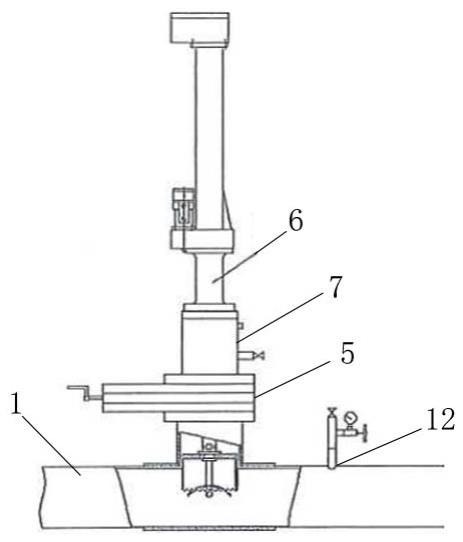
1.本发明涉及油气管道封堵技术领域,具体而言,涉及一种气囊隔离油气管道封堵抢修施工方法。
背景技术:2.在机场供油工程项目中,有时候需将管道迁改以防止新建导流坪在飞机输油管道上,为不影响飞行任务,通常要求在较短时间内完工,管道迁改施工难度大、要求高、时间紧。
3.公开号为cn105987253a的中国发明专利公开了一种油气管道封堵方法,是在维修改造管段两侧的管道上通过封堵三通安装封堵夹板阀,在封堵夹板阀远离维修改造管段侧的管道上通过旁通三通安装压力平衡阀,在封堵夹板阀上组装封堵接合器和封堵器;在两封堵三通之间的管道上设压力平衡短节,联接压力平衡管路,通过开孔机在旁通三通的管道上开旁通孔、封堵孔;架设旁通管道,通过旁通管道导通两旁通三通;通过封堵器对管道进行封堵,并通过压力平衡短节放空;对封堵改造管段维修改造后解除封堵,拆除旁通管道。
4.上述管道封堵方法中没有公开如何快速降低管道中油气含量的措施,存在安全风险大的问题。
技术实现要素:5.本发明要解决的技术问题是提供一种气囊隔离油气管道封堵抢修施工方法,以提高施工效率及施工过程的安全性。
6.为解决以上技术问题,本发明采用的技术方案是:一种气囊隔离油气管道封堵抢修施工方法,包括步骤:步骤一,确定待改线管道的封堵段,所述封堵段上游和下游的两端为封堵部位,封堵部位内侧为断管部位,在封堵部位上各安装一个抱管三通,抱管三通顶部安装夹板阀;步骤二,将开孔设备安装到夹板阀上,在封堵部位开孔;然后对封堵段进行气密性试验及氮气置换;步骤三,将封堵设备安装在夹板阀上,对封堵段两端进行封堵,先封堵下游后封堵上游;步骤四,封堵完成后,对封堵段内进行抽油施工;步骤五,采用切管器对断管部位进行机械断管,断管作业后在封堵段的封堵部位与断管部位之间填入气囊,将气囊充气到与管道内表面结合充分为止;在断管部位的管道口放置干冰,干冰挥发使管口油气氧含量低于2%;步骤六,新旧管道对口焊接,拆卸封堵设备,安装塞柄塞堵;然后拆除夹板阀,在抱管三通顶部盖盲板。
7.进一步地,在待改线管路的两个封堵位置底部分别开挖封堵作业基坑,在断管部
位底部开挖新旧管道连头作业区。
8.进一步地,封堵作业基坑与新旧管道连头作业区之间有安全隔墙。
9.进一步地,步骤二中,在封堵部位开孔时,先将氮气瓶与开孔设备的开孔结合器的打压接头进行连接,打开打压阀对封堵段内进行严密性试验,试验压力控制在管线运行压力之上,通过向各连接面喷洒肥皂水观察是否有气泡产生进行判断是否有泄漏,若有泄漏,查找原因进行解决,直至无泄漏开始开孔作业;然后向开孔结合器内充入氮气,并在开孔结合器排气阀门处进行氧含量检测,在开孔结合器内氧含量低于2%后,确认开孔结合器内氮气置换完成。
10.进一步地,步骤三中,封堵设备安装完成后进行整体严密性试验,试验压力为管道运行压力,确认各连接部位无渗漏;封堵段管壁上设置有两个平衡孔,利用平衡孔平衡压力。
11.进一步地,步骤四中,抽油施工时,首先将抽油胶管与封堵段管道底部的排油阀连接好,连接抽油胶管与油罐车,开启排油阀,利用另一个平衡孔作为排油进气孔,将余油排入油罐车。
12.本发明采用气囊和干冰用于隔离油气,控制施工过程中的油气氧浓度,将油气氧浓度降到2%以下的时间大幅缩短,提高了施工效率并保证了施工过程的安全性。
13.施工过程中,管道切割采用机械切割,减少了管道切割火花的发生,降低了安全风险。
14.本发明所述施工方法特别适用于航油管道抢修改迁施工。采用本方法施工,可明显减少航油管道或类似管道迁改施工的时间,有效解决了类似施工情况下油气浓度高、安全性低难题,提高了带油管线施工的效率及质量,有效降低施工安全风险,并整体节约了施工成本。
附图说明
15.此处的附图用来提供对本发明的进一步说明,构成本技术的一部分,本发明的示意性实施例及其说明用来解释本发明,并不构成对本发明的不当限定。
16.图1是管线开孔示意图;图2是管线封堵示意图;图3是管线封堵段抽油示意图;图4是气囊及干冰设置的位置示意图。
17.图中,1-旧油管管线,2-新油管管线,3-封堵部位,4-断管部位,5-夹板阀,6-开孔机,7-开孔结合器,8-封堵接合器,9-封堵器,10-气囊,11-干冰,12-平衡孔,13-排油阀,14-油罐车。
具体实施方式
18.为了使本领域技术人员更好的理解本发明,以下结合参考附图并结合实施例对本发明作进一步清楚、完整的说明。需要说明的是,在不冲突的情况下,本技术中的实施方式及实施例中的特征可以相互组合。
19.本发明一种典型的实施方式提供的气囊隔离油气管道封堵抢修施工方法,包括步
骤:步骤一,确定待改线管道的封堵段,所述封堵段上游和下游的两端为封堵部位3,封堵部位3内侧为断管部位4,在封堵部位3上各安装一个抱管三通,抱管三通顶部安装夹板阀5。
20.依据确定的施工工艺对旧油管管线1进行表面处理,确定封堵、开孔部位,并测量管线的椭圆度及管线壁厚,其中,开孔封堵部位的管道圆度误差不得超过管外径的1%,开孔选择的位置应避开管道焊缝。剥离封堵、开孔部位的管线防腐层,并清除焊接处的表面油污、杂质,然后安装密封垫片、夹板阀5。
21.在待改线管路的两个封堵位置3底部分别开挖封堵作业基坑,在断管部位4底部开挖新旧管道连头作业区。封堵作业基坑与新旧管道连头作业区之间有安全隔墙。
22.步骤二,将开孔设备安装到夹板阀上,在封堵部位开孔;然后对封堵段进行气密性试验及氮气置换。
23.上述开孔设备包括开孔机6和开孔结合器7,将氮气瓶与开孔结合器7上的打压接头进行连接,打开阀门对开孔设备密封腔进行严密性试验。由于管线内介质含有可燃气体需要进行氮气置换,向开孔结合器7内冲入氮气,并在开孔结合器7的排气阀门处进行氧含量检测,在开孔结合器7内氧含量低于2%后,确认结合器内氮气置换完成。
24.开孔作业完毕后,将筒刀及切下来的切板收回至开孔结合器7内,关闭阀门,打开开孔结合器7上的排气球阀进行泄压,介质排放。
25.步骤三,将封堵设备安装在夹板阀上,对封堵段两端进行封堵,先封堵下游后封堵上游。
26.上述封堵设备包括封堵接合器8和封堵器9,将封堵接合器8及封堵器9安装在夹板阀5上并用螺栓紧固完好,安装完成后进行整体严密性试验,确认各连接部位无渗漏。
27.步骤四,封堵完成后,对封堵段内进行抽油施工;步骤五,采用切管器对断管部位进行机械断管,断管作业后在封堵段的封堵部位与断管部位之间填入气囊10,将气囊10充气到与管道内表面结合充分为止;在断管部位的管道口放置干冰11,干冰11挥发使管口油气氧含量低于2%。
28.步骤六,新旧管道对口焊接,拆卸封堵设备,安装塞柄塞堵;然后拆除夹板阀,在抱管三通顶部盖盲板。
29.下面结合一个相对具体的实施例对本发明要求保护的技术方案做进一步清楚、完整的说明。
30.(一)施工场地平整布置及作业坑开挖支护封堵作业基坑分上游和下游共2处,每处长
×
宽为8m
×
4m,其中一处挖至管线底部1米;另一处管道底部设平衡孔(也作为抽油孔),因此,管道局部需挖至管线底部1.8米。封堵作业基坑与新旧管道连头作业区之间有安全隔墙,隔墙顶部宽度大于1m。
31.封堵作业基坑与新旧管道连头作业区的边坡和底部用砂袋进行支护和基底保护,砂袋按50cm厚进行堆码。同时用钢管搭设操作平台,用于现场放置设备和操作,两端设有方便上下行走的安全通道,坑内设有降水坑,周围采取防塌方措施。
32.(二)剥离防腐层、测量椭圆度及壁厚确定封堵、开孔部位,选择的位置避开管道焊缝,无法避开时,对开孔机6的开孔刀
切削部位的焊道适量打磨,开孔刀中心钻不落在焊缝上。剥离封堵、开孔施工部位的管线防腐层,清除焊接处的表面油污及杂质。
33.用测厚仪测出原管道壁厚。测量管线的椭圆度及管线壁厚,若不满足封堵作业要求,在附近位置另外选择作业点,开孔封堵部位的管道椭圆度误差不得超过管外径的1%。
34.(三)焊接封堵抱管三通焊接抱管三通时,先同时焊接两侧直焊缝,再焊接环焊缝。对焊缝进行100%外观检查。法兰短接焊前使用水平尺找准管线中心,进行点焊固定,并将短接下半部分安装拼装到位。
35.(四)安装夹板阀在抱管三通处安装密封垫片、夹板阀5,然后将开孔设备安装到夹板阀5上。
36.(五)管线开孔、管线停输开孔时要注意开孔机6的转数,控制开孔刀在16转/min以内,液压站运行压力控制在4mpa以下,额定排量在50l/min左右。按照开孔机6转数及开孔大小计算开孔时间,钻机额定进给量m=0.1mm/转,开孔时间计算公式如下:开孔时间t=h/(转数/min
×
m)当中心钻钻尖到达管顶,记录开孔位置,按计算好的开孔行程进行开孔,直至开孔作业完成。
37.将油库输油泵关闭,管线两端阀门关闭,管线停止输油。
38.(六)平衡将氮气瓶与开孔结合器7上打压接头进行连接,打开打压阀对封堵段管线的密封空腔进行严密性试验,试验压力控制在管线运行压力之上,通过向各连接面喷洒肥皂水观察是否有气泡产生进行判断是否有泄漏,若有泄漏,查找原因进行解决,直至无泄漏开始开孔作业。
39.由于管线内介质含有可燃气体需要进行氮气置换,向开孔结合器7内冲入氮气,并在开孔结合器7的排气阀门处进行氧含量检测,在开孔结合器内氧含量低于2%后,确认开孔结合器内氮气置换完成。
40.(七) 管线封堵、封堵验证封堵段管壁上设置有两个平衡孔12,平衡孔12上安装平衡短节,利用平衡孔12平衡压力。
41.将封堵接合器8及封堵器9安装在夹板阀5上并用螺栓紧固完好,安装完成后进行整体严密性试验,试验压力为管道运行压力,确认各连接部位无渗漏,然后平衡压力,打开夹板阀5,按照测量尺寸进行封堵作业;先封堵下游,后封堵上游。
42.封堵完成后,关闭平衡管线两端阀门,卸下平衡管后,开启主管线上平衡短节处阀门,将封堵段内的压力排放,利用平衡短节上的压力表检查封堵效果。
43.封堵点如有大的渗漏,调整封堵尺寸,若依然泄漏,更换封堵头上的密封胶皮,重新进行封堵作业,直至无泄漏。
44.(八) 封堵段抽油封堵成功后,对动火区封堵段内进行抽油施工,排油量约5m3。首先将抽油胶管与管道底部排油阀13连接好,连接抽油胶管与油罐车14,缓慢开启排油阀13,待油流入排油泵
内再将排油泵开启,利用另一平衡孔12作为排油进气孔,将管内余油排入油罐车14。排油过程注意油罐车、抽油泵接地。如管线内的航煤抽不干净,可在中间管线低点部位底部再焊接dn50备用抽油孔,进行油品的回收作业。
45.(九) 机械断管采用管道不动火切割作业,断管部位要求与封堵部位最少距离2米。
46.首先安装切管器,结合新旧管线的碰头位置确定切管器的安装位置,进行切割断管作业,切割过程注意给刀片冷却降温。断管作业后在封堵段的封堵部位与断管部位之间填入气囊10,将气囊10充气到与管道内表面结合充分为止;在断管部位的管道口放置干冰11,结合干冰11挥发使管口油气氧含量低于2%。
47.(十)新旧管道对口焊接断管作业结束后,焊接前需检查封堵密封效果,确保无任何油气泄漏,焊接无风险。焊接新油管管线2时,焊缝采用断续焊(跳跃式焊接),每焊20-30mm长,停止待冷却后继续焊接,严格控制焊接层间温度。所有管道焊缝均要求进行无损检测。
48.(十一)压力平衡利用一个平衡孔连接封堵器的联箱,打开阀门进油,然后打开另一个平衡孔排气。
49.(十二)解除封堵在保证封堵头两侧压力平衡后,进行提取封堵头作业。提取封堵头时先提上游封堵头,后提下游封堵头。
50.(十三)安装塞柄、加盖盲板及防腐拆卸上述封堵设备后,安装塞柄塞堵。然后拆除夹板阀,盖盲板。
51.除去抱管三通表面油污、灰尘等杂物,然后用聚乙烯冷缠带进行防腐施工。
52.(十四) 清理现场将现场施工产生废弃物集中处理,封堵后管道按要求进行回填。
53.本发明要求保护的范围不限于以上具体实施方式,对于本领域技术人员而言,本发明可以有多种变形和更改,凡在本发明的构思与原则之内所作的任何修改、改进和等同替换都应包含在本发明的保护范围之内。