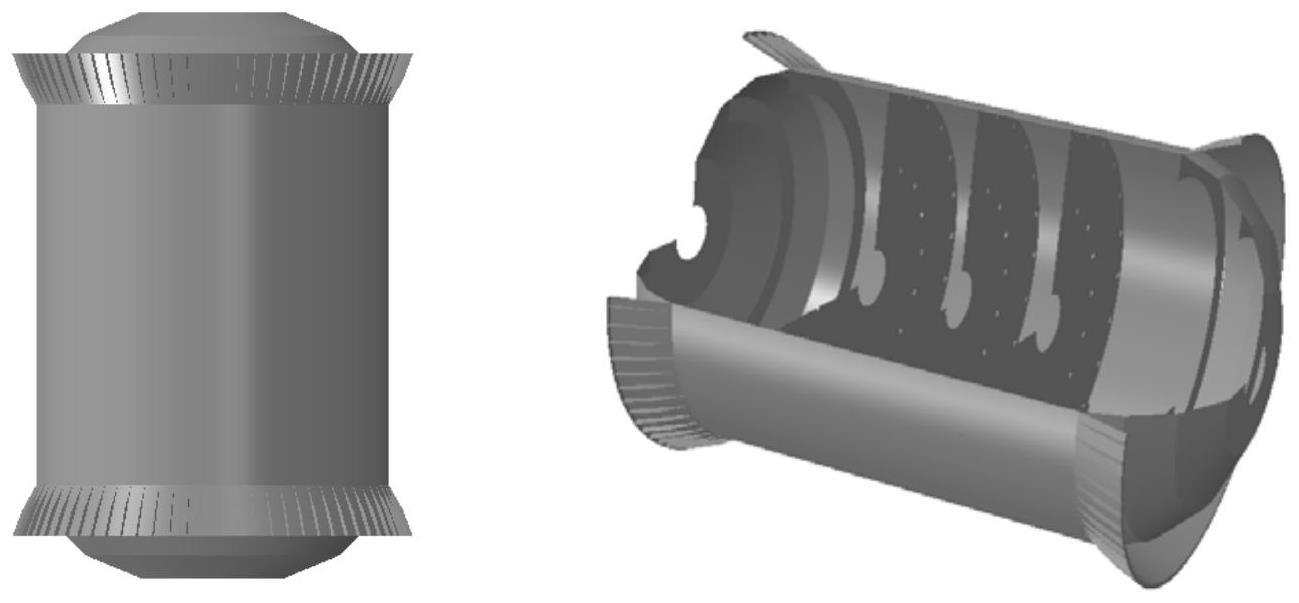
1.本发明涉及压力容器制造领域,是一种基于胀形技术制造金属压力容器的新技术,实现了低成本制造相交球壳压力容器、贮箱的工艺创新。
背景技术:2.发明申请号:202110242791.9、202210049625.1公开了两种类型的相交球壳压力容器,其结构均由若干个相交球壳组成,在相同的材料、容积和压力要求下,具有理论上与球壳压力容器相等的结构效率,两个专利的不同点在于采用圆形隔板板还是纤维缠绕环圈对球壳连接处进行径向约束。上述两项发明仅公开了压力容器的结构形式,未考虑其生产、制造方法。对采用金属材料制造该类型压力容器一般可考虑如下两种技术路线:
3.1)首先加工出各段的球壳和隔板,然后焊接到一起,存在球壳制造工艺复杂,成本高,焊缝数量多、可靠性低等缺点。
4.2)采用3d打印形式制造,存在制造成本高、薄壁结构难以实现等缺点。
5.传统的奥氏体不锈钢制圆柱形压力容器为了提高强度往往采用胀形工艺实现一定程度的冷作硬化,从而提高材料强度,降低材料用量。但由于普通的圆柱形压力容器在内压下应力不均匀,因此只能有限程度的胀形,胀形应变率一般小于10%。
6.哈尔滨工业大学王仲仁教授在1985年发明了球形压力容器的无模胀形工艺,并推广应用于椭球、圆环形压力容器的制造。由于结构内压趋球效应的影响,除了球形压力容器外,其他形式的容器普遍存在变形褶皱、最终趋近圆球等问题,限制了该技术更广泛地推广应用。
7.发明申请号:202110242791.9和202210049625.1公开的相交球壳压力容器是一种理想的等应力结构,在内压下作用下仍然为各方向等比例变形,不会出现整体趋球胀形问题,而且,结构趋近于该结构的压力容器,内压下也会向相交球壳形式变形,从而为该类型结构的制造启发了一个可行方向。
8.本发明提出首先制造一个趋近相交球壳压力容器的简单筒段结构,然后采用内压胀形工艺制造相交球壳压力容器,实现了一种简单、低成本、高可靠制造相交球壳压力容器的技术方法。
技术实现要素:9.本发明主要解决在使用简单、低成本工艺,可靠生产制造相交球壳压力容器的工艺难题。
10.本发明的有益效果是:使用低成本的材料和工艺实现了高强度相交球壳压力容器的制造。
11.基于本发明制造金属相交球壳的压力容器的步骤如下:
12.1)根据相交球壳压力容器的半径、隔板间距、球壳厚度,考虑材料许用塑性应变值,计算胀形前圆柱形容器的直径、隔板间距和板材厚度或者纤维环圈横截面积;计算方法
见本发明的权利要求部分。
13.2)使用金属板材下料焊接制造圆柱形容器,对于有含隔板的结构,如果容器直径较大可以采用整体圆管制作筒段,在其内部焊接隔板,如果直径较小则分段焊接,并且两个筒段夹持一个隔板,以外部“t”形双面焊缝焊接到一起;
14.3)对于纤维缠绕的压力容器结构,预制出经固化的若干个纤维环圈;
15.4)使用充内压胀形方式完成容器制作。对于奥氏体不锈钢材料,可以选用液氮温度深冷胀形,提高压力容器的低温强度。对于存在焊接退火现象的材料,应避免在胀形后焊接作业。
16.5)为减小焊缝区域的不均匀内应力,可以采用“预胀形-退火-二次胀形”分三步甚至更多步进行胀形。
附图说明
17.图1含隔板的相交球壳压力容器胀形前焊接件及其内部图;
18.图2含隔板的相交球壳压力容器胀形后成品;
19.图3含隔板的相交球壳压力容器胀形前焊接件剖面示意图;
20.图4纤维缠绕相交球壳压力容器胀形前焊接件;
21.图5胀形前纤维缠绕相交球壳压力容器焊接件与纤维环圈;
22.图6胀形后纤维缠绕相交球壳压力容器成品。
23.附图中各部件的标记如下:
24.①
圆柱壳段
25.②
分段锥形底
26.③
隔板
27.④
短壳
28.⑤
工艺人孔
29.⑥
防晃板
30.⑦
胀形前金属壳体
31.⑧
纤维缠绕环圈
具体实施方式
32.下面结合附图对本发明的较佳实施例进行详细阐述,以使本发明的优点和特征能更易于被本领域技术人员理解,从而对本发明的保护范围做出更为清楚明确的界定。
33.本发明实施例包括:
34.实施例1:一种用于运载火箭的薄壁大直径贮箱结构制造方法,制造工艺如下:
35.1)本实施例贮箱直径3.35m,容积40m3,设计内压0.5mpa,使用材料为奥氏体304不锈钢,要求最高承载压力不低于设计内压的1.5倍;
36.2)本实施例胀形后结构由4个直径约3.35m的球壳相交组成,球壳之间以及球壳与隔板之间采用焊接连接,球心间距为半径的50%,容积为40.2m3;
37.3)最大胀形应变率s取21%,则胀形前参数为:圆柱直径d=3.35/sqrt(1+21%)=3.024m,球心距为半径的50%,即0.756m,锥段与圆柱焊缝到相邻隔板距离取0.85m,近球底
截面为正16边形;
38.4)贮箱包含3个隔板,胀形前筒段总长度为2.748m;
39.5)胀形前隔板、前底和后底中心设置直径500mm工艺人孔,隔板上另外设两圈直径50mm的小孔;
40.6)各个隔板采用焊接形式与筒段壁板连接;
41.7)为了与其他结构连接方便,本实施例中设计了前后短壳结构;
42.8)胀形前圆柱壳体厚度约为1.2mm,隔板厚度0.6mm,隔板中心直径500mm圆孔周围设置宽度70mm、厚度2mm加厚区,隔板上直径50mm小孔周围设置宽度8mm、厚度2mm加厚区;
43.9)近球形底中部到圆柱与近球形底焊缝的轴向距离约500mm位置设置防晃环板,宽度200mm、厚度0.6mm,胀形前结构如附图1所示;
44.10)首先胀形内压充至0.5mpa,前后底已经涨圆,然后进行退火处理,消除焊缝内应力,然后二次胀形至0.80mpa;
45.11)在内压0.80mpa左右结构胀形到直径3.35m,长度为5.45m,胀形后结构如附图2所示;
46.12)胀形后得到的薄壁大直径相交球壳贮箱容积为40.2m3,贮箱重量约800kg;
47.从本实施例可以看出,采用本发明技术制造的贮箱重量轻,强度高,材料成本低,工艺简单,大大降低了制造成本。
48.实施例2:一种纤维缠绕相交球壳压力容器,制造工艺如下:
49.1)本实施例贮箱直径0.6m,总长2.5m,设计压力13.5mpa。
50.2)首先焊接一个等壁厚,总长略小于2.5米的不锈钢筒段,如附图4所示。
51.3)加工若干个碳纤维复合材料环圈,等间距套在筒段上,如附图5所示。
52.4)高压胀形至设计压力,金属进入塑性,得到复合材料缠绕相交球壳压力容器,如图6所示。
53.以上所述仅为本发明的实施例,并非因此限制本发明的专利范围,凡是利用本发明说明书及附图内容所作的等效结构或等效流程变换,或直接或间接运用在其他相关的技术领域,均同理包括在本发明的专利保护范围内。