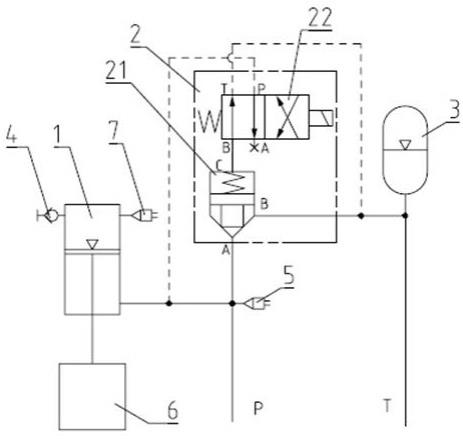
一种油缸加力装置及其加力方法
1.技术领域
2.本发明涉及工程机械技术领域,更具体地说,特别涉及一种油缸加力装置及其加力方法。
3.
背景技术:4.目前液压冲击锤的大多采用单作用液压系统,油缸将重锤提升至一定高度后释放,重锤自由下落,由于重锤高速下落时油缸下腔排油阻力及上腔补油阻力大,实际落锤加速度小于1g ,落锤末速度及冲击能量小于自由落体。单作用液压冲击锤一般竖直使用或小角度倾斜,可满足大多使用工况。
5.为了提高冲击效能,部分液压冲击锤采用双作用液压系统,如差动落锤技术。落锤时油缸无杆腔、有杆腔及回油管等连通,利用活塞两侧面积差与平衡压力的乘积加力。由于与回油管连通,平衡压力低,加力水平低,仅能少量抵消液流阻力。
6.发明cn201911099054.7 公开了一种效能较高的差动落锤技术。回油油路设有与无杆腔连通的背压阀,蓄能器,重锤提升时无杆腔排油向蓄能器充液,达背压阀开启压力时多余油液回油箱;落锤时有杆腔也与无杆腔、蓄能器连通,最大平衡压力为背压阀设定开启压力。差动力可有效抵消液流阻力,背压大时差动力大于液流阻力,落锤速度大于自由落体。缺点是背压大时,背压阀开启瞬间对回油管冲击大,剧烈抖动。
7.作为液压锤典型案例,中央电视台公开报道了一款大国重器:太原重型机械集团有限公司的“tz-1900双作用式全液压打桩锤”,重锤质量200t、最大落锤高度1.5m、最大落锤高度时击打能量1900kj,其击打能量仅为重锤势能的63%(落锤加速度0.63g),相当于不足1m的自由落体。“双作用式全液压”的加力效果远未抵消落锤时的液流阻力。可见,直接向油缸上腔提供压力油加力及相关落锤加力技术也未必能够有效提高落锤速度。
8.只有在有效降低落锤瞬间的排油、补油阻力的前提下,提高油缸无杆腔压力方可显著提高液压锤冲击效能。
9.国家严格控制炸药爆破作业后,铁矿等地下矿藏开采时只能在狭小的巷道使用小型挖掘机拖带的液压破碎锤,效率低、死角大。需要一种冲击能大,可倾斜及向上击打的破碎设备。山体开挖、露天开采、隧道开掘维修等也需大角度倾斜击打。当液压冲击锤击打能量大于势能、甚至达2倍以上势能时可满足需求。
10.
技术实现要素:11.本发明的目的在于提供一种提升液压冲击锤冲击效能的液压冲击锤油缸装置及其加力方法。
12.为了达到上述目的,本发明采用的技术方案如下:一种油缸加力装置,包括落锤系
统,落锤系统包括液压站、油缸、提升阀、蓄能器和充气阀,所述油缸为竖向设置、活塞杆向下的双作用单活塞杆液压缸,无杆腔设有充气阀并充有氮气或空气或惰性气体,液压站供油压力或设定工作压力与有杆腔容积的乘积大于重锤提升所需压力与获得设定势能所需有杆腔容积的乘积,其活塞杆端部联接有重锤,所述提升阀为二通基本插件与二位四通电磁换向阀组成的二通插装阀,二通基本插件为锥阀式或滑阀式,所述液压站的压力管接所述油缸有杆腔油口和二通基本插件的进油口,二通基本插件出油口接蓄能器和液压站的回油管,所述二位四通电磁换向阀的进油口接所述液压站的压力管,其回油口接液压站的回油管,其常通出油口封闭或连通其回油口,其另一出油口接二通基本插件的控制口。
13.优选地,压力管路上设有压力传感器ⅰ。
14.优选地,油缸的无杆腔上设有压力传感器ⅱ。
15.优选地,所述提升阀可用具有接通、断开压力管与回油管连接的等效开关阀、方向阀替代,如外控(电控、液控)截止阀(闸阀、开关阀等)可替代所述提升阀。
16.优选地,所述提升阀用二位四通换向阀或中位时进回油口连通的三位四通换向阀替代,进油口p接所述液压站的压力管和油缸1有杆腔油口,其回油口t接蓄能器和液压站的回油管,其一个出油口封闭,其另一出油口连通其回油口或接回油管。
17.优选地,所述提升阀的先导阀二位四通电磁换向阀用三位四通电磁换向阀替代,进油口p接所述液压站的压力管和油缸1有杆腔油口,其回油口t接蓄能器和液压站的回油管,其一个出油口封闭,其另一出油口接二通基本插件的控制口c,中位时连接二通基本插件控制口c的油口与回油口连通。
18.优选地,油缸的无杆腔连通空气(大气)。
19.利用上述油缸加力装置,其加力方法如下:s1、正常停机状态时,由于提升阀的先导阀二位四通电磁换向阀的b、t口常通,二通基本插件相当于单向阀,油缸的有杆腔、动力站进油管通过二通基本插件与蓄能器、动力站回油管连通,重锤稳定在初始位;s2、二位四通电磁换向阀的电磁铁通电后换向,二位四通电磁换向阀的进油口p、出油口b连通,二通基本插件的c口加压后封闭进油口a,压力油向油缸有杆腔供油,推动活塞,重锤提升,由于液压站供油压力或设定工作压力(以下简称额定压力)大于重锤提升所需压力,重锤提升同时压缩无杆腔内气体蓄能,无杆腔气体还可缓冲重锤落锤变为提升瞬间的液流冲击;s3、二位四通电磁换向阀的电磁铁断电后复位(采用双电磁铁时另一电磁铁通电后复位),二位四通电磁换向阀的进油口p与常通出油口a连通、另一出油口b与回油口t连通,二通基本插件呈单向阀状态,重锤在重力及无杆腔压缩气体的共同作用下加速下落,油缸有杆腔排出的液压油及动力站供油通过二通基本插件及回油管回液压站,蓄能器3缓冲重锤提升变为下落瞬间的液流冲击及降低瞬时回油压力,落锤时动力站供油也可另设回路利用;s4、无杆腔充气或直通大气时,不存在无杆腔进排油时的液流损失,与加力技术等效;s5、压力管路上设有的压力传感器ⅰ可实时监控系统压力,根据工作需要及实时工况自动或人工调整冲击能量及统计计算;
s6、油缸无杆腔路上设有压力传感器ⅱ可直接获得无杆腔气体动态压力,便于精确调整、控制击打能量。
20.当结构及其它系统参数一定且不计损耗时(本设定适用全文),重锤势能等于重锤重力折算压力(重锤重力/有杆腔活塞面积,下同)与油缸活塞杆回缩行程的乘积,提升重锤的压力功等于重锤折算压力与有杆腔容积(有杆腔活塞面积与活塞杆回缩行程的乘积)的乘积。额定压力与重锤重力折算压力之差用于压缩无杆腔气体蓄能。所以,重锤击打动能等于重锤势能与气体压力能之和,大于势能。
21.与现有技术相比,本发明的优点在于:1、本发明不存在落锤及提升时无杆腔的进排油阻力,系统效能提高,系统温升降低。
22.2、重锤提升的同时压缩无杆腔气体、积蓄能量,落锤时被压缩气体释放能量,具有确定的加速落锤效果。
23.3、可实现大角度倾斜击打及向上击打,满足多种施工需求。
24.4、可用较小规格的本发明等效替代较大规格的单作用等低效液压冲击锤,匹配较小的挖掘机等承载设备,适应更小施工空间,降低使用成本,适用范围更广。
25.因此,本发明具有提高液压冲击锤击打效能及适用范围广的特点。
26.附图说明
27.为了更清楚地说明本发明实施例或现有技术中的技术方案,下面将对实施例或现有技术描述中所需要使用的附图作简单地介绍,显而易见地,下面描述中的附图仅仅是本发明的一些实施例,对于本领域普通技术人员来讲,在不付出创造性劳动的前提下,还可以根据这些附图获得其他的附图。
28.图1是本发明实施例一和实施例二的结构框图。
29.图中:1油缸、2提升阀、21二通基本插件、22二位四通电磁换向阀、3蓄能器、4充气阀、5压力传感器ⅰ、6重锤、7压力传感器ⅱ。
具体实施方式
30.下面结合附图对本发明的优选实施例进行详细阐述,以使本发明的优点和特征能更易于被本领域技术人员理解,从而对本发明的保护范围做出更为清楚明确的界定。
31.实施例1附图1为本实施例的附图,本实施例为本发明的基础方案。
32.一种油缸加力装置,包括液压系统,液压系统包括液压站、油缸1、提升阀2、蓄能器3、和充气阀4,所述油缸1为双作用单活塞杆液压缸,无杆腔油口设有充气阀4并充有氮气或空气或惰性气体,额定压力与有杆腔容积的乘积大于重锤6提升所需压力与获得设定势能所需有杆腔容积的乘积,油缸1竖向安装在机架上,垂直向下的活塞杆端部联接有重锤6,所述提升阀2为二通基本插件21与二位四通电磁换向阀22组成的二通插装阀,所述液压站的压力管接油缸1的有杆腔油口和二通基本插件11的进油口a,所述二通基本插件21出油口b接蓄能器3、回油管,所述二位四通电磁换向阀22的进油口p接所述液压站的压力管,其回油
口t接液压站的回油管,其常通出油口a封闭或连通其回油口,其另一出油口b接二通基本插件21的控制口c。
33.为了方便理解工作原理,附图中各阀体的各口均通过字母进行标记。
34.其工作方法为:正常停机状态时,由于提升阀2的先导阀二位四通电磁换向阀22的b、t口常通,二通基本插件21相当于单向阀,提升缸1的有杆腔、动力站进油管通过二通基本插件21与蓄能器3、动力站回油管连通,重锤6稳定在初始位;二位四通电磁换向阀22的电磁铁通电后换向,二位四通电磁换向阀22的p、b口连通,二通基本插件21的c口加压a口封闭,压力油推动油缸1有杆腔活塞,重锤6提升的同时压缩无杆腔气体。积蓄能量等于提升重锤6至设定高度所做压力功与压缩气体所做压力功之和,油缸1的无杆腔气体可缓冲重锤6落锤变为提升瞬间的液流冲击;二位四通电磁换向阀22的电磁铁断电后复位,二位四通电磁换向阀22的p、a口通、b、t口通,二通基本插件21呈单向阀状态,重锤6在重力及油缸1无杆腔压缩气体的共同作用下加速下落,击打功等于重锤提升时积蓄能量,即重锤势能与气体压力能之和,油缸1有杆腔排出的油液通过二通基本插件21的a口、b口及回油管回动力站,蓄能器3可缓冲有杆腔由回缩瞬间转换为伸出时的液流冲击及降低回油阻力;压力管路上设有的压力传感器ⅰ5可实时监控系统压力,根据工作需要及实时工况自动或人工调整冲击能量及统计计算;油缸1的无杆腔可设有压力传感器ⅱ7,直接测得无杆腔气体压力,减少计算误差及液流损失等因素影响。
35.本发明不存在落锤及提升时无杆腔的液流阻力,系统效能提高,系统温升降低。
36.重锤提升的同时压缩无杆腔气体、积蓄能量,落锤时被压缩气体释放能量,具有确定的加速落锤效果。
37.可用较小规格的本发明等效替代较大规格的单作用等低效液压冲击锤,匹配较小的挖掘机等承载设备,适应更小施工空间,降低使用成本,适用范围更广。
38.因此,本发明的本实施例具有提高液压冲击锤击打效能的作用和特点及节能。
39.实施例2山体开挖、边坡加固时液压冲击锤需大角度倾斜作业;地下巷道破碎采矿及隧道开挖维修时需水平击打,甚至向上击打破碎,单作用或加力水平低的双作用液压冲击锤不适用,本发明的本实施例可实现。本实施例为水平击打及垂直向上击打工况。
40.设定条件同实施例1。
41.水平击打活塞杆回缩时重力轴向分力为0,活塞杆初始回缩压力等于折算充气压力(充气压力
×
无杆腔活塞面积/有杆腔活塞面积,下同),活塞杆最大回缩压力等于额定压力,气体压缩过程液压油做功的累积量,即积蓄的能量,亦即击打能量。
42.压力传感器ⅰ5可通过压力管压力计算无杆腔气体压力,从而自动或人工调整击打能量。通过对活塞杆初始回缩压力的测定可计算倾斜角度及调减活塞杆回缩压力。
43.油缸1无杆腔可设有压力传感器ⅱ7,直接测得无杆腔气体压力,减少计算误差及液流损失等因素影响。
44.垂直向上击打时,重力的轴向分力的大小同重力,为活塞杆回缩推力,活塞杆初始
回缩压力等于充气折算压力与重力折算压力之和,活塞杆最大回缩压力等于额定压力与重力折算压力之和,气体压缩过程液压油做功的累积量,即积蓄的能量,积蓄能量大于重锤势能时具有向上击打能量。额定压力与重锤6势能要求一定时,击打能量大小取决于油缸1有杆腔活塞面积。
45.向下击打时重锤加速度达2g时,向上击打时的重锤加速度可达1g。
46.本实施例可见,动力站额定压力(一般31.5mpa)及重锤质量一定时,可通过调整油缸结构参数及充气压力改变加力水平,通过监测调整工作压力可控制击打能量。
47.本实施例及实施例1可见,本发明的本实施例能够实现360
)
全方位击打作业,改变了大质量重锤只能向下击打的传统作业方式和思维定式,扩大了液压冲击锤的应用范围。虽然结合附图描述了本发明的实施方式,但是专利所有者可以在所附权利要求的范围之内做出各种变形或修改,只要不超过本发明的权利要求所描述的保护范围,都应当在本发明的保护范围之内。