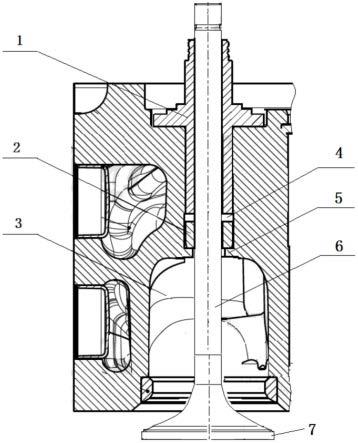
1.本实用新型属于发动机进气技术领域,具体是一种气门组件安装结构、发动机及车辆。
背景技术:2.目前发动机行业内普遍采用整体式铸铁材质气门导管,具有结构简单,便于加工生产的特定。
3.参见图1所示,发动机中采用的与气门杆相适配的气门导管普遍都是整段式,该气门导管8本体内壁设有多孔耐高温嵌件9,且所述多孔耐高温嵌件9与所述气门导管8本体形成与所述气门杆间隙配合的内圆柱表面。其中,多孔耐高温嵌件的气孔能够储存大量机油,使用过程中随着气门上下往复运动,机油可在气门杆和气门导管之间形成合适的油膜,从而保证了润滑性能。但是,这种整体式铸铁材质气门导管发动机运行过程中气门在气门导管内上下运行,因为铸铁材质的气门导管耐磨性低于钢材质的气门,且气门导管底部,也就是靠近气门盘的一端易受高温影响,冷却、润滑普遍不是非常良好,很容易造成气门导管底部偏磨问题,进而造成气门晃动幅度大,其气门关闭不严等一系列问题。
技术实现要素:4.为了解决现有技术中存在的技术问题,本实用新型提供了一种气门组件安装结构、发动机及车辆。该安装结构将传统的整体式铸铁材质气门导管设计为分段式气门导管,相邻的两段之间设有间隙,该间隙内可以储存润滑油,这样提高冷却润滑效果,强化气门导管耐磨性。
5.本实用新型提供了一种气门组件安装结构,包括气门座上的气门孔,气门孔内设有气门杆和气门导管,气门杆插在气门导管内,气门杆的端部连接气门盘,其特征在于,气门导管至少分成两段,其中靠近气门盘的一段与相邻的一段之间设有间隙,该间隙内设有润滑油。
6.进一步地,其中气门孔靠近气缸盖的一端形成缩口端用于支撑气门导管,所述缩口端的内径位于气门导管的外径和内径之间。
7.进一步地,气门杆与气门导管过盈配合。
8.进一步地,其中气门导管中在远离气门盘的一端延伸至气门孔外部形成弹簧固定座,弹簧固定座为多台阶设置。
9.进一步地,弹簧固定座的顶部延伸形成导向柱。
10.进一步地,气门导管分成两段,靠近气门盘的一段的长度小于另一段的长度。
11.进一步地,气门导管中相邻两段之间的间隙小于单段的长度。
12.进一步地,气门导管中靠近气门盘的一段选用耐磨、耐高温材料。
13.本实用新型还提供了一种发动机,该发动机包括上述任一项所述的一种气门组件安装结构。
14.本实用新型还提供了一种车辆,该车辆包括上述所述的一种发动机。
15.本实用新型的有益效果:
16.本实用新型提供的气门组件安装结构将传统的整体式铸铁材质气门导管设计为分段式气门导管,安装气门孔内的气门导管分成至少两段,其中靠近气门盘的一段与相邻的一段之间设有间隙,该间隙内可以储存润滑油,这样气门杆在导管内移动的时候,通过该间隙内的润滑油可以对靠近气门盘的气门导管进行充分润滑,从而减少其磨损情况。
附图说明
17.图1为本实用新型实施例提供的现有气门导管的整体结构图;
18.图2为本实用新型实施例提供的气门组件安装结构的整体结构图。
19.图中:1、上段气门导管,2、下段气门导管,3、气缸盖,4、间隙,5、缩口端,6、气门杆,7、气门盘,8、气门导管,9、多孔耐高温嵌件。
具体实施方式
20.参见图2所示,本实用新型提供了一种气门组件安装结构,该安装结构包括气门座,其中气门座上设有气门孔,气门孔的一端连接气缸盖3,在气门孔内安装有气门杆6和气门导管8,气门导管8的端部连接气门盘7,气门导管8开设有轴向贯通的通孔,其中气门导管用于供气门杆6可活动地插设。
21.在气门孔内,气门导管主要由上段气门导管1和下段气门导管2组成,其中上段气门导管1与下段气门导管2的厚度相同,其中上段气门导管1与下段气门导管2之间设有一定的间隙,该间隙内用于存储一定的润滑油。
22.所以,本实施例提供的气门组件安装结构将安装气门孔内的气门导管分成至少两端,其中靠近气门盘7的一段与相邻的一段之间设有间隙,该间隙内可以储存润滑油,这样气门杆6在导管内移动的时候,通过该间隙内的润滑油可以对靠近气门盘7的气门导管进行润滑,从而减少其磨损情况。
23.具体地,参见图2所示,在本实施例中国的气门导管分成上段气门导管1和下段气门导管2,其中上段气门导管1和下段气门导管2之间设有间隙,这样冷却润滑机油通过安装在上段气门导管1端部的气门杆衬套控制流量后进入气门孔,因上段气门导管1与下段气门导管2安装后存在间隙,机油会在间隙处积留,起到隔热、冷却并润滑下端气门导管的作用。
24.所述上段气门导管1的整体长度要远远大于下段气门导管2的长度,这样保证润滑油能够充分润滑下段气门导管2。
25.其中上段气门导管1与下段气门导管2支架之间的间隙高度要小于下段气门导管2的高度。
26.当然,本实施例提供的气门导管不仅仅限于本实施例中的上段气门导管1和下段气门导管2中的两个,也可以多于两个,考虑到通常气门导管中靠近气门盘7的部分经常磨损严重,所以气门导管中靠近气门盘7的一端可以多分成几段,其中相邻的两段之间设有间隙,每个间隙内都存储有一定的润滑油,这样对分成的每段进行润滑。
27.参见图1所示,在本实施中气门孔靠近气门盘7的一端呈缩口状,从而形成缩口端5,用于支撑气门导管避免气门导管滑出,一般的气门导管的端部是直接伸出,而本技术中
的气门导管靠近气门盘7的一端不伸出气门孔。
28.该气门管缩口状的端部内径位于气门导管8的外径和内径之间,这样在发动机运行的过程中,气门杆6在气门导管内上下运动的时候,气门口的缩口端能够有效减少气道内热气与下段气门导管2的接触,从而降低气道内热气与下段气门导管2的接触,从而降低气门导管的受热。
29.参见图1所示,在本实施例中的上段气门导管1的顶部伸出于气门孔的外部形成弹簧底座,该弹簧座的呈多台阶设置,且弹簧座的中心形成一个导向柱,这样可以将压缩弹簧安装在盖弹簧底座上,通过弹簧底座的台阶对弹簧进行定位,通过该导向柱进行导向,这样可以起到安装限位作用。
30.在本实施例中的气门导管与气门孔之间通过过盈配合,这样可以保证两者连接的稳定性。
31.本实施例中的气门导管应当选用耐温、耐磨材料,同时配合气门导管结构及安装结构,能够加强气门导管的冷却与润滑,大幅度降低气门杆6与下段气门导管2的磨损,解决了气门导管偏磨造成气门关闭不严等问题。
32.本实用新型实施例还提供了一种发动机,该发动机包括气缸座,该气缸座上设有上述所述的一种气门组件安装结构,由于该发动机采用了上述所有实施例的全部技术方案,因此至少具有上述所有实施例的全部技术方案所带来的所有有益效果,在此不再一一赘述。
33.本实用新型实施例还提供了一种车辆,该车辆包括上述所述的一种发动机。
34.上述虽然结合附图对本实用新型的具体实施方式进行了描述,但并非对本实用新型保护范围的限制,所属领域技术人员应该明白,在本实用新型的技术方案的基础上,本领域技术人员不需要付出创造性劳动即可做出的各种修改或变形仍在本实用新型的保护范围以内。