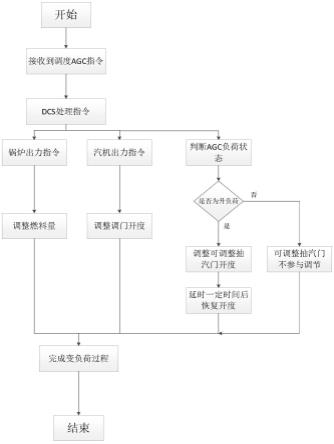
一种基于末级加热器可调整抽汽的agc提速控制方法
技术领域
1.本发明涉及火力发电技术领域,更确切地说,它涉及一种基于末级加热器可调整抽汽的agc提速控制方法。
背景技术:2.为保证电网供电质量的要求,电网调度机构对并网运行的火力发电汽轮机组实行自动发电控制(automatic generation control,agc),同时对火电机组的agc指令响应速率、响应时间和控制精度等指标提出了控制要求。
3.机组的各系统由分散控制系统(distributed control system,dcs)进行实时控制。dcs将接收到的agc负荷指令进行限幅与限速处理,生成机组负荷指令与主汽压力设定值,再将其与机组实时功率与实时压力比较,调节锅炉燃料量、送风量与给水流量,以此改变锅炉的出力,以满足汽轮机的做功需求;同时,dcs对汽轮机调速汽门开度进行控制,改变汽轮机出力,进而调整机组的发电功率。dcs通过协调锅炉与汽轮机间的能量供需平衡,实时调整机组出力,实现对agc指令的响应。高压加热器是火电机组为了提高汽轮机热效率的抽汽回热的换热器,利用从汽轮机高中压缸抽出来的高温高压蒸汽去加热从给水泵升压后至锅炉这一段给水的温度,末级的高压加热器正是从高压缸中进行抽汽,根据机组技术型号的差别,末级加热器一般为0号高压加热器或1号高压加热器。
4.为了满足电网对于机组不断提升的负荷响应速率要求,目前的火电机组普遍采用以锅炉跟随为基础的负荷控制策略,以发挥汽轮机的快速负荷调节作用。但由于锅炉具有大惯性、大时延的设备特性,变负荷过程中锅炉出力变化速率往往跟不上汽轮机出力的变化需求。特别是在变负荷初期,汽轮机的负荷快速调节与锅炉侧出力变化迟缓的矛盾尤为突出,极易造成整个变负荷过程中机、炉能量供需的不平衡,导致锅炉蓄热被大量消耗,主汽压力偏差加大,影响机组整体的agc运行性能。
技术实现要素:5.本发明的目的是克服现有技术中的不足,提供了一种基于末级加热器可调整抽汽的agc提速控制方法。
6.第一方面,提供了一种基于末级加热器可调整抽汽的agc提速控制方法,包括:
7.s1、指令接收装置接收调度机构下发的自动发电控制agc指令,并将所述agc指令发送至分散控制系统dcs;dcs对所述agc指令进行处理,并根据当前的机组负荷指令及运行需求,计算生成机组的锅炉出力指令与汽轮机出力指令,下发给相应设备调整锅炉燃料量与汽轮机调门开度;
8.s2、dcs对所述agc指令的状态进行判断,所述agc指令的状态分为“升负荷”或“降负荷”;
9.s3、dcs根据所述agc指令的状态判断结果,确定是否需要可调整抽汽门参与调节,并根据控制逻辑对其开度进行调整;
10.s4、在锅炉出力上升后,逐步恢复可调整抽汽门开度至正常运行状态。
11.作为优选,s3中,所述agc指令的状态为“升负荷”时,对可调整抽汽门的开度进行调整;所述agc指令的状态为“降负荷”时,可调整抽汽门不参与调节。
12.作为优选,s3中,对于配备0号高压加热器抽汽进行agc提速控制的机组,所述可调整抽汽门的控制逻辑包括:
13.s301、在90%机组额定负荷pe以上负荷段,0号高压加热器不投入运行,所述可调整抽汽门处于关闭状态;
14.s302、在75%pe至90%pe负荷段,可调整抽汽门保留有第一开度,所述agc指令的状态为“升负荷”时,dcs控制可调整抽汽门至全关位;
15.s303、在75%pe以下负荷段,可调整抽汽门保持全开,所述agc指令的状态为“升负荷”时,dcs控制可调整抽汽门至第二开度。
16.作为优选,s303中,机组设计有超驰保护逻辑,当给水温度或排烟温度低于设定阈值时,超驰开启可调整抽汽门,所述可调整抽汽门放弃参与调节。
17.作为优选,s3中,对于采用1号高压加热器抽汽进行agc提速控制的机组,可调整抽汽门在机组稳定工况下均保持全开,所述agc指令的状态为“升负荷”时,dcs控制可调整抽汽门至第二开度。
18.作为优选,s3中,可抽汽调整门单次的agc提速控制时间为60s~90s。
19.本发明的有益效果是:本发明能够在响应agc过程中调整末端加热器的抽汽量,利用抽汽蓄热在变负荷初期补偿由于锅炉响应延迟带来的机、炉能量供需不平衡的问题,辅助汽轮机的出力提升,稳定主汽压力,有效提高机组变负荷速率及对agc指令的响应能力。
附图说明
20.图1为本技术提供的agc指令处理及变负荷状态判断逻辑示意图;
21.图2为本技术提供的一种基于末级加热器可调整抽汽的agc提速控制方法的流程图;
22.图3为本技术提供的0号高加可调整抽汽门开度控制逻辑示意图;
23.图4为本技术提供的1号高加可调整抽汽门开度控制逻辑示意图;
24.图5为本技术提供的变负荷过程中指令及煤量变化曲线示意图;
25.图6为本技术提供的变负荷过程中汽压变化仿真示意图。
具体实施方式
26.下面结合实施例对本发明做进一步描述。下述实施例的说明只是用于帮助理解本发明。应当指出,对于本技术领域的普通人员来说,在不脱离本发明原理的前提下,还可以对本发明进行若干修饰,这些改进和修饰也落入本发明权利要求的保护范围内。
27.实施例1:
28.高压加热器通过管道及可调整抽汽门与汽轮机高压缸相连。正常运行过程中,进入汽轮机1做功的部分蒸汽通过该管道进入高压加热器3加热给水,以提高机组运行的经济性。dcs4通过专用设备接收电网agc指令,经计算后调整汽轮机调门开度与锅炉出力,同时根据变负荷需要调整可调整抽汽门的开度。
29.实施例2:
30.机组的动态模型可描述如下:
[0031][0032][0033][0034][0035]
其中,dq为锅炉蒸汽流量,m为燃料量,d
t
为汽轮机蒸汽流量,p
t
为主汽压力,μ
t
为汽轮机调门开度,pd为汽包压力或分离器出口压力,n为机组输出功率,t为惯性环节传递函数中的时间常数,k(km、k1、k2、k3)为对应函数关系式的增益系数,s为传递函数中的复数自变量,τ为实数时间,c
t
为蓄热系数。
[0036]
由数学模型可见,由于从燃料量变化
△
m到实际蒸汽流量变化
△dq
的过程为一惯性滞后环节,变负荷的初期蒸汽流量无法迅速增加,为了确保机组功率n与设定功率匹配,就必须调整调门开度μ
t
,进而影响汽轮机蒸汽流量d
t
。由于锅炉主汽流量dq的滞后及惯性特性,在变负荷初期就势必出现汽轮机与锅炉的蒸汽流量不平衡的情况,使得锅炉出口压力pd和主汽压力p
t
发生波动,锅炉蓄热被大量消耗,汽轮机为确保功率就必须进一步开大调门μ
t
,从而使得参数波动进一步加剧,影响后续机组整体的变负荷能力和agc运行性能。该情况将持续,直至锅炉蒸汽流量dq实际变化,并与汽轮机蒸汽流量重新建立平衡后,才能稳定参数并恢复机组的调节能力。
[0037]
为了减小变负荷过程中,特别是变负荷初期机、炉出力不平衡导致的机组汽压偏差大、负荷响应迟滞,提高火力发电机组对电网agc指令的响应能力,本发明提出一种基于末级加热器可调整抽汽的agc提速控制方法。本发明利用末级加热器的可调整抽汽门,在变负荷时通过改变末级加热器抽汽量,调整部分高参数抽汽返回汽轮机做功,在变负荷初期补充汽轮机做功所需能量,减少对锅炉蓄热的消耗。在锅炉实际出力增加后,再逐步恢复抽汽量,确保变负荷期间机炉间能量供给的平衡。采用该方法能够避免变负荷过程中机炉出力不平衡导致的汽压偏差,有效提升机组的变负荷速率和对agc指令的响应能力。
[0038]
从机组的数学模型可知,在变负荷初期通过控制末级加热器的抽汽,相当于直接为汽轮机功率提升提供额外的能量补充,为汽轮机增加了
△
n的输出功率。对此,汽轮机为控制机组的功率至设定值,需要调整汽机调门μ
t
,进而减小汽轮机的进汽流量d
t
的变化幅度。因此,在变负荷初期锅炉蒸汽流量dq可以与汽轮机的进汽流量d
t
相匹配,锅炉的蓄热消耗较少,可确保主汽压力p
t
与锅炉出口压力pd的相对稳定。待经过锅炉响应的惯性与滞后过程,锅炉蒸汽流量dq实际变化后,再恢复抽汽至常规运行状态。此时dq与d
t
的供需关系达到平衡,汽轮机再通过调整调门开度μ
t
进行负荷调节就可确保压力的稳定。从整个过程看,通过利用抽汽调整在变负荷初期为汽轮机提供额外能量支持,能够避免过渡消耗锅炉蓄热而使得主汽压力出现较大偏差,也就确保了机组agc的调节性能。
[0039]
具体地,本发明提供了一种基于末级加热器可调整抽汽的agc提速控制方法,能够用于燃煤发电机组的agc指令响应过程。本发明将机组末级加热器的抽汽阀门(1级抽汽或0
级抽汽)升级改造为调节门,在变负荷初期通过改变抽汽量的方式,调整部分高参数抽汽返回汽轮机做功,在发挥汽轮机快速负荷响应优势的同时,不过多消耗锅炉的蓄热,确保主汽压力参数的稳定,提高机组的agc响应能力,如图2所示,本方法包括:
[0040]
s1、指令接收装置接收调度机构下发的自动发电控制agc指令,并将agc指令发送至分散控制系统dcs;dcs对agc指令进行处理,并根据当前的机组负荷指令及运行需求,计算生成机组的锅炉出力(主控)指令与汽轮机出力(主控)指令,下发给相应设备调整锅炉燃料量与汽轮机调门开度。
[0041]
s2、dcs对agc指令的状态进行判断,agc指令的状态分为“升负荷”或“降负荷”。
[0042]
s3、dcs根据agc指令的状态判断结果,确定是否需要可调整抽汽门参与调节,并根据控制逻辑对其开度进行调整,实现对agc指令的辅助响应。
[0043]
s4、在锅炉出力上升后,逐步恢复可调整抽汽门开度至正常运行状态,完成机组agc提速辅助调节过程。示例地,在完成agc提速控制后,可调整抽汽门的开度将以一定速率恢复至原开度,以防止调节速率过快影响机组实际负荷。
[0044]
s3中,agc指令的状态为“升负荷”时,对可调整抽汽门的开度进行调整;agc指令的状态为“降负荷”时,可调整抽汽门不参与调节。这是由于高压加热器的可调整抽汽门在正常运行过程中可能保持全开,仅能够通过减小开度实现对agc“升负荷”指令的响应,因此需要进行变负荷方向的判断。具体判断逻辑如图1所示,其中,“≯≮”表示agc指令限幅功能,“v≯”表示agc指令限速功能,“+
‑”
表示减法功能,“h”表示高限判断,“l”表示低限判断。
[0045]
需要说明的是,本发明将结合多种测量数据及逻辑运算进行判断在机组运行过程中对可调整抽汽门的开度进行控制,其具体控制策略如下:
[0046]
在agc指令稳定、机组未变负荷时,dcs控制将调整抽汽门至预定位置,确保机组运行的经济性;在出现agc指令“升负荷”时,dcs结合机组的运行工况和安全边界情况,控制可调整抽汽门开度至某一位置。
[0047]
示例地,s3中,对于配备0号高压加热器抽汽进行agc提速控制的机组,可调整抽汽门的控制逻辑包括:
[0048]
s301、在90%机组额定负荷pe以上负荷段,由于给水温度较高,日常运行中为防止省煤器沸腾,0号高压加热器不投入运行,故无法参与agc提速控制,所述可调整抽汽门处于关闭状态。
[0049]
s302、在75%pe至90%pe负荷段,给水温度相对较高,机组运行过程中可调整抽汽门控制抽汽压力,可调整抽汽门保留有一定开度(如第一开度),agc指令的状态为“升负荷”时,dcs控制可调整抽汽门至全关位,以充分发挥调整抽汽量对机组负荷响应的提升作用。
[0050]
s303、在75%pe以下负荷段,锅炉排烟温度与给水温度随之下降。特别是进入低负荷段后,给水温度过低将威胁脱硝环保设施的正常投运,可调整抽汽门保持全开,agc指令的状态为“升负荷”时,dcs控制可调整抽汽门至某一开度(如第二开度)。其中,第二开度由机组负荷指令根据函数f(x)对应生成,防止抽汽量过小导致给水温度过低。
[0051]
此外,s303中,机组设计有超驰保护逻辑,当给水温度或排烟温度低于设定阈值时,超驰开启可调整抽汽门,可调整抽汽门放弃参与调节,确保环保运行安全。控制策略示意图如图3所示,其中,a表示机组升负荷,b表示加热器压力控制指令,c表示机组负荷,d表示给水温度,e表示75%pe<机组负荷<90%pe,f表示机组负荷>90pe%,g表示0号高压加
热器可调整抽汽门开度指令,h表示90s脉冲,f(x)表示负荷-开度设定曲线,l表示判断给水温度是否低于设定阈值;a代表常数功能块,0%代表对应常数功能块中设置常数0,100%代表对应常数功能块中设置常数100,t代表切换功能块,虚线代表开关量信号,实线代表模拟量信号,当切换功能块的开关量输入信号为0时,选择n端输入作为输出,反之开关量输入信号为1时,选择y端输入作为输出。
[0052]
s3中,对于采用1号高压加热器抽汽进行agc提速控制的机组,可调整抽汽门在机组稳定工况下均保持全开,agc指令的状态为“升负荷”时,其开度控制策略可与75%pe以下负荷段采用0号高加抽汽进行agc提速控制一致,比如,dcs控制可调整抽汽门至第二开度。控制策略示意图如图4所示,其中a表示机组升负荷,c表示机组负荷,d表示给水温度,h表示90s脉冲,f(x)表示负荷-开度设定曲线,l表示判断给水温度是否低于设定阈值,i表示1号高压加热器可调整汽门开度指令。
[0053]
需要说明的是,以上采用可调整抽汽门进行agc提速控制的时间长度应当能够补偿锅炉出力上升的滞后过程,以达到平衡汽机与锅炉能量供给平衡的目的。但过长时间的减少抽汽量可能影响给水温度,进而影响机组环保设备运行安全和机组运行经济性,因此应当限制可抽汽调整门单次的agc提速控制时间。一般设置为60s~90s,具体时间应根据锅炉响应速率和加热器抽汽量等参数加以区分。
[0054]
实施例3:
[0055]
为了满足电网对于机组不断提升的负荷响应速率要求,目前的火电机组负荷控制策略普遍以锅炉跟随为基础,以发挥汽轮机的快速负荷调节作用。但由于锅炉具有大惯性、大时延的设备特性,极易造成整个变负荷过程中机、炉能量供需的不平衡,导致锅炉蓄热被大量消耗,主汽压力偏差加大,影响机组整体agc运行性能。对此,本发明在变负荷初期利用可调整抽汽门调节末级加热器的抽汽量,使部分高参数蒸汽返回汽轮机做功,平衡机炉间的能量供需关系,提升机组负荷响应速度和agc指令响应能力。下面结合示例说明本发明的工作原理。
[0056]
某660mw超临界火电机组,配置有0号高压加热器,采用可调整抽汽门进行抽汽量控制,在正常运行时对给水进行加热。为提升机组的agc响应能力,于机组dcs中采用本发明控制方法调整0号高加的可调整抽汽调整门开度。某日机组于495mw负荷运行,0号高加投入,抽汽量约为64.6t/h。某时刻起,机组接收到agc指令升负荷50mw,变负荷速率为12mw/min。dcs采用本发明所提出的控制策略对抽汽调整门进行控制,同时调整汽轮机与锅炉的出力,完成机组对agc指令的响应。为具体说明本发明的效果,对该agc响应工况进行了数值仿真。在该过程中,机组负荷、主汽压力、抽汽调整门指令变化如图5所示,其中,曲线1表示agc指令,曲线2表示实际负荷,曲线3表示限速后负荷指令,曲线4表示主汽压力,曲线5表示主汽压设定值,曲线6表示可调整抽汽门开度,曲线7表示抽汽量影响负荷。
[0057]
本仿真对机组运行情况进行了简化处理,仅表征采用本方法后的主要参数的变化趋势。如图5所示,机组在t0时刻收到agc指令后,dcs根据相关逻辑对指令进行了处理,生成限幅限速后agc指令以及主汽压力设定指令;同时判断得到升负荷信号,将0号高加的可调整抽汽门开度由75%关闭至0%。根据理论计算,改变0号高加抽汽量对机组负荷产生约17.3mw的影响。在t1时刻,抽汽调整门参与负荷调节时间达到预定值(约90s),其开度恢复至初始值。后续随着负荷指令的上升和锅炉出力的增加,机组至t2时刻变负荷过程结束。由
图可见,在变负荷初期由于可调整抽汽门的参与,机组负荷与实际主汽压力的响应均较为迅速。特别是在变负荷初期,通过对高参数抽汽的调整,为汽轮机出力增加提供了额外支持,减少了对锅炉蓄热的消耗,使在整体变负荷过程中的主汽压力参数较为稳定。为说明方法的有效性,通过数值仿真,对比了采用传统控制策略与采用本发明的控制效果,其主要区别体现在主蒸汽压力变化趋势上,具体情况如图6所示,图6中,曲线1表示主汽压力设定值,曲线2表示本方法主汽压力,曲线2表示传统控制方法主汽压力。
[0058]
除了采用调整抽汽辅助响应agc指令外,两次仿真过程中机组的控制参数完全一致。从图中可见,由于在变负荷初期(t0-t1时间段)调整部分抽汽进入汽轮机做功,补偿了部分锅炉与汽机间的能量供需缺口,锅炉蓄热的消耗较少,变负荷过程中的整体压力波动也较小。而传统控制方法在变负荷初期消耗了过多的锅炉蓄热,压力下降过多;同时为了补充损失锅炉蓄热,锅炉主控变化剧烈,导致后期过调的情况较为严重,整体的压力波动较为严重。仿真结果表明,采用传统控制方法变负荷过程中的主汽压力最大偏差超过0.6mpa,本发明在变负荷过程中可将汽压偏差控制在0.4mpa。如在采用本发明提供的方法的基础上进一步进行控制参数的优化,则可取得更好的调节效果与agc响应能力。因此,相对于传统控制方法,采用本发明提供的方法可有效辅助变负荷初期的汽轮机出力增加,使得机组的变负荷能力得到提升,并稳定变负荷过程中的参数。
[0059]
综上所述,本发明能够在响应agc过程中调整末端加热器的抽汽量,利用抽汽蓄热在变负荷初期补偿由于锅炉响应延迟带来的机、炉能量供需不平衡的问题,辅助汽轮机的出力提升,稳定主汽压力,有效提高机组变负荷速率及对agc指令的响应能力。