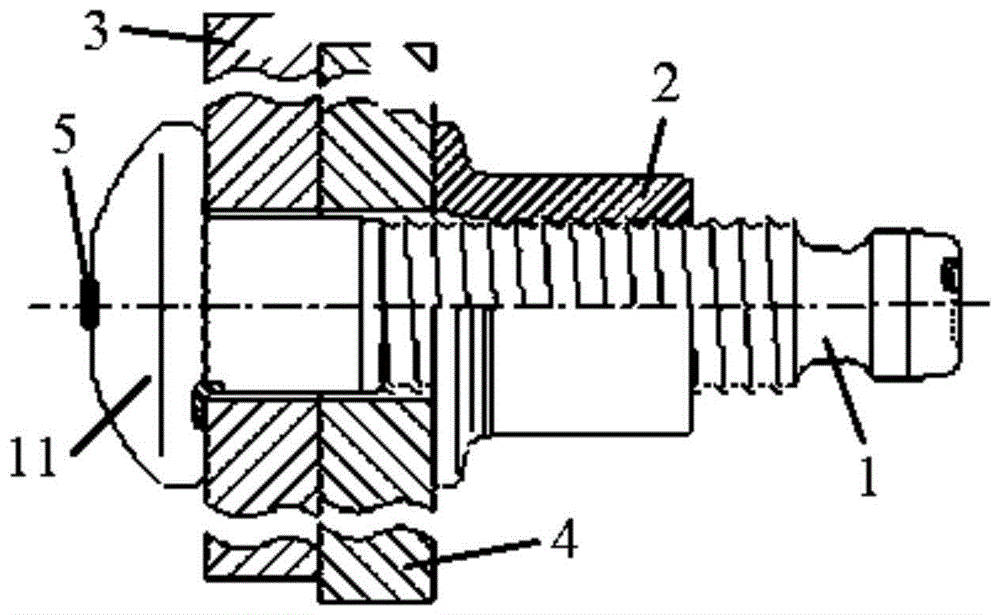
本发明涉及监测数据校准
技术领域:
,特别是涉及一种短尾铆钉标定矫正方法。
背景技术:
:在监测铆钉的安装效果是否达标时,往往采用超声波测试的方法来获取铆钉所受的轴向力,超声波测试的原理是通过测量超声波在铆钉中传播超声波的时间延迟来计算得出与上述时间延迟呈正比关系的轴向力。目前,铆钉的时间延迟与轴向力的关系数据可以通过实验监测预先标定,其具体产生轴向力的方式是通过铆枪拽拉铆钉的尾部,同时利用超声波测试仪测量铆钉的时间延迟,通过调整铆枪的输出拉力来获得多组轴向力与时间延迟的对应关系,这样便可获得铆钉的标定曲线。但是对于短尾铆钉来说,由于其末端在长时间受力时容易发生形变,这样会影响短尾铆钉的受力参数的准确性,其实际所受的轴向力大于轴向力的检测值,进而使短尾铆钉的标定曲线不能通过传统的实验方法进行确定,进而会使超声波测试仪无法准确地测出短尾铆钉所受的轴向力。因此,如何确定短尾铆钉实际所受的轴向力是本领域技术人员亟待解决的问题。技术实现要素:本发明的目的是提供一种短尾铆钉标定矫正方法,该短尾铆钉标定矫正方法能够准确地获取短尾铆钉所承受的轴向力,解决了超声波测试仪检测短尾铆钉所受轴向力不精准的问题。为实现上述目的,本发明提供一种短尾铆钉标定矫正方法,包括:步骤s1:利用液压铆枪以预设铆接力将短尾铆钉安装于套环,在所述短尾铆钉的冒头和所述套环之间设置轴力传感器;步骤s2:利用所述轴力传感器测量所述短尾铆钉所承载的实际轴向力;步骤s3:利用超声波测试仪测量所述短尾铆钉的实际时间延迟;步骤s4:将实际轴向力与实际时间延迟的对应数据导入所述超声波测试仪。优选地,所述步骤s1还包括:在所述轴力传感器处设置垫片,使所述轴力传感器与所述垫片二者的厚度等于所述短尾铆钉的待夹持厚度。优选地,所述步骤s3具体包括:s31:在所述冒头处设置陶瓷贴片;s32:利用所述超声波测试仪接触所述陶瓷贴片并测量所述短尾铆钉的实际时间延迟。优选地,所述步骤s1具体为:利用所述液压铆枪以相同的预设铆接力将多个所述短尾铆钉安装于多个所述套环,在任一所述短尾铆钉的冒头和相应的所述套环之间均设置所述轴力传感器。优选地,所述步骤s2与所述步骤s4之间包括:步骤s401:计算所述轴力传感器测量的全部实际轴向力的平均值;所述步骤s3与所述步骤s4之间包括:步骤s402:计算所述超声波测试仪测量的全部实际时间延迟的平均值。优选地,所述步骤s4具体包括:步骤s411:计算实际轴向力与实际时间延迟的比例系数;步骤s412:将所述比例系数导入所述超声波测试仪。优选地,所述步骤s4具体包括:步骤s421:获取所述超声波测试仪中具有预设时间延迟与预设轴向力对应数据的标定伪文件;步骤s422:按照实际轴向力与实际时间延迟修改标定伪文件中的数据;步骤s423:将更新后的标定伪文件导入所述超声波测试仪。相对于上述
背景技术:
,本发明提供的短尾铆钉标定矫正方法,通过将压力传感器测得的短尾铆钉实际所受的轴向力导入超声波测试仪来矫正短尾铆钉的标定曲线。具体来说,液压铆枪作用于短尾铆钉的冒头将短尾铆钉的螺纹端安装于套环内,此时冒头与套环将夹紧轴力传感器,进而测得短尾铆钉所受的实际轴向力,与此同时,通过超声波测试仪测量短尾铆钉的实际时间延迟,进而获得一组实际轴向力与实际时间延迟的对应数据,然后将上述对应输入导入超声波测试仪内,以矫正超声波测试仪内预设轴向力与预设时间延迟的对应数据,使超声波测试仪能够单独且精准地测量短尾铆钉实际所受的轴向力。附图说明为了更清楚地说明本发明实施例或现有技术中的技术方案,下面将对实施例或现有技术描述中所需要使用的附图作简单地介绍,显而易见地,下面描述中的附图仅仅是本发明的实施例,对于本领域普通技术人员来讲,在不付出创造性劳动的前提下,还可以根据提供的附图获得其它的附图。图1为本发明所提供的一种短尾铆钉标定矫正方法所对应的实体布置示意图;图2为本发明实施例所提供的第一种短尾铆钉标定矫正方法的流程图;图3为本发明实施例所提供的第二种短尾铆钉标定矫正方法的流程图;图4为图2和图3中步骤s3的具体流程图;图5为本发明实施例所提供的第三种短尾铆钉标定矫正方法的流程图;图6为图2、图3和图5中步骤s4的第一种具体流程图;图7为图2、图3和图5中步骤s4的第二种具体流程图;其中,1-短尾铆钉、11-冒头、2-套环、3-轴力传感器、4-垫片、5-陶瓷贴片。具体实施方式下面将结合本发明实施例中的附图,对本发明实施例中的技术方案进行清楚、完整地描述,显然,所描述的实施例仅仅是本发明一部分实施例,而不是全部的实施例。基于本发明中的实施例,本领域普通技术人员在没有做出创造性劳动前提下所获得的所有其它实施例,都属于本发明保护的范围。为了使本
技术领域:
的技术人员更好地理解本发明方案,下面结合附图和具体实施方式对本发明作进一步的详细说明。请参考图1至图7,图1为本发明所提供的一种短尾铆钉标定矫正方法所对应的实体布置示意图;图2为本发明实施例所提供的第一种短尾铆钉标定矫正方法的流程图;图3为本发明实施例所提供的第二种短尾铆钉标定矫正方法的流程图;图4为图2和图3中步骤s3的具体流程图;图5为本发明实施例所提供的第三种短尾铆钉标定矫正方法的流程图;图6为图2、图3和图5中步骤s4的第一种具体流程图;图7为图2、图3和图5中步骤s4的第二种具体流程图。本发明所提供的一种短尾铆钉标定矫正方法,如图1和图2所示,该方法包括:步骤s1:利用液压铆枪以预设铆接力将短尾铆钉1安装于套环2,在短尾铆钉1的冒头11和套环2之间设置轴力传感器3。通过液压铆枪(图中未示)的铁砧内的卡爪抓紧短尾铆钉1的尾部,然后在轴向拉伸并在径向挤压将短尾铆钉1与套环2配合;而且在套环2的安装端设置轴力传感器3,当短尾铆钉1在液压铆枪的作用下与套环2配合时,套环2和冒头11将夹紧轴力传感器3。可以理解的是,在短尾铆钉1的弹性范围之外,短尾铆钉1所受的轴向力与时间延迟将不再呈正比关系,所以应控制液压铆枪的预设铆接力适宜以保证在短尾铆钉1的弹性范围内实现短尾铆钉1与套环2的配合。值得一提的是,在实际装配短尾铆钉1时发现短尾铆钉1的夹持厚度也会影响短尾铆钉1所受轴向力的大小,因此需要使轴力传感器3的受力端厚度与短尾铆钉1的待夹持厚度一致,但是若针对不同夹持厚度采用具有相应厚度受力端的轴力传感器3,则会增加本方法的成本。为此,如图4所示,步骤s1还包括:在轴力传感器3处设置垫片4,使轴力传感器3的厚度与垫片4二者的厚度等于短尾铆钉1的待夹持厚度。具体来说,这里可以选用厚度较薄受力端的轴力传感器3,然后在上述受力端处设置垫片4,该垫片4贴合受力端,作为优选,垫片4设于轴力传感器3的受力端与套环2之间,并保证垫片4与上述受力端二者的厚度等于短尾铆钉1的待夹持厚度,进而保证轴力传感器3能够准确地测得短尾铆钉1以待夹持厚度装配时所受的轴向力。步骤s2:利用轴力传感器3测量短尾铆钉1所承载的实际轴向力。在液压铆枪的作用下,冒头11和套环2将挤压轴力传感器3使轴力传感器3能够测出冒头11与套环2之间的挤压作用力,也即得到断尾铆钉所承载的实际轴向力。需要说明的是,为了保证轴力传感器3测量数据的精准性,优选将轴力传感器3的受力端设计为环状,以供短尾铆钉1的螺纹端穿过,同时还能够与冒头11和套环2的端面紧密接触上述受力端。步骤s3:利用超声波测试仪测量短尾铆钉1的实际时间延迟。通过超声波测试仪测量超声波在短尾铆钉1中的传播时间,以获取承载上述实际轴向力的断尾铆钉的实际时间延迟,进而得到实际轴向力与实际时间延迟的对应数据。具体来说,如图4所示,步骤s3包括:步骤s31:在冒头11处设置陶瓷贴片5。将陶瓷贴片5装设于冒头11远离套环2一侧的中心位置。步骤s32:利用超声波测试仪接触陶瓷贴片5并测量短尾铆钉1的实际时间延迟。作为优选,上述超声波测试仪具体为mc950超声波测试仪。值得一提的是,为了保证超声波测试仪检测数据的精准性,在步骤s1之前还需要对短尾铆钉1进行预处理,也即将短尾铆钉1的两端磨平,作为优选,设置短尾铆钉1两端的平行度为0.01mm,并保证粗糙度为ra0.16。步骤s4:将实际轴向力与实际时间延迟的对应数据导入超声波测试仪。根据实际轴向力与实际时间延迟的对应关系更新超声波测试仪中轴向力与时间延迟的对应关系数据,使更新数据后的超声波测试仪能够准确地通过测量短尾铆钉1的时间延迟来得出其所受的轴向力大小。总的来说,本短尾铆钉标定矫正方法的核心有二:一是通过液压铆枪作用于短尾铆钉1的尾部以避免短尾铆钉1发生形变,进而避免上述形变影响轴向力和时间延迟的精准测量,也即保证数据测量精准;二是通过轴力传感器3直接测量短尾铆钉1所承载的轴向力,以避免利用其它物理参量标准来间接计算得出轴向力的大小,也即保证轴向力的测量结果精准,进而便于对超声波测试仪中的数据进行矫正。在第一种实施例中,为了保证由轴力传感器3和超声波测试仪分别测得的实际轴向力与实际时间延迟的精准性,上述步骤s1具体为:利用液压铆枪以相同的预设铆接力将多个短尾铆钉1安装于多个套环2,在任一短尾铆钉1的冒头11和相应的套环2之间设置轴力传感器3,也即设置多个短尾铆钉1与套环2配合的测试组。作为优选,设置三个短尾铆钉1与套环2配合的测试组。在第二种实施例中,对于步骤s2来说,如图5所示,步骤s2与步骤s4之间还包括步骤s401:计算轴力传感器3测量的全部实际轴向力的平均值。这样便可以通过多个轴力传感器3测得多组短尾铆钉1所受的实际轴向力,然后剔除上述多组实际轴向力中偏差明显的数值,并对其它数据进行平均值计算以消除随机误差;同理,对于步骤s3来说,如图5所示,步骤s3与步骤s4之间还包括步骤s402:计算超声波测试仪测量的全部实际时间延迟的平均值。这样便可通过超声波测试仪对每一短尾铆钉1的实际时间延迟进行测量,接着剔除全部实际时间延迟中的偏差数据,并对其它数据做均值计算,以消除实际时间延迟检测值的随机误差,这样在步骤s4中便可将较为准确的实际轴向力与实际时间延迟的对应数据导入超声波测试仪。在第三种实施例中,如图6所示,步骤s4包括:步骤s411:计算实际轴向力与实际时间延迟的比例系数。根据
背景技术:
内容可知,短尾铆钉1在其弹性范围内所受的轴向力与时间延迟呈正比,这样便可通过步骤s3和步骤s4中所得到的实际轴向力与实际时间延迟求出短尾铆钉1所受轴向力与时间延迟的比例系数。结合上述第一种实施例需要说明的是,在本步骤s411中,若进行了多组短尾铆钉1的矫正数据测量,则可先求出每一组实际轴向力和实际时间延迟的比例系数,然后去除偏差较大的比例系数,最后对剩余的比例系数做均值计算,以消除上述比例系数的随机误差。步骤s412:将所述比例系数导入所述超声波测试仪。将超声波测试仪内存储的原有比例系数更新为步骤s411中所求得的比例系数,以矫正超声波测试仪中轴向力与时间延迟的计算公式,使超声波测试仪能够直接准确地检测全部同一型号短尾铆钉1所承载的轴向力。在第四种实施例中,如图7所示,步骤s4包括:步骤s421:获取超声波测试仪中具有预设时间延迟与预设轴向力对应数据的标定伪文件。具体来说,标定伪文件中预设时间延迟与预设轴向力的对应数据可以直接挪用超声波测试仪中用于检测普通铆钉的标定文件数据,当然也可以重新制作一份标定伪文件,其中,从坐标系原点处以同一预设的比例系数设定标定伪文件中的对应数据如下:表1标定伪文件的数据参数预设时间延迟(ns)预设轴向力(kn)00208.199.71216.9103.9225.4107.99233.9112.06步骤s422:按照实际轴向力与实际时间延迟修改标定伪文件中的数据。按照步骤s3和步骤s4中所得到的实际轴向力与实际时间延迟更新上述标定伪文件的数据参数,也即按照上述实际轴向力与实际时间延迟的比例关系更新上述标定伪文件的数据参数。步骤s423:将更新后的标定伪文件导入超声波测试仪。将超声波测试仪内存储的原有标定伪文件更新为步骤s422中矫正得到的标定伪文件,使超声波测试仪能够直接准确地检测全部同一型号短尾铆钉1所承载的轴向力。针对上述两种实施例需要说明的是,由于超声波测试仪能够精准地测出短尾铆钉1的时间延迟,而且步骤s4的作用是矫正超声波测试仪中轴向力与时间延迟的比例关系,所以使被矫正后的超声波测试仪能够单独地测出短尾铆钉1所承载的实际轴向力。以上对本发明所提供的短尾铆钉标定矫正方法进行了详细介绍。本文中应用了具体个例对本发明的原理及实施方式进行了阐述,以上实施例的说明只是用于帮助理解本发明的方法及其核心思想。应当指出,对于本
技术领域:
的普通技术人员来说,在不脱离本发明原理的前提下,还可以对本发明进行若干改进和修饰,这些改进和修饰也落入本发明权利要求的保护范围内。当前第1页12