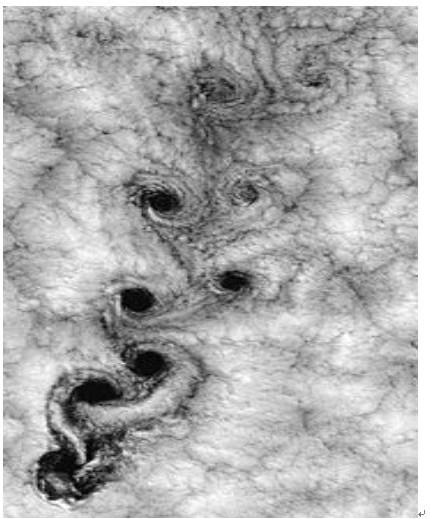
1.本发明涉及超高速粉体加工工艺和气炮实验领域,具体为基于涡街激发整形的超高速粉体管道检测装置。
背景技术:2.在各种化工、发电、炼钢、制药等生产行业以及轻气炮冲击失效等科研领域,超高速粉体(颗粒)的在线检测是一个迄今还未完全解决的难题。在这些工作环境下,粉体的粒度小(如微米量级),强度高,速度快,如在轻气炮冲击力学实验中产生的粉体速度可达几百米甚至上千米每秒。此外,在粉体工业加工领域,加工粉体置于超高速状态下运行时,可以明显提升粉体加工效率。在这些应用环境下,粉体的在线检测是控制粉体加工效果至关重要的一环。
3.但现有的粉体在线检测装置只在粉体处于低速时才能有效运行,如运行速度几十米每秒的粉体。现有的对加工粉体检测方式这样进行:将高速加工粉体装置停下来之后,通过手动取样装置将粉体从管道内取出,再送至化验室进行分析,如:2017年张学平发明的一体式化工粉末取样探针,在取样时采用手动方式将取样探针向上抽出以完成取样(申请号201720186169.x),取样后再将样品转移到常用检测设备上进行人工检测。
4.此外,现有的自动取样检测方法,如2013年毛明等人在与四通管相互垂直的出样管内设置气缸,在气缸的作用下,取样杆产生回程往复运动,从而完成取样,由此代替人工取样(申请号201320782997.1);在这样的检测过程中,仍是取到粉体样品后再转移到常用检测设备上进行人工检测,同样无法实现在线粒径检测。
5.以上两种取样装置都不能用于超高速粉体在线检测,其原因是在实际生产过程中,超高速运动的微米粉体都具有较大的强度和动能,很容易直接将设置在超高速加工管道内的检测或采样装置击碎。
6.因此,针对超高速粉体在线收集和检测,采用现有的停机手动或自动取样的检测方法存在以下缺点。
7.(1)操作过程复杂繁琐,费时费力。(2)采集到的粉体数据无法直接反馈控制实时生产加工或生产流程,检测结果时间滞后,不利于指导生产和实验。
技术实现要素:8.本发明的目的是为了实现对持续运行的用于工业生产管道中超高速粉体的降速和在线检测,能够在保证粉体加工装置持续运行的前提下对超高速粉体的粒径等参数进行有效检测。
9.本发明的技术方案是,通过在超高速粉体管道中设置特制的涡街激发整形器,降低管内流动的气体-粉体混合物速度之后再进行有效检测。具体做法是将原本沿着管道方向呈直线超高速行进的粉体与流线型的涡街激发整形器作用后,形成卡门涡街,速度大幅下降。之后通过簧形阻体捕获降速之后的粉体,最终粉体落入凹槽中,被激光粉体在线检测
装置检测,从而实现在线检测目的。
10.整体装置包括前后两根管套合组成,用来保证涡街粉体完整有效捕获,两管之间通过电动滑动导轨连接。
11.管一内设置四组涡街激发整形器,一个簧形阻体,四个凹槽和四组激光发射头、激光传感器;管外设置用于控制涡街激发整形器金属板升降的板簧;管二内设置另一组簧形阻体,四个凹槽和对应的四组激光发射头、激光传感器。由于粉体直径有大有小,一些较细、较轻的粉体形成的涡街距离激发整形器较远,会错过管一中的簧形阻体,而被管二中的簧形阻体捕获。
12.所述的四组涡街激发整形器设置在管一的前端,每组由五块紧邻的,可单独控制升降的高强度纳米陶瓷板或金属板组成。
13.板呈片状,向后倾斜,整体组成鱼头流线形状;(设置成此形状可以增加粉体-气体混合物与涡街激发整形器的摩擦作用时间,降低粉体-气体混合物对涡街激发整形器的冲力)。板内有一根固定的铁钉与管外的板簧卷曲装置连接。涡街激发整形器部分嵌入管壁中,其弧状的头部在管道内露出,尾部延伸至管道外。
14.在涡街激发整形器中每块板尾部设有板簧卷曲装置,用于控制涡街激发器中金属板的升降,卷曲装置包括一块卷曲的金属条和两组带齿轮的板簧马达。
15.金属条形状长度略小于管外壁周长,金属条的两端外侧有一段齿槽,与板簧马达上的齿轮齿合。板簧马达启动时,金属条围成的圆圈半径可变。
16.金属条上与涡街激发整形器的金属板下端对应位置处开槽,槽内有一根与涡街激发整形器中金属板相连的铁钉,依靠组合螺帽,铁钉尾部可以沿槽滑动,随之金属板可以升降。
17.所述两根管内的簧形阻体都设置在管道中段,分为管内部分和管外部分,整体呈螺线状;阻体由高强度的粗金属线绕旋而成,兼具高强度和一定弹性。管内阻体位于凹槽的斜上方。阻体的一端固定在外壁,另一端固定在弹簧马达的转轴上,弹簧马达转动控制调整阻体的尺寸,以便有效捕获粉体。
18.所述管一和管二内的凹槽位于各个涡街激发整形器正后方,簧形阻体的斜下方,每个凹槽到涡街激发整形器的距离都不同,整体近似螺线分布,可确保对不同间距涡街的采集效果。凹槽内设有激光发射头和激光传感器,用于检测粉体的粒径大小参数。每个凹槽都有一个进口和一个出口,以便粉体在进入凹槽被检测后能够再次回到后续加工工艺中。
19.激光粉体检测装置包括激光发射头、激光传感器、光电信号转换系统,信号处理系统和反馈控制系统。其中的激光发射头和激光传感器设置于凹槽的后半段靠近出口处,此位置粉体浓度最大,可以被激光传感器有效探测。激光发射头和激光传感器分别固定于槽道上下开设的暗仓中。光电信号转换系统、信号处理系统和反馈控制系统置于管道外。
20.本发明提供的基于涡街激发整形的超高速粉体管道检测装置,有益技术效果为。
21.(1)有效降低粉体速度,检测即时进行,实现了超高速粉体的在线检测。
22.(2)涡街形状可控,装置可用于气炮冲击的科学实验;采集到的粉体数据可以直接反馈控制实时生产加工或生产流程。为粉体超高速冲击过程中加工效果的即时检验奠实基础。
23.(3)避免了超高速粉体对取样和检测装置的直接冲击破坏结果。装置可以安装在
超高速粉体加工流程中持续工作。
24.(4)通过两级捕获设置,可以实现对轻重两种粉体的检测。
附图说明
25.图1是卡门涡街现象示意图。
26.图2是本发明的平面示意图。
27.图3是本发明的部分剖面图。
28.图4是本发明的涡街激发整形器结构示意图,其中(a)为主视图,(b)为左视图,(c)为俯视图,(d)为立体效果图。
29.图5是本发明的板簧卷曲装置结构示意图,其中(a)为左视图,(b)为连接涡街激发整形器的板簧主视图。
30.图6是本发明的板簧卷曲装置开槽部分结构示意图,其中(a)为主视图,(b)为立体示意图。
31.图7是本发明的簧形阻体平面示意图。
32.图8是本发明管道壁内设置的凹槽结构示意图,其中(a)为上(下)凹槽立体示意图,(b)为左(右)凹槽立体示意图。
33.图9是本发明的激光发射头和激光传感器安装示意图,其中(a)为上(下)凹槽内的激光发射头和激光传感器安装平面示意图,(b)为左(右)凹槽内的激光发射头和激光传感器安装立体示意图。
34.图10是本发明的工作原理图,其中(a)为涡街激发示意图,(b)为涡街激发整形器的形状改变对涡街间距和大小影响的效果图。
35.图11是本发明的工作流程图。
36.图中所有结构编号:1-涡街激发整形器,2-光电信号导线,3-电动滑动导轨,4-板簧卷曲装置,5-簧形阻体,6-上凹槽,7-左(右)凹槽,8-下凹槽,9-金属或纳米陶瓷板,10-升降位置铁钉,11-六角螺帽,12-金属条,13-开槽,14-电机转轴上的齿轮,15-齿槽,16-弹簧马达,17-用于容纳金属丝的管壁开孔,18-暗仓,19-激光发射头,20-激光传感器,21-管一,22-管二, 23-板簧马达,24-导轨马达,25-光电转换放大系统,26-信号处理系统,27-反馈控制系统。
具体实施方式
37.下面结合附图对本发明作进一步的说明。
38.如图1所示,为典型的卡门涡街形成图,通过涡街激发整形器后的粉体产生的卡门涡街现象与此类似。
39.如图2、图3所示,基于涡街激发整形的超高速粉体管道检测装置,由管一21和管二22两大部分套合组成,两根管道由电动滑动导轨3相连。四组电动滑动导轨3呈上下左右对称形状分布,固定在管一21末端外壁上,管二22前端的内壁与电动滑动导轨3相对应位置有形状契合的轨道,迫使两根管道只能沿长度方向变化而不能相对转动。导轨马达24带动管二22沿导轨3滑动时,管二22内壁上的收集粉体的凹槽6、7、8与涡街激发器1的距离随之发生变化。管一21内包括四组涡街激发整形器1,一个簧形阻体5,四个凹槽6、7、8,四组激光发
射头19和激光传感器20;管一21外设置五组板簧卷曲装置4,用于控制涡街激发整形器中的每块金属板9露头部位在管一21内的升降高度;管二22内包括簧形阻体5,四个凹槽6、7、8和对应的四组激光发射头19和激光传感器20。
40.如图4所示,涡街激发整形器1一部分嵌入管壁中,每组涡街激发整形器1由五块相邻的,可单独升降控制的板9组成;板9由高强度纳米陶瓷或金属加工而成;板9整体向后倾斜,头部形状呈弧状,头部露于管道内,尾部延伸至管道外;五块板在管道内的露头整体组成鱼头形状,设置成这种形式可以有效降低超高速粉体露头的冲击。板9尾部中间嵌有一根铁钉10,铁钉倾斜角度与板9倾斜角度一样,以保证板9中相邻两块可以平行倾斜滑动而不会卡住;铁钉10在管外尾端固定有两枚六角螺帽11;两枚螺帽11间夹有金属条12。
41.如图5,板簧卷曲装置4由一块环状金属条12和两组转轴上带齿轮15的板簧马达23构成。金属条12由富弹性,高韧性的金属材料加工而成;呈半闭合的圆弧状,长度略小于管外壁的周长,呈薄片状,便于改变其形状;金属条12两端外侧设有一段齿槽15,可与板簧马达23上的齿轮14齿合。
42.如图6,金属条12上开槽13,内壁光滑,内置铁钉10,铁钉10由螺帽11固定,使其只能在开槽内滑动。当板簧马达23启动,齿轮14带动金属条12两端向内收缩或向外扩张,由此推动位于内侧或外侧的螺帽11,使得铁钉10带动板9向上或向下运动,从而实现涡街激发器1中同一位序的板9在管一内21内露头部位的升降。
43.如图7,簧形阻体5分为管内部分和管外部分,采用金属线缠绕成类似弹簧形状制成,整体呈螺线状与管壁贴合。管内部分固定在对应凹槽6、7、8的斜上方;管壁内置圆孔17,孔径大于环状金属线直径,圆孔与金属线接触端面圆角,便于金属线在孔内的进出。
44.簧形阻体5一端固定在管壁外,另一端穿出管壁固定在弹簧马达16转轴上,弹簧马达启动时,拉动(放松)金属线,则在管内部分的缠度和直径随之发生变化,由此调得金属线环状直径与涡街直径相近,此时粉体捕获效果最佳。
45.如图8所示,每个凹槽6、7、8都有一个进口和一个出口,进口和出口的边角圆滑,左右凹槽7的出口高度低于进口高度,以便粉体在进入凹槽后能够再次回到后续工艺中,每个凹槽到涡街激发整形器的距离都不同,整体近似螺线分布,可确保对不同间距的涡街的采集效果。凹槽出口小,进口大,这样设计可以进一步降低粉末速度,增加粉体浓度,利于检测。
46.如图9所示,激光发射头19和激光传感器20在各凹槽后半段靠近出口处,分别固定于凹槽内壁开设的暗仓18中。
47.下面结合图10对整个装置的工作原理进行叙述。
48.如图10(a)所示,管道内的超高速粉体在经过涡街激发整形器1后降速,形成间距依次增大的球状涡街继续向前运动,球状涡街的间距和大小都可以通过调节涡街激发整形器1的形状来改变。当这些球状涡街与簧形阻体5相遇时,涡街外层粉体就会被簧形阻体5捕获,由此进一步降速后落入后方凹槽6、7、8中并被布置在凹槽内的激光粉体检测探头识别分析。如图10(b)所示,涡街激发整形器1的整体形状决定了涡街形状(包含涡街外部直径大小、涡街上的粉体浓度等)以及涡街与激发整形器1之间的距离;由此实现对涡街形成过程的控制。
49.下面结合图11对超高速粉体的检测流程进行叙述。
50.管道内的超高速粉体进入管一21,经过涡街激发整形器1形成球状涡街,若未形成球状涡街,则通过反馈控制系统27启动板簧马达23,逐次控制板9在管一21内露头的高低,调节整形器1的整体形状,直到产生球状漩涡为止。
51.形成的球状涡街沿管一21内壁继续前进,与管一21内的簧形阻体5相遇碰撞,涡街外层粉体被簧形阻体5捕获,落入凹槽6、7、8中。若激光传感器20收集的信号较弱,则通过反馈控制系统27启动弹簧马达16控制簧形阻体5,改变簧形阻体5与涡街碰撞的有效圈数和中心直径,启动板簧马达23微调涡街激发整形器1的整体形状,直至管一21内的激光传感器20信号达到最强。
52.一些较细、较轻的粉体形成的涡街会经过管一21,进一步前行进入管二22,并被管二22内的簧形阻体5捕获,落入后方的凹槽中,若管二22内的激光传感器20收集的信号较弱,则通过反馈控制系统27启动导轨马达24,控制导轨3滑动,由此改变管二22中簧形阻体5离涡街激发整形器1之间距离、同时改变簧形阻体5与涡街碰撞的有效圈数和中心直径,直至信号达到最强。