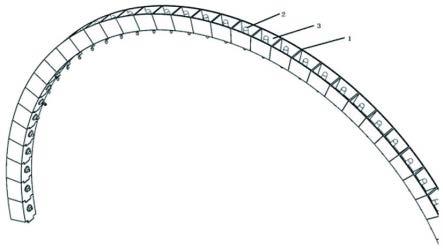
1.本发明属于隧道围岩加固支护技术领域,具体涉及吸水挤密隧道围岩的型钢格室承载拱支护结构技术,主要用于富水松散软弱土质隧道围岩的初期支护。
背景技术:2.近年来,随着西部地区高速铁路、公路等基础设施的不断加快,在黄土高原沟壑、梁峁区修建的黄土隧道工程越来越多,由于黄土是一种大孔隙、结构疏松、弱胶结、遇水具有湿陷性等特点的特殊土。黄土隧道初期支护结构多由系统锚杆、钢架、锁脚锚杆(管)、钢筋网、喷射混凝土等单独或组合使用,由于系统锚杆施工易诱发土体湿陷变形,且拱部锚杆受压,锚固效果发挥不明显,同时支护结构设计未考虑黄土的自承载能力,土拱效应发挥不足。如何充分利用围岩的自稳能力,发挥土拱效应,使围岩土体进入三向受力应力状态,是隧道围岩支护技术发展的方向。
技术实现要素:3.本发明的目的是提供一种吸水挤密隧道围岩的型钢格室承载拱支护结构及施工方法。
4.本发明是吸水挤密隧道围岩的型钢格室承载拱支护结构及施工方法,其中的吸水挤密隧道围岩的型钢格室承载拱支护结构,由型钢格室承载拱结构1和吸水挤密结构2构成,型钢格室承载拱结构1由沿隧道环向依次布置的单个型钢格室3构成、单个型钢格室3由第一类型钢板4和第二类型钢板5焊接构成、第一类型钢板4呈扇形或矩形、第二类型钢板5呈弧形、第二类型钢板5板面几何中心开有圆形的安装孔6、第二类型钢板5板面的左端中部呈矩形的凸出端、第二类型钢板5板面的右端中部呈矩形的凹进端、凸出端与凹进端的尺寸和形状相互匹配、在凸出端和凹进端端部均开有平行于板面的圆形销钉孔7、将两块第一类型钢板4板面平行同向放置、将第三块第一类型钢板4与前两块第一类型钢板4在板面端部垂直板面焊接形成“匚”形格室、将第二类型钢板5板面的凹进端与“匚”型格室的右开口端对齐布置、在第二类型钢板5的板面上垂直板面焊接“匚”型格室形成单个型钢格室3、沿隧道环向依次布置单个型钢格室3、相邻的单个型钢格室3之间通过销钉孔7采用销钉8销接后形成整体型钢格室承载拱结构1;吸水挤密结构2由填充干石灰的吸水外膜袋9和充气的挤密内膜袋10构成、吸水外膜袋9为圆柱形透水土工布膜袋、挤密内膜袋10为圆柱形橡胶膜袋、吸水外膜袋9与挤密内膜袋10呈同心圆柱状、吸水外膜袋9与挤密内膜袋10间填充吸水介质干石灰、挤密内模袋10充填气体、吸水挤密结构2封口处设有防漏气嘴11、将吸水挤密结构2通过圆形安装孔6依次装入整体型钢格室承载拱结构1的单个型钢格室3中,由空压机通过防漏气嘴11给挤密内膜袋10充气至设计压力,最终形成吸水挤密隧道围岩的型钢格室承载拱支护结构。
5.本发明的吸水挤密隧道围岩的型钢格室承载拱支护结构的施工方法,其步骤为:步骤(1)加工制作单个型钢格室3各构件:依据隧道开挖轮廓的曲率半径、吸水、挤
密加固范围,设计确定权利要求1所述的单个型钢格室3的第一类型钢板4和第二类型钢板5的尺寸、形状、曲率,现场或工厂焊接形成单个型钢格室3;步骤(2)加工制作吸水挤密结构2:依据吸水、挤密加固围岩土体的范围和处理后的土体抗剪强度目标参数,设计确定以上所述的吸水挤密结构2的半径、高度、填充干石灰的质量及设计挤密压力,根据设计参数向吸水外膜袋9和挤密内膜袋10间填充干石灰至设计填充质量后缝合、利用空压机通过防漏气嘴11给挤密内膜袋10充压至50%设计压力后关闭防漏气嘴11,形成吸水挤密结构2;步骤(3)测量放样:根据隧道分部开挖施工工序,确定围岩土体挤密加固处理范围,沿隧道环向依次测量定位放样型钢格室承载拱结构1的插入位置;步骤(4)型钢格室承载拱结构施工:根据隧道分部开挖施工工序,采用小型静力压桩机沿隧道环向按照定位边线安装单个型钢格室3、待单个型钢格室3未插入隧道围岩部分的高度约为10cm时,通过销钉孔7采用销钉8销接与下一个型钢格室3销接后将前一个型钢格室3静压到位,沿隧道环向依次静压施工单个型钢格室3并与相邻型钢格室3销接后形成整体型钢格室承载拱结构,同时在拱脚利用锁脚锚管(杆)对其锁定;步骤(5)吸水挤密结构安装孔开挖施工:沿隧道环向依次在单个型钢格室3的第二类型钢板5板面的圆形安装孔6处采用电动工具钻孔开挖土体至设计深度形成吸水挤密结构2的安装孔;步骤(6)吸水挤密结构安装施工:沿隧道环向依次将加工制作好的吸水挤密结构2通过圆形安装孔6插入开挖好的安装孔,由空压机通过防漏气嘴11逐个给吸水挤密结构2的挤密内膜袋10充压至100%设计压力、关闭防漏气嘴11,吸水挤密结构2与整体型钢格室承载拱结构1协同工作,形成具有“加筋”、“吸水”、“挤密”及“组合梁”效应的承载拱支护结构;步骤(7)喷射混凝土施工:利用喷浆机向围岩喷射混凝土,使吸水挤密围岩的型钢格室承载拱支护结构与围岩形成整体的初期支护层;步骤(8)按照步骤(3)~步骤(7)的步骤重复进入下一工作面的循环施工,直至施工结束。
6.本发明的有益效果:本发明将加筋、挤密、物理改良等技术应用到隧道围岩加固支护领域,通过型钢格室加筋挤密的钢箱梁承载拱支护结构,改善了隧道洞壁围岩的二向受力状态,使隧道围岩土体进入三向受力应力状态,既充分利用围岩的自稳能力,又发挥了土拱效应及组合梁效应,实现了对松动围岩的主动加固。与系统锚杆支护结构相比,具有以下优点:(1)利用型钢板对围岩土体起到了格室加筋作用,增强了围岩土体的整体性,形成了组合梁承载拱结构;(2)利用吸水挤密结构侧向挤密围岩使土体由二向受力状态真正进入三向受力应力状态,有效改善了围岩土体参数,促进了加筋效应、土拱效应的发挥,最大程度的利用了围岩的自承载能力;(3)型钢格室加筋挤密承载拱结构构造简单,可模块化加工组装,能够快速施工,及时封闭成环;(4)施工时减少了对围岩的扰动,解决了系统锚杆多次扰动围岩,锚杆施作不及时引起的围岩及地表变形问题;(5)型钢格室承载拱结构与格栅钢架易连接形成整体支护结构,接触状态优于锚喷支护结构,同时可减少钢架使用量,施工过程安全环保、节约材料,且具有一定的防排水功能。本发明工作原理简单,型钢格室制作及静压施工工艺成熟,结构易实现。
附图说明
7.图1是本发明的吸水挤密隧道围岩的型钢格室承载拱支护结构的整体安装示意图;图2是单个型钢格室结构单元示意图;图3是第一类型钢板示意图;图4是第二类型钢板示意图;图5是销钉、图6是吸水挤密结构示意图、图7是吸水挤密结构i-i剖面图。附图标记及对应名称:型钢格室承载拱结构1、吸水挤密结构2、单个型钢格室3、第一类型钢板4、第二类型钢板5、圆形膜袋安装孔6、销钉孔7、销钉8、吸水外膜袋9、挤密内模袋10、防漏气嘴11。
具体实施方式
8.本发明的工作原理为:(1)加筋原理:将型钢板焊接而成的单个型钢格室结构静压插入软弱土体,型钢格室结构能够有效限制围岩土体的侧向位移,改善了围岩土体的力学性能,提高围岩土体的强度和稳定性。
9.(2)吸水挤密原理:将吸水挤密结构安装在开挖好的安装孔中,通过给挤密内膜袋充压使膜袋侧向鼓胀,进而对型钢格室内围岩土体侧向挤压,使周围一定范围内的土体密实度提高,且相邻格室挤密效应叠加,改善了隧道洞壁围岩的二向受力状态,使围岩土体进入三向受力状态,提高了围岩土体的强度和稳定性。
10.(3)物理改良:通过填充干石灰的吸水外膜袋吸收周围土体中的水,降低了围岩的含水率,提高了围岩土体的抗剪强度参数。
11.(4)组合梁效应:沿隧道环向依次安装单个型钢格室结构形成整体的型钢格室承载拱支护结构,有效改善了围岩的应力分布。
12.下面结合附图及具体的实施实例对本发明进一步描述说明,所举实例只用于解释本发明,并非仅限制本发明的范围。本发明自公布日起,凡在本发明原理内所做的等同替换和改进都属于本发明的保护范围。
13.如图1所示,本发明的吸水挤密隧道围岩的型钢格室承载拱支护结构,主要包括型钢格室承载拱结构1和吸水挤密结构2,型钢格室承载拱结构1由相邻的单个型钢格室3通过销钉孔7采用销钉8沿隧道环向依次销接构成。
14.如图2~图4所示,单个型钢格室1由第一类型钢板4和第二类型钢板5焊接构成、第一类型钢板4呈扇形或矩形、第二类型钢板5呈弧形、第二类型钢板5板面几何中心开有圆形的安装孔6、第二类型钢板5板面的左端中部呈矩形的凸出端、第二类型钢板5板面的右端中部呈矩形的凹进端、凸出端与凹进端尺寸和形状相互匹配、在凸出端和凹进端端部均开有平行于板面的圆形的销钉孔7、将两块第一类型钢板4板面平行同向放置、将第三块第一类型钢板4与前两块第一类型钢板4在板面端部垂直板面焊接形成“匚”形格室、将第二类型钢板5板面的凹进端与“匚”型格室的右开口端对齐布置、在第二类型钢板5的板面上垂直板面焊接“匚”型格室形成单个型钢格室3、沿隧道环向依次布置单个型钢格室3。
15.如图5所示,销钉8呈圆柱形,沿隧道环向依次安装单个型钢格室3,相邻单个型钢格室3通过销钉孔7采用销钉8销接;如图6、图7所示,吸水挤密结构2由填充干石灰的吸水外膜袋9和充气的挤密内膜袋10构成、吸水外膜袋9为透水土工布膜袋、挤密内膜袋10为橡胶膜袋、吸水外膜袋9与挤密内膜袋10呈同心圆柱状、吸水外膜袋9与挤密内膜袋10间填充吸水介质干石灰、挤密内膜袋10填充气体、吸水挤密结构2封口处设有防漏气嘴11。
16.本发明的吸水挤密隧道围岩的型钢格室承载拱支护结构的施工方法,其步骤为:步骤(1)加工制作单个型钢格室3各构件:依据隧道开挖轮廓的曲率半径、吸水、挤密加固范围,设计确定权利要求1所述的单个型钢格室3的第一类型钢板4和第二类型钢板5的尺寸、形状、曲率,现场或工厂焊接形成单个型钢格室3;步骤(2)加工制作吸水挤密结构2:依据吸水、挤密加固围岩土体的范围和处理后的土体抗剪强度目标参数,设计确定以上所述的吸水挤密结构2的半径、高度、填充干石灰的质量及设计挤密压力,根据设计参数向吸水外膜袋9和挤密内膜袋10间填充干石灰至设计填充质量后缝合、利用空压机通过防漏气嘴11给挤密内膜袋10充压至50%设计压力后关闭防漏气嘴11,形成吸水挤密结构2;步骤(3)测量放样:根据隧道分部开挖施工工序,确定围岩土体挤密加固处理范围,沿隧道环向依次测量定位放样型钢格室承载拱结构1的插入位置;步骤(4)型钢格室承载拱结构施工:根据隧道分部开挖施工工序,采用小型静力压桩机沿隧道环向按照定位边线安装单个型钢格室3、待单个型钢格室3未插入隧道围岩部分的高度约为10cm时,通过销钉孔7采用销钉8销接与下一个型钢格室3销接后将前一个型钢格室3静压到位,沿隧道环向依次静压施工单个型钢格室3并与相邻型钢格室3销接后形成整体型钢格室承载拱结构,同时在拱脚利用锁脚锚管(杆)对其锁定;步骤(5)吸水挤密结构安装孔开挖施工:沿隧道环向依次在单个型钢格室3的第二类型钢板5板面的圆形安装孔6处采用电动工具钻孔开挖土体至设计深度形成吸水挤密结构2的安装孔;步骤(6)吸水挤密结构安装施工:沿隧道环向依次将加工制作好的吸水挤密结构2通过圆形安装孔6插入开挖好的安装孔,由空压机通过防漏气嘴11逐个给吸水挤密结构2的挤密内膜袋10充压至100%设计压力、关闭防漏气嘴11,吸水挤密结构2与整体型钢格室承载拱结构1协同工作,形成具有“加筋”、“吸水”、“挤密”及“组合梁”效应的承载拱支护结构;步骤(7)喷射混凝土施工:利用喷浆机向围岩喷射混凝土,使吸水挤密围岩的型钢格室承载拱支护结构与围岩形成整体的初期支护层;步骤(8)按照步骤(3)~步骤(7)的步骤重复进入下一工作面的循环施工,直至施工结束。