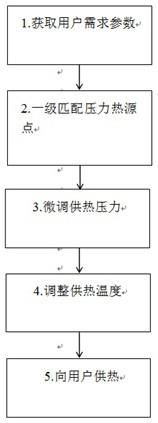
1.本发明涉及一种分级匹配的工业供热参数匹配方法,具体涉及工业供热范畴内能量梯级利用,属于工程热力学领域。
背景技术:2.热电联产是典型的能量梯级利用技术,电厂高品质的蒸汽用来生产高品质的电能,同时,根据用户需要,抽取合适的蒸汽供给工业或民用,实现的梯级利用,由于分配得当,热电联产机组一般具有较高的热效率,热效率可达到60%以上,远高于纯凝发电机组,是一种高效的能源利用方式。
3.按照热用户性质不同,供热分为民用供热和工业供热两类。民用供热一般供采暖使用,一般只要求供热温度和总热量,对供热压力要求不高,供热工质压力主要用来克服供热系统的流动阻力。工业供热和工业生产过程关联,除了需要热量外,还需要考虑供热工质的压力影响,因此,工业供热的热源点匹配,既要考虑“温度对口”,又要考虑压力的匹配。目前工业供热需求按照工艺要求不同,存在高参数、中参数和低参数供热,高参数供热:4.0mpa 等级,400℃ 以上,一般从电厂过热器出口抽汽;中参数供热:1. 0~2.5 mpa,300~400℃,一般从电厂一抽、冷再或热再段抽汽;低参数供热:0. 3~0. 6 mpa, 350℃以下,一般从电厂中低压连通管抽汽。目前工业供热技术中,一般要综合考虑温度和压力的需求,选择热源点时,要能同时满足压力和温度需求,一般采用压力和温度等级更高的抽汽点抽汽,再进行减温减压后供热用户使用,这就造成了“高能低用”的能源浪费,降低了热电联产的效率。
技术实现要素:4.本发明为了解决现有技术中存在的问题,提供一种提高热电联产能源利用效率的分级匹配的工业供热参数匹配方法。
5.为了达到上述目的,本发明提出的技术方案为:一种分级匹配的工业供热参数匹配方法,该方法将电厂供热系统中与用户需求压力参数匹配的点作为抽汽点进行抽汽,对从该抽汽点抽出的供热抽汽进行升温或降温以匹配用户需求温度参数后为用户供热。
6.对上述技术方案的进一步设计为:所述抽气点为最接近用户需求压力参数,且压力高于用户需求压力参数的热源点。
7.上述技术方案的一种优选方案为:采用蒸汽再热系统或烟气再热系统对从抽汽点抽出的供热抽汽进行升温。
8.所述蒸汽再热系统包括汽汽换热器和加热抽汽系统;所述供热抽汽进入汽汽换热器冷侧,所述加热抽汽系统从电厂供热系统中抽取温度高于供热抽汽温度的加热抽汽,加热抽汽进入汽汽换热器热侧,在汽汽换热器中完成热交换,提升供热抽汽温度。
9.所述蒸汽再热系统还包括减压器,所述供热抽汽进入减压器减压后进入汽汽换热器冷侧。
10.所述烟气再热系统包括供热烟气加热器,所述供热烟气加热器设置于电厂供热系统的锅炉内,所述供热抽汽进入供热烟气加热器与锅炉内烟气换热,提升供热抽汽温度。
11.所述烟气再热系统还包括减压器,所述供热抽汽进入减压器减压后进入供热烟气加热器。
12.上述技术方案的另一种优选方案为:采用喷水减温系统和热交换降温系统对从抽汽点抽出的供热抽汽进行降温。
13.所述热交换降温系统包括间壁式换热器,所述供热抽汽进入间壁式换热器热侧,抽取电厂供热系统中的工质进入间壁式换热器冷侧,在间壁式换热器中完成热交换,降低供热抽汽温度。
14.所述工业供热用户包括高参数用户和中参数用户,分别从电厂供热系统中选取与高参数用户和中参数用户的需求压力参数匹配的点作为高参数抽汽点和中参数抽汽点,对从高参数抽汽点和中参数抽汽点抽取的供热抽汽分别进入汽汽换热器进行换热,分别提升和降低两供热抽汽的温度。
15.本发明的有益效果为:本发明设计了提出了一种分级匹配的供热参数匹配方法,将供热热源参数匹配技术原则由“同时满足温度和压力要求”转变为“分级满足温度和压力要求”,减少了供热过程中源荷能级错配导致的能量损失,提高了能源利用效率。
16.本发明设计了压力匹配方法,减少供热过程中源荷匹配压力损失。本发明设计了温度匹配方法,减少温度匹配过程中的能级错配损失,提高系统效率;本发明从压力和温度两个维度去匹配,使匹配更加精确,能量利用更加合理。
附图说明
17.图1为本发明的分级匹配方法流程图;图2为本发明实施例中分级匹配方案一结构示意图;图3为本发明实施例中分级匹配方案二结构示意图;图4为一次性匹配方法流程图;图5为一次性匹配方案示意图。
18.图中:1为电厂锅炉;2为主蒸汽;3为汽轮机高压缸;4为冷再热蒸汽;5为热再蒸汽;6为汽轮机中压缸;7为热再供热抽汽,8为高参数供热抽汽,9为减压器,10为中参数供热蒸汽,11为中参数供热联箱,12为高参数供热联箱,13为高参数供热蒸汽,14为汽汽换热器,15为减温减压器,16为供热烟气加热器,17为高参数减温减压器,18为中参数减温减压器。
具体实施方式
19.下面结合附图以及具体实施例对本发明进行详细说明。
20.实施例一本实施例以亚临界300mw机组为例,其主要工况参数见表1,热用户需求参数见表2。
21.表1亚临界300mw机组主要参数
表2 热用户需求参数(供热联箱)如图1所示,本实施例的分级匹配的工业供热参数匹配方法,先获取用户的参数需求,以压力为第一级匹配参数,从电厂供热系统中寻找压力匹配的抽汽点;然后以此抽汽点蒸汽参数为基础,进行第二级参数匹配,即供热蒸汽温度匹配,通过升温或降温,使蒸汽参数和用户需求匹配。与一次性匹配相比,分级匹配能更加精确的实现热源和热负荷的匹配程度,提高系统能效。
22.本实施例中压力匹配技术原则是:按照用户需求,选择最接近用户压力参数,且压力高于用户参数的热源点。按照上述原则,综合系统、设备和用户需求特点,可以选择增设抽汽点、压力匹配器匹配抽汽等方式,选择抽汽位置。之所以第一级匹配压力,是因为在动力循环中,压力调节一般只能从高往低调,提升压力比较困难,目前采用如蒸汽压缩机之类的技术还很不成熟,且能耗较高,故压力匹配的主要采用的是降压技术,在匹配热源时,选择压力接近用户参数的供汽热源点,减少降压造成的能量损失,由于选择的抽汽点压力高于用户需求压力,因此在抽汽后需要对压力进行微调。
23.本实施例中为供热抽汽升温的方法分为蒸汽再热技术和烟气再热技术。蒸汽再热技术是利用高温蒸汽,加热供热蒸汽,提升蒸汽温度;烟气再热技术是利用锅炉侧烟气温度,加热供热蒸汽,使之匹配供热用户需求。为供热抽汽降温的方法分为喷水减温技术和热交换降温技术,喷水减温技术是用低温的冷水喷入蒸汽中,降低蒸汽的温度;热交换降温技术是采用间壁式换热技术,将蒸汽中多余的热量交换给系统的工质,同时降低供热蒸汽温度,使之匹配供热需求。采用热交换技术能够提高系统的能量利用效率,优于喷水减温技术。
24.如图2所示,本实施例中分级匹配技术方案包括高参数供热系统、中参数供热系统和温度匹配系统。
25.本实施例系统中电厂锅炉1的主蒸汽2进入汽轮机高压缸3,冷再热蒸汽4从汽轮机高压缸3回到电厂锅炉1,然后经热再蒸汽5进入汽轮机中压缸6。
26.高参数供热系统根据高参数用于需求在汽轮机高压缸3上选择抽汽点抽取高参数供热抽汽8,高参数供热抽汽8经减压器9减压进入汽汽换热器14冷侧,在汽汽换热器14升温后进入高参数供热联箱12,最后成为高参数供热蒸汽13为高参数用户供热。
27.中参数供热根据中参数用户需求在选择热再蒸汽5为抽汽点抽取热再供热抽汽7,热再供热抽汽7进入汽汽换热器14热侧,在汽汽换热器14降温后进入减温减压器15进行压
力和温度的微调,然后进入中参数供热联箱11,最后成为中参数供热蒸汽10,为中参数用户供热。
28.温度匹配系统为汽汽换热器14用于高参数供热抽汽8和热再供热抽汽7的换热。
29.本实施例中高参数供热抽汽8压力为4.9mpa,温度为359.9℃,经过减压器9减压,至高参数供热联箱12压力为4.1mpa,温度为352.67℃,压力降低0.8mpa;热再供热抽汽7压力为3.52mpa,温度为538℃,经过汽汽换热器14与高参数供热抽汽8进行热交换,提升高参数供热蒸汽至410℃,热再供热蒸汽降至362℃,再进入中参数供热联箱11,经过减温减压器15微调至用户压力为2.5mpa,温度为350℃,压力降低1.02mpa,降温调节温度为12℃。由上述调节过程可以看出,本实施例方案抽汽热源参数压力接近用户参数,温度调节采用供热蒸汽之间的换热,代替大部分喷水降温方式,经过上述技术措施,大大降低了高参数和中参数供热大压力降和大温降的调节方式,减少了系统的减温减压损失,提高了系统经济性。
30.实施例二本实施例中分级匹配方案二如图3所示,包括高参数供热系统和烟气温度匹配系统。
31.高参数供热系统根据高参数用户需求,在汽轮机高压缸3上选择抽汽点抽取高参数供热抽汽8,高参数供热抽汽8经减压器9减压后,进入供热烟气加热器16,供热烟气加热器16设置于电厂锅炉1内,换热后的高参数供热抽汽8进入高参数供热联箱12,最后成为高参数供热蒸汽13为高参数用户供热。
32.烟气温度系统包括供热烟气加热器16,用于高参数供热抽汽8与锅炉内烟气的换热。
33.本实施例中方案二主要是针对仅有高参数供热,而无中参数供热的场景。高参数供热抽汽8压力为4.9mpa,温度为359.9℃,经过减压器9,将压力调整为4.1mpa,温度为352.67℃,压力降低0.8mpa;高参数供热抽汽进入供热烟气加热器2,将温度提升至供热所需蒸汽温度410℃,进入高参数供热联箱12。由上述调节过程可以看出,本方案抽汽热源参数压力接近用户参数,温度调节采用烟气加热方式,代替一次性匹配的减温减压技术,经过上述技术措施,大大降低了高参数供热大压力降和大温降的调节方式,减少了系统的减温减压损失,提高了系统经济性。
34.上述两实施例提出的“分级匹配,梯级利用”的供热方法,设计了分级匹配两种技术方案,采用蒸汽再热技术和烟气再热技术调节供热蒸汽温度,代替一次性匹配技术方案采用的减温减压调节技术,降低了供热系统的能量损失。通过上述技术实现能量的梯级利用,提高能源利用效率。
35.对比例如图4所示,现有技术中一次性匹配热源参数方法为,根据用户的需求参数,从压力和温度要求去匹配供热热源,匹配原则是温度和压力均不低于用户所需参数,然后采用降压技术,将供热蒸汽压力调节到用户需求的压力;采用减温技术,将供热蒸汽温度调节到用户需求的温度。从上述的匹配思路来看,在选择热源时,要同时满足温度和压力要求,且重点是满足二者中参数要求较高的参数,当满足这个要求时,温度和压力中有一个参数要高于热用户需求,需要对其进行降参数(减温和降压)处理,这就造成了能级不匹配的浪费现象。
36.按照一次性匹配技术路线,如果满足高参数用户的供热需求,系统抽汽热源点只能为主蒸汽;中参数供热抽汽热源可为主蒸汽、一抽蒸汽和热再蒸汽。综合考虑机组锅炉和汽机的设备特性,系统高参数供热热源点选用主蒸汽,中参数供热热源点选用热再,供热方案见附图5所示。
37.本对比例的一次性匹配技术方案,包括高参数供热系统和中参数供热系统。
38.高参数供热系统在主蒸汽2上抽取高参数供热抽汽8,高参数供热抽汽8经高参数减温减压器17减温减压后进入高参数供热联箱12,形成高参数供热蒸汽13。
39.中参数供热在热再蒸汽5上抽取中参数供热抽汽7,中参数供热抽汽7经中参数减温减压器18减温减压后进入中参数供热联箱11,形成中参数供热蒸汽10。
40.本实施例中高参数供热热源点蒸汽压力为16.67mpa,温度为538℃,经过减温减压,至联箱压力为4.0mpa,温度为410℃,压力降低12.67mpa,温度降低128℃;中参数供热热源点蒸汽压力为3.52mpa,温度为538℃,经过减温减压,至联箱压力为2.5mpa,温度为350℃,压力降低1.02mpa,温度降低188℃。由于一次性匹配方案为了同时匹配压力和温度,需要选择参数较高的蒸汽热源点,在调节压力和温度时,采用降温和降压的措施,系统不可逆损失较大,系统经济性较差。
41.本发明的技术方案不局限于上述各实施例,凡采用等同替换方式得到的技术方案均落在本发明要求保护的范围内。