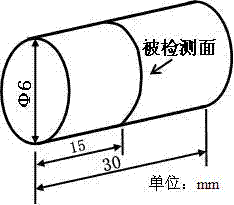
本发明涉及一种金属材料延迟裂纹敏感性评价方法,特别涉及到服役环境中含氢且吸氢后容易产生氢致延迟裂纹的金属材料及焊接接头的裂纹敏感性评价方法。
背景技术:
:长期暴露于氢环境中的设备,如输送含湿硫化氢气体的天然气输气管道、与高温高压水蒸气直接接触的核反应堆蒸气发生器及各类紧固件等,易导致材料在服役过程中吸氢脆化,产生氢致延迟裂纹。此外,焊接作为设备建造中的关键环节,焊接接头受焊接热循环影响,其热影响区的组织脆化倾向增加,同时残留不同程度的焊接应力,一旦在服役过程中吸收的扩散氢浓度超标,也会产生延迟裂纹,并且受组织脆化和残余应力的影响,焊接接头的延迟裂纹敏感性一般高于母材。因此,为安全有效地使用这类材料,在使用前对材料及其焊接接头能否发生延迟断裂进行评价和预测十分重要。现有的氢致裂纹敏感性评价方法是美国腐蚀工程师协会提出的管道压力容器抗氢致开裂钢性能评价的试验方法(nacetm0284),该方法仅评价了材料在特定的扩散氢浓度下的裂纹敏感性,对现场生产不具备直接的指导作用,并且该方法的充氢介质为硫化氢,因硫化氢是一种剧毒及易燃性气体,故对试验的安全性要求较高,且须建立独立的实验室。技术实现要素:针对现有技术存在的不足,本发明的目的在于提出一种金属材料延迟裂纹敏感性评价方法,该方法通过测定材料的临界扩散氢浓度,简便直观且有效地评价了金属材料的延迟裂纹敏感性,为使用部门选材及焊接提供依据。为实现上述发明目的,本发明采用了如下技术方案:一种金属材料延迟裂纹敏感性评价方法,其特征在于,包括以下步骤:1)电解液配制:取硫酸和蒸馏水配制不同浓度的硫酸水溶液,然后取0.5g/l硫代硫酸钠(na2s2o3)放入硫酸水溶液中,搅拌均匀,完成电解液配制过程;2)电解充氢:将各试样放入不同浓度的电解液中,接通直流电源并将试样作为阴极进行电解充氢,电解电流密度可调,充氢时间为24h;3)扩散氢浓度测试:采用热析氢法使充氢试样中的氢逸出,然后测试扩散氢浓度;4)裂纹检测:将试样垂直于长度方向或焊缝方向剖开,观察剖面是否产生裂纹;5)将试样产生裂纹的最低扩散氢浓度定为临界扩散氢浓度(hc),通过比较hc与服役中可能渗入的最大扩散氢浓度(hm),评价材料的延迟裂纹敏感性。进一步,配制电解液的硫酸水溶液的浓度为0.05-2mol/l。进一步,电解充氢时的电流密度为10-100ma/cm2。进一步,热析氢法的升温速率为80-100℃/h,将350℃以下的吸氢曲线第一峰值结束前的氢析出总量作为试样中的扩散氢浓度。进一步,用于测试扩散氢浓度的仪器对氢气的测试精度为0.1ppm,测量范围≥0.2ppm。与现有技术比较,本发明至少具有以下有益效果:本发明通过比较材料的临界扩散氢浓度与服役中可能渗入的最大扩散氢浓度的大小,简便直观且有效地评价了金属材料的延迟裂纹敏感性,对现场生产具有指导作用。附图说明图1为本发明实施例所述的金属材料延迟裂纹敏感性评价方法的流程图。图2为本发明实施例所述的钢板试验样品尺寸及裂纹检测面取样位置。图3为本发明实施例所述的焊接接头试验样品尺寸及裂纹检测面取样位置。具体实施方案下面结合实施例进一步说明本发明:实施例一本实施例评价材料为x70管线钢,板厚为12.7mm,试验样品尺寸见附图2。按附图1所示流程对该钢种进行延迟裂纹敏感性评价,具体步骤如下:取硫酸和蒸馏水配制浓度分别为0.2、0.5和1.0mol/l的硫酸水溶液,容量为1l,然后各取0.5g硫代硫酸钠(na2s2o3)放入硫酸水溶液中,搅拌均匀,完成电解液的配制。将试样放入配制好的电解液中,接通直流电源并将试样作为阴极进行电解充氢,电解电流密度分别为50、70和90ma/cm2,充氢时间为24h。根据表1所述试验参数对试样进行充氢试验。表1试验序号硫酸水溶液浓度(mol/l)电解电流密度(ma/cm2)10.25020.27030.29040.55050.57060.59071.05081.07091.090采用热析氢法使充氢试验后的试样中的氢逸出,热析氢法的升温速率为100℃/h,将350℃以下的吸氢曲线第一峰值结束前的氢析出总量作为试样中的扩散氢浓度,然后采用气相色谱仪测试扩散氢浓度。裂纹检测面取样位置见附图2,磨抛后在金相显微镜下观察是否产生裂纹。将各试样的扩散氢浓度与是否产生裂纹一一对应,得到该钢种产生裂纹的临界扩散氢浓度为5.3ppm,对比该钢种服役中可能渗入的最大扩散氢浓度,即可评价其延迟裂纹敏感性。实施例二本实施例评价材料为采用双面埋弧焊焊接的x70管线钢的焊接接头,板厚为12.7mm,试验样品尺寸见附图3。按附图1所示流程对该钢种进行延迟裂纹敏感性评价,具体步骤如下:取硫酸和蒸馏水配制浓度分别为0.1、0.4和0.8mol/l的硫酸水溶液,容量为1l,然后各取0.5g硫代硫酸钠(na2s2o3)放入硫酸水溶液中,搅拌均匀,完成电解液的配制。将试样放入配制好的电解液中,接通直流电源并将试样作为阴极进行电解充氢,电解电流密度分别为20和50ma/cm2,充氢时间为24h。根据表2所述试验参数对试样进行充氢试验。表2试验序号硫酸水溶液浓度(mol/l)电解电流密度(ma/cm2)10.12020.15030.42040.45050.82060.850采用热析氢法使充氢试验后的试样中的氢逸出,热析氢法的升温速率为90℃/h,将350℃以下的吸氢曲线第一峰值结束前的氢析出总量作为试样中的扩散氢浓度,然后采用气相色谱仪测试扩散氢浓度。裂纹检测面取样位置见附图3,磨抛后在金相显微镜下观察是否产生裂纹。将各试样的扩散氢浓度与是否产生裂纹一一对应,得到该接头产生裂纹的临界扩散氢浓度为4.5ppm,对比该焊接接头服役中可能渗入的最大扩散氢浓度,即可评价其延迟裂纹敏感性。实施例三本实施例评价材料为紧固螺栓用马氏体不锈钢0cr16ni5mo,直径为47mm,试验样品尺寸见附图2。按附图1所示流程对该钢种进行延迟裂纹敏感性评价,具体步骤如下:取硫酸和蒸馏水配制浓度分别为0.7、1.3和1.9mol/l的硫酸水溶液,容量为1l,然后各取0.5g硫代硫酸钠(na2s2o3)放入硫酸水溶液中,搅拌均匀,完成电解液的配制。将试样放入配制好的电解液中,接通直流电源并将试样作为阴极进行电解充氢,电解电流密度分别为10、30和60ma/cm2,充氢时间为24h。根据表3所述试验参数对试样进行充氢试验。表3试验序号硫酸水溶液浓度(mol/l)电解电流密度(ma/cm2)10.71020.73030.76041.31051.33061.36071.91081.93091.960采用热析氢法使充氢试验后的试样中的氢逸出,热析氢法的升温速率为80℃/h,将350℃以下的吸氢曲线第一峰值结束前的氢析出总量作为试样中的扩散氢浓度,然后采用气相色谱仪测试扩散氢浓度。裂纹检测面取样位置见附图2,磨抛后在金相显微镜下观察是否产生裂纹。将各试样的扩散氢浓度与是否产生裂纹一一对应,得到该钢种产生裂纹的临界扩散氢浓度为5.7ppm,对比该钢种服役中可能渗入的最大扩散氢浓度,即可评价其延迟裂纹敏感性。实施例四本实施例评价材料为核电压力容器用sa508-3钢,板厚为100mm,试验样品尺寸见附图2。按附图1所示流程对该钢种进行延迟裂纹敏感性评价,具体步骤如下:取硫酸和蒸馏水配制浓度分别为0.1、0.5和1.0mol/l的硫酸水溶液,容量为1l,然后各取0.5g硫代硫酸钠(na2s2o3)放入硫酸水溶液中,搅拌均匀,完成电解液的配制。将试样放入配制好的电解液中,接通直流电源并将试样作为阴极进行电解充氢,电解电流密度分别为10、30和60ma/cm2,充氢时间为24h。根据表4所述试验参数对试样进行充氢试验。表4试验序号硫酸水溶液浓度(mol/l)电解电流密度(ma/cm2)10.11020.13030.16040.51050.53060.56071.01081.03091.060采用热析氢法使充氢试验后的试样中的氢逸出,热析氢法的升温速率为100℃/h,将350℃以下的吸氢曲线第一峰值结束前的氢析出总量作为试样中的扩散氢浓度,然后采用气相色谱仪测试扩散氢浓度。裂纹检测面取样位置见附图2,磨抛后在金相显微镜下观察是否产生裂纹。将各试样的扩散氢浓度与是否产生裂纹一一对应,得到该钢种产生裂纹的临界扩散氢浓度为2.6ppm,对比该钢种服役中可能渗入的最大扩散氢浓度,即可评价其延迟裂纹敏感性。以上所述实施例仅表达了本发明的具体实施方式,但并不能因此理解为对本发明专利范围的限制。本领域的技术人员在本发明构思的启示下对本发明所做的任何变动均落在本发明的保护范围内。当前第1页12