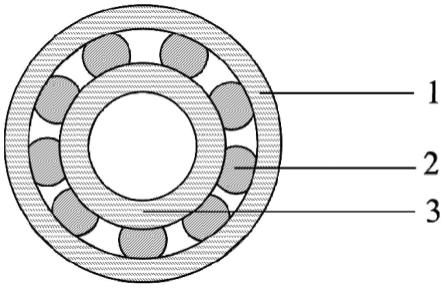
1.本发明属于轴承材料技术领域,涉及高温耐磨轴承及其制备方法。
背景技术:2.高温耐磨轴承是一种需要耐高温并同时具有良好耐磨性的轴承。由于特殊工况的要求,需要轴承具有优异的耐高温和抗磨损性能,同时必须具备较低的摩擦系数,以满足轴承的运动摩擦行为。常规金属材料制备的轴承在高温下将发生软化,同时其耐磨性大幅降低,这必然导致轴承的结构性变化,包括外圈、内圈和轴承的结构变形和磨损。轴承在结构上的变化将会导致设备突发性的停机事故,而且轴承的更换相对来说是较大的维修工程,需要较大的时间成本。因此轴承的失效不仅会造成突发的事故损失,同时也将引入巨大的时间成本,总体上造成巨大的经济和时间损失。
3.另一方面,高温合金材料(镍基、钴基高温合金等)所制备的高温轴承具有较为优异的高温性能,但其耐磨性相对较差,同时其摩擦系数相对较高,不利于轴承的运动行为。因此,寻求更为优异的材料制备高温耐磨轴承,对极端工况下的特殊需求有着极其重要的意义和迫切应用需求。
技术实现要素:4.本发明的一个目的是提供一种高温耐磨轴承,解决了现有轴承在苛刻工况下耐磨性不足和高温性能较低的问题。
5.本发明的另一个目的是提供一种高温耐磨轴承的制备方法。
6.本发明所采用的第一技术方案是一种高温耐磨轴承,包括轴承外圈、轴承内圈和滚珠,轴承外圈、轴承内圈和滚珠都以高温tinb合金为基体,轴承外圈的内壁、轴承内圈的外壁以及滚珠表面都具有原位生成的层状多尺度(tinb)c耐磨层。
7.其中,层状多尺度(tinb)c耐磨层内(tinb)c的体积分数大于97%。
8.层状多尺度(tinb)c耐磨层由外层、中间层和内层组成,外层由准纳米级的(tinb)c颗粒组成,中间层由微米级的(tinb)c颗粒组成,内层由亚微米级的(tinb)c颗粒组成。
9.本发明所采用的第二技术方案是一种高温耐磨轴承的制备方法,包括以下步骤:
10.步骤1,按照质量百分比分别称取以下组分:果壳木炭80~85%,高纯石墨粉1~5%,高纯na2co32~5%,高纯baco310~15%,以上各组分的质量百分比之和为100%;
11.步骤2,将步骤1称取的各组分装入混料机中,混料10min~20min,制得均匀混合粉末;
12.步骤3,将tinb合金原料按照轴承外圈、轴承内圈和滚珠的既定尺寸进行机械加工,并且对表面进行精加工和抛光处理,使工件表面粗糙度ra不大于3μm;
13.步骤4,在轴承外圈和轴承内圈的非工作面涂覆防渗碳涂料,涂层厚度为0.5mm~1.2mm,该涂层厚度若太小,会影响轴承外圈和轴承内圈非工作面的防渗碳效果,若太大,容易剥落,导致渗碳处理时起不到防渗碳的效果;
14.步骤5,将步骤2中所得混合粉末铺设在模具内部底面上,然后将步骤3加工后的滚珠、步骤4涂覆后的轴承外圈和轴承内圈放置在铺设有混合粉末的模具内部,最后用混合粉末填充模具中孔隙;
15.步骤6,将步骤5填充好的模具装入高温炉内,进行850℃~1150℃高温渗碳处理,即可在轴承外圈内壁、轴承内圈外壁和滚珠表面原位生成层状多尺度(tinb)c耐磨层;
16.步骤7,清除步骤4中在轴承外圈和轴承内圈非工作面所涂覆的防渗碳涂料,然后对轴承外圈、轴承内圈和滚珠进行喷砂和抛光处理,将轴承内圈、滚珠和轴承外圈组装在一起,即制得高温耐磨轴承。
17.步骤1中,果壳木炭和高纯石墨粉的质量百分比总和不大于90%,果壳木炭为颗粒状,粒径为0.1mm~7.5mm。
18.步骤5中,将步骤3加工后的滚珠、步骤4涂覆后的轴承外圈和轴承内圈间隔放置在铺设有混合粉末的模具内部,相邻间距不小于4mm,模具内壁与滚珠、轴承外圈、轴承内圈的间距不小于3mm,最后用混合粉末填充模具中孔隙,在顶面平铺一层混合粉末。
19.步骤5中,将步骤3加工后的滚珠、步骤4涂覆后的轴承外圈和轴承内圈依次叠层铺设在模具内部,中间由混合粉末间隔开,滚珠、轴承外圈和轴承内圈之间的相邻间距不小于4mm,模具内壁与滚珠、轴承外圈、轴承内圈的间距不小于3mm,最后用混合粉末填充模具中孔隙,在顶面平铺一层混合粉末。
20.步骤6中,高温渗碳处理包括将炉温升至300℃~400℃保温10min~20min进行预脱气、脱水,然后升温至850℃~1150℃保温1h~24h进行表面渗碳处理,再降温至400-500℃,随后随炉冷却至室温。
21.步骤6中,炉温的升温速率和降温速率都不高于10℃/min。
22.高温炉具有良好的密闭性,高温渗碳处理过程中,炉内气压不小于0.3mpa。
23.本发明的有益效果是,tinb合金具有优异的高温强韧性和抗蠕变性能,在其表面原位生成的层状多尺度(tinb)c耐磨层具有优异的耐高温、抗腐蚀和抗磨损性能,可满足轴承类较低摩擦系数的要求;本发明利用固体渗碳工艺,在用tinb高温合金制备的轴承外圈内壁、内圈外壁和滚珠表面原位生成高致密、高硬、高耐磨、耐高温、耐腐蚀的层状多尺度(tinb)c耐磨层,层状多尺度结构具有改善金属碳化物高脆性的作用,进而使得表面(tinb)c耐磨层不仅表现出超高的耐磨性,同时兼有良好的韧性;同时,原位生成的(tinb)c耐磨层具有更为优异的异质界面结合强度,改善了耐磨层易于剥落的问题;相较于常规渗碳或渗氮工艺制备的耐磨轴承(表面硬度不超hv 900),本发明高温耐磨轴承表面(tinb)c耐磨层的硬度不小于hv 2000;同时,表面(tinb)c耐磨层具有更低的干摩擦系数,(tinb)c/(tinb)c干摩擦系数小于0.1,而常规钢/钢干摩擦系数不小于0.3,因而表面(tinb)c耐磨层的轴承不仅可以大幅提高轴承的耐磨性,同时更低的摩擦系数减小了轴承在运动过程中的摩擦阻力。
附图说明
24.图1是本发明高温耐磨轴承的结构示意图;
25.图2是本发明高温耐磨轴承表面(tinb)c耐磨层位置示意图;
26.图3是本发明高温耐磨轴承表面(tinb)c耐磨层结构示意图。
27.图中,1.轴承外圈,2.滚珠,3.轴承内圈,4.基体,5.层状多尺度(tinb)c耐磨层,6.外层,7.中间层,8.内层。
具体实施方式
28.下面结合附图和具体实施方式对本发明进行详细说明。
29.本发明一种高温耐磨轴承,参照图1和图2,包括轴承外圈1、轴承内圈3和滚珠2,轴承外圈1、轴承内圈3和滚珠2都以高温tinb合金为基体4,轴承外圈1的内壁、轴承内圈3的外壁以及滚珠2表面都具有原位生成的层状多尺度(tinb)c耐磨层5,表面耐磨层是在tinb高温合金基体表面原位生成,与基体具有优异的结合界面和异质界面结合力。
30.其中,层状多尺度(tinb)c耐磨层5内(tinb)c的体积分数大于97%。
31.参照图3,层状多尺度(tinb)c耐磨层5由外层6、中间层7和内层8组成,外层6由准纳米级的(tinb)c颗粒组成,中间层7由微米级的(tinb)c颗粒组成,内层8由亚微米级的(tinb)c颗粒组成。层状多尺度结构大幅改善了金属碳化物类材料的高脆性,同时表面(tinb)c耐磨层的高硬度(大于hv 2000)大幅提高工件的表面耐磨性。
32.实施例1
33.制备一种滚珠尺寸为φ6.35mm的高温耐磨轴承,包括以下步骤:
34.步骤1,按照质量百分比分别称取以下组分:颗粒等级为1mm级的果壳木炭80%,高纯石墨粉5%,高纯na2co35%,高纯baco310%,以上各组分的质量百分比之和为100%;高纯石墨粉末的的纯度大于99.0%,高纯na2co3的纯度大于99.8%;高纯baco3的纯度大于99.0%;
35.步骤2,将步骤1称取的各组分粉末装入混料机中,混料10min,制得均匀混合粉末;
36.步骤3,按照轴承中滚珠直径φ6.35mm,将tinb合金原料机械加工成轴承外圈、轴承内圈和滚珠工件,对其表面进行精加工和抛光处理,使工件表面粗糙度ra约为3μm;
37.步骤4,在轴承外圈和轴承内圈的非工作面涂覆防渗碳涂料,涂层厚度为0.6mm,以防止非工作面发生渗碳,此处的非工作面,是指除过轴承外圈内壁和轴承内圈外壁与滚珠发生滑动作用以外的表面;
38.步骤5,将步骤2中所得混合粉末均匀铺在在模具底面上,然后将步骤3加工后的滚珠、步骤4涂覆后的轴承外圈和轴承内圈依次叠层铺设在模具内部,中间由混合粉末间隔开,滚珠、轴承外圈和轴承内圈之间的相邻间距约为5mm,模具内壁与滚珠、轴承外圈、轴承内圈的最小间距约为3mm,最后用混合粉末填充模具中孔隙,在顶面平铺一层混合粉末;
39.步骤6,将步骤5中填充好的模具装入高温炉内,将炉温以8℃/min升至300℃保温10min进行预脱气、脱水,然后以7℃/min升温至850℃保温24h进行表面渗碳处理(炉内气压约为0.3mpa),再以6℃/min降温至500℃,随后随炉冷却至室温,即可在轴承外圈内壁、滚珠表面和轴承内圈外壁表面形成均匀的层状多尺度(tinb)c耐磨层;
40.步骤7,清除步骤4中对轴承外圈和轴承内圈非工作面的涂覆防渗碳涂料,然后对轴承外圈、轴承内圈和滚珠进行喷砂和抛光处理,将轴承内圈、滚珠和轴承外圈组装在一起,即制得滚珠尺寸为φ6.35mm的高温耐磨轴承。
41.对实施例1制备的滚珠尺寸为φ6.35mm的高温耐磨轴承进行组织和性能检测,其中,该高温耐磨轴承外圈内壁、滚珠表面和轴承内圈外壁表面形成均匀致密的层状多尺度
(tinb)c耐磨层,耐磨层中(tinb)c的体积百分比为98.6%,余量为fe、si和sic,耐磨层厚度约为110μm,表面硬度平均值为hv
0.1 2514,(tinb)c耐磨层/(tinb)c耐磨层摩擦副干摩擦测试得出的磨损率为3.2
×
10-7
g/m,约是tinb基体的1/157。
42.实施例2
43.制备一种滚珠尺寸为φ4.763mm的高温耐磨轴承,包括以下步骤:
44.步骤1,按照质量百分比分别称取以下组分:颗粒等级为5mm级的果壳木炭85%,高纯石墨粉1%,高纯na2co34%,高纯baco310%,以上各组分的质量百分比之和为100%;
45.步骤2,将步骤1称取的各组分粉末装入混料机中,混料20min,制得均匀混合粉末;
46.步骤3,按照轴承中滚珠直径φ4.763mm,将tinb合金原料机械加工成轴承外圈、轴承内圈和滚珠工件,对其表面进行精加工和抛光处理,使工件表面粗糙度ra约为2μm;
47.步骤4,在轴承外圈和轴承内圈的非工作面涂覆防渗碳涂料,涂层厚度为0.5mm,以防止非工作面发生渗碳,此处的非工作面,是指除过轴承外圈内壁和轴承内圈外壁与滚珠发生滑动作用以外的表面;
48.步骤5,将步骤2中所得混合粉末均匀铺在在模具底,然后将步骤3加工后的滚珠、步骤4涂覆后的轴承外圈和轴承内圈间隔放置在铺设有混合粉末的模具内部,相邻间距约为5mm,模具内壁与滚珠、轴承外圈、轴承内圈的最小间距约为4mm,最后用混合粉末填充模具中孔隙,在顶面平铺一层混合粉末;
49.步骤6,将步骤5中填充好的模具装入高温炉内,将炉温以7℃/min升至300℃保温20min进行预脱气、脱水,然后以6℃/min升温至1150℃保温1h进行表面渗碳处理(炉内气压约为0.4mpa),再以6℃/min降温至420℃,随后随炉冷却,降温至室温,即可在轴承外圈内壁、滚珠表面和内圈外壁表面形成层状多尺度(tinb)c耐磨层;
50.步骤7,清除步骤4中对轴承外圈和轴承内圈非工作面涂覆的防渗碳涂料,然后对轴承外圈、轴承内圈和滚珠进行喷砂和抛光处理,将轴承内圈、滚珠和轴承外圈组装在一起,即制得滚珠尺寸为φ4.763mm高温耐磨轴承。
51.对实施例2制备的滚珠尺寸为φ4.763mm的高温耐磨轴承进行组织和性能检测,其中,该高温耐磨轴承外圈内壁、滚珠表面和轴承内圈外壁表面形成致密层状多尺度(tinb)c耐磨层,耐磨层中(tinb)c的体积百分比为99.1%,余量为fe、si和sic,耐磨层厚度约为36μm,表面硬度平均值为hv
0.1 2363,(tinb)c耐磨层/(tinb)c耐磨层摩擦副干摩擦测试得出(tinb)c耐磨层的磨损率为3.3
×
10-7
g/m,约是tinb基体的1/139。
52.实施例3
53.制备一种滚珠尺寸为φ7.937mm的高温耐磨轴承,包括以下步骤:
54.步骤1,按照质量百分比分别称取以下组分:颗粒等级为2mm级的果壳木炭83%,高纯石墨粉3%,高纯na2co32%,高纯baco312%,以上各组分的质量百分比之和为100%;高纯石墨粉末的的纯度大于99.0%,高纯na2co3的纯度大于99.8%;高纯baco3的纯度大于99.0%;
55.步骤2,将步骤1称取的各组分粉末装入混料机中,混料15min,制得均匀混合粉末;
56.步骤3,按照轴承中滚珠直径φ7.937mm,将tinb合金原料机械加工成轴承外圈、轴承内圈和滚珠工件,对其表面进行精加工和抛光处理,使工件表面粗糙度ra约为2μm;
57.步骤4,在轴承外圈和轴承内圈的非工作面涂覆防渗碳涂料,涂层厚度为0.8mm,以
防止非工作面发生渗碳,此处的非工作面,是指除过轴承外圈内壁和轴承内圈外壁与滚珠发生滑动作用以外的表面;
58.步骤5,将步骤2中所得混合粉末均匀铺在在模具底,然后将步骤3加工后的滚珠、步骤4涂覆后的轴承外圈和轴承内圈依次叠层铺设在模具内部,中间由混合粉末间隔开,滚珠、轴承外圈和轴承内圈之间的相邻间距约为8mm,模具内壁与滚珠、轴承外圈、轴承内圈的最小间距约为4mm,最后用混合粉末填充模具中孔隙,在顶面平铺一层混合粉末;
59.步骤6,将步骤5中填充好的模具装入高温炉内,将炉温以8℃/min升至400℃保温10min进行预脱气、脱水,然后以7℃/min升温至1100℃保温8h进行表面渗碳处理(炉内气压约为0.5mpa),再以6℃/min降温至400℃,随后随炉冷却,降温至室温,即可在轴承外圈内壁、滚珠表面和轴承内圈外壁表面形成层状多尺度(tinb)c耐磨层;
60.步骤7,清除步骤4中对轴承外圈和轴承内圈非工作面涂覆的防渗碳涂料,然后对轴承外圈、轴承内圈和滚珠进行喷砂和抛光处理,将轴承内圈、滚珠和轴承外圈组装在一起,即制得滚珠尺寸为φ7.937mm高温耐磨轴承。
61.对实施例3制备的滚珠尺寸为φ7.937mm的高温耐磨轴承进行组织和性能检测,其中,该高温耐磨轴承外圈内壁、滚珠表面和轴承内圈外壁形成致密层状多尺度(tinb)c耐磨层,(tinb)c的体积百分比为98.9%,余量为fe、si和sic,耐磨层厚度约83μm,表面硬度平均值为hv
0.1 2482,(tinb)c耐磨层/(tinb)c耐磨层摩擦副干摩擦测试得出(tinb)c耐磨层的磨损率为3.2
×
10-7
g/m,约是tinb基体的1/152。
62.实施例4
63.制备一种滚珠尺寸为φ16.668mm的高温耐磨轴承,包括以下步骤:
64.步骤1,按照质量百分比分别称取以下组分:颗粒等级为5mm级的果壳木炭81%,高纯石墨粉4%,高纯na2co3为2%,高纯baco3为13%,以上各组分的质量百分比之和为100%;
65.步骤2,将步骤1称取的各组分粉末装入混料机中,混料20min,制得均匀混合粉末;
66.步骤3,按照轴承中滚珠直径φ16.668mm,将tinb合金原料机械加工成轴承外圈、轴承内圈和滚珠工件,对其表面进行精加工和抛光处理,使工件表面粗糙度ra约为1.5μm;
67.步骤4,在轴承外圈和轴承内圈的非工作面涂覆防渗碳涂料,涂层厚度为1.2mm,以防止非工作面发生渗碳,此处的非工作面,是指除过轴承外圈内壁和轴承内圈外壁与滚珠发生滑动作用以外的表面;
68.步骤5,将步骤2中所得混合粉末均匀铺在在模具底面上,然后将步骤3加工后的滚珠、步骤4涂覆后的轴承外圈和轴承内圈依次叠层铺设在模具内部,中间由混合粉末间隔开,滚珠、轴承外圈和轴承内圈之间的相邻间距约为13mm,模具内壁与滚珠、轴承外圈、轴承内圈的最小间距约为9mm,最后用混合粉末填充模具中孔隙,在顶面平铺一层混合粉末;
69.步骤6,将步骤5中填充好的模具装入高温炉内,将炉温以8℃/min升至300℃保温10min进行预脱气、脱水,然后以6℃/min升温至1100℃保温16h进行表面渗碳处理(炉内气压约为0.3mpa),再以6℃/min降温至450℃,随后随炉冷却,降温至室温,即可在轴承外圈内壁、滚珠表面和轴承内圈外壁表面形成均匀的层状多尺度(tinb)c耐磨层;
70.步骤7,清除步骤4中对轴承外圈和轴承内圈非工作面的涂覆的防渗碳涂料,然后对轴承外圈、轴承内圈和滚珠进行喷砂和抛光处理,将轴承内圈、滚珠和轴承外圈组装在一起,即制得滚珠尺寸为φ16.668mm的高温耐磨轴承。
71.对实施例4制备的滚珠尺寸为φ16.668mm的高温耐磨轴承进行组织和性能检测,其中,该高温耐磨轴承外圈内壁、滚珠表面和内圈外壁形成致密层状多尺度(tinb)c耐磨层,(tinb)c的体积百分比为99.2%,余量为fe、si和sic,耐磨层厚度约124μm,表面硬度平均值为hv
0.1 2531,(tinb)c耐磨层/(tinb)c耐磨层摩擦副干摩擦测试得出(tinb)c耐磨层的磨损率为3.2
×
10-7
g/m,约是tinb基体的1/158。
72.实施例5
73.制备一种滚珠尺寸为φ21.431mm的高温耐磨轴承,包括以下步骤:
74.步骤1,按照质量百分比分别称取以下组分:颗粒等级为7.5mm级的果壳木炭82%,高纯石墨粉1%,高纯na2co32%,高纯baco315%,以上各组分的质量百分比之和为100%;
75.步骤2,将步骤1称取的各组分粉末装入混料机中,混料15min,制得均匀混合粉末;
76.步骤3,按照轴承中滚珠直径φ21.431mm,将tinb合金原料机械加工成轴承外圈、轴承内圈和滚珠工件,对其表面进行精加工和抛光处理,使工件表面粗糙度ra约为1.5μm;
77.步骤4,在轴承外圈和轴承内圈的非工作面涂覆防渗碳涂料,涂层厚度为1.0mm,以防止非工作面发生渗碳,此处的非工作面,是指除过轴承外圈内壁和轴承内圈外壁与滚珠发生滑动作用以外的表面;
78.步骤5,将步骤2中所得混合粉末均匀铺在在模具底,然后将步骤3加工后的滚珠、步骤4涂覆后的轴承外圈和轴承内圈依次叠层铺设在模具内部,中间由混合粉末间隔开,滚珠、轴承外圈和轴承内圈之间的相邻间距约为15mm,模具内壁与滚珠、轴承外圈、轴承内圈的最小间距约为10mm,最后用混合粉末填充模具中孔隙,在顶面平铺一层混合粉末;
79.步骤6,将步骤5中填充好的模具装入高温炉内,将炉温以8℃/min升至300℃保温10min进行预脱气、脱水,然后以7℃/min升温至950℃保温24h进行表面渗碳处理(炉内气压约为0.6mpa),再以6℃/min降温至480℃,随后随炉冷却,降温至室温,即可在轴承外圈内壁、滚珠表面和轴承内圈外壁表面均匀形成层状多尺度(tinb)c耐磨层;
80.步骤7,清除步骤4中对轴承外圈和轴承内圈非工作面涂覆的防渗碳涂料,然后对轴承外圈、轴承内圈和滚珠进行喷砂和抛光处理,将轴承内圈、滚珠和轴承外圈组装在一起,即得滚珠尺寸为φ21.431mm高温耐磨轴承。
81.对实施例5制备的滚珠尺寸为φ21.431mm的高温耐磨轴承进行组织和性能检测,其中,该高温耐磨轴承外圈内壁、滚珠表面和轴承内圈外壁形成致密层状多尺度(tinb)c耐磨层,(tinb)c的体积百分比为99.3%,余量为fe、si和sic,耐磨层厚度约118μm,表面硬度平均值为hv
0.1 2548,(tinb)c耐磨层/(tinb)c耐磨层摩擦副干摩擦测试得出(tinb)c耐磨层的磨损率为3.1
×
10-7
g/m,约是tinb基体的1/161。