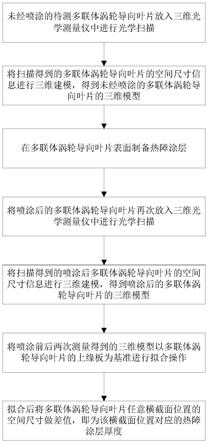
1.本发明涉及涂层厚度无损检测技术领域,尤其涉及一种多联体涡轮导向叶片热障涂层厚度三维光学测量方法。
背景技术:2.热障涂层一般由金属粘结层和陶瓷层组成,其厚度及均匀性直接影响涡轮叶片的抗氧化、隔热效果、热不均匀性及气膜冷却效果,因而涂层厚度控制是涂层生产质量控制的关键指标,也是涂层服役过程中检查的重要指标。目前有多种无损检测方法可用于热障涂层厚度的测量,主要有涡流法、红外法和超声波法等方法。涡流法属于接触式测量,其结果受粘结层特性、界面特性和叶片型面曲率特征影响较大,无法保证测量的精度,通常用于定性表征;红外法是根据被检测涂层在红外线的照射下吸收对应波长的红外线,分析处理被吸收的强度就可以对涂层进行厚度测定,测厚精度受照射时间、涂层成分均匀性等因素影响较大;超声法检测操作过程操作复杂,对于厚度较薄的热障涂层,其测量精度低,误差较大。以上方法均无法直接测量具有复杂型面的多联体涡轮导向叶片表面的热障涂层厚度。
技术实现要素:3.针对上述现有技术的不足,本发明提供一种多联体涡轮导向叶片热障涂层厚度三维光学测量方法。
4.为解决上述技术问题,本发明所采取的技术方案是:一种多联体涡轮导向叶片热障涂层厚度三维光学测量方法,包括如下步骤:
5.步骤1:将未经喷涂的待测多联体涡轮导向叶片放入三维光学测量仪中进行光学扫描;
6.所述三维光学测量仪进行光学扫描的方法为:采用可见光,将光栅条纹投射到多联体涡轮导向叶片表面,利用光学拍照定位和光栅测量原理进行扫描,得到多联体涡轮导向叶片的空间尺寸信息。
7.所述光栅条纹为蓝光。
8.步骤2:将扫描得到的多联体涡轮导向叶片的空间尺寸信息进行三维建模,得到未经喷涂的多联体涡轮导向叶片的三维模型;
9.步骤3:在多联体涡轮导向叶片表面制备热障涂层;
10.所述热障涂层至少为两层,在喷涂时对多联体涡轮导向叶片上缘板进行保护,确保上缘板无涂层。
11.步骤4:将喷涂后的多联体涡轮导向叶片再次放入三维光学测量仪中进行光学扫描;
12.步骤5:将扫描得到的喷涂后多联体涡轮导向叶片的空间尺寸信息进行三维建模,得到喷涂后的多联体涡轮导向叶片的三维模型;
13.步骤6:将喷涂前后两次测量得到的三维模型以多联体涡轮导向叶片的上缘板为
基准进行拟合操作;
14.步骤7:拟合后将多联体涡轮导向叶片任意横截面位置的空间尺寸做差值,即为该横截面位置对应的多联体涡轮导向叶片表面的热障涂层厚度。
15.采用上述技术方案所产生的有益效果在于:
16.1、本发明提供的方法采用三维光学测量,不仅不受叶片基体材料的影响,应用范围更广阔,还能实现复杂型面的叶片表面的热障涂层厚度的测量;
17.2、本发明的方法不仅测试速度快,还能实现无损和非接触测量,并且能达到较高的测量精度;
18.3、本发明的方法可直接测量多联体涡轮导向叶片表面热障涂层厚度,解决了传统无损检测方法无法直接测量多联体涡轮导向叶片表面热障涂层厚度的问题,降低了检测成本,提高了多联体涡轮导向叶片表面热障涂层厚度的稳定性及涡轮导向叶片的可靠性。
附图说明
19.图1为本发明实施例中提供的多联体涡轮导向叶片热障涂层厚度三维光学测量方法的流程图;
20.图2为本发明实施例中喷涂前后两次测量得到的三维模型以多联体涡轮导向叶片的上缘板为基准进行拟合操作的局部拟合效果图;
21.图3为本发明实施例中拟合后多联体涡轮导向叶片任意横截面位置的涂层厚度示意图;
22.图4为本发明实施例中金相检测法测量时叶片的切割位置示意图;
23.图5为本发明实施例中本发明的方法和金相测量得到的底层厚度的结果对比图;
24.图6为本发明实施例中本发明的方法和金相测量得到的面层厚度的结果对比图;
25.图7为本发明实施例中本发明的方法和金相测量得到的总厚度的结果对比图。
具体实施方式
26.下面结合附图和实施例,对本发明的具体实施方式作进一步详细描述。以下实施例用于说明本发明,但不用来限制本发明的范围。
27.如图1所示,本实施例中多联体涡轮导向叶片热障涂层厚度三维光学测量方法如下所述:
28.步骤1:将未经喷涂的待测多联体涡轮导向叶片放入三维光学测量仪中进行光学扫描;
29.所述三维光学测量仪进行光学扫描的方法为:采用可见光,将光栅条纹投射到多联体涡轮导向叶片表面,利用光学拍照定位和光栅测量原理进行扫描,得到多联体涡轮导向叶片的空间尺寸信息。
30.所述光栅条纹为蓝光。
31.本实施例中,采用的gom公司的三维光学测量仪,型号为atos core 80,该三维光学测量仪除立体摄像技术外,采用三次扫描技术、立体相机与投影仪相结合。在单次扫描中一次性捕捉工件的三个不同方向上的数据。即使是扫描光面和复杂的几何形状,所需扫描次数更少,且依然能够提供高质量的数据。该测量仪采用窄带蓝光,避免了外界光线条件的
影响,当蓝光光栅投影到被测物体的表面后,左右两个立体相机会把这些偏折或栅距变化的图像都拍下来,并基于相机芯片上正弦曲线强度分布形成相移,atos core使用外差原理的多频相移达到最高亚像素精度。通过atos软件计算后,各相机像素会转换成独立的三维坐标。
32.步骤2:将扫描得到的多联体涡轮导向叶片的空间尺寸信息进行三维建模,得到未经喷涂的多联体涡轮导向叶片的三维模型;
33.步骤3:在多联体涡轮导向叶片表面制备热障涂层;
34.所述热障涂层至少为两层,在喷涂时对多联体涡轮导向叶片上缘板进行保护,确保上缘板无涂层。
35.本实施例中,热障涂层厚度为2层,分别为金属粘结层和陶瓷层,厚度为0.02~0.3mm。
36.步骤4:将喷涂后的多联体涡轮导向叶片再次放入三维光学测量仪中进行光学扫描;
37.步骤5:将扫描得到的喷涂后多联体涡轮导向叶片的空间尺寸信息进行三维建模,得到喷涂后的多联体涡轮导向叶片的三维模型;
38.步骤6:将喷涂前后两次测量得到的三维模型以多联体涡轮导向叶片的上缘板为基准进行拟合操作,其效果如图2所示;
39.本实施例中,采用超音速喷涂在叶身表面制备热障涂层底层,底层喷涂后采用三维光学测量仪进行扫描;在采用等离子喷涂在底层上喷涂面层,面层喷涂后再采用三维光学测量仪进行扫描;将喷涂完底层后的扫面结果三维建模,与未喷涂的三维模型,以上缘板为基准拟合对齐,两次测量的插值即为热障涂层底层厚度。按相同的方法得到热障涂层面层厚度和涂层总厚度。
40.步骤7:拟合后将多联体涡轮导向叶片任意横截面位置的空间尺寸做差值,即为该横截面位置对应的多联体涡轮导向叶片表面的热障涂层厚度,如图3所示。
41.本实施例中,为了验证本发明的方法的准确性和稳定性,将测量后的叶片按照测量的横截面进行切割,如图4所示,再采用金相分析得到该截面处的涂层的实际厚度。将本发明的方法的测量结果与金相测量的结果进行对比分析,绘制涂层厚度曲线,其中本发明的方法和金相测量得到的底层厚度的结果对比如图5所示,本发明的方法和金相测量得到的面层厚度的结果对比如图6所示,本发明的方法和金相测量得到的总厚度的结果对比如图7所示。
42.通过厚度数据对比分析,本发明的方法得到的涂层厚度测量值与金相测量厚度的平均偏差小于6.0%,说明本发明的方法测量结果具有较高的准确率。