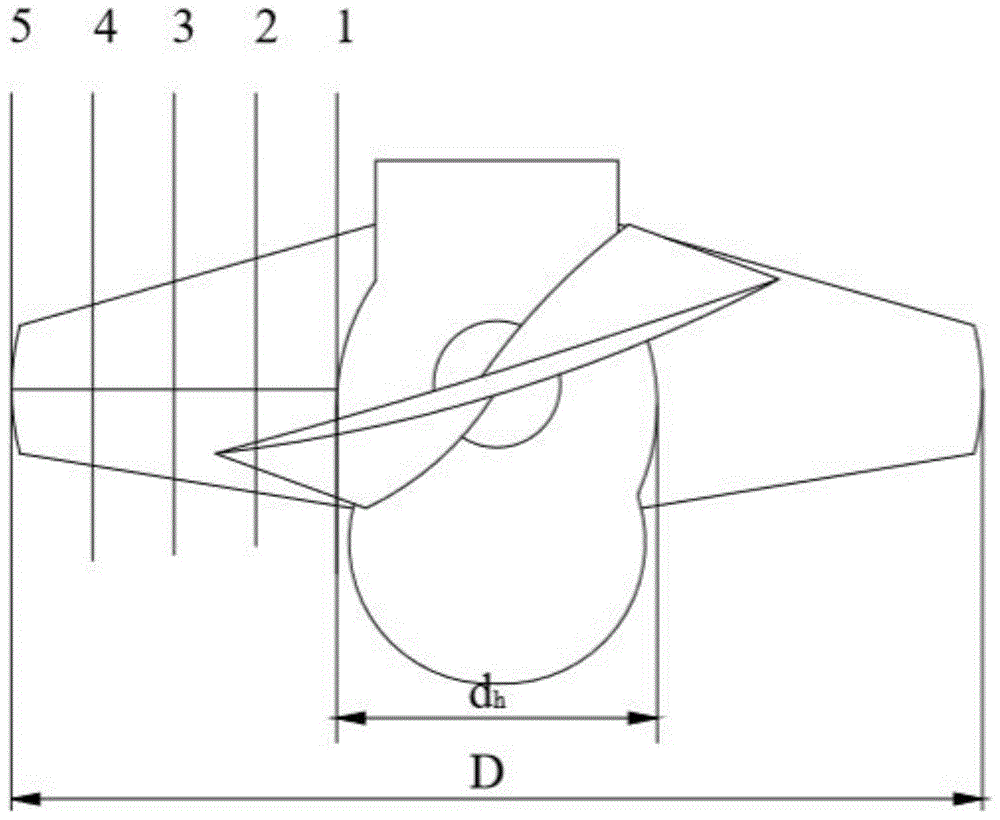
本发明属于流体机械设计领域,特指涉及一种基于轴距的轴流泵叶轮设计方法。
背景技术:
:泵站和水闸是水利、环保、城市供排水及企业水务等工程的重要组成部分,其中泵是排灌设备,闸是调节水位、控制流量的低水头水工建筑物。传统泵闸建设通常采用轴流式水泵和水闸相结合的方式,即沿着河道横截面处,在中间布置一扇闸门,闸门两边各布置一台水泵的形式。这种泵闸的泵、闸分离设计导致传统泵闸排水量远低于实际需要,汛期往往不能及时有效的进行疏洪,进行河流换水治污的效率也远远低于理想值,同时这种布置方式也限制了河道的过水断面,减缓了河流流动,对内河的水量交换和水体循环不利,不能满足内河水生态环境的要求,弱化了河流的自净能力。新型一体化泵闸,将泵组直接布置在闸门上,闸门既是挡水结构又是水泵支承的基础,使水闸和泵站合二为一。与传统泵闸相比,一体化泵闸具有如下优点:(1)泵垂直安装于闸门上,不需要额外的泵室,升闸时可使河流的过流面积增大1倍以上,落闸时泵可明显提高排水速度;(2)只需要配电室、水泵、闸门和拍门,不建主厂房,没有辅助油、水、气系统,占地面积小,施工方便、快捷,从而减少了泵站的土建和机电设备投资;(3)通过安装液位控制系统和闸门自动控制系统等辅助设施,可以使整个系统联动控制,真正实现无人值守,自动控制,大幅降低了泵闸后期人员维护费用。目前关于一体化泵闸的设计多集中在优化闸门结构和与改善前后水池流动状态的研究;轴流泵作为一体化泵闸的关键动力设备一般都是从现有产品中直接选型。事实上,由于闸门厚度的限制,一体化泵闸要求轴流泵的轴向长度要尽可能的短。轴流泵轴向长度过大,闸门越厚,导致一体化泵闸的设计、制造、运行和维护成本都会大幅提升,同时闸门的响应速度也会大幅下降。这就使得现有轴流泵产品并不能很好的满足一体化泵闸的结构和性能要求。因此,迫切需要发展一种简单实用的基于轴距的轴流泵叶轮设计方法,使得其既能保证轴流泵水力性能,又能根据实际需要有效控制轴流泵叶轮的轴向长度。为此,提出一种基于轴距的轴流泵叶轮设计方法,该方法以l=l×sinβl为基础,通过流量q、扬程h和转速n并基于实际需要,确定轴流泵叶轮翼型弦长l和叶片安放角βl的取值;并以叶轮翼型弦长l和叶片安放角βl为基础,确定叶轮其余设计参数叶轮直径d、轮毂直径dh和节距t。最后,选择791翼型厚度变化规律进行叶片加厚。迄今为止,尚未见一种基于轴向长度的轴流泵叶轮设计方法公开报道,本发明提供了一种基于轴距的轴流泵叶轮设计方法。技术实现要素:本发明的目的是提供一种基于轴距的轴流泵叶轮设计方法,包括如下步骤:s1:以轴流泵轴向距离l=l×sinβl为基础,根据给定的轴流泵设计流量q、扬程h、转速n、比转速ns设计参数,从叶轮轮毂至叶轮外缘等间距划分断面,通过比转速ns确定断面数和叶片数;然后确定轴流泵叶轮轴向长度l的翼型弦长l和叶片安放角βl;s2:当l1/lw=0.95~1;其中,l1为设计要求轴向长度;lw最外侧断面的轴向长度;选取轴流泵叶轮参数翼型弦长l,叶弦安放角βl为基准参数,确定叶轮直径d,轮毂直径dh,节距t;s3:以翼型弦长l为基准,选择791翼型厚度变化规律进行叶片加厚。本发明的技术方案为:步骤s1中,通过流量q、扬程h、转速n确定翼型弦长l和叶片安放角βl,计算方法如下:(1)确定叶轮设计断面数量和叶片数将轴流泵叶轮分为4~6个断面,从叶轮轮毂至叶轮外缘等间距划分断面;断面数和叶片数通过比转速ns确定;比转速nsns≤450450≤ns≤800800≤ns叶轮断面数456比转速nsns≤600600≤ns≤850850≤ns≤1500叶片数543(2)根据升力法计算翼型弦长l翼型弦长lc通过最外侧断面翼型弦长lw确定;当叶轮断面数为6时,最外侧断面即为断面6;当叶轮断面数为5时,最外侧断面即为断面5;当叶轮断面数为4时,最外侧断面即为断面4;其中,a为修正系数,取值方法如下所示;翼型断面翼型弦长lc通过以下通式确定:lc=a1×lw其中,a1为比例系数,具体取值如下表所示:(3)根据升力法计算叶片安放角βl翼型断面叶片安放角βlc通过最外侧叶片安放角βlw确定;最外侧断面叶片安放角βlw的计算方法如下所示:其中,vm1进口轴面速度;vm2出口轴面速度;u圆周速度;vu2旋转分速度;β1叶片进口角;叶片出口角;b为修正系数,通过比转速确定;比转速ns0~380380~610610~930930~1500修正系数b(6个断面)0.21~0.280.16~0.210.12~0.160.05~0.12修正系数b(5个断面)0.19~0.240.13~0.190.08~0.130.03~0.08修正系数b(4个断面)0.16~0.220.13~0.160.07~0.130.03~0.07翼型断面叶片安放角βlc通过以下通式确定:βlc=b1×βlw其中,b1为比例系数,具体取值如下表所示:(4)轴向长度l通过l=l×sinβl确定轴流泵叶轮的轴向长度;l1为设计要求轴向长度;lw最外侧断面的轴向长度;设计误差允许范围为5%,即l1/l=0.95~1;若l1>l且误差大于5%,则返回步骤(2)增大修正系数a的取值,或者返回步骤(3)增加修正系数b的取值;若l1<l且误差大于5%,则返回步骤(2)减小修正系数a的取值,或者返回步骤(3)减小修正系数b的取值。步骤s2中,通过翼型弦长l和叶片安放角βl确定叶轮直径d,轮毂直径dh,节距t;(1)叶轮直径d各断面的叶轮直径dc通过以下通式确定;叶轮最大直径dw通过以下通式确定其中,c为比例系数,k为修正系数,具体取值如下表所示;(2)叶轮轮毂直径dh其中,dw为叶轮最大直径,轮毂比通过比转速ns+3.87×sinβl确定;当ns+3.87×sinβl≤470,当470≤ns+3.87×sinβl≤720,当720≤ns+3.87×sinβl≤940,当940≤ns+3.87×sinβl≤1200,当1200≤ns+3.87×sinβl≤1500,(3)节距t各断面节距tc通过以下通式确定;步骤s3中,选择791翼型厚度变化规律进行叶片加厚;(1)翼型最大厚度δmax(2)以翼型弦长l为基准,采用791翼型厚度变化规律进行加厚;791翼型厚度变化规律如下表所示;x为距翼型左侧边缘的距离,δ为翼型厚度;(3)加厚时,以型线为工作面向背面加厚。本发明的有益效果为:(1)采用基于轴距轴流泵叶轮设计方法,可实现与较短轴向长度的一体化泵闸的完美配合;(2)相比于通过相似模型换算的传统设计方法,不仅效率低而且适应性差,本方法给定了快速确定轴流泵叶轮尺寸的公式,具有适应性好,计算快,效率高的优点;(3)现有的轴流泵水力设计方法大多以保证流量扬程为主,并导致轴流泵轴向长度过长,本设计方法可在保证流量扬程的同时控制轴流泵轴向长度;(4)建立的基于轴距轴流泵叶轮设计方法具有建造周期短、建造成本低的优点;(5)建立的基于轴距轴流泵叶轮设计方法可为解决一体化泵闸的发展瓶颈提供出路;(6)随着国家水力工程的建设,国家大型和中小型泵站的更新换代,对于轴流泵各参数的要求将越来越高,因此本发明将会取得较高的经济效益和社会效益。附图说明图1为实施例1叶轮轴向剖视图。图2叶片剖视图。图3翼型加厚示意图。图4为本发明的流程图。图中,l为翼型弦长、βl为叶片安放角、d为叶轮直径、dh为轮毂直径、t为节距,1为断面1,2为断面2,3为断面3,4为断面4,5为断面5,x为距翼型左侧边缘的距离,δ为翼型厚度,δmax为翼型最大厚度。具体实施方式实施例:轴流泵设计流量q=0.35m3/s,扬程h=6.72m,转速n=1450r/min,设计轴向长度l1=26mm。下面对本发明做进一步的说明:1.通过流量q、扬程h、转速n确定翼型弦长l和叶片安放角βl,计算方法如下:(1)确定叶轮设计断面数量和叶片数根据下表,取叶轮断面数为5比转速nsns≤450450≤ns≤800800≤ns叶轮断面数456根据下表,取z=4;比转速ns0~600600~850850~1500叶片数z345(2)翼型弦长l断面5的翼型弦长l5根据下表,取a=6;叶片数z345修正系数a3.4~5.85.8~7.67.6~9.4所以断面4的翼型弦长l4根据l4=a1×l5=(0.931~0.963)×l5,取l4=0.951×l5=0.951×79.2=75.3mm断面3的翼型弦长l3根据l3=a1×l5=(0.826~0.894)×l5,取l3=0.842×l5=0.842×79.2=66.7mm断面2的翼型弦长l2根据l2=a1×l5=(0.712~0.787)×l5,取l2=0.762×l5=0.762×79.2=60.4mm断面1的翼型弦长l1根据l1=a1×l5=(0.623~0.685)×l5,取l1=0.651×l5=0.651×79.2=51.6mm(3)叶片安放角βl断面5的叶片安放角βl5因为ns=750,根据下表,取b=0.1;比转速ns0~380380~610610~930930~1500修正系数b0.19~0.240.13~0.190.08~0.130.03~0.08断面4的叶片安放角βl4根据βl4=b1×βlw=(1.06~1.15)×βl5,取βl4=1.12×βl5=1.12×19.29=21.60°;断面3的叶片安放角βl3根据βl3=b1×βlw=(1.22~1.34)×βl5,取βl3=1.31×βl5=1.31×19.29=25.27°;断面2的叶片安放角βl2根据βl2=b1×βlw=(1.43~1.68)×βl5,取βl2=1.53×βl5=1.53×19.29=29.51°;断面1的叶片安放角βl2根据βl1=b1×βlw=(1.84~2.18)×βl5,取βl1=2.02×βl5=2.02×19.29=38.97°;(4)轴向长度llw=l×sinβlw=79.2×sin19.29°=26.16mm误差范围小于5%,满足设计要求;2.通过翼型弦长l和叶片安放角βl确定叶轮直径d,轮毂直径dh和节距t,计算方法如下:(1)叶轮直径d断面5的叶轮直径d5断面4的叶轮直径d4断面3的叶轮直径d3断面2的叶轮直径d2断面1的叶轮直径d1(2)叶轮轮毂直径dh因为ns+3.87×sinβl=750+3.87×sin38.58°=752,根据下表,取(3)节距t断面5的节距t5断面4的节距t4断面3的节距t3断面2的节距t2断面1的节距t13.以翼型弦长l为基准,采用791翼型厚度变化规律进行加厚;(1)断面5的翼型厚度a.翼型最大厚度δmax根据取b.以翼型弦长l为基准,采用791翼型厚度变化规律进行加厚;其对应翼型厚度为下表所示:(2)断面4的翼型厚度a.翼型最大厚度δmax根据取b.以翼型弦长l为基准,采用791翼型厚度变化规律进行加厚;791翼型厚度变化规律如下表所示;(3)断面3的翼型厚度a.翼型最大厚度δmax根据取b.以翼型弦长l为基准,采用791翼型厚度变化规律进行加厚;791翼型厚度变化规律如下表所示;(4)断面2的翼型厚度a.翼型最大厚度δmax根据取b.以翼型弦长l为基准,采用791翼型厚度变化规律进行加厚;791翼型厚度变化规律如下表所示;(5)断面1的翼型厚度a.翼型最大厚度δmax根据取b.以翼型弦长l为基准,采用791翼型厚度变化规律进行加厚;791翼型厚度变化规律如下表所示;(6)加厚时,以型线为工作面向背面加厚。当前第1页12