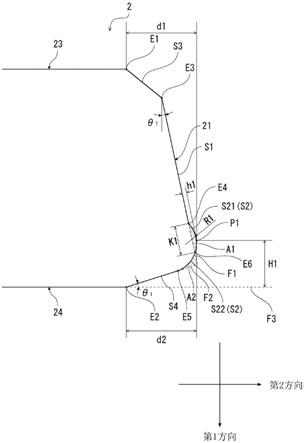
1.本发明涉及活塞环用线材以及活塞环的制造方法。
背景技术:2.一般的汽车所搭载的内燃机采用在气缸安装的活塞上设置多个活塞环的结构。多个活塞环根据其功能大致分为配置在燃烧室侧的压缩环(压力环)和配置在曲柄室侧的油环。
3.压缩环具有:气封功能,通过保持气密来抑制燃烧气体从燃烧室侧流出到曲柄室侧(漏气);散热功能,将活塞的热量传递给气缸来散热。油环具有油封功能:通过将附着在气缸的内壁(以下称为气缸内壁)的多余的机油(润滑油)向曲柄室侧刮落来抑制油流入到燃烧室侧(油上升)。这些活塞环可以通过包括以下工序的制造方法来制造:卷取工序,对带状的线材进行塑性加工至环状;切割工序,将线材切割至环状得到环;表面处理工序,对环施以表面处理;以及研磨工序,对环的表面进行研磨。
4.在此,已知外周面的至少一部分为锥形的压缩环。通过赋予压缩环的外周面适当的锥面,可以在活塞的下降过程时将油环没有刮落的油适当地刮落,在活塞的上升工序时通过锥面与气缸内壁之间的楔效应形成油膜。这样的锥形多用于作为在设置在活塞上的多个压缩环中从燃烧室侧起的第2道压缩环的第二道环(第2压力环)。
5.而且,已知在外周面为锥形的压缩环中,为了保证相对于气缸内壁的初始磨合性,在外周面形成平坦的抵接面(滑动面)。抵接面是通过在研磨工序中对环的外周面进行研磨加工而形成的。为了得到良好的初始磨合性,优选抵接面在整周上以均匀的宽度(抵接宽度)形成。为了得到均匀的抵接宽度,需要延长研磨工序的研磨时间(研磨的时间的长度),但是研磨时间越长抵接宽度越趋向增大。抵接宽度过大,将导致对气缸内壁的表面压力降低,恐怕会使油的刮落性能降低。为了应对这个问题,也考虑通过提高压缩环的张力来确保表面压力,但是那样做恐怕摩擦会增加,燃料效率会恶化。
6.与此相关,专利文献1中公开了在外周面为锥形的压缩环用的线材中,在成为环的外周面的面上形成第1锥部和比第1锥部锥角大的第2锥部。专利文献1中记载的技术意图通过研磨加工而在第2锥部的顶端的角部分形成抵接面,由此使抵接宽度变小而且均匀。
7.现有技术文献
8.专利文献
9.专利文献1:日本特许第5564082号公报
技术实现要素:10.发明所要解决的问题
11.为了均匀地得到更小的抵接宽度,需要使用于形成抵接面的研磨对象的部分更细(尖锐)。然而,由于线材通过模具的拉拔加工而成型,因此在线材的角部分形成依赖于模具的形状的圆角。因此,在所述的现有技术中,使成为研磨对象的部分超越模具的形状的限制
变细是很困难的。
12.本发明鉴于上述情况而完成的,其目的是提供一种能在外周面为锥形的活塞环中,形成抵接宽度小且均匀的抵接面的技术。
13.用于解决问题的方案
14.为解决上述问题,本发明采用以下构成。即本发明是一种活塞环用线材,是成为在内燃机中安装于活塞的环槽的活塞环的材料的线材,其中,
15.包括:第1侧面,在所述活塞环中形成外周面;第2侧面,在所述活塞环中形成内周面;第3侧面,连接所述第1侧面和所述第2侧面,并且在所述活塞环中形成与所述环槽的燃烧室侧的内壁对置的面;以及第4侧面,连接所述第1侧面和所述第2侧面,并且在所述活塞环中形成与所述环槽的曲柄室侧的内壁对置的面,
16.所述第1侧面包括:锥面,在与所述线材的延伸方向正交的剖面中以随着朝向第1方向而扩宽的方式倾斜,所述第1方向是从所述第3侧面侧朝向所述第4侧面侧的方向;以及凸出面,连接所述锥面和位于比所述锥面靠所述第1方向侧的规定的面,并且向第2方向侧凸出,所述第2方向是从所述第2侧面朝向所述第1侧面的方向,
17.所述凸出面由将所述锥面向所述第1方向侧延伸而成的第1虚拟面划分为第1部位和第2部位,所述第1部位与所述锥面连接并且相对于所述第1虚拟面向所述第2方向侧凸出所述第2部位连接所述第1部位和所述规定的面并且相对于所述第1虚拟面位于所述第2方向的相反侧,
18.所述第1部位形成为包括所述第1侧面中最位于所述第2方向侧的顶部并且向所述第2方向侧成为凸状。
19.当利用这样的线材制造活塞环时,在卷取工序中凸出面的第1部位被向第1虚拟面侧压溃,由此凸出面变形,能得到向径向外侧凸出的角部。然后,通过在研磨工序中研磨角部的顶端,能得到平坦的抵接面(滑动面)。就是说,本发明的线材通过卷取工序形成成为形成抵接面的研磨对象的角部。由此,对于本发明的线材来说,能不依赖于用于制造线材的模具的形状而尖锐地形成角部。其结果是,根据本发明的线材,能均匀地得到小的抵接宽度。在此,抵接宽度是指在活塞环的轴向上的抵接面的宽度。
20.此外,可以是,在本发明的线材中,在与所述线材的延伸方向正交的剖面中,作为由所述第1部位和所述第1虚拟面围成的区域的第1区域的面积是作为由所述第2部位、所述第1虚拟面、以及将所述规定的面延伸与所述第1虚拟面相交的第2虚拟面围成的区域的第2区域的面积以下。第1区域是表示线材中相对于第1虚拟面隆起的部分的区域。线材中的第1区域包括的部分通过卷取工序移动到第2区域,由此形成角部。根据本发明的线材,能通过将第1区域的面积设为第2区域的面积以下,在第2区域内形成角部。其结果是,能尖锐地形成角部,能得到小的抵接宽度。
21.此外,可以是,在本发明的线材中,所述第1侧面包括连接所述凸出面和所述第4侧面并且在与所述线材的延伸方向正交的剖面中以随着朝向所述第1方向而缩宽的方式倾斜的倾斜面作为所述规定的面。
22.此外,可以是,在本发明的线材中,形成为:
23.所述第1侧面包括连接所述凸出面和所述第4侧面的切割面,
24.所述切割面包括与所述凸出面相连的作为所述规定的面的第1底切割面以及连接
所述第1底切割面和所述第4侧面的第2底切割面,
25.所述第2底切割面的相对于所述第2方向的倾斜角度比所述第1底切割面的相对于所述第2方向的倾斜角度大。
26.优选,将所述第4侧面向所述第2方向延伸而成的第3虚拟面与所述顶部的在所述第1方向上的平行距离设为h1,
27.将所述第1虚拟面与所述顶部的与该第1虚拟面垂直的距离设为h1,
28.将在与所述线材的延伸方向正交的剖面中所述第1虚拟面的平行方向上的所述第1部位的与所述第1虚拟面相交的宽度设为k1,
29.将所述规定的面相对于所述第2方向的倾斜角度设为θ1时,
30.满足0.01mm≤h1≤0.2mm、0.005mm≤h1≤0.02mm、0.05mm≤k1≤0.15mm、θ1≥3
°
的条件。由此,能得到更小且均匀的抵接宽度。
31.此外,本发明还可以确定作为一种从线材制造活塞环的方法。就是说,本发明是一种在内燃机中安装于活塞的环槽的活塞环的制造方法,
32.所述线材包括:第1侧面,在所述活塞环中形成外周面;第2侧面,在所述活塞环中形成内周面;第3侧面,连接所述第1侧面和所述第2侧面,并且在所述活塞环中形成与所述环槽的燃烧室侧的内壁对置的面;以及第4侧面,连接所述第1侧面和所述第2侧面,并且在所述活塞环中形成与所述环槽的曲柄室侧的内壁对置的面,
33.所述第1侧面包括:锥面,在与所述线材的延伸方向正交的剖面中以随着朝向第1方向而扩宽的方式倾斜,所述第1方向是从所述第3侧面侧朝向所述第4侧面侧的方向;以及凸出面,连接所述锥面和位于比所述锥面靠所述第1方向侧的规定的面,并且向第2方向侧凸出,所述第2方向是从所述第2侧面朝向所述第1侧面的方向,
34.所述凸出面由将所述锥面向所述第1方向侧延伸而成的第1虚拟面划分为第1部位和第2部位,所述第1部位与所述锥面连接并且相对于所述第1虚拟面向所述第2方向侧凸出,所述第2部位连接所述第1部位和所述规定的面并且相对于所述第1虚拟面位于所述第2方向的相反侧,
35.所述第1部位形成为包括所述第1侧面中最位于所述第2方向侧的顶部并且向所述第2方向侧成为凸状,
36.所述活塞环的制造方法包括:
37.卷取工序,将所述线材送出,通过对所述线材施加外力使所述线材成型为环状;
38.切割工序,将成型为环状的所述线材切割得到环;以及
39.研磨工序,对所述环的表面进行研磨,
40.在所述卷取工序中,通过对所述第1侧面施加作用的外力来将所述第1部位向所述第1虚拟面侧压溃,由此使所述凸出面变形而形成角部,
41.在所述研磨工序中,通过对所述角部的顶端进行研磨来形成平坦的抵接面。
42.此外,可以是,在本发明的活塞环的制造方法中,在所述研磨工序前包括在所述环的外周面形成硬质覆膜的表面处理工序,所述硬质覆膜包括pvd处理膜、dlc膜、以及镀铬处理膜中至少任意一层。由此,能降低活塞环的外周面的摩擦力,使耐磨耗性提高。需要说明的是,“pvd(physical vapor deposition)处理膜”是指通过pvd法形成的覆膜。pvd法是通过使从靶射出的粒子附着在配对件的表面形成膜的一种蒸镀法,也被称作物理气相生长。
此外,“dlc(diamond like carbon)膜”是指主要由烃、碳的同素异形体构成的无定形的硬质碳膜。此外,“镀铬处理膜”是指通过镀铬形成的覆膜。此外,所述研磨工序前可以包括氮化处理工序。
43.发明效果
44.根据本发明,能在外周面为锥形的活塞环中,形成抵接宽度小并且均匀的抵接面。
附图说明
45.图1是表示利用实施方式1的线材制造的第二道环设置在内燃机的状态的图。
46.图2是表示实施方式1的线材的图。
47.图3是用于对实施方式1的线材的第1侧面进行说明的图。
48.图4是表示实施方式1的第二道环的制造方法的工序的图。
49.图5用于是对卷取工序进行说明的图。
50.图6是表示通过切割工序得到的环的外周面的图。
51.图7是用于对表面处理工序进行说明的图。
52.图8是表示研磨工序后的环的外周面的图。
53.图9是表示比较例的线材的图。
54.图10是表示利用实施方式2的线材制造的第二道环的图。
55.图11是表示实施方式2的线材的图。
56.图12是表示实施方式2的线材的图。
57.图13是表示通过切割工序得到的环的外周面的图。
58.图14是表示研磨工序后的环的外周面的图。
59.图15是表示利用实施方式3的线材制造的第二道环的图。
60.图16是表示实施方式3的线材的图。
具体实施方式
61.以下,一边参照附图一边对本发明的实施方式进行说明。在以下的实施方式中,作为活塞环的一例,将本发明的线材应用于作为压缩环的第二道环。但是,本发明并不限定于此。本发明的线材也可以应用于第一道环、油环。此外,只要没有特别记载,以下的实施方式所记载的配置就不是将发明的技术范围仅限定于这些的主旨。
62.需要说明的是,在以下的说明中,只要没有特别指定,“周长方向”是指第二道环的周长方向。只要没有特别指定,“径向”是指第二道环的半径方向。“径向内侧”是指第二道环的内周面侧,“径向外侧”是指其相反侧(即第二道环的外周面侧)。只要没有特别指定,“轴向”是指沿第二道环的中心轴的方向。活塞的环槽的“上壁”是指环槽的内壁中的燃烧室侧的内壁,“下壁”是指曲柄室侧的内壁。此外,只要没有特别指定,“延伸方向”是指线材的延伸方向。第二道环、线材的“上侧”是指第二道环设置于环槽时的环槽的上壁侧,“下侧”是指第二道环设置于环槽时的环槽的下壁侧。
63.<实施方式1>
64.图1是表示利用实施方式1的线材制造的第二道环设置在内燃机的状态的图。图1中示出了与第二道环的周长方向正交的剖面。图1所示的内燃机100具有气缸10、安装于气
缸10的内燃机用活塞20(以下称为活塞20)、以及未图示的燃烧室和曲柄室。在俯视图1的情况下,上侧为燃烧室侧,下侧为曲柄室侧。如图1所示,内燃机100中,通过在作为气缸10的内周面的气缸内壁10a和作为活塞20的外周面的活塞外周面20a之间确保规定的分离距离,形成间隙pc1。在活塞外周面20a形成有大致矩形剖面的环槽30。环槽30具有:形成于燃烧室侧的上壁301;形成于曲柄室侧并与上壁301对置的下壁302;以及连接上壁301和下壁302的内周缘的连接壁303。在环槽30中,安装有第二道环1。
65.[第二道环]
[0066]
第二道环1是随着活塞20的往复运动而在气缸内壁10a滑动的滑动构件。如图1所示,第二道环1的表面具有外周面11、内周面12、上表面13以及下表面14。第二道环1的外周面11形成为所谓的锥形。在第二道环1安装于环槽30的状态(使用状态)下,外周面11与气缸内壁10a滑动接触,内周面12与连接壁303对置,上表面13与上壁301对置,下表面14与下壁302对置。该第二道环1具有形成有接缝(未图示)的环状。此外,第二道环1具有自我张力,在安装于环槽30的情况下外周面11会按压气缸内壁10a。此外,在第二道环1的外周面11上也可以形成后述那样的硬质覆膜。
[0067]
如图1所示,第二道环1的外周面11包括锥面111、抵接面112、第1倾斜面113以及第2倾斜面114。锥面111具有以随着朝向下侧而扩径的方式倾斜的锥形。抵接面(滑动面)112是构成第二道环1的最外周部位的面。抵接面112连接锥面111的下缘并且沿轴向平坦地延伸,在第二道环1的整周上形成。抵接面112在第二道环1的使用状态下与气缸内壁10a滑动接触,将间隙pc1内的油刮落。通过形成该抵接面112,确保了相对于气缸内壁10a的初始磨合性。第1倾斜面113是连接上表面13的外周缘和锥面111的上缘的面,以随着朝向下侧而扩径的方式倾斜。第2倾斜面114是连接抵接面112的下缘和下表面14的外周缘的面,以随着朝向下侧而缩径的方式倾斜。需要说明的是,第1倾斜面113和第2倾斜面114在图2所示剖面中不仅可以是直线,也可以是由曲线表示的面,第1倾斜面113和上表面13、以及第2倾斜面114和下表面14也可以由规定半径的曲线连接。
[0068]
[线材]
[0069]
图2是表示实施方式1的线材2的图。图2中示出了与线材2的延伸方向正交的剖面。实施方式1的线材2是成为上述的第二道环1的材料的构件。线材2主要以钢材(钢)为材质,形成为长条的带状。作为线材2的材质的钢材,可以列举出碳素钢材、不锈钢材、合金钢、铸铁材质以及铸钢材质。但是,线材2的材料不限于此,也可以使用钛系、铜系的材料、铝系的材质。
[0070]
如图2所示,线材2的表面具有第1侧面21、第2侧面22、第3侧面23以及第4侧面24。第1侧面21是在第二道环1中形成外周面11的面。第2侧面22是在第二道环1中形成内周面12的面。第3侧面23是连接第1侧面21和第2侧面22,在第二道环1中形成上表面13的面。第4侧面24是连接第1侧面21和第2侧面22,在第二道环1中形成下表面14的面。第3侧面23和第4侧面24形成为相互平行的平坦面。在此,将与线材2的延伸方向正交,从第3侧面23侧朝向第4侧面24侧的方向设为第1方向。第1方向与第二道环1的轴向向下方向相对应。此外,将与线材2的延伸方向正交的方向,从第2侧面22侧朝向第1侧面21侧的方向设为第2方向。第2方向与第二道环的径向外向相对应。
[0071]
线材2的第1侧面21包括锥面s1、凸出面s2、第1倾斜面s3以及第2倾斜面s4。第1倾
斜面s3是在第二道环1中形成第1倾斜面113的面,与第3侧面23的第2方向侧的边缘e1连接并且以随着朝向第1方向而扩宽的方式倾斜。第2倾斜面s4是在第二道环中形成第2倾斜面114的面,以随着朝向第1方向而缩宽的方式倾斜并且与第4侧面24的第2方向侧的边缘e2连接。锥面s1是在第二道环1中形成锥面111的面,与第1倾斜面s3的第2方向侧的边缘e3连接并且以随着朝向第1方向而扩宽的方式倾斜。凸出面s2是在第二道环1中形成抵接面112的面,连接锥面s1的第1方向侧的边缘e4和第2倾斜面s4的第2方向侧的边缘e5并且向第2方向侧凸出。如图2所示,第2倾斜面s4位于比锥面s1靠第1方向侧,连接凸出面s2和第4侧面24。第2倾斜面s4相当于本发明的“规定的面”。
[0072]
图3是用于对实施方式1的线材2的第1侧面21进行说明的图。在此,将对锥面s1向第1方向侧延伸而成的虚拟的面称为第1虚拟面,以附图标记f1来表示。此外,将对第2倾斜面s4进行延伸与第1虚拟面相交的虚拟的面称为第2虚拟面,以附图标记f2来表示。如图3所示,凸出面s2由第1虚拟面f1划分为第1部位s21和第2部位s22。第1部位s21与锥面s1的第1方向侧的边缘e4连接,相对于第1虚拟面f1向第2方向侧凸出。此外,第1部位s21弯曲为包括在第1侧面21中最位于第2方向侧的顶部p1并且向第2方向侧成为凸状。就是说,线材2在第1部位s21处相对于第1虚拟面f1隆起。一方面,第2部位s22连接第1部位s21的第1方向侧的边缘e6和第2倾斜面s4的第2方向侧的边缘e5,相对于第1虚拟面f1位于第2方向的相反侧。就是说,线材2在第2部位s22处相对于第1虚拟面f1凹陷。在此,将由第1部位s21和第1虚拟面f1围成的区域设为第1区域a1。就是说,第1区域a1表示线材2中相对于第1虚拟面f1隆起的部分。此外,将由第2部位s22、第1虚拟面f1以及第2虚拟面f2围成的区域设为第2区域a2。
[0073]
[活塞环的制造方法]
[0074]
接着,对利用实施方式1的线材2来制造在图1中示出的第二道环1的方法进行说明。图4是表示实施方式1的第二道环的制造方法的工序的图。如图4所示,实施方式1的制造方法包括卷取工序、切割工序、表面处理工序以及研磨工序。以下,对各工序进行说明。
[0075]
首先,在s110的卷取工序中,通过对送出的线材2施加外力使线材2成型为环状。图5是用于对卷取工序进行说明的图。如图5所示,在卷取工序中,从卷绕有线材2的线圈母盘200中拉出线材2向卷取装置300送出。卷取装置300具备夹送辊310、芯轴320、助卷辊330以及张力辊340。通过夹送辊310与线材2的第1侧面21抵接,芯轴320与线材2的第2侧面22抵接,从线圈母盘200送出的线材2被引导至由助卷辊330和张力辊340构成的弯曲成型部350。在弯曲成型部350中,线材2插入助卷辊330和张力辊340之间,助卷辊330按压于第1侧面21,张力辊340按压于第2侧面22,由此线材2弯曲成型为规定的曲率半径。由此,线材2将第1侧面21作为外周面、将第2侧面22作为内周面被塑性加工为环状。
[0076]
接着,在s120的切割工序中,通过对成型为环状的线材2进行切割,得到形成有接缝的环3。
[0077]
图6是表示通过切割工序得到的环3的外周面(第1侧面21)的图。在卷取工序中,通过由助卷辊330对线材2的第1侧面21施加作用的外力,凸出面s2的第1部位s21被向第1虚拟面f1侧压溃。由此,凸出面s2变形为线材2中图3所示的第1区域a1包括的部分移动到第2区域a2。其结果是,如图6所示,在环3的外周面形成向径向外侧凸出的角部c1。角部c1由相对于锥面s1成为了大致平坦的第1部位s21和相对于第2倾斜面s4成为了大致平坦的第2部位s22形成。角部c1的顶端(边缘)p2,在环3的外周面上位于径向最外侧。在卷取工序中通过助
卷辊330来压溃凸出面s2的第1部位s21,由此角部c1的表面由于压延效应而平滑化。需要说明的是,在角部c1中,代替第1部位s21相对于锥面s1成为大致平坦,也可以成为留有少量的凸状的形状。
[0078]
接着,在步骤s130的表面处理工序中,在环3的外周面形成硬质覆膜。通过在环3的外周面形成硬质覆膜,能降低第二道环1的外周面11上的摩擦力,提高耐磨耗性。作为硬质覆膜,例如,可以采用包括pvd处理膜、dlc膜以及镀铬处理膜中至少任意一层的构成。需要说明的是,“pvd(physical vapor deposition)处理膜”是指通过pvd法形成的覆膜。pvd法是通过使从靶射出的粒子附着于线材而在物质的表面形成膜的一种蒸镀法,也被称作物理气相生长。pvd法可以包括离子镀法、真空蒸镀法、离子束蒸镀法、溅射法、fcva(filtered cathodic vacuum arc)法等。此外,“dlc(diamond like carbon)膜”是指主要由烃、碳的同素异形体构成的无定形的硬质碳膜。此外,“镀铬处理膜”是指通过镀铬形成的覆膜。镀铬也被称作工业用镀铬。
[0079]
在实施方式1的表面处理工序中,利用pvd法对多个环同时进行成膜处理。图7是用于对表面处理工序进行说明的图。在图7中,方便起见,仅对多个环3中的一部分的环3进行了图示。如图7所示,利用例示为pvd法的蒸镀法的表面处理工序在环3的外周面(第1侧面21)和靶对置的状态下进行。此时,多个环3配置为在各自的中心轴一致的状态下在轴向堆叠。就是说,多个环3配置为成为同轴。该状态下,靶t1包含的材料蒸发高能粒子向环3射出,撞击环3的外周面,并附着。由此,在环3的外周面形成硬质覆膜。
[0080]
接着,在步骤s140的研磨工序中,通过研磨加工对形成了硬质覆膜的环3的表面进行研磨。具体而言,将环3插入具有与环3外径相等的内径的套筒内,在套筒内放入了磨粒的状态下使环3上下滑动。由此,环3的外周面(第1侧面21)在套筒的内周面滑动,环3的外周面被研磨。图8是表示研磨工序后的环3的外周面的图。在研磨工序中,环3的外周面中的向径向外侧凸出的角部c1的顶端p2率先与套筒的内周面接触。因此,角部c1的顶端p2被研磨,形成平坦的抵接面112。进行了如上步骤后,制造出如图1所示的第二道环1。
[0081]
[作用、效果]
[0082]
如上所述,实施方式1的线材2的第1侧面21包括连接锥面s1和第2倾斜面s4并且向第2方向侧凸出的凸出面s2。此外,凸出面s2由第1虚拟面f1划分为第1部位s21和第2部位,第1部位s21与锥面s1连接并相对于第1虚拟面f1向第2方向侧凸出,第2部位连接第1部位s21和第2倾斜面s4并且相对于第1虚拟面f1位于第2方向的相反侧。而且,第1部位s21弯曲为包括在第1侧面21中最位于第2方向侧的顶部p1并且相对于第1虚拟面f1隆起。
[0083]
当利用这样的线材2制造第二道环1时,在卷取工序中凸出面s2的第1部位s21被向第1虚拟面侧压溃,由此凸出面s2变形,能得到向径向外侧凸出的角部c1。然后,通过在研磨工序中对角部c1的顶端p2进行研磨,能得到平坦的抵接面112。
[0084]
在此,为得到良好的初始磨合性,优选抵接面112在整周上以均匀的抵接宽度形成。在此,“抵接宽度”是指第二道环1的轴向上的抵接面的宽度。需要说明的是,在图8中第二道环1作为环3而被参照,其抵接宽度以附图标记w1来表示。为了得到在整周上抵接宽度均匀的抵接面,需要延长研磨工序的研磨时间(研磨的时间的长度),但是研磨时间越长抵接宽度越增大。因此,在以相同研磨时间进行比较的情况下,角部所成的角度越小,就是说,角部越尖锐,越能得到小的抵接宽度。
[0085]
图9是表示比较例的线材4的图。在图9中示出了线材4卷取前的状态。比较例的线材4中,在应通过研磨工序形成抵接面的地方预先形成有角部c2。在此,通常,线材通过模具的拉拔加工而成型。因此,在比较例的线材4的角部c2形成有依赖于模具的形状的圆角。就是说,在通过模具的拉拔加工形成成为用于形成抵接面的研磨对象的角部c2的线材4中,超越模具的形状的限制使角部c2尖锐是很困难的。
[0086]
与此相对,实施方式1的线材2通过卷取工序形成成为用于形成抵接面的研磨对象的角部c1。因此,根据线材2,能不依赖模具的形状而使角部c1尖锐。图6中以θ
c
表示角部c1的角度。就是说,根据线材2,能形成小θ
c
。其结果是,根据线材2,关于抵接面112,能均匀地得到比比较例的线材4小的抵接宽度。
[0087]
此外,实施方式1的线材2在卷取工序中凸出面s2的第1部位s21被压溃而形成角部c1。因此,由于卷取工序的压延效应,能使角部c1的表面平滑化。由此,成为用于形成抵接面112的研磨对象的角部c1的表面被平滑化,因此能使抵接宽度更均匀。
[0088]
在此,实施方式1的线材2构成为,将由凸出面s2的第1部位s21和第1虚拟面f1围成的区域设为第1区域a1,由凸出面s2的第2部位s22、第1虚拟面f1以及第2虚拟面f2围成的区域设为第2区域a2时,在与线材2的延伸方向正交的剖面中第1区域a1的面积成为第2区域a2的面积以下。如上所述,在卷取工序中,线材2中的第1区域a1包括的部分移动到第2区域a2,由此形成角部c1。因此,根据实施方式1的线材2,能通过将第1区域a1的面积设为第2区域a2的面积以下,在第2区域a2内形成角部c1。其结果是,能尖锐地形成角部c1,能得到小的抵接宽度。
[0089]
此外,在实施方式1的第二道环1的制造方法中包括在通过切割工序得到的环3的外周面形成硬质覆膜的表面处理工序,其中硬质覆膜包括pvd处理膜、dlc膜以及镀铬处理膜中的至少任意一层。由此,能降低第二道环1的外周面11上的摩擦力,提高耐磨耗性。需要说明的是,也可以在第二道环1的外周面1不形成上述的覆膜。
[0090]
而且,实施方式1的线材2形成为,从凸出面s2的顶部p1到第3侧面23的第2方向侧的边缘e1为止的距离d1和从顶部p1到第4侧面24的第2方向侧的边缘e2为止的距离d2相等(参照图3)。然后,在表面处理工序中,将多个环3以各自的中心轴一致的方式,在轴向堆积的状态下进行。由此,如图7所示,在表面处理工序中在轴向上邻接的两个环3的相互对置的第3侧面23和第4侧面24在径向上不产生位差(无偏差)地重合。因此,能抑制在第3侧面23和第4侧面24上形成覆膜。这样的表面处理方法适合对多个环3形成pvd覆膜的情况。此外,也可以采用图7所示的表面处理方法以外的方法。
[0091]
此外,在利用通过使从靶射出的粒子附着在线材上而在物质的表面形成膜的蒸镀法(例如,pvd法)在环3的外周面形成覆膜的情况下,如图7所示,在环3的外周面(第1侧面21)和靶对置的状态下进行成膜处理。根据线材2,通过以随着朝向第1方向而缩宽的方式倾斜的第2倾斜面s4连接凸出面s2和第4侧面24,因此能易于使从靶射出的粒子附着在第2倾斜面s4的整个区域。其结果是,能在第2倾斜面s4上形成膜厚的均匀性高的覆膜。此外,也可以采用该蒸镀法以外的表面处理方法。
[0092]
在此,如图3所示,优选将第4侧面24向第2方向延伸而成的第3虚拟面f3与凸出面s2的顶部p1在第1方向上的平行距离设为h1,将第1虚拟面f1与顶部p1的与第1虚拟面f1垂直的距离设为h1,将在与线材2的延伸方向正交的剖面中与第1虚拟面f1平行的方向上的第
1部位s21的与第1虚拟面f1相交的宽度设为k1,将第2倾斜面s4的相对于第2方向的倾斜角度设为θ1时,满足以下的算式(1)~(4)的条件。
[0093]
0.01mm≤h1≤0.2mm (1)
[0094]
0.005mm≤h1≤0.02mm (2)
[0095]
0.05mm≤k1≤0.15mm (3)
[0096]
θ1≥3
°ꢀ
(4)
[0097]
通过构成这样的线材2,能在第二道环1上形成抵接宽度更小且均匀的抵接面。需要说明的是,优选上述θ1的上限值为25
°
。
[0098]
[抵接宽度评价]
[0099]
对通过上述的制造方法制造的第二道环的抵接宽度进行了评价。
[0100]
[实施例]
[0101]
作为实施例,对利用图2~图3所示的实施方式1的线材2制造的第二道环进行了评价。将锥面s1的相对于第1方向的倾斜角度θt设为了2.5
°
,将研磨工序中的研磨时间设为了50秒。
[0102]
[比较例]
[0103]
作为比较例,对利用图9所示的比较例的线材4制造的第二道环进行了评价。除将倾斜角度θt设为了3.2
°
以外,与实施例相同。
[0104]
[评价结果]
[0105]
在表1中示出实施例和比较例的抵接宽度的评价结果。在评价中,计算出了在第二道环的整周上的抵接宽度的平均值和偏差(标准偏差)。如表1所示,在实施例中,抵接宽度的平均值为0.048mm,偏差为0.033mm。在比较例中,抵接宽度的平均值为0.052mm,偏差为0.065mm。通过比较实施例和比较例中抵接宽度的平均值,能确认相比于比较例实施例能得到抵接宽度小的抵接面。此外,通过比较实施例和比较例中抵接宽度的偏差,能确认相比于比较例实施例能得到抵接宽度均匀的抵接面。
[0106]
[表1]
[0107][0108]
<实施方式2>
[0109]
图10是表示利用实施方式2的线材2a制造的第二道环1a的图。在图10中示出了与第二道环1a的周长方向正交的剖面。图11是表示实施方式2的线材2a的图。在图11中示出了与线材2a的延伸方向正交的剖面。以下,关于实施方式2,主要对其与实施方式1的不同点进行说明,对于与实施方式1相同的构成赋予同一附图标记,由此省略详细的说明。
[0110]
如图10所示,实施方式2的第二道环1a是在外周面侧的下部形成有台阶状(阶梯状)的切口的所谓的刮板环。第二道环1a的外周面11包括锥面111、抵接面112、第1倾斜面113以及切割面115。切割面115以在下表面14和抵接面112之间形成作为台阶状的切口的底
面切口15的方式,连接下表面14的外周边缘和抵接面112的下缘。由此,在安装了第二道环1a的内燃机100中,在外周面11的下部和气缸10之间,形成由底面切口15而成的空间。该空间成为储油槽,在活塞20下降第二道环1a将间隙pc1内的油刮落时,油被缓存下来,油圧的上升被抑制。其结果是,能得到良好的刮油性能。
[0111]
如图11所示,实施方式2的线材2a的第1侧面21包括锥面s1、凸出面s2、第1倾斜面s3以及切割面s5。切割面s5是在第二道环1a中形成切割面115的面。切割面s5位于比锥面s1靠第1方向侧,连接凸出面s2和第4侧面24。切割面s5包括与凸出面s2连接的第1底切割面s51以及连接第1底切割面s51和第4侧面24的第2底切割面s52。第1底切割面s51相当于本发明的“规定的面”。此外,在实施方式2中,将延长第1底切割面s51而与第1虚拟面f1交差的虚拟的面设为第2虚拟面f2。
[0112]
图12是用于对线材2a的第1侧面21进行说明的图。在实施方式2中,将第1底切割面s51的相对于第2方向的倾斜角度设为θ1。此外,将第2底切割面s52的相对于第2方向的倾斜角度设为θ2。第1底切割面s51以随着朝向第1方向而缩宽的方式倾斜。需要说明的是,第1底切割面s51可以沿第2方向延伸。就是说,θ1可以是0
°
。此外,第2底切割面s52沿第1方向延伸。就是说,θ2为90
°
。需要说明的是,第2底切割面s52也可以相对第1方向倾斜。但是,在切割面s5中,设定为θ2比θ1大。
[0113]
如图12所示,线材2a的凸出面s2与实施方式1相同地由第1虚拟面f1划分为第1部位s21和第2部位s22,第1部位s21与锥面s1连接并且相对于第1虚拟面f1向第2方向侧凸出,第2部位s22连接第1部位s21和第1底切割面s51并且相对于第1虚拟面f1位于第2方向的相反侧。然后,第1部位s21弯曲为包括在第1侧面21中最位于第2方向侧的顶部p1并且向第2方向侧成为凸状。
[0114]
实施方式2的第二道环1a也同实施方式1的第二道环1一样,可以通过在图4等说明的制造方法来制造。就是说,通过包含以下的制造方法来制造第二道环1a:卷取工序,将线材2a送出,通过对线材2a施加外力使线材2a成型为环状;切割工序,将成型为环状的线材2a切割得到环3a;表面处理工序,在环3a的外周面(第1侧面21)形成硬质覆膜;研磨工序,对环3a的表面进行研磨。
[0115]
图13是表示通过切割工序得到的环3a的外周面(第1侧面21)的图。在卷取工序中,通过对线材2a的第1侧面21施加作用的外力来将凸出面s2的第1部位s21向第1虚拟面f1侧压溃。在环3a的外周面上,形成向径向外侧凸出的角部c1。角部c1由相对于锥面s1成为了大致平坦的第1部位s21和相对于第1底切割面s51成为了大致平坦的第2部位s22形成。图14是表示研磨工序后的环3a的外周面的图。在研磨工序中,角部c1的顶端p2被研磨,形成平坦的抵接面112。
[0116]
在上述的实施方式2中也可以得到同实施方式1一样的效果。就是说,实施方式2的线材2a通过卷取工序形成成为用于形成抵接面的研磨对象的角部c1。由此,根据线材2a,能均匀地得到小的抵接宽度。此外,在实施方式2中也能由于卷取工序的压延效应,使角部c1的表面平滑化。其结果是,能使抵接宽度更均匀。
[0117]
此外,在实施方式2中也同实施方式1一样,能通过将第2区域a2的面积设为第1区域a1的面积以上,在第2区域a2内形成角部c1。其结果是,能尖锐地形成角部c1,能得到小的抵接宽度。此外,通过表面处理工序在环3a的外周面形成硬质覆膜,由此能降低第二道环1a
的外周面11上的摩擦力,提高耐磨耗性。此外,通过使从凸出面s2的顶部p1到第3侧面23的边缘e1为止的距离d1和从顶部p1到第4侧面24的边缘e2为止的距离d2相等,能抑制在表面处理工序中在第3侧面23和第4侧面24形成覆膜。此外,在实施方式2中,也能通过满足上述的算式(1)~(4)的条件,在第二道环1a上形成抵接宽度更小且均匀的抵接面。
[0118]
<实施方式3>
[0119]
图15是表示利用实施方式3的线材2b制造的第二道环1b的图。在图15中示出了与第二道环1b的周长方向正交的剖面。图16是表示实施方式3的线材2b的图。在图16中示出了与线材2b的延伸方向正交的剖面。上述的实施方式1中第2倾斜面s4相当于本发明的“规定的面”,实施方式2中切割面s5的第1底切割面s51相当于“规定的面”,但本发明的线材也可以不具有上述的第2倾斜面s4、切割面s5。图16所示的线材2b中,在第二道环1b中成为下表面14的第4侧面24相当于本发明的“规定的面”,由凸出面s2连接锥面s1和第4侧面24。
[0120]
<其他>
[0121]
以上对本发明的优选实施方式进行了说明,但可以尽可能地组合上述的各种方式。
[0122]
附图标记说明
[0123]
1:第二道环(活塞环的一例);2:线材;21:第1侧面;22:第2侧面;23:第3侧面;24:第4侧面(规定的面的一例);s1:锥面;s2:凸出面;s21:第1部位;s22:第2部位;s3:第1倾斜面;s4:第2倾斜面(规定的面的一例);s5:切割面;s51:第1底切割面(规定的面的一例);s52:第2底切割面;p1:顶部;f1:第1虚拟面;f2:第2虚拟面;f3:第3虚拟面;c1:角部;a1:第1区域;a2:第2区域。