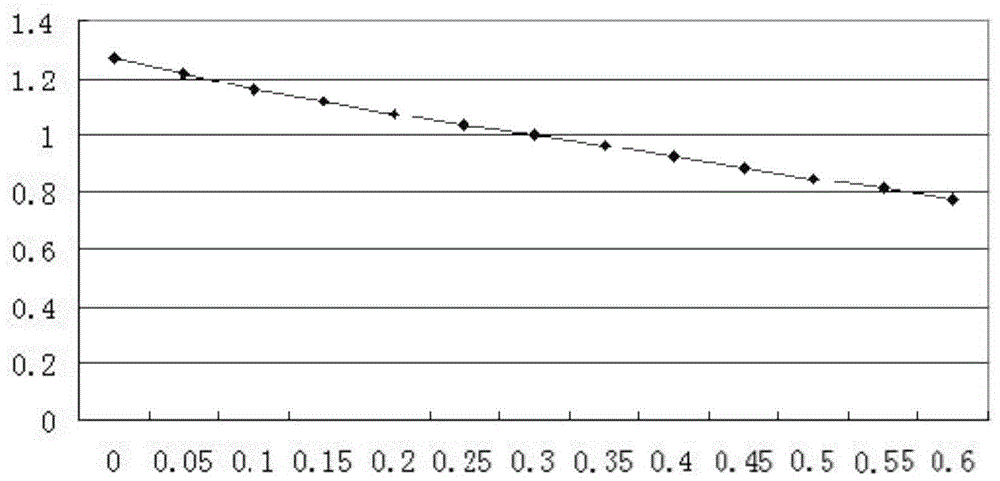
本发明属于检测仪器校准领域;涉及一种航空飞行器滑油室压力传感器校准装置及其校准方法。
背景技术:
:航天发动机技术的发展对飞行器的性能改进具有非常重要的意义,但目前,发动机的压力检测方面还存在许多不足。据统计,航天发动机的滑油系统故障在飞机各类故障中占有较高的比例,滑油压力作为测量发动机润滑状况的一个非常重要的参数,若压力出现偏差,将导致发动机不正常工作或润滑状况不正常的现象,增加事故发生几率。压力传感器作为测量压力的工具,它的精度、稳定性等性能的变化将直接影响压力测量的准确性,但是,现有的滑油压力传感器校验装置还存在诸多弊端。受现有技术条件的限制,现有的航天发动机滑油室压力传感器的校准装置,体积大,测量精度差,工作效率低。压力传感器故障情况不能及时被检测到,致使飞行员的人身安全得不到保障。为保证飞行员的安全降低事故发生几率,同时推进发动机技术的发展,急需开发设计出一套新的滑油压力传感器校准系统,对既有的校准原理和方法进行优化。技术实现要素:本发明所要解决的技术问题是提供一种航空飞行器滑油室压力传感器校准装置及其校准方法;旨在以滑油压力传感器为研究对象,设计并开发出一套基于嵌入式系统的滑油压力传感器校准系统,简化现有的校准设备、优化检测方法。为解决上述技术问题,本发明所采取的技术方案是:一种航空飞行器滑油室压力传感器校准装置,其特征在于:包括气泵、密闭容器、单相交流发电机、直流稳压电源、待测传感器、标准传感器、信号调理电路、数据采集卡和嵌入式系统、液晶屏;所述单相交流发电机为信号调理电路供电;所述直流稳压电源为传感器、数据采集卡和嵌入式系统供电;所述气泵的气体出口与密闭容器贯通;所述待测传感器与标准传感器并行置于密闭容器内,待测传感器的信号输出端串接信号调理电路、数据采集卡后与嵌入式系统总线电连接,而标准传感器的信号输出端串接数据采集卡后与嵌入式系统总线电连接;所述液晶屏显示测量结果和判断结果;所述信号调理电路将待测传感器输出的模拟电信号转换为数据采集卡接受的数字电信号。进一步的技术方案在于,所述嵌入式系统采用嵌入式主板pcm-3363,使用labview编程系统。进一步的技术方案在于,所述数据采集卡采用高精度多功能采集板卡pcm-3810i,并采用数据采集驱动程序包daqnavi。进一步的技术方案在于,所述信号调理电路由36v/400hz单相交流发电机供电。进一步的技术方案在于,所述的标准传感器为扩散硅压力传感器。进一步的技术方案在于,利用上述所述的一种航空飞行器滑油室压力传感器校准装置的校准方法,其特征在于:(1)将航空飞行器滑油室压力传感器校准装置各器件组装、连接完毕,正确安装labview、daqnavi和输出报表插件后,检测各数据采集通道是否完好,并指定信号调理电路的信号输入数据采集卡的方式为差分输入,标准传感器压力电信号输入数据采集卡为单端输入;(2)根据数据采集卡内存和程序运行速度,合理配置采样率和单次采样点数;(3)编写主程序,含混合信号分离、高频信号滤波和信号特征提取功能的滑油压力采集与分析子程序,数据超限控制子程序和滑油测试子程序,并启动硬件设备和运行部分程序;标准传感器输出的标准信号利用均方根算法提取特征值;待测传感器输出的待测电信号经信号调理电路变换为2路待测信号后,利用二者正峰的比值作为特征值;(4)以测试密闭容器压力的标准压力表的示数为基准,通过不断增加气压和减少气压的方式,记录标准传感器在不同测试点0,0.05,0.1,…,0.6mpa的虚拟压力表示数;重复多次实验,并分别求取各测试点测量值的均值;(5)以标准压力表的示数值为标定压力测试点,并作为为横轴;虚拟压力表的示数值为纵轴绘制数量关系曲线;根据曲线的特性和测定精度要求,将曲线划分为三段并作直线拟合;(6)将新出厂无磨合产品作为新品,将返修后产品作为大修,将新品、大修作为待测传感器,为新品、大修另增加拟合偏差函数;这样,经折算后的标准压力表与虚拟压力表示数一致;(7)编写标准信号拟合、测试结果判断和抑制零点温漂子程序;进行0.8mpa测试点的临界耐压测试,并根据其测试流程,编写倒计时子程序;设计包含记录测试结果、时间等信息的报表模板,编写数据保存、报表打印子程序和查看历史数据程序;(8)规范前面板和各控件形式,并根据用户需求生成可脱离开发环境labview的exe程序和标准化的安装程序。采用上述技术方案所产生的有益效果在于:本发明充分设计了系统的总体方案及所需的技术指标;设计了信号调理电路、选择了数据采集卡pcm-3810i和嵌入式系统pcm-3363等硬件开发环境,并对其基本参数进行配置;再以labview软件为程序开发平台设计了系统主程序,滑油压力采集与分析子程序、数据超限控制子程序、标准信号拟合子程序、滑油测试子程序和输出结果判断子程序等;最后,对软件系统和硬件系统进行联机调试,测试结果证明系统运行达到设计要求。附图说明下面结合附图和具体实施方式对本发明作进一步详细的说明。图1是本发明系统方案流程图;图2是本发明虚拟仪器构成方式;图3是本发明虚拟仪器结构图;图4是本发明硬件系统设计原理图;图5是本发明嵌入式计算机系统结构;图6是本发明等效原理图(1、硅膜片;2、低压腔;3、高压腔;4、硅环;5、引线);图7是本发明信号调理电路电路图;图8是本发明差分输入通道连接;图9是本发明一次函数拟合曲线;图10是本发明校准测试拟合函数图像。具体实施方式下面结合本发明实施例中的附图,对本发明实施例中的技术方案进行清楚、完整地描述,显然,所描述的实施例仅仅是本发明的一部分实施例,而不是全部的实施例。基于本发明中的实施例,本领域普通技术人员在没有做出创造性劳动前提下所获得的所有其他实施例,都属于本发明保护的范围。在下面的描述中阐述了很多具体细节以便于充分理解本发明,但是本发明还可以采用其他不同于在此描述的其它方式来实施,本领域技术人员可以在不违背本发明内涵的情况下做类似推广,因此本发明不受下面公开的具体实施例的限制。本发明的具体技术方案如下:1、系统总体设计方案及开发环境1.1系统方案设计1.1.1系统方案设计流程图根据技术方案的要求,本发明系统方案流程图如图1所示。1.1.2系统技术指标(1)在系统设计过程中,需要满足以下设计要求:①能够在0~0.8mpa范围内对滑油压力传感器进行校准,0,0.05,0.1,…,0.6mpa为正常测试点,0.8mpa为耐压测试点。0~0.6mpa范围内须判断检测点是否超差。②气密性检查,传感器内加过负荷压力0.8mpa,关闭气源,保持1min,压力指示下降值应不超过6kpa。③过负荷实验,传感器内加过负荷压力0.8mpa,保持2min,除去压力静置1h后,检查允许误差应符合要求。④标准传感器的在压力测量点的显示(前面板的虚拟压力表),与标准压力表并不完全一致,需通过直线拟合和比例折算进行修订。⑤待测传感器需要与标准传感器进行比较,判断待测传感器时候在误差允许范围内,并在测试列表中显示“合格”或者“超差”。⑥程序需设计测试、保存、打印、耐压测试、查看历史记录、停止等功能,能够将保存的测试数据生成报表,也可在测试过程中执行打印、查看历史记录等操作。⑦滑油压力传感器校准系统的测量精度为小数点以后3位。⑧利用调理调离灵敏反映待测传感器内部等效电桥的响应特性,并用采样信号的正峰比值作为特征值,这是滑油室压力传感器所特有的形式。(2)滑油压力传感器性能规范表1-1为滑油压力传感器校准时的性能检查标准表,根据允许误差值和误差控件的数值进行比较,判断滑油压力传感器是否合格。表1-1性能检查记录表表1-1(a)检查压力值与常温允许误差记录表表1-1(b)出厂性能检查记录表表1-1(c)修理性能检查记录表1.2虚拟仪器及labview简述(1)虚拟仪器概述虚拟仪器是高效灵活的软件与高性能的硬件模块结合的产物,用户可以通过操作图形化界面来控制计算机。虚拟仪器的突出优点是它可以利用pc组建虚拟系统,通过不同的接口总线,组建各类型自动测试系统。通过不同的接口总线的通信,调配虚拟仪器、各种带总线接口的电子仪器以及各种插件单元组建成可以实现各种功能的自动测试系统。与传统仪器相比较,虚拟仪器最大特点在于它的核心是软件。表1-2为虚拟仪器与传统仪器的比较:表1-2虚拟仪器与传统仪器的比较(2)虚拟仪器的组成虚拟仪器是基于计算机系统的仪器,主要是将虚拟仪器装入计算机,通过应用程序将通用计算机与功能化硬件结合起来,完成对测量的采集、分析、处理等功能。虚拟仪器按功能可以划分为采集数据、数据分析处理、结果表达三大模块。图2为其内部功能框图。虚拟仪器由通用仪器硬件平台和应用软件两大部分组合而成。虚拟仪器的硬件平台由计算机和i/o接口设备组成。软件是将可选硬件(如daq、gpib)与可重复使用源码库函数的软件结合起来,实现模块间的通信、定时与触发。应用程序可以实现虚拟仪器前面板功能,实现用户与仪器之间有效地信息交流。虚拟仪器结构框图如图3所示。(3)labview概述labview是目前世界上唯一编译型的图形化编程语言,又称g语言,它具有图形化编程方式的高性能和灵活性,以及专为测试测量和自动化控制应用设计的高性能模块及其配置功能,能为数据采集、仪器控制、测量分析与数据显示等各种应用提供必要的开发工具。在使用这种语言编程时,基本是用图标代替程序代码,连线构成流程图。因此,labview是一个面向最终用户的工具。labview的特点在于当程序在出现错误时,labview会提示用户,用户可以快速查出错误所在位置、类型及原因,方便用户编译程序。此外,labview在程序调试时,可以在程序中插入数据探针,检查任意中间结果。图形编程方式可以节约程序60%的开发时间,但是程序运行速率不会受到影响。(4)labview编程环境labview2013是目前ni推出的功能最强大的labview系列软件。1.3系统硬件开发平台1.3.1供压系统采用高压气泵30mpa空气压缩机。选择气泵代替液压系统供压,在于气泵工作介质为空气或者氮气,来源方便,且对环境无污染;与液压相比,气压传动动作迅速,反应快,维护简单;气泵的管路不容易堵塞,不存在介质变质、补充和更换问题;气泵对工作环境适应性好,能够安全可靠的应用在易燃易爆等场所;气压传动不需要像液压传动一样,需要有单独的能源且当液压系统发生故障时不易检查和排除。1.3.2单相交流发电机交流电源的频率一般是50hz或者60hz,而航空及军用电子电气设备设计的专用频率是400hz,原因是航空设备的容量、质量都有严格的要求,为了减小体积,减轻重量,要求航空发电机采用高频率。因此在设计中采用400hz单相交流电机。1.3.3pcm-3363嵌入式系统介绍atomn4551.66ghz单核/d525双核1.8ghz的处理器;支持扩展温度-40-85℃;24位lvds支持和板载1gbddr3800mhz内存;halt测试和100%锁定连接器;支持精简版imanager,susiaccess和嵌入式软件api。1.3.4pcm-3810i数据采集卡介绍滑油室压力传感器校准系统采用的是pcm-3810i多功能采集卡,实现模拟信号的精确采集。(1)概述pcm-3810i是一款功能强大的高速多功能板卡,适用于pci-104总线。pcm-3810i支持一个250khz,12-bita/d转换器和一个板载fifo缓存(能够为a/d存储多达4k个采样,为a/d转换存储多达4k个采样)。pcm-3810i总共提供了多达16个单端或8个差分a/d输入通道或混合组合、2个12-bitd/a输出通道、16个数字量i/o通道和3个10mhz24-bit多功能计数器通道。(2)pcm-3810i设备特性pcm-3810i是250ks/s、12-bit、16路pci-104的多功能板卡。主要特性:①16路单端或8路差分或模拟量输入的结合;②12-bita/d转换器,采样率高达250khz;③可编程增益;④自动通道/增益扫描;⑤用于模拟量输入和输出的板载环形缓冲区;⑥2个12-bit模拟量输出通道,支持连续波形输出功能;⑦16路数字量输入和16路数字量输出;⑧3个24-bit可编程10mhz多功能计数器/定时器;⑨自动校准(ai/ao);⑩灵活的触发和计时性能;2系统硬件设计及配置2.1硬件系统设计原理图如图4所示,为系统的硬件设计的原理图,通过硬件设备实现压力信号的转换和采集。2.2嵌入式系统嵌入式系统,是一种完全嵌入受控器件内部,为特定应用而设计的专用计算机系统,嵌入式系统一般用来控制或者监视机器、装置、工厂机械等大规模设备的运行情况。它的的核心元件由预先编程执行专项任务的微处理器或者单片机组成。嵌入式系统的软件通常一般不会被改动,所以形象的称它为“固件”。完整的嵌入式系统一般由嵌入式计算机系统和执行装置组成,嵌入式计算机系统是整个嵌入式系统的核心,执行装置可以接受嵌入式计算机系统发出的控制命令,执行所规定的操作或任务。此次嵌入式采用的是pcm-3363板卡。嵌入式计算机系统结构如图5所示。此选题的嵌入式系统(pcm-3363板卡)是研华n455/d525平台的一款pc104主板,它采用n455/d525处理器,具有板载1gddr3内存,4个usb接口,2个rs-232串行接口,1个rs-232/422/485串行接口,8位通用输入输出,极大的增加了可靠性,满足此滑油压力传感器校准系统设计的运行要求。2.3信号变换模块2.3.1扩散硅压力传感器工作原理利用压阻效应,采用集成工艺技术,沿单晶硅片上的特点晶向,制成应变电阻,构成惠斯登电桥,利用硅材料的弹性力学特性,制成了一个集力敏与力电转换检测于一体的扩散硅传感器。被测对象的压力作用到传感器的膜片上,膜片产生形变使扩散硅受到压力产生相应的微小位移,传感器的电阻值也随之发生变化,电子线路检测到这一变化,并转换输出一个对应于这一压力的标准测量信号。图6为等效原理图。2.3.2压阻式压力传感器特点(1)集感受、信号转换和检测于一体,无机械动件连接、转换环节,迟滞误差很小;(2)硅材料刚性好,形变小,线性度好;(3)扩散硅敏感膜片的弹性形变量在微应变数量级,不存在机械磨损,故障率低;(4)扩散硅材料不易被化学防腐,能适应各类工作环境;(5)硅材料与硅油有良好的兼容性,使它的结构工艺更易于实现;(6)低功耗、低成本、安全防爆。2.4信号调理单元信号调理是对从传感器输出的信号做加工和处理,包括信号的转换、滤波、存储、重放和一些专门的信号处理操作。在此设计中,信号调理电路的作用是提高滑油压力传感器输出响应特性,即敏锐反映传感器内部等效电桥的工作状态。另外,该电路具有线性变换的作用,具体的信号调理电路见图7。2.5信号采集单元数据采集,是根据数据采集卡设定的指令自动执行对传感器或其它待测设备的被测单元中的模拟或数字信号的采集,并送到计算机系统中进行分析和处理。在实际的生产作业中,采集到的数据会被生产过程中的计算机控制系统获取,用来控制某些特征物理量。数据采集单元性能主要取决于它的精度和速度。在保证精度的条件下设置较高的采样速度,以满足实时采集、实时控制和及时处理对速度的要求。2.5.1数据采集卡的应用滑油压力传感器校准的数据采集单元采用pcm-3810i采集卡,pcm-3810i是研华多功能pci-104模块,具有集成数字i/o,模拟i/o,以及各种嵌入式系统应用,此次选用采集卡的模拟i/o模块对信号进行输入/输出操作。pcm-3810i具备研华的pc-104模块的最高采样率,可以很好满足滑油通道初始化对多路通道信号的采集要求。2.5.2labview中daqnavi属性设置此次信号的采集利用研华最新的数据采集驱动程序包daqnavi,它能够很好的节约开发时间、支持运行多种程序语言、在多通道和多核心环境下保证执行性能、方便接口操作、支持多种操作系统作业等特性,是一全新的跨平台数据采集驱动套件。在daqnavi属性中对信号通道连接类型、采样率、采样点进行以下设置:采样率为20khz,采样点数设定为128。ai5为标准信号输入通道,ai6、ai7、ai8、ai9为差分信号输入,设定ai5为标准信号输入,ai6为a路信号输入,ai7、ai9为b路信号输入,ai8为c路信号输入,其余通道为单端输入。则ai6-ai7为a-b,ai8-ai9为c-b。a-b为信号1,c-b为信号2,标准信号为信号0。2.6通道选择及端子接线电压是电气或电子电路两点间的电势差,测量参考点的电平是进行测量时的参考电平。然而,如何确定测量参考点是需要经常考虑的问题。信号采用不同的输入方式,测量参考点的设置也会有差别。在此采用差分输入,每一个输入信号都有自己的基准地线,差分输入会抵消共模噪声,减小了噪声对传输信号的影响。(1)差分信号输入差分信号指的是用两根传输线传输信号,传输的是两路信号之间的电平差。当传输信号受到周围环境因素的影响出现偏差时,两路信号都会受到扰动,但是由于差分输入的是两路信号的差值,进而减小外界因素对传输信号的影响。差分输入通道连接图如图8所示。(2)差分信号优势①抗干扰能力强,当外界发生扰动时,扰动信号几乎同时被耦合到两条传输线上,在接收端两路耦合做差,外界的干扰几乎完全被抵消掉。②能有效抑制emi,两路信号的极性相反使他们对外辐射的电磁场可以相互抵消。③时序定位精确,差分通道的两路信号是同时被采集和检测,不存在滞后现象,能降低时序上的误差。在此次滑油压力传感器校准系统的设计中,滑油压力传感器输送的信号微弱,噪声干扰对原信号的影响特别大,从而影响测量结果,使校准出现偏差。为了降低外界干扰,选用差分信号输入方式,减小环境因素对测量结果的影响。3基于labview的软件系统设计3.1滑油采集与分析3.1.1程序框图在labview中建立子滑油通道初始化子vi;利用数据采集卡采集信号时,标准压力电信号采用单端输入,经过daqnavi后指定为标准信号0,并利用均方根算法求其特征值;待测压力电信号经调理后变为2路电信号,均采用差分方式,经过daqnavi后分别指定为待测信号1和待测信号2;并指定二者正峰的比值为待测电信号的特征值。输入方式和特征值的选取方式是由滑油压力传感器的输出特性决定。3.2滑油选择设置3.2.1程序框图滑油选择vi实现测试信号的行索引,进行滑油测试时,程序要对输入的标准信号的进行判别,测量信号不同时,进入测试面板不同的行内,在不同的测试点被测量的允许误差以及拟合的函数都存在差异。滑油选择程序实际是待测滑油压力信号对所在行、误差的选择。首先,此程序先对标准信号的范围进行判断,将各个判断结果送入相应的条件结构中,若数值在范围内,则执行相应的行索引,若不在范围内则不动作。最后对多个判断结果进行复合运算,输出结果。测量点范围与索引行关系列表如表3-1所示:表3-1测量点范围与索引行关系列表3.3传感器数据比较设计3.3.1程序框图传感器数据比较子vi是对各测量点是否超差进行判断。根据设计要求,各测量点都有允许误差,若实际测量误差超出允许误差,则系统给出此测量点超差、传感器不合格的结论。在设计程序时,采用条件结构的多层嵌套模式,根据滑油压力传感器性能规范部分要求,对传感器数据比较程序设计要求如表3-2所示(定义标准信号为a,误差为b)。表3-2程序设计要求经过条件结构判断后,结果调用到滑油压力传感器校准vi当中,在检测结果表格的结论框中显示超差还是合格。3.4滑油实验器功用设计3.4.1程序框图滑油实验器功用vi是滑油测试类型选择程序。滑油压力传感器的校准分为新品滑油传感器的校准和修理后的滑油压力传感器的校准。通过这个程序,选择滑油传感器的校准类型并进入相应的滑油校准程序,进行测试。也可以退出返回测试主界面。此程序对while循环结构进行设计,整个循环分为四个事件:(1)超时。等待操作;(2)滑油新品测试确定。即调用滑油新品校准程序对即将出厂的滑油压力传感器进行性能测试;(3)滑油大修测试确定。即调用滑油大修校准程序对返厂维修后的滑油压力传感器进行性能测试;(4)停止。退出实验器功用界面,返回主界面。3.5滑油压力传感器校准程序设计滑油压力传感器校准程序分为滑油新品校准和滑油大修校准两部分,这两个测试程序在信号采集和分析处理等方面是相同的,主要差别在于校准曲线的拟合和允许误差的大小。下面以滑油新品校准程序设计为例介绍滑油压力传感器校准系统。滑油校准程序是滑油压力传感器校准系统的核心部分,它具有测试、保存、打印、查看历史记录等多个事件分支结构,可以行驶多种功能。3.5.1校准程序事件结构设计等待测试的数据以队列形式进入while循环,在等待测试部分又分为以下6个事件分支。(1)超时分支设计该分支调用滑油通道初始化子vi的输出结果,对待测信号进行函数运算、曲线拟合,使之显示实际待测传感器的压力值。前面介绍到,由于环境等因素的影响,实际的传感器的静态特性并不是完全线性的,此次对待测传感器的校准采取多折线形式。下面对校准曲线的拟合过程进行简要介绍:设定标准控件的值为m,待测控件的值为n,条件结构运算输出结果为r,标准控件输出结果为s。控件值与控件输出的关系如表3-3、3-4所示。表3-3标准控件值与输出结果关系表3-4待测控件值与输出结果关系条件控件输出与各点的微小偏差做和,为待测传感器输出。(2)测试分支设计测试分支调用滑油选择vi的输出结果,根据测量点的不同进入相应的行。然后根据标准传感器压力、待测传感器压力和两者的误差,对传感器的性能进行判断。当标准信号在正常测量范围内即滑油检测值在0~0.615范围内,则执行以下步骤:标准信号输入后,经过滑油选择子vi,选择相应的索引行,标准、待测传感器和误差数值转化为浮点型字符串。测试时,转化过来的字符串不断替换数组中的数组子集,再将结果输入到表格控件和测试列表中。当比较结果也就是误差在误差允许范围内时,测试列表的结论列相应的位置输出黑色“合格”当比较结果超出允许误差范围时,则测试列表结论列相应的位置输出红色“超差”。当滑油检测数值不在滑油选择vi设置的行索引的范围。测试程序不能被执行,在前面板会输出“检查点设置不当,需调节”字符串提示操作者检查点无法检测。当滑油检测数据大于0.85时,测试程序不能被执行,在前面板输出“压力选择错误,需立即调节”字符串,警告操作者压力已经超出滑油压力传感器的临界耐压范围,需要立即调节。(3)保存分支设计将表格控件内的测试数据存储在express的msofficereportvi当中,生成excel自定义报告,然后,将生成的报告保存,方便打印和查看历史记录等操作。(4)打印分支设计表格控件将测试数据送入msofficereport子vi当中,与前面保存分支对此vi设置的路径相同,另外一个子vi连接打印机可以对测试报表进行打印操作(5)查看历史记录分支设计经过连接字符串执行systemexec.vi系统命令,查看新品_滑油测试以前保存的所有测试报表。(6)耐压测试分支设计当标准控件的数值在0.785~0.815范围内,则可以进行耐压测试,耐压测试时,前面板会有120秒倒计时时间提示操作者,在120秒倒计时过程中,测试、打印、查看历史记录等按钮不能被操作,当120s计时结束后,所有功能恢复正常。当标准控件的数值大于0.615小于0.785时,前面板显示“耐压测试点选择不当,需调节”字符串,提醒检测人员此时的耐压测试点不合适,需重新选择。(7)停止测试分支设计结束以上所有操作,回到测试主界面。3.5.2滑油压力传感器校准程序前面板设置滑油压力传感器测试平台实现测试、保存、打印等功能。3.6滑油传感器校准实验器设计总程序的执行实际是是各子vi的执行,在总程序的执行过程中,需要不断地调用子vi程序。当程序开始执行时,首先调用试验器功用子vi,进入试验器功用界面,然后根据滑油校准选择,进入新品滑油测试程序或大修滑油测试程序,进行滑油压力传感器校准测试,测试完成后可进行保存、打印等操作。按下相应的滑油测试程序的停止按钮,退出滑油测试程序回到总程序执行界面,当按下总程序执行界面的停止按钮时,关闭滑油测试总程序。根据校准系统设计流程图,对滑油压力传感器校准程序框图进行设计。4滑油压力传感器校准系统测试与分析4.1滑油压力传感器校准程序功能实现滑油压力传感器的软件程序与硬件平台相结合,开始对滑油压力传感器展开测试,测试步骤如下:打开“滑油压力传感器实验器”程序,运行程序,出现“滑油压力传感器实验器”主界面,点击“运行总程序”按钮,进入“实验器功用”界面,在此界面选择对滑油传感器进行“新品检测”还是“大修检测”,按下相应检测的按钮,进入相应的“滑油压力传感器测试平台”界面,开始对滑油压力传感器在临界耐压值以下进行校准测试,同时,在压力临界点对测试可以对传感器进行临界耐压测试,测试结果可保存、查看和打印。测试结束后,按下停止按钮,返回“实验器功用”界面,可进行下一轮测试,若结束测试操作,则连续按下各界面的“停止“按钮即可。4.2程序生成labview编写的测试校准程序最后需要移植到滑油传感器校准实验器上运行,但是labview程序安装复杂,占用主机内存较大,程序启动时间过长,一般工厂对仪器的要求不仅是测试结果精确,而且还要保证效率高。为满足这一要求,将labview编写的程序在计算机上编译生成独立可执行的exe文件,将生成的exe和传感器校准程序用到的组件打包生成installer,然后在任意电脑上运行安装程序即可快速打开滑油压力传感器的校准程序,结合硬件测量平台即可进行传感器的校准检测。安装文件安装完成后,之前生成的exe、labview运行引擎以及其他用到的工具包会自动安装到目标电脑上,将labview程序封装成一个小软件。这种方法移植程序比较简单,而且程序占用内存小,启动速度快。4.2.1生成应用程序新建一个labview项目,或者打开滑油压力传感器校准程序的项目,在项目浏览器的“程序生成规范”处右击“新建”>“应用程序(exe)”,然后设置目标文件名和目标目录,目标文件名以将要生成的exe文件命名,该文件位于目标目录中,生成的exe文件保存到这个目录中。然后,选择“源文件”,选中顶层vi单击“添加项”箭头,将顶层vi添加到启动vi栏中,其他用到的子vi和文件添加到始终包括栏中,然后选择“预览”>“生成预览”,可以看到独立可执行应用程序,最后选择“生成”,labview就会弹出生成状态窗口,当生成结束后单击“完成”,关闭生成状态窗口。生成独立可执行应用程序的操作已经完成,如果目标电脑上已经安装了labview运行引擎和其他需要的组件,就可以直接将生成的exe文件安装到目标电脑上运行。如果没有安装运行引擎和其他需要的组件,则在生成exe文件的基础上生成installer,即生成安装文件。4.2.2生成安装文件在同一个项目中右击“程序生成规范”,选择“新建”>“安装程序”,在“产品信息”中设置产品名称和安装程序生成目录,选择“目标”,修改目标名称,选择“源文件”,在“项目文件”视图中单击选择之前创建的“应用程序生成规范”,然后单击添加箭头,将应用程序添加到目标文件夹中。选择“附加安装程序”,勾选相应的labview运行引擎和必要的驱动程序以及工具包。单击“生成”按钮会弹出一个生成状态窗口,开始生成安装程序。生成过程完成后,可以打开安装文件所在路径,会看到一个setup.exe文件,这个文件就是最终的安装文件。单击“完成”按钮关闭状态窗口。现在,可以将打包生成好的安装程序安装到任何一台电脑上运行,安装的时候需要将整个文件夹拷到目标电脑上然后再运行setup.exe,安装过程与普通windows应用程序相类似,安装结束后可以在目标电脑上运行该应用程序。4.3程序调试过程中遇到的问题(1)标准滑油压力传感器在程序显示中的校准在程序前面板中,由于标准传感器的输出结果是电压信号并非压力值,且标准传感器自身并非纯线性,因而调试程序中要首先考虑标准传感器的显示问题,即在显示程序前必须有传感器测量结果校准部分。选用已经校准好的精密机械量表对校准标准滑油压力传感器进行显示校准操作,观察标准压力表是否与机械量表示数完全一致,从而判断标准表是否精确无误。对标准表的测量分为正向测量和反向测量两种方式,由于测量仪表在正向检测和反向检测过程中的误差是存在差别的,为保证实验的准确性,采取多次测量,反复校准。(2)标准滑油压力传感器的校准曲线拟合首先,对滑油指示器电压进行测量,得到其电压数据如表4-1所示:表4-1滑油指示器电压数据根据前期的电压测量数据,用matlab进行待测传感器的曲线拟合,由于压力传感器的静态特性是线性的,所以,首先采用一次函数进行拟合,拟合曲线如图9所示。其函数表达式为:f(x)=-1.215x+1.534(x表示待测压力,f(x)表示比值信号vb1/vb2)。理论上讲,传感器的静态特性是线性的,但实际上,由于材料、环境等因素的影响,传感器的实测输入/输出关系并不是一条直线。因此传感器实际的静态特性的校准特性曲线与某一参考直线在一定程度上存在不吻合现象。由图像看出,并不是所有的点都在曲线上,不能精确地进行校准测量,所以用一个函数拟合出来的校准曲线不是最理想的,经过研究讨论,采用多折线形式来拟合待测传感器校准曲线。对各压力检查点进行采集并记录,记录结果如表4-2所示,再根据虚拟压力表的示数进行校准曲线拟合。表4-2待测信号采集表拟合函数图像如图10所示。其曲线拟合函数表达式为:由图10可以看出,各点都在函数曲线上,且在每一段折线范围内是线性的,能够在各测量点较准确地进行测量和判断,此外,由于测量时进来的信号存在偏差,为了使测量更精确,在拟合的函数的基础上,在各测量点加上一个小的偏差,新品的偏差函数表示为式(5-2),校准的偏差函数表示为式(5-3)所示。y1=60.42x6-107.7x5+68.85x4-18.91x3+2.155x2-0.1102x+0.012(5-2)y2=90.28x6-152.1x5+92.57x4-24.15x3+2.215x2+0.04167x+0.017(5-3)用此函数进行模拟测试结果如表4-3、4-4所示。表4-3滑油传感器新品1校准表4-4滑油传感器新品2校准检查点标准值(mpa)检测值(mpa)误差(mpa)结论0.000.0000.002-0.002合格0.050.0500.051-0.001合格0.100.1000.0960.004合格0.150.1500.1500.001合格0.200.2000.1980.002合格0.250.2500.250-0.000合格0.300.2990.300-0.001合格0.350.3500.3470.003合格0.400.4000.3950.005合格0.450.4500.4430.007合格0.500.5000.4910.009合格0.550.5500.5490.007合格0.600.6000.5980.002合格(3)指针跳动现象及解决方案初步设定的采样率为2khz,采样点数为128,发现标准压力表和待测压力表的指针存在跳动现象,不能稳定在测量点位置。针对这一现象,在daq内重新设置采样率和采样点数。根据初步设定采样点和采样率,计算可得:一秒内的采样点数是2k×128=256k,指针出现跳动的原因是采样率或者采样点数目偏低,将采样率提高到4khz,采样点数目不变,再次运行程序发现,指针跳动幅度减小,但不够稳定,还需进一步调整,当采样率调整为20khz,采样点为128时,指针跳动现象基本消失,数据可以平滑的改变。(4)产生零点漂移的原因及解决办法所有的传感器都存在零点漂移,漂移的主要形式是温度偏移,零点漂移对传感器的测量精度产生一定的影响。由于传感器中惠斯登桥路的元件参数本身存在不对称现象,弹性元件和电阻应变计材料的温度系数、线胀系数不同,组桥引线长度不一致等因素的影响,导致电桥相邻臂的温度系数有一定差异,当温度变化时,相邻臂电阻变化量不同,从而使电桥产生输出不平衡,即产生了零点漂移。同时,气泵也有自身的局限性,一方面,气泵加压时,气体并不是均匀分布的,另一方面,当温度发生变化时,气压会有明显的改变。此外,电源电压不稳也会引起零点漂移。对于硬件系统来说,零点漂移问题不可避免,因此,选择通过软件程序的设计来解决传感器温度漂移问题。设定在标准压力表零点左右很小的范围内的信号值强制为零,减小零点漂移对零点的影响。在电源的选取上,选用12v、5v大功率稳压电源对系统进行供电,减少电压不稳给零点带来的影响。当前第1页12