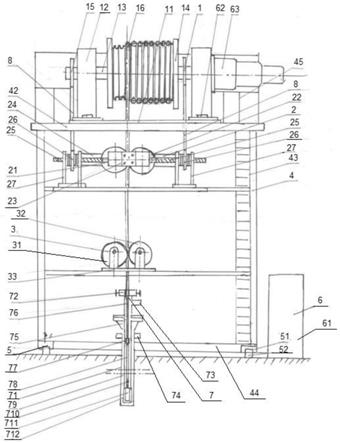
1.本发明属于石油矿场机械技术领域,特别是涉及到一种塔架式智能控制长冲程无游梁抽油机。
背景技术:2.用绞车滚筒缠绕钢丝绳代替光杆或者钢性抽油杆,进行采油作业,是近年来逐渐兴起的一种有杆采油机械,它有两类机型,一类是“卧式”机型,如专利“一种低矮型超长冲程智能控制卷扬式提拉采油系统及工作方法”,申请号:201410184063.7;专利“超长行程采油装置”,申请号:201420750926.8。这类机型由绞车滚筒总成,井口立架和导向定滑轮两大部分组成。另一类是“立式塔架”机型,如专利“一种卷扬式采油装置”,申请号:201410360663.4;专利:“一种智能超长冲程抽油机”,申请号:201911112157.2。这类“立式塔架”机型在井口立架上直接固定安装绞车滚筒总成,或者是绞车滚筒总成在井口立架上轴向移动。
3.近几年来,已有批量的“卧式”机型在大庆油田生产运行,而“立式塔架”机型,只有极少数样机,或者连样机都没有。“卧式”机型经过3
‑
4年的现场运行,暴露出钢丝绳在导向定滑轮绳槽边和滚筒出绳处的挤压,弯折和摩擦破坏比较严重,钢丝绳的使用寿命和设备运行的可靠性都存在着问题。特别是包裹高分子聚合物的钢丝绳柔性光杆。
[0004]“立式”塔架机型,“一种智能超长冲程抽油机”,用绞车滚筒总成轴向移动的方法,克服了“卧式”机型存在的一些问题。但是,“一种卷扬式采油装置”,虽然是绞车滚筒总成固定在井口立架上,用双定滑轮夹持钢丝绳引入井口中,仍然没能很好地解决“卧式”机型存在的问题,而且结构复杂,传动链长,制造成本和后期维护成本都没有比“卧式”机型明显降低,其运行的可靠性也没能明显提高。
[0005]
因此现有技术当中亟需要一种新型的技术方案来解决这一问题。
技术实现要素:[0006]
本发明所要解决的技术问题是:提供一种塔架式智能控制长冲程无游梁抽油机用于解决已有的绞车式无游梁抽油机均存在钢丝绳弯折和摩擦破坏严重的技术问题。
[0007]
塔架式智能控制长冲程无游梁抽油机,包括绞车滚筒总成、移动双滑轮系统、固定双滑轮系统、塔架总成、修井让位机构、智能控制和驱动系统以及采油井口系统,
[0008]
所述塔架总成包括塔架框架、框架上平台、梯子和塔架底部固定型钢,塔架总成通过塔架底部固定型钢安装固定于采油井口的上方;所述塔架框架的上部固定安装有框架上平台,塔架框架的侧部设置有梯子,塔架框架的下部设置有塔架底部固定型钢;所述移动双滑轮系统、固定双滑轮系统竖向布置在塔架总成的中部;
[0009]
所述绞车滚筒总成安装在框架上平台的上部,绞车滚筒总成包括总成底座、轴承座、滚筒轴、滚筒体、主传动链轮和柔性光杆;所述总成底座固定安装在框架上平台的上部,总成底座的两端分别固定安装有轴承座;所述滚筒轴的两端分别与轴承座连接,滚筒轴的
两端还分别连接有主传动链轮,滚筒轴的中部套装有滚筒体;所述滚筒体的容绳槽内的圆柱面上设置厘巴斯螺旋槽;所述柔性光杆的一端与滚筒体的一端固定连接,柔性光杆嵌入厘巴斯螺旋槽内并沿槽环绕滚筒体的外圆柱面,柔性光杆的另一端依次穿过移动双滑轮系统和固定双滑轮系统的双滑轮的滑轮绳槽孔;
[0010]
所述修井让位机构包括让位滚轮盒和让位轨道;所述让位轨道设置在井口的两侧;所述让位滚轮盒固定安装在塔架框架的底部两侧,让位滚轮盒通过滚轮与让位轨道连接;
[0011]
所述智能控制和驱动系统包括智能控制箱、负荷传感器、电磁制动器、转速编码器和行星减速器变频调速电机;所述行星减速器变频调速电机与滚筒轴的一端连接,行星减速器变频调速电机的输出轴一侧安装有转速编码器和电磁制动器;所述负荷传感器安装于两个轴承座下;所述智能控制箱分别与负荷传感器、电磁制动器、转速编码器以及行星减速器变频调速电机电性连接;
[0012]
所述采油井口系统包括套管、清蜡阀门、油管三通、套管四通、油管挂座、盘根盒、钢性抽油杆悬挂器、钢性抽油杆、油管、泵拉杆、柱塞和泵筒;所述油管设置在采油井口内,油管自上而下依次设置有清蜡阀门、油管三通和套管四通,油管的内部上部设置有盘根盒,油管通过油管挂固定在套管的下部,油管的下部与泵筒固定连接;所述油管挂座安装在套管四通上;所述钢性抽油杆的上端通过钢性抽油杆悬挂器与穿过移动双滑轮系统和固定双滑轮系统滑轮绳槽孔后的柔性光杆连接,钢性抽油杆的下端与泵拉杆的上端固定连接;所述泵拉杆的下端与柱塞的上端固定连接;所述柱塞在泵筒内上下往复运动。
[0013]
所述移动双滑轮系统包括左移动滑轮、右移动滑轮、滑轮支架、移动轨道、牵引丝杠、被动链轮丝母和丝母支架;所述滑轮支架安装于移动轨道上;所述移动轨道固定安装在丝母支架上;所述左移动滑轮和右移动滑轮的轴上均安装有压力轴承,左移动滑轮和右移动滑轮分别通过支撑轴安装在滑轮支架的两端,左移动滑轮和右移动滑轮分别与对应设置的牵引丝杠的一端连接;所述牵引丝杠的另一端与被动链轮丝母螺纹连接,牵引丝杠与被动链轮丝母的螺距等于柔性光杆的直径;所述被动链轮丝母通过丝母支架与塔架框架连接,被动链轮丝母的外部通过传动链条与主传动链轮连接。
[0014]
所述固定双滑轮系统包括左固定滑轮、右固定滑轮和滑轮固定底座;所述左固定滑轮和右固定滑轮分别通过滑轮固定底座安装在塔架框架上。
[0015]
所述固定双滑轮系统的两个滑轮绳槽圆心连线的中点向下对正采油井口的中心,固定双滑轮系统的两个滑轮绳槽圆心连线的中点向上对正滚筒体上厘巴斯螺旋槽内柔性光杆的行程中点,并且固定双滑轮系统的两个滑轮绳槽圆心连线的中点到滚筒体行程起始第一圈出绳处切线切点连线与固定双滑轮系统的两个滑轮绳槽圆心连线的中点到滚筒体行程终止最后一圈出绳切线点连线所形成的夹角α小于或等于3
°
。
[0016]
通过上述设计方案,本发明可以带来如下有益效果:
[0017]
本发明把绞车滚筒总成固定在井口塔架框架的上平台上,消除和减小钢丝绳柔性光杆在绞车滚筒出绳处和定滑轮绳槽两侧入绳处,以及定滑轮上形成的弯折和挤压交变应力所造成的疲劳破坏,摩擦破坏。简化传动结构和减少传动链,以减少运动部件和润滑点。使维护、保养、调控的安全风险点大幅度减少。进一步提高运行的可靠性和使用寿命。本发明结构极其简单,紧凑,因此制造、安装,维修方便,使制造成本和后期维护保养成本大大降
低。有效地消除和减小钢丝绳柔性光杆的疲劳破坏程度,提高了钢丝绳柔性光杆的使用寿命,增加了设备运行的可靠性,皮实耐用。
附图说明
[0018]
以下结合附图和具体实施方式对本发明作进一步的说明:
[0019]
图1为本发明塔架式智能控制长冲程无游梁抽油机的结构示意图。
[0020]
图2为现有技术中卧式机型的柔性光杆受力分析图一。
[0021]
图3为现有技术中卧式机型的柔性光杆受力分析图二。
[0022]
图4为现有技术中立式机型“一种卷扬式采油装置”的受力分析图。
[0023]
图5为本发明塔架式智能控制长冲程无游梁抽油机的柔性光杆受力分析图。
[0024]
图中1
‑
绞车滚筒总成、2
‑
移动双滑轮系统、3
‑
固定双滑轮系统、4
‑
塔架总成、5
‑
修井让位机构、6
‑
智能控制和驱动系统、7
‑
采油井口系统、8
‑
传动链条、11
‑
总成底座、12
‑
轴承座、13
‑
滚筒轴、14
‑
滚筒体、15
‑
主传动链轮、16
‑
柔性光杆、21
‑
左移动滑轮、22
‑
右移动滑轮、23
‑
滑轮支架、24
‑
移动轨道、25
‑
牵引丝杠、26
‑
被动链轮丝母、27
‑
丝母支架、31
‑
左固定滑轮、32
‑
右固定滑轮、33
‑
滑轮固定底座、41
‑
塔架框架、42
‑
框架上平台、43
‑
梯子、44
‑
塔架底部固定型钢、45
‑
护栏、51
‑
让位滚轮盒、52
‑
让位轨道、61
‑
智能控制箱、62
‑
负荷传感器、63
‑
行星减速器变频调速电机、71
‑
套管、72
‑
清蜡阀门、73
‑
油管三通、74
‑
套管四通、75
‑
油管挂座、76
‑
盘根盒、77
‑
钢性抽油杆悬挂器、78
‑
钢性抽油杆、79
‑
油管、710
‑
泵拉杆、711
‑
柱塞、712
‑
泵筒。
具体实施方式
[0025]
如图所示,塔架式智能控制长冲程无游梁抽油机,包括绞车滚筒总成1、移动双滑轮系统2、固定双滑轮系统3、塔架总成4、修井让位机构5、智能控制和驱动系统6以及采油井口系统7,
[0026]
所述塔架总成4包括塔架框架41、框架上平台42、梯子43和塔架底部固定型钢44,塔架总成通过塔架底部固定型钢44安装固定于采油井口的上方;所述塔架框架41的上部固定安装有框架上平台42,塔架框架41的侧部设置有梯子43,塔架框架41的下部设置有塔架底部固定型钢44;所述移动双滑轮系统2、固定双滑轮系统3竖向布置在塔架总成4的中部;
[0027]
所述绞车滚筒总成1安装在框架上平台42的上部,绞车滚筒总成包括总成底座11、轴承座12、滚筒轴13、滚筒体14、主传动链轮15和柔性光杆16;所述总成底座11固定安装在框架上平台42的上部,总成底座11的两端分别固定安装有轴承座12;所述滚筒轴13的两端分别与轴承座12连接,滚筒轴13的两端还分别连接有主传动链轮15,滚筒轴13的中部套装有滚筒体14;所述滚筒体14的容绳槽内的圆柱面上设置厘巴斯螺旋槽;所述柔性光杆16的一端与滚筒体14的一端固定连接,柔性光杆16嵌入厘巴斯螺旋槽内并环绕滚筒体14的外圆柱面,柔性光杆16的另一端依次穿过移动双滑轮系统2和固定双滑轮系统3的双滑轮的滑轮绳槽孔;所述框架上平台42的上部安装有护栏45;
[0028]
所述修井让位机构5包括让位滚轮盒51和让位轨道52;所述让位轨道52设置在井口的两侧;所述让位滚轮盒51固定安装在塔架框架41的底部两侧,让位滚轮盒51通过滚轮与让位轨道52连接。修井作业前,调整移动双滑轮系统2、固定双滑轮系统3的柔性光杆16退
出机构,上提钢性抽油杆悬挂器77、脱下钢性抽油杆78后,拆下塔架框架41下部的固定螺栓,后撤塔架总成4,完成修井让位。
[0029]
所述智能控制和驱动系统6包括智能控制箱61、负荷传感器62、电磁制动器、转速编码器和行星减速器变频调速电机63;所述行星减速器变频调速电机63与滚筒轴13的一端连接,行星减速器变频调速电机63的输出轴一侧安装有转速编码器和电磁制动器;所述负荷传感器62安装于两个轴承座12下;所述智能控制箱61分别与负荷传感器62、电磁制动器、转速编码器以及行星减速器变频调速电机63电性连接;
[0030]
所述采油井口系统7包括套管71、清蜡阀门72、油管三通73、套管四通74、油管挂座75、盘根盒76、钢性抽油杆悬挂器77、钢性抽油杆78、油管79、泵拉杆710、柱塞711和泵筒712,所有杆件、管件,安装在一个轴心线上;所述油管79设置在采油井口内,油管79自上而下依次设置有清蜡阀门72、油管三通73和套管四通74,油管79的上部设置有盘根盒76,油管79通过油管挂座75固定在套管71内的上部,油管79的下部与泵筒712固定连接;所述油管挂座75安装在套管四通74上;所述钢性抽油杆78的上端通过钢性抽油杆悬挂器77与穿过移动双滑轮系统2和固定双滑轮系统3滑轮绳槽孔后的柔性光杆16连接,钢性抽油杆78的下端与泵拉杆710的上端固定连接;所述泵拉杆710的下端与柱塞711的上端固定连接;所述柱塞711在泵筒712内上下往复运动。
[0031]
安装时,首先在套管71的地面端安装固定油管挂座75的套管四通74,然后在套管71中下入泵筒712,泵筒712的上端连接油管79,上至油管79的地面端安装油管挂,然后在油管79中下入柱塞711和泵拉杆710,泵拉杆710的上端连接钢性抽油杆78至井口,并用垫叉悬挂钢性抽油杆78于油管挂上,把后撤让位的塔架总成4前移到预定位置,并使行程总长度中心点对正井口清蜡阀门72中心。把柔性光杆16的自由端穿过清蜡阀门72和油管三通73。在柔性光杆16自由端固定钢性抽油杆悬挂器77后,用钢性抽油杆悬挂器77的母扣接头连接垫叉上的钢性抽油杆78的公扣,然后连接在油管三通73与油管挂座75上,并且紧固,再连接清蜡阀门72与油管三通73。至此安装完毕,可调试运行。
[0032]
所述移动双滑轮系统2包括左移动滑轮21、右移动滑轮22、滑轮支架23、移动轨道24、牵引丝杠25、被动链轮丝母26和丝母支架27;所述滑轮支架23安装于移动轨道24上;所述移动轨道24固定安装在丝母支架27上;所述左移动滑轮21和右移动滑轮22的轴上均安装有压力轴承,左移动滑轮21和右移动滑轮22分别通过支撑轴安装在滑轮支架23的两端,左移动滑轮21和右移动滑轮22分别与对应设置的牵引丝杠25的一端连接;所述牵引丝杠25的另一端与被动链轮丝母26螺纹连接,牵引丝杠25与被动链轮丝母26的螺距等于柔性光杆16的直径;所述被动链轮丝母26通过压力轴承安装在丝母支架27上,被动链轮丝母26的外部通过传动链条8与主传动链轮15连接;所述丝母支架27与塔架框架41固定连接。
[0033]
所述固定双滑轮系统3包括左固定滑轮31、右固定滑轮32、滑轮固定底座33;所述左固定滑轮31和右固定滑轮32分别通过滑轮固定底座33安装在塔架框架41上。工作时左固定滑轮31、右固定滑轮32两个滑轮移到中心位置,两个滑轮绳槽的圆心保证1至2mm的间隙后,固定并锁紧。修井作业让位时,左固定滑轮31、右固定滑轮32两滑轮向左右外移大于柔性光杆16直径的距离后固定好。
[0034]
所述固定双滑轮系统3的两个滑轮绳槽圆心连线的中点向下对正采油井口的中心,固定双滑轮系统3的两个滑轮绳槽圆心连线的中点向上对正滚筒体14上厘巴斯螺旋槽
内柔性光杆16的行程中点,并且固定双滑轮系统3的两个滑轮绳槽圆心连线的中点到滚筒体14行程起始第一圈出绳处切线切点连线与固定双滑轮系统3的两个滑轮绳槽圆心连线的中点到滚筒体14行程终止最后一圈出绳切线点连线所形成的夹角α小于或等于3
°
。
[0035]
主传动链轮15包括右主动链轮和左主动链轮,左、右主动链轮通过左、右侧的传动链条8与左、右侧的被动链轮丝母26相连接。左侧的被动链轮丝母26通过压力轴承安装在左侧的丝母支架27上,左侧的牵引丝杠25套装在左侧的被动链轮丝母26上。左侧的牵引丝杠25与滑轮支架23的一侧固定连接,滑轮支架23通过滑套与左侧的移动轨道24连接,左侧的移动轨道24固定安装在左侧的丝母支架27上。右侧的被动链轮丝母26通过压力轴承安装在右侧的丝母支架27上,右侧的牵引丝杠25套装在右侧的被动链轮丝母26上,右侧的牵引丝杠25与滑轮支架23的另一侧固定连接。左、右两侧的牵引丝杠25,左、右两侧的被动链轮丝母26螺距相等,旋向相同。右侧的移动轨道24固定安装在右侧的丝母支架27上;当行星减速器变频调速电机63带动滚筒轴13旋转时,右主动链轮和左主动链轮同时旋转,通过左、右两侧的传动链条8带动左、右两侧的被动链轮丝母27同速同向旋转,因为主传动链轮15和被动链轮丝母26的齿数相等。同时驱动左、右两侧的牵引丝杠25左右移动。左、右两侧的牵引丝杠25带动滑轮支架23左右移动,每转1圈,牵引丝杠25移动一个螺距,因为一个螺距等于柔性光杆16的直径,所以滚筒体14每转一圈牵引丝杠25移动一个螺距,左移动滑轮21和右移动滑轮22移动一个绳径的距离,以保证柔性光杆16在滚筒体14容绳槽内圆柱面切点处不被弯折。
[0036]
柔性光杆16行程总长度所包含的总圈数中点为切线切点,此时柔性光杆16与滚筒体14容绳槽圆柱面所形成的切线向下对正采油井口系统7的清蜡阀门72的中心。滚筒轴13与左移动滑轮21、右移动滑轮22的轴以及左固定滑轮31、右固定滑轮32的轴空间垂直。并且从附图1可以看出,当左移动滑轮21与右移动滑轮22在中间位置时,柔性光杆16与滚筒体14容绳槽圆柱面形成切线切点、左移动滑轮21与右移动滑轮22两轮中心连线的中点、左固定滑轮31与右固定滑轮32两轮中心连线的中点、清蜡阀门72的中心点四点共线。左固定滑轮31与右固定滑轮32两轮中心连线的中点到滚筒体14容绳槽内柔性光杆16的一个行程起点连线,和同一行程终点连线所形成的夹角α小于或等于3
°
。减小滚筒体14出绳处的弯折破坏程度,以提高柔性光杆16的抗疲劳破坏强度。
[0037]
附图2和图3是卧式机型的柔性光杆受力分析。从图中可以看出在滚筒体14容绳槽内柔性光杆16出绳处与圆柱面切线切点处,在井口定滑轮绳槽入绳处与两边切点处,都存在拐点弯折。而且井口定滑轮上的包角φ小于90
°
,所以这种机型弯折挤压破坏最严重。
[0038]
附图3中柔性光杆16在绞车滚筒容绳槽内圆柱面切线切点处的弯折角β1的大小也取决于井口定滑轮到滚筒体14之间的距离和行程总长度所缠绕的圈数。这两种机型柔性光杆16在切点处弯折都无滑轮支撑,夹角α越大,弯折角β1越小,弯折破坏越严重。在同样距离时,行程越长,弯折角β1越小,弯折破坏越严重,反之弯折破坏越轻微。β2为柔性光杆在井口定滑轮绳槽内形成的弯折角,φ1为柔性光杆在固定双滑轮上所形的包角。
[0039]
附图4是立式机型“一种卷扬式采油装置”的受力分析图,柔性光杆16在滚筒体14容绳槽内圆柱面出绳切点处的弯折角度β1取决于固定双滑轮两轮中心连线中点到绞车滚筒的距离和行程长度,在距离不变的前提下,β1角也是一个变量,随着圈数的收放在变化,行程起点和终点时β1角最大。柔性光杆16在滑轮上的包角φ取决于滑轮直径,与滑轮直径
成反比。φ1为柔性光杆在固定双滑轮上所形的包角,β2为柔性光杆在井口定滑轮绳槽内形成的弯折角。
[0040]
附图5是本发明的机型中柔性光杆16受力分析图。图5中可以看出,柔性光杆16在滚筒体14容绳槽的内圆柱面切点处弯折时的拐点有移动滑轮支撑,且滑轮直径足够大,所以拐点处的没有弯折应力。主传动链轮15、被动链轮丝母26的直径和齿数相等。两个牵引丝杠25的螺距均与柔性光杆16的直径相等,保证了左移动滑轮21、右移动滑轮22与滚筒体14旋转同步。在切点处无弯折,克服了无滑轮支撑的弯折破坏。φ1为柔性光杆在游动双滑轮上所形成的包角保证了滑轮合理的直径,增大了包角φ1,减小了滑轮上的弯折和摩擦破坏。所以本发明机型基本上解决了柔性光杆的弯折挤压破坏,保证了设备的运行可靠性和降低了后期维护成本。