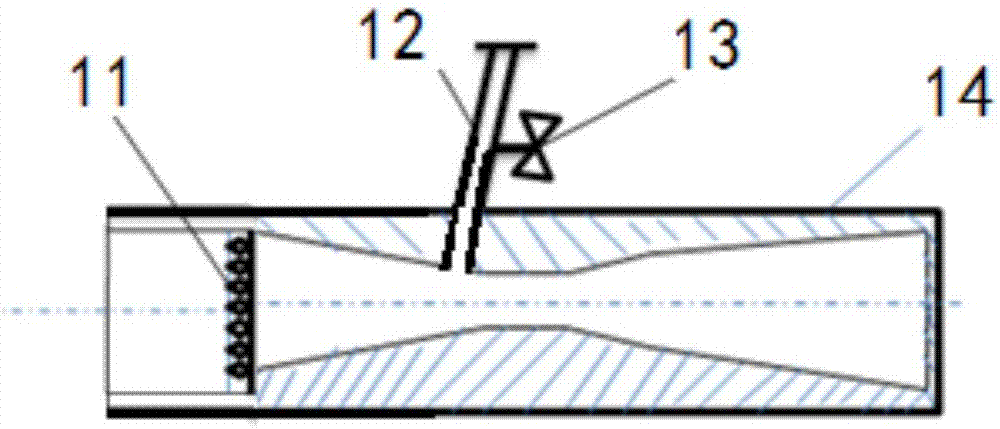
本发明涉及冲蚀磨损试验
技术领域:
,尤其涉及一种喷射式浆体冲蚀磨损试验装置及其试验方法。
背景技术:
:磨损是金属零件失效的三种主要原因(磨损、腐蚀和疲劳)之一。它所造成的经济损失是十分巨大的,如美国1981年公布的数字,每年由于磨损而造成的损失高达1000亿美元。其中材料消耗约为200亿美元,相当于材料年产量的7%。由于材料耐磨性较差,我国大量基础零件的损失寿命普遍大幅度低于国外先进产品的水平,因此直接及间接的经济损失也是十分惊人的。仅就冶金矿山、农机、煤炭、电力、和建材五个工业部门不完全的统计,每年仅由于磨料磨损而需要补充的备件就达100万吨钢材,相当于15~20亿人民币。又如机械工业每年所用的钢材,约有一半是消耗在备件的生产上,而备件中的大部分是由于磨损寿命不高而失效的,如约40%的农机具备件是由于磨料磨损消耗的,约30%的锅炉钢管是由于腐蚀磨损失效的。叶片因高速作业,在循环热应力作用下,易发生因热疲劳而引起的热龟裂、表层剥落以及叶轮轴断裂、表面磨损等。大型风机,是电站锅炉煤粉制造系统中输送煤粉的主要设备。而风机叶轮又是风机的“心脏”,风机叶轮在生产过程中受到煤粉的冲刷,造成磨损,当磨损积累到一定的程度,将严重影响风机的效率,引起风机震动,缩短风机的使用寿命,带来风机的频繁维修或更新,提高生产成本。目前修复风机叶轮的主要工艺方法有手工堆焊耐磨焊条粘贴陶瓷片和氧气、乙炔火焰喷等。这些方法,在一定程度上提高了风机的使用寿命,但也存在一些缺点,耐磨效果不太理想。热喷涂技术,特别是超音速喷涂技术,制备的涂层具有耐腐蚀、耐磨损的特性,是一种解决电力工业中大型风机叶轮耐腐蚀、耐磨损问题有效而经济的手段。风机输送含有5%~10%的煤粉的介质空气,在工作过程中,由于叶轮的转速高,煤粉颗粒易趋向于叶片的工作面,从而增大叶片的磨损(以冲蚀磨损为主),因此,不但要求风机叶轮叶片表面的涂层,具有较高的结合强度,良好的耐磨性,而且,涂层与叶片基体也具有较好的结合强度。除磨损失效外,具有涂层结构的轧辊还面临因涂层与基体结合不良而引起的剥落等失效形式。当涂层与基体存在气泡、夹渣、分层,常会在正常磨损失效之前,引发表面裂纹或表面剥落等失效。由于叶片在自身残余拉应力以及循环热应力影响下,涂层结合强度以及涂层表面成分均匀性不足引起轧辊涂层材料抗热冲击性能欠佳。有时,在实际制造轧辊过程中,涂层材料与基体结合不良时往往出现微裂纹,微裂纹在循环热应力条件下发生蔓延扩展,以致发生剥落,甚至辊身断裂。因此,涂层材料选择以及制备工艺是非常重要的影响因素。涂层材料的应用,使风机叶片的磨损修复成为一种常规选择,但涂层材料的选择和喷涂厚度以及喷涂方法的确定需要组织批量的涂层材料样品库进行检测试验,因此,针对涂层材料样品库尺寸大,涂层平整度难以控制等特点,如果设计一个冲蚀磨损试验的装置,是技术人员需要考量的技术问题。经检索,中国专利申请,公开号:cn205426702u,公开日:2018.08.03,公开了一种能够进行转动试验的摩擦磨损试验机,属于磨损试验机
技术领域:
。该实用新型的摩擦磨损试验机,包括底座、固定在底座上的驱动机构和上夹具,所述的驱动机构包括依次相连的电机、减速机和传动轴,其中,待试验的下试件为圆环形且固定安装于传动轴的输出端,所述的上夹具对应设于下试件的上方,待试验的上试件与装夹块固定相连,且装夹块固定于上夹具的卡槽内。该实用新型是在现有往复式直线运动摩擦磨损试验机的基础上进行改进得到的,能够模拟不同形式摩擦副在不同接触状态下的旋转滑动磨损过程,从而能够更好地反映沉没辊滑动轴承轴套与轴瓦之间的实际磨损工况。该实用新型只能对沉没辊摩擦磨损进行试验,对于风机叶轮来说,其耐冲蚀磨损试验更为必要。技术实现要素:1.发明要解决的技术问题针对现有技术中存在冲蚀磨损试验中涂层材料样品库尺寸大,涂层平整度难以控制的问题,本发明提供了一种喷射式浆体冲蚀磨损试验装置及其试验方法。它通过采用浆体磨料,可以有效减小环境污染,实现多组试样同步检测,能大大提升冲蚀磨损分析效率以及检测精度。2.技术方案为达到上述目的,本发明提供的技术方案为:一种喷射式浆体冲蚀磨损试验装置,包括压缩空气辅助动力机构、试样冲蚀机构以及供浆机构组成,所述压缩空气辅助动力机构包括压缩气体罐;所述试样冲蚀机构包括喷嘴和试样室;所述供浆机构包括通过管道连通的浆体罐和磨液泵;所述压缩气体罐通过气管和喷嘴相通;所述磨液泵通过磨液管和喷嘴相通;所述试样室内置试样,所述喷嘴插入试样室内,喷嘴口正对试样。本装置采用浆体磨料,采用磨液泵作为输出动力,压缩空气作为补充动力,可实现冲蚀浆体速度的大范围调控,有利于具体服役工况的模拟与检测。进一步的技术方案,喷嘴和气管、磨液管通过三通管连接在一起;所述浆体罐内置搅拌器,搅拌器上的搅拌叶片伸入至浆体罐底部,确保浆料的均匀;磨液管和喷嘴均外接压力表,显示浆体流速,再通过调节磨液泵功率可以控制浆体流速。进一步的技术方案,试样室底部通过外接回流管和浆体罐相通,浆体循环利用,避免浪费和污染环境。进一步的技术方案,喷嘴呈文丘里喷嘴结构;端口为多组喷嘴,喉管处外接压缩空气进口,尾端的浆料通道外接磨液管;压缩空气进口的进气管上外接气体压力调节阀。文丘里喷嘴结构的锥型入口具有一定集束作用,喉管设计可以加强浆料的冲蚀能力,同时也可以使其在喷嘴截面上的分布更为均匀。浆体经磨液泵抽取进入管道,在进入喷嘴前,压缩气流通过压缩空气进口进入,产生边界层的紊流扩散作用,将与磨液泵抽取的浆料发生能量及动量交换,以使混合浆料分布更为均匀。进一步的技术方案,多组喷嘴由呈阵列模式排列的若干喷嘴微孔组成,减小混合区(类似于喉管)长度,并使各微孔的喷射冲蚀保持相对一致性。一种喷射式浆体冲蚀磨损试验装置的试验方法,步骤为:a、固定试样:正冲着喷嘴固定试样;b、启动搅拌:启动搅拌器,将浆体罐内的浆料搅拌均匀;c、磨液泵和压缩气体罐启动:磨液泵将浆料从浆体罐中抽出,通过磨液管输送到喷嘴处;同时,打开压缩气体罐作为辅助动力,将浆料通过喷嘴对试样高速冲蚀。由于浆料对试样表面的冲蚀磨损主要依赖于喷嘴类型、数目、分布以及喷射距离、压缩空气和磨液泵相互作用等。充分考虑到喷射效率以及保证各喷嘴喷射不发生相互干扰,喷嘴数目以及分布可以根据内部流场数值模拟方法进行计算,喷射距离根据喷嘴尺寸以及扩散倾角加以确定。冲蚀速度可以由磨液泵运行功率以及压缩空气压力进行调节,其速率是通过测定单位时间内通过喷嘴的浆体流量,并除以喷嘴的横截面积计算而得的。试样室中,试样可以通过夹具固定在可旋转的固定板上,旋转角度可通过测角仪进行测定,旋转固定板,可以实现不同角度对试样进行冲蚀。由于喷嘴采用文丘里结构设计,后端扩散段使喷射浆体具有一定倾角,因此,试样冲蚀面积可以根据喷射距离的调整进行微调。进一步的试验方法,试样为表面修复后的风机叶片,其修复步骤为:步骤一、叶片表面预处理:a、将叶片的磨损部位进行打磨,损坏的部分用新的材料焊接好后修磨,使得各部位均达到规定要求;b、去除叶片表面的油污、锈渍、氧化皮焊渣颗粒;c、用清洁剂清洗待喷涂面;d、对所有的焊缝进行磁粉探伤处理,以确定叶片无裂纹等致命缺陷;e、叶片进行喷涂前的粗化处理,以提高涂层附着力和结合力;步骤二、喷涂前的预热:将叶片置于预热装置内进行预热处理,以消除待喷涂表面的水分和湿气,提高喷涂粒子与工件接触的界面温度,减少因工件热膨胀造成的涂层应力,提高涂层与基体的结合强度;步骤三、超音速喷涂:a、喷涂底层用nial材料打底后用钢丝刷去除打底层表面的浮灰粉;b、喷涂工作层;步骤四、封孔处理:采用刷或喷涂的方法对金属喷涂层进行封孔处理。为降低涂层孔隙,提高涂层的耐磨性、耐腐蚀性、耐冲击性,必须对金属喷涂层进行封孔处理。可以选择用空气干燥型酚醛树脂作为封孔材料,其连续工作温度在145~205℃。采用刷或喷的方法,喷涂时要用甲酮、芳香烃和无水乙醇作稀释剂进行稀释,然后在空气干燥30~60min,1~5h实现完全固化。进一步的试验方法,步骤一的e步骤中,用24#热喷涂专用金刚砂进行粗化处理;步骤二中,预热的温度控制在80~100℃;步骤三中,用nial材料打底,其厚度为0.08~0.12mm,能够消除耐磨工作层与叶片基层之间材料热膨胀系数不匹配的问题,以减小由工作层和叶片基层膨胀系数不匹配而引起的热应力,改善工作层与叶片基层间的力学匹配和物理相容性;工作层为wc-12co复合涂层,0.15~0.18mm,耐磨损、耐腐蚀性较强;或nicr-cr3c2复合涂层,0.20~0.22mm,nicr合金具有优异的耐热、耐腐蚀、抗高温氧化等性能,还起到粘结相的作用,cr3c2具有较好的高温硬度和抗高温氧化性,起硬质相的作用,在涂层中还主要起到第二相粒子弥散强化的作用,能够解决叶片在冲蚀磨损的复杂工况下极易损耗、使用寿命偏低的问题。而且,nicr-cr3c2具有与叶片相近的线膨胀系数,从而可大大降低因热冲击而造成的涂层剥落甚至失效;步骤四中,封孔材料为空气干燥型酚醛树脂,喷涂时要用甲酮、芳香烃和无水乙醇作稀释剂进行稀释;所述nial材料中,ni含量为93~97%,al含量为3~7%,al可以抑制合金层的氧化,但过高al量会带来额外的脆性,ni与al发生反应,生成金属间化合物,并释放出大量热量,使粘结底层与叶片基层表面形成微冶金结合,从而提高粘结底层与叶片基层的结合强度;所述nicr-cr3c2复合涂层中,cr3c2含量为70~80%,nicr为20~30%,这两个百分比范围的nicr粘结层与nicr-cr3c2金属陶瓷具有较好的互熔性,其中cr3c2含量多为75%,nicr为25%,后续通过耐磨性等表征方法的检测,可以证明是最佳比例;所述cr3c2的制备方法为:1)混合:将重铬酸铵粉体和纳米碳黑粉体置于蒸馏水或去离子水中,混合搅拌均匀呈流体状,加入模具中压制成型呈前驱体;压制后呈块状,以方便进行急冻;2)急冻:将前驱体快速转入急冻空间中进行急冻,急冻的目的是在尽可能短的时间里让流体冻结,重铬酸铵粉体和纳米碳黑粉体搅拌均匀后迅速定位,以防止块状流体由于密度的不同而分层,造成后续冻干处理后铬源和碳源的分布不均,而造成碳化反应不均衡的不良后果;3)冻干:将急冻好的前驱体快速转入真空冷冻干燥仓中进行冻干,冻干后的块状体只是水分子升华后形成的多微孔状蜂窝块,体积变化微小,均匀的铬源和碳源定位不会发生变化,而且,冻干过程中,重铬酸铵粉体在低温下干燥过程中发生下列反应:(nh4)2cr2o7(s)=cr2o3(s)+n2↑+4h2o(2-1);4)碳化:关闭真空冷冻干燥仓冷阱,升温进行碳化还原反应制得纳米cr3c2粉。随着温度的升高,碳逐渐将铬的高价氧化物还原成铬的低价氧化物,位置固定的碳源和其周围位置也相对固定的铬源进行反应,最终生成均匀的碳化铬,而且还是纳米级的碳化铬;由于冻干后块状体微孔孔隙的均匀性,反应中热量的吸收也比较均匀,从而实现制得粒度均匀的纳米级的碳化铬的目的;3cr2o3(s)+13c(s)=2cr3c2(s)+9co(2-2);3(nh4)2cr2o7(s)+13c(s)=2cr3c2(s)+9co+12h2o+3n2↑(2-3)(整体反应过程)。进一步的试验方法,步骤1)中,重铬酸铵和纳米碳黑粉体的配比为1:(0.17~0.21),以防止碳源或铬源过多的残留;蒸馏水或去离子水用量为:粉体总重的55%~60%,对于重铬酸铵和纳米碳黑粉体的均匀混合来说,是适宜的流体成型状态范围;步骤2)中急冻温度为-100~-140℃,时间为30~150min,以达到迅速和彻底形成块状体的效果;步骤3)中,冻干工艺曲线为:a、初期:板温0℃~100℃,升温斜率2℃/min,100℃保持30~40分钟,抽真空至60pa以内;b、中期:板温降温至80~85℃/min,保持50~60分钟,真空控制在100pa以内;c、后期,板温降温至50~65℃/min,保持80~200分钟,真空控制在80pa以内;冻干过程中,保持物料的相对低温状态,防止反应过于强烈而导致反应不均匀。步骤4)中,升温至900~1200℃进行碳化还原。进一步的试验方法,还包括步骤五:封孔后用激光器进行激光重熔工艺处理,激光功率为900~1000w,扫描速度为550~600mm/min,光斑大小10×3mm。3.有益效果采用本发明提供的技术方案,与现有技术相比,具有如下有益效果:(1)本发明的喷射式浆体冲蚀磨损试验装置,采用浆体磨料,可以有效减小环境污染,充分继承了浆体冲蚀磨损试验设备的优势,同时引入数目及位置可调的多喷嘴设计方案,可实现多组试样同步检测,将大大提升冲蚀磨损分析效率以及检测精度;同时,采用磨液泵作为输出动力,压缩空气作为补充动力,可实现冲蚀浆体速度的大范围调控,有利于具体服役工况的模拟与检测;喷嘴设计,可有效降低单喷嘴冲蚀面积小、不同步检测过程中冲蚀过程发生变化而导致的检测精度较低等难题;相对于旋臂式冲蚀磨损试验机(可实现多组试样的检测分析),多喷嘴喷射式浆体冲蚀磨损试验装置对试样要求不高,而且冲蚀速度可精准测定,冲蚀角度可调;(2)本发明的喷射式浆体冲蚀磨损试验装置,磨液泵将搅拌均匀的浆料从浆料罐中抽出,通过管道输送到喷嘴处,通过调节磨液泵功率可以控制浆体流速;压缩空气作为辅助动力,一方面可以有效引射浆体,避免高粘度浆体输运堵塞,提高其分散均匀性,另一方面可以提高并调控浆体喷射冲蚀速度;浆体从喷嘴喷射至试样表面,对试样造成冲蚀磨损,最终浆体由试样室底部管道回流至胶料罐中循环使用;(3)本发明的喷射式浆体冲蚀磨损试验装置,试样室中,试样通过夹具固定在可旋转的固定板上,旋转角度可通过测角仪进行测定,旋转固定板,可以实现不同角度对试样进行冲蚀。由于喷嘴采用文丘里结构设计,后端扩散段使喷射浆体具有一定倾角,因此,试样冲蚀面积可以根据喷射距离的调整进行微调;(4)本发明的喷射式浆体冲蚀磨损试验装置,针对喷涂涂层的试样风机叶片来说,在叶片基层喷涂nial作为金属粘结层即过渡层,能够消除耐磨耐热工作层与叶片基层之间材料热膨胀系数不匹配的问题,以减小由工作层和叶片基层膨胀系数不匹配而引起的热应力,改善工作层与叶片基层间的力学匹配和物理相容性;nicr合金还具有优异的耐热、耐腐蚀、抗高温氧化等性能,还起到粘结相的作用,cr3c2具有较好的抗冲蚀磨损性,起硬质相的作用,在涂层中还主要起到第二相粒子弥散强化的作用,能够检测叶片在高温复杂工况下极易损耗、使用寿命偏低的问题。而且,nicr-cr3c2具有与叶片相近的线膨胀系数,从而可大大降低冲蚀磨损冲击而造成的涂层剥落甚至失效;(5)本发明的喷射式浆体冲蚀磨损试验装置,试样膜层成分配比的限定,al可以抑制合金层的氧化,但过高al量会带来额外的脆性,ni与al发生反应,生成金属间化合物,并释放出大量热量,使粘结底层与叶片基层表面形成微冶金结合,从而提高粘结底层与叶片基层的结合强度,al含量为3~7%的限定兼顾了两方面的因素;而al含量6.5%的涂层,经对比试验,效果更佳;cr3c2含量为70~80%,nicr为20~30%,这两个百分比范围限定的nicr粘结层与nicr-cr3c2金属陶瓷具有较好的互熔性,其中cr3c2含量多为75%,nicr为25%,后续通过耐磨性等表征方法的检测,可以证明是最佳比例;(6)本发明的一种喷射式浆体冲蚀磨损试验装置,风机叶片涂层中,尤其是cr3c2的冻干工艺制备,冻干后的前驱块状体只是水分子升华后形成的多微孔状蜂窝块,体积变化微小,均匀的铬源和碳源定位不会发生变化,位置固定的碳源和其周围位置也相对固定的铬源进行反应,最终生成均匀的碳化铬,而且还是纳米级的碳化铬;由于冻干后块状体微孔孔隙的均匀性,反应中热量的吸收也比较均匀,从而实现制得粒度均匀的纳米级的碳化铬的目的;(7)本发明的喷射式浆体冲蚀磨损试验装置,试样组分冻干工艺的使用,使重铬酸铵和纳米碳黑粉体的配比限定范围可以根据化学反应式进行尽量精确的确定,避免了过多的杂质,能够防止碳源或铬源过多的残留而影响膜层质量;(8)本发明的喷射式浆体冲蚀磨损试验装置,cr3c2的冻干过程中,加热板温度的范围限定,能够保持物料的相对低温状态(低于加热板温),防止反应过于强烈而导致反应不均匀;(9)本发明的喷射式浆体冲蚀磨损试验装置,试样用hvof方法进行喷涂,由于多元合金涂层中的各种成分,均能够制得纳米级的粒度,因此,用hvof(超音速喷涂)方法进行喷涂,效果更加明显,制得的合金涂层附着力更强,涂层的孔隙率更小;(10)本发明的喷射式浆体冲蚀磨损试验装置,试样喷涂前处理以及喷涂中的各种工艺参数,均是发明人结合本发明制得的纳米级粉料,在进行了各种数据采集、分析、总结等创造性劳动的基础上获得,制得的涂层的强度达到80mpa以上,硬度达到1200hv以上,孔隙率1%以下,使用寿命较常规涂层提高1倍以上;而且,在硬度试验:nicr/cr3c2-20nicr涂层由界面至面层表面,显微硬度逐步升高,最高达1363.3hv;对风机叶片的持续性疲劳冲蚀磨损试验数据采集奠定了坚实的基础;(11)本发明的喷射式浆体冲蚀磨损试验装置,试样激光重熔工艺可使涂层与基材形成冶金结合,其合金层的金相组织均有细密的针状或枝状的共晶组织,提高了金属原子的亲和力,进而进一步提高了涂层与基材结合程度。附图说明图1为本发明的喷射式浆体冲蚀磨损试验装置结构示意图;图2为本发明中的喷嘴结构示意图;图3为实施例中的陈列式喷嘴放大后结构示意图。图中:1、喷嘴;2、压缩气体罐;3、试样室;4、试样;5、搅拌器;6、浆体罐;7、回流管;8、搅拌叶片;9、压力表;10、磨液泵;11、多组喷嘴;12、压缩空气进口;13、气体压力调节阀;14、浆料通道;111、喷嘴微孔。具体实施方式为进一步了解本发明的内容,结合附图对本发明作详细描述(注:如未特别注明,实施例中含量表示为重量含量)。实施例1本实施例的一种喷射式浆体冲蚀磨损试验装置,如图1所示,包括压缩空气辅助动力机构、试样冲蚀机构以及供浆机构组成,所述压缩空气辅助动力机构包括压缩气体罐2;所述试样冲蚀机构包括喷嘴1和试样室3;所述供浆机构包括通过管道连通的浆体罐6和磨液泵10;所述压缩气体罐2通过气管和喷嘴1相通;所述磨液泵10通过磨液管和喷嘴1相通;所述试样室3内置试样4,所述喷嘴1插入试样室3内,喷嘴1口正对试样4;所述浆体罐6内置搅拌器5,搅拌器5上的搅拌叶片8伸入至浆体罐6底部,确保浆料的均匀。本实施例的一种喷射式浆体冲蚀磨损试验装置的试验方法,步骤为:a、固定试样4:正冲着喷嘴1固定试样4;b、启动搅拌:启动搅拌器5,将浆体罐6内的浆料搅拌均匀;c、磨液泵和压缩气体罐启动:磨液泵10将浆料从浆体罐6中抽出,通过磨液管输送到喷嘴1处;同时,打开压缩气体罐2作为辅助动力,将浆料通过喷嘴1对试样4高速冲蚀。本装置采用浆体磨料,采用磨液泵作为输出动力,压缩空气作为补充动力,可实现冲蚀浆体速度的大范围调控,有利于具体服役工况的模拟与检测。由于浆料对试样4表面的冲蚀磨损主要依赖于喷嘴1类型、数目、分布以及喷射距离、压缩空气和磨液泵10相互作用等。充分考虑到喷射效率以及保证各喷嘴喷射不发生相互干扰,喷嘴1数目以及分布可以根据内部流场数值模拟方法进行计算,喷射距离根据喷嘴尺寸以及扩散倾角加以确定。实施例2本实施例的一种喷射式浆体冲蚀磨损试验装置,基本结构同实施例1,不同和改进之处在于:喷嘴1、气管和磨液管通过三通管连接在一起;磨液管和喷嘴1均外接压力表9,显示浆体流速,再通过调节磨液泵功率可以控制浆体流速。试样室3底部通过外接回流管7和浆体罐6相通,浆体循环利用,避免浪费和污染环境。本实施例的一种喷射式浆体冲蚀磨损试验装置的试验方法,步骤为:a、固定试样4:正冲着喷嘴1固定试样4;b、启动搅拌:启动搅拌器5,将浆体罐6内的浆料搅拌均匀;c、磨液泵和压缩气体罐启动:磨液泵10将浆料从浆体罐6中抽出,通过磨液管输送到喷嘴1处;同时,打开压缩气体罐2作为辅助动力,将浆料通过喷嘴1对试样4高速冲蚀。冲蚀速度可以由磨液泵10运行功率以及根据压力表9数据进行调节,其速率是通过测定单位时间内通过喷嘴1的浆体流量,并除以喷嘴1的横截面积计算而得的。d、浆料回流:喷往试样4的浆料滴落至试样室3后,通过回流管7滚入浆体罐6中,试样室3可以设计成收口状底部,回流管7与收口相通,方便浆体的循环式收集。实施例3本实施例的一种喷射式浆体冲蚀磨损试验装置,基本结构同实施例2,不同和改进之处在于:如图2所示,喷嘴1呈文丘里喷嘴结构;端口为多组喷嘴11,喉管处外接压缩空气进口12,尾端的浆料通道14外接磨液管;压缩空气进口12的进气管上外接气体压力调节阀13。文丘里喷嘴结构的锥型入口具有一定集束作用,喉管设计可以加强浆料的冲蚀能力,同时也可以使其在喷嘴1截面上的分布更为均匀。浆体经磨液泵10抽取进入管道,在进入喷嘴1前,压缩气流通过压缩空气进口12进入,产生边界层的紊流扩散作用,将与磨液泵10抽取的浆料发生能量及动量交换,以使混合浆料分布更为均匀。实施例4本实施例的一种喷射式浆体冲蚀磨损试验装置,基本结构同实施例3,不同和改进之处在于:多组喷嘴11由呈阵列模式排列的若干喷嘴微孔111组成,如图3所示,多组喷嘴11可以呈九宫格式,每格内陈列4个喷嘴微孔111,可以减小混合区(类似于喉管)长度,并使各微孔的喷射冲蚀保持相对一致性。试样室3中,试样4可以通过夹具固定在可旋转的固定板上,旋转角度可通过测角仪进行测定,旋转固定板,可以实现不同角度对试样进行冲蚀。由于喷嘴采用文丘里结构设计,后端扩散段使喷射浆体具有一定倾角,因此,试样冲蚀面积可以根据喷射距离的调整进行微调。本实施例的一种喷射式浆体冲蚀磨损试验装置,可以应用于表1所示的九宫格式涂层材料样品库的试验。表1九宫格式涂层材料样品库具体成分配比本实施例的一种喷射式浆体冲蚀磨损试验装置的试验方法,步骤为:a、固定试样4:将表1所示的九宫格式涂层材料样品库通过夹具固定在可旋转的固定板上,旋转角度可通过测角仪进行测定,旋转固定板,可以实现不同角度对试样进行冲蚀,调节时,使九宫格式涂层材料样品库对准九宫格式阵列模式排列的喷嘴微孔111;b、启动搅拌:启动搅拌器5,将浆体罐6内的浆料搅拌均匀;c、磨液泵和压缩气体罐启动:磨液泵10将浆料从浆体罐6中抽出,通过磨液管输送到喷嘴微孔111;同时,打开压缩气体罐2作为辅助动力,将浆料通过喷嘴微孔111对九宫格式涂层材料样品库高速冲蚀。冲蚀速度可以由磨液泵10运行功率以及根据压力表9数据进行调节,其速率是通过测定单位时间内通过喷嘴1的浆体流量,并除以喷嘴1的横截面积计算而得的。d、浆料回流:喷往试样4的浆料滴落至试样室3后,通过回流管7滚入浆体罐6中,试样室3可以设计成收口状底部,回流管7与收口相通,方便浆体的循环式收集。实施例5至实施例14共设计8个风机叶片涂层和1个沉没辊涂层,并以此用喷射式浆体冲蚀磨损试验装置进行检测。实施例5本实施例的一种喷射式浆体冲蚀磨损试验装置,基本结构同实施例4,应用于表面修复后的风机叶片试样的检测,风机叶片的修复步骤为:步骤一、叶片表面预处理:a、将叶片的磨损部位进行打磨,损坏的部分用新的材料焊接好后修磨,使得各部位均达到规定要求;b、去除叶片表面的油污、锈渍、氧化皮焊渣颗粒;c、用清洁剂清洗待喷涂面;d、对所有的焊缝进行磁粉探伤处理,以确定叶片无裂纹等致命缺陷;e、叶片进行喷涂前的粗化处理,以提高涂层附着力和结合力;步骤二、喷涂前的预热:将叶片置于预热装置内进行预热处理,以消除待喷涂表面的水分和湿气,提高喷涂粒子与工件接触的界面温度,减少因工件热膨胀造成的涂层应力,提高涂层与基体的结合强度;预热的温度可控制在100℃左右;步骤三、超音速喷涂:a、喷涂底层用nial材料打底,厚度为0.10mm左右,喷涂后用钢丝刷去除打底层表面的浮灰粉;b、喷涂工作层;工作层为wc-12co复合涂层,喷涂厚度为0.15mm,超音速喷涂工艺参数如表2:表2超音速喷涂工艺参数步骤四、封孔处理:采用刷涂的方法对金属喷涂层进行封孔处理。为降低涂层孔隙,提高涂层的耐磨性、耐腐蚀性、耐冲击性,必须对金属喷涂层进行封孔处理。可以选择用空气干燥型酚醛树脂作为封孔材料,其连续工作温度在145~205℃,以上步骤制得样品1。实施例6本实施例的风机叶片表面修复方法,基本步骤同实施例5,不同和改进之处在于:步骤一的e步骤中,用24#热喷涂专用金刚砂进行粗化处理;步骤二中,预热的温度控制在80℃左右;步骤三中,用nial材料打底,其厚度为0.08mm,能够消除耐磨工作层与叶片基层之间材料热膨胀系数不匹配的问题,以减小由工作层和叶片基层膨胀系数不匹配而引起的热应力,改善工作层与叶片基层间的力学匹配和物理相容性;工作层为wc-12co复合涂层,厚度为0.18mm;以上步骤制得样品2。实施例7本实施例的风机叶片表面修复方法,基本步骤同实施例6,不同和改进之处在于:步骤四、封孔处理:采用喷涂的方法对金属喷涂层进行封孔处理。喷涂时要用甲酮、芳香烃和无水乙醇作稀释剂进行稀释,喷涂后在空气干燥30~60min(本实施例中可以为30、40、50或60min等数值),1~5h(本实施例中可以为1、2、4或5h等数值)实现完全固化。工作层采用nicr-cr3c2复合涂层,厚度为0.20mm,nicr合金具有优异的耐热、耐腐蚀、抗高温氧化等性能,还起到粘结相的作用,cr3c2具有较好的高温硬度和抗高温氧化性,起硬质相的作用,在涂层中还主要起到第二相粒子弥散强化的作用,能够解决叶片在冲蚀磨损的复杂工况下极易损耗、使用寿命偏低的问题。而且,nicr-cr3c2具有与叶片相近的线膨胀系数,从而可大大降低因热冲击而造成的涂层剥落甚至失效。以上步骤制得样品3。实施例8本实施例的风机叶片表面修复方法,基本步骤同实施例7,不同和改进之处在于:nial喷涂层厚度为0.08mm,ni含量为93%,al含量为7%;nicr-cr3c2复合涂层厚度为0.22mm,cr3c2含量为70%,nicr为30%,这个百分比范围的nicr粘结层与nicr-cr3c2金属陶瓷具有较好的互熔性。本实施例的风机叶片表面修复方法中材料准备:nicr纳米粉,nicr-cr3c2混合纳米粉,其中,纳米cr3c2粉的制备方法为:1:混合:将重铬酸铵粉体和纳米碳黑粉体按重量比1:0.17的配比置于粉体总重55%的蒸馏水中,混合搅拌均匀呈流体状,加入方形模具中压制成型呈前驱体;压制后呈块状,以方便进行急冻;2:急冻:将前驱体快速转入-100℃急冻空间中进行急冻150min;急冻的目的是在尽可能短的时间里让流体冻结,重铬酸铵粉体和纳米碳黑粉体搅拌均匀后迅速定位,以防止块状流体由于密度的不同而分层,造成后续冻干处理后铬源和碳源的分布不均;3:冻干:将急冻好的前驱体快速转入真空冷冻干燥仓中进行冻干,板温控制在100℃以下,冻干后的块状体只是水分子升华后形成的多微孔状蜂窝块,体积变化微小,均匀的铬源和碳源定位不会发生变化,而且,冻干过程中,重铬酸铵粉体在低温下干燥过程中发生下列反应:(nh4)2cr2o7(s)=cr2o3(s)+n2↑+4h2o(2-1);4:碳化:关闭真空冷冻干燥仓冷阱,随着温度的升高,碳逐渐将铬的高价氧化物还原成铬的低价氧化物,位置固定的碳源和其周围位置也相对固定的铬源进行反应,最终生成均匀的碳化铬,而且还是纳米级的碳化铬;由于冻干后块状体微孔孔隙的均匀性,反应中热量的吸收也比较均匀,从而实现制得粒度均匀的纳米级的碳化铬的目的;3cr2o3(s)+13c(s)=2cr3c2(s)+9co(2-2)碳化反应;3(nh4)2cr2o7(s)+13c(s)=2cr3c2(s)+9co+12h2o+3n2↑(2-3)整体反应过程;本实施例一种风机叶片表面修复方法:步骤一的叶片表面预处理中,a步骤的打磨使用800#~1000#砂纸对叶片表面进行打磨;b步骤用丙酮脱脂;c步骤用无水乙醇清洗;e步骤表面粗糙度到达ra7~9。步骤二、喷涂前的预热:将叶片置于预热装置内进行预热处理,以消除待喷涂表面的水分和湿气,提高喷涂粒子与工件接触的界面温度,减少因工件热膨胀造成的涂层应力,提高涂层与基体的结合强度;预热温度可以控制在90℃左右。步骤三、超音速喷涂,工艺参数如表3:表3hvof喷涂工艺参数以上步骤制得样品4。实施例9本实施例的风机叶片表面修复方法,基本步骤同实施例8,不同和改进之处在于:nial喷涂层厚度为0.12mm,ni含量为97%,al含量为3%;nicr-cr3c2复合涂层厚度为0.20mm,cr3c2含量为75%,nicr为25%。本实施例的风机叶片表面修复方法材料准备:nicr纳米粉,nicr-cr3c2混合纳米粉,其中,纳米cr3c2粉的制备方法为:1:混合:将重铬酸铵粉体和纳米碳黑粉体按重量比1:0.21的配比置于粉体总重60%的蒸馏水中,混合搅拌均匀呈流体状,加入方形模具中压制成型呈前驱体;用2mpa压力压制后呈块状,压至厚度为3cm,以方便进行急冻;2:急冻:将前驱体快速转入-140℃急冻空间中进行急冻30min;3:冻干:将急冻好的前驱体快速转入真空冷冻干燥仓中进行冻干,冻干工艺曲线为:a、初期:板温0℃~100℃,升温斜率2℃/min,100℃保持30分钟,抽真空至60pa以内;b、中期:板温降温至80℃/min,保持60分钟,真空控制在100pa以内;c、后期,板温降温至50℃/min,保持200分钟,真空控制在80pa以内。4:碳化:关闭真空冷冻干燥仓冷阱,采用快速升温后再阶段式降温的模式,30分钟内升温至1200℃保持30分钟,10分钟内降温至1100℃再保持40分钟,10分钟内再降温至1000℃保温20分钟,10分钟内再降温至900℃保持10分钟,这种阶段式降温的优点是,保持反应的稳定性,进而可以保证碳化反应的均匀性以及实现制得粒度更加均匀的纳米级的碳化铬,经sem扫描电镜检测,颗粒尺寸大约为35-40nm之间,粒度差距较小。步骤三、超音速喷涂,工艺参数如表4:表4hvof喷涂工艺参数以上步骤制得样品5。实施例10本实施例的风机叶片表面修复方法,基本步骤同实施例9,不同和改进之处在于:nial喷涂层厚度为0.10mm,ni含量为95%,al含量为5%;nicr-cr3c2复合涂层厚度为0.21mm,cr3c2含量为80%,nicr为20%。本实施例的风机叶片表面修复方法,材料准备:nial纳米粉,nicr-cr3c2混合纳米粉,其中,纳米cr3c2粉的制备方法为:1:混合:将重铬酸铵粉体和纳米碳黑粉体按重量比1:0.19的配比置于粉体总重60%的蒸馏水中,混合搅拌均匀呈流体状,加入方形模具中压制成型呈前驱体;用1.2mpa压力压制后呈块状,压至厚度为2cm,以方便进行急冻;2:急冻:将前驱体快速转入-120℃急冻空间中进行急冻80min;3:冻干:将急冻好的前驱体快速转入真空冷冻干燥仓中进行冻干,冻干工艺曲线为:a、初期:板温0℃~100℃,升温斜率2℃/min,100℃保持40分钟,抽真空至60pa以内;b、中期:板温降温至85℃/min,保持50分钟,真空控制在100pa以内;c、后期,板温降温至55℃/min,保持120分钟,真空控制在80pa以内。4:碳化:关闭真空冷冻干燥仓冷阱,采用快速升温后再阶段式降温的模式,40分钟内升温至1200℃保持25分钟,10分钟内降温至1100℃再保持45分钟,10分钟内再降温至1000℃保温30分钟,5分钟内再降温至900℃保持5分钟,这种阶段式降温的优点是,保持反应的稳定性,进而可以保证碳化反应的均匀性以及实现制得粒度更加均匀的纳米级的碳化铬,经sem扫描电镜检测,颗粒尺寸大约为35-40nm之间,粒度差距较小。以上步骤制得样品6。实施例11本实施例的风机叶片表面修复方法,基本步骤同实施例10,不同和改进之处在于:nial喷涂层厚度为0.12mm,ni含量为93%,al含量为7%;nicr-cr3c2复合涂层厚度为0.21mm,cr3c2含量为80%,nicr为20%。本实施例的风机叶片表面修复方法,材料准备:nial纳米粉,nicr-cr3c2混合纳米粉,其中,纳米cr3c2粉的制备方法为:1:混合:将重铬酸铵粉体和纳米碳黑粉体按重量比1:0.20的配比置于粉体总重60%的蒸馏水中,混合搅拌均匀呈流体状,加入方形模具中压制成型呈前驱体;用1.4mpa压力压制后呈块状,压至厚度为2.5cm,以方便进行急冻;2:急冻:将前驱体快速转入-110℃急冻空间中进行急冻90min;3:冻干:将急冻好的前驱体快速转入真空冷冻干燥仓中进行冻干,冻干工艺曲线为:a、初期:板温0℃~100℃,升温斜率2℃/min,100℃保持35分钟,抽真空至60pa以内;b、中期:板温降温至80℃/min,保持50分钟,真空控制在100pa以内;c、后期,板温降温至60℃/min,保持100分钟,真空控制在80pa以内。4:碳化:关闭真空冷冻干燥仓冷阱,采用快速升温后再阶段式降温的模式,40分钟内升温至1200℃保持25分钟,10分钟内降温至1100℃再保持45分钟,10分钟内再降温至1000℃保温30分钟,5分钟内再降温至900℃保持5分钟,这种阶段式降温的优点是,保持反应的稳定性,进而可以保证碳化反应的均匀性以及实现制得粒度更加均匀的纳米级的碳化铬,经sem扫描电镜检测,颗粒尺寸大约为30-35nm之间,粒度差距较小。步骤五:冷却后用激光器进行激光重熔工艺处理,激光功率为900w,扫描速度为550mm/min,光斑大小10×3mm。以上步骤制得样品7。实施例12本实施例的风机叶片表面修复方法,基本步骤同实施例11,不同和改进之处在于:nial喷涂层厚度为0.10mm,ni含量为95%,al含量为5%;nicr-cr3c2复合涂层厚度为0.22mm,cr3c2含量为75%,nicr为25%。本实施例的风机叶片表面修复方法,材料准备:nial纳米粉,nicr-cr3c2混合纳米粉,其中,纳米cr3c2粉的制备方法为:1:混合:将重铬酸铵粉体和纳米碳黑粉体按重量比1:0.18的配比置于粉体总重60%的蒸馏水中,混合搅拌均匀呈流体状,加入方形模具中压制成型呈前驱体;用1.1mpa压力压制后呈块状,压至厚度为3cm,以方便进行急冻;2:急冻:将前驱体快速转入-130℃急冻空间中进行急冻100min;3:冻干:将急冻好的前驱体快速转入真空冷冻干燥仓中进行冻干,冻干工艺曲线为:a、初期:板温0℃~100℃,升温斜率2℃/min,100℃保持40分钟,抽真空至60pa以内;b、中期:板温降温至85℃/min,保持50分钟,真空控制在100pa以内;c、后期,板温降温至55℃/min,保持120分钟,真空控制在80pa以内。4:碳化:关闭真空冷冻干燥仓冷阱,采用快速升温后再阶段式降温的模式,40分钟内升温至1200℃保持25分钟,10分钟内降温至1100℃再保持45分钟,10分钟内再降温至1000℃保温30分钟,5分钟内再降温至900℃保持5分钟,这种阶段式降温的优点是,保持反应的稳定性,进而可以保证碳化反应的均匀性以及实现制得粒度更加均匀的纳米级的碳化铬,经sem扫描电镜检测,颗粒尺寸大约为35-40nm之间,粒度差距较小。以上步骤制得样品8。实施例13本实施例制作模拟沉没辊涂层,过渡层nicraly喷涂层厚度为100μm,cr含量为30%,y含量为3%,ni含量为67%;工作层nicr-cr3c2复合涂层厚度为500μm,cr3c2含量为75%,nicr为25%。本实施例的模拟沉没辊的多元合金涂层材料准备:nicr纳米粉,nicr-cr3c2混合纳米粉,其中,纳米cr3c2粉的制备方法为:步骤一:混合:将重铬酸铵粉体和纳米碳黑粉体按重量比1:0.21的配比置于粉体总重60%的蒸馏水中,混合搅拌均匀呈流体状,加入方形模具中压制成型呈前驱体;用2mpa压力压制后呈块状,压至厚度为3cm,以方便进行急冻;步骤二:急冻:将前驱体快速转入-140℃急冻空间中进行急冻30min;步骤三:冻干:将急冻好的前驱体快速转入真空冷冻干燥仓中进行冻干,冻干工艺曲线为:a、初期:板温0℃~100℃,升温斜率2℃/min,100℃保持30分钟,抽真空至60pa以内;b、中期:板温降温至80℃/min,保持60分钟,真空控制在100pa以内;c、后期,板温降温至50℃/min,保持200分钟,真空控制在80pa以内。步骤四:碳化:关闭真空冷冻干燥仓冷阱,采用快速升温后再阶段式降温的模式,30分钟内升温至1200℃保持30分钟,10分钟内降温至1100℃再保持40分钟,10分钟内再降温至1000℃保温20分钟,10分钟内再降温至900℃保持10分钟,这种阶段式降温的优点是,保持反应的稳定性,进而可以保证碳化反应的均匀性以及实现制得粒度更加均匀的纳米级的碳化铬,经sem扫描电镜检测,颗粒尺寸大约为35~40nm(本实施例为35、36、38或40nm等数值)之间,粒度差距较小。本实施例模拟沉没辊的喷涂方法,步骤为:步骤1前处理:将沉没辊表面机械打磨,打磨使用1000#碳化硅砂纸对基材表面进行打磨,用无水乙醇清洗,丙酮脱脂;将沉没辊表面机械打磨至至少sa3级清洁度;后喷砂处理,使用粒径为0.5mm铸铁砂为磨粒,压缩空气压力1.2mpa,喷砂距离为100mm,喷砂角度为20°,使精糙度到达rz70μm;步骤2喷涂:用hvof方法进行喷涂:nicry的喷涂方法参数为:氧气流量:2000scfh;煤油流量:21lph;送粉速度为:5.5rpm;喷涂距离380mm;nicr-cr3c2的喷涂方法参数为:氧气流量:1900scfh;煤油流量:23lph;送粉速度为:5.5rpm;喷涂距离380mm。以上步骤制得样品9。实施例14本实施例一种喷射式浆体冲蚀磨损试验装置,应用于表5所示的实施例5至13样品组成的九宫格式涂层材料样品库的试验,表5九宫格式涂层材料样品库样品1样品2样品3样品4样品5样品6样品7样品8样品9本实施例的一种喷射式浆体冲蚀磨损试验装置的试验方法,步骤为:a、固定试样4:将表5所示的九宫格式涂层材料样品库通过夹具固定在可旋转的固定板上,旋转角度可通过测角仪进行测定,旋转固定板,可以实现不同角度对试样进行冲蚀,调节时,使九宫格式涂层材料样品库对准九宫格式阵列模式排列的喷嘴微孔111;b、启动搅拌:启动搅拌器5,将浆体罐6内的浆料搅拌均匀;c、磨液泵和压缩气体罐启动:磨液泵10将浆料从浆体罐6中抽出,通过磨液管输送到喷嘴微孔111;同时,打开压缩气体罐2作为辅助动力,将浆料通过喷嘴微孔111对九宫格式涂层材料样品库高速冲蚀。并通过以下公式计算:上式中:e为试样冲蚀磨损率;m0为试样冲蚀前的质量;m1为试样冲蚀后的质量;q为浆料流量;t为冲蚀试验时间。d、浆料回流:喷往试样4的浆料滴落至试样室3后,通过回流管7滚入浆体罐6中,试样室3可以设计成收口状底部,回流管7与收口相通,方便浆体的循环式收集。试验过程中,每隔10个工作日对样品的侵蚀程度进行计算。经计算,冲蚀磨损率e的大小顺序为:样品1>样品2>样品3>样品4>样品6>样品7>样品5>样品8>样品9。以上示意性的对本发明及其实施方式进行了描述,该描述没有限制性,附图中所示的也只是本发明的实施方式之一,实际的结构并不局限于此。所以,如果本领域的普通技术人员受其启示,在不脱离本发明创造宗旨的情况下,不经创造性的设计出与该技术方案相似的结构方式及实施例,均应属于本发明的保护范围。当前第1页12