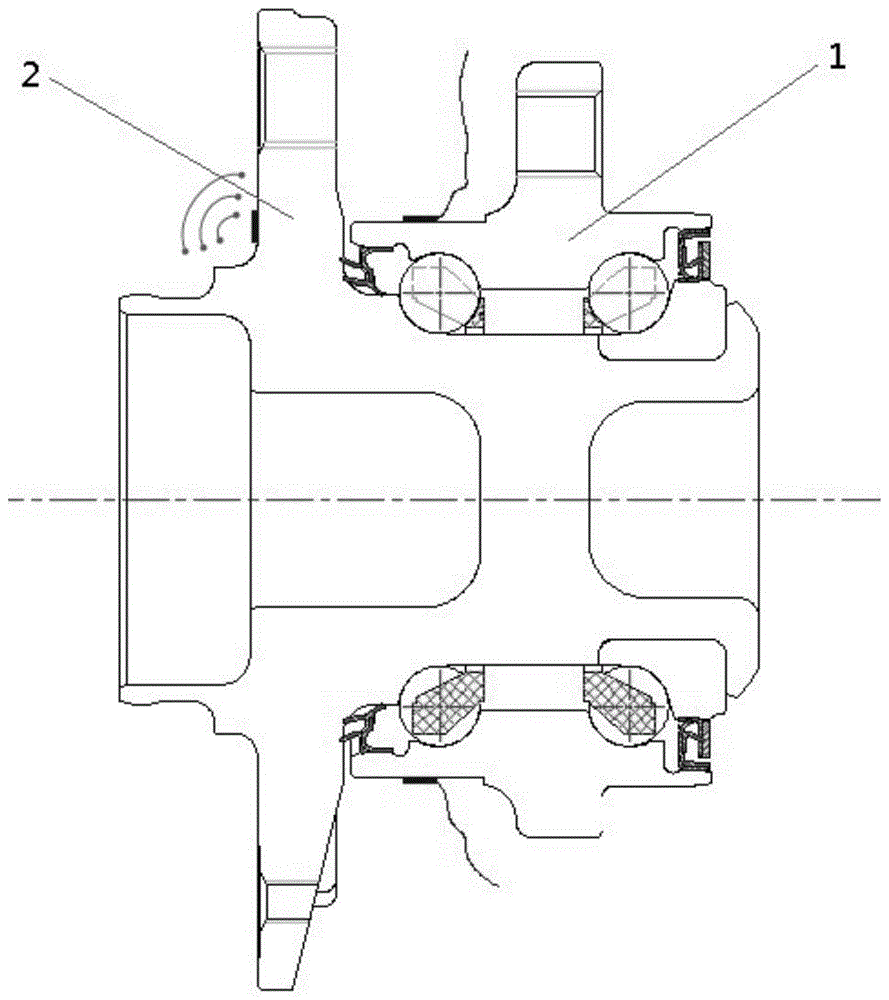
本发明涉及轮毂轴承的领域,具体涉及一种轮毂轴承动态试验台的应变对标方法。
背景技术:
:动态试验台是模拟轮毂轴承在实际驱动与承载条件下的试验系统。应变是指因材料承受载荷状态下所引起的变形描述。随着汽车技术的发展,对轮毂轴承性能试验结果的准确性关注度日益提高,传统的对试验台架上的载荷传感器进行每年校准1次的校准方法较难保证试验结果的准确性,主要是因为试验样品上的受力是按照“加载缸-载荷传感器-加载臂-试验样品”这个路径传递至试验样品上,即使保证了载荷传感器的准确,但受到从载荷传感器至试验样品之间有一个加载臂的传递环节影响,也会影响实际受力效果。因此,两个动态试验台即使保证了其载荷传感器加载载荷是相同的,但试验寿命结果也会千差万别,无法确定影响寿命的因素。技术实现要素:本发明的目的在于克服现有技术存在的不足,而提供一种轮毂轴承动态试验台的应变对标方法。本发明的目的是通过如下技术方案来完成的:这种轮毂轴承动态试验台的应变对标方法,主要包括以下步骤:1)应变型标准样品的制作:选择一个由外圈和法兰构成的轮毂轴承单元,对外圈外表面的六个区域位置做打磨处理,然后采用空气固化胶水分别把应变片a、应变片b、应变片c、应变片d、应变片e、应变片f粘贴于外圈表面,粘贴的方位保持在竖直方向上,车轮竖直线方向上布置的分别是应变片b与应变片e号应变片,竖直线两侧分别对称布置应变片a、应变片c和应变片d、应变片f,在法兰端面圆周方向上每隔120°的三个区域进行打磨,然后采用空气固化胶水,分别把应变片g、应变片h、应变片i粘贴于被打磨三个区域上,应变片g、应变片h、应变片i旁分别连接安装集成供电与信号发生器a、集成供电与信号发生器b、集成供电与信号发生器c进行供电测量与信号发出;2)测试工装匹配与载荷谱制定,主要包括以下步骤:a)选择所需要对标的试验机进行工装设计与制作,制作出主轴连接盘、法兰连接盘、外圈连接盘、l型加载臂,把主轴连接盘与试验机的主轴连接锁紧,把法兰连接盘与主轴连接盘连接锁紧,把法兰连接盘与法兰连接锁紧,把外圈连接盘与外圈连接锁紧,把外圈连接盘与l型加载臂连接锁紧,完成一个试验总成的安装;b)编制一个标准型的试验载荷谱,结合现有乘用车的一般行驶特征,选定一个乘用车的典型车型参数,制定的载荷条件;c)进行相关参数的调整,调整出试验机的加载中心,满足对载荷条件中的加载半径r与加载偏距e的实现,同时,按照载荷条件中的参数输入对标的试验机软件程序中,包括转速、径向载荷fr、轴向载荷fa、持续时间,对应变片a、应变片b、应变片c、应变片d、应变片e、应变片f、应变片g、应变片h、应变片i采用电桥接线,做出相应的信号接收器的硬件匹配,并引入数采模块,再由数采模块把信号传输进入工控机进行数据存储;3)测试实施:启动所需要对标的试验机、数采模块、工控机,三者同时工作,把载荷条件中每个步骤载荷条件下的应变数据采集下来,使用同一应变型标准样品,对两台、多台试验机按照载荷条件进行测试,分析不同试验机之间的应变差异;4)数据分析评估:定义所测试的一台试验机为标准应变,其他试验机均为非标应变,采用了八个载荷步骤,则把其中一台试验机标准应变定义为:y11、y12、y13……y18,进一步其他非标试验机的应变分别为:第1台非标试验机的应变:y21、y22、y23……y28,……第n台非标试验机的应变:yn1、yn2、yn3……yn8,根据所采集的应变数据,对非标试验台与标准试验台在每个载荷条件下应变的相对误差pn1、pn2、pn3……pn8计算出来,如下:至此,把每一载荷步骤的应变误差计算出来,并判断是否满足误差绝对值≤5%。所述外圈和法兰上的摩擦区域表面粗糙度控制在ra0.8以内。所述载荷条件参数包括侧向加速度、转速、径向载荷fr、径向载荷fa、加载半径r、加载偏距e、持续时间。本发明的有益效果为:本发明用于对比评价两台或多台试验台在相同加载载荷下的应变差异,直接采用终端样件应变的测量评估方式,充分考虑了从载荷传感器到加载臂、连接紧固件之间的传递问题,从而评估不同试验台对产品动态寿命试验的影响程度,也便于深入分析影响原因,为两个或多个试验台的动态寿命差异提供了有效的分析手段。附图说明图1为本发明的应变型标准样品结构示意图。图2为本发明的法兰上应变片布置示意图。图3为本发明的外圈上应变片布置示意图。图4为本发明的工装与加载匹配示意图。图5为本发明的实施例2的应变片g输出结果示意图。附图标记说明:外圈1、法兰2、应变片a31、应变片b32、应变片c33、应变片d34、应变片e35、应变片f36、应变片g41、应变片h42、应变片i43、集成供电与信号发生器a51、集成供电与信号发生器b52、集成供电与信号发生器c53、应变型标准样品5、主轴连接盘6、法兰连接盘7、外圈连接盘8、l型加载臂9。具体实施方式下面将结合附图对本发明做详细的介绍:实施例1:如附图所示,这种轮毂轴承动态试验台的应变对标方法,主要包括以下步骤:1)应变型标准样品5的制作:如附图1所示,选择一个由外圈1和法兰2构成的轮毂轴承单元,对外圈1外表面的六个区域位置做打磨处理,使得表面粗糙度控制在ra0.8以内,然后采用空气固化胶水(如502胶水)分别把应变片a31、应变片b32、应变片c33、应变片d34、应变片e35、应变片f36粘贴于外圈1表面,外圈1在轮毂轴承工作中是非旋转零件,粘贴的方位保持在竖直方向上,车轮竖直线方向上布置的分别是应变片b32与应变片e35号应变片,竖直线两侧分别对称布置应变片a31、应变片c33和应变片d34、应变片f36,外圈1在轮毂轴承工作中是非旋转零件,在工作中可采用有线式应变片,进行应变信号的测量,当然也可采用无线式应变部件,法兰2是旋转零件,带动制动盘与车轮一起旋转,在法兰2端面圆周方向上每隔120°的三个区域进行打磨,使得表面粗糙度控制在ra0.8以内,然后采用空气固化胶水(如502胶水)分别把应变片g41、应变片h42、应变片i43粘贴于被打磨三个区域上,由于法兰盘2在轮毂轴承工作中是旋转零件,应变片g41、应变片h42、应变片i43旁分别连接安装集成供电与信号发生器a51、集成供电与信号发生器b52、集成供电与信号发生器c53进行供电测量与信号发出,至此完成对应变型标准样品5的制作;2)测试工装匹配与载荷谱制定,主要包括以下步骤:a)如附图4所示,选择所需要对标的试验机进行工装设计与制作,制作出主轴连接盘6、法兰连接盘7、外圈连接盘8、l型加载臂9,采用螺栓把主轴连接盘6与试验机的主轴连接锁紧,采用螺栓把法兰连接盘7与主轴连接盘6连接锁紧,采用螺栓把法兰连接盘7与法兰2连接锁紧,采用螺栓把外圈连接盘8与外圈1连接锁紧,采用螺栓把外圈连接盘1与l型加载臂9连接锁紧,完成一个试验总成的安装;b)编制一个标准型的试验载荷谱,作为试验机动态运行对标测试的前提条件,也是九组应变测试的载荷条件,结合现有乘用车的一般行驶特征,选定一个乘用车的典型车型参数,制定的载荷条件如下表1:表1对标测试参数c)如图4所示,进行相关参数的调整,调整出试验机的加载中心,满足对表1中的加载半径r与加载偏距e的实现,同时,按照表1中的参数输入对标的试验机软件程序中,包括转速、径向载荷fr、轴向载荷fa、持续时间,对应变片a31、应变片b32、应变片c33、应变片d34、应变片e35、应变片f36、应变片g41、应变片h42、应变片i43采用电桥接线,做出相应的信号接收器的硬件匹配,如其中的应变片a31、应变片b32、应变片c33、应变片d34、应变片e35、应变片f36为有线式,通过引线引入数采模块,再由数采模块把信号传输进入工控机进行数据存储,应变片g41、应变片h42、应变片i43的信号被其对应的集成供电与信号发生器a51、集成供电与信号发生器b52、集成供电与信号发生器c53发出也被数采模块所接收,进入工控机存储;3)测试实施:启动所需要对标的试验机、数采模块、工控机,三者同时工作,把表1中八个步骤载荷条件下的应变数据采集下来,因为是对标测试,使用同一应变型标准样品5,对两台、多台试验机按照表1中八步载荷进行测试,分析不同试验机之间的应变差异,对两台、多台试验机进行测试,规避了样品差异或粘贴应变片方向上的误差导致较难评估试验机的差异;4)数据分析评估:定义所测试的一台试验机为标准应变,其他试验机均为非标应变,为此,因采用了八个载荷步骤,把其中一台试验机标准应变定义为:y11、y12、y13……y18,进一步其他非标试验机的应变分别为:第1台非标试验机的应变:y21、y22、y23……y28,……第n台非标试验机的应变:yn1、yn2、yn3……yn8,根据所采集的应变数据,对非标试验台与标准试验台在每个载荷条件下应变的相对误差pn1、pn2、pn3……pn8计算出来,如下:至此,把每一载荷步骤的应变误差计算出来,按照试验机的开发规范要求,需要满足误差绝对值:≤5%,因此,对pn1、pn2、pn3……pn8的评估,需要满足均小于≤5%,才认为是可接受的,否则,若所对标的非标试验台测试应变误差大于5%,认为该试验台是不可接受的,需要进行调查分析原因,并调整直至≤5%。实施例2:采用本发明方法,分别进行1台标准试验台与1台非标试验台的测试,选取8个载荷步骤中的第6步的进行测试采集数据的分析评估,在第6步条件下:外圈1为非旋转零件,其上6个应变片输出的结果如下表2:表2外圈1应变输出结果表应变片编号标准试验台应变(μeps)非标试验台应变(μeps)相对误差(%)评价311932024.3ok322652691.5ok331861944.4ok34-123-120-3.2ok35-242-239-1.2ok36-133-129-3.0ok法兰2属于旋转零件,其上3个应变片的输出结果均为正弦曲线,如附图5所示的应变片g41的信号输出结果图。对产品动态疲劳寿命影响主要来源于应变幅值,取正弦曲线的峰谷值进行评估,法兰2上3个应变片输出的结果如下表3:表3法兰2应变输出结果表应变片编号标准试验台应变(μeps)非标试验台应变(μeps)相对误差(%)评价41-峰值453449-0.9ok41-谷值-452-437-3.3ok42-峰值4564611.1ok42-谷值-454-4672.9ok43-峰值4504592.0ok43-谷值-453-4581.1ok根据以上对9个应变片在标准试验台与非标试验台上第6步的测试结果可知,误差绝对值均小于5%,满足要求。可以理解的是,对本领域技术人员来说,对本发明的技术方案及发明构思加以等同替换或改变都应属于本发明所附的权利要求的保护范围。当前第1页12