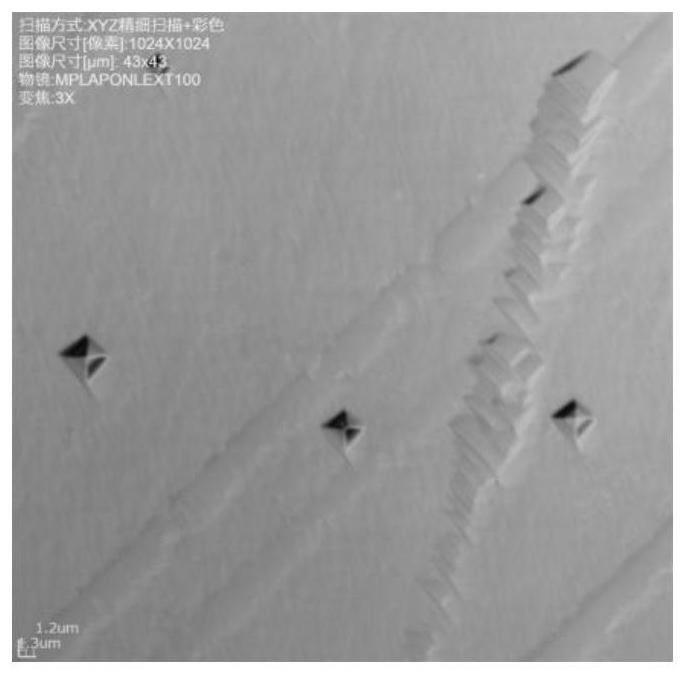
1.本技术涉及单晶缺陷检测技术领域,尤其涉及一种单晶金刚石衬底中的缺陷检测方法。
背景技术:2.金刚石晶体在生长过程中及后期半导体器件的辐照处理过程中都会产生一些微观缺陷,包括间隙原子和空位等本征缺陷,还有一些杂质缺陷以及它们组成的各种复合缺陷等类型,这些微观缺陷对金刚石半导体器件宏观性能影响很大。因此研究金刚石微观缺陷的形成、扩散以及扩散的类型、程度等方面很有必要。
3.金刚石衬底中通常有两类缺陷存在,一类是由于衬底表面状态如加工等引入的晶体表面缺陷,一类是衬底内部原本存在的缺陷。这两类缺陷能在外延生长过程中增殖到新形成的外延层中,由于高密度缺陷密度的增加会降低载流子的输运和寿命,影响器件性能和可靠性。表征并降低这两类缺陷的密度是实现高质量外延的关键因素。如何有效的快速便捷的分析缺陷是实现降低缺陷的必要条件。
技术实现要素:4.本技术实施例提供了一种单晶金刚石衬底中的缺陷检测方法,以快速便捷的分析金刚石衬底中的缺陷。
5.本技术实施例提供的单晶金刚石衬底中的缺陷检测方法,主要包括如下步骤:
6.对单晶金刚石衬底的(100)面进行表面研磨、抛光处理;
7.利用微波等离子体法,对所述单晶金刚石衬底的(100)面进行等离子体刻蚀;
8.利用检测设备,获取刻蚀后的所述单晶金刚石衬底(100)面上的凹坑形貌,其中,尖底坑为金刚石单晶内部原有的缺陷,平底坑金刚石表面损伤引入的缺陷。。
9.本技术实施例提供的单晶金刚石衬底中的缺陷检测方法,通过等离子体刻蚀金刚石单晶(100)面,用检测设备对刻蚀后产生的刻蚀坑形貌进行观察,其中,由损伤带来的缺陷,经刻蚀会得到平底坑,而由晶片内部原有缺陷,经刻蚀会产生尖底坑,尖底坑会随刻蚀时间逐渐变大变深,一直存在于表面。因此,利用上述缺陷检测方法可以快速区分金刚石衬底中的两类缺陷。
附图说明
10.此处的附图被并入说明书中并构成本说明书的一部分,示出了符合本发明的实施例,并与说明书一起用于解释本发明的原理。
11.为了更清楚地说明本发明实施例或现有技术中的技术方案,下面将对实施例或现有技术描述中所需要使用的附图作简单地介绍,显而易见地,对于本领域普通技术人员而言,在不付出创造性劳动性的前提下,还可以根据这些附图获得其他的附图。
12.图1为本技术实施例提供的单晶金刚石衬底的(100)面刻蚀后的表面形貌图;
13.图2a为本技术实施例提供的尖底坑的形貌图;
14.图2b为本技术实施例提供的平底坑的形貌图;
15.图2c为本技术实施例提供的尖底坑的截面图;
16.图2d为本技术实施例提供的平底坑的截面图;
17.图3a为本技术实施例提供的刻蚀时间为2.5h时平底坑的形貌图;
18.图3b为本技术实施例提供的刻蚀时间为4h时平底坑的形貌图;
19.图4a为本技术实施例提供的刻蚀时间为1.5h时平底坑与尖底坑宽度与深度统计;
20.图4b为本技术实施例提供的刻蚀时间为2.5h时平底坑与尖底坑宽度与深度统计;
21.图4c为本技术实施例提供的刻蚀时间为4h时平底坑与尖底坑宽度与深度统计;
22.图5a为本技术实施例提供的尖底坑的刻蚀变化模型图;
23.图5b为本技术实施例提供的平底坑的刻蚀变化模型图。
具体实施方式
24.这里将详细地对示例性实施例进行说明,其示例表示在附图中。下面的描述涉及附图时,除非另有表示,不同附图中的相同数字表示相同或相似的要素。以下示例性实施例中所描述的实施方式并不代表与本发明相一致的所有实施方式。相反,它们仅是与如所附权利要求书中所详述的、本发明的一些方面相一致的装置和方法的例子。
25.本实施例利用微波等离子体法等离子体刻蚀金刚石单晶(100)面后,根据等离子体刻蚀后刻蚀坑的形貌,区别金刚石表面损伤引入的缺陷和单晶内部原有的缺陷。基于上述原理,下面将对本实施例提供的方法进行详细介绍。
26.首先,对单晶金刚石衬底的(100)面进行表面研磨、抛光处理。
27.由于激光切割属于热切割。激光使金刚石断面区域的温度升高,高于金刚石相向石墨相转换的温度,所以切割后会导致表面生成石墨相,造成切割刀痕。在抛光之前,本实施例采用研磨工艺除去多余的石墨层,获得平整的表面。机械研磨去除效率较高,但加工后表面粗糙度依然较大,不能满足外延生长和器件制备的要求。化学机械抛光加工后表面粗糙度较好,但加工效率较低,为充分发挥二者的优点,我们使用机械研磨和化学机械抛光工艺相结合的加工流程。研磨抛光后,表面粗糙度要求为:afm测试10um*10um的情况下表面粗糙度<1nm,但并不限于该数值范围。
28.在研磨时,可以采用相对较软的铸铁盘作为研磨盘,并将一定颗粒度金刚石磨粒嵌入到盘中。利用铁的催化作用和高速旋转摩擦产生的热量达到研磨表面的效果。化学机械抛光是在对金刚石氧化的化学热动力学研究基础上,配制了以kmno4为主要氧化剂的抛光液,制定加快化学机械抛光过程中金刚石氧化的工艺措施。当然,在具体实施过程中,还可以采用其它研磨、抛光方式。
29.然后,利用微波等离子体法,对所述单晶金刚石衬底的(100)面进行等离子体刻蚀。
30.其中,可以利用h2作为等离子体刻蚀气体,反应腔室压力为20
‑
300torr,衬底表面温度为800
‑
1300℃,刻蚀时间0.5~5h,为保证刻蚀效果,优选地,反应腔室压力为200~300torr,衬底表面温度为≥1000~1300℃,刻蚀时间1~5h。
31.需要说明的是,刻蚀所用的等离子体不仅限于用单一气体h2,也可用混合气体,如
h2中加入o2或ar,加入o2或ar会增加刻蚀速率,例如,可以是o2/h2=1.5%、o2/h2=2%、o2/h2=3%、o2/h2=4%、o2/h2=5%等其他等离子体。最后,利用检测设备,获取刻蚀后的所述单晶金刚石衬底(100)面上的凹坑形貌,其中,尖底坑为金刚石单晶内部原有的缺陷,平底坑金刚石表面损伤引入的缺陷。
32.例如,设置刻蚀时间为1.5h,实验的刻蚀条件如表1所示。刻蚀后的表面形貌如图1所示,可看到尖底坑和平底坑同时存在于晶面表面,平底坑沿划痕处分布,尖底坑随意分散于晶片表面。当表面损伤缺陷和晶体原有的内部缺陷同时存在时,利用刻蚀后刻蚀坑的形貌可以区别这两种缺陷。
33.表1
[0034][0035]
继续刻蚀上述单晶金刚石衬底,刻蚀时间为2.5h,刻蚀的具体条件如表1所示。通过afm测试后观察平底坑和尖底坑的形貌图,如图2a至2d所示。由图像可看到,尖底坑形状为顶部尖尖的倒金字塔型,截面图像为倒三角形,其深度在1.47μm左右,宽度为7.6μm左右。平底坑形状为顶部较平,截面图为平台状,其深度为0.56μm左右,宽度为10.3μm左右。经等离子体刻蚀后,由表面损伤造成的平底坑相对于晶片内部原缺陷产生的尖底坑来说,其宽度较大,深度较浅。
[0036]
继续刻蚀上述单晶金刚石衬底,刻蚀时间为4h,刻蚀的具体条件如表1所示。观察平底坑随刻蚀时间的变化,如图3a和3b所示。平底坑随刻蚀时间的增加变得更加平坦。
[0037]
对于上述单晶金刚石衬底存在的平底坑和尖底坑,统计坑深和坑宽和随刻蚀时间1.5h、2.5h、4h的变化,如图4a至4c所示。尖底坑和平底坑在刻蚀初期深度、宽度相差不大,随刻蚀时间的增加,尖底坑深度、宽度逐渐增加,平底坑坑宽增加,坑深在减小。由此推断,继续刻蚀,当坑深接近为零是,由加工带来的表面损伤层会被刻蚀去掉,只剩尖底坑存在于表面。
[0038]
根据尖底坑和平底坑随刻蚀时间的变化特征,做出平底坑与尖底坑形成原理的模型图,如图5a和5b所示。刻蚀坑的大小由四个刻蚀速率决定,深度刻蚀速率(vdef)、自由刻蚀速率(vfree)、和表面刻蚀速率(vface)和水平刻蚀速率(vlat),vfree可在每次蚀刻后测量样品的厚度,直接测定vfree的值,vdef and vlat可由坑宽和坑深随刻蚀时间的变化得到,vface可由vdef cosθ得到。由刻蚀坑的优先选择性vdef是最大的,vdef和vfree决定刻蚀坑的深度,vlat和vface决定刻蚀坑的大小,刻蚀坑存在的条件vface>vfreecosθ。由图5a可知,尖底坑由于位错线的存在,其尺寸和深度会随刻蚀时间一直增加,刻蚀坑不会消失;由图5b可知,平底坑随着刻蚀时间变平坦,θ逐渐减小,当θ~0时,vface>vfreecosθ此公式将不再成立,平底坑将消失于晶体表面。
[0039]
因此,可得到衬底加工过程会引入表面损伤,损伤层带来的缺陷,由刻蚀可得到平底坑,平底坑随刻蚀时间的增加会逐渐变大变浅,直至消失于表面,而由晶片内部缺陷产生的尖底坑会随刻蚀时间逐渐变大变深,一直存在于表面。
[0040]
本说明书中的各个实施例均采用递进的方式描述,各个实施例之间相同相似的部分互相参见即可,每个实施例重点说明的都是与其他实施例的不同之处。本领域技术人员在考虑说明书及实践这里申请的公开后,将容易想到本技术的其它实施方案。本技术旨在涵盖本技术的任何变型、用途或者适应性变化,这些变型、用途或者适应性变化遵循本技术的一般性原理并包括本技术未公开的本技术领域中的公知常识或惯用技术手段。说明书和实施例仅被视为示例性的,本技术的真正范围和精神由下面的权利要求指出。本技术的范围仅由所附的权利要求来限制。