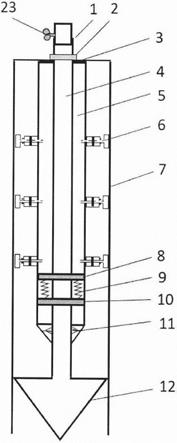
1.本发明属于岩土工程边坡或巷道加固处理的技术领域,具体涉及一种利用氧化镁-二氧化碳碳化的预应力锚杆施作方法。
背景技术:2.在隧道工程、采矿工程、基坑工程或边坡工程的施工过程中,常出现因地层变形、坍塌或边坡失稳而危及人身与工程安全的现象,需对边坡或基坑进行加固。现有加固方式多为锚杆+注浆,即通过设置锚杆来提高地层或边坡的抗拉和抗剪能力,以控制地层变形、提高地层的整体稳定性。锚杆支护作为一种主动支护方式,是抑制开挖后岩土体变形和加固失稳岩体的有效措施,在边坡支护中得到了广泛应用。随着地下空间和基坑开挖条件的愈加复杂,以及开挖活动对围岩扰动的增大,围岩变形量也逐渐变大,使传统锚固支护技术暴露出明显问题。例如锚杆与岩体间的锚固和紧固性变差,造成岩体内部崩裂松动,使锚杆未能充分发挥支护能力;普通预应力锚杆或注浆锚杆受其材料变形能力限制,当围岩产生过大变形时,即出现锚杆拉断、锚头损坏等问题。
3.在地应力条件下,因大变形造成的工程问题时有发生,大变形问题往往难以有效解决,当围岩发生大变形时,锚杆因不能适应围岩大变形而发生断裂破坏,导致锚杆支护失效。专利cn209212272u公开了一种能适应围岩大变形的可伸长锚杆,该锚杆在受到外力时就开始产生位移、释放能量,使前期支护强度降低,破坏强度相比普通锚杆更低。专利cn1182810a公开了一种大变形自适应释能锚杆,它包括了杆体和杆体后段上的内阶梯管筒,杆体和管筒可发生相对位移,且通过发生位移时所产生的摩擦力来提供支护作用,该方法虽可适应大变形问题,但在尺寸上要求严格,摩擦头容易损坏,若遭遇剪切地应力,容易使管筒直径以及管筒与摩擦头接触应力发生改变,导致锚杆工作受阻。专利cn111412003a公布了一种自适应大变形隧道可伸缩式注浆锚杆,此锚杆利用伸缩弹簧解决了大变形问题,但锚杆的锚固力全部来自于套筒和围岩间的接触应力,当围岩发生变形,套筒与围岩间锚固的紧密性以及锚杆所能提供的锚固力将降低,甚至导致整个锚杆支护体系的失效。
4.预应力锚杆也被广泛用作隧道结构的初期支护,通过施加预应力来加固土体或岩体,提高土体或岩体的稳定性,避免其塌方。但大多数锚杆的预应力张拉是在现场施工时施加,容易出现预应力达不到设计值情况。如专利cn110670599a公布了一种中空注浆预应力锚杆及其施工方法,包括中空杆体、锚头、螺母和垫板,其能达到的最大拉力相比于传统锚杆有大幅增加,从而提升锚杆支护结构的安全性能,但该锚杆预应力是通过张拉施加,很可能达不到设计值,影响其正常应用。专利cn11946375a公布了一种分段式注浆锚杆,但该锚杆在剪应力作用下易产生形变,受浆体影响可能无法移动至预定位置,无法触发下一阶段的止浆塞开启和后续注浆工作。专利cn112360530a公布了一种岩土工程施工用注浆锚杆,此锚杆有较好抗渗性和整体稳定性,但不能解决地层中可能出现的大变形和高地应力问题。专利cn112253194a公布了一种注浆锚杆索的支护装置及其支护方法,但在施工过程中,锚杆或锚杆索放入之后需静置半月以上直至岩体自然裂开,该方法施工时间长、适用范围
小。此外,专利cn112360534a公布了一种全锚注浆锚杆及其锚固方法,该锚杆注浆时所用的浆液为水泥浆,其凝固时间长,并且该装置通过旋出内螺纹杆尖端部位的凸体,使该锚杆的锚固长度增加,但锚固长度和锚固能力的增长幅度极其有限。
5.结合现有锚杆结构和处理地应力、大变形岩体结构中所存在的不足,立足我国工程建设快速发展的现状和需求,申请低碳高效、抗拉抗剪性能高、适应大变形岩体的锚固处理方法已成为业界亟待解决的重要课题。因此,提出一种利用氧化镁-二氧化碳碳化的预应力锚杆施作方法对边坡和巷道工程中的岩体加固处理具有十分重要的工程意义。
技术实现要素:6.鉴于上述背景技术中所存在的不足,本发明旨在提出一种利用氧化镁-二氧化碳碳化的预应力锚杆施作方法,解决现有技术所存在的锚杆锚固能力低、适应大变形能力差、锚固处理周期长、稳定性低和环境经济效益不佳等缺陷或问题。该发明根据岩层实际情况选用不同长度的变截面锚杆,增强了锚杆与岩体间的锚固性;锚杆可施加预应力以应对地层中可能出现的地应力;锚杆特设弹簧装置以适应岩体产生的大变形并提高支护能力;锚杆注浆以低碳氧化镁和工业废渣为主,通过吸收大量co2气体来快速提高浆体强度,具有低碳环保、施工高效的显著优点。
7.为了解决上述技术问题,本发明所采用的技术方案为:一种利用氧化镁-二氧化碳碳化的预应力锚杆施作方法,其特征在于,所述施作方法包括以下步骤:
8.a.放线定位:按照勘查资料和设计文件,确定锚杆孔的位置、间距、深度、直径与倾角,确定锚杆变截面处的深度、长度及直径,并在边坡坡面上放线;
9.b.挖孔清孔:按照放线定位所确定的锚杆参数,使用锚杆钻机旋挖钻孔至设计深度,在设计的变截面处和底部调节钻机钻头的旋转直径,旋挖形成带变截面和扩大头的锚杆孔,最后用高压风枪将锚杆孔清理干净;
10.c.植入锚杆:将合格锚杆植入锚杆孔内,微调锚杆使锚杆的伸缩碳化器对准锚杆孔的变截面,然后旋调螺母固定注气通道a;
11.d.拔筒注浆:将注气孔a和注气孔b关闭,将注浆泵与套筒上的注浆通道上端连接,启动注浆泵,调节注浆压力,使浆液从套筒壁内的注浆通道下端喷出,待扩大头中的浆液注满后,旋转套筒并向外拔出,浆液继续注入至锚杆外侧的碳化层区域,浆液注入和套筒外拔同步进行,当浆液注满锚杆外侧的碳化层区域且套筒完全被拔出时,关闭注浆泵,完成拔筒注浆;
12.e.注气碳化:将co2高压气罐与注气孔b连接,打开注气孔b上的通气阀b并调节至第一设计通气压力,使co2气体通过注气通道b上的注气孔区b和伸缩碳化器向碳化层区域扩散,通气养护至第一设计碳化时间后,关闭通气阀b,完成碳化层的注气碳化;
13.f.施加预应力:通过旋转螺母调节与注气通道a固定连接的升降盘a位置,达到设计的预应力;
14.g.碳化扩大头区域:将co2高压气罐与注气孔a连接,打开注气孔a上的通气阀a,调节至第二设计通气压力,使co2气体通过注气通道a的注气孔区a向扩大头区域扩散,通气养护至第二设计碳化时间后,关闭通气阀a,完成扩大头区域的注气碳化;
15.h.施作收尾:卸掉通气阀a,将微型探测仪从注气孔a进入,沿着注气通道a匀速向
内行进,行进过程中检验碳化层和扩大头区域的碳化加固效果,如果检验不合格,对不合格区域进行二次碳化处理;当检验合格时,卸掉螺母,在锚杆尾部进行防腐保护处理,完成锚杆施作。
16.作为本发明的一种改进,所述锚杆包括注浆装置、注气装置和伸缩装置,所述注浆装置包括套筒和注浆通道,套筒套设于锚杆装置的外部,注浆通道设于套筒壁的内部;所述注浆通道的内径小于套筒的壁厚,注浆通道的数量根据套筒直径确定,为3-12个,套筒直径越大,注浆通道数量越多;所述注气装置包括注气通道a、注气通道b、伸缩碳化器、扩大头、注气孔区a、注气孔区b、注气孔a、注气孔b、通气阀a和通气阀b;所述伸缩碳化器固设在注气通道b的外部,伸缩碳化器包括碳化头、注气孔区c、限位筒、升降盘b、弹簧b和注气通道c;所述注气通道a下方连通扩大头,扩大头的外表面设有注气孔区a,注气通道a上方设有注气孔a,且注气孔a上设有通气阀a,所述注气通道b上方的钢板上设有注气孔b,注气孔b上设有通气阀b,注气通道b连通伸缩碳化器中的注气通道c,且注气通道b外表面设有注气孔区b,注气通道c连通碳化头,且碳化头上设有注气孔区c,所述弹簧b周向布置在升降盘b的下方且弹簧b的另一端与伸缩碳化器外壳固定连接;所述限位筒固设于伸缩碳化器的上方并套设于注气通道c的外部;所述伸缩装置包括钢板、螺母、限位盘、弹簧a、升降盘a和刷子,所述钢板架设在注气通道b的上方,所述螺母设于钢板上方,所述限位盘和升降盘a设于注气通道b内部且注气通道a外部,限位盘与注气通道b内壁固定连接,升降盘a和注气通道a外壁固定连接,限位盘和升降盘a之间用弹簧a连接,升降盘a与限位盘之间的相对位移通过螺母限定;当螺母卸掉时,注气通道a、扩大头和升降盘a组合而成的整体与注气通道b和限位盘组合成的整体可通过弹簧a发生相对滑移,以适应岩土层的大变形。
17.作为本发明的另一种改进,所述套筒的材质为硬质塑料或不锈钢,直径为100-300mm,所述套筒拔出为顺时针和逆时针交替旋转进行,拔出的套筒可循环利用;所述注浆通道均匀地布设在套筒壁内,注浆通道的内径小于套筒的壁厚,注浆通道的数量根据套筒直径确定,为3-12个,套筒直径越大,注浆通道数量越多。
18.作为本发明的另一种改进,所述浆液由平均粒径小于1mm的细粒料、水和减水剂组成,所述细粒料由碱性胶凝激发材料和工业固废组成,所述碱性胶凝激发材料由轻烧氧化镁、生石灰粉组成,所述工业固废由矿渣粉和污泥焚烧灰组成;所述浆液的水固比为0.4-0.7,碱性材料的含量越高,则水固比越大;所述碱性胶凝激发材料和工业固废分别占细粒料的20-50%和50-80%,所述轻烧氧化镁和生石灰粉分别占碱性胶凝激发材料的70-100%和0-30%,所述矿渣粉和污泥焚烧灰分别占工业固废的70-85%和15-30%。
19.作为本发明的另一种改进,所述co2是从高碳排放的煤电厂和水泥厂收集压缩的高压co2,所用co2浓度大于40%,所述第一设计通气压力为100~200kpa,所述第一设计碳化时间为3-12小时,第一设计通气压力和第一设计碳化时间根据碳化层的厚度确定,碳化层越厚,第一设计通气压力和第一设计碳化时间越大;所述第二设计通气压力为200~400kpa,所述第二设计碳化时间为6-12小时,第二设计通气压力和第二设计碳化时间根据锚杆长度和扩大头直径确定,锚杆长度和扩大头直径越大,第二设计通气压力和第二设计碳化时间越大。
20.与现有技术相比,本发明具有以下技术优势和有益效果:
21.(1)锚杆特设变截面,增强锚杆与碳化层以及碳化层与岩体间的锚固和紧固性,能
充分发挥并提高锚杆的支护能力。
22.(2)锚杆特设伸缩装置,可适应地层的大变形,增大锚杆变形的延伸率,有效释放围岩变形所产生的能量,大幅提升锚杆的破坏强度和前期支护能力,具有良好的支护作用和长期稳定性。
23.(3)锚杆结构特设限位器和螺母,通过螺母的旋转圈数来精确调节锚杆的限位器位置和预应力大小,当围岩中产生一定地应力时,锚杆预应力便能抵消岩土层中的地应力,使锚杆及碳化固化后的碳化层能适应岩土层的变形,保护锚杆支护系统。
24.(4)锚杆结构体特设注气通道a和注气通道b,以及注气孔区a、注气孔区b和注气孔区c,实现了扩大头和碳化层的独立通气碳化,并显著提高了扩大头和碳化层的通气碳化效率。
25.(5)本发明所用浆液以轻烧氧化镁和矿渣为主,也掺有一定量生石灰粉和污泥焚烧灰,取代传统硅酸盐水泥,所用胶凝材料具有显著的低碳环保特性;同时轻烧氧化镁和生石灰具有一定膨胀性,一定程度上促进了锚杆碳化层与岩土层间的摩擦结合。
26.(6)本发明中胶凝材料需通过co2碳化来发挥作用,通气碳化时间短、强度增长快,大大减小了传统注浆锚杆的养护时间、提高了锚杆的施作效率;同时本发明大量吸收co2,实现了岩土围岩加固过程中的碳利用,对节能减排和环境保护具有重要意义。
附图说明
27.为更清楚地说明本发明的技术方案,下面将对实施方式中所需要的附图作简单介绍,显而易见地,以下附图仅是本发明的一些实施方式,对于本领域技术人员来讲,还可以根据这些附图获得其他附图。
28.图1是一种利用氧化镁-二氧化碳碳化的预应力锚杆施工步骤示意图(a-挖孔清孔,b-植入锚杆,c-拔筒注浆,d-注气碳化,e-施加预应力,f-碳化扩大头区域);
29.图2是一种利用氧化镁-二氧化碳碳化的预应力锚杆结构示意图;
30.图3是一种利用氧化镁-二氧化碳碳化的预应力锚杆的伸缩碳化器结构示意图;
31.图4是一种利用氧化镁-二氧化碳碳化的预应力锚杆取下套筒后外观示意图;
32.图5是一种利用氧化镁-二氧化碳碳化的预应力锚杆俯视图;
33.图中:1、注气孔a,2、螺母,3、钢板,4、注气通道a,5、注气通道b,6、伸缩碳化器,7、套筒,8、限位盘,9、弹簧a,10、升降盘a,11、刷子,12、扩大头,13、碳化头,14、注气孔区c,15、限位筒,16、升降盘b,17、弹簧b,18、注气通道c,19、注气孔区a,20、注气孔区b,21、注浆通道,22、注气孔b,23、通气阀a,24、通气阀b。
具体实施方式
34.在本发明的描述中,“上”、“下”、“顶”、“底”、“内”、“外”等指示的方位关系为附图所示的方位关系,仅是为方便本发明的描述,而不是指示或暗示所指的特定方位。实施步骤中的具体特征是对本技术方案的详细说明,而不是对本技术技术方案的限定。即在不冲突情况下,实施步骤中的技术特征可以相互组合。为了使本发明实现的技术手段、创作特征、达到目的与功效易于明白理解,下面将结合说明书附图及具体实施方式对技术方案进行进一步阐述。为使本发明的目的、技术方案及优点更加清楚明白,结合以下附图,对本发明进
行进一步详细说明。
35.参见图1,一种利用氧化镁-二氧化碳碳化的预应力锚杆施作方法,其特征在于,所述施作方法包括以下步骤:
36.a.放线定位:按照勘查资料和设计文件,确定锚杆孔的位置、间距、深度、直径与倾角,确定锚杆变截面处的深度、长度及直径,并在边坡坡面上放线;
37.b.挖孔清孔:按照放线定位所确定的锚杆参数,使用锚杆钻机旋挖钻孔至设计深度,在设计的变截面处和底部调节钻机钻头的旋转直径,旋挖形成带变截面和扩大头12的锚杆孔,最后用高压风枪将锚杆孔清理干净(如图1(a));
38.c.植入锚杆:将合格锚杆植入锚杆孔内,微调锚杆使锚杆的伸缩碳化器6对准锚杆孔的变截面,然后旋调螺母2固定注气通道a4(如图1(b));
39.d.拔筒注浆:将注气孔a1和注气孔b22关闭,将注浆泵与套筒7上的注浆通道21上端连接,启动注浆泵,调节注浆压力,使浆液从套筒7壁内的注浆通道21下端喷出,待扩大头12中的浆液注满后,旋转套筒7并向外拔出,浆液继续注入至锚杆外侧的碳化层区域,浆液注入和套筒7外拔同步进行,当浆液注满锚杆外侧的碳化层区域且套筒7完全被拔出时,关闭注浆泵,完成拔筒注浆(如图1(c));
40.e.注气碳化:将co2高压气罐与注气孔b22连接,打开注气孔b22上的通气阀b24并调节至第一设计通气压力,使co2气体通过注气通道b5上的注气孔区b20和伸缩碳化器6向碳化层区域扩散,通气养护至第一设计碳化时间后,关闭通气阀b24,完成碳化层的注气碳化(如图1(d));
41.f.施加预应力:通过旋转螺母2调节与注气通道a4固定连接的升降盘a10位置,达到设计的预应力(如图1(e));
42.g.碳化扩大头区域:将co2高压气罐与注气孔a1连接,打开注气孔a1上的通气阀a23,调节至第二设计通气压力,使co2气体通过注气通道a4的注气孔区a19向扩大头12区域扩散,通气养护至第二设计碳化时间后,关闭通气阀a23,完成扩大头12区域的注气碳化(如图1(f));
43.h.施作收尾:卸掉通气阀a23,将微型探测仪从注气孔a1进入,沿着注气通道a4匀速向内行进,行进过程中检验碳化层和扩大头12区域的碳化加固效果,如果检验不合格,对不合格区域进行二次碳化处理;当检验合格时,卸掉螺母2,在锚杆尾部进行防腐保护处理,完成锚杆施作。
44.下面结合附图2-5进行具体说明。
45.作为本发明的一种改进,所述锚杆包括注浆装置、注气装置和伸缩装置,所述注浆装置包括套筒7和注浆通道21,套筒7套设于锚杆装置的外部,注浆通道21设于套筒7壁的内部;所述注浆通道21的内径小于套筒7的壁厚,注浆通道21的数量根据套筒7直径确定,为3-12个,套筒7直径越大,注浆通道21数量越多;所述注气装置包括注气通道a4、注气通道b5、伸缩碳化器6、扩大头12、注气孔区a19、注气孔区b20、注气孔a1、注气孔b22、通气阀a23和通气阀b24;所述伸缩碳化器6固设在注气通道b5的外部,伸缩碳化器6包括碳化头13、注气孔区c14、限位筒15、升降盘b16、弹簧b17和注气通道c18;所述注气通道a4下方连通扩大头12,扩大头12的外表面设有注气孔区a19,注气通道a4上方设有注气孔a1,且注气孔a1上设有通气阀a23,所述注气通道b5上方的钢板3上设有注气孔b22,注气孔b22上设有通气阀b24,注
气通道b5连通伸缩碳化器6中的注气通道c18,且注气通道b5外表面设有注气孔区b20,注气通道c18连通碳化头13,且碳化头13上设有注气孔区c14,所述弹簧b17周向布置在升降盘b16的下方且弹簧b17的另一端与伸缩碳化器6外壳固定连接;所述限位筒15固设于伸缩碳化器6的上方并套设于注气通道c18的外部;所述伸缩装置包括钢板3、螺母2、限位盘8、弹簧a9、升降盘a10和刷子11,所述钢板3架设在注气通道b5的上方,所述螺母2设于钢板3上方,所述限位盘8和升降盘a10设于注气通道b5内部且注气通道a4外部,限位盘8与注气通道b5内壁固定连接,升降盘a10和注气通道a4外壁固定连接,限位盘8和升降盘a10之间用弹簧a9连接,升降盘a10与限位盘8之间的相对位移通过螺母2限定;当螺母2卸掉时,注气通道a4、扩大头12和升降盘a10组合而成的整体与注气通道b5和限位盘8组合成的整体可通过弹簧a9发生相对滑移,以适应岩土层的大变形。
46.作为本发明的另一种改进,所述套筒7的材质为硬质塑料或不锈钢,直径为100-300mm,所述套筒7拔出为顺时针和逆时针交替旋转进行,拔出的套筒7可循环利用;所述注浆通道21均匀地布设在套筒7壁内,注浆通道21的内径小于套筒7的壁厚,注浆通道21的数量根据套筒7直径确定,为3-12个,套筒7直径越大,注浆通道21数量越多。
47.作为本发明的另一种改进,所述浆液由平均粒径小于1mm的细粒料、水和减水剂组成,所述细粒料由碱性胶凝激发材料和工业固废组成,所述碱性胶凝激发材料由轻烧氧化镁、生石灰粉组成,所述工业固废由矿渣粉和污泥焚烧灰组成;所述浆液的水固比为0.4-0.7,碱性材料的含量越高,则水固比越大;所述碱性胶凝激发材料和工业固废分别占细粒料的20-50%和50-80%,所述轻烧氧化镁和生石灰粉分别占碱性胶凝激发材料的70-100%和0-30%,所述矿渣粉和污泥焚烧灰分别占工业固废的70-85%和15-30%。
48.作为本发明的另一种改进,所述co2是从高碳排放的煤电厂和水泥厂收集压缩的高压co2,所用co2浓度大于40%,所述第一设计通气压力为100~200kpa,所述第一设计碳化时间为3-12小时,第一设计通气压力和第一设计碳化时间根据碳化层的厚度确定,碳化层越厚,第一设计通气压力和第一设计碳化时间越大;所述第二设计通气压力为200~400kpa,所述第二设计碳化时间为6-12小时,第二设计通气压力和第二设计碳化时间根据锚杆长度和扩大头12直径确定,锚杆长度和扩大头12直径越大,第二设计通气压力和第二设计碳化时间越大。
49.下面将几何附图1-5和五个具体实施例予以说明。
50.本发明所用浆液由平均粒径小于1mm的细粒料、水和减水剂组成,所述细粒料由碱性胶凝激发材料和工业固废组成,所述碱性胶凝激发材料由轻烧氧化镁、生石灰粉组成,所述工业固废由矿渣粉和污泥焚烧灰组成,所述浆液的水固比范围0.4-0.7。水固比即水的体积与固相体积的比例,水固比越大,气体进入浆液中难度越大,需要相应增加通气压力和通气碳化时间。浆液中碱性胶凝激发材料和工业固废分别占细粒料的20-50%和50-80%,轻烧氧化镁和生石灰粉分别占碱性胶凝激发材料的70-100%和0-30%,矿渣粉和污泥焚烧灰分别占工业固废的70-85%和15-30%,碱性物料越多,占比越大,则碳化生成的物质越多,需要的碳化时间越多,因此也需要增加通气压力和通气碳化时间;工业固废(矿渣、污泥焚烧灰)活性较低,被碱性胶凝材料激发也需要一定时间,因此当工业固废的比例增大时,需增加通气碳化时间来保证其加固效果。套筒7的拔出方式为顺时针和逆时针交替旋转,其目的是防止锚杆孔被破坏,并且顺时针和逆时针交替旋转可以保证注浆的均匀性,保证碳化
层和扩大头12区域的完整性。
51.工作原理:锚杆的碳化层和扩大头区域注入由平均粒径小于1mm的细粒料、水和减水剂组成的浆体,浆体中包含活性氧化镁、生石灰、矿渣粉和污泥焚烧灰,氧化镁和生石灰可以激发矿渣粉和污泥焚烧灰发生碱激发反应,生成胶凝物质,使碳化层和扩大头区域具有一定初期强度,形状基本形成,通入co2使活性氧化镁和生石灰发生碳化反应,生成一系列对应的以镁为主的碱式碳酸盐,以进一步快速提高碳化层和扩大头12区域的强度,经过碱激发加固和碳化加固的碳化层和扩大头12区域共同作用,提高锚杆的整体支护强度。
52.首先,按照勘查资料和设计文件,确定锚杆孔的位置、间距、深度、直径与倾角,确定锚杆变截面处的深度、长度及直径,并在边坡坡面上放线;然后按照放线定位所确定的锚杆参数,使用锚杆钻机旋挖钻孔至设计深度,在设计的变截面处和底部调节钻机钻头的旋转直径,旋挖形成带变截面和扩大头12的锚杆孔,后用高压风枪将锚杆孔清理干净(如图1(a));然后将锚杆植入锚杆孔内,微调锚杆使锚杆的伸缩碳化器6对准锚杆孔的变截面,然后旋调螺母2固定注气通道a4(如图1(b));接着将注气孔a1和注气孔b22关闭,将注浆泵与套筒7上的注浆通道21上端连接,启动注浆泵,调节注浆压力,使浆液从套筒7壁内的注浆通道21下端喷出,待扩大头12中的浆液注满后,顺时针与逆时针交替旋转套筒7并向外拔出,浆液继续注入至锚杆外侧的碳化层区域,浆液注入和套筒7外拔同步进行,当浆液注满锚杆外侧的碳化层区域且套筒7完全被拔出时,关闭注浆泵,完成拔筒注浆(如图1(c));将co2高压气罐与注气孔b22连接,打开注气孔b22上的通气阀b24并调节第一设计通气压力,使co2气体通过注气通道b5上的注气孔区b20和伸缩碳化器6向碳化层区域扩散,通气养护后,关闭通气阀b24,完成碳化层的注气碳化(如图1(d));通过旋转螺母2调节与注气通道a4固定连接的升降盘a10位置,达到设计的预应力(如图1(e));碳化扩大头12区域:将co2高压气罐与注气孔a1连接,打开注气孔a1上的通气阀a23,调节第二设计通气压力,使co2气体通过注气通道a4的注气孔区a19向扩大头12区域扩散,通气养护后,关闭通气阀a23,完成扩大头12区域的注气碳化(如图1(f));
53.最后施作收尾,卸掉通气阀a23,将微型探测仪从注气孔a1进入,沿着注气通道a4匀速向内行进,行进过程中检验碳化层和扩大头12区域的碳化加固效果,检验合格时,卸掉螺母2,在锚杆尾部进行防腐保护处理,完成锚杆施作。
54.实施例具体数据取值如下:
55.实施例1
56.当浆液的水固比为0.4、细粒料由20%碱性激发物料和80%的工业固废组成时(其中碱性激发物料由70%轻烧氧化镁和30%生石灰粉组成,工业固废由70%矿渣和30%污泥焚烧灰组成),碳化层部分的通气压力为100kpa、通气时间为3h,扩大头12区域的通气压力为200kpa、通气时间为6h。
57.表1实施例1下的材料与施工参数
58.59.备注:p1:第一设计通气压力;t1:第一设计碳化时间;p2:第二设计通气压力;t2:第二设计碳化时间。
60.以下表格中的符号含义一致。
61.实施例2
62.当浆液的水固比为0.5、细粒料由30%碱性激发物料和70%的工业固废组成时(其中碱性激发物料由70%轻烧氧化镁和30%生石灰粉组成,工业固废由70%矿渣和30%污泥焚烧灰组成),碳化层部分的通气压力为150kpa、通气时间为3h,扩大头12区域的通气压力为300kpa、通气时间为6h。
63.表2实施例2下的材料与施工参数
[0064][0065][0066]
实施例3
[0067]
当浆液的水固比为0.5、细粒料由30%碱性激发物料和70%的工业固废组成时(其中碱性激发物料由80%轻烧氧化镁和20%生石灰粉组成,工业固废由80%矿渣和20%污泥焚烧灰组成),碳化层部分的通气压力为150kpa、通气时间为6h,扩大头12区域的通气压力为300kpa、通气时间为9h。
[0068]
表3实施例3下的材料与施工参数
[0069][0070]
实施例4
[0071]
当浆液的水固比为0.6、细粒料由40%碱性激发物料和60%的工业固废组成时(其中碱性激发物料由80%轻烧氧化镁和20%生石灰粉组成,工业固废由80%矿渣和20%污泥焚烧灰组成),碳化层部分的通气压力为150kpa、通气时间为9h,扩大头12区域的通气压力为300kpa、通气时间为9h。
[0072]
表4实施例4下的材料与施工参数
[0073][0074]
实施例5
[0075]
当浆液的水固比为0.7、细粒料由50%碱性激发物料和50%的工业固废组成时(其中碱性激发物料由100%轻烧氧化镁和0%生石灰粉组成,工业固废由85%矿渣和15%污泥焚烧灰组成),碳化层部分的通气压力为200kpa、通气时间为12h,扩大头12区域的通气压力为400kpa、通气时间为12h。
[0076]
表5实施例5下的材料与施工参数
[0077][0078][0079]
上述的具体实施例仅以说明和解释技术方案而不是对本方面的限制,本领域的普通技术员是应当理解的,也可以对本发明的技术方案进行修改或同等替换;在不脱离本发明技术方案精神实质和范围的条件下,均应涵盖在本发明的权利要求范围当中。