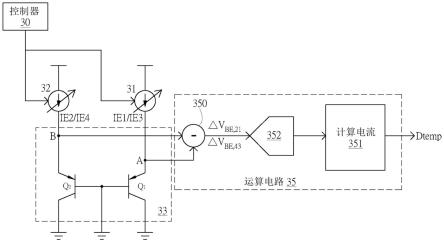
1.本发明与温度感测有关,尤其是关于一种温度感测装置及其运作方法。
背景技术:2.对于任何具有温度感测功能的集成电路而言,其生产过程均需对基准温度-基准电压进行修整(trim)以确保温度感测结果正确。此类晶圆在封装前测试/封装后测试(cp/ft)阶段需先得知晶片的内部温度,以利修整流程的进行。
3.现有的方法是在密封舱内将晶圆加热至预设温度并测量代表所述预设温度的感测电压。然而,通过此方法仅能测量到整片晶圆的温度而无法分别得知各晶片的准确温度,并且容易受到环境温度及设备影响而导致各晶片的温度不均,使得同一晶圆上的各晶片之间可能存在着10~20%的误差,因而影响后续修整的准确度。
4.为了克服前述问题,如图1所示,现有技术在每个晶片中配置具有电压校正(voltage calibration)功能的温度感测电路,通过让同一晶圆上的各晶片分别送出代表其内部温度的感测电压δv
be
来得知各晶片的内部温度。电压感测的公式为:
[0005][0006][0007]
t为温度,η与k为常数,β为元件特性参数。
[0008]
然而,随着半导体元件工艺的进步,图1的温度感测电路中的第一晶体管q1及第二晶体管q2的工艺参数会影响感测电压差δv
be
,亦即流经晶体管q1、q2的电流i
e1
、i
e2
与晶体管q1、q2的元件特性参数(β值)为非线性关系,进而影响温度感测电路的精准度。尤其是β值随着元件工艺的演进而有愈来愈低的趋势(β值约为1),导致前述非线性效应已无法忽略。
技术实现要素:[0009]
有鉴于此,本发明提出一种温度感测装置及其运作方法,以有效解决现有技术所遭遇到的所述问题。
[0010]
依据本发明的一具体实施例为一种温度感测装置。于此实施例中,温度感测装置包括第一电流源、第二电流源、测量电路、运算电路以及控制器。测量电路分别耦接第一电流源与第二电流源。运算电路耦接测量电路。控制器耦接第一电流源与第二电流源,且于第一时间控制第一电流源与第二电流源分别提供第一电流与第二电流至测量电路,以得到第一电压差,并于第二时间控制第一电流源与第二电流源分别提供第三电流与第四电流至测量电路,以得到第二电压差。运算电路依据第一电压差与第二电压差得到误差值。第一电流与第二电流的比值等于第三电流与第四电流的比值。
[0011]
于一实施例中,运算电路还将第一电压差减去误差值以得到温度感测电压。
[0012]
于一实施例中,测量电路包括第一晶体管及第二晶体管。第一晶体管耦接第一电流源,且第一晶体管与第一电流源之间具有第一节点。第二晶体管耦接第二电流源,且第二晶体管与第二电流源之间具有第二节点。运算电路耦接第一节点与第二节点,且运算电路通过第一节点及第二节点的电压来分别获得第一电压差及第二电压差。
[0013]
于一实施例中,运算电路包括减法电路及计算电路。减法电路分别耦接第一节点及第二节点,计算电路耦接减法电路,以依据第一电压差与第二电压差得到误差值。
[0014]
于一实施例中,运算电路包括减法电路及计算电路。减法电路分别耦接第一节点及第二节点。计算电路耦接减法电路,以依据第一电压差与第二电压差得到误差值。
[0015]
于一实施例中,第一电流与第二电流的比值及第三电流与第四电流的比值均小于100。
[0016]
依据本发明的另一具体实施例为一种温度感测装置运作方法。于此实施例中,温度感测装置包括测量电路,分别耦接第一电流源及第二电流源。运作方法包括:(a)于第一时间控制第一电流源与第二电流源分别提供第一电流及第二电流至测量电路,以得到第一电压差;(b)于第二时间控制第一电流源与第二电流源分别提供第三电流及第四电流至测量电路,以得到第二电压差;以及(c)根据第一电压差及第二电压差得到误差值。第一电流与第二电流的比值等于第三电流与第四电流的比值。
[0017]
于一实施例中,运作方法还包括:(d)将第一电压差减去误差值,以得到温度感测电压。
[0018]
于一实施例中,测量电路包括第一晶体管及第二晶体管。第一晶体管的第一端与第一电流源之间具有第一节点,第二晶体管的第一端与第二电流源之间具有第二节点。运作方法还包括:通过第一节点及第二节点的电压来分别获得第一电压差及第二电压差。
[0019]
于一实施例中,步骤(c)还包括:将第一电压差与第二电压差转换为数字信号。
[0020]
于一实施例中,第一电流与第二电流的比值以及第三电流与第四电流的比值均小于100。
[0021]
相较于现有技术,本发明的温度感测装置及其运作方法根据于不同时间提供的具有相等电流比例、不同电流密度的两组输入电流取得非线性误差值来作为补偿值,可达到下列功效/优点:
[0022]
(1)在不大幅修改现有电路的前提下,能够有效提高温度测量的精确度;
[0023]
(2)无须复杂的电路,故能有效降低电路成本及设计复杂度;
[0024]
(3)无须考虑晶体管的元件特性(即β值)的影响,故可适用于各种工艺生产的元件;
[0025]
(4)温度感测装置中的两个晶体管元件不需彼此匹配,故可降低工艺成本并提高电路设计灵活度;以及
[0026]
(5)不限制使用于封装前测试/封装后测试(cp/ft),亦适用于一般温度感测过程,随时提供温度校正。
[0027]
关于本发明的优点与精神可以通过以下的发明详述及所附附图得到进一步的了解。
附图说明
[0028]
图1为传统的温度感测电路的示意图。
[0029]
图2为依据本发明的一实施例的温度感测装置的示意图。
[0030]
图3为电压及电流于第一时间及第二时间的时序图。
[0031]
图4为模拟本发明的温度感测装置在25℃下之相同m值(m=5)的不同电流基准值(i
e1
=1、2、4μa)相对应的温度感测结果。
[0032]
图5为模拟本发明的温度感测装置在85℃下之相同m值(m=5)的不同电流基准值(i
e1
=1、2、4μa)相对应的温度感测结果。
[0033]
图6为本发明的另一实施例中的温度感测装置运作方法的流程图。
[0034]
主要元件符号说明:
[0035]iref
...参考电流
[0036]
m...比值
[0037]
n...比值
[0038]
q1...第一晶体管
[0039]
q2...第二晶体管
[0040]vbe1
...第一电压
[0041]vbe2
...第二电压
[0042]
δv
be
...感测电压差
[0043]ie1
...第一电流
[0044]ie2
...第二电流
[0045]
δv
err
...误差值
[0046]
err...温度误差
[0047]
t...测量温度
[0048]
η...常数
[0049]
3...温度感测装置
[0050]
30...控制器
[0051]
31...第一电流源
[0052]
32...第二电流源
[0053]
33...测量电路
[0054]
35...运算电路
[0055]
350...减法电路
[0056]
351
…
计算电路
[0057]
352...模拟数字转换电路
[0058]
a、b
…
节点
[0059]
dtemp...校正后的温度感测值
[0060]
t1...第一时间
[0061]
t2...第二时间
[0062]ie3
...第三电流
[0063]ie4
...第四电流
[0064]vbe3
...第三电压
[0065]vbe4
...第四电压
[0066]
δv
be,21
...第一电压差
[0067]
δv
be,34
...第二电压差
[0068]n21
...比值
[0069]n43
...比值
[0070]
to...未修正的测量温度
[0071]
s10~s14...步骤
具体实施方式
[0072]
现在将详细参考本发明的示范性实施例,并在附图中说明所述示范性实施例的实例。在附图及实施方式中所使用相同或类似标号的元件/构件是用来代表相同或类似部分。
[0073]
依据本发明的一具体实施例为一种温度感测装置。于此实施例中,温度感测装置具有电压校正(voltage calibration)功能,其可通过在不同时间提供具有相等电流比例、不同电流密度的两组输入电流来校正感测电压,以消除因晶体管元件特性参数(β值)的非线性效应所导致的误差,进而提供正确的温度感测结果。如图2为此实施例中的温度感测装置的功能方块图。
[0074]
如图2所示,温度感测装置3包括控制器30、第一电流源31、第二电流源32、测量电路33及计算电路35。控制器30分别耦接第一电流源31与第二电流源32。第一电流源31与第二电流源32通过第一节点a及第二节点b耦接测量电路33。测量电路33耦接运算电路35。
[0075]
于一实施例中,第一电流源31与第二电流源32是可变电流源,控制器30控制第一电流源31与第二电流源32,以于不同时间提供不同大小的电流,但不以此为限。
[0076]
于第一时间,控制器30控制第一电流源31提供第一电流i
e1
至测量电路33以及控制第二电流源32提供第二电流i
e2
至测量电路33,以使测量电路33进行第一次测量而在第一节点a与第二节点b之间得到第一电压差δv
be,21
。于第二时间,控制器30控制第一电流源31提供第三电流i
e3
至测量电路33以及控制第二电流源32提供第四电流i
e4
至测量电路33,以使测量电路33进行第二次测量而在第一节点a与第二节点b之间得到第二电压差δv
be,43
。在第一时间提供至测量电路33的第一电流i
e1
与第二电流i
e2
的比值会等于在第二时间提供至测量电路33的第三电流i
e3
与第四电流i
e4
的比值。
[0077]
于一实施例中,测量电路33包括第一晶体管q1及第二晶体管q2,且第一晶体管q1与第二晶体管q2不需彼此匹配,而可降低工艺成本并提高电路设计灵活度,但不以此为限。
[0078]
第一晶体管q1的第一端通过第一节点a耦接第一电流源31及运算电路35且第一晶体管q1的第二端及其基极接地。第二晶体管q2的第一端通过第二节点b分别耦接第二电流源32及运算电路35且第二晶体管q2的第二端及其基极接地。
[0079]
运算电路35包括减法电路350及计算电路351。减法电路350的一输入端耦接至第一节点a且其另一输入端耦接至第二节点b。减法电路350的输出端耦接至计算电路351。
[0080]
在数字电路应用中,运算电路35还包括模拟数字转换电路352。模拟数字转换电路352耦接于减法电路350与计算电路351之间,用以将模拟型号转换为数字信号后提供给数位的计算电路351。
[0081]
如图3所示,于第一时间t1,第一电流源31提供第一电流i
e1
至第一晶体管q1的第一端且第二电流源32提供第二电流i
e2
至第二晶体管q2的第一端。减法电路330的两输入端分别接收到第一晶体管q1的第一端的第一电压v
be1
与第二晶体管q2的第一端的第二电压v
be2
并将两者相减后得到第一电压差δv
be,21
。于第二时间t2,第一电流源31提供第一电流i
e3
至第一晶体管q1的第一端且第二电流源32提供第二电流i
e4
至第二晶体管q2的第一端。减法电路350的两输入端分别接收到第一晶体管q1的第一端的电压与第二晶体管q2的第一端的电压并将两者相减后得到第二电压差δv
be,43
。
[0082]
于此实施例中,第一电流i
e1
为1μa且第二电流i
e2
为5μa,第三电流i
e3
为2μa且第四电流i
e4
为10μa,亦即第一电流i
e1
与第二电流i
e2
的比值m与第三电流i
e3
与第四电流i
e4
的比值m均为5;测量出的第一电压差δv
be21
为41.344355mv且第二电压差δv
be,43
为41.445596mv。
[0083]
于实际应用中,第一电流i
e1
与第二电流i
e2
的比值以及第三电流i
e3
与第四电流i
e4
的比值均小于100,比值的较佳范围为5~10,但不以此为限。
[0084]
当减法电路350将第一电压差δv
be,21
与第二电压差δv
be,34
依序输出至模拟数字转换电路352时,模拟数字转换电路352会将第一电压差δv
be,21
与第二电压差δv
be,34
从模拟信号转换为数字信号,然后再由计算电路351根据数位的第一电压差δv
be,21
与第二电压差δv
be,34
得到非线性的误差值δv
err
。
[0085][0086]
根据公式1可知:假设n
21
=1且n
43
=2,则校正后的温度感测电压dtemp即等于第一电压差δv
be,21
减去误差值δv
err
,如公式2所示。
[0087]
dtemp=δv
be,21-δv
err
(公式2)
[0088]
因此,计算电路351即可将第一电压差δv
be,21
减去误差值δv
err
来得到校正后的温度感测电压dtemp。
[0089]
如图4所示,图4为模拟本发明的温度感测装置在25℃下之相同m值(例如m=5)的不同电流基准值(例如第一电流i
e1
=1、2、4μa)相对应的温度感测结果。假设m=5、n
21
=1、n
43
=2、δv
err
=101.241μv,将其带入至公式2后重新得到δv
be
=41.243114mv、等效温度t为25.007℃、修正后的温度误差err低于0.01℃,与现有技术未修正的测量温度to相比,可大幅改善约100倍。此外,对于不同电流基准值(例如第一电流i
e1
=1、2、4μa)而言,最后得到修正后的温度误差err均低于0.01℃,故能有效提升温度感测装置的精准度及稳定度。
[0090]
如图5所示,图5为模拟本发明的温度感测装置在85℃下的相同m值(m=5)的不同电流基准值(例如第一电流i
e1
=1、2、4μa)相对应的温度感测结果。同理,可利用在不同时间提供具有相等电流比例、不同电流密度的两组输入电流所产生的测量电压差来得到非线性误差值,最后得到修正后的温度误差err低于0.03℃。
[0091]
综合上述可知:本发明的温度感测装置无论在高温(85℃)或低温(25℃)下均能有效校正传统的温度感测装置由于其晶体管的元件特性(β值)的非线性效应所导致的感测温度误差,故可大幅提升温度感测装置的精准度且不需复杂的电路,适合各种不同的温度感测的应用(例如封装前测试/封装后测试(cp/ft)或一般的温度感测)。
[0092]
依据本发明的另一具体实施例为一种温度感测装置的运作方法。于此实施例中,
所述方法用以运作温度感测装置。温度感测装置包括第一晶体管及第二晶体管。第一晶体管的第一端耦接第一电流源且其第二端及其基极接地。第二晶体管的第一端耦接第二电流源且其第二端及其基极接地。
[0093]
图6为此实施例中的温度感测装置运作方法的流程图。如图6所示,温度感测装置运作方法包括下列步骤:
[0094]
步骤s10:于第一时间控制第一电流源与第二电流源分别提供第一电流及第二电流至测量电路,以得到第一电压差;
[0095]
步骤s12:于第二时间控制第一电流源与第二电流源分别提供第三电流及第四电流至测量电路,以得到第二电压差;以及
[0096]
步骤s14:根据第一电压差及第二电压差得到误差值。
[0097]
需说明的是,第一电流与第二电流的比值等于第三电流与第四电流的比值。当执行步骤s14得到误差值时,还可将第一电压差减去误差值,以得到温度感测电压,但不以此为限。
[0098]
于一实施例中,步骤(c)还包括:将第一电压差与第二电压差转换为数字信号,以符合数字电路设计的需求。
[0099]
于一实施例中,第一电流与第二电流的比值以及第三电流与第四电流的比值均小于100,较佳比值为5至10,但不以此为限。
[0100]
于实际应用中,测量电路包括第一晶体管、第二晶体管。第一晶体管的第一端通过第一节点耦接第一电流源,第二晶体管的第一端通过第二节点耦接第二电流源。第一电压差是于第一时间将第一节点与第二节点的电压相减而得;第二电压差是于第二时间将第一节点与第二节点的电压相减而得,但不以此为限。
[0101]
相较于现有技术,本发明的温度感测装置及其运作方法根据于不同时间提供的具有相等电流比例、不同电流密度的两组输入电流取得非线性误差值来作为补偿值,可达到下列功效/优点:
[0102]
(1)在不大幅修改现有电路的前提下,能够有效提高温度测量的精确度;
[0103]
(2)无须复杂的电路,故能有效降低电路成本及设计复杂度;
[0104]
(3)无须考虑晶体管的元件特性(β值)的影响,故可适用于各种工艺;
[0105]
(4)温度感测装置中的两个晶体管元件不需彼此匹配,故可降低工艺成本并提高电路设计灵活度;以及
[0106]
(5)不限制使用于封装前测试/封装后测试(cp/ft),亦适用于一般温度感测过程,随时提供温度校正。