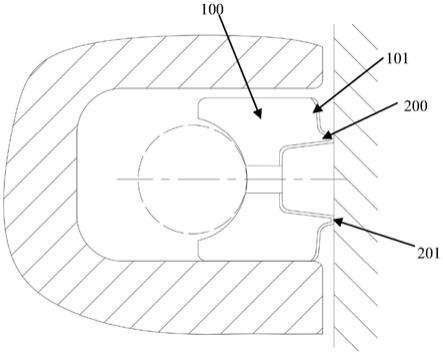
1.本实用新型涉及一种油环,特别涉及一种具有低摩擦低机油耗性能的钢质油环。
背景技术:2.二组合式油环,包括油环本体和对油环本体起支撑作用的弹簧。该油环本体的内侧具有容纳该弹簧的弹簧槽,弹簧装入油环本体,进而再装入气缸后,弹簧受压缩,因而对油环本体产生了所需的张力,并依靠此张力使油环外圆的刮油带产生对机油的刮除作用,使活塞环组保持适量的机油润滑并维持正常的使用功能。
3.通过长期的经验发现,油环有三个参数最为重要:油环的材料、刮油带的宽度和刮油带的涂层。它们对整机的机油耗性能、颗粒排放和可靠性有重要影响。油环的材料决定了其抗断强度、刮油带宽度决定了环与气缸壁的接触面积,进而影响环对气缸壁的接触压力,最终影响环的刮油能力和摩擦功耗。刮油带的涂层也对环与气缸壁的摩擦磨损性能有重要影响。现已有一些新技术对传统油环进行改善,比如采用异形刮油带、采用新的涂层等。现有技术提供了一种多部件式油环(cn2010800438001),要求要先氮化处理,氮化会造成氮脆性,对油环的抗断性能和疲劳强度会有不利影响。
技术实现要素:4.实用新型目的:为了解决现有技术的问题,本实用新型提供了一种具有低摩擦低机油耗性能的钢质油环,本实用新型减小工作油带宽度,降低切向弹力,进而降低摩擦功耗。
5.技术方案:本实用新型所述的一种具有低摩擦低机油耗性能的钢质油环,包括油环本体及其刮油带,所述刮油带为设置在油环本体上的向外凸出的凸部,两个所述刮油带在所述油环本体的环高中心线两侧对称设置,两个所述刮油带之间的间距与所述油环本体的环高比为0.35~0.5。
6.作为本实用新型的一种优选结构,所述刮油带的外圆面设置有厚度为0.01~0.04mm的类金刚石镀膜作为第一涂层。
7.作为本实用新型的一种优选结构,所述第一涂层的厚度为0.015~0.03mm,第一涂层的硬度为2000~4000hv0.025。
8.作为本实用新型的一种优选结构,所述刮油带的两棱边处具有截面呈圆弧形的过渡带,所述过渡带的截面圆弧半径为0.005~0.02mm。
9.作为本实用新型的一种优选结构,所述刮油带的宽度为0.05~0.15mm。
10.作为本实用新型的一种优选结构,所述刮油带凸出的高度为0.15~0.3mm。
11.作为本实用新型的一种优选结构,油环的名义切向弹力与名义缸径的比值为0.20~0.40n/mm。
12.作为本实用新型的一种优选结构,油环的名义切向弹力与名义缸径的比值为0.20~0.30n/mm。
13.作为本实用新型的一种优选结构,刮油带内侧角度α为5~10
°
。
14.作为本实用新型的一种优选结构,刮油带外侧角度β为10~20
°
。
15.有益效果:(1)本实用新型通过减小工作油带的宽度、采用低摩擦高耐磨的涂层,改善油环性能,实现不减小甚至提高接触压力的前提下,降低切向弹力,提高油环强度、降低摩擦功耗、提高耐磨性。(2)本实用新型通过在刮油带的外圆面设置有具有低摩擦系数和自润滑性能、坚硬耐磨的涂层降低摩擦功耗并且提高耐磨性,满足整机长寿命的要求。(3)本实用新型通过缩小了两刮油带的间距,使得刮油带靠向环高的中心线,因而有利于在加工和使用过程保持极小的径向偏移度,进而有利于机油耗的控制,并且防止由于单侧刮油带与气缸接触而导致的拉缸现象。(4)本实用新型通过油环整体结构的改进在满足耐磨以及降低油耗的基础上,保证了刮油带为常规结构,并非现有技术中的异形结构,因而提供了一个比较简单的型材工艺条件,有利于控制型材成本。
附图说明
16.图1为本实用新型的钢质油环的整体结构示意图;
17.图2为本实用新型图1的钢质油环的a-a截面图;
18.图3为本实用新型图1的i部的放大结构示意图;
19.图4为本实用新型的钢质油环在活塞的环槽中工作状态图;
20.图5为油带径向偏移度的结构示意图;
21.图6为本实用新型采用的涂层与其他涂层的耐磨性对比图。
具体实施方式
22.本实用新型的钢质油环整体结构如图1所示,具体为螺旋撑簧油环,钢质油环的结构满足iso6626-3的加工标准,本实施例所述的钢质油环适用缸径为该钢质油环的横截面如图2和图3所示,钢质油环包括油环本体100、刮油带200以及设置在油环本体100内圆槽处的弹簧300,弹簧装入油环本体,进而再装入气缸后,弹簧受压缩,因而对油环本体产生了所需的张力,并依靠此张力使油环外圆的刮油带产生对机油的刮除作用,钢质油环的工作状态如图4所示。
23.钢质油环的基体材料为碳钢或合金钢,具有370~580hv的维氏硬度,本实施例的钢质油环采用具有较高硬度的碳钢或合金钢材料,因而端面无需做硬化涂层处理即可满足油环的端面的耐磨性要求,并且,由于该材料具有极高的抗拉强度,因而该活环具有极高的抗断性能,即使用手也很难掰断,特别适用于具有极高爆发压力的发动机。为了进一步提高钢质油环的性能,作为一种优选结构,本实用新型的油环本体的油带两侧面及外侧其余部位具有第二涂层102,第二涂层102为厚度为0.01~0.04mm的类金刚石镀膜(dlc涂层),优选地,第二涂层的厚度为0.015~0.03mm,硬度为2000~4000hv0.025,该涂层外观呈碳黑色,涂层中不含氢,涂层金相组织为非晶态。
24.如图2所示,刮油带200为设置在油环本体100上的向外凸出的凸部,两个刮油带200在油环本体100的环高中心线o1两侧对称设置,两个刮油带200之间的间距b3与油环本体100的环高h1比值为0.35~0.5,在本实施例中,刮油带200的宽度h5为0.05~0.15mm,刮油带200凸出的高度t为0.15~0.3mm,如图5所示,本实施例的钢质油环与常规设计相比,缩
小了两刮油带的间距,有利于刮油带靠向环高的中心线,因而有利于在加工和使用过程保持极小的径向偏移度,径向偏移度为图5中所示的x的大小,进而有利于机油耗的控制,并且防止由于单侧刮油带与气缸接触而导致的拉缸现象。
25.刮油带200的外圆面设置有厚度为0.01~0.04mm的类金刚石镀膜(dlc涂层)作为第一涂层201,优选地,第一涂层的厚度p为0.015~0.03mm,第一涂层201的硬度为2000~4000hv0.025,同样地,该涂层外观呈碳黑色,涂层中不含氢,涂层金相组织为非晶态。本实施例通过在刮油带200的外圆面设置有具有低摩擦系数和自润滑性能、坚硬耐磨的涂层,进一步降低摩擦功耗并且提高耐磨性,满足整机长寿命的要求,比如对于重卡柴油机而言,能够满足200万公里的b10寿命要求。
26.为了进一步验证该dlc涂层的优势,如图6所示,将该dlc涂层与现有的其他涂层进行磨损性能测试,试验设备:快速磨损试验机,转速:800rpm,行程:110mm;机油状态:机油中掺入了万分之六的500目的al2o3磨粒,富油状态;气缸套状态:110mm缸径,贝氏体材料,硬度300hb,具有平台珩磨网纹;试验环状态:除涂层不同外其余状态相同,检查试验前后的闭口间隙差值来评估耐磨性;试验时长:16h。从图6可以看出,本实用新型选择的耐磨涂层的磨损性能明显优于现有技术中其他涂层的磨损性能。
27.为了进一步增加第一涂层201在刮油带200外圆面的附着稳定性并防止尖锐棱边崩缺现象,本实施例在刮油带的上下两个棱边处设置有一个导角作为过渡带202,具体地,刮油带200与油环本体100之间的外角101包括与刮油带200的外圆面连接的第一外角面1011以及将第一外角面1011与油环本体100的顶面连接的第二外角面1012,刮油带200的两棱边处具有截面呈圆弧形的过渡带202,即过渡带202设置于刮油带200的棱与第一外角面1011之间,过渡带202的截面圆弧半径为0.005~0.02mm。
28.如图3所示,本实施例中在刮油带内侧角度α为5~10
°
,刮油带外侧角度β为10~20
°
,油环的名义切向弹力与名义缸径的比值ft/d1为0.20~0.40n/mm,作为一种优选结构,钢质油环的名义切向弹力与名义缸径的比值ft/d1为0.20~0.30n/mm。
29.本实用新型通过减小工作油带宽度改善油环性能,提高油环强度、降低弹力、降低机油耗、降低摩擦功耗,并通过外圆面具有低摩擦系数和自润滑性能、坚硬耐磨的涂层进一步降低摩擦功耗并且提高耐磨性,满足整机长寿命的要求。