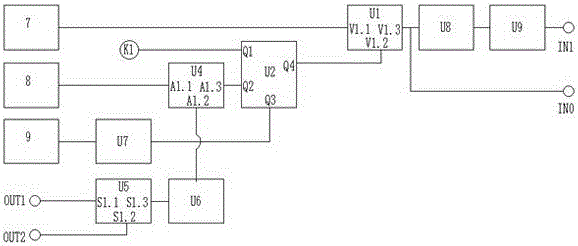
本发明低热值煤发电机组协调控制系统,属于电站自动控制的技术领域。
背景技术:煤炭生产和洗选中会产生大量煤矸石、煤泥、洗中煤等低热值煤资源,因缺乏市场,大多长期堆存在矿区,由于易自燃,并对大气、水体和土壤造成严重污染,长距离运输还会增加运输能耗等缺点,已成为矿区的老大难问题,因此,利用低热值煤发电就成为解决这一问题的有效手段。在利用低热值煤发电过程中,由于低热值煤锅炉与普通煤粉锅炉的动态特性除了同样具有参数多、非线性和纯迟延及大惯性特点外,还存在着具有输入输出变量多、耦合关系复杂,产汽及蓄热的滞后时间大等问题,导致低热值煤锅炉的燃烧控制系统自动投入效果不好、主汽压力波动较大,进而导致低热值煤发电机组协调控制系统不能正常投运。
技术实现要素:本发明克服现有技术存在的不足,所要解决的技术问题为:提供一种可快速合理的调节锅炉负荷和汽轮机负荷的低热值煤发电机组协调控制系统。为了解决上述技术问题,本发明采用的技术方案为:低热值煤发电机组协调控制系统,包括:锅炉调控模块、汽轮机调控模块、负荷指令处理模块和机组运行数据测量模块;所述协调控制系统还包括:主汽压力设定值运算模块和负荷协调控制模块;所述负荷指令处理模块包括:机组负荷指令设定模块、机组负荷速率设定模块和机组负荷变动模块,所述机组运行数据测量模块包括:主汽压力测量值模块、汽包压力测量值模块、调节级压力测量值模块、实际负荷测量值模块;所述主汽压力设定值运算模块分别与所述机组负荷指令设定模块、机组负荷速率设定模块和机组负荷变动模块相连;所述负荷协调控制模块分别与所述机组负荷指令设定模块、主汽压力测量值模块、汽包压力测量值模块、调节级压力测量值模块、实际负荷测量值模块、主汽压力设定值运算模块、锅炉调控模块和汽轮机调控模块相连。本发明中,所述主汽压力设定值运算模块包括:限速模块U1、模拟量切换模块U2、变负荷速率参数输入模块K1、第一加运算模块U4、第一减运算模块U5、第一函数运算模块U6、脉冲模块U7、第二函数运算模块U8和第三函数运算模块U9;所述第一减运算模块U5的正输入端S1.1与负荷协调控制模块的能量需求输出端OUT1相连,所述第一减运算模块U5的负输入端S1.2与负荷协调控制模块的锅炉热量输出端OUT2相连,所述第一减运算模块U5的输出 端S1.3与第一函数运算模块U6的输入端相连,所述第一函数运算模块U6的输出端与所述第一加运算模块U4的输入端A1.2相连,所述第一加运算模块U4的输入端A1.1与所述机组负荷速率设定模块的输出端相连,所述第一加运算模块U4的输出端A1.3与模拟量切换模块U2的输入端Q2相连,所述模拟量切换模块U2的输入端Q1与所述变负荷速率参数输入模块K1相连,所述模拟量切换模块U2的输入端Q3与所述脉冲模块U7的输出端相连,所述脉冲模块U7的输入端与所述机组负荷变动模块相连,所述模拟量切换模块U2的输出端Q4与所述限速模块U1的输入端V1.2相连,所述限速模块U1的输入端V1.1与所述机组负荷指令设定模块的输出端相连,所述限速模块U1的输出端V1.3与负荷协调控制模块的负荷指令输入端IN0、第二函数运算模块U8的输入端均相连,所述第二函数运算模块U8的输出端与第三函数运算模块U9的输入端相连,所述第三函数运算模块U9的输出端与所述负荷协调控制模块的主汽压力设定值输入端IN1相连。所述负荷协调控制模块包括:汽轮机负荷指令运算模块和锅炉负荷指令运算模块;所述汽轮机负荷指令运算模块包括:第二加运算模块U32、第一PD控制模块U33、第一乘运算模块U34、第一微分参数输入模块K5、第二减运算模块U36、第一PID控制运算模块U37;所述负荷协调控制模块的负荷指令输入端IN0分别与所述第二加运算模块U32的输入端A2.1、所述第一PD控制模块U33的输入端相连,所述第二加运算模块U32的输入端A2.2与所述第一乘运算模块U34的输出端M1.3相连,所述第一乘运算模块U34的输入端M1.2与第一微分参数输入模块K5相连,所述第一乘运算模块U34的输入端M1.1与所述第一PD控制模块U33的输出端相连,所述第二加运算模块U32的输出端A2.3与所述第二减运算模块U36的正输入端S2.1相连,所述第二减运算模块U36的负输入端S2.2与所述实际负荷测量值模块相连,所述第二减运算模块U36的输出端S2.3与第一PID控制运算模块U37的输入端相连,所述第一PID控制运算模块U37的输出端与汽轮机负荷指令输出端OUT3相连,所述汽轮机负荷指令输出端OUT3与汽轮机调控模块相连;所述锅炉负荷指令运算模块包括:第一除运算模块U10、第二乘运算模块U11、第三减运算模块U12、第三加运算模块U13、第二PD控制模块U14、第三乘运算模块U15、汽包蓄热参数输入模块K2、第二PID控制运算模块U17、第四加运算模块U18和前馈信号运算模块;所述第一除运算模块U10的被除数输入端D1.1、除数输入端D1.2分别与所述负荷协调控制模块的主汽压力设定值输入端IN1、主汽压力测量值模块相连,所述第一除运算模块U10的输出端D1.3与第二乘运算模块U11的输入端M2.1相连,所述第二乘运算模块U11的输入端M2.2与所述调节级压力测量值模块相连,所述第二乘运算模块U11的输出端M2.3分别与所述负荷协调控制模块的能量需求输出端OUT1、第三减运算模块U12的正输入端S3.1相连;所述调节级压力测量值模块还与所述第三加运算模块U13的输入端 A3.1相连,所述第三加运算模块U13的输入端A3.2与所述第三乘运算模块U15的输出端M3.3相连,所述第三乘运算模块U15的输入端M3.2与汽包蓄热参数输入模块K2相连,所述第三乘运算模块U15的输入端M3.1与第二PD控制模块U14的输出端相连,所述第二PD控制模块U14的输入端与汽包压力测量值模块相连,所述第三加运算模块U13的输出端A3.3分别与所述负荷协调控制模块的锅炉热量输出端OUT2、第三减运算模块U12的负输入端S3.2相连;所述第三减运算模块U12的输出端S3.3与第二PID控制运算模块U17的输入端相连,所述第二PID控制运算模块U17的输出端与所述第四加运算模块U18的输入端A4.1相连,所述第四加运算模块U18的输入端A4.2与前馈信号运算模块的输出端OUT5相连,所述第四加运算模块U18的输出端A4.3与锅炉负荷指令输出端OUT4相连,所述锅炉负荷指令输出端OUT4与锅炉调控模块相连;所述前馈信号运算模块包括:第四减运算模块U19、第四函数运算模块U20、第五加运算模块U21、第三PD控制模块U22、第六加运算模块U23、第四乘运算模块U24、第七加运算模块U25、第八加运算模块U26、第四PD控制模块U27、第五减运算模块U28、第五PD控制模块U29、第五乘运算模块U30、热值校正参数输入模块K3、第二微分参数输入模块K4;所述第四减运算模块U19的正输入端S4.1与机组负荷指令设定模块相连,所述第四减运算模块U19的负输入端S4.2与负荷协调控制模块的负荷指令输入端IN0相连,所述负荷指令输入端IN0还与第三PD控制模块U22的输入端、第四乘运算模块U24的输入端M4.1相连,所述第四减运算模块U19的输出端S4.3与第四函数运算模块U20的输入端相连,所述第四函数运算模块U20的输出端与第五加运算模块U21的输入端A5.1相连,所述第五加运算模块U21的输入端A5.2与第三PD控制模块U22的输出端相连,所述第五加运算模块U21的输出端A5.3与第六加运算模块U23的输入端A6.1相连,所述第六加运算模块U23的输入端A6.2与所述第四乘运算模块U24的输出端M4.3相连,所述第四乘运算模块U24的输入端M4.2与热值校正参数输入模块K3相连,所述第六加运算模块U23的输出端A6.3与第七加运算模块U25的输入端A7.1相连,所述第七加运算模块U25的输入端A7.2与第四PD控制模块U27的输出端相连,所述第四PD控制模块U27的输入端与所述负荷协调控制模块的主汽压力设定值输入端IN1相连,所述主汽压力设定值输入端IN1还与第五减运算模块U28的正输入端S5.1相连,所述第五减运算模块U28的负输入端S5.2与主汽压力测量值模块相连,所述第五减运算模块U28的输出端S5.3与第五PD控制模块U29的输入端相连,所述第五PD控制模块U29的输出端与第五乘运算模块U30的输入端M5.1相连,所述第五乘运算模块U30的输入端M5.2与第二微分参数输入模块K4相连,所述第五乘运算模块U30的输出端M5.3与第八加运算模块U26的输入端A8.2相连,所述第八加运算模块U26的输入端A8.1与第七加运算模块U25的输出端A7.3相连,所述第八加运算模块U26的输出端A8.3与所述前馈信号运算模块的输 出端OUT5相连。本发明与现有技术相比具有以下有益效果:本发明通过指令设定模块、机组运行数据测量模块、主汽压力设定值运算模块以及负荷协调控制模块之间的运算,得到了汽轮机负荷指令和锅炉负荷指令;保证低热值煤机组能够在各种工况下,即能维持机组的稳定,同时又能尽快满足电网对机组负荷调整性能的要求;本发明能快速合理的调节锅炉负荷和汽轮机负荷,避免了因负荷调整引起的主汽压力大幅度波动,使得负荷变化幅值与速率均能满足电网对AGC考核的要求、实用性极强。附图说明下面结合附图对本发明做进一步详细的说明。图1为本发明的电路结构示意图;图2为本发明中主汽压力设定值运算模块的连接示意图;图3为本发明负荷协调控制模块中的汽轮机负荷指令运算模块的连接示意图;图4为本发明负荷协调控制模块中的锅炉负荷指令运算模块的连接示意图;图5为本发明中第一函数运算模块U6的模块特性图;图6为本发明中第二函数运算模块U8的模块特性图;图7为本发明中第三函数运算模块U9的模块特性图;图8为本发明中第四函数运算模块U20的模块特性图;图中:1为锅炉调控模块,2为汽轮机调控模块,3为负荷指令处理模块,4为机组运行数据测量模块,5为主汽压力设定值运算模块,6为负荷协调控制模块,7为机组负荷设定模块,8为机组负荷速率设定模块,9为机组负荷变动模块,10为主汽压力测量值模块,11为汽包压力测量值模块,12为调节级压力测量值模块,13为实际负荷测量值模块,14为汽轮机负荷指令运算模块,15为锅炉负荷指令运算模块,16为前馈信号运算模块。具体实施方式如图1至图8所示,低热值煤发电机组协调控制系统,包括:锅炉调控模块1、汽轮机调控模块2、负荷指令处理模块3和机组运行数据测量模块4、主汽压力设定值运算模块5和负荷协调控制模块6;所述负荷指令处理模块3包括:机组负荷设定模块7、机组负荷速率设定模块8和机组负荷变动模块9,所述机组运行数据测量模块4包括:主汽压力测量值模块10、汽包压力测量值模块11、调节级压力测量值模块12、实际负荷测量值模块13;所述主汽压力设定值运算模块5分别与所述机组负荷设定模块7、机组负荷速率设定模块8和机组负荷变动模块9相连;所述负荷协调控制模块6分别与所述机组负荷设定模块7、主汽压力测量值模块10、汽包压力测量值模块11、调节级压力测量值模块12、实际负荷测量值模块 13、主汽压力设定值运算模块5、锅炉调控模块1和汽轮机调控模块2相连。本发明通过负荷指令处理模块、机组运行数据测量模块、主汽压力设定值运算模块以及负荷协调控制模块之间的运算,得到了汽轮机负荷指令和锅炉负荷指令,实现了在低热值煤机组负荷发生变化时,根据锅炉负荷指令实时控制燃料量、一次风量、送风量、引风量等的变化,根据汽轮机负荷指令实时控制汽轮机调门开度;保证低热值煤机组能够在各种工况下,即能维持机组的稳定,同时又能尽快满足电网对机组负荷调整性能的要求。如图2所示,所述主汽压力设定值运算模块5包括:限速模块U1、模拟量切换模块U2、变负荷速率参数输入模块K1、第一加运算模块U4、第一减运算模块U5、第一函数运算模块U6、脉冲模块U7、第二函数运算模块U8和第三函数运算模块U9;所述第一减运算模块U5的正输入端S1.1与负荷协调控制模块6的能量需求输出端OUT1相连,所述第一减运算模块U5的负输入端S1.2与负荷协调控制模块6的锅炉热量输出端OUT2相连,所述第一减运算模块U5的输出端S1.3与第一函数运算模块U6的输入端相连,所述第一函数运算模块U6的输出端与所述第一加运算模块U4的输入端A1.2相连,所述第一加运算模块U4的输入端A1.1与所述机组负荷速率设定模块8的输出端相连,所述第一加运算模块U4的输出端A1.3与模拟量切换模块U2的输入端Q2相连,所述模拟量切换模块U2的输入端Q1与所述变负荷速率参数输入模块K1相连,所述模拟量切换模块U2的输入端Q3与所述脉冲模块U7的输出端相连,所述脉冲模块U7的输入端与所述机组负荷变动模块9相连,所述模拟量切换模块U2的输出端Q4与所述限速模块U1的输入端V1.2相连,所述限速模块U1的输入端V1.1与所述机组负荷指令设定模块7的输出端相连,所述限速模块U1的输出端V1.3与负荷协调控制模块6的负荷指令输入端IN0、第二函数运算模块U8的输入端均相连,所述第二函数运算模块U8的输出端与第三函数运算模块U9的输入端相连,所述第三函数运算模块U9的输出端与所述负荷协调控制模块6的主汽压力设定值输入端IN1相连。具体地,机组负荷变动模块9与脉冲模块U7的输入端相连,在负荷变动初期脉冲模块U7的输出端将产生一个给定脉冲宽度的脉冲输出信号,并接入模拟量切换模块U2的控制输入端Q3,当Q3=1时,模拟量切换模块U2的输出端Q4将变负荷速率参数输入模块K1的输入值作为输出,并接入限速模块U1的限速值输入端V1.2,作为负荷变动初期一定时间内的限速值;在负荷变动后期,即脉冲信号消失后,Q3=0,模拟量切换模块U2则将第一加运算模块U4输出端A1.3作为模拟量切换模块U2的输出,并接入限速模块U1的限速值输入端V1.2,作为负荷变动后期的限速值。进一步地,所述限速模块U1的输出端V1.3输出的信号为负荷指令,该负荷指令分别与负荷协调控制模块6的负荷指令输入端IN0、第二函数运算模块U8的输入端相连,第二函数 运算模块U8将负荷指令转变成随负荷变化的主汽压力特性后作为第二函数运算模块U8的输出信号接入第三函数运算模块U9的输入端,第三函数运算模块U9是根据专家经验设置的低热值煤锅炉产汽和储能所需要的过程特性,所述第三函数运算模块U9的输出就是主汽压力设定值信号,上述过程完成了主汽压力设定值的运算;随后该主汽压力设定值信号与所述负荷协调控制模块6的主汽压力设定值输入端IN1相连,参与到汽轮机负荷指令运算、锅炉负荷指令运算的过程中。本实施例中,所述负荷协调控制模块6包括:汽轮机负荷指令运算模块14和锅炉负荷指令运算模块15;如图3所示,所述汽轮机负荷指令运算模块14包括:第二加运算模块U32、第一PD控制模块U33、第一乘运算模块U34、第一微分参数输入模块K5、第二减运算模块U36、第一PID控制运算模块U37;所述负荷协调控制模块6的负荷指令输入端IN0分别与所述第二加运算模块U32的输入端A2.1、所述第一PD控制模块U33的输入端相连,所述第二加运算模块U32的输入端A2.2与所述第一乘运算模块U34的输出端M1.3相连,所述第一乘运算模块U34的输入端M1.2与第一微分参数输入模块K5相连,所述第一乘运算模块U34的输入端M1.1与所述第一PD控制模块U33的输出端相连,所述第二加运算模块U32的输出端A2.3与所述第二减运算模块U36的正输入端S2.1相连,所述第二减运算模块U36的负输入端S2.2与所述实际负荷测量值模块13相连,所述第二减运算模块U36的输出端S2.3与第一PID控制运算模块U37的输入端相连,所述第一PID控制运算模块U37的输出端与汽轮机负荷指令输出端OUT3相连,所述汽轮机负荷指令输出端OUT3与汽轮机调控模块2相连;上述过程中,所述第一PID控制运算模块U37的输出端即为低热值煤机组的汽轮机负荷指令,该汽轮机负荷指令作为汽轮机组调控模块2的输入信号,使得汽轮机调控模块2可根据汽轮机负荷指令实时控制汽轮机调门开度,保证低热值煤机组能够在各种工况下,既能维持机组的稳定,同时又能尽快满足电网对机组负荷调整性能的要求。如图4所示,所述锅炉负荷指令运算模块15包括:第一除运算模块U10、第二乘运算模块U11、第三减运算模块U12、第三加运算模块U13、第二PD控制模块U14、第三乘运算模块U15、汽包蓄热参数输入模块K2、第二PID控制运算模块U17、第四加运算模块U18和前馈信号运算模块16;所述第一除运算模块U10的被除数输入端D1.1、除数输入端D1.2分别与所述负荷协调控制模块6的主汽压力设定值输入端IN1、主汽压力测量值模块10相连,所述第一除运算模块U10的输出端D1.3与第二乘运算模块U11的输入端M2.1相连,所述第二乘运算模块U11的输入端M2.2与所述调节级压力测量值模块12相连,所述第二乘运算模块U11的输出端M2.3分别与所述负荷协调控制模块6的能量需求输出端OUT1、第三减运算模块U12 的正输入端S3.1相连;所述调节级压力测量值模块12还与所述第三加运算模块U13的输入端A3.1相连,所述第三加运算模块U13的输入端A3.2与所述第三乘运算模块U15的输出端M3.3相连,所述第三乘运算模块U15的输入端M3.2与汽包蓄热参数输入模块K2相连,所述第三乘运算模块U15的输入端M3.1与第二PD控制模块U14的输出端相连,所述第二PD控制模块U14的输入端与汽包压力测量值模块11相连,所述第三加运算模块U13的输出端A3.3分别与所述负荷协调控制模块6的锅炉热量输出端OUT2、第三减运算模块U12的负输入端S3.2相连;所述第三减运算模块U12的输出端S3.3与第二PID控制运算模块U17的输入端相连,所述第二PID控制运算模块U17的输出端与所述第四加运算模块U18的输入端A4.1相连,所述第四加运算模块U18的输入端A4.2与前馈信号运算模块16的输出端OUT5相连,所述第四加运算模块U18的输出端A4.3与锅炉负荷指令输出端OUT4相连,所述锅炉负荷指令输出端OUT4与锅炉调控模块1相连;进一步地,所述前馈信号运算模块16包括:第四减运算模块U19、第四函数运算模块U20、第五加运算模块U21、第三PD控制模块U22、第六加运算模块U23、第四乘运算模块U24、第七加运算模块U25、第八加运算模块U26、第四PD控制模块U27、第五减运算模块U28、第五PD控制模块U29、第五乘运算模块U30、热值校正参数输入模块K3、第二微分参数输入模块K4;所述第四减运算模块U19的正输入端S4.1与机组负荷指令设定模块7相连,所述第四减运算模块U19的负输入端S4.2与负荷协调控制模块6的负荷指令输入端IN0相连,所述负荷指令输入端IN0还与第三PD控制模块U22的输入端、第四乘运算模块U24的输入端M4.1相连,所述第四减运算模块U19的输出端S4.3与第四函数运算模块U20的输入端相连,所述第四函数运算模块U20的输出端与第五加运算模块U21的输入端A5.1相连,所述第五加运算模块U21的输入端A5.2与第三PD控制模块U22的输出端相连,所述第五加运算模块U21的输出端A5.3与第六加运算模块U23的输入端A6.1相连,所述第六加运算模块U23的输入端A6.2与所述第四乘运算模块U24的输出端M4.3相连,所述第四乘运算模块U24的输入端M4.2与热值校正参数输入模块K3相连,所述第六加运算模块U23的输出端A6.3与第七加运算模块U25的输入端A7.1相连,所述第七加运算模块U25的输入端A7.2与第四PD控制模块U27的输出端相连,所述第四PD控制模块U27的输入端与所述负荷协调控制模块6的主汽压力设定值输入端IN1相连,所述主汽压力设定值输入端IN1还与第五减运算模块U28的正输入端S5.1相连,所述第五减运算模块U28的负输入端S5.2与主汽压力测量值模块10相连,所述第五减运算模块U28的输出端S5.3与第五PD控制模块U29的输入端相连,所述第五PD控制模块U29的输出端与第五乘运算模块U30的输入端M5.1相连,所述第五乘运算模块U30的输入端M5.2与第二微分参数输入模块K4相连,所述第五乘运算模块U30的输出端M5.3与第八加运 算模块U26的输入端A8.2相连,所述第八加运算模块U26的输入端A8.1与第七加运算模块U25的输出端A7.3相连,所述第八加运算模块U26的输出端A8.3与所述前馈信号运算模块16的输出端OUT5相连。本实施例中,所述第二PD控制模块U14的输入端与汽包压力测量值模块11相连,所述第二PD控制模块U14的输出端输出的信号为汽包压力变化速度,与汽包蓄热参数输入模块K2输出的汽包蓄热系数通过第三乘运算模块U15做乘积运算,该第三乘运算模块U15的输出端M3.3连接到第三加运算模块U13的输入端A3.2,第三加运算模块U13的输入端A3.1为调节级压力测量值模块12输入值,第三加运算模块U13的输出端A3.3的输出信号为低热值煤锅炉热量;第二乘运算模块U11的输出端接入第三减运算模块U12的正输入端S3.1,第三加运算模块U13输出端A3.3接入第三减运算模块U12的负输入端S3.2,第三减运算模块U12的输出端S3.3得到的是低热值煤锅炉的能量偏差;该能量偏差信号接入第二PID控制运算模块U17的输入端,经过第二PID控制运算模块U17的控制运算后输出的能量反馈控制信号连接到第四加运算模块U18输入端A4.1,第四加运算模块U18的另一路输入端A4.2接前馈信号运算模块16送来的前馈控制信号,所述的前馈控制信号由5路信号相加得到;第四加运算模块U18的输出端A4.3输出的即为低热值煤机组的锅炉负荷指令,该锅炉负荷指令作为锅炉调控模块1的输入信号,使得锅炉调控模块1可根据锅炉负荷指令及时控制燃料量、一次风量、送风量、引风量等的变化,保证低热值煤机组能够在各种工况下,既能维持机组的稳定,同时又能尽快满足电网对机组负荷调整性能的要求。具体地,图5至图6分别为:第一函数运算模块U6的模块特性图、第二函数运算模块U8的模块特性图、第三函数运算模块U9的模块特性图、第四函数运算模块U20的模块特性图,图中:i表示输入,o表示输出;进一步地,第一PD控制模块U33、第二PD控制模块U14、第三PD控制模块U22、第四PD控制模块U27、第五PD控制模块U29的模块特性均可用公式(1)表示如下:公式(1)中:o为输出值、i为输入值、k1为比例增益系数、k2是微分增益系数;所述第一PD控制模块U37、第二PID控制运算模块U17的模块特性均可用公式表示如下:公式(2)中:o为输出值、i为输入值、k1为比例增益系数、k2是积分增益系数、k3为微分增益系数。综上,本发明解决了低热值煤机组负荷协调控制系统在适应AGC考核过程中的技术难题,避免了因负荷调整引起的主汽压力大幅度波动,使得负荷变化幅值与速率均能满足电网对AGC考核的要求,具有突出的实质性特点和显著的进步;上面结合附图对本发明的实施例作了详细说明,但是本发明并不限于上述实施例,在本领域普通技术人员所具备的知识范围内,还可以在不脱离本发明宗旨的前提下作出各种变化。