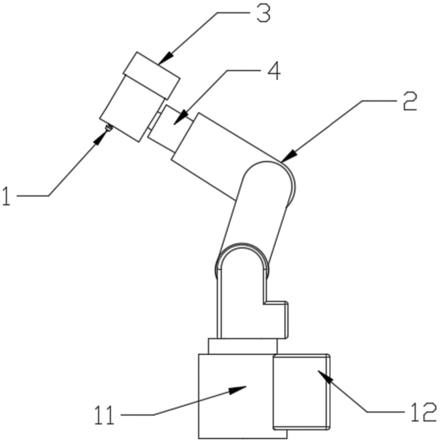
一种基于stft时频分析的车身焊点缺陷检测装置
技术领域
[0001]
本实用新型涉及工业检测领域,具体涉及一种基于stft时频分析的车身焊点缺陷检测装置。
背景技术:[0002]
汽车白车身制造过程中,主要连接工艺是焊接。焊接在汽车制造中发挥着不可替代的重要作用,焊点位置的性能和疲劳强度直接影响汽车的整体性能。在实际生产中不可避免地会出现一些焊接缺陷,致使焊点质量不稳定,严重时将成批出现不合格的焊点,因此汽车出厂时需要对各部分的焊点位置性能进行检测。现有的超声波探伤仪可对全车身焊点进行检测,主要利用焊点与母材晶体结构的差异,通过时域分析观察返回波形来判断焊点质量;但是,这种检测分析方法无法直观捕捉特定频率的衰减情况,需要根据从业人员大量的检验判断,人工时效性低,难以保证检测的准确性。现在有些超声波检测技术采用频域分析,获取的频域函数对应的是整个时间轴,傅里叶变换对频谱的描绘是“全局性”的,能够清楚地获取一整段信号包含的每一个频率的分量值;但是,这种检测分析方法不能反映时间维度局部区域上的特征,难以获取对应于频率域成分的时间信息,缺少时间信息使得傅立叶分析在更精密的分析中失去作用,从而不利于判断焊点的缺陷类型。可见,单从时域分析或频域分析均不能直观地提取出焊点的特征,难以准确分析焊点质量问题。
技术实现要素:[0003]
本实用新型的目的在于克服现有技术中存在的缺点,提供一种基于stft(短时傅里叶变换)时频分析的车身焊点缺陷检测装置,通过利用时域分析、频域分析和时频分析相结合,对超声检测信号进行处理与分析,可以得到较为细致的时频图,准确地对车身焊点进行无损伤的质量检测,解决了现有技术存在的人工时效性低和检测信息不全等技术问题,提高检测准确性,保证焊点检测工作的连续高效性,节约人力物力。
[0004]
本实用新型的目的通过下述技术方案实现:
[0005]
一种基于stft时频分析的车身焊点缺陷检测装置,包括超声波检测模块1、六自由度机器人2、超声波发生器4、超声波探头5、控制模块11和上位机12;所述超声波检测模块1位于六自由度机器人2的上部前方,超声波检测模块1中内置有超声波探头5;所述超声波发生器4位于超声波检测模块1与六自由度机器人2的连接处;所述控制模块11固定于六自由度机器人2的下部前方,所述上位机12固定于六自由度机器人2的下部后方;超声波检测模块1与超声波发生器4相连接,控制模块11分别与六自由度机器人2、超声波检测模块1、超声波发生器4、上位机12相连接。
[0006]
所述控制模块11,是采用arm架构单片机,设有ec20ce-minipcie-c通信模块。
[0007]
所述超声波检测模块1内置有超声波探头5,超声波探头5与超声波发生器4相连接。工作时,超声波发生器4发射超声波至车身焊点,超声波探头5收集焊点反射的超声波信号并传输到控制模板11。
[0008]
优选的,超声波检测模块1采用可变超声波探头设计以适应不同条件下对探头的需求。超声波检测模块1包括超声波探头5、复位弹簧6、旋转盘7、电机8、推杆9、液压缸10、液压泵及液压油储存器3;不同型号大小的超声波探头5通过复位弹簧6与旋转盘7相连并固定于旋转盘7的套筒上,超声波探头5可沿套筒轴向方向移动;所述旋转盘7与电机8通过电机轴相连;所述推杆9置于液压缸10内,可沿液压缸轴向移动,推杆9通过导线与超声波发生器4相连,推杆9上设有导体,当推杆9与超声波探头5的金属导体槽相接触时,超声波发生器与超声波探头电路接通;所述电机8位于超声波检测模块1的外壳内部,并与外壳固定;液压缸10固定在外壳上,并与液压泵相连;所述液压泵及液压油储存器3位于六自由度机器人2的上部后方,并与超声波检测模块1相连接。
[0009]
所述上位机12为数据处理系统,上位机12与控制模块11相连接,能够接受控制模块11的信号;所述上位机12能够进行特定特征的基于数学形态学的机械振动信号降噪方法进行噪声过滤,进行stft(短时傅里叶变换)时频分析以及特征提取。
[0010]
一种基于stft时频分析的车身焊点缺陷检测方法,包括下述步骤:
[0011]
(1)初始化和校准:导入被测车身模型数据,设定控制模块和超声波检测模块的工作参数,进行初始化;校准超声波检测模块;
[0012]
(2)数据采集:控制模块根据被测车身模型数据和工作参数对采样点进行分匹配,输出采样点的空间坐标,控制超声波探头移动至采样点;控制模块根据工作参数,向超声波发生器输出信号,超声波发生器将市电转换成相应的高频交流电驱动换能器,通过放大器后,超声波发生器产生一定频率和振幅的声波信号;然后超声波检测模块收集反射回来的采样点声波信号,并以采样率fs对连续信号进行采样以获取离散采样值,存储为向量组再通过控制模块将收集的声波信号初始数据发送到数据处理系统;
[0013]
(3)信号降噪:数据处理系统对收集的声波信号进行基于数学形态学的机械振动信号降噪;
[0014]
(4)焊点特征提取:数据处理系统对降噪后的声波信号进行stft(短时傅里叶变换)时频分析以及特征提取,获得焊点特征;
[0015]
(5)超声波探头移动至下一采样点,重复步骤(1)-(4),直至历遍所有采样点;数据处理系统根据全部采样点的焊点特征数据,计算全车不合格焊点百分比,并将数据反馈给控制模块。
[0016]
步骤(1)中,所述控制模块和超声波检测模块的工作参数包括采样数、采样频率、超声波发生器所产生声波信号的频率和振幅。
[0017]
步骤(1)中,所述校准超声波检测模块,是将超声波探头移动到质量较好的焊点上,超声波发生器产生声波信号,并通过探头传导至试块,然后探头收集反射回来的声波信号,记录信号并以此为基础校准超声波检测模块。
[0018]
优选的,在数据采集之前,先选择超声波探头。超声波探头的选择过程为:控制模块根据需检测焊点类型,判断当前探头类型是否符合检测需要;若符合,保持不变,继续下面流程工作;若不符合,控制模块向电机发送脉冲信号,电机带动旋转盘转过一定角度后选择相应的超声波探头;当超声波探头随电机转动到达指定位置后,与推杆对齐处于同轴心位置,完成更换超声波探头。
[0019]
步骤(3)中,所述基于数学形态学的机械振动信号降噪,是根据机械振动信号的特
点,采用开—闭和闭—开组合数学形态滤波,处理含噪声的振动信号,重构原始信号,提取出信号特征,消除振动信号噪声。即使原始信号伴随较强的噪声,甚至发生了严重的畸变,其基本形状仍可以被识别和重构及增强。
[0020]
步骤(4)中,所述stft(短时傅里叶变换)时频分析以及特征提取,包括下述步骤:
[0021]
(4-1)读取经过降噪后的声波信号为x(m),对信号使用窗函数w(n-m)进行截取指定长度的短信号进行傅里叶变换,则经过短时傅里叶变换满足以下关系:其中f(n,w)为关于时间n和频率w的二维函数,e-jwm
为关于原声波信号时刻m的指数函数,e为自然常数,j为虚数单位;则对经过有限长度加窗的短信号的离散采样后满足以下关系:时域的采样周期t=1/fs,窗函数截取短信号长度为l,采样点数n为最接近窗函数长度l的2的整数次幂,采样点构成向量组
[0022]
(4-2)数据处理系统将信号分解成一系列指数函数的和,其中变换满足以下关系:1≤k≤n,p(k)为关于第k个元素的函数,x(m)为声波信号,e为自然常数,j为虚数单位,并利用计算当中对称性和周期性,将n个离散采样值分解为原来n/2个采样值,并对剩下的采样值继续进行分解以减少运算量;
[0023]
(4-3)经过快速傅里叶变换后,求解真实幅值,幅值满足以下关系式:3)经过快速傅里叶变换后,求解真实幅值,幅值满足以下关系式:a为关于p(k)的函数,n为采样点数,其中经过快速傅里叶变换后的频率满足以下关系式f为关于第k个采样点的函数;最终系统将这一系列函数转换成三维图像,频率为横轴,时间为纵轴,振幅为立轴;
[0024]
(4-4)数据处理系统对所得采样点时频图的所占比重较大频率和振幅采集主要特征,并记录波形变化时间信息,与正常焊点的时频图进行振幅的对比,判断焊点是否达到标准。
[0025]
本实用新型与现有技术相比具有如下优点和效果:
[0026]
(1)本实用新型的检测方法准确性高,利用超声波反射进行检测和基于stft时频分析,通过数字化分析超声波信号时频关系,提高焊点检测准确性。
[0027]
(2)本实用新型适用性广,通过设置旋转盘来设置不同探头类型,满足更多工作环境需要。
[0028]
(3)本实用新型的装置操作简单,成本低,使用时装置在定点处进行工作,按照设定好的程序进行测试,收集声波进行系统分析,得出焊点是否缺陷的结果,可实现对焊点缺陷的长时间检测。
附图说明
[0029]
图1是一种基于stft时频分析的车身焊点缺陷检测装置主视图。
[0030]
图2是超声波检测模块内部结构图。
[0031]
图3是超声波检测模块内部结构剖视图。
[0032]
图4是超声波检测模块工作状态内部结构图。
[0033]
图5是超声波检测模块工作状态内部结构剖视图。
[0034]
图6是一种基于stft时频分析的车身焊点缺陷检测装置的工作流程图。
[0035]
图中,1、超声波检测模块;2、六自由度机器人;3、液压泵及液压油储存器;4、超声波发生器;5、超声波探头;6、复位弹簧;7、旋转盘;8、电机;9、推杆;10、液压缸;11、控制模块;12、上位机。
具体实施方式
[0036]
下面将结合附图,对本实用新型实施例中的技术方案进行清楚、完整地描述,显然,所描述的实施例仅是本实用新型的一部分实施例,而不是全部的实施例。基于本实用新型中的实施例,本领域普通技术人员在没有做出创造性劳动前提下所获得的所有其他实施例,都属于本实用新型保护的范围。
[0037]
需要说明,若本实用新型实施例中有涉及方向性指示(诸如上、下、左、右、前、后
……
),则该方向性指示仅用于解释在某一特定姿态下各部件之间的相对位置关系、运动情况等,如果该特定姿态发生改变时,则该方向性指示也相应地随之改变。
[0038]
实施例1
[0039]
如图1、图2和图3所示,一种基于stft时频分析的车身焊点缺陷检测装置,包括超声波检测模块1,六自由度机器人2,液压泵及液压油储存器3,超声波发生器4,超声波探头5,复位弹簧6,旋转盘7,电机8,推杆9,液压缸10,控制模块11,上位机12。所述超声波检测模块1位于六自由度机器人2上部前方。所述液压泵及液压油储存器3位于六自由度机器人2上部后方,并与超声波检测模块1相连接。所述超声波发生器4位于超声波检测模块1与六自由度机器人4连接处。所述超声波探头5、复位弹簧6、旋转盘7、电机8、推杆9、液压缸10等内置于超声波检测模块1中,其中不同型号大小超声波探头5与复位弹簧6相连接并置于旋转盘中,旋转盘中心与电机8相连接,推杆9置于液压缸10内,液压缸10与液压泵及液压油储存器3相连接。所述上位机12固定在六自由度机器人2下部后方。
[0040]
机器工作时,控制模块可以控制六自由度机器人到指定工作点处,然后操控机械臂,以进一步带动探头进行作业。
[0041]
如图2和如图3所示,装置不工作时,液压缸10中无液压油,缸内压力小于大气,推杆9被推进液压缸10内。超声波探头5在复位弹簧的作用下被固定在旋转盘套筒内。
[0042]
如图4和图5所示,装置工作时,液压泵工作并将液压油从储存器中泵向液压缸10,推杆9在液压作用下沿着液压缸10轴向移动,推杆9部分被推出液压缸10,当推杆9导体与超声波探头5所设置的金属导体槽接合时,接通超声波探头5与超声波发生器4的电路,超声波探头5开始工作。推杆9在液压作用下克服复位弹簧6的作用力,推动超声波探头5继续向前移动,直至被推出旋转盘7套筒到达限定位置,液压泵维持液压缸压力,使得超声波探头5可以与被测工件稳定接触。
[0043]
当检测过程中需要随时更换超声波探头时,液压泵停止向液压缸供油,液压油从出油口回流至储存器,液压缸10内压力减小,在大气压力作用下,推杆9被推回至液压缸10内,当推杆9导体与超声波探头5所设置的金属导体槽断开接触时,断开超声波探头5与超声波发生器4的电路,超声波探头5停止工作,超声波探头5在复位弹簧6的作用下回到原位。此时旋转盘7与推杆9无接触,可转动。控制模块11向电机8发送脉冲信号,电机8带动旋转盘7转过一定角度后选择相应的超声波探头。当超声波探头随电机8转动到达指定位置后,与推
杆9对齐处于同轴心位置,完成更换超声波探头。
[0044]
如图6所示,超声波探头采集端采集声波信号,将声波信号信息传输至上位机。对于连续信号则以采样率fs采样以获取离散采样值,并存储为向量组上位机对采集到的声波信号进行预处理中,利用基于数学形态学的机械振动信号降噪方法进行噪声比对信号进行处理,通过数学形态变换将一个复杂的信号分解为具有物理意义的各个部分,将其与背景剥离,同时保持信号主要的形状特征,重构原始信号,提取出信号特征,消除振动信号噪声,最大程度降低直流电机与舵机等工作环境带来的噪声。上位机读取经过降噪后的声波信号x(m),对信号使用窗函数w(n-m)进行截取指定长度的短信号进行傅里叶变换,则经过短时傅里叶变换满足以下关系:其中f(n,w)为关于时间n和频率w的二维函数,e-jwm
为关于原声波信号时刻m的指数函数,e为自然常数,j为虚数单位。则对经过有限长度加窗的短信号的离散采样后满足以下关系:时域的采样周期t=1/fs,窗函数截取短信号长度为l,采样点数n为最接近窗函数长度l的2的整数次幂,采样点构成向量组系统将信号分解成一系列指数函数的和,其中变换满足以下关系:系统将信号分解成一系列指数函数的和,其中变换满足以下关系:1≤k≤n,p(k)为关于第k个元素的函数,x(m)为声波信号,e为自然常数,j为虚数单位,并利用计算当中对称性和周期性,将n个离散采样值分解为原来n/2个采样值,并对剩下的采样值继续进行分解以减少运算量。经过短时傅里叶变换后,求解真实幅值。幅值满足以下关系式:变换后,求解真实幅值。幅值满足以下关系式:a为关于p(k)的函数,n为采样点数,其中经过短时傅里叶变换后的频率满足以下关系式1≤k≤n,f为关于第k个采样点的函数。最终数据处理系统将这一系列函数转换成以频率为横轴,时间为纵轴,振幅为立轴的时频图。数据处理系统对所得采样点时频图的所占比重较大频率和振幅采集主要特征,与试块(或正常焊点)的时频图进行波形振幅的对比,判断焊点是否达到标准。标准可由不同试块制定,从而判断不同焊点质量要求。
[0045]
上位机记录焊点合格和焊点不合格的数据以及位置信息,上位机计算处理所有数据后,筛选出其中不合格采样点的位置数据以及整车的焊点合格率,并反馈给控制模块。
[0046]
以上所述仅为本实用新型的实施例,但本实用新型的实施方式并不受上述实施例的限制,其他的任何未背离本实用新型的精神实质与原理下所作的改变、修饰、替代、组合、简化,均为等效的置换方式,都包含在本实用新型的保护范围之内。