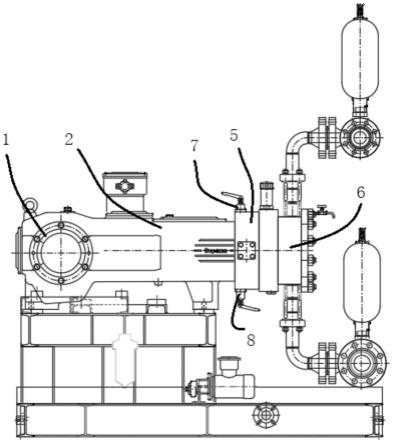
1.本发明涉及往复泵技术领域,尤其涉及一种减少调试时间的往复泵。
背景技术:2.三柱塞往复泵是一种容积式泵,借助工作腔里的容积周期性变化来达到输送液体的目的,被广泛应用于石油、化工、供水、热电、核工业、制药、食品等各个行业,专业配套性强,可满足不同客户、不同工艺工况要求,但因其为柱塞式结构,总是有一定的泄漏,如果输送介质有毒、有腐蚀性、易燃易爆,或者为贵重物料,则不允许有泄漏存在,那么,三柱塞液压隔膜泵就是最佳选择。
3.使用现场启动调试时,由于内部窝存空气要经过泄放阀起跳排放,而调试阶段泵的运行还不正常,在没有建立起足够的排出流量时,液压腔的空气排放需要一定的时间,相对较长时间反复运行。在此过程中,泵的振动、噪音会非常大,对现场生产非常不利,给调试操作造成很大影响。
4.在中国专利申请号:cn201710399232.2中公开了一种三柱塞液压隔膜往复泵,包括:具有前端面、后端面及若干个侧面的过渡板、三个泵头和动力端;过渡板前端设有并列排布的第一液压通道、第二液压通道和第三液压通道,第一液压通道、第二液压通道和第三液压通道均通过缸套连通动力端;过渡板后端设有用于连接三个泵头的第一泵头接口、第二泵头接口和第三泵头接口;第二泵头接口位于过渡板后端面上;第一泵头接口和第三泵头接口分别位于过渡板后端的相对的侧面上。该技术方案在现场调试时,需要较长时间。
5.鉴于此,故提出本技术。
技术实现要素:6.为解决背景技术中存在的至少一个方面的技术问题,本发明提出一种减少调试时间的往复泵。
7.本发明提出的一种减少调试时间的往复泵,包括:
8.动力部;
9.机箱;
10.缸套,所述缸套布置于所述机箱上;
11.活塞组件,所述活塞组件位于所述缸套内,所述活塞组件能够沿所述缸套往复移动,所述活塞组件与所述动力部传动连接;
12.过渡板,所述过渡板安装在所述机箱上,所述过渡板内设有液压腔,所述液压腔与所述缸套连通;
13.泵头组件,所述泵头组件安装在所述过渡板远离所述机箱的一侧,所述泵头组件与所述液压腔连通;
14.第一排气阀,所述第一排气阀安装在所述过渡板的顶端,所述第一排气阀的当量直径为12-20mm;所述第一排气阀与所述液压腔连通;
15.第一补油阀,所述第一补油阀安装在所述过渡板的底端,所述第一补油阀的当量直径为12-15mm;所述第一补油阀与所述液压腔连通。
16.优选地,所述第一排气阀包括:
17.第一阀座,所述第一阀座安装在所述过渡板的顶端,所述第一阀座内设有第一出气孔,所述第一出气孔与所述液压腔连通;
18.第一阀体,所述第一阀体安装在所述第一阀座上,所述第一阀体内设有第一阀腔,所述第一阀腔与所述第一出气孔连通,所述第一阀腔与所述机箱连通;
19.第一阀球,所述第一阀球位于所述第一阀腔内,用于封闭或打开所述第一排气孔;
20.第一阀杆,所述第一阀杆与所述第一阀腔螺纹连接,所述第一阀杆的底端与所述第一阀球抵接。
21.所述过渡板上设有第一出气通道、第一排气通道,所述第一出气通道与所述液压腔、所述第一出气孔连通;所述第一排气通道与所述第一阀腔连通;
22.所述机箱上设有连通其内部的第一连接通道,所述第一连接通道与所述第一排气通道连通。
23.优选地,所述往复泵还包括安全阀,所述安全阀的进气孔与所述液压腔连通。
24.优选地,所述过渡板上设有第二出气通道、第二排气通道,所述第二出气通道与所述液压腔、所述安全阀的进气孔连通;所述第二排气通道的两端分别与所述安全阀的出气孔、所述第一排气通道连通。
25.优选地,所述第一补油阀包括:
26.第二阀座,所述第二阀座安装在所述过渡板的底端,所述第二阀座内设有第一进油孔、第二阀腔,所述第二阀腔通过所述第一进油孔与所述液压腔连通;
27.第三阀座,所述第三阀座安装在所述第二阀座上,所述第三阀座内设有第二进油孔,所述第二进油孔与所述第二阀腔连通;
28.第二阀体,所述第二阀体安装在所述第三阀座上,所述第二阀体内设有第三阀腔,所述第三阀腔与所述第二进油孔连通,所述第三阀腔与所述机箱连通;
29.第二阀球,所述第二阀球位于所述第二阀腔内,用于封闭或打开所述第二进油孔;
30.第三阀球,所述第三阀球位于所述第二阀腔内,用于封闭或打开所述第二进油孔;
31.第二阀杆,所述第二阀杆与所述第三阀腔螺纹连接,所述第二阀杆的顶端与所述第三阀球抵接。
32.优选地,所述过渡板上设有第一补油通道、第一进油通道,所述第一补油通道与所述液压腔、所述第一进油孔连通;所述第一进油通道与所述第三阀腔连通;
33.所述机箱上设有连通其内部的第二连接通道,所述第二连接通道与所述第一进油通道连通。
34.优选地,所述往复泵还包括第二补油阀,所述第二补油阀安装在所述过渡板的底端,所述补油阀与所述机箱、所述液压腔连通。
35.优选地,所述过渡板上设有第二补油通道、第二进油通道,所述第二补油通道与所述液压腔、所述补油阀的出油口连通;所述第二进油通道的两端分别与所述补油阀的进油口、所述第一进油通道连通。
36.本发明公开的一个方面带来的有益效果是:
4mm。
56.结合图1、2,本实施例中,通过选择较大当量直径的第一排气阀7、第一补油阀8,在调试阶段,打开第一排气阀7、第一补油阀8。活塞组件4右行时,其前端液压腔503内的气体被快速排放,左行时,其前端一旦形成负压,则快速通过第一补油阀8进行随机补油。往复循环,在短时间内,排净液压腔503内的空气,并使液压腔503内充满液压油,达到运行平稳正常。而后关闭第一排气阀7、第一补油阀8即可。
57.本实施例采用较大当量直径的第一排气阀7、第一补油阀8,调试时间短,使往复泵快速进入正常运行。
58.本实施例中,所述第一排气阀7包括:第一阀座701,第一阀体702,第一阀球703,第一阀杆704;
59.所述第一阀座701安装在所述过渡板5的顶端,所述第一阀座701内设有第一出气孔7011,所述第一出气孔7011与所述液压腔503连通;
60.所述第一阀体702安装在所述第一阀座701上,所述第一阀体702内设有第一阀腔7021,所述第一阀腔7021与所述第一出气孔7011连通,所述第一阀腔7021与所述机箱2连通;
61.所述第一阀球703位于所述第一阀腔7021内,用于封闭或打开所述第一排气孔;
62.所述第一阀杆704与所述第一阀腔7021螺纹连接,所述第一阀杆704的底端与所述第一阀球703抵接。
63.所述过渡板5上设有第一出气通道501、第一排气通道502,所述第一出气通道501与所述液压腔503、所述第一出气孔7011连通;所述第一排气通道502与所述第一阀腔7021连通。
64.所述机箱2上设有连通其内部的第一连接通道201,所述第一连接通道201与所述第一排气通道502连通。
65.在调试阶段,通过转动第一阀杆704,让第一阀杆704与第一阀球703分离。液压腔503内的空气经过第一出气通道501、第一出气孔7011,而后顶开第一阀球703进入第一阀腔7021内,在经过第一排气通道502、第一连接通道201进入机箱2内。
66.在调试完成后,反向转动第一阀杆704,让第一阀杆704的底端抵住第一阀球703。
67.本实施例能够在调试阶段快速的排出液压腔503内的空气,减少调试时间。
68.液压腔503内的空气含有液压油,通过设置第一排气通道502、第一连接通道201,进入机箱2内。本实施例没有外设管路进行连接,而是内置通道,从内部输送,有效的减少泄漏点。
69.本实施例中,所述往复泵还包括安全阀9,所述安全阀9的进气孔与所述液压腔503连通。
70.在正常使用过程中,利用安全阀9进行保护。
71.现有技术中仅具有安全阀9,在调试阶段,液压腔503内的空气经过安全阀9被不断排出,直到液压腔503充满油液,往复泵才能达到正常运行。往复泵在正常运行时,液压油中会混合空气继而进入液压腔503,空气聚集起来,达到往复泵头顶部,通过安全阀9排出。
72.现有技术中,在调试阶段仅仅利用安全阀9进行排气,其当量直径小,调试时间长。
73.本实施例中,在调试阶段利用第一排气阀7进行排气,调试时间短。在正常运转时,
利用安全阀9进行排气,进行安全保护。
74.本实施例中,所述过渡板5上设有第二出气通道504、第二排气通道505,所述第二出气通道504与所述液压腔503、所述安全阀9的进气孔连通;所述第二排气通道505的两端分别与所述安全阀9的出气孔、所述第一排气通道502连通。
75.在正常运转过程中,液压腔503内的空气聚集达到一定压强时,经过第二出气通道504进入安全阀9,而后经过第二排气通道505、第一排气通道502进入机箱2内。没有外设管路,减少泄漏点。现有技术中是外设管路的,容易泄漏。
76.本实施例中,所述第一补油阀8包括:第二阀座801,第三阀座802,第二阀体803,第二阀球804,第三阀球805,第二阀杆806。
77.所述第二阀座801安装在所述过渡板5的底端,所述第二阀座801内设有第一进油孔8011、第二阀腔8012,所述第二阀腔8012通过所述第一进油孔8011与所述液压腔503连通。
78.所述第三阀座802安装在所述第二阀座801上,所述第三阀座802内设有第二进油孔8021,所述第二进油孔8021与所述第二阀腔8012连通。
79.所述第二阀体803安装在所述第三阀座802上,所述第二阀体803内设有第三阀腔8031,所述第三阀腔8031与所述第二进油孔8021连通,所述第三阀腔8031与所述机箱2连通。
80.所述第二阀球804位于所述第二阀腔8012内,所述第二阀球804用于封闭或打开所述第二进油孔8021的顶端;所述第三阀球805位于所述第二阀腔8012内,用于封闭或打开所述第二进油孔8021的底端。
81.所述第二阀杆806与所述第三阀腔8031螺纹连接,所述第二阀杆806的顶端与所述第三阀球805抵接。
82.所述过渡板5上设有第一补油通道506、第一进油通道507,所述第一补油通道506与所述液压腔503、所述第一进油孔8011连通;所述第一进油通道507与所述第三阀腔8031连通。
83.所述机箱2上设有连通其内部的第二连接通道202,所述第二连接通道202与所述第一进油通道507连通。
84.结合图6、7,在调试阶段,转动第二阀杆806,让第二阀杆806与第三阀球805分离,第三阀球805下降,机箱2内的液压油经过第二连接通道202、第一进油通道507进入第三阀腔8031内,而后进入第二进油孔8021内。再将第二阀球804顶开进入第二阀腔8012,再经过第一进油孔8011、第一补油通道506进入液压腔503内进行补油。在调试完成后,反向转动第二阀杆806,让第二阀杆806的顶端抵住第三阀球805,封住第二进油孔8021的底端。
85.本实施例中的第一补油阀8的当量直径大,能够快速补油,减少调试时间。
86.本实施例没有外设管路进行连接,而是内置通道,从内部输送,有效的减少泄漏点。
87.本实施例中,所述往复泵还包括第二补油阀10,所述第二补油阀10安装在所述过渡板5的底端,所述补油阀与所述机箱2、所述液压腔503连通。
88.本实施例中,所述过渡板5上设有第二补油通道508、第二进油通道509,所述第二补油通道508与所述液压腔503、所述补油阀的出油口连通;所述第二进油通道509的两端分
别与所述补油阀的进油口、所述第一进油通道507连通。
89.现有技术中仅具有第二补油阀10,在调试阶段,机箱2内的液压油经过第二补油阀10进入液压腔503内,直到液压腔503充满油液,往复泵才能达到正常运行。往复泵在正常运行时,液压腔503内的液压油不足时,机箱2内的液压油经过第二连接通道202、第一进油通道507、第二进油通道509、第二补油阀10、第二补油通道508进行补油。
90.现有技术中,在调试阶段仅仅利用第二补油阀10进行补油,其当量直径小,调试时间长。
91.本实施例中,在调试阶段利用第一补油阀8进行补油,调试时间短。在正常运转时,利用第二补油阀10进行补油。没有外设管路,减少泄漏点。现有技术中设置的第二补油阀10是与外设管路连接的,容易泄漏。
92.往复泵在运行过程中,如果发生异常,噪音、振动很大,则也可打开第一排气阀7,手动调节,以检测排查噪音、振动的原由,逐步分析解决问题。
93.这种配置灵活、工艺完善的往复泵,极大地满足了客户对工艺系统的配置要求,专业性强,实用性强,操作简便,很受市场欢迎。
94.以上所述,仅为本发明较佳的具体实施方式,但本发明的保护范围并不局限于此,任何熟悉本技术领域的技术人员在本发明揭露的技术范围内,根据本发明的技术方案及其发明构思加以等同替换或改变,都应涵盖在本发明的保护范围之内。