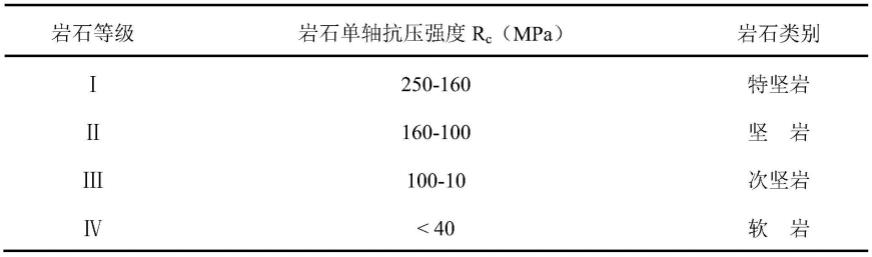
1.本发明属于煤矿施工技术领域,具体涉及一种陷落柱静态破裂方法。
背景技术:2.我国煤矿浅部资源逐渐枯竭,深部开采成为必然的发展趋势。然而,煤炭深部开采伴随着复杂的地质条件,我国华北地区的煤矿普遍存在岩溶陷落柱,岩溶陷落柱(简称陷落柱)是一种特殊隐伏垂向构造。煤矿开采遇见陷落柱内部岩石较硬时,影响采煤机正常工作,阻挡煤矿高效开采作业。目前煤矿主要采用直接硬过和修改设计避开两种方法,然而修改设计避开陷落柱会导致工程量加大、资源浪费。若开拓大巷前方遇见陷落柱,开拓大巷无法绕巷掘进,则需要强行硬过陷落柱的方法。强行硬过陷落柱时,由于陷落柱内部岩石介质的力学参数较大,综采机在切割时对截齿的消耗损伤较大,设备维修率较高,大幅度缩减设备使用寿命,导致矿井无法实现快速掘进作业。
3.目前,煤矿现场主要采用爆破方式降低煤岩硬度,这种方式存在一些问题,例如:需要大量炸药进行循环作业、爆破可能诱发巷道失稳甚至发生冲击地压、爆破作业过程中会产生大量粉尘,存在一定安全隐患。国内一些学者提出盐酸软化法,然而酸具有腐蚀性对截齿具有一定腐蚀伤害。酸与岩石介质发生反应挥发出刺激性气味,对作业人员健康有损害。
技术实现要素:4.基于上述问题,本发明提供一种陷落柱静态破裂方法,包括:
5.步骤1:采用物探与钻探方式联合探测陷落柱以确定陷落柱的边界、岩性和透水性;
6.步骤2:对陷落柱内部岩石进行钻探岩芯取样;
7.步骤3:采用岩石切割机将岩芯样本切割为圆柱形试样;采用电液伺服万能试验机对试样进行单轴抗压实验,确定试样的破坏荷载与抗压强度;采用x-射线衍射实验装置测定试样的矿物组分;
8.步骤4:确定静态破碎剂的组成成分、膨胀力、最优配比;具体过程如下:
9.步骤4.1:根据陷落柱破岩实际工程,综合考虑静态破碎剂的反应时间、破岩效果、现场施工效率,确定静态破碎剂主要成份为cao;水合延缓剂为石膏、膨润土、三聚磷酸钠;胶结增强剂为水泥;减水剂为聚羧酸、粉煤灰;
10.步骤4.2:将静态破碎剂灌入钢管中,当膨胀剂发生膨胀后,根据钢管的径向应力、切向应力以及应变计算静态破碎剂的膨胀力;
11.步骤4.3:设计正交实验,将静态膨胀剂成分设为实验因素,成分的不同含量设为实验水平,将膨胀力与反应时间作为实验评价指标,获取多组实验结果;
12.步骤4.4:计算各组实验结果的极差和均值,将极差小于设定阈值且均值小于设定阈值的一组实验成分配比作为最优的静态膨胀剂配比;
13.步骤5:按照多孔布置方式在试样上进行钻孔,确定钻孔的孔间距;具体过程如下:
14.步骤5.1:采用钻孔变频立式取芯机对试样进行钻孔;
15.步骤5.2:按照步骤4确定的最优配比制作静态膨胀剂,混合后灌入试样的钻孔中,每间隔一定时间观察一次,将裂纹不再发展时的时间作为静态破碎剂完全发挥作用的时间;
16.步骤5.3:记录试样在多孔布置方式下试样裂缝发育规律与时间的规律;
17.步骤5.4:根据裂缝发育规律与时间规律确定钻孔的布控方式;
18.步骤5.5:计算静态破碎剂钻孔布置间距a:
19.a=mw
[0020][0021]
式中:m为静态破碎剂间距系数;w为两个相邻静态破碎剂钻孔布置的最小抵抗线平均值;w1、w2为两个相邻静态破碎剂钻孔布置的最小抵抗线。
[0022]
步骤6:将最优配比与布置方式应用到煤矿现场陷落柱,根据现场陷落柱破碎程度选择确定采煤机型号进行静态破裂。
[0023]
本发明的有益效果是:
[0024]
本发明提出了一种陷落柱静态破裂方法,通过静态破碎致裂剂软化岩石,安全、快速直接过陷落柱,在陷落柱布置合适的钻孔,并注入静态破碎剂,利用静态膨胀剂使岩石发生有效胀裂,陷落柱内部岩石产生裂纹发生破碎,降低力学参数,提高煤矿安全,降低采煤机截齿的消耗,确保开拓大巷正常推进,操作简单、使用安全,具有较好的推广前景与应用价值。
附图说明
[0025]
图1为本发明中陷落柱静态破裂方法流程图;
[0026]
图2为本发明中静态破碎致裂布置方式为“矩形”和“正六边形”布控方式示意图;其中(a)为“矩形”布控方式示意图;(b)为“正六边形”布控方式示意图;
[0027]
图3为本发明中某矿开拓大巷过陷落柱灌入静态破碎致裂剂的钻孔布置平面示意图;
[0028]
图4为本发明中某矿开拓大巷过陷落柱灌入静态破碎致裂剂的钻孔布置剖面示意图;
[0029]
图中,1、岩溶陷落柱;2、某矿材料大巷;3、联络巷;4、某矿皮带大巷;5、静态致裂剂灌入钻孔;6、钻孔间距。
具体实施方式
[0030]
下面结合附图和具体实施实例对发明做进一步说明。
[0031]
如图1所示,本发明提供的一种陷落柱静态破裂方法,包括:
[0032]
步骤1:采用物探(地球物理勘探)与钻探方式联合探测陷落柱以确定陷落柱的边界、岩性和透水性;
[0033]
步骤2:对陷落柱内部岩石进行钻探岩芯取样;在取好样品后,用保鲜膜包裹样品,
防止样品在空气中发生氧化;
[0034]
步骤3:采用岩石切割机将岩芯样本切割为圆柱形试样;将其切割成尺寸为50mm
×
100mm(直径
×
高度)的圆柱形试样。采用电液伺服万能试验机对试样进行单轴抗压实验,确定试样的破坏荷载与抗压强度;采用x-射线衍射实验装置测定试样的矿物组成成分;
[0035]
根据单轴抗压强度查表1得到岩石坚硬程度,确定岩石类别,然后就可以设计实验确定钻孔的排距、布置方式。
[0036]
表1岩石坚硬程度表
[0037][0038]
步骤4:确定静态破碎剂的组成成分、膨胀力、最优配比;具体过程如下:
[0039]
步骤4.1:根据陷落柱破岩实际工程,综合考虑静态破碎剂的反应时间、破岩效果、现场施工效率,确定静态破碎剂主要成份为cao;水合延缓剂为石膏、膨润土、三聚磷酸钠;胶结增强剂为水泥;减水剂为聚羧酸、粉煤灰;
[0040]
步骤4.2:将静态破碎剂灌入钢管中,当膨胀剂发生膨胀后,根据钢管的径向应力、切向应力以及应变计算静态破碎剂的膨胀力;
[0041]
步骤4.3:设计正交实验,将静态膨胀剂成分设为实验因素,成分的不同含量设为实验水平,将膨胀力与反应时间作为实验评价指标,获取多组实验结果;
[0042]
步骤4.4:计算各组实验结果的极差和均值,将极差小于设定阈值且均值小于设定阈值的一组实验成分配比作为最优的静态膨胀剂配比;
[0043]
步骤5:按照多孔布置方式在试样上进行钻孔,确定钻孔的孔间距与排距;具体过程如下:
[0044]
步骤5.1:采用钻孔变频立式取芯机对试样进行钻孔,控制钻进速度为1cm/min左右,使试样预留直径为2.5cm、宽度为0.25cm的钻孔缝隙;
[0045]
步骤5.2:按照步骤4确定的最优配比制作静态膨胀剂,混合后灌入试样的钻孔中,每间隔10min观察一次,将裂纹不再发展时的时间作为静态破碎剂完全发挥作用的时间;
[0046]
步骤5.3:记录试样在多孔布置方式下试样裂缝发育规律与时间的规律;
[0047]
步骤5.4:根据裂缝发育规律与时间规律确定钻孔的布控方式;
[0048]
步骤5.5:计算静态破碎剂钻孔布置间距a:
[0049]
a=mw
[0050][0051]
式中:m为静态破碎剂间距系数;w为两个相邻静态破碎剂钻孔布置的最小抵抗线平均值;w1、w2为两个相邻静态破碎剂钻孔布置的最小抵抗线。
[0052]
步骤6:将最优配比与布置方式应用到煤矿现场陷落柱,根据现场陷落柱破碎程度
选择确定采煤机型号进行静态破裂。
[0053]
本实施例分别设置了单孔和多孔两种钻孔布置方式以此来确定哪种方式更优。
[0054]
本实施例在单孔布置时至少会产生三条裂缝,他们之间夹角在120
°
左右;多孔布置时,主裂缝与其他小裂缝之间夹角在90
°
左右;根据裂缝发育规律确定现场陷落柱钻孔为“正六边形”或“矩形”布控方式,如图2所示。
[0055]
本实施例参考《gb 50862-爆破工程工程量计算规范》,根据如下公式计算静态破碎剂钻孔布置间距:
[0056]
a=mw
[0057][0058]
式中:a为两个相邻静态破碎剂钻孔布置间距,m;m为静态破碎剂间距系数,一般取0.8-1.2。w为两个相邻静态破碎剂钻孔布置的最小抵抗线平均值。w1、w2为两个相邻静态破碎剂钻孔布置的最小抵抗线,m。
[0059]
本实施例最终确定的多孔布置方式、正多边形的布控方式,其孔间距为400-500mm,根据现场陷落柱破碎程度最终确定采煤机型号为mg400/930-wd。图4为钻孔布置的剖面示意图,将静态破碎剂灌入钻孔5中,根据步骤5.4确定合理静态破碎剂钻孔间距6为400-500mm。
[0060]
图3为某矿采掘平面布置图,在平面图中1为陷落柱;2为某矿的材料大巷,担任某矿的材料运输任务;3为联络巷;4为某矿的皮带巷,主要担任运煤任务;5为施加静态破碎剂布置的钻孔;根据步骤4与步骤5得到的最优配比为cao75%;水合延缓剂为石膏3%、膨润土5%、三聚磷酸钠0.6%;胶结增强剂为水泥8%;减水剂为聚羧酸0.4%、粉煤灰8%,多孔布置方式孔间距为400-500mm应用到某矿现场陷落柱进行破碎。