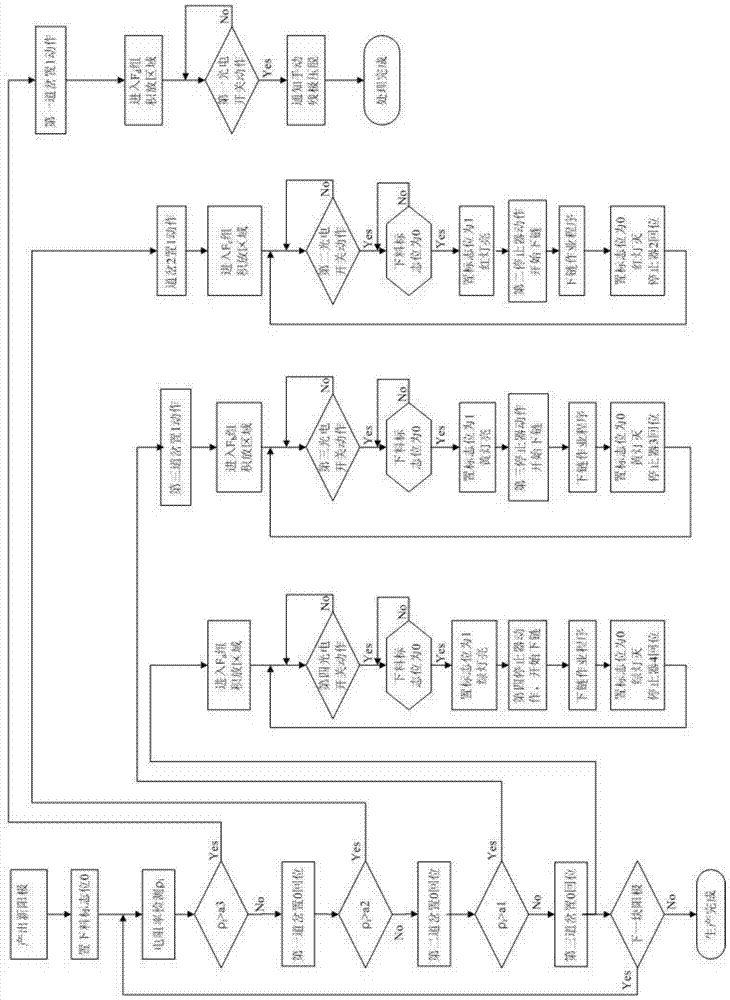
一种阳极组装产品质量控制装置及方法所属技术领域本发明属于电解铝生产技术领域,特别涉及一种阳极组装产品质量控制装置及方法。
背景技术:在铝电解生产过程中,阳极属于消耗品。电解后不能再使用的阳极(残极)送到阳极组装车间,在装站工位通过托盘和装载小车把残极挂在积放式悬挂输送机上,首先通过残极抛丸清理机除掉残极上的电解质,接着通过残极压脱机把残极上的残留碳块与铝导杆分离,之后分别通过钢爪抛丸清理机、铁环压脱机、钢爪矫直机、导杆矫直机和导杆清刷机处理铝导杆,处理完成后的铝导杆在蘸石墨工段完成蘸石墨后,在浇铸站工序与碳块仓库输送过来的阳极炭块组合成电解使用的新阳极,最后在卸站通过托盘脱离积放式悬挂输送机后由运输车辆运送到仓库备用。目前,国内电解铝厂阳极组装系统均采用上述工艺,浇铸好的新阳极产品的质量检测是在浇铸站工序用人工肉眼判断,对浇铸好的新阳极的电阻率不做检测,阳极组装产品的质量得不到有效控制。且新阳极的质量随浇铸站工序上工人的操作水平起伏波动,导致电解槽生产不稳定,运行成本提高。
技术实现要素:针对现有技术存在的不足,本发明提出一种阳极组装产品质量控制装置及方法。本发明的技术方案是这样实现的:一种阳极组装产品质量控制装置,设置在浇铸站工序与卸站之间,该装置包括:电阻率检测仪、积放式悬挂输送机和PLC控制器;所述电阻率检测仪用于对浇铸站工序产出的阳极组装产品的电阻率进行在线检测,并将电阻率值传送至PLC;所述积放式悬挂输送机,具有依次连接的3组单开道岔、若干个停止器、4个满位检测开关;所述各道岔的控制电路均与PLC的控制输出端连接;所述3组单开道岔分别对应的通往卸站的各条线路上,分布设置分别用于暂存优质品、良品、合格品和不合格品4种质量类别阳极组装产品的优质品组等待区、良品组等待区、合格品组等待区和不合格品组等待区共4个分组等待区;所述4个满位检测开关,分布设置在4个分组等待区的各满位置处,分别用于检测并判断4个分组等待区阳极组装产品满位状态,当分组等待区满位时发送满位信号给PLC;所述若干个停止器分布设置在电阻率检测仪位置处、优质品组等待区最前端位置处、良品组等待区最前端位置处、合格品组等待区最前端位置处和不合格品组等待区前端位置处;所述PLC控制器,用于对电阻率值进行分类存储后,控制电阻率检测仪位置处的停止器放行该阳极组装产品;根据该阳极组装产品的电阻率,确定该阳极组装产品的质量类别;根据该阳极组装产品的质量类别,控制道岔的走向,让阳极组装产品进入相应的分组等待区;接收满位信号后,控制停止器放行该分组等待区中的阳极产品进入卸站或者进入手工残极压脱工序。根据所述的阳极组装产品质量控制装置,所述设置在电阻率检测仪位置处、优质品组等待区最前端位置处、良品组等待区最前端位置处和合格品组等待区最前端位置处的停止器均为自动控制停止器;所述自动控制停止器的控制信号输入端均连接到PLC上。根据所述的阳极组装产品质量控制装置,所述设置在不合格品组等待区前端位置处的停止器为手动控制停止器。根据权利要求所述的阳极组装产品质量控制装置,所述的4个分组等待区的容量与卸站的托盘容量相同。采用所述的阳极组装产品质量控制装置的阳极组装产品质量控制方法,包括如下步骤:步骤1:等待阳极组装产品到电阻率检测仪位置处;步骤2:阳极组装产品到电阻率检测仪位置处停止,电阻率检测仪对该阳极产品的电阻率进行检测,并将该阳极产品的电阻率值传送至PLC;步骤3:PLC对电阻率值进行分类存储后,控制电阻率检测仪位置处的停止器放行该阳极产品;步骤4:PLC根据该阳极产品的电阻率,确定该阳极组装产品的质量类别;所述阳极组装产品的质量类别,包括优质品、良品、合格品和不合格品;电阻率ρi≤a1的阳极组装产品为优质品;a1<ρi≤a2的阳极组装产品为良品;a2<ρi≤a3的阳极组装产品为合格品;电阻率ρi>a3的阳极组装产品为不合格品;其中:a1的取值为56μΩ·m;a2的取值为61μΩ·m;a3的取值为65μΩ·m;步骤5:根据该阳极产品的质量类别,控制道岔的走向,让阳极组装产品进入相应的分组等待区,当相应的分组等待区满容量时,该等待区的满位检测开关向PLC发送满位信号,PLC接到满位信号后,控制该等待区最前端位置的停止器放行该区中的阳极产品进入卸站或者进入残极压脱工序;其中阳极组装产品优质品进入优质品组等待区;阳极组装产品良品进入良品组等待区;阳极组装产品合格品进入合格品组等待区;阳极组装产品不合格品进入不合格品组等待区;步骤6:返回步骤1或者生产结束。根据所述的阳极组装产品质量控制方法,所述步骤5包括如下步骤:步骤5.1:若采集到的阳极产品的电阻率ρi>a3,则该阳极组装产品为不合格品,PLC控制第一道岔动作,承载小车进入不合格品组等待区,在不合格品组等待区最前端位置的停止器处停止;当该不合格品组等待区满容量时,该不合格品组等待区的满位检测开关向PLC发送满位信号,PLC接到满位信号后,控制该等待区最前端位置的停止器放行该区中的阳极产品进入残极压脱工序;步骤5.2:若阳极电阻率ρi≤a3,承载小车直行;步骤5.3:若阳极电阻率ρi>a2,则该阳极组装产品为合格品,PLC控制第二道岔动作,承载小车进入合格品组等待区,在合格品组等待区最前端位置的停止器处停止;当该合格品组等待区满容量时,该合格品组等待区的满位检测开关向PLC发送满位信号;当托盘下链标志位为0时,PLC设置托盘下链标志位为1,控制该合格品组等待区最前端位置的停止器放行该区中的所有阳极产品进入卸站;卸站完成后,PLC设置托盘下链标志位为0;步骤5.4:若阳极电阻率ρi≤a2,承载小车直行;步骤5.5:若阳极电阻率ρi>a1,则该阳极组装产品为良品,PLC控制第三道岔动作,承载小车进入良品组等待区,在该区最前端位置的停止器处停止;当该区满容量时,该区的满位检测开关向PLC发送满位信号;当托盘下链标志位为0时,PLC设置托盘下链标志位为1,控制该良品组等待区最前端位置的停止器放行该区中的所有阳极产品进入卸站;卸站完成后,PLC设置托盘下链标志位为0;步骤5.6:若阳极电阻率ρi≤a1,则该阳极组装产品为优质品,承载小车直行进入优质品组等待区,在该区最前端位置的停止器处停止;当该区满容量时,该区的满位检测开关向PLC发送满位信号;当托盘下链标志位为0时,PLC设置托盘下链标志位为1,控制该优质品组等待区最前端位置的停止器放行该区中的所有阳极产品进入卸站;卸站完成后,PLC设置托盘下链标志位为0。本发明的有益效果是:(1)本发明利用阳极电阻率检测仪对阳极产品的电阻率进行在线检测,并根据阳极产品的电阻率将阳极组装产品划分为合格阳极组装产品和不合格阳极组装产品,且只允许合格产品进入电解工序,不合格产品直接进入人工残极压脱处理工序,实现组装阳极产品的质量控制。(2)本发明根据检测到的阳极产品的电阻率值进一步将合格阳极组装产品划分为优质品、良品和合格品,并使电阻率一致的产品分组存放,每一台电解槽可以使用电阻率一致的阳极。电解槽的电场和磁场的稳定性能显著提高,能提高电解槽的稳定性、电解效率和电解槽槽寿命等和技术经济指标。附图说明图1为本发明一种实施方式的阳极组装产品质量控制装置结构示意图;图2为本发明一种实施方式的阳极组装产品质量控制方法流程图。具体实施方式下面结合附图和具体实施方式对本发明作进一步详细说明。本实施方式的阳极组装产品质量控制装置,如图1所示,设置在浇铸站工序与卸站之间,该装置包括:电阻率检测仪、积放式悬挂输送机和PLC控制器;本实施方式的电阻率检测仪用于对浇铸站工序产出的到达电阻率检测仪位置处的阳极产品的电阻率进行在线检测,并将获得的电阻率值传送至PLC;本实施方式的电阻率检测仪采用的是型号为SHY-J902的炭素电极电阻率仪。本实施方式的积放式悬挂输送机,具有若干个承载小车、依次连接的第一道岔、第二道岔和第三道岔3组单开道岔、4个自动控制停止器、1个手动控制停止器、4个满位检测开关和1套三色信号指示灯柱;本实施方式的积放式悬挂输送机采用的是ZTX500积放式悬挂输送机。本实施方式的承载小车,悬挂于积放式悬挂输送机,用于承载阳极产品;本实施方式中3组单开道岔的控制电路与PLC的控制输出端连接,道岔对应的通往卸站的各条线路上分别设置有优质品组等待区、良品组等待区、合格品组等待区和不合格品组等待区共4个分组等待区;所述优质品组等待区为用于暂存若干优质品的区域;所述良品组等待区为用于暂存若干良品的区域;所述合格品组等待区为用于暂存若干合格品的区域;所述不合格品组等待区为用于暂存若干不合格品的区域;所述4个分组等待区的容量与卸站的托盘容量相同;本实施方式的设置在电阻率检测仪位置处、优质品组等待区最前端位置处、良品组等待区最前端位置处和合格品组等待区最前端位置处的停止器均为自动控制停止器;在不合格品组等待区前端位置处的停止器为手动控制停止器或者自动控制停止器。手动控制停止器可以用于根据残极压脱工序进程,人工手动控制不合格品组等待区中的阳极组装产品进入残极压脱工序。本实施方式的自动控制停止器的控制信号输入端均连接到PLC上。本实施方式的4个满位检测开关,分布设置在每个分组等待区的阳极积放满位置处,分别用于检测并判断4个分组等待区阳极满位状态,当分组等待区满位时发送满位信号给PLC;本实施方式的满位检测开关采用的是型号为XS015-Q10-ANP6X2-H1141-0.15的图尔克定区域背景抑制型直反式光电检测开关。本实施方式的PLC,用于将从电阻率检测仪接收的该阳极电阻率检测数据进行分类存储并建立数据库,并控制电阻率检测仪位置处的自动控制停止器放行该阳极产品;根据该阳极产品的电阻率,确定该阳极产品的质量类别;根据该阳极产品的质量类别,控制相应停止器的动作和相应道岔的走向,让阳极产品进入相应的分组等待区;接收满位信号后,控制停止器放行该分组等待区中的阳极产品;例如,若接收到非不合格品组等待区的某个满位检测开关的满位信号后,若卸站的托盘下链机的下链标志位为0,则控制相应的分组等待区最前端位置处的自动控制停止器放行该分组等待区中的所有阳极产品进入卸站,并向卸站的托盘下链机下达下链命令;阳极产品进入卸站后开始托盘下链作业,在指定的区域进行存放;若接收到不合格品组等待区的满位检测开关(图1中的第一光电检测开关)的满位信号后,控制不合格品组等待区最前端位置出的停止器(第五停止器)放行该分组等待区中的阳极产品进入残疾压脱工序。所述阳极产品的质量类别包括优质品、良品、合格品和不合格品;本实施方式的PLC采用的是罗克韦尔的Rslogix5550PLC控制器(配套模拟量和数字量输入输出模块)。本实施方式的三色信号指示灯柱设置在托盘下链处,用来指示产品的品质,连接PLC控制器模块的数字量输出接口。本实施方式的三色信号指示灯柱采用的是施耐德的型号为XVMB2R5A5GSLED的三色信号指示灯柱。本实施方式的阳极组装产品质量控制方法,如图2所示,包括如下步骤:步骤1:等待阳极产品到达炭素电极电阻率仪位置处;步骤2:阳极到达炭素电极电阻率仪位置处停止;炭素电极电阻率仪检测该阳极产品的电阻率,并将得到的该阳极产品的电阻率值传送至PLC;步骤3:PLC将从电阻率检测仪接收的该阳极电阻率检测数据进行分类存储并建立数据库,并控制电阻率检测仪位置处的第一停止器放行该阳极产品;步骤4:根据该阳极产品的电阻率,确定该阳极产品的质量类别;本实施方式中根据阳极产品的电阻率对阳极产品的质量进行了划分,共划分了4种质量类别,包括优质品、良品、合格品和不合格品;电阻率ρi≤a1的阳极产品为优质品;a1<ρi≤a2的阳极产品为良品;a2<ρi≤a3的阳极产品为合格品;电阻率ρi>a3的阳极产品为不合格品。其中:a1的取值范围为50~56μΩ·m;a2的取值范围为57~61μΩ·m;a3的取值范围为62~65μΩ·m;根据阳极产品的4种质量类别,相应地在道岔对应的通往卸站的各条线路上分别设置了优质品组等待区(图1中的Fa组积放区域)、良品组等待区(图1中的Fb组积放区域)、合格品组等待区(图1中的Fc组积放区域)和不合格品组等待区(图1中的Fd组积放区域)共4个分组等待区。步骤5:根据该阳极产品的质量类别,控制道岔的走向,让阳极产品进入相应的分组等待区;步骤5.1:若采集到的阳极产品的电阻率ρi>a3,第一道岔动作,承载小车进入Fd组积放区域,在停止器5处停止。当Fd组积放区域的阳极产品数量达到设定值Ym时,第一光电检测开关向PLC发送满位信号,PLC接到第一光电检测开关的满位信号后,控制与其连接的位于相关位置处的指示灯闪亮及蜂鸣器鸣响进行声光报警,来通知相关人员利用残极压脱机进行手动残极压脱。步骤5.2:若阳极电阻率ρi≤a3,承载小车直行。步骤5.3:若阳极电阻率ρi>a2,PLC控制第二道岔动作,承载小车进入Fc组积放区域。当Fc组积放区域的第二光电检测开关发出满位信号且托盘下链标志位为0时,PLC设置托盘下链标志位为1,控制第二停止器放行Fc组积放区域中的所有阳极产品进入卸站;信号指示灯柱红灯亮以指示此托盘阳极产品为合格产品。Fc组积放区域中的阳极产品进入卸站后开始托盘下链作业,在指定的区域进行存放。卸站完成后红灯灭,PLC设置托盘下链标志位为0。步骤5.4:若阳极电阻率ρi≤a2,承载小车直行。步骤5.5:若阳极电阻率ρi>a1,PLC控制第三道岔动作,承载小车进入Fb组积放区域。当Fb组积放区域的第三光电检测开关发出满位信号且托盘下链标志位为0时,PLC设置托盘下链标志位为1,控制第三停止器放行Fb组积放区域中的所有阳极产品进入卸站;信号指示灯柱黄灯亮以指示此托盘阳极产品为良品。Fb组积放区域中的阳极产品进入卸站后开始托盘下链作业,在指定的区域进行存放。卸站完成后黄灯灭,PLC设置托盘下链标志位为0。步骤5.6:若阳极电阻率ρi≤a1,承载小车直行进入Fa组积放区域。当Fa组积放区域的第四光电检测开关发出满位信号且托盘下链标志位为0时,PLC设置托盘下链标志位为1,控制第四停止器放行Fa组积放区域中的所有阳极产品进入卸站;信号指示灯柱绿灯亮以指示此托盘阳极产品为优质品。Fa组积放区域中的阳极产品进入卸站后开始托盘下链作业,在指定的区域进行存放。卸站完成后绿灯灭,PLC设置托盘下链标志位为0。步骤6:返回步骤1或者生产结束。若仍有新阳极组装产品产出时,返回步骤1;若不再有新阳极组装产品产出时,生产结束。