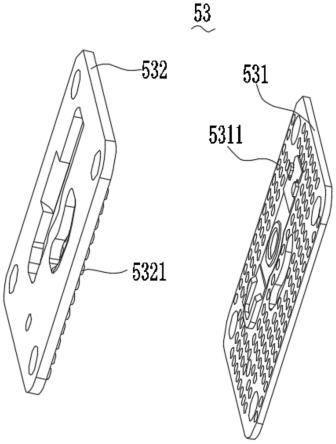
1.本发明属于压缩机设计技术领域,具体涉及一种往复式活塞压缩机用的复合阀板、往复式活塞压缩机。
背景技术:2.对于往复式活塞压缩机而言,其气缸的泵头除包含吸气阀和排气阀的阀组件以外,还包括将阀组件压紧固定在气缸座上的气缸盖,该气缸盖完全将阀组件覆盖而形成一个密闭的腔体,当活塞在气缸内部做往复运动,进而对气体或冷媒进行压缩做功后,再由排气孔和排气阀排出气缸,进入并充满气缸盖包围的腔体内。而在压缩过程中,气缸内的气体或冷媒的温度会逐渐升高,该高温气体或冷媒不仅会将一部分热量传递给阀板(如图4中的金属阀板53’),而且该高温气体或冷媒排入到气缸盖与阀组件之间的腔体内后,也会将一部分热量传递给阀板,故阀板温度基本与压缩机的排气温度相当。被加热后的阀板主要带来的问题有两个方面,一方面由于阀板直接与吸气通道接触,所以吸气通道内的气体或冷媒会被温度较高的阀板加热而膨胀,而吸气通道的容积并不会改变,所以吸气通道内的气体或冷媒的量变少,进入到压缩腔内的气体或冷媒的量也就相应的变少;另一方面,在排气未开始之前,气体或冷媒被活塞压缩后也会升温,但该气体或冷媒的升高的温度还是比被加热后的阀板温度低,导致压缩腔内被压缩升温的气体或冷媒被进一步加热而膨胀,排气阀片也会过早打开,进而导致压缩机的容积效率降低,最终导致压缩机能效降低。
3.为解决以上问题,现有技术中的一种处理方式是开设油路来间隔开吸气口和排气口,避免排气口的高温气体或冷媒直接对吸气口的低温气体或冷媒进行加热,同时油路内流动的润滑油也能带走阀板的部分热量,避免被加热后的阀板再对吸气口的低温气体或冷媒进行加热,但这些油路通道会使得处于气缸盖与阀板之间的密封垫片处于悬空的状态,阀板对密封垫片的有效支撑平面减少,进而导致气缸与阀板之间出现了泄露的风险,排气通道与吸气通道之间也有连通泄露的风险。
4.有的技术方案使用隔热陶瓷材料直接作为阀板的基材,也有技术方案直接采用导热率很低的高聚物作为阀板的基材,以解决以上吸气通道内气体或冷媒吸气过热的问题及压缩腔内气体或冷媒受热膨胀而过早排出而导致容积效率降低的问题,但把陶瓷材料加工成阀板精件的成本比较高,不适应大规模推广使用;同时,聚合物的弹性模量较低,因此其抵抗变形能力也较弱,而气缸盖并不能完全压紧处于悬空状态的聚合物阀板,所以聚合物阀板未被压住的部位会出现翘曲变形的情况,进而导致排出气体泄漏的问题出现。
技术实现要素:5.因此,本发明提供一种往复式活塞压缩机用的复合阀板、往复式活塞压缩机,能够解决现有技术中往复式活塞压缩机中的阀组件内的阀板导热导致压缩腔内被压缩升温的气体或冷媒被进一步加热而膨胀,排气阀片过早打开,进而导致压缩机的容积效率降低,最终导致压缩机能效降低以及为了提高阀板的隔热性能使密封垫片悬空或阀板翘曲变形进
而导致冷媒泄漏的技术问题。
6.为了解决上述问题,本发明提供一种往复式活塞压缩机用的复合阀板,包括阀板本体,所述阀板本体上构造有吸气通孔以及排气通孔,所述阀板本体包括金属基板以及贴合覆盖于所述金属基板的第一侧的聚合物隔热层,当复合阀板被组装于往复式活塞压缩机中时,所述聚合物隔热层处于所述往复式活塞压缩机具有的气缸盖的一侧。
7.在一些实施方式中,所述金属基板的导热系数为λa、弹性模量为ea,λa≤40.0w/m
·
k且100gpa≤ea≤200gpa。
8.在一些实施方式中,所述金属基板的基材为铁基金属材料。
9.在一些实施方式中,所述聚合物隔热层的导热系数为λb,λb≤1.0w/m
·
k;和/或,所述聚合物隔热层的材料为聚四氟乙烯ptfe、聚醚醚酮peek、聚酰胺pa、聚酰亚胺pai、聚碳酸酯pc、聚苯硫醚pps、聚砜psu、超高分子量聚乙烯uhmwpe、氟塑料、酚醛树脂的其中至少一种。
10.在一些实施方式中,所述金属基板的厚度为a,a=0.5~2.0mm。
11.在一些实施方式中,所述聚合物隔热层的厚度为b,a=b。
12.在一些实施方式中,所述阀板本体的综合导热系数为λ,λ≤(a+b)λb/b。
13.在一些实施方式中,所述金属基板与所述聚合物隔热层之间具有凹凸连接结构。
14.在一些实施方式中,所述凹凸连接连接包括处于所述金属基板的所述第一侧的多个凹孔以及处于所述聚合物隔热层朝向所述金属基板一侧的多个凸台,所述凸台与所述凹孔的形状相适配,多个所述凸台一一对应地处于多个所述凸台内;和/或,所述聚合物隔热层采用注射成型、热模压制成型或模压烧结成型中的一种形成。
15.在一些实施方式中,所述凹孔采用机加工或者掩膜腐蚀的方式形成。
16.在一些实施方式中,所述金属基板的第二侧贴合覆盖有所述聚合物隔热层。
17.本发明还提供一种往复式活塞压缩机,包括上述的往复式活塞压缩机用的复合阀板。
18.本发明提供的一种往复式活塞压缩机用的复合阀板、往复式活塞压缩机,由于采用了由金属基板以及聚合物隔热层复合形成的阀板本体,吸气通道内的气体或冷媒不再被加热而膨胀,进入到压缩腔内的气体或冷媒的量增加,压缩腔内的容积效率得到提升;在排气开始之前,压缩腔内的气体或冷媒不被加热膨胀而被过早排出,而是到达气体或冷媒的临界压力才排出,压缩腔内的容积效率得到进一步提升,压缩机的性能得到一定的提升;由于金属基板则具有较高的弹性模量能够对阀板本体形成支撑,避免了采用纯聚合物阀板中部翘曲引起的泄漏问题,而具有一定塑性的聚合物隔热层则无需采用现有技术中的往复式活塞压缩机中的密封垫片也能够保证气缸盖与阀板本体之间的密封性能,减少了活塞压缩机气缸头零部件的数量,压缩机的可靠性得到提升;复合阀板的聚合物板的延伸率高,也并不会出现被压破裂而失效的问题。
附图说明
19.图1为本发明实施例的往复式活塞压缩机用的复合阀板拆解结构示意图;
20.图2为本发明实施例的往复式活塞压缩机用的复合阀板的截面图,图中示出了金属基板与聚合物隔热层结合为一体;
21.图3为本发明实施例的往复式活塞压缩机的立体拆解结构示意图;
22.图4为本发明实施例的活塞压缩机的吸气过程复合阀板隔热原理图;
23.图5为本发明实施例的活塞压缩机的压缩过程复合阀板隔热原理图;
24.图6为本发明实施例的活塞压缩机的排气过程复合阀板隔热原理图;
25.图7为未装配本发明的复合阀板与装配本发明的复合阀板的压缩机测试后制冷量对比图;
26.图8为现有技术中的往复式活塞压缩机的立体拆解结构示意图。
27.附图标记表示为:
28.10、气缸座;20、平面滚动轴承;30、曲轴组件;31、曲轴;32、配重块;40、活塞组件;41、连杆;42、活塞;43、销钉;44、卡簧销;50、阀组件;51、吸气阀垫片;52、吸气阀片;53、阀板本体;53’、金属阀板;531、金属基板;5311、凹孔;532、聚合物隔热层;5321、凸台;54、排气阀片;55、限位板;56、密封垫片;60、气缸盖;70、吸气消音器。
具体实施方式
29.实施例1
30.结合参见图1至图4所示,根据本发明的实施例,提供一种往复式活塞压缩机用的复合阀板,包括阀板本体53,阀板本体53上构造有吸气通孔以及排气通孔,阀板本体53包括金属基板531以及贴合覆盖于金属基板531的第一侧的聚合物隔热层532,当复合阀板被组装于往复式活塞压缩机中时,聚合物隔热层532处于往复式活塞压缩机具有的气缸盖60的一侧,此时能够理解的是,金属基板531的第二侧,也即与第一侧相对的一侧与气缸的压缩腔组装配合。该技术方案中,由于采用了由金属基板531以及聚合物隔热层532复合形成的阀板本体53,吸气通道内的气体或冷媒不再被加热而膨胀,进入到压缩腔内的气体或冷媒的量增加,压缩腔内的容积效率得到提升;在排气开始之前,压缩腔内的气体或冷媒不被加热膨胀而被过早排出,而是到达气体或冷媒的临界压力才排出,压缩腔内的容积效率得到进一步提升,压缩机的性能得到一定的提升;由于金属基板531则具有较高的弹性模量能够对阀板本体53形成支撑,避免了采用纯聚合物阀板中部翘曲引起的泄漏问题,而具有一定塑性的聚合物隔热层532则无需采用现有技术中的往复式活塞压缩机中的密封垫片56也能够保证气缸盖60与阀板本体53之间的密封性能,减少了活塞压缩机气缸头零部件的数量,压缩机的可靠性得到提升;复合阀板的聚合物板的延伸率高,也并不会出现被压破裂而失效的问题。
31.具体而言,金属基板531的导热系数为λa、弹性模量为ea,λa≤40.0w/m
·
k且100gpa≤ea≤200gpa,以保证阀板本体具有较低导热性能的同时还具有足够的变形能力与刚度,保证其支撑能力。作为优选方案,金属基板531的基材为铁基金属材料,所述铁基金属材料为粉末冶金或铸铁的其中一种,采用铁基金属材料具有较低的材料成本。
32.在一些实施方式中,聚合物隔热层532的导热系数为λb,λb≤1.0w/m
·
k,以保证该聚合物隔热层532具有更低的导热性能;具体而言,聚合物隔热层532的材料为聚四氟乙烯ptfe、聚醚醚酮peek、聚酰胺pa、聚酰亚胺pai、聚碳酸酯pc、聚苯硫醚pps、聚砜psu、超高分子量聚乙烯uhmwpe、氟塑料、酚醛树脂的其中至少一种,相对于金属材料、无机固体材料等而言,这些材料都具有极低的导热,隔热性能极佳。
33.参见图2所示,金属基板531的厚度为a,a=0.5~2.0mm,以保证金属基板531抵抗变形的能力,防止因气缸盖60压紧复合阀板的外周围后,复合阀板的中心部产生心部翘曲变形导致的泄露问题的出现。聚合物隔热层532的厚度为b,a=(1/5~1/2)b,也即聚合物隔热层532的厚度较金属基板531的厚度要大,以使得其热传导的距离尽量长,保证其隔热性能的发挥。
34.而由金属基板531和聚合物隔热层532构成的阀板本体53的整体也有一个对应的综合导热系数λ,该导热系数λ虽比聚合物隔热层532的基材导热系数稍高,但却比金属基板531的基材导热系数低了很多,而且该阀板本体53的导热系数λ与金属基板531的厚度a及聚合物隔热层532的厚度b满足关系式:λ≤(a+b)λb/b。
35.结合参见图1及图2所示,金属基板531与聚合物隔热层532之间具有凹凸连接结构。具体的,如图1所示出,凹凸连接连接包括处于金属基板531的第一侧的多个凹孔5311以及处于聚合物隔热层532朝向金属基板531一侧的多个凸台5321,凸台5321与凹孔5311的形状相适配,多个凸台5321一一对应地处于多个凸台5321内,以提高两者的连接可靠性,防止两种不同的材料在受热后发生变形导致的脱离现象发生。前述凹孔5311可以采用机加工或者掩膜腐蚀的方式形成,优选采用掩膜腐蚀的方式形成,能够简化凹孔5311的形成过程,提高加工效率并降低成本。
36.在另一个具体的实施例中,凹孔5311被设计为缩口孔,也即该凹孔5311的孔口直径小于其内部孔腔的直径,如此,处于孔腔内的凸台5321的直径将大于处于孔口中的凸台5321的直径,这种结构的连接强度更加可靠。聚合物隔热层532采用注射成型、热模压制成型或模压烧结成型中的一种形成,尤其是在凹孔5311为缩口孔时,其中,热模压制成型或模压烧结成型工艺都比较简单,而且开设的模具可以反复使用,生产成本较低。在凹孔5311为等直径凹孔或者不具有凹孔5311时,聚合物隔热层532可以采用粘贴的方式连接于金属基板531的第一侧。凹孔5311的形状可以是圆形、矩形、三角形、多边形和其他不规则形状的其中至少一种。
37.阀板本体53的加工及成型工艺流程具体如下:
38.1、先加工出金属基板531半精件。
39.2、再使用热模压制成型或模压烧结成型的其中一种成型工艺在金属基板531半精件上热压成型出表面粗糙度和平面度稍差的聚合物隔热层532。
40.3、接着剪切掉脱模后的分型面处的聚合物边角料,再使用细砂纸打磨隔热板上与金属基板531对应的吸气避让孔和排气避让孔,使得聚合物隔热层532上吸气避让孔和排气避让孔的轮廓与金属基板的吸气孔(其与吸气避让孔共同形成吸气通孔)和排气孔(其与排气避让孔共同形成排气通孔)的轮廓完全重合,避免因配合精度不高而突出的棱边会使得吸气和排气的气流在流动过程流动不顺畅而引发气流的波动和异响噪声,使得用户的听感更佳,体验感更好。
41.4、最后再对成型后复合阀板半精件的吸、排气口凸台和两个密封端面做精磨加工处理,提升吸、排气口凸台和两个密封端面的平面度,并使得吸、排气口凸台和两个密封端面的粗糙度控制到最低,最终得到精度相对较高的复合阀板(阀板本体53)。
42.实施例2
43.与实施例1的技术方案的不同之处在于,金属基板531的第二侧贴合覆盖有聚合物
隔热层532,也即金属基板531的两侧皆设置有具有塑性的聚合物隔热层532,进一步提升复合阀板的隔热性能,且能够对两侧的组装件形成有效密封。此时假定第二侧的聚合物隔热层532的厚度为c,则λ≤(a+b+c)λb/b。
44.如图8所示,常规活塞压缩机泵体组件主要包括气缸座10、平面滚动轴承20、曲轴组件30、活塞组件40、阀组件50、气缸盖60、吸气消音器70。其中,曲轴组件30包括曲轴31及配重块32,所述曲轴组件30在电机的驱动下带动所述活塞组件40在气缸座10的气缸内对气体或冷媒做吸入和压缩排出的往复性运动,且所述活塞组件40由连杆41、活塞42、销钉43及卡簧销44组成。而所述平面滚动轴承20使得曲轴组件30与气缸座10的之间的滑动摩擦变为滚动摩擦,进而降低了因摩擦产生的功耗。而且气体或冷媒的吸入和压缩排出主要由阀组件50来进行控制,且该阀组件50主要包括吸气阀垫片51、吸气阀片52、金属阀板53’、排气阀片54、限位板55及密封垫片56,并用气缸盖60将所述阀组件50压紧固定在气缸座10上,且气缸盖60与阀组件之间装配具有密封性能的石棉材质的密封垫片56,以此来保证气缸盖60包围形成的排气腔的气密性。同时,还在吸入的气体或冷媒的前段装设吸气消音器70后,能够有效降低因吸入气体的脉动而产生的噪声,进而达到降低压缩机整体噪声的目的。
45.如图3所示,为减少活塞压缩机泵头零部件的数量,降低成本,并提升压缩机的可靠性,将以上所述常规活塞压缩机中阀组件50中的密封垫片56取消掉,并将如图8所示的常规压缩机中的金属阀板53’替换成本发明的具有双层结构的复合阀板。
46.如图4、图5及图6所示,活塞压缩机的泵头组件的阀板本体53不仅将气缸座10上的压缩腔与吸气通道隔开,还将气缸座10上的压缩腔和气缸盖60包围形成的排气腔也分隔开,气缸盖60同时又将吸气通道和气缸盖60包围形成的排气腔分隔开,即形成了一个吸气通道与压缩腔连通、压缩腔与排气腔连通的压缩通路系统。压缩机的运行过程主要包括吸气、压缩和排气的过程。当压缩机开始运行时,曲轴组件30及活塞组件40在电机的驱动下对从吸气通道内进入到压缩腔内的气体或冷媒进行压缩,吸气过程开始;而在压缩过程中,气体或冷漠的体积逐渐变小,热量增加,这个过程也是将机械能转化成为了气体或冷媒的内能(热能)的过程,致使压缩腔内的温度升高;同时,当压缩腔内压力值达到气体或冷媒的临界压力值之后,排气阀片54打开,开始进行排气过程,高温高压的气体或冷媒又进入到气缸盖60包围形成的排气腔内;而且在以上压缩过程和排气过程中,气体通道内还会充满低温的气体或冷媒。因此装配了导热率很低的阀板本体53和气缸盖60来对热量进行阻挡后,压缩机的制冷性能提升的原理及有益效果是:
47.1、吸气过程,见图4:吸气过程中热量的传导主要分为压缩机刚开始运行时的启动阶段和压缩机运行了一段时间后的运行阶段。压缩机刚开启的启动阶段,压缩腔和排气腔内并无高温高压的气体或冷媒,这个阶段也就不会有热传导致使吸气过热的问题出现;当压缩机运行过一段时间后,即使从吸气通道内进入到压缩腔内的气体或冷媒的温度较低,也未被压缩而升温,但由于前期压缩机的长时间运行,气缸座10和金属材质的气缸盖60具有比吸气腔内气体或冷媒高的温度,而且排气腔内也残留有高温高压的气体或冷媒(若气缸盖60为聚合物材料时,气缸盖60的温度相对较低,所以可不用考虑气缸盖60的温度传导对吸气通道内气体或冷媒的不利影响),而由于受到阀板本体53的阻隔作用,气缸座10的热量不能或只有少部分传递到吸气通道内,气缸盖60及排气腔内高温气体或冷媒的热量也不能或只有少量传递到吸气通道内,吸气通道内的气体或冷媒也不会因为受热膨胀而导致气
体或冷媒的量减少,进入到压缩腔内的气体或冷媒的量也就不会变少,压缩腔内的容积效率得到提升。
48.2、压缩过程,见图5:压缩过程中热量的传导也主要分为压缩机刚开始运行时的启动阶段和压缩机运行了一段时间后的运行阶段。压缩机刚开启的启动阶段,排气腔内并无高温高压的气体或冷媒,这个阶段也就不会有热传导致使吸气过热的问题出现;当压缩机运行过一段时间后,这时并无低温的气体或冷媒从吸气通道内进入到压缩腔内,压缩腔内的气体或冷媒虽逐渐被压缩而升温,该过程因压力未达到气体或冷媒的临界压力值,所以压缩腔内气体或冷媒的温度要低于前期排气腔内高温高压的气体或冷媒的温度,而由于受到阀板本体53的阻隔作用,排气腔内高温气体或冷媒的热量不能或只有少量传递到吸气通道内,压缩腔内已经被压缩但并未达到临界压力值的气体或冷媒也不会因为受热膨胀而导致排气阀片54过早打开,压缩腔的容积效率也就也得到进一步的提升。
49.3、排气过程,见图6:排气过程中热量的传导在压缩机刚开始启动及压缩机运行过一段时间后的影响都一致,这时压缩腔内的压力达到了气体或冷媒的零件压力值,压缩腔内高温高压的气体或冷媒逐渐被排到并充满排气腔,由于受到阀板本体53的阻隔作用,压缩腔及排气腔内高温气体或冷媒的热量不能或只有少量传递到吸气通道内,吸气通道内的气体或冷媒也不会因为受热膨胀而导致气体或冷媒的量减少,在排气过程完成之后,吸气过程开始,这时从吸气通道内进入到压缩腔内的气体或冷媒的量也不会变少,压缩腔内的容积效率再得到进一步的提升。
50.如图7所示,装配有阀板本体53与装配常规金属阀板53’的活塞压缩机做完不同频率下的性能测试之后,装配常规金属阀板53’的活塞压缩机的制冷量较装配有本发明的阀板本体53的活塞压缩机低,说明装入具有优良隔热性能的阀板本体53能够提升活塞压缩机的制冷能力,压缩机的能效也得到了提升。
51.本领域的技术人员容易理解的是,在不冲突的前提下,上述各方式的有利技术特征可以自由地组合、叠加。
52.以上仅为本发明的较佳实施例而已,并不用以限制本发明,凡在本发明的精神和原则之内所作的任何修改、等同替换和改进等,均应包含在本发明的保护范围之内。以上仅是本发明的优选实施方式,应当指出,对于本技术领域的普通技术人员来说,在不脱离本发明技术原理的前提下,还可以做出若干改进和变型,这些改进和变型也应视为本发明的保护范围。