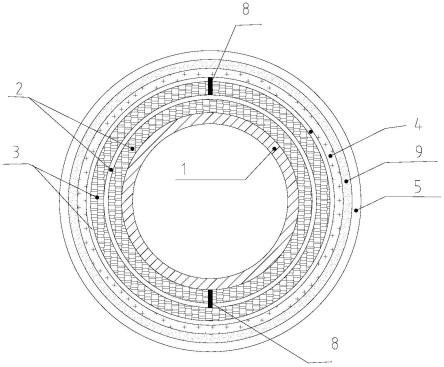
1.本实用新型属于燃气输送工程技术领域,尤其涉及一种燃气输送管道连接处的加固防腐绝缘层结构。
背景技术:2.燃气输送管网中的大小直径变异口径管道连接、燃气管的变向连接,如弯头、各种三通、四通或y型三通的连接统称为燃气输送管道连接处。燃气输送管道连接处通过防腐层检测发现,在燃气管网管道中的弯头、三通、四通和引入管处部位经过2-3年运行后,其防腐层就会开裂失效,产生接地腐蚀。如果不及时处理,防腐层很快就被腐蚀而穿孔,导致输气管网漏气,甚至发生爆燃事故。专利授权公告号为cn 214064163 u的专利文献公开了一种燃气输送管道连接处的加固防腐绝缘层结构,包括燃气管道连接处的连接件,其特征是:所述燃气管道连接处的连接件包括碳纤维布加固防腐层、带膜无纺布套筒和整形带,所述连接件外圆表面设有碳纤维布加固防腐层,所述碳纤维布加固防腐层外面包覆有带膜无纺布套筒,带膜无纺布套筒上设有若干条整形带,所述碳纤维布加固防腐层和带膜无纺布套筒之间设有树脂材料固化层。本实用新型针对燃气管道连接处的腐蚀部位进行加固防腐,使燃气管道连接处可安全运行10-20年,碳纤维布加固防腐层耐压是其它加固防腐方法的10倍以上。上述现有技术在施工中又出现了新的问题。问题一是,燃气管道补漏施工完成后需要采用电火花检测加固防腐层厚度是否合格。上述的加固防腐结构在进行电火花检测时,末端经常发出误报信号。剖开施工位置实测其防腐层厚度完全合格,但是电火花的检测结论却是不合格,影响施工进度。出现上述问题是由于碳纤维布是良好的导电材料;问题二是,施工中由于弯头处复膜无纺布有很大的褶皱,用整形带限制褶皱注胶后,褶皱会被胶液顶起,无法限制弯头处胶液的厚度,使其结构层厚度不均匀,降低了弯头处抗压耐腐蚀能力。
技术实现要素:3.本实用新型是为了克服现有技术中的不足,提供一种燃气输送管道连接处的加固防腐绝缘层结构,既能保证燃气管道连接处腐蚀部位的良好防腐补强性能,又能避免电火花检测时末端出现误报信号;同时还可以保证弯头处结构层厚度均匀,提高了弯头处抗压耐腐蚀能力。
4.本实用新型为实现上述目的,通过以下技术方案实现,一种燃气输送管道连接处的加固防腐绝缘层结构,包括燃气管道连接件,其特征是:所述燃气管道连接件自其外圆依次设有第一聚乙烯膜复合无纺布层、第二聚乙烯膜复合无纺布层、胶粘带封口层和整形带,所述第一聚乙烯膜复合无纺布层及第二聚乙烯膜复合无纺布层缠绕燃气管道连接件呈对口式连接,沿对口位置处纵向设有若干固接封口点,固接后的第二聚乙烯膜复合无纺布层包覆胶粘带封口层,胶粘带封口层通过整形带整形加固。
5.所述燃气管道连接件自其外圆侧依次包覆有第一聚乙烯膜复合无纺布层、1-3层
树脂碳纤维布层、第二聚乙烯膜复合无纺布层、胶粘带封口层和整形带。
6.所述燃气管道连接件自其外圆侧依次包覆有树脂绝缘纤维层、第一聚乙烯膜复合无纺布层、第二聚乙烯膜复合无纺布层、胶粘带封口层和整形带。
7.所述燃气管道连接件自其外圆侧依次包覆有树脂绝缘纤维层、第一聚乙烯膜复合无纺布层、树脂碳纤维布层、第二聚乙烯膜复合无纺布层、胶粘带封口层和整形带。
8.所述第一聚乙烯膜复合无纺布层和第二聚乙烯膜复合无纺布层的层数分别为1-3层。
9.所述第一聚乙烯膜复合无纺布层和第二聚乙烯膜复合无纺布层的对口呈90
°‑
180
°
错位设置。
10.所述整形带采用开口pp阻燃波纹管、开口pe理线管或整形带的一种或多种组合使用。
11.所述整形带与胶粘带封口层之间设有防老化涂料层。
12.有益效果:与现有技术相比,本实用新型的燃气管道连接件包括弯头、三通、四通和引入管处部位的燃气管的变向连接件。燃气管道连接处的连接件采用具有绝缘特性的聚乙烯膜复合无纺布作为加固防腐层既可以保证燃气管道连接处腐蚀部位的良好防腐补强性能,又能避免电火花检测时末端出现误报信号。在聚乙烯膜复合无纺布层之间增加树脂碳纤维布层是的防腐结构强度得以加强,与现有技术的仿佛结构相比,其抗压强度又大大提高,可用于高中低压所有管网连接处的加固防腐,使用寿命可大于20年。
附图说明
13.图1是本实用新型结构示意图;
14.图2是实施例1的结构示意图;
15.图3是实施例2的结构示意图;
16.图4是实施例3的结构示意图;
17.图5是弯头整形带后的效果图。
18.图中:1、燃气管道连接件,2、第一聚乙烯膜复合无纺布层,3、第二聚乙烯膜复合无纺布层,4、胶粘带封口层,5、整形带,6、树脂碳纤维布层,7、树脂绝缘纤维层,8、对口位置,9、防老化涂料层,10、开口pe理线管,11、整形带。
具体实施方式
19.以下结合较佳实施例,对依据本实用新型提供的具体实施方式详述如下:详见附图1,本实施例提供了一种燃气输送管道连接处的加固防腐绝缘层结构,包括,包括燃气管道连接件1,所述燃气管道连接件自其外圆侧依次设有第一聚乙烯膜复合无纺布层2、第二聚乙烯膜复合无纺布层3、胶粘带封口层4和整形带5,所述第一聚乙烯膜复合无纺布层及第二聚乙烯膜复合无纺布层缠绕燃气管道连接件呈对口位置式连接,沿对口位置处纵向设有若干固接封口点,固接后的第二聚乙烯膜复合无纺布层包覆胶粘带封口层,胶粘带封口层通过整形带整形加固。
20.本实施例的优选方案是,所述第一聚乙烯膜复合无纺布层和第二聚乙烯膜复合无纺布层的层数分别为1-3层。本实施例第一聚乙烯膜复合无纺布层和第二聚乙烯膜复合无
纺布层的层数分别选为一层。
21.本实施例的优选方案是,所述第一聚乙烯膜复合无纺布层和第二聚乙烯膜复合无纺布层的对口位置8呈90
°‑
180
°
错位设置。本实施例为180
°
错位设置。
22.本实施例的优选方案是,所述整形带采用开口pp阻燃波纹管、开口pe理线管或整形带的一种或多种组合使用。
23.本实施例的优选方案是,所述整形带与胶粘带封口层之间设有防老化涂料层9。本实施例采用仅在弯管的整形带外侧上表面涂覆防老化涂料层,其下方接近地面处可以不涂覆。
24.实施例1
25.详见附图2,所述第一聚乙烯膜复合无纺布层和第二聚乙烯膜复合无纺布层之间设有1-3层树脂碳纤维布层6。
26.在燃气输送管连接处直接包裹一层第一聚乙烯膜复合无纺布层,再包裹1-3层树脂碳纤维布层,树脂碳纤维布层外层再包裹一层第二聚乙烯膜复合无纺布层,层间接口错开大于90
°
小于180
°
,再用胶粘带封口缠裹密封,燃气管弯头至地下水平管处包覆开口pp阻燃波纹管,末端用2-3根整形带扎紧密封,连续注入调配好的树脂胶液固化后,外侧刷防老化涂料8。使用寿命大于15年,可用于高中低压燃气管网加固防腐。
27.实施例2
28.详见附图3,所述燃气管道连接件自其外圆侧依次包覆有树脂绝缘纤维层、第一聚乙烯膜复合无纺布层、第二聚乙烯膜复合无纺布层、胶粘带封口层和整形带。
29.燃气输送管连接处包裹1-3层树脂绝缘纤维层,再依次包裹第一聚乙烯膜复合无纺布层、第二聚乙烯膜复合无纺布层,第一聚乙烯膜复合无纺布层及第二聚乙烯膜复合无纺布层的对口错位置开大于90
°
小于180
°
,外侧用胶胶粘带封口缠裹,燃气管弯头至地下水平管处扎上开口pe理线管10,末端用2-3根整形带11扎紧密封,连续注入调配好的树脂胶液固化后,外侧刷防老化涂料层。使用寿命大于15年,可用于高中低压燃气管网加固防腐。
30.实施例3
31.详见附图4,所述燃气管道连接件自其外圆侧依次包覆有树脂绝缘纤维层、第一聚乙烯膜复合无纺布层、树脂碳纤维布层、第二聚乙烯膜复合无纺布层、胶粘带封口层和整形带。
32.燃气输送管连接处包覆树脂绝缘纤维布1-3层,再包裹一层第一聚乙烯膜复合无纺布层,对口接后在外层再缠裹1-3层树脂碳纤维布层,由于中间有树脂绝缘纤维层、第一聚乙烯膜复合无纺布层隔离绝缘,电火花测量时就不会误报。同时树脂碳纤维布层放到结构层中间使加固防腐结构强度有很大的提高,树脂碳纤维布层外面再包覆1层第二聚乙烯膜复合无纺布层,对口位置与第一第一聚乙烯膜复合无纺布层错开180
°
,再用胶带粘接密封,末端用2-3根整形带扎紧,注入树脂胶液固化后外面刷防老化涂料。
33.详见附图5,施工中由于弯头处复膜无纺布有很大的褶皱,现有技术用整形带限制褶皱注胶后褶皱会被胶液顶起,无法限制弯头处胶液的厚度,改进后的方案,是注胶前弯头处扎上连体整形带,整形带可以限制胶液厚度使其均匀;或者,在弯头处卡上开口pp阻燃波纹管,再用整形带限制其外侧,让弯头处胶液均匀;或者,是注胶前弯头处扎上开口pe理线管,再用整形带限制其外侧。由连体整形带,整形带加开口波纹管和整形带加pe理线管结合
单根整形带组合成的连体整形带,使其结构层均匀,提高了弯头处抗压耐腐蚀能力。
34.实施例的第一聚乙烯膜复合无纺布层及第二聚乙烯膜复合无纺布层的规格采用300g/m
2-600g/m2。聚乙烯膜复合无纺布层也可以采用聚丙膜复合无纺布层。
35.上述参照实施例对该一种燃气输送管道连接处的加固防腐绝缘层结构的详细描述,是说明性的而不是限定性的,可按照所限定范围列举出若干个实施例,因此在不脱离本实用新型总体构思下的变化和修改,应属本实用新型的保护范围之内。