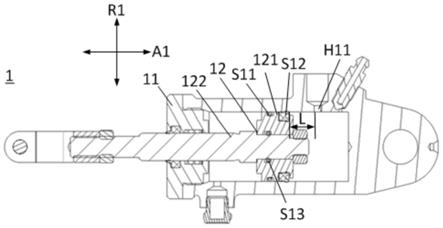
1.本发明涉及车辆用离合系统。
背景技术:2.在现有的车辆(例如拖拉机)用离合系统中存在如下问题。当该离合系统处于未工作的初始状态时,在分离轴承和离合器分离指之间存在一定的间隙。在经过一段时间的工作之后,离合器盘将被磨耗,使得离合器分离指产生了倾斜。在这种情况下,上述间隙可能消失,则离合器分离指将与分离轴承彼此抵接。这样,经由拨叉和连杆系统,离合器分离指与分离轴承之间抵接而产生的压力将对离合系统的其它部件造成不利的影响,例如将使得从动缸活塞组件的初始位置改变而阻塞从动缸进油孔。这样,在经过一段时间之后,需要对离合系统进行重新设定。
技术实现要素:3.鉴于上述现有技术的缺陷而做出了本发明。本发明的目的在于提供一种车辆用离合系统,其能够尽可能避免由于离合器盘被磨耗导致的从动缸活塞组件阻塞从动缸进油孔的问题。
4.为了实现上述发明目的,本发明采用如下的技术方案。
5.本发明提供了一种如下的车辆用离合系统,其包括从动缸、主动缸、拨叉和分离轴承,所述从动缸与所述主动缸流体连通,使得能够通过控制所述从动缸和所述主动缸两者内部的液压流体的流动来驱动所述拨叉推动所述分离轴承,
6.所述从动缸包括从动缸缸体和能够相对于所述从动缸缸体沿着所述从动缸的轴向往复运动的从动缸活塞组件,所述从动缸缸体形成有与所述主动缸流体连通的从动缸进油孔,所述从动缸活塞组件始终位于所述从动缸进油孔的轴向一侧且与所述拨叉始终传动联接,
7.当所述离合系统处于未工作的初始状态时,所述从动缸活塞组件的与所述从动缸缸体接触的部位的轴向另一侧端缘与所述从动缸进油孔的轴向一侧端缘之间在所述从动缸的轴向上具有预定的补偿间隔。
8.优选地,所述从动缸活塞组件包括活塞本体和至少一个从动缸密封圈,所述至少一个从动缸密封圈外套于该活塞本体且与所述从动缸缸体接触密封,所述补偿间隔为所述至少一个从动缸密封圈中的最靠轴向另一侧的从动缸密封圈的轴向另一侧端缘与所述从动缸进油孔的轴向一侧端缘之间在所述从动缸的轴向上的间隔。
9.更优选地,所述主动缸包括主动缸缸体和能够相对于所述主动缸缸体沿着所述主动缸的轴向往复运动的主动缸活塞组件,所述主动缸缸体形成有与所述从动缸进油孔流体连通的主动缸出油孔,使得在所述主动缸活塞组件被朝向所述主动缸出油孔驱动时所述主动缸内的液压流体能够经由所述主动缸出油孔和所述从动缸进油孔进入所述从动缸内。
10.更优选地,所述主动缸缸体还形成有与所述液压流体的供给源连通的主动缸进油
孔和供所述液压流体返回所述供给源的主动缸回油孔,所述主动缸进油孔、所述主动缸回油孔和所述主动缸出油孔在所述主动缸的轴向上间隔开地布置,
11.当所述离合系统处于未工作的初始状态时,所述主动缸进油孔、所述主动缸回油孔和所述主动缸出油孔彼此连通,当所述离合系统处于工作状态时,所述主动缸进油孔、所述主动缸回油孔和所述主动缸出油孔彼此之间的连通关闭。
12.更优选地,所述主动缸活塞组件包括套筒和能够相对于该套筒在所述主动缸的轴向上的预定范围内运动的柱塞,
13.所述套筒具有套筒主体部和从该套筒主体部朝向径向外侧凸出的两个套筒凸缘部,所述两个套筒凸缘部将所述主动缸缸体的内部分隔成与所述主动缸进油孔连通的第一空间、与所述主动缸回油孔连通的第二空间和与所述主动缸出油孔连通的第三空间。
14.更优选地,所述套筒主体部的内部形成有中央通孔,所述柱塞能够相对于所述套筒在所述中央通孔内运动,在所述中央通孔内所述柱塞的轴向一侧端部与所述套筒之间形成环状的导油空间,
15.当所述柱塞相对于所述套筒处于轴向一侧的第一极限位置时,所述导油空间仅与所述第二空间连通,当时所述柱塞相对于所述套筒处于轴向另一侧的第二极限位置时,所述导油空间与所述第一空间、所述第二空间和所述第三空间均连通。
16.更优选地,所述柱塞的轴向一侧端部形成密封部,当所述柱塞处于所述第一极限位置时,所述密封部与所述套筒的被密封部接触密封,使得关闭所述导油空间与所述第三空间之间的连通,并且
17.所述主动缸活塞组件还包括介于所述柱塞和所述套筒之间的柱塞密封圈,当所述柱塞处于所述第一极限位置时,所述柱塞密封圈与所述套筒的对应部位接触密封,使得关闭所述导油空间和所述第一空间之间的连通。
18.更优选地,所述离合系统还包括与所述柱塞始终传动联接的致动组件,使得所述致动组件能够驱动所述柱塞在所述第一极限位置和所述第二极限位置之间运动并且能够以起到至少部分驱动力的方式驱动所述主动缸活塞组件整体朝向轴向一侧运动。
19.更优选地,所述主动缸还包括复位弹簧,所述复位弹簧位于所述第三空间内且设置于所述套筒和所述主动缸缸体的底部之间,
20.通过所述致动组件驱动所述柱塞的驱动力能够克服所述复位弹簧的弹簧力以驱动所述主动缸活塞组件将所述第三空间内的液压流体压入所述从动缸缸体内,在所述致动组件的驱动力解除之后所述复位弹簧的弹簧力能够使得所述套筒复位。
21.更优选地,所述主动缸活塞组件还包括主动缸密封圈,所述主动缸密封圈外套于各所述套筒凸缘部且与所述主动缸缸体接触密封。
22.通过采用上述技术方案,本发明提供了一种新型的车辆用离合系统。该车辆用离合系统的从动缸包括从动缸缸体和能够在从动缸缸体内沿着从动缸的轴向往复运动的从动缸活塞组件,从动缸缸体形成有与主动缸流体连通的从动缸进油孔,从动缸活塞组件始终位于从动缸进油孔的轴向一侧。当离合系统处于未工作的初始状态时,从动缸活塞组件的与从动缸缸体接触的部位的轴向另一侧端缘与从动缸进油孔的轴向一侧端缘之间在从动缸的轴向上具有预定的补偿间隔。这样,即使离合器分离指与分离轴承彼此抵接之后产生的压力传递到从动缸活塞组件,使得在上述初始状态下从动缸活塞组件的位置朝向从动
缸进油孔移动,但是由于补偿间隔的存在使得在这种情况下从动缸活塞组件也不容易阻塞从动缸进油孔。
附图说明
23.图1是示出了根据本发明的一实施方式的车辆用离合系统的立体结构示意图。
24.图2是示出了图1中的离合系统的从动缸的沿着中心轴线截取的剖视示意图,其中从动缸处于未工作的初始状态。
25.图3a是示出了图1中的离合系统的主动缸的沿着中心轴线截取的剖视示意图,其中该主动缸处于未工作的初始状态且主动缸的柱塞处于第二极限位置;图3b是示出了图1中的离合系统的主动缸的沿着中心轴线截取的剖视示意图,其中主动缸处于工作状态的开始阶段且主动缸的柱塞处于第一极限位置;图3c是示出了图1中的离合系统的主动缸的沿着中心轴线截取的剖视示意图,其中主动缸处于工作状态的最终阶段且主动缸的柱塞处于第一极限位置。
26.附图标记说明
27.1从动缸 11从动缸缸体 12从动缸活塞组件 121活塞本体 122塞杆 h11从动缸进油孔 s11、s12、s13密封圈 l补偿间隔 a1从动缸的轴向 r1从动缸的径向
28.2主动缸 21主动缸缸体 22主动缸活塞组件 221套筒 2211套筒主体部 2212套筒凸缘部 221h中央通孔 221s被密封部 222柱塞 222s密封部 h21主动缸进油孔 h22主动缸回油孔 h23主动缸出油孔 h24第一导油孔 h25第二导油孔 p1第一空间 p2第二空间 p3第三空间 p4导油空间 s21、s22密封圈 a2主动缸的轴向 r2主动缸的径向
29.3管 4连杆系统 5拨叉 6分离轴承 7踏板组件。
具体实施方式
30.下面参照附图描述本发明的示例性实施方式。应当理解,这些具体的说明仅用于示教本领域技术人员如何实施本发明,而不用于穷举本发明的所有可行的方式,也不用于限制本发明的范围。在本发明中,“传动联接”是指两个部件之间直接连接或者经由例如连杆系统等传动机构间接联接,使得能够在两个部件之间传递驱动力。
31.以下将首先结合说明书附图说明根据本发明的一实施方式的离合系统的整体结构及工作过程。
32.(根据本发明的一实施方式的离合系统的整体结构及工作过程)
33.如图1所示,根据本发明的一实施方式的离合系统包括组装在一起的从动缸1、主动缸2、管3、连杆系统4、拨叉5、分离轴承6以及踏板组件7。
34.具体地,踏板组件7作为驾驶员使用的致动组件与主动缸2的下述主动缸活塞组件22始终传动联接。管3使主动缸2的内部和从动缸1的内部连通。连杆系统4一方面与从动缸活塞组件12始终传动联接,另一方面与拨叉5也始终传动联接。
35.这样,在来自踏板组件7的驱动力的作用下,主动缸活塞组件22能够将主动缸2的内部的液压流体(例如液压油)经由管3压入从动缸1的内部,从而驱动从动缸1的从动缸活塞组件12进行动作,由此从动缸活塞组件12经由连杆系统4带动拨叉5以推动分离轴承6对离合器分离指(未示出)施加对应的压力,以使得离合器盘(未示出)分离/接合。
36.以下将结合说明书附图说明图1中的离合系统的从动缸1的结构。
37.(从动缸1的结构)
38.在本实施方式中,如图2所示,从动缸1包括从动缸缸体11和能够相对于从动缸缸体11沿着从动缸1的轴向a1往复运动的从动缸活塞组件12。
39.具体地,从动缸缸体11的内部形成供从动缸活塞组件12的活塞本体121往复运动的圆柱状的空间。从动缸缸体11形成有与主动缸2的下述主动缸出油孔h23流体连通的从动缸进油孔h11,从动缸进油孔h11沿着从动缸1的径向r1延伸并且与从动缸缸体11的内部的空间连通。
40.从动缸活塞组件12包括组装在一起的活塞本体121、塞杆122以及三个密封圈s11、s12、s13。活塞本体121处于从动缸缸体11的内部并且将从动缸缸体11的内部的空间划分为两部分。塞杆122的一端固定安装于活塞本体121并且朝向轴向一侧(图2中的左侧)直线状地延伸到从动缸缸体11的外部以与连杆系统4直接联接,塞杆122能够随着活塞本体121的运动而运动。
41.三个密封圈中s11、s12、s13中的两个密封圈s11、s12外套于该活塞本体121且与从动缸缸体11接触,用于在活塞本体121与从动缸缸体11之间实现密封;另一个密封圈s13外套于塞杆122且与活塞本体121接触,用于在塞杆122和活塞本体121之间实现密封。
42.在本实施方式中,从动缸进油孔h11形成于从动缸缸体11的轴向另一侧(图2中的右侧)的端部,而且无论离合系统处于未工作的初始状态还是工作状态,从动缸活塞组件12均始终位于从动缸进油孔h11的轴向一侧的位置。进一步地,如图2所示,当离合系统处于未工作的初始状态时,从动缸活塞组件12的与从动缸缸体11接触的部位的轴向另一侧端缘与从动缸进油孔h11的轴向一侧端缘之间在从动缸1的轴向a1上具有预定的补偿间隔l。也就是说,在本实施方式中,补偿间隔l为外套于活塞本体121上的最靠轴向另一侧的密封圈s12的轴向另一侧端缘与从动缸进油孔h11的轴向一侧端缘之间在从动缸1的轴向a1上的间隔。另外,该间隔为例如从动缸缸体11的在从动缸1的轴向a1上的长度的1/5至1/3,从而在保证补偿间隔l足够的情况下不影响从动缸活塞组件12在从动缸缸体内的行程。
43.这样,即使离合器分离指与分离轴承6彼此抵接之后的压力传递到从动缸活塞组件12,使得在上述初始状态下从动缸活塞组件12的位置朝向从动缸进油孔h11移动,但是由于补偿间隔l的存在使得在这种情况下从动缸活塞组件12也不容易移动到阻塞从动缸进油孔h11的位置,从而节省了由于上述原因维护离合系统的成本,延长了离合系统的使用寿命。
44.以下将结合说明书附图说明图1中的离合系统的主动缸2的结构。
45.(主动缸2的结构)
46.在本实施方式中,如图3a至图3c所示,主动缸2包括主动缸缸体21、能够相对于主动缸缸体21沿着主动缸2的轴向a2往复运动的主动缸活塞组件22以及位于主动缸缸体21内的复位弹簧23。
47.在本实施方式中,主动缸缸体21具有带底的圆筒形状,其轴向一侧端被主动缸缸体21的底部封闭,轴向另一侧端被与主动缸缸体21螺纹接合的端堵(未示出)封闭。主动缸缸体21的内部形成供主动缸活塞组件22的套筒221沿着主动缸2的轴向a2往复运动的空间。
48.进一步地,主动缸缸体21形成有均与主动缸缸体21的内部的空间连通的主动缸进
油孔h21、主动缸回油孔h22和主动缸出油孔h23。主动缸进油孔h21与液压流体的供给源连通,主动缸回油孔h22用于供液压流体返回上述供给源,主动缸出油孔h23与从动缸进油孔h11经由管3流体连通。在本实施方式中,主动缸进油孔h21、主动缸回油孔h22和主动缸出油孔h23以从轴向另一侧(图3a至图3c中的右侧)朝向轴向一侧(图3a至图3c中的左侧)按照上述顺序在主动缸2的轴向a2上间隔开地布置。主动缸进油孔h21、主动缸回油孔h22和主动缸出油孔h23均沿着主动缸2的径向r2延伸。由于主动缸出油孔h23与从动缸进油孔h11始终经由管3流体连通,一方面,在主动缸活塞组件22被朝向主动缸出油孔h23驱动时主动缸2内的下述第三空间p3内的液压流体能够经由主动缸出油孔h23和从动缸进油孔h11进入从动缸1内;另一方面,当离合系统工作完成之后来自从动缸1的液压流体能够经由从动缸进油孔h11和主动缸出油孔h23返回主动缸2的第三空间p3内。而且,由于离合器分离指与分离轴承6之间的压力导致从动缸活塞组件12在初始状态下的位置朝向从动缸进油孔h11移动之后也能够将多余的液压流体经由从动缸进油孔h11和主动缸出油孔h23输送到主动缸2的第三空间p3内。
49.在本实施方式中,主动缸活塞组件22包括套筒221、柱塞222以及多个密封圈s21、s22。
50.具体地,套筒221具有套筒主体部2211和从该套筒主体部2211朝向径向外侧凸出的两个套筒凸缘部2212,套筒主体部2211的外径小于主动缸缸体21的内径。在主动缸2的轴向a2上,两个套筒凸缘部2212中的一个套筒凸缘部2212位于主动缸进油孔h21和主动缸回油孔h22之间,另一个套筒凸缘部2212位于主动缸回油孔h22和主动缸出油孔h23之间,两个套筒凸缘部2212分别套设有密封圈s21,使得密封圈s21与主动缸缸体21接触以在各套筒凸缘部2212和主动缸缸体21之间实现接触密封。因此,两个套筒凸缘部2212将主动缸缸体21的内部分隔成与主动缸进油孔h21连通的第一空间p1、与主动缸回油孔h22连通的第二空间p2和与主动缸出油孔h23连通的第三空间p3。
51.进一步地,套筒主体部2211的内部形成有中央通孔221h,柱塞222能够相对于套筒221在中央通孔221h的一部分内进行相对运动。另外,一方面,在中央通孔221h内,柱塞222的轴向一侧端部与套筒221之间形成环状的导油空间p4;另一方面,在位于主动缸进油孔h21和主动缸回油孔h22之间的套筒凸缘部2212的轴向两侧,套筒主体部2211分别形成能够使得第一空间p1与导油空间p4连通的第一导油孔h24和用于使得第二空间p2与导油空间p4连通的第二导油孔h25。
52.具体地,柱塞222具有沿着主动缸2的轴向a2直线状延伸的杆状,柱塞222从轴向另一侧插入套筒221的中央通孔221h内部,并且柱塞222能够相对于该套筒221在主动缸2的轴向a2上的预定范围内运动。柱塞222的外径较小的轴向一侧端部形成密封部222s,当柱塞222相对于套筒221处于轴向一侧的第一极限位置时(如图3b和图3c所示),密封部222s与套筒221的用于形成中央通孔221h的孔壁的被密封部221s接触密封,使得关闭导油空间p4与第三空间p3之间的连通。另外,作为柱塞密封圈的一个密封圈s22介于柱塞222的除了该轴向一侧端部以外的部分和套筒221之间,当柱塞222处于上述第一极限位置时,该密封圈s22与套筒221的位于第一导油孔h24和第二导油孔h25之间的部位接触密封,使得关闭导油空间p4和第一空间p1之间的连通。
53.这样,当柱塞222相对于套筒221处于轴向一侧的第一极限位置时,导油空间p4仅
与第二空间p2连通,当时柱塞222相对于套筒221处于轴向另一侧的第二极限位置时,导油空间p4与第一空间p1、第二空间p2和第三空间p3均连通。也就是说,当离合系统处于工作状态时,主动缸进油孔h21、主动缸回油孔h22和主动缸出油孔h23彼此之间的连通关闭,当离合系统处于未工作的初始状态时,主动缸进油孔h21、主动缸回油孔h22和主动缸出油孔h23彼此连通。
54.需要说明的是,柱塞222始终与踏板组件7传动联接,使得踏板组件7的驱动力能够驱动柱塞222在第一极限位置和第二极限位置之间运动。而且,利用踏板组件7的驱动力能够驱动主动缸活塞组件22相对于主动缸缸体21整体朝向轴向一侧运动,使柱塞222从所述第一极限位置处推动套筒221使第三空间p3中的液压流体输送到从动缸1中,驱动从动缸活塞组件12。
55.而当柱塞222位于所述第一极限位置时,此时第一空间p1与导油空间p4之间的第一导油孔h24被堵住,如图3b所示,而导油空间p4通过第二导油孔h25与第二空间p2相连,那么此时优选地,当存在助力油泵(图中未示出,连接于主动缸进油孔h21)时,助力油泵输出的带有压力的液压流体经由主动缸进油孔h21进入到第一空间p1中,而此时第一空间p1相对封闭,该带有压力的液压流体即在图3b中的右侧的套筒凸缘部2212上施加一定的压力,从而使得该一定的压力与踏板组件7的驱动力一起克服复位弹簧23的阻力将第三空间p3中的液压流体经由主动缸出油孔h23输入到从动缸1中进而驱动从动缸活塞组件12。这将降低对踏板组件7的驱动力的大小的要求,也即采用较小的驱动力,使得柱塞222先与套筒221的密封部221s密封,然后助力油泵输出的带有压力的液压流体即对套筒221产生轴向的推力,起到助力的作用。而当柱塞222位于第二极限位置时,此时第一空间p1、导油空间p4、第二空间p2、第三空间p3相互连通,如图3a中所示,助力油泵输出的带有压力的液压流体经由主动缸进油孔h21进入第一空间p1,然后经由导油空间p4、第二空间p2从主动缸回游孔h22返回,带有压力的液压流体并不会对套筒221产生轴向推力而推动套筒221轴向移动。
56.在本实施方式中,复位弹簧23为圆柱形螺旋弹簧。复位弹簧23位于第三空间p3内且设置于套筒221和主动缸缸体21的底部之间。通过踏板组件7驱动柱塞222的驱动力能够克服复位弹簧23的弹簧力以驱动主动缸活塞组件22将第三空间p3内的液压流体压入从动缸缸体11内,在踏板组件7的驱动力解除之后复位弹簧23的弹簧力能够使得套筒221复位。
57.以上说明了主动缸2的结构,以下将说明主动缸2的初始状态和工作状态。
58.如图3a所示,当离合系统处于未工作的初始状态时,踏板组件7不施加驱动力。这时,在复位弹簧23的弹簧力的作用下,主动缸活塞组件22的套筒221相对于主动缸缸体21位于轴向另一侧的初始位置;例如在第三空间p3内的流体介质的压力的作用下,主动缸活塞组件22的柱塞222位于第二极限位置。因此,主动缸进油孔h21、主动缸回油孔h22和主动缸出油孔h23三者彼此连通。
59.如图3b所示,当离合系统处于工作状态的开始阶段时,踏板组件7施加驱动力。这时,在驱动力的作用下,主动缸活塞组件22的柱塞222相对于套筒221移动到第一极限位置,但是套筒221相对于初始状态并未移动。在开始阶段,主动缸进油孔h21、主动缸回油孔h22和主动缸出油孔h23三者之间的连通被关闭,但是第三空间p3内的液压流体并未输送到从动缸缸体11内。
60.如图3c所示,当离合系统处于工作状态的最终阶段时,踏板组件7施加的驱动力,
克服复位弹簧23的弹簧力使得主动缸活塞组件22整体相对于主动缸缸体21位于轴向一侧的极限位置;主动缸活塞组件22的柱塞222相对于套筒221保持第一极限位置。在另一实施方式中,优选地,踏板组件7施加的驱动力加上助力油泵的助动力(图中未示出),克服复位弹簧23的弹簧力使得主动缸活塞组件22整体相对于主动缸缸体21位于轴向一侧的极限位置;主动缸活塞组件22的柱塞222相对于套筒221保持第一极限位置。因此,主动缸进油孔h21、主动缸回油孔h22和主动缸出油孔h23三者之间的连通保持被关闭的状态,第三空间p3内的液压流体被压入从动缸1内,进而推动从动缸活塞组件12进行动作。
61.在工作完成之后,一旦踏板组件7解除驱动力,在复位弹簧23的弹簧力和第三空间p3内的流体介质的压力的作用下,主动缸活塞组件22能够复位到图3a所示的位置。
62.综上,本发明提供了一种新的车辆用离合系统,其并不限于上述具体实施方式所列举的示例,进行如下补充说明。
63.(i)虽然在以上的具体实施方式中没有具体说明,但是应当理解,该车辆可以是拖拉机,也可以是其它的用作交通载具的车辆。
64.(ii)虽然在以上的具体实施方式中没有说明,但是在根据本发明的离合系统中,当离合系统处于未工作的初始状态时,分离轴承6与离合器分离指之间可以没有如现有技术那样的间隙。
65.(iii)通过采用上述方案,根据本发明的离合系统不需要在使用一段时间之后由于离合器盘磨耗而对离合系统进行维护,因而节省了成本。也就是说,根据本发明的离合系统具有更长的使用寿命。
66.(iv)根据本发明的离合系统的主动缸2的结构与现有技术的离合系统的主动缸的结构相比具有更少的部件,结构也更加简化,因而节省了成本而且存在潜在故障的部件也相应地减少了。另外,主动缸2内的能够产生相对运动的运动副也减少了,因此减少了摩擦力和能量损耗。
67.(v)虽然在以上的具体实施方式中没有明确说明,但是应当理解由于主动缸活塞组件22的柱塞222与踏板组件7相连,因此踏板组件7解除驱动力之后,除了利用第三空间p3内的液压流体的压力,柱塞222还可以随着踏板组件7的复位而复位到图3a所示的位置。
68.(vi)在以上的具体实施方式中没有明确说明,柱塞222在图3a所示的相对于套筒221的第二极限位置可以通过固定于套筒221的挡圈来确定。