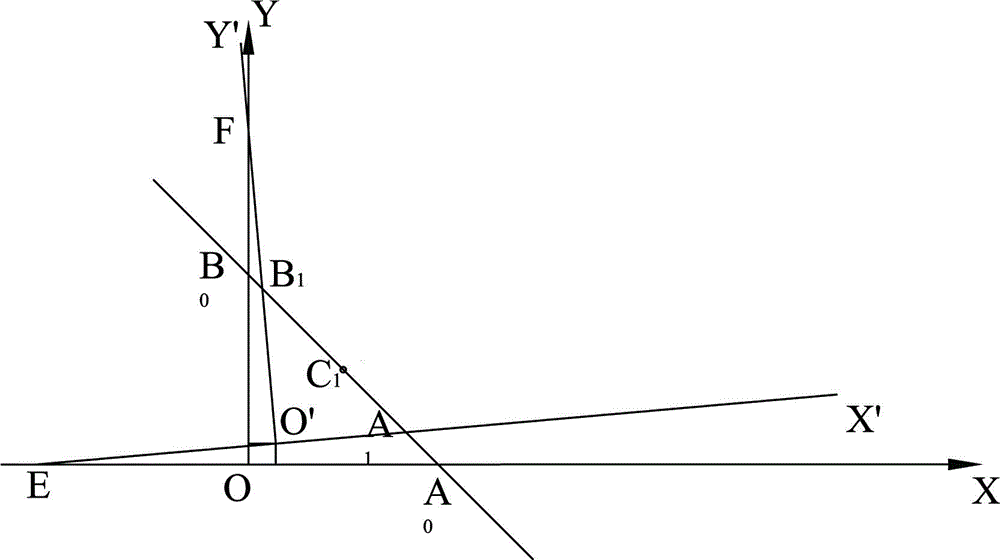
本发明属于工业测量领域,尤其涉及一种矩形工件位置和角度测量方法,适用于大尺寸矩形工件的位置和角度的非接触式测量。
背景技术:
:在机床切割领域,对大尺寸的薄钢板进行激光切割时,必须要对放置到切割平台上的工件进行定位,使工件相对于机床及激光切割头处于正确的位置,特别是工件的边部要被利用为成品零件的边部时,对工件的定位精度要求较高,否则会导致切割零件尺寸误差。工件定位传统的方法是利用机械夹具对工件进行装夹,配合百分表、划线法进行找正调整,方能使工件的定位基准面分别与机床的工作台面和工作台的进给方向x、y保持平行。这种方法需要较长的调整时间,效率低下,不适用于快速在线作业。另一种方法是,利用机械挡块来限定工件位置,用拍打机构使工件和挡块压靠对齐。这种方法需要对挡块的位置进行标定,一旦机床的工件坐标原点变化,就要重新调整挡块位置,重新进行标定。而且在长期拍打下,挡块的松动也会带来工件定位误差。因此,一套可以在线自动测量工件摆放的实际位置和角度,并传输到计算机系统进行工件坐标系自动修正的系统,对于现代化高速高精度生产是必不可少的。比较常见的做法是采用CCD相机和图像处理技术来测量,如中国专利CN200410015617.7提出了一种工件定位光电测控系统,包括计算机系统,图像信号摄取装置,该图像信号摄取装置分别摄取标准工件与待加工工件的位置图像信号,并传输到计算机系统中,将待加工工件的位置图像信号与标准工件的位置图像信号比较产生误差值,计算机系统根据该误差值控制伺服电机移动待加工工件达到预定位置。这种方法测量灵活、范围较大、测量过程快捷,具有很多优点,而且随着高分辨率高性能CCD相机的出现和计算机图像处理技术的发展,测量精度也在逐步提升。 但缺点是,测量精度易受光照等条件的干扰,需要有相机和光源的安装条件,系统结构较为复杂,成本也较高。本发明针对这种情况,提出一种安装简便、测量迅速,且安装、维护要求较低的测量系统和方法。技术实现要素:本发明的目的在于提供一种矩形工件位置和角度测量方法,可自动对工件位置和角度进行在线测量,并能根据测量结果自动生成误差补偿数据反馈到数控系统,调整工件坐标系后进行切割加工,以保证工件的加工尺寸精度及批量工件的尺寸一致性,大大增强数控机床的智能化程度。为达到上述目的,本发明的技术方案是:一种矩形工件位置和角度测量方法,其特征是,包括,1)采用一个二维形状测量传感器,安装在激光切割头上,激光切割头安装于三轴数控机床的Z轴,传感器随激光切割头在切割范围内X轴或Y轴方向平面移动,传感器的光线竖直向下照射在钢板的边部,光线与X轴方向成一角度θ,获取钢板边沿轮廓;在传感器安装好后,对传感器的安装位置进行标定,即传感器中心点和激光切割头的喷嘴中心点的相对位置,这样就可以通过数控机床Z轴的移动来精确控制传感器光线的照射位置;2)第一次测量将待切割的矩形片料在数控机床切割工位上放置好,控制传感器位于矩形片料角度上方,触发传感器进行第一次测量,得到矩形片料的左边沿和右边沿位置值;3)平移扫描测量矩形片料长边激光切割头携带传感器沿X轴方向平移,移动过程中以一定时间间隔或距离间隔触发多次测量,对矩形片料的长边边沿位置进行采样,同时实时记录采样时的数控机床X轴坐标位置;4)利用测量得到的矩形片料长边边沿数据样本,用二点直线法或最小二乘法拟合直线,计算矩形片料长边和X轴的偏角;5)利用步骤2)测量得到的矩形片料左右边沿位置值,与理论左右边沿位置值进行对比,推算矩形片料在X、Y轴方向的偏移量;6)将步骤4)计算得到的偏角和步骤5)得到的X、Y偏移值传输给数控机床控制系统,对数控机床的理论工件坐标系进行补偿;7)数控机床控制系统使用补偿后的工件坐标系开始激光切割加工。进一步,所述传感器的光线与X轴方向成角度θ为30~60度,优选θ为45度。在激光切割领域,待切割的片料多为规则的矩形。矩形料的工件坐标系原点一般设定在片料的角点,X、Y轴分别和构成该角点的两条直角边重合。搬运装置将矩形料放置到切割工位,实际的放置位置和角度存在偏差,尤其是在缺乏定位装置的情况下。本发明采用一个二维形状测量传感器,这种传感器通过向物体发射出具有一定宽度的激光线束,并通过CCD感应器接受反射回来的激光,来检测物体的截面轮廓形状尺寸,如高度、宽度、边沿位置、转折点位置等。本发明所述的二维形状测量传感器安装在激光切割头上,可以随激光切割头在切割范围内X或Y轴方向平面移动。传感器的光线竖直向下与X轴方向成角度θ,照射在钢板的边部,获取边沿轮廓,可以检测边沿位置,测量精度非常高。在传感器安装好后,对传感器的安装位置进行标定,即传感器中心点和激光切割头的喷嘴中心点的相对位置。这样就可以通过数控机床Z轴的移动来精确控制传感器光线的照射位置。在理想的工件摆放情况下,数控机床初始设定的工件坐标系是与矩形片料的零件坐标系重合的,即坐标系原点在矩形片料的角点,坐标系X、Y轴与矩形片料的两条直边重合。但由于搬运装置的重复定位精度等因素影响,实际摆放好的矩形片料与设定的工件坐标系成一定的偏角,并且片料的角点也偏离了设定的工件坐标系原点。本发明的目的是在线自动测量该偏角和在X、Y轴方向上的偏移量。本发明的有益效果:本发明方法测量过程简洁、快速、自动化程度高,对安装条件和环境光线的要求低,非常适合矩形工件的位置和角度的高精度测量,在加工前可协助操作者进行工件的找正,自动完成工件坐标系的设定,从而降低了对上料搬运装置的定位精度要求,简化工装夹具,节省夹具费用,缩短辅助时间,提高加工效率。在以矩形片料为加工对象的机床切割、刻字等领 域具有良好的推广应用价值。附图说明图1本发明采用二维形状测量传感器对矩形片料边部进行测量的示意图;图2为本发明在测量过程中传感器光线与测量对象的几何关系图;图3为本发明计算X、Y偏移值的几何示意图。具体实施方式下面结合具体实施例,进一步阐述本发明。应理解,这些实施例仅用于说明本发明而不用于限制本发明的范围。此外应理解,在阅读了本发明表述的内容之后,本领域技术人员可以对本发明作各种改动或修改,这些等价形式同样落于本申请所附权利要求书所限定的范围。如图1所示,矩形片料1放置在切割平台上,二维形状测量传感器的探头2安装在其上方,可以随激光切割头在切割范围内X或Y轴方向平面移动。探头2的安装使其线状光与X轴方向成一角度θ—45°。探头2发出具有一定宽度的激光照射矩形片料1的边部,其连接的传感器控制器3负责测量处理和结果输出。测量得到的轮廓图如图1所示,A、B分别表示轮廓的左边沿点和右边沿点。C为传感器的中心点。A和B相对于C的位置即为边沿点的位置值,可以从传感器中直接读取,传输到计算机系统。图2为在测量过程中,传感器光线与测量对象的几何关系图。图中,坐标系XOY为机床初始设定的工件坐标系,其X、Y轴与机床坐标系的X、Y轴平行。图中坐标系X′O′Y′为矩形片料的零件坐标系,其原点O′为矩形片料的角点,X′、Y′轴与片料的两条直边重合。在理想的工件摆放情况下,初始设定的工件坐标系XOY与零件坐标系X′O′Y′重合。但由于实际摆放中不可避免的误差,零件坐标系X′O′Y′与初始设定的工件坐标系XOY存在一定的偏差。本发明的目的就是要在线自动测量实际零件坐标系X′O′Y′相对于初始设定的工件坐标系XOY的位置关系,即坐标系偏移(Δx,Δy)和偏角δ。以便数控系统可以补偿工件坐标系,使调整后的工件坐标系与实际零件坐标系重合。结合图2,本发明实施例的自动测量过程如下:1)切割头携带传感器在测量起始位置待机。该测量起始位置由机床事先设定,其要使激光照射在钢板的角部,可以同时获得截面轮廓的左边沿和右边沿。传感器光线与X轴负方向成θ角,一般设定为45°角,实际数值要进行标定后获得。C1为该位置的传感器中心点,A0和B0分别为光线与坐标系XOY的交点。传感器光线相对于坐标系XOY的位置固定,即A0C1、B0C1为固定的已知值,分别表示为L0和R0;2)第一次测量当待切割的矩形片料在机床切割工位上放置好后,系统触发传感器对片料角部进行第一次测量,同时获取左边沿位置L1和右边沿位置R1,也就是图2中所示的A1C1、B1C1;3)平移测量切割头携带传感器沿X方向平移,移动过程中以一定时间间隔或距离间隔触发多次测量,对矩形片料的单个长边进行扫描。依次获得N组左边沿位置值Li及对应测量位置的X坐标值xi,i=1,2……,N;4)计算机系统利用测量值计算偏角δ、以及偏移Δx和Δy;5)将Δx、Δy和δ传输给数控系统,对工件坐标系进行补偿;6)数控系统开始切割加工过程。上述步骤4)中偏角δ的计算,一种最简便的方法是两点直线法,只需要取矩形片料长边上两个位置的边部测量值,连接两次测量的边沿点A1和A2而形成的直线A1A2,认为是矩形片料的长边即X′轴。可以这样判断的前提条件是矩形片料长边的平直度较好,且A1和A2之间的距离尽可能大。结合图2,在三角形ΔA1A2D中,由三角函数关系可推导,tanδ=A1DA2D=(A1C1-A2C2)sinθC1C2-(A1C1-A2C2)cosθ=(L2-L1)sinθ(x2-x1)-(L2-L1)cosθ]]>从而,δ=tan-1(L2-L1)sinθ(x2-x1)-(L2-L1)cosθ]]>式中,L1和L2分别为两次测量的传感器的左边沿位置读数,x1和x2分别为两次测量的实时数控机床X轴坐标值,θ为传感器光线相对于X轴的安装角度。进一步,如果矩形片料长边的平直度较差,两点直线法的测量误差可能较大,也可以采用多点测量、然后用最小二乘法来拟合长边,使测量结果尽可能精确。假设拟合直线表示为直线方程y=a0+a1x,式中有两个待定参数,a0代表截距,a1代表斜率。对于等精度测量所得到的N组数据(xi,yi),i=1,2……,N,xi值被认为是准确的,所有的误差只联系着yi。我们以左边沿读数L1在Y方向的投影作为Lisinθ作为直线的yi,以N次测量的实时机床坐标值为xi,计算最小二乘法拟合的直线方程的斜率:a1=N(Σi=1nxiyi)-(Σi=1nxi)(Σi=1nyi)N(Σi=1nxi2)-(Σi=1nxi)2=N(Σi=1nxiLi)-(Σi=1nxi)(Σi=1nLi)N(Σi=1nxi2)-(Σi=1nxi)2sinθ]]>根据直线斜率与倾斜角的关系得出:δ=tan-1a1接下来计算偏移Δx和Δy。结合图3的几何关系进行三角函数变换,可以如下推导,及Δy=O′Esinδ=(A1E-O′A1)sinδ=(sinθsinδA0A1-A1B1cos(θ+δ))sinδ=(C1A0-C1A1)sinθ-(A1C1+B1C1)sinδcos(θ+δ)=(L0-L1)sinθ-(L1+R1)sinδcos(θ+δ)]]>根据以上计算公式,计算机系统将计算得到的Δx、Δy和δ传输给数控机床控制系统,补偿理论工件坐标系,找正零件后进行加工作业,确保零件 的加工尺寸精度。本发明整个测量过程简洁、快速、自动化程度高,对安装条件和环境光线的要求低,降低了对上料搬运装置的定位精度要求,节省夹具费用,缩短辅助时间,提高加工效率。在以矩形片料为加工对象的机床切割、刻字等领域具有良好的推广应用价值。当前第1页1 2 3