间划分为两部分;
42.所述纵向挡板1两侧的低压分离器顶部均设有进料管,所述进料管延伸到低压分离器内部,所述纵向挡板1两侧的低压分离器中均设有聚结器,所述纵向挡板1两侧的低压分离器的下部外侧均设有水包,所述纵向挡板1的一侧距离纵向挡板1由远及近依次为进料管、聚结器和水包,所述纵向挡板1的另一侧距离纵向挡板1由近及远依次为进料管、聚结器和水包;所述纵向挡板1的另一侧的低压分离器底部还设有油相出口,顶部设有气包7,所述油相出口和气包7与纵向挡板1的距离大于这一侧的水包与纵向挡板1的距离。
43.以下为本实用新型典型但非限制性实施例:
44.实施例1:
45.本实施例提供了一种低分油脱气脱水的分离装置,所述分离装置的结构示意图如图1所示,包括低压分离器,所述低压分离器横向放置,中部设有纵向挡板1,将低压分离器内部空间划分为两部分;
46.所述纵向挡板1两侧的低压分离器顶部均设有进料管,所述进料管延伸到低压分离器内部,所述纵向挡板1两侧的低压分离器中均设有聚结器,所述纵向挡板1两侧的低压分离器的下部外侧均设有水包,所述纵向挡板1的一侧距离纵向挡板1由远及近依次为进料管、聚结器和水包,所述纵向挡板1的另一侧距离纵向挡板1由近及远依次为进料管、聚结器和水包;所述纵向挡板1的另一侧的低压分离器底部还设有油相出口,顶部设有气包7,所述油相出口和气包7与纵向挡板1的距离大于这一侧的水包与纵向挡板1的距离。
47.所述纵向挡板1与低压分离器的顶部之间留有空隙,纵向挡板1的顶部与低压分离器的顶部之间的距离为300mm。
48.所述纵向挡板1两侧的进料管分别为第一进料管21和第二进料管22,所述第一进料管21为内伸弯管,靠近封头一端,远离纵向挡板1,所述第二进料管22为内伸直管,紧邻纵向挡板1。
49.经第一进料管21进入的低分油为第一低分油,来自中压分离器,经第二进料管22进入的低分油为第二低分油,来自高压分离器。
50.所述第一进料管21的结构示意图如图2所示,所述内伸弯管的出口段呈水平方向,朝向低压分离器的封头,所述封头内壁上与内伸弯管出口对应的位置设有防冲挡板3;所述内伸弯管的水平段中临近出口的一段不设置上半部分的管壁。
51.所述第二进料管22的结构示意图如图3所示,其末端延伸到低压分离器的下部,其末端横截面由盲板4封口,在第二进料管22的侧面对称设有两个矩形开口槽。
52.与第一进料管21位于同一侧的聚结器和水包分别为第一聚结器51和第一水包61,所述第一聚结器51的高度为低压分离器高度的75%,所述第一水包61的底部设有第一水相出口。
53.与第二进料管22位于同一侧的聚结器和水包分别为第二聚结器52和第二水包62,所述第二聚结器52的高度为低压分离器高度的75%,所述第二水包62的底部设有第二水相出口。
54.所述油相出口和气包7均位于第二进料管22一侧,所述油相出口处设有防涡流器8。
55.所述气包7内装填有填料柱,所述气包7的顶部设有气相出口。
56.实施例2:
57.本实施例提供了一种低分油脱气脱水的分离装置,所述分离装置包括低压分离器,所述低压分离器横向放置,中部设有纵向挡板1,将低压分离器内部空间划分为两部分;
58.所述纵向挡板1两侧的低压分离器顶部均设有进料管,所述进料管延伸到低压分离器内部,所述纵向挡板1两侧的低压分离器中均设有聚结器,所述纵向挡板1两侧的低压分离器的下部外侧均设有水包,所述纵向挡板1的一侧距离纵向挡板1由远及近依次为进料管、聚结器和水包,所述纵向挡板1的另一侧距离纵向挡板1由近及远依次为进料管、聚结器和水包;所述纵向挡板1的另一侧的低压分离器底部还设有油相出口,顶部设有气包7,所述油相出口和气包7与纵向挡板1的距离大于这一侧的水包与纵向挡板1的距离。
59.所述纵向挡板1与低压分离器的顶部之间留有空隙,纵向挡板1的顶部与低压分离器的顶部之间的距离为200mm。
60.所述纵向挡板1两侧的进料管分别为第一进料管21和第二进料管22,所述第一进
料管21为内伸弯管,靠近封头一端,远离纵向挡板1,所述第二进料管22为内伸直管,紧邻纵向挡板1。
61.经第一进料管21进入的低分油为第一低分油,来自中压分离器,经第二进料管22进入的低分油为第二低分油,来自高压分离器。
62.所述内伸弯管的出口段呈水平方向,朝向低压分离器的封头,所述封头内壁上与内伸弯管出口对应的位置设有防冲挡板3。
63.所述第二进料管22的末端延伸到低压分离器的下部,其末端横截面由盲板4封口,在第二进料管22的侧面对称设有两个矩形开口槽。
64.与第一进料管21位于同一侧的聚结器和水包分别为第一聚结器51和第一水包61,所述第一聚结器51的高度为低压分离器高度的80%,所述第一水包61的底部设有第一水相出口。
65.与第二进料管22位于同一侧的聚结器和水包分别为第二聚结器52和第二水包62,所述第二聚结器52的高度为低压分离器高度的80%,所述第二水包62的底部设有第二水相出口。
66.所述油相出口和气包7均位于第二进料管22一侧,所述油相出口处设有防涡流器8。
67.所述气包7内装填有填料柱,所述气包7的顶部设有气相出口。
68.实施例3:
69.本实施例提供了一种低分油脱气脱水的分离装置,所述分离装置包括低压分离器,所述低压分离器横向放置,中部设有纵向挡板1,将低压分离器内部空间划分为两部分;
70.所述纵向挡板1两侧的低压分离器顶部均设有进料管,所述进料管延伸到低压分离器内部,所述纵向挡板1两侧的低压分离器中均设有聚结器,所述纵向挡板1两侧的低压分离器的下部外侧均设有水包,所述纵向挡板1的一侧距离纵向挡板1由远及近依次为进料管、聚结器和水包,所述纵向挡板1的另一侧距离纵向挡板1由近及远依次为进料管、聚结器和水包;所述纵向挡板1的另一侧的低压分离器底部还设有油相出口,顶部设有气包7,所述油相出口和气包7与纵向挡板1的距离大于这一侧的水包与纵向挡板1的距离。
71.所述纵向挡板1与低压分离器的顶部之间留有空隙,纵向挡板1的顶部与低压分离器的顶部之间的距离为400mm。
72.所述纵向挡板1两侧的进料管分别为第一进料管21和第二进料管22,所述第一进料管21为内伸弯管,靠近封头一端,远离纵向挡板1,所述第二进料管22为内伸直管,紧邻纵向挡板1。
73.经第一进料管21进入的低分油为第一低分油,来自中压分离器,经第二进料管22进入的低分油为第二低分油,来自高压分离器。
74.所述内伸弯管的出口段呈水平方向,朝向低压分离器的封头,所述封头内壁上与内伸弯管出口对应的位置设有防冲挡板3;所述内伸弯管的水平段中临近出口的一段不设置上半部分的管壁。
75.所述第二进料管22的末端延伸到低压分离器的下部,其末端横截面由盲板4封口,在第二进料管22的侧面对称设有两个矩形开口槽。
76.与第一进料管21位于同一侧的聚结器和水包分别为第一聚结器51和第一水包61,
所述第一聚结器51的高度为低压分离器高度的78%,所述第一水包61的底部设有第一水相出口。
77.与第二进料管22位于同一侧的聚结器和水包分别为第二聚结器52和第二水包62,所述第二聚结器52的高度为低压分离器高度的78%,所述第二水包62的底部设有第二水相出口。
78.所述油相出口和气包7均位于第二进料管22一侧,所述气包7内装填有填料柱,所述气包7的顶部设有气相出口。
79.采用上述实施例中的分离装置进行低分油的分离,从第一进料管21加入来自中压分离器的第一低分油,从第二进料管22加入来自高压分离器的第二低分油,第一低分油的含水量、含气量大于第二低分油的相应含量,第一低分油进入低压分离器后,先通过第一聚结器51,聚结器的表面具有亲水性,油中的水会被聚结器吸附,然后形成更大的水滴,再利用水和油的密度差,在重力作用下沉降而与油液分离,水相密度大,进入第一水包61,通过第一水相出口排出,油相密度小,通过纵向挡板1上方进入挡板另一侧;同理,第二低分油进入后,同样进行油水分离,油相经油相出口排出,送至下游的分馏系统;低分油进入低压分离器后,因压力降低会闪蒸产生气体,气体经气包7过滤后排出;所述分离装置实现了含水量、含气量均不同的两种低分油同时脱水脱气分离的目的,与两种低分油混合后共同脱气脱水的方式相比,气体含液率降低5~20%,水相含油率降低10~25%。
80.综合上述实施例可以看出,本实用新型所述分离装置针对两股含水量、含气量不同的低分油,通过纵向挡板的设置将低压分离器划分为两部分,并在两侧均设置聚结器和水包,使得其中一股低分油能够进行两段脱水过程,从而实现含水量、含气量均不同的两种低分油同时脱水脱气分离的目的,保证良好的分离效果,与两种低分油混合后共同脱气脱水的方式相比,气体含液率降低5~20%,水相含油率降低10~25%;所述分离装置能够降低设备成本,简化装置结构,适用范围更广。
81.本实用新型通过上述实施例来说明本实用新型的详细装置,但本实用新型并不局限于上述详细装置,即不意味着本实用新型必须依赖上述详细装置才能实施。所属技术领域的技术人员应该明了,对本实用新型的任何改进,对本实用新型装置的等效替换及辅助装置的添加、具体方式的选择等,均落在本实用新型的保护范围和公开范围之内。