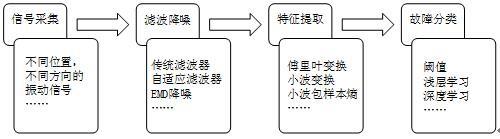
1.本发明涉及工业物联网与数据处理领域,尤其涉及一种应用于旋转机电设备故障源追溯的振动信号采集与处理方法。
背景技术:2.电机驱动的设备在工业生产中占据重要地位,由于大规模生产的流程化作业越来越普遍,每一台旋转机电设备的可靠性都具有重要意义,一旦某台旋转机电设备发生故障,不仅会造成生产环节的中断与巨大的经济损失,而且还有可能引起人员的伤亡,环境的污染以及各种社会问题。旋转机电设备发生故障时,或者设备处于亚健康状态时,设备的异常振动是判断设备能否健康运行的重要指标,现有的对振动信号的监测具有以下几个问题。
3.1.振动传感器灵敏度较低,频率响应较低,采集的是振动的某一段时间的平均值,得到数据的采样频率也低,不能够从细节描述振动的情况。
4.2.对于一台设备,采集的振动信息往往是某个点,在某一个方向的振动情况,数据不够全面,无法通过振动信号检测来准确确定故障发生的位置。
5.3.传统的振动信号监测,对信号的处理不够智能化,需要专业人士对数据进行分析才能确定故障。
技术实现要素:6.本发明针对以上的问题,提出了一种应用于旋转机电设备故障源追溯的振动信号采集与处理方法。该系统采用工业级mems技术加速度传感器,在单台设备多点多方向采集数据,并根据采集数据的量、智能选取特征工程或深度学习的方法对数据进行分析,得到旋转机电设备故障情况。有效的解决以上问题。所采用的技术方案如下:步骤1:采用工业级的mems技术的模拟振动传感器采集振动加速度信号,传感器端带有ad转换模块和数字处理器,信号在传感器端进行信号处理。
7.步骤2:在同一台设备上安装多个振动传感器,组成传感器网络。
8.步骤3:传感器信号的融合和智能分析。
9.本发明进一步包括以下的优选方案:优选的,步骤1所述的信号处理包括模拟信号的处理和数字信号的处理。
10.所述的模拟信号处理利用硬件电路的模拟滤波和信号调理,滤除高于采样频率的噪音信号。
11.所述的数字信号处理主要是对模拟信号进行数字化采样,采样频率设定为旋转机电设备转速频率的8倍。模数转换之后,将采用数字化的滤波方法以及频域分析、主元分析等方法得到信号的高级特征表示。
12.优选的,步骤2中单台设备安装多个振动传感器的方法将根据故障可能发生的点来确定安装传感器数量,一般传感器数量是可能发生故障的点数的2倍,传感器沿着旋转轴轴向分布,每个可能发生故障的点正交安装振动传感器。这样由多个步骤1中的传感器单
元,按照步骤2的安装方法安装之后,就扩展的传感器的网络组成,传感器间通过有线或者无线的通讯方式组成网络,多个传感器的数据将进行汇总、融合分析。
13.优选的,步骤3中传感器信号智能分析将按照如下方法进行分析:结合前面提出的带信号预处理的传感器和多维数据采集,能够使神经网络能够快速学习和识别重要特征。为了增加信号处理的方法更加灵活,本发明提出的方法将根据设备的实际情况,可以在云端,也可以在边缘设备上处理分析数据。同时,他们不仅仅使用深度神经网络,根据项目的实际情况,系统也会选择其他智能算法来解决,比如传统的特征工程与深度学习方法并用,或者在拥有大量数据的情况下,往往选择深度学习方法,当数据量较少的时候,则会选择其他的算法。整个信号分析的过程,不需要专家参与,系统将直接给出设备的诊断报告,指导运行维护人员对设备进行必要的维护工作,既能降低设备停机的可能性,也减少了定期维护的高额费用,将设备的维护有基于时间的维护变成基于运行状态的维护。
14.采取以上技术方案的一种应用于旋转机电设备故障源追溯的振动信号采集与处理方法具有如下有益效果:1.选用工业级mems振动加速度传感器,依赖传感器特有的高灵敏度高频率响应特性,能够提高振动信号的数据量、信噪比,更好地描述旋转机电设备的振动情况。
15.2.使用多个传感器采集振动信息,既能反映振动信号随时间的变化情况,又能反映振动信号沿空间的传播情况,丰富了传感器信息,便于实现传感器数据融合,为后续做基于数据的故障源追溯算法做准备。
16.3.采用智能的信号处理方法,传统方法与深度学习相结合,弥补方法的不足,提高对设备故障源追溯准确度。
17.附图说明:图1是按照发明中的优选实例的多维振动信号采集方法图2是本发明所述的振动信号采集与处理方法具体实施方式:本发明是通过上述的技术方案来实现故障信号的分类,该方法具有一个完整的信号采集与处理的流程。为了使本技术领域的人员更好的理解本发明提出的一种应用于旋转机电设备故障源追溯的振动信号采集与处理方法,下面将结合说明书附图对发明中提到的方法进行具体实施方式的描述。
18.步骤1:采用工业级的mems技术的模拟振动传感器采集振动加速度信号,传感器端带有ad转换模块和数字处理器,信号在传感器端进行信号处理。
19.实施例中,步骤1所述的信号处理包括模拟信号的处理和数字信号的处理。
20.所述的模拟信号处理利用硬件电路的模拟滤波和信号调理,滤除高于采样频率的噪音信号。
21.所述的数字信号处理主要是对模拟信号进行数字化采样,采样频率设定为旋转机电设备转速频率的8倍。模数转换之后,将采用数字化的滤波方法以及频域分析、主元分析等方法得到信号的高级特征表示。
22.步骤2:在同一台设备上安装多个振动传感器,组成传感器网络。
23.步骤2中单台设备安装多个振动传感器的方法将根据故障可能发生的点来确定安
装传感器数量,一般传感器数量是可能发生故障的点数的2倍,传感器沿着旋转轴轴向分布,每个可能发生故障的点正交安装振动传感器。这样由多个步骤1中的传感器单元,按照步骤2的安装方法安装之后,就扩展的传感器的网络组成,传感器间通过有线或者无线的通讯方式组成网络,多个传感器的数据将进行汇总、融合分析。
24.图1是用于振动信号采集的mems振动加速度传感器的安装示意,在本优选实例中,旋转机电设备是以1个单轴旋转的设备为例,可以是电机,也可以是有电机驱动的其他旋转设备。旋转设备的转轴往往通过滚动轴承或滑动轴承与保持架相连接。轴承的内圈和旋转轴装配不当、外圈和轴承座装配不当、杂物进入和润滑不当都会导致轴承的失效,进而导致设备故障瘫痪。由转轴导致的如转轴不平衡、不对中等也会导致设备故障瘫痪。以上这些机械故障,在故障的早期故障点往往是单一的,并且可以通过早期的维护而消除安全隐患的。早期的故障产生时就会产生异常的振动,振动情况既有随时间变化的时间特征,也有沿着机械设备传播的空间特征。图1所示的振动信号采集方法,是通过在不同位置安装多轴振动传感器来捕捉振动信号的时间和空间的特征的。传感器采用工业级的mems振动加速度传感器,在保证传感器可靠性的同时,能够获得更多,更高品质的振动信号。
25.步骤3:传感器信号的融合和智能分析。
26.步骤3中传感器信号智能分析将按照如下方法进行分析:图2所示为振动信号的采集与处理的整体流程图,在完成振动信号的采集之后,将对振动信号进行滤波降噪。滤波降噪后的信号更能反映旋转机电设备的振动状况。对滤波降噪后的信号进行特征提取如采用傅里叶变换、小波变换,得到振动信号的频率特征与不同频带的能量特征,再融合不同位置的传感器,根据已有的故障类型和经验数据,采用阈值判断、浅层学习或深度学习的算法来追溯旋转机电设备的故障源。
27.结合前面提出的带信号预处理的传感器和多维数据采集,能够使神经网络能够快速学习和识别重要特征。为了增加信号处理的方法更加灵活,本发明提出的方法将根据设备的实际情况,可以在云端,也可以在边缘设备上处理分析数据。同时,他们不仅仅使用深度神经网络,根据项目的实际情况,系统也会选择其他智能算法来解决,比如传统的特征工程与深度学习方法并用,或者在拥有大量数据的情况下,往往选择深度学习方法,当数据量较少的时候,则会选择其他的算法。整个信号分析的过程,不需要专家参与,系统将直接给出设备的诊断报告,指导运行维护人员对设备进行必要的维护工作,既能降低设备停机的可能性,也减少了定期维护的高额费用,将设备的维护有基于时间的维护变成基于运行状态的维护。