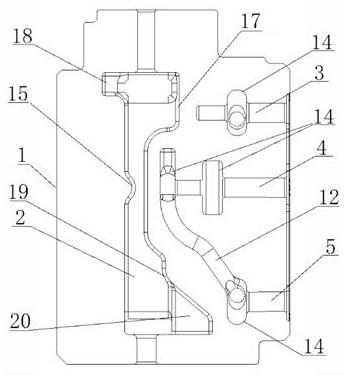
1.本发明涉及阀体铸件领域,具体涉及一种挖掘机控制阀阀体铸件。
背景技术:2.挖掘机控制阀阀体铸件是应卡特彼勒机械部件有限公司的要求及市场需求自主开发的一种液压阀体铸件,该阀体铸件应用于挖掘机控制阀。目前国内工程机械制造产业大而不强,中低档产品产能过剩,高档液压元件几乎全部依赖进口,液压行业的发展严重滞后于主机行业的发展,成为制约为装备制造业发展的主要瓶颈。目前,液压件行业整体制造技术水平与国际先进国家相比仍有较大差距。为改变国内同类铸件精度差,技术含量低的局面,挖掘机控制阀阀体铸件产品作为液压系统中的关键零部件,如何生产铸造加工出具有集成度高、可靠性强、寿命长,满足国内高端液压阀用户需求的挖掘机控制阀阀体铸件,是目前一大难题。
技术实现要素:3.为了解决上述技术问题,本发明提出了一种挖掘机控制阀阀体铸件,设计合理,结构紧凑,集成度高、可靠性强、寿命长。
4.本发明的技术方案:挖掘机控制阀阀体铸件,它包括主体、主流道、第一流道、第二流道、第三流道、第四流道、第五流道、第六流道、第七流道、第八流道和第九流道,主体是一体铸造成型铸铁块,主体内部设计有一个主流道,主流道前后联通主体的前后两个端面,主体内还设计有三个流道且三个流道位于主流道的右侧,三个流道分别是第一流道、第二流道、第三流道,三个流道相互平行设计且三个流道垂直于主流道,三个流道的口部联通主体的右侧端面,第二流道的内侧端部与第三流道的内侧端部通过第一辅助流道联通;主流道的上侧还垂直设计有第四流道且第四流道的内侧端部联通主流道,第四流道的口部联通主体的上侧端面;主流道上方还设计有第五流道,第四流道与第五流道相平行,第五流道的内侧端部通过第二辅助流道联通第二流道的中间位置;第一流道下方垂直设计有第六流道且第六流道的内侧端部联通第一流道的中间位置;第三流道下方垂直设计有第七流道且第七流道的内侧端部联通第三流道的内侧端部位置;主流道的下方靠近两端位置分别垂直设计有第八流道和第九流道,第八流道和第九流道的内侧端部联通主流道;第六流道、第七流道、第八流道和第九流道的口部联通主体的下侧端面。
5.所述的主流道的前后分别通过圆形通道联通前后的端面。
6.所述的第一流道、第二流道、第三流道、第四流道、第五流道、第六流道、第七流道都是圆形通道。
7.所述的第八流道和第九流道是矩形状通道或腰圆状通道。
8.所述的第一流道的中间位置设计有环形凹槽,第一流道通过环形凹槽与第六流道相联通;第三流道的内侧端部设计有环形凹槽,第三流道通过环形凹槽与第七流道相联通;
第二流道的中间位置和内侧端部为分别设计有环形凹槽,第三流道的内侧端部和第五流道的内侧端部分别设计有环形凹槽,第一辅助流道的一端连接第二流道的内侧端部的环形凹槽,第一辅助流道的另一端连接第三流道的内侧端部的环形凹槽,第二辅助流道的一端连接第二流道的中间位置的环形凹槽,第二辅助流道的另一端连接第五流道的内侧端部的环形凹槽。
9.所述的主流道是矩形状体,主流道的靠近后端位置的上侧设计有第一矩形状凹槽,主流道的靠近后端位置的右侧以及第一矩形状凹槽的中间和后侧位置的右侧设计有第二矩形状凹槽,主流道的靠近后端位置的左侧以及第一矩形状凹槽的中间和后侧位置的左侧设计有第三矩形状凹槽;主流道的靠近前端位置的右侧设计有二层阶梯状凹槽,二层阶梯状凹槽的右侧还设计有三角状槽;主流道靠近中间位置的左侧设计有弧形凸起。
10.所述的第一辅助流道与第二流道的内侧端部的环形凹槽连接后,还有一段向后端突出的槽。
11.本发明的优点是设计合理,结构紧凑,集成度高、可靠性强、寿命长,可替代进口,同时还可以供出口。
附图说明
12.图1是本发明的立体图一。
13.图2是本发明的立体图二。
14.图3是本发明的立体图三。
15.图4是本发明的立体图四。
16.图5是图1中第一流道、第二流道和第三流道位置的俯视剖视图。
17.图6是图5中主流道处的侧向剖视图。
18.图7是图5中第六流道、第七流道处的侧向剖视图。
19.图8是图5中第一流道处的主视剖视图。
20.图9是图5中第二流道处的主视剖视图。
21.图10是图5第三流道处的主视剖视图。
22.图11是图5第八流道处的主视剖视图。
23.图12是本发明的泥芯的示意图一。
24.图13是本发明的泥芯的示意图二。
25.图14是本发明的泥芯的示意图三。
26.图15是本发明的泥芯的示意图四。
具体实施方式
27.参照附图1
‑
11,挖掘机控制阀阀体铸件,它包括主体1、主流道2、第一流道3、第二流道4、第三流道5、第四流道6、第五流道7、第六流道8、第七流道9、第八流道10和第九流道11,主体1是一体铸造成型铸铁块,主体1内部设计有一个主流道2,主流道2前后联通主体1的前后两个端面,主体1内还设计有三个流道且三个流道位于主流道2的右侧,三个流道分别是第一流道3、第二流道4、第三流道5,三个流道相互平行设计且三个流道垂直于主流道2,三个流道的口部联通主体1的右侧端面,第二流道4的内侧端部与第三流道5的内侧端部
通过第一辅助流道12联通;主流道2的上侧还垂直设计有第四流道6且第四流道6的内侧端部联通主流道2,第四流道6的口部联通主体1的上侧端面;主流道2上方还设计有第五流道7,第四流道6与第五流道7相平行,第五流道7的内侧端部通过第二辅助流道13联通第二流道4的中间位置;第一流道3下方垂直设计有第六流道8且第六流道8的内侧端部联通第一流道3的中间位置;第三流道5下方垂直设计有第七流道9且第七流道9的内侧端部联通第三流道5的内侧端部位置;主流道2的下方靠近两端位置分别垂直设计有第八流道10和第九流道11,第八流道10和第九流道11的内侧端部联通主流道2;第六流道8、第七流道9、第八流道10和第九流道11的口部联通主体1的下侧端面。
28.所述的主流道2的前后分别通过圆形通道联通前后的端面。
29.所述的第一流道3、第二流道4、第三流道5、第四流道6、第五流道7、第六流道8、第七流道9都是圆形通道。
30.所述的第八流道10和第九流道11是矩形状通道或腰圆状通道。
31.所述的第一流道3的中间位置设计有环形凹槽14,第一流道3通过环形凹槽14与第六流道8相联通;第三流道5的内侧端部设计有环形凹槽14,第三流道5通过环形凹槽14与第七流道9相联通;第二流道4的中间位置和内侧端部为分别设计有环形凹槽14,第三流道5的内侧端部和第五流道7的内侧端部分别设计有环形凹槽14,第一辅助流道12的一端连接第二流道4的内侧端部的环形凹槽14,第一辅助流道12的另一端连接第三流道5的内侧端部的环形凹槽14,第二辅助流道13的一端连接第二流道4的中间位置的环形凹槽14,第二辅助流道13的另一端连接第五流道7的内侧端部的环形凹槽14。
32.所述的主流道2是矩形状体,主流道2的靠近后端位置的上侧设计有第一矩形状凹槽16,主流道2的靠近后端位置的右侧以及第一矩形状凹槽16的中间和后侧位置的右侧设计有第二矩形状凹槽17,主流道2的靠近后端位置的左侧以及第一矩形状凹槽16的中间和后侧位置的左侧设计有第三矩形状凹槽18;主流道2的靠近前端位置的右侧设计有二层阶梯状凹槽19,二层阶梯状凹槽19的右侧还设计有三角状槽20;主流道2靠近中间位置的左侧设计有弧形凸起15。
33.所述的第一辅助流道12与第二流道4的内侧端部的环形凹槽14连接后,还有一段向后端突出的槽。
34.本发明产品在生产过程中主流道2部分泥芯厚大,其余流道的部分小泥芯却细小且支撑不足,容易在浇注后产生泥芯弯曲变形,厚大泥芯容易在浇注过程中发气,造成上表面气孔。
35.参照附图12
‑
15,本发明阀体铸件在生产过程中,根据产品外形制作砂箱内的型腔,再根据产品的流道结构设计主流道大泥芯21和其余流道小泥芯22,然后把主流道大泥芯21和其余流道小泥芯22指定放置在砂箱的型腔中,合上砂箱,再把铁水从预留的浇冒口倒入,等待冷却后,打开砂箱,取出阀体铸件,再把内部泥芯清理导出,完成加工。其中油道变形:本发明的小泥芯22采用4mm的芯骨放入直径9.5mm的泥芯孔内以增强泥芯的强度且在该小泥芯上方加芯撑支撑小泥芯,让芯骨和芯撑共同作用此小泥芯,来减少变形。对于气孔缺陷:主流道大泥芯21采用多处钻孔方式进行排气,这样能让泥芯中的气体在所钻孔中排出,避免铸件产生气孔缺陷。在主流道大泥芯21的前后两端圆形通道的轴心方向进行钻孔23,钻孔深度为主流道大泥芯的三分之一长度;在第四流道、第八流道、第九流道的小泥芯
的轴心方向进行钻孔23,钻孔的深度小于主流道大泥芯该处的主流道轴向垂直方向的最大厚度。
36.本发明阀体铸件的主要技术参数:1)、材质:qt550。
37.2)、抗拉强度(单铸试棒):≥550mpa。
38.3)、布氏硬度:187
‑
255hbw。
39.4)、球化等级:≥3级。
40.5)、金相组织应符合gb/t 9441
‑
2009评定。
41.6)、无夹渣、气孔、缩孔、缩松等铸造缺陷。
42.7)、阀体重量:15.5kg。