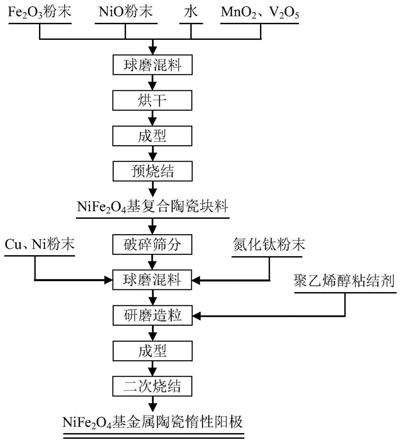
一种铝电解用nife2o4基金属陶瓷惰性阳极材料及其制备方法
技术领域
1.本发明涉及铝电解及铝电解用惰性阳极有关,特别涉及一种铝电解用nife2o4基金属陶瓷惰性阳极材料及其制备方法;属于金属陶瓷基复合材料制备技术领域。
背景技术:2.现行的工业铝电解一直采用碳素阳极,消耗大量优质碳素材料的同时产生大量的温室气体co2、致癌物质氟碳化合物和有毒物质co、沥青烟气等,严重污染环境。在碳达峰、碳中和的国家战略背景下,传统铝电解行业面临巨大危机。惰性阳极是一种不消耗或者微量消耗阳极,采用惰性阳极电解工艺时阳极气体为氧气,没有阳极效应,避免了co2和氟碳化合物的排放,符合低碳环保的发展要求;不需要周期性地更换阳极,节省阳极更换时的人力消耗,电解槽热平衡更稳定;通过改变电解槽结构、降低极距等措施,能提高电流效率、降低生产成本,实现铝电解生产过程的无污染、低能耗等目标。
3.目前惰性阳极选材主要集中在金属合金阳极、氧化物陶瓷阳极和金属陶瓷阳极等三个方面。nife2o4基金属陶瓷惰性阳极兼具nife2o4陶瓷相的强耐腐蚀性、良好热稳定性以及金属相的良好导电性及抗热冲击性等优点,被认为是最有可能代替现行碳素阳极的铝电解用惰性阳极材料。国内外对nife2o4基金属陶瓷惰性阳极进行了大量研究并取得一定成果,但是nife2o4基金属陶瓷惰性阳极中金属相能提高阳极材料的导电性、力学性能和抗热震性能等。为保证nife2o4基金属陶瓷惰性阳极具备足够的高温导电性能,金属相含量一般为17%甚至更高。专利cn101255577a描述了一种金属相由外及里呈梯度分布的金属陶瓷惰性阳极材料及制备方法,金属陶瓷中金属相质量含量在5
‑
40%之间,陶瓷相由ni、fe、ca和m(cu、mn、 zn、ba、co、v、ti等)氧化物组成,其中cao含量最高可达10%。专利cn103556184a描述了一种全润湿型纳米nife2o4‑
nio
‑
cu
‑
ni金属陶瓷惰性阳极的制备方法,得到的纳米nife2o4‑
nio
‑
cu
‑
ni金属陶瓷惰性阳极各组分质量分数为:nife2o4粉66.3%~75.6%,nio粉10%~15%,cu粉14%~17%,ni粉2%~5%。专利cn100507091c描述了一种铁酸镍
‑
铜金属陶瓷惰性阳极材料,陶瓷相为铁酸镍或铁酸镍基复合陶瓷,占总质量的60%~85%,金属相由金属铜和氧化亚铜组成,占总质量的15%~40%。
4.但是,金属相的耐腐蚀性能和抗氧化性能远低于nife2o4陶瓷相,电解过程中金属相优先腐蚀溶解,降低了nife2o4基金属陶瓷惰性阳极的耐腐蚀性能。因此,nife2o4基金属陶瓷惰性阳极的耐腐蚀性能不满足铝电解工业要求,产品铝纯度也未达标,制约惰性阳极的工业化应用。
5.nife2o4基金属陶瓷惰性阳极中金属相含量越多,阳极材料的导电性能越优异,但耐腐蚀性能越差。在目前的金属陶瓷惰性阳极制备技术和电解工艺条件下,nife2o4基金属陶瓷惰性阳极的导电性和耐腐蚀性不能兼顾,严重制约惰性阳极在铝电解工业中应用。以导电性能优异的活性陶瓷相代替金属陶瓷中的部分金属相,减少金属相的添加量,通过粉末冶金法制备铝电解用nife2o4基金属陶瓷惰性阳极,在保证金属陶瓷阳极导电性能的前提下提高其耐腐蚀性能,有助于推动铝电解用惰性阳极的工业化应用。
技术实现要素:6.本发明的目的是针对nife2o4基金属陶瓷惰性阳极导电性和耐腐蚀性不能兼顾的难题,提供一种兼具高导电能力和高耐蚀性能的铝电解用nife2o4基金属陶瓷惰性阳极及其制备方法。本发明通过掺杂导电性能优异的活性tin陶瓷相代替部分金属相,减少金属相的加入量,降低金属相的优先腐蚀几率,在保证金属陶瓷阳极导电性能的前提下提高其耐腐蚀性能,满足现行铝电解工艺要求的高导电性和强耐腐蚀能力等性能要求。
7.本发明的目的是通过以下技术方案实现的。
8.本发明的铝电解用nife2o4基金属陶瓷惰性阳极物相由nife2o4基复合陶瓷相、金属相和氮化钛相组成,nife2o4基复合陶瓷相占总质量的75~90%,金属相占总质量的5~10%,氮化钛相占总质量的5~15%; nife2o4基复合陶瓷相中nio的质量分数为10~17%,mno2的质量分数为1~3%,v2o5的质量分数为 0.5~1.5%,余量为nife2o4尖晶石;金属相由cu、ni组成,cu粉、ni粉质量比为3:1~17:3;氮化钛相为组成范围为tin
0.37
~tin
1.2
、粒径≤1μm的氮化钛粉末。
9.本发明的铝电解用nife2o4基金属陶瓷惰性阳极的制备方法包括以下步骤:
10.(1)nife2o4基复合陶瓷颗粒制备:按要求的质量配比分别称取原料fe2o3粉末、nio粉末、mno2粉末和v2o5粉末;加入去离子水湿磨4~6小时,然后在100
±
5℃下烘干;将烘干混合物料在60~100mpa 下模压成型制成一次生坯,空气气氛条件下在900~1100℃下预烧结保温4~6小时获得nife2o4基复合陶瓷块料;将nife2o4基复合陶瓷块料破碎后筛分出粒径≤74μm的部分,作为nife2o4基复合陶瓷颗粒。
11.(2)混料:按照设计的质量配比分别称取nife2o4基复合陶瓷颗粒、cu粉、ni粉和氮化钛粉末,以无水乙醇为介质,湿磨混合6~8小时,然后将混合物料在100
±
5℃真空干燥箱内烘干;向烘干混合物料中加入质量分数为4~8%的有机粘结剂,研磨混合均匀后再筛分出粒径≤250μm的部分作为粘结物料。
12.(3)成型:将粘结物料模压成形或冷等静压成型制得二次生坯,成型圧力为100~300mpa;
13.(4)烧结:将二次生坯置入高温烧结炉中,在氧分压为10~50pa氩气保护气氛下,在1150~1250℃二次烧结保温4~8小时制备得到nife2o4基金属陶瓷惰性阳极材料。
14.上述的fe2o3粉末粒径≤1μm,nio粉末粒径≤10μm,mno2粉末粒径≤50μm,v2o5粉末粒径≤10μm, cu粉末粒径≤50μm,ni粉末粒径≤50μm,氮化钛粉末粒径≤1μm。
15.上述的步骤(2)中的有机粘结剂为质量分数为4~6%的聚乙烯醇溶液。
16.上述的nife2o4基陶瓷惰性阳极材料的960℃时电导率≥40s/cm,腐蚀速率≤15mm/年。
17.本发明与现有技术相比,具有如下特点和积极效果:
18.(1)通过掺杂导电性能和耐腐蚀性能优异的活性tin颗粒代替部分金属相,减少金属相的添加量,在保证金属陶瓷阳极导电性能的前提下提高其耐腐蚀性能,降低电解过程中金属陶瓷惰性阳极的消耗速率,延长惰性阳极的使用寿命,降低产品铝的杂质含量。
19.(2)与陶瓷阳极相比,少量金属相的加入有利于提高阳极材料的高温力学性能和热学性能,提高阳极材料的抗热震性能。
附图说明
20.图1为本发明制备铝电解用nife2o4基金属陶瓷惰性阳极的工艺流程图;
21.图2为本发明实施例1制备的nife2o4基金属陶瓷惰性阳极的显微形貌图;
22.图3为本发明实施例2制备的nife2o4基金属陶瓷惰性阳极的显微形貌图;
23.图4为本发明实施例3制备的nife2o4基金属陶瓷惰性阳极的显微形貌图;
24.图5为本发明实施例4制备的nife2o4基金属陶瓷惰性阳极的显微形貌图;
25.图6为本发明实施例5制备的nife2o4基金属陶瓷惰性阳极的显微形貌图;
26.图7为本发明实施例6制备的nife2o4基金属陶瓷惰性阳极的显微形貌图。
具体实施方式
27.下面结合实施例对本发明的较佳实施案例进行详细阐述。
28.本发明实施例中采用的fe2o3粉末、nio粉末、mno2粉末、v2o5粉末、cu粉、ni粉和氮化钛粉末均为市购产品。
29.本发明实施例中测试电导率的方法为通过直流四探针法测量960℃时试样的电阻率计算得到电导率。
30.本发明实施例中测试腐蚀速率的方法为通过失重法测量阳极材料在960℃冰晶石熔盐体系 (2.2naf
·
alf3+5%caf2+5%al2o3)中电解腐蚀(阳极电流密度为0.8a/cm2)48小时后的腐蚀量,计算后得到年腐蚀速率。
31.下面结合实施例对本发明的较佳实施案例进行详细阐述。
32.实施例1:
33.按照设计所需的质量配比分别称取原料fe2o3粉末、nio粉末、mno2粉末和v2o5粉末,质量配比按 fe2o3与nio全部反应生成nife2o4尖晶石,其余的nio的质量分数为10%,mno2的质量分数为3%,v2o5的质量分数为0.5%;其中fe2o3粉末粒径≤1μm,nio粉末粒径≤10μm,mno2粉末粒径≤50μm,v2o5粉末粒径≤10μm;
34.全部原料放入球磨罐中,加入去离子水湿磨混合6小时,然后将混合物料在100
±
2℃条件下烘干;
35.将烘干混合物料在60mpa条件下模压成型,制成一次生坯;
36.将一次生坯在1100℃条件下预烧结保温4小时,再随炉冷却至常温,获得nife2o4基复合陶瓷块料;
37.将nife2o4基复合陶瓷块料破碎后筛分出粒径≤74μm的部分,作为nife2o4基复合陶瓷颗粒;
38.按照nife2o4基复合陶瓷相占总质量的90%、金属相占总质量的5%(cu粉:ni粉质量比为3:1)和氮化钛相占总质量的5%分别称取nife2o4基复合陶瓷颗粒、cu粉末、ni粉末和氮化钛粉末,加入无水乙醇湿磨混合6小时,再在100
±
2℃条件下烘干;向烘干的混合物料中加入有机粘结剂质量分数4%的聚乙烯醇溶液,有机粘结剂占烘干后混合物料总质量的8%,然后研磨混合均匀,再筛分出粒径≤250μm的部分作为粘结物料;其中cu粉末粒径≤50μm,ni粉末粒径≤50μm,氮化钛粉末粒径≤1μm;
39.将次粘结物料冷等静压成型制得二次生坯,成型圧力为300mpa;
40.将二次生坯置入高温烧结炉中,在氧分压为50pa的氩气保护气氛下,于1250℃条
件下二次烧结保温 4小时,制备得到nife2o4基金属陶瓷惰性阳极材料;所得阳极材料960℃时电导率40s/cm,年腐蚀速率 9mm/年。
41.实施例2:
42.按照设计所需的质量配比分别称取原料fe2o3粉末、nio粉末、mno2粉末和v2o5粉末,质量配比按 fe2o3与nio全部反应生成nife2o4尖晶石,其余的nio的质量分数为13.5%,mno2的质量分数为2%, v2o5的质量分数为1%;其中fe2o3粉末粒径≤1μm,nio粉末粒径≤10μm,mno2粉末粒径≤50μm,v2o5粉末粒径≤10μm;
43.全部原料放入球磨罐中,加入去离子水湿磨混合4小时,然后将混合物料在100
±
2℃条件下烘干;
44.将烘干混合物料在80mpa条件下模压成型,制成一次生坯;
45.将一次生坯在1000℃条件下预烧结保温5小时,再随炉冷却至常温,获得nife2o4基复合陶瓷块料;
46.将nife2o4基复合陶瓷块料破碎后筛分出粒径≤74μm的部分,作为nife2o4基复合陶瓷颗粒;
47.按照nife2o4基复合陶瓷相占总质量的75%、金属相占总质量的10%(cu粉:ni粉质量比为17:3) 和氮化钛相占总质量的15%分别称取nife2o4基复合陶瓷颗粒、cu粉末、ni粉末和氮化钛粉末,加入无水乙醇湿磨混合8小时,再在100
±
2℃条件下烘干;向烘干的混合物料中加入有机粘结剂质量分数6%的聚乙烯醇溶液,有机粘结剂占烘干后混合物料总质量的4%,然后研磨混合均匀,再筛分出粒径≤250μm的部分作为粘结物料;其中cu粉末粒径≤50μm,ni粉末粒径≤50μm,氮化钛粉末粒径≤1μm;
48.将次粘结物料冷等静压成型制得二次生坯,成型圧力为200mpa;
49.将二次生坯置入高温烧结炉中,在氧分压为10pa的氩气保护气氛下,于1150℃条件下二次烧结保温 8小时,制备得到nife2o4基金属陶瓷惰性阳极材料;所得阳极材料960℃时电导率62s/cm,年腐蚀速率 15mm/年。
50.实施例3:
51.按照设计所需的质量配比分别称取原料fe2o3粉末、nio粉末、mno2粉末和v2o5粉末,质量配比按 fe2o3与nio全部反应生成nife2o4尖晶石,其余的nio的质量分数为17%,mno2的质量分数为1%,v2o5的质量分数为1.5%;其中fe2o3粉末粒径≤1μm,nio粉末粒径≤10μm,mno2粉末粒径≤50μm,v2o5粉末粒径≤10μm;
52.全部原料放入球磨罐中,加入去离子水湿磨混合5小时,然后将混合物料在100
±
2℃条件下烘干;
53.将烘干混合物料在100mpa条件下模压成型,制成一次生坯;
54.将一次生坯在900℃条件下预烧结保温6小时,再随炉冷却至常温,获得nife2o4基复合陶瓷块料;
55.将nife2o4基复合陶瓷块料破碎后筛分出粒径≤74μm的部分,作为nife2o4基复合陶瓷颗粒;
56.按照nife2o4基复合陶瓷相占总质量的82.5%、金属相占总质量的7.5%(cu粉:ni粉质量比为4:1) 和氮化钛相占总质量的10%分别称取nife2o4基复合陶瓷颗粒、cu粉末、ni粉末和氮化钛粉末,加入无水乙醇湿磨混合7小时,再在100
±
2℃条件下烘干;向烘干的混
合物料中加入有机粘结剂质量分数5%的聚乙烯醇溶液,有机粘结剂占烘干后混合物料总质量的6%,然后研磨混合均匀,再筛分出粒径≤250μm的部分作为粘结物料;其中cu粉末粒径≤50μm,ni粉末粒径≤50μm,氮化钛粉末粒径≤1μm;
57.将次粘结物料冷等静压成型制得二次生坯,成型圧力为100mpa;
58.将二次生坯置入高温烧结炉中,在氧分压为30pa的氩气保护气氛下,于1200℃条件下二次烧结保温 6小时,制备得到nife2o4基金属陶瓷惰性阳极材料;所得阳极材料960℃时电导率49s/cm,年腐蚀速率 13mm/年。
59.实施例4:
60.按照设计所需的质量配比分别称取原料fe2o3粉末、nio粉末、mno2粉末和v2o5粉末,质量配比按 fe2o3与nio全部反应生成nife2o4尖晶石,其余的nio的质量分数为17%,mno2的质量分数为1%,v2o5的质量分数为1%;其中fe2o3粉末粒径≤1μm,nio粉末粒径≤10μm,mno2粉末粒径≤50μm,v2o5粉末粒径≤10μm;
61.全部原料放入球磨罐中,加入去离子水湿磨混合4小时,然后将混合物料在100
±
2℃条件下烘干;
62.将烘干混合物料在70mpa条件下模压成型,制成一次生坯;
63.将一次生坯在1050℃条件下预烧结保温5小时,再随炉冷却至常温,获得nife2o4基复合陶瓷块料;
64.将nife2o4基复合陶瓷块料破碎后筛分出粒径≤74μm的部分,作为nife2o4基复合陶瓷颗粒;
65.按照nife2o4基复合陶瓷相占总质量的80%、金属相占总质量的7.5%(cu粉:ni粉质量比为4:1) 和氮化钛相占总质量的12.5%分别称取nife2o4基复合陶瓷颗粒、cu粉末、ni粉末和氮化钛粉末,加入无水乙醇湿磨混合6小时,再在100
±
2℃条件下烘干;向烘干的混合物料中加入有机粘结剂质量分数5%的聚乙烯醇溶液,有机粘结剂占烘干后混合物料总质量的5%,然后研磨混合均匀,再筛分出粒径≤250μm的部分作为粘结物料;其中cu粉末粒径≤50μm,ni粉末粒径≤50μm,氮化钛粉末粒径≤1μm;
66.将次粘结物料冷等静压成型制得二次生坯,成型圧力为150mpa;
67.将二次生坯置入高温烧结炉中,在氧分压为40pa的氩气保护气氛下,于1200℃条件下二次烧结保温 5小时,制备得到nife2o4基金属陶瓷惰性阳极材料;所得阳极材料960℃时电导率55s/cm,年腐蚀速率 14mm/年。
68.实施例5:
69.按照设计所需的质量配比分别称取原料fe2o3粉末、nio粉末、mno2粉末和v2o5粉末,质量配比按 fe2o3与nio全部反应生成nife2o4尖晶石,其余的nio的质量分数为10%,mno2的质量分数为3%,v2o5的质量分数为1.5%;其中fe2o3粉末粒径≤1μm,nio粉末粒径≤10μm,mno2粉末粒径≤50μm,v2o5粉末粒径≤10μm;
70.全部原料放入球磨罐中,加入去离子水湿磨混合6小时,然后将混合物料在100
±
2℃条件下烘干;
71.将烘干混合物料在90mpa条件下模压成型,制成一次生坯;
72.将一次生坯在900℃条件下预烧结保温4小时,再随炉冷却至常温,获得nife2o4基复合陶瓷块料;
73.将nife2o4基复合陶瓷块料破碎后筛分出粒径≤74μm的部分,作为nife2o4基复合陶瓷颗粒;
74.按照nife2o4基复合陶瓷相占总质量的77.5%、金属相占总质量的10%(cu粉:ni粉质量比为17:3) 和氮化钛相占总质量的12.5%分别称取nife2o4基复合陶瓷颗粒、cu粉末、ni粉末和氮化钛粉末,加入无水乙醇湿磨混合8小时,再在100
±
2℃条件下烘干;向烘干的混合物料中加入有机粘结剂质量分数4%的聚乙烯醇溶液,有机粘结剂占烘干后混合物料总质量的4%,然后研磨混合均匀,再筛分出粒径≤250μm的部分作为粘结物料;其中cu粉末粒径≤50μm,ni粉末粒径≤50μm,氮化钛粉末粒径≤1μm;
75.将次粘结物料冷等静压成型制得二次生坯,成型圧力为250mpa;
76.将二次生坯置入高温烧结炉中,在氧分压为20pa的氩气保护气氛下,于1175℃条件下二次烧结保温 7小时,制备得到nife2o4基金属陶瓷惰性阳极材料;所得阳极材料960℃时电导率58s/cm,年腐蚀速率 14mm/年。
77.实施例6:
78.按照设计所需的质量配比分别称取原料fe2o3粉末、nio粉末、mno2粉末和v2o5粉末,质量配比按 fe2o3与nio全部反应生成nife2o4尖晶石,其余的nio的质量分数为17%,mno2的质量分数为3%,v2o5的质量分数为1%;其中fe2o3粉末粒径≤1μm,nio粉末粒径≤10μm,mno2粉末粒径≤50μm,v2o5粉末粒径≤10μm;
79.全部原料放入球磨罐中,加入去离子水湿磨混合5小时,然后将混合物料在100
±
2℃条件下烘干;
80.将烘干混合物料在100mpa条件下模压成型,制成一次生坯;
81.将一次生坯在950℃条件下预烧结保温6小时,再随炉冷却至常温,获得nife2o4基复合陶瓷块料;
82.将nife2o4基复合陶瓷块料破碎后筛分出粒径≤74μm的部分,作为nife2o4基复合陶瓷颗粒;
83.按照nife2o4基复合陶瓷相占总质量的85%、金属相占总质量的7.5%(cu粉:ni粉质量比为3:1) 和氮化钛相占总质量的7.5%分别称取nife2o4基复合陶瓷颗粒、cu粉末、ni粉末和氮化钛粉末,加入无水乙醇湿磨混合7小时,再在100
±
2℃条件下烘干;向烘干的混合物料中加入有机粘结剂质量分数6%的聚乙烯醇溶液,有机粘结剂占烘干后混合物料总质量的6%,然后研磨混合均匀,再筛分出粒径≤250μm的部分作为粘结物料;其中cu粉末粒径≤50μm,ni粉末粒径≤50μm,氮化钛粉末粒径≤1μm;
84.将次粘结物料冷等静压成型制得二次生坯,成型圧力为200mpa;
85.将二次生坯置入高温烧结炉中,在氧分压为30pa的氩气保护气氛下,于1225℃条件下二次烧结保温 6小时,制备得到nife2o4基金属陶瓷惰性阳极材料;所得阳极材料960℃时电导率44s/cm,年腐蚀速率 11mm/年。