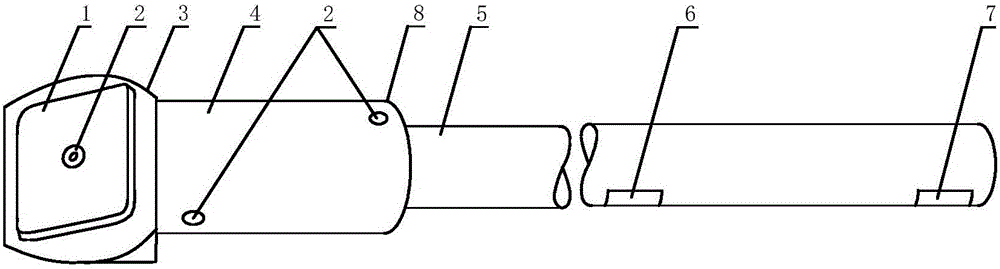
本发明涉及钢结构加工制造或船舶建造技术中的工业测量领域,具体说是一种钢结构剖面圆度评定辅助测量臂、及其标定和使用方法。
背景技术:
:为了最大能力承受深水压力或者其他外压,某些钢结构通常加工成断面轮廓为圆型的形状,如液化气罐、潜艇耐压壳体等。由于尺寸较大,这些结构通常由多块钢板辊弯成形后装焊在一起组成整体,辊弯存在误差,装焊过程也会引起结构变形,使得最终得到的结构断面偏离理论设计的纯圆形状,偏离程度通常称为径向初挠度,用来表征结构剖面圆度。因此,建造过程中必须对断面圆度进行测量、控制,建造完成后也需要对圆度进行测量,检查是否满足规范要求。大型结构圆度评定较为精准的现代测量方法是:采用激光全站仪测量结构上空间点三维坐标,然后通过计算分析确定断面圆度。对于比较简单空旷的大型结构,可以直接测量分析,但是当大型结构内部较为复杂,比如结构遮挡、附属结构空间狭窄,导致出现隐蔽点,激光无法直射,这些情况就需要采取辅助装置。如图1所示为现有技术中比较具有代表性的结构形式,这种测量臂一端为尖点,使用时直接对着待测点,然后测量测量臂上部两个反射棱镜中心点,内部计算得到待测点坐标。这样的设计要求测量臂加工制作精度非常高,尖点必须在两个反射棱镜连成的直线上,并且使用过程中测量臂不能发生变形。这些要求也限制了测量臂的长度,也就使得它的应用范围大大缩小。技术实现要素:本发明所要解决的技术问题是提供一种钢结构剖面圆度评定辅助测量臂、及其标定和使用方法,使辅助测量臂的结构要求大幅降低,测量过程也得到大幅简化。本发明方案中的钢结构剖面圆度评定辅助测量臂,其特征在于:仅需下述结构即可满足测量要求:设有刚性直杆和连接头,所述连接头为刚性材料,固定连接于所述刚性直杆的前端,所述刚性直杆的前端部为磁连接部,磁连接部的前端面固定连接有磁性材料,所述磁性材料的外端面主体为一平面,磁性材料的外端面与磁连接部的前端面平齐或凸出于磁连接部的前端面。典型地,所述连接头为铝合金接头,所述刚性直杆为碳纤维杆。优选地,所述磁性材料的外端面与刚性直杆的夹角为0~180°,典型地为90°、30°或60°。优选地,所述磁性材料与所述磁连接部之间通过螺钉和粘合剂连接,所述连接头与所述刚性直杆之间通过螺钉和粘合剂连接。在所述刚性直杆的一侧可拆卸地固定设有第一反射片和第二反射片,第一反射片和第二反射片的连线与刚性直杆的轴线平行,且第一反射片和第二反射片的连线延长线与所述磁性材料的外端面相交。一种对上述的辅助测量臂的标定方法,其特征在于:按照以下的步骤操作即可得到标定的长度值结果:A、固定一带可导磁材料平面的部件,以可导磁材料平面为标定平面,采用全站仪测量标定平面上的三个以上不位于同一直线上的测量点,确定三维坐标轴的X轴、Y轴、Z轴和坐标原点,利用所测出的测量点坐标拟合出一个拟合平面;B、将辅助测量臂的磁性材料外端面吸附于标定平面上,测量辅助测量臂上第一反射片和第二反射片所代表点A1和A2的空间坐标,得到过A1和A2的直线,求取直线A1A2与拟合平面交点A0的三维空间坐标,按下式计算d1、d2:d1=(x1-x0)2+(y1-y0)2+(z1-z0)2,]]>d2=(x1-x2)2+(y1-y2)2+(z1-z2)2,]]>其中,d1、d2分别为直线段A0A1的长度和直线段A1A2的长度,x0、y0、z0分别为点A0在X轴、Y轴、Z轴上的坐标值,x1、y1、z1分别为点A1在X轴、Y轴、Z轴上的坐标值,x2、y2、z2分别为点A2在X轴、Y轴、Z轴上的坐标值。在步骤A中,以下述步骤最终确定拟合平面的空间参数:各测点在拟合平面上的投影点坐标为(xi,yi,zi),(1).利用最小二乘法或特征值法计算得到拟合平面方程Ax+By+Cz=D拟合平面参数A、B、C、D的初始值为A0、B0、C0、D0;各测量点的坐标投影到拟合平面上,以公式x=A(D-Byi-Czi)+(1-A2)xiy=B(D-Axi-Czi)+(1-B2)yiz=C(D-Axi-Byi)+(1-C2)zi,]]>得到各测点在拟合平面上的投影点坐标(x,y,z);(2).利用计算出的A0、B0、C0、D0值,根据下式计算出每个测量点至拟合平面的距离di:di=|A0·xi+B0·yi+C0·zi-D0|;(3).利用下式计算距离di的标准偏差σ:σ=(di-d‾)T(di-d‾)n-1,]]>其中:字母T表示矩阵转置,n为参与计算的测点数;(4).当di≥2σ时,删除此测点,当di<2σ时,此测点保留;(5).利用所有保留下来的点计算平面参数A、B、C、D的值;(6).重复第(2)到第(5)步,直到剩下所有测点的di都满足di<2σ的条件时为止;(7).利用保留下来的点的数据计算A、B、C、D的值,得到最终的拟合平面;在步骤B中,反复测量点A1、A2的三维空间坐标,取平均值作为最终A1、A2的三维空间坐标。一种辅助测量臂的使用方法,其特征在于:按照下述步骤获得全站仪测量盲区的待测点A0坐标(x0,y0,z0):a.选取合适形状的辅助测量臂,使辅助测量臂上的第一反射片和第二反射片位于全站仪可测量位置,将辅助测量臂的磁性材料(1)外端面吸附在待测点A0位置;b.测量辅助测量臂上第一反射片所代表点A1的三维空间坐标(x1,y1,z1)和第二反射片所代表点A2的三维空间坐标(x2,y2,z2);c.以下式计算出A0点的三维空间坐标(x0,y0,z0):x0=(1+T)x1-x2y0=(1+T)y1-y2z0=(1+T)z1-z2,]]>T=d1d2,]]>其中,d1为点A0、A1之间的距离,d2为点A1、A2之间的距离。反复测量点A1的三维空间坐标和点A2的三维空间坐标,得到每次测量值计算出的待测点A0的三维空间坐标,计算各次测量计算结果的A0的三维空间坐标平均值,作为A0的三维空间坐标测量计算结果。进一步地,重复测量计算A0的三维空间坐标,得到计算出的待测点A0的三维空间坐标,删除大于两倍标准偏差测量点,将保留的A0点三维空间坐标计算平均值作为A0的三维空间坐标测量计算结果。大型结构断面圆度评定一般是测量该断面上若干点的三维空间坐标,然后进行三维空间平面拟合(测量总是有误差的,因此测得的点不可能精确通过该断面),再将测点投影到该拟合平面上,最后进行最小二乘圆拟合评定圆度。对于某个点,如果处于狭小空间或者被遮挡,成为隐蔽点,就可以使用测量臂进行间接测量。由于圆度评定过程的特殊性,辅助测量臂指向的测点并不需要精确在理论测点上,只要落在理论测点附近的结构表面就行(周向偏移对圆度评估没有影响,垂直于断面方向的偏移经过投影过程也没有影响)。利用这一特殊性,我们就可以简化测量臂结构的设计,降低加工要求,延长使用寿命,提高辅助测量臂长度从而增加辅助测量臂应用范围,并且即使长期使用后测量臂发生累积变形,只要重新用全站仪本身进行简单的标定即可继续使用。本发明方案根据圆度评估过程中个别点可以为非准确理论设计点(只需是结构表面上理论设计点附件的点)这一特点,巧妙设计出一种简单结构完成辅助测量。测量过程中并不精确要求测量点为磁性材料外端面上的具体某一点,只需满足磁性材料外端面与待测物体表面重合,且第一反射片与第二反射片的连线延长线与重合面有交点,因此,大为降低了对辅助测量臂的要求,现有技术要求辅助测量臂三点一线,且重合点精确。本发明还进一步具体提出了解决这一问题的思路及辅助测量臂的标定、使用方法。本发明的辅助测量臂结构比现有的测量臂大为简化,对加工制作没有苛刻的特殊要求,只要将这些结构牢固装配在一起即可,而能够保证较高的测量精度。使用时磁铁端吸附在钢板上待测点附近,底部磁铁表面与待测结构表面重合。为了适应不同应用场合,磁连接部设计成不同坡度类型,与刚性直杆设有不同的夹角,刚性直杆也设计成不同长度,从而组合安装成不同型号的辅助测量臂。附图说明图1是传统辅助测量臂示意图,图2是本发明中辅助测量臂实施例结构示意图,图3是坐标测量示意图。图中:1—磁性材料,2—螺钉,3—磁连接部,4—杆连接部,5—刚性直杆,6—第一反射片,7—第二反射片,8—连接头。具体实施方式下面结合附图和实施例对本发明进一步说明:大型结构断面圆度评定一般是测量该断面上若干点的三维空间坐标,然后进行三维空间平面拟合(测量总是有误差的,因此测得的点不可能精确通过该断面),再将测点投影到该拟合平面上,最后进行最小二乘圆拟合评定圆度。对于某个点,如果处于狭小空间或者被遮挡,成为隐蔽点,就可以使用测量臂进行间接测量。由于圆度评定过程的特殊性,辅助测量臂指向的测点并不需要精确在理论测点上,只要落在理论测点附近的结构表面就行(周向偏移对圆度评估没有影响,垂直于断面方向的偏移经过投影过程也没有影响)。利用这一特殊性,我们就可以简化测量臂结构的设计,降低加工要求,延长使用寿命,提高辅助测量臂长度从而增加辅助测量臂应用范围,并且即使长期使用后测量臂发生累积变形,只要重新用全站仪本身进行简单的标定即可继续使用。如图2中所示钢结构剖面圆度评定辅助测量臂,设有刚性直杆5和连接头8,典型地,所述连接头使用铝合金接头,所述刚性直杆为碳纤维杆。所述连接头8固定套接于所述刚性直杆5的前端,所述刚性直杆5的前端部为磁连接部3,磁连接部3的前端面固定连接有磁性材料1,所述磁性材料1与所述磁连接部3之间的连接方式通过螺钉2和粘合剂连接,所述连接头8与所述刚性直杆5之间的连接方式通过螺钉2和粘合剂连接。所述磁性材料1的外端面主体为一平面,磁性材料1的外端面与磁连接部3的前端面平齐或凸出于磁连接部3的前端面。所述磁性材料1的外端面与刚性直杆5的夹角为0~180°,典型地,磁性材料1的外端面与刚性直杆5轴线之间的夹角为90°、30°或60°。在所述刚性直杆5的一侧粘贴第一反射片6和第二反射片7,第一反射片6和第二反射片7的连线与刚性直杆5的轴线平行,且第一反射片6和第二反射片7的连线延长线与所述磁性材料1的外端面相交。所述磁性材料1的外端面可以直接吸附于钢制结构的表面,当待测点被遮挡而难以通过全站仪测量时,可以通过适当角度型号的辅助测量臂,将第一反射片6和第二反射片7伸出到可测量位置,通过对第一反射片6和第二反射片7的测量得到待测点的坐标。由此进行大型钢结构的圆度评定。如图2中所示的本发明方案,结构较为简单,对加工制作没有苛刻的特殊要求,只要将这些结构牢固装配在一起即可,能够保证较高的测量精度。使用时磁铁端吸附在钢板上待测点附近,底部磁铁表面与待测结构表面重合。为了适应不同应用场合,铝合金结构设计成不同坡度类型,碳纤维杆也设计成不同长度,从而组合安装成不同型号的辅助测量臂。辅助测量臂组装完成后需要进行标定,然后才能用于测量。对上述的辅助测量臂的标定方法,可按照以下的步骤操作即可得到标定的长度值结果:A、固定一平面钢制,以设定钢制部件的表面平面为标定平面,采用全站仪测量标定平面上的多个不位于同一直线上的测量点,确定三维坐标轴的X轴、Y轴、Z轴和坐标原点,利用所测出的测量点坐标拟合出一个拟合平面。以下述步骤最终确定拟合平面的空间参数:各测点在拟合平面上的投影点坐标为(xi,yi,zi),拟合平面方程为:Ax+By+Cz=D(1)利用最小二乘法、特征值法计算得到平面参数为A0、B0、C0、D0的初始值;(2)利用计算出的A0、B0、C0、D0值,由下式计算出每个测点至拟合平面的距离di:di=|A0·xi+B0·yi+C0·zi-D0|;(3)计算距离di的标准偏差σ=(di-d‾)T(di-d‾)n-1;]]>其中:字母T表示矩阵转置,n为参与计算的测点数。(4)当di≥2σ时,此测点被认为是异常点,则删除;当di<2σ时,此测点被认为是正常点,则保留;(5)利用所有保留下来的点重新计算平面参数A、B、C、D的值;(6)重复第(2)到第(5)步,直到剩下所有测点的di都满足di<2σ的条件时为止;(7)计算最佳的A、B、C、D值,即得到最佳的平面拟合方程(Ax+By+Cz=D)。B、将辅助测量臂的磁性材料1外端面吸附于标定平面上,测量辅助测量臂上第一反射片6和第二反射片7所代表点A1和A2的空间坐标,得到过A1和A2的直线,求取直线A1A2与拟合平面交点A0的三维空间坐标,按下式计算d1、d2:d1=(x1-x0)2+(y1-y0)2+(z1-z0)2,]]>d2=(x1-x2)2+(y1-y2)2+(z1-z2)2,]]>其中,d1、d2分别为直线段A0A1的长度和直线段A1A2的长度,x0、y0、z0分别为点A0在X轴、Y轴、Z轴上的坐标值,x1、y1、z1分别为点A1在X轴、Y轴、Z轴上的坐标值,x2、y2、z2分别为点A2在X轴、Y轴、Z轴上的坐标值。反复测量点A1、A2的三维空间坐标,取平均值作为最终A1、A2的三维空间坐标。某个待测点所处的位置位于全站仪的测量盲区,先选取合适型号的辅助测量臂,将其吸附在待测点位置,然后测量A1、A2点的三维空间坐标,软件自动反算出A0点三维空间坐标,代替理论待测点用于圆度评估。辅助测量臂的使用方法,如图3所示,按照下述步骤获得全站仪测量盲区的待测点A0坐标(x0,y0,z0):如图3,辅助测量臂上部所贴反射片点记为A1、A2,则A1、A2连成的直线必定与底部磁铁表面有一个交点,记为A0,这里并不需要确切标定A0点的具体位置,总之它在底部磁铁表面上,当磁铁吸附在结构表面时,该点也必然在结构表面上。假设某个待测点所处的位置位于全站仪的测量盲区,只需选取合适型号的辅助测量臂,将其吸附在待测点位置,测量A1、A2点的三维空间坐标,就可以反推出A0点三维空间坐标,代替理论待测点用于圆度评估。a.选取合适形状的辅助测量臂,使辅助测量臂上的第一反射片6和第二反射片7位于全站仪可测量位置,将辅助测量臂的磁性材料1外端面吸附在待测点A0位置;b.测量辅助测量臂上第一反射片6所代表点A1的三维空间坐标(x1,y1,z1)和第二反射片7所代表点A2的三维空间坐标(x2,y2,z2);c.以下式计算出A0点的三维空间坐标(x0,y0,z0):x0=(1+T)x1-x2y0=(1+T)y1-y2z0=(1+T)z1-z2,]]>T=d1d2,]]>其中,d1为点A0、A1之间的距离,d2为点A1、A2之间的距离。反复测量点A1的三维空间坐标和点A2的三维空间坐标,得到每次测量值计算出的待测点A0的三维空间坐标,为保证测量过程的正确性,系统增加测量有效性检验,计算各次测量计算结果的A0的三维空间坐标平均值,作为A0的三维空间坐标测量计算结果。当前第1页1 2 3