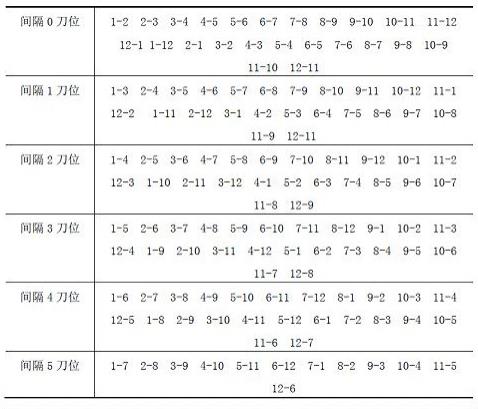
1.本发明属于机床部件静或动平衡测试技术领域;具体涉及一种全工况模拟的双三联齿盘可靠性试验装置及方法。
背景技术:2.近几年随着装备制造业的快速发展,我国已成为数控机床生产及应用的大国,目前国内研发的数控机床在精度、速度、大型化和多轴联动方面取得了明显进展。但随着功能的增多,故障隐患增多,先进功能和性能指标不能维持,可靠性问题严重,已经成为企业、用户与销售市场关注的焦点和数控机床产业发展的瓶颈。国产数控机床可靠性水平偏低的主要原因之一是国产数控机床关键功能部件的可靠性水平较低,因此研究开发数控机床关键功能部件可靠性试验装置和试验技术具有重要的实际意义。数控刀架作为高端数控车床的关键功能部件之一,其自身的可靠性水平对整机的可靠性水平有重要的影响。三联齿盘作为数控刀架最重要的关键组件,其可靠性对于数控刀架的可靠性水平影响重大。
3.我国的三联齿盘可靠性试验研究起步较晚,目前仅有一些功能简单的可靠性试验装置。例如,某些试验台可以对三联齿盘进行齿盘运转试验,试验对象单一,试验模拟的工况与真实工况有很大的差距。
技术实现要素:4.本发明目的是为了解决上述问题,而提供了一种全工况模拟的双三联齿盘可靠性试验装置及方法;一种全工况模拟的双三联齿盘可靠性试验装置,它包括:第一齿盘运转部、第一三联齿盘2、加载部分、第二三联齿盘4、第二齿盘运转部、液压站6、控制台7、地平铁8、检测单元9;所述的第一三联齿盘2固定在第一齿盘运转部上;第二三联齿盘4固定在第二齿盘运转部上;第一三联齿盘2、加载部分、第二三联齿盘4依次连接;加载部分通过检测单元9固定在地平铁8上;液压站6和控制台7设在地平铁8两侧;所述的液压站6为装置内提供液压动力支持;所述的检测单元9包括:激光位移传感器91、多面棱镜组件、激光位移传感器底座93、移动平台94、平台驱动组件、检测装置底座99;所述的多面棱镜组件中设有多棱体镜923,多棱体镜923通过多棱体安装轴921轴接在多棱体支撑架922上;激光位移传感器底座9和多棱体支撑架922固定在移动平台94上;平台驱动组件驱动移动平台94在检测装置底座99上移动;所述的控制台7分别与第一三联齿盘运转支撑部分、第一三联齿盘、加载部分3、第二三联齿盘、第二三联齿盘运转支撑部分、平台驱动组件的控制端电气连接。
5.所述的第二齿盘运转部与第一齿盘运转部结构相同;第一齿盘运转部包括:第一液压缸支撑座11、第一液压缸12、第一支撑架13、第一驱动电机14;第一液压缸支撑座11底
部通过螺栓锁固在地平铁8上;第一液压缸12设在第一液压缸支撑座11上部;第一液压缸12的活塞杆与第一支撑架13连接;第一驱动电机14固定在第一电机支撑盘15中部,第一电机支撑盘15可在第一支撑架13内滑动连接。
6.所述的第二三联齿盘4与第一三联齿盘2结构相同;第一三联齿盘2包括:第一动齿盘21、第一内齿盘22、第一外齿盘23;第一动齿盘21一侧与第一支撑架13连接;第一动齿盘21、第一内齿盘22、第一外齿盘23的圆盘上分布有t型齿槽;第一动齿盘21的t型齿槽与第一内齿盘22、第一外齿盘23上的t型齿槽啮合为数控刀架刀盘转动起到传动动力。
7.所述的加载部分包括:第一三联齿盘加载装置、第二三联齿盘加载装置;第一三联齿盘加载装置和第二三联齿盘加载装置结构对称相同并固定在检测装置底座99上;所述的第一三联齿盘加载装置和第二三联齿盘加载装置中均设有:加载压电陶瓷、直线电机;加载压电陶瓷通过直线电机直线移动;两个加载压电陶瓷可实现对第一三联齿盘2、第二三联齿盘4加载与卸载。
8.所述的多棱体镜923为一等精度12面棱体;激光位移传感器91为激光三角反射式位移传感器,发射激光到多棱体镜923上,通过反射激光测算多棱体镜923偏角,得到三联齿盘定位精度偏差。
9.本发明还提供了一种全工况模拟的双三联齿盘可靠性试验装置。
10.一种全工况模拟的双三联齿盘可靠性试验装置,包括如下步骤:(1)开启设备a.打开电源b.打开工控机,开启液压控制软件、电机控制软件、多棱体镜(923)检测软件、压电陶瓷控制软件;c.开启液压站;(2)调整试验台至工作位控制台7发送指令,调整三联齿盘运转部分至三联齿盘分离工作位,调整检测单元至两三联齿盘中间位置。
11.(3)试验前三联齿盘精度检测第一三联齿盘定位精度、重复定位精度检测a.控制台7发送指令,控制平移驱动电机955运转通过丝杠螺母副带动检测单元9移动,直至多棱体安装轴921与第一内齿盘22内孔配合上;b.制定齿盘运转方案按间隔0、1、2、
…
和/或n刀位换刀,正转和/或反转运转;c.按照上述齿盘运转方案,控制台发送指令给第一液压缸12控制第一动齿盘21与第一内齿盘22,第一外齿盘23的分离与啮合,控制台7发送指令给第一驱动电机14控制三联齿盘内齿盘运转;每次三联齿盘运转试验都包含上述两个动作,其中第一驱动电机14运转角度由齿盘运转方案决定;d.每次运转试验在多棱体镜(923)检测软件记录试验数据,直至全部运转试验结束;c.第一三联齿盘试验前精度检测实验结束,控制台7发送指令,控制平移驱动电机955运转通过丝杠螺母副带动检测单元9移动,直至多棱体安装轴921与第一内齿盘22解除
配合,和检测单元回到非工作位;第二三联齿盘定位精度、重复定位精度检测a.控制台7发送指令,控制平移驱动电机955运转通过丝杠螺母副带动检测单元9移动,直至多棱体安装轴921与第二内齿盘42内孔配合上;b.制定齿盘运转方案按间隔0、1、2、
…
和/或n刀位换刀,正转和/或反转运转;c.按照上述齿盘运转方案,控制台7发送指令给液压缸:第二液压缸52控制第二动齿盘41与第二内齿盘42,第二外齿盘43的分离与啮合;控制台7发送指令给第二驱动电机54控制三联齿盘内齿盘运转;每次三联齿盘运转试验都包含上述两个动作,其中第一驱动电机14运转角度由上述的齿盘运转方案决定;d.每次运转试验在12面棱体检测软件记录试验数据,直至全部运转试验结束;e.第二三联齿盘试验前精度检测实验结束,控制台7发送指令,控制平移驱动电机955运转通过丝杠螺母副带动检测单元9移动,直至多棱体安装轴921与第二内齿盘42解除配合,和检测单元回到非工作位。
12.(4)三联齿盘加载a.三联齿盘运转方案:按间隔0、1、2、
…
和/或n刀位换刀,正转和/或反转运转;b.三联齿盘载荷谱编制:采用数控刀架在实际切削过程中切削力分析结果,并将其转换为三联齿盘受力情况搭建三联齿盘载荷谱三联齿盘载荷谱搭建步骤如下:step1采集切削力样本数据;step2选取最小样本;step3截取信号进行预处理,去除奇异点;step4采用雨流计数法处理预处理过得信号得到切削力载荷均值、幅值、切削力方向;step5根据切削力受力分析,计算切削力均值在轴向分力及三联齿盘所受载荷均值;step6根据算得的三联齿盘载荷力均值、幅值编制三联齿盘载荷谱;c.三联齿盘可靠性试验谱编制所述的三联齿盘可靠性试验谱由三联齿盘运转谱和三联齿盘载荷谱联合构成;(5)试验后三联齿盘精度检测第一三联齿盘定位精度、重复定位精度检测a.控制台7发送指令,控制平移驱动电机955运转通过丝杠螺母副带动检测单元9移动,直至多棱体安装轴921与第一内齿盘22内孔配合上;b.制定齿盘运转方案按间隔0、1、2、
…
和/或n刀位换刀,正转和/或反转运转;c.按照上述的齿盘运转方案,控制台发送指令给第一液压缸12控制第一动齿盘21与第一内齿盘22,第一外齿盘23的分离与啮合,控制台7发送指令给第一驱动电机14控制三
联齿盘内齿盘运转;每次三联齿盘运转试验都包含上述两个动作,其中第一驱动电机14运转角度由三联齿盘运转试验表决定;d.每次运转试验在12面棱体检测软件记录试验数据,直至全部运转试验结束;e.第一三联齿盘试验前精度检测实验结束,控制台7发送指令,控制平移驱动电机955运转通过丝杠螺母副带动检测单元9移动,直至多棱体安装轴921与第一内齿盘22解除配合,和检测单元回到非工作位。
13.第二三联齿盘定位精度、重复定位精度检测a.控制台7发送指令,控制平移驱动电机955运转通过丝杠螺母副带动检测单元9移动,直至1多棱体安装轴921与第一内齿盘22内孔配合上;b.制定齿盘运转方案按间隔0、1、2、
…
和/或n刀位换刀,正转和/或反转运转;c.按照上述的齿盘运转方案,控制台发送指令给第二液压缸52控制第二动齿盘41与第二内齿盘42,第二外齿盘43的分离与啮合,控制台7发送指令给第二驱动电机54控制三联齿盘内齿盘运转;每次三联齿盘运转试验都包含上述两个动作,其中第二驱动电机54运转角度由上述的齿盘运转方案决定;d.每次运转试验在多棱体镜923检测软件记录试验数据,直至全部运转试验结束;e.第二三联齿盘试验前精度检测实验结束,控制台7发送指令,控制平移驱动电机955运转通过丝杠螺母副带动检测单元9移动,直至多棱体安装轴921与第二内齿盘42解除配合,和检测单元回到非工作位;(6)调整试验台至非工作位控制台7发送指令,调整三联齿盘运转部分至三联齿盘分离工作位,调整检测单元至两三联齿盘中间位置。
14.(7)数据分析将采集到的精度指标以向量的形式存放入控制台7,进行长时间多次了靠性试验后,以时间为横坐标,每次三联齿盘可靠性试验的到的试验后检测数据为变量代入可靠性模型分析,得到对应的可靠性指标。
15.所述的按间隔0、1、2、
…
和/或n刀位分别换刀,正转和/或反转运转,所述的n=控刀架的刀位数
÷
2-1;间隔0、1、2、
…
和/或n-1正转和反转分别运转,间隔n刀位换刀正转运转。
16.所述的三联齿盘控刀架为12刀位,:一次转位过程可分为间隔0刀位换刀、间隔1刀位换刀、间隔2刀位换刀、间隔3刀位换刀、间隔4刀位换刀、间隔5刀位换刀六种情况,前五种换刀情况都有正转、反转各12种正转换法,间隔5刀位换刀只有12种正转换法,共有132种换法。
17.所述的可靠性模型为:退化模型;所述的退化模型为维纳过程、逆高斯过程或伽马模型。
18.本发明提供了一种全工况模拟的双三联齿盘可靠性试验装置,它包括:第一齿盘运转部、第一三联齿盘、加载部分、第二三联齿盘、第二齿盘运转部、液压站、控制台、检测单元;第一三联齿盘固定在第一齿盘运转部上;第二三联齿盘固定在第二齿盘运转部上;第一三联齿盘、加载部分、第二三联齿盘依次连接;加载部分通过检测单元固定在地平铁上;检测单元可同时检测两个三联齿盘;液压站和控制台设在地平铁两侧;控制台分别与各个被
控制端电气连接;本装置同时对两种不同型号三联齿盘进行可靠性试验,试验装置结构紧凑,利用率高,无需在重复对两套三联齿盘进行定位精度调整,提升了检测效率。
19.与现有技术相比本发明的有益效果是:1.本发明所述的全工况模拟的双三联齿盘可靠性试验装置提供一个一种可以同时对两种不同型号三联齿盘进行可靠性试验的装置,试验装置结构紧凑,设备利用率高,不仅解决了现有三联齿盘可靠性试验装置无法同时对两套不同型号三联齿盘进行同时加载的问题,同时考虑了经济适用性。
20.2.本发明所述的全工况模拟的双三联齿盘可靠性试验装置提出了在对每套三联齿盘进行齿盘运转试验的基础上,同时运用两套压电陶瓷为主导的高频力加载装置进行加载,使得本发明相比于其他三联齿盘可靠性试验装置更加接近实际工况,可靠性模拟效果更好。
21.3.本发明所述的全工况模拟的双三联齿盘可靠性试验装置中采用了一套检测装置通过安装检测装置的可移动平台,实现同时对两套三联齿盘进行定位精度重复定位精度检测功能,检测平台调好一次设备,后续在进行精度检测时无需在重复调整,大大提升了检测效率。
22.4.本发明所述的全工况模拟的双三联齿盘可靠性试验装置中提出的三联齿盘运转支撑装置由液压缸和电机组合,由简单的组成结构便完成了其他三联齿盘可靠性试验装置需要复杂组合装置才能完成的功能,且本发明所提出的三联齿盘运转支撑装置可以通过定位孔位置改变而实现对不同型号的三联齿盘进行可靠性试验,大大增加的本发明实验装置的鲁棒性。
23.5.本发明所述的由压电陶瓷加载的双三联齿盘可靠性试验方法提出了本发明提供配套试验台使用的模拟三联齿盘实际工况的可靠性试验方法,明确了本实验装置进行可靠性试验的具体流程,对于三联齿盘可靠性试验装置使用具有指导意义。
附图说明
24.图1为本发明所述的全工况模拟的双三联齿盘可靠性试验装置的总体布局轴测投影图;图2为本发明所述的全工况模拟的双三联齿盘可靠性试验装置的对两套三联齿盘进行可靠性试验轴测投影图;图3 为本发明所述的全工况模拟的双三联齿盘可靠性试验装置的对两套三联齿盘进行可靠性试验俯视图;图4为本发明所述的全工况模拟的双三联齿盘可靠性试验装置的精度检测装置及两套三联齿盘的分解式轴测投影图;图5为本发明所述的全工况模拟的双三联齿盘可靠性试验方法的流程图图6为本发明所述的全工况模拟的双三联齿盘可靠性试验方法中雨流计数法原理图。
25.图7为本发明所述的全工况模拟的双三联齿盘可靠性试验装置的刀具切削力分析示意图;图中:第一液压缸支撑座11,第一支撑部连接座111,第一液压缸12,第一支撑架
13,第一驱动电机14,第一三联齿盘2,第一动齿盘21,第一内齿盘22,第一外齿盘23,第一直线电机底座32,第一直线电机动子33,第二加载压电陶瓷34,第二直线电机底座35,第二直线电机动子36,第二三联齿盘4,第二动齿盘41,第二内齿盘42,第二外齿盘43,第二液压缸支撑座51,第二支撑部连接座511,第二液压缸52,第二支撑架53,第二驱动电机54,第二电机支撑盘55,液压站6,控制台7,地平铁8,检测单元9,激光位移传感器91,多棱体安装轴921,多棱体支撑架922,多棱体镜923,安装轴轴承924,激光位移传感器底座93,移动平台94,滑轨951,丝杠952,丝母、联轴器954,平移驱动电机955,检测装置底座99。
具体实施方式
26.实施例1一种全工况模拟的双三联齿盘可靠性试验装置参见图1至图4所示,一种全工况模拟的双三联齿盘可靠性试验装置,它包括:第一齿盘运转部、第一三联齿盘2、加载部分、第二三联齿盘4、第二齿盘运转部、液压站6、控制台7、地平铁8、检测单元9;第一三联齿盘2固定在第一齿盘运转部上;第二三联齿盘4固定在第二齿盘运转部上;第一三联齿盘2、加载部分、第二三联齿盘4依次连接;加载部分通过检测单元9固定在地平铁8上;液压站6和控制台7设在地平铁8两侧;所述的液压站6为装置内提供液压动力支持;所述的第一齿盘运转部包括:第一液压缸支撑座11、第一液压缸12、第一支撑架13、第一驱动电机14;所述的第一液压缸支撑座11为t型板式支撑件,第一液压缸支撑座11的底部设有第一支撑部连接座111;第一支撑部连接座111为矩形钢板;第一支撑部连接座111的4角处开有4个等大的螺栓通孔;螺栓通过第一支撑部连接座111上端螺栓通孔,将第一液压缸支撑座11锁固在地平铁8上;第一液压缸12通过螺栓锁固固定在第一液压缸支撑座11上;所述的第一液压缸12选用单活塞杆式液压缸,第一液压缸12上装有第一液压阀,第一液压阀与控制台7电气连接;所述的第一液压缸12的活塞杆端顶部设有矩形钢板;第一液压缸12的活塞杆端顶部与矩形钢板焊接;第一支撑架13一端为圆形钢板;第一液压缸12顶部的矩形钢板与第一支撑架13一端的圆形钢板通过螺栓锁固连接;所述的第一驱动电机14为三相电机,第一驱动电机14固定在第一电机支撑盘15中部;第一支撑架13上设有4个架杆,第一电机支撑盘15四角为4个等大的通孔,4个等大的通孔套接第一支撑架13上的4个架杆上,4个架杆分别与第一电机支撑盘15上的通孔间隙连接,第一电机支撑盘15可在第一支撑架13内滑动;所述的第一三联齿盘2包括:第一动齿盘21、第一内齿盘22、第一外齿盘23;所述的第一动齿盘21为齿盘类结构件,第一动齿盘21一侧与第一支撑架13连接;第一动齿盘21为双层圆盘结构;第一动齿盘21上部小圆盘上分布有t型齿槽,第一动齿盘21的t型齿槽与第一内齿盘22、第一外齿盘23上的t型齿槽啮合为数控刀架刀盘转动起到传动动力;所述的第一内齿盘22齿盘类结构件,第一内齿盘22为双层圆盘结构;第一驱动电机14为第一内齿盘22提供动力;第一内齿盘22上分布有t型齿槽,第一内齿盘22上的t型齿
槽与第一动齿盘21上的t型齿槽啮合为数控刀架刀盘转动起到传动动力;所述的第一外齿盘23为齿盘类结构件,第一外齿盘23为双层圆盘结构,第一外齿盘23上部小圆盘上分布有t型齿槽,第一动齿盘21上的t型齿槽啮合为数控刀架刀盘转动起到传动动力;第一外齿盘23的下部大圆盘圆周与检测装置底座99上圆形通孔过盈连接;检测装置底座99固定在地平铁8上;所述的第二三联齿盘4与第一三联齿盘2结构相同;第二齿盘运转部与第一齿盘运转部结构相同;所述的第二三联齿盘4与第一三联齿盘2结构相同;第二三联齿盘4包括:第二动齿盘41、第二内齿盘42、第二外齿盘43;第二动齿盘41、第二内齿盘42和第二外齿盘43的连接关系与第一动齿盘21、第一内齿盘22和第一外齿盘23的连接关系相同;所述的第二齿盘运转部包括:第二液压缸支撑座51、第二液压缸52、第二支撑架53、第二驱动电机54;所述的第二液压缸支撑座51为t型板式支撑件,第二液压缸支撑座51的底部设有第二支撑部连接座511;第二支撑部连接座511为矩形钢板;第二支撑部连接座511的4角处开有4个等大的螺栓通孔;螺栓通过第二支撑部连接座511上端螺栓通孔,将第二液压缸支撑座51锁固在地平铁8上;第二液压缸52通过螺栓锁固固定在第二液压缸支撑座51上;所述的第二液压缸52选用单活塞杆式液压缸,第二液压缸52上装有第二液压阀,第二液压阀与控制台7电气连接;所述的第二液压缸52的活塞杆端顶部设有矩形钢板;第二液压缸52的活塞杆端顶部与矩形钢板焊接;第二支撑架53一端为圆形钢板;第二液压缸52顶部的矩形钢板与第二支撑架53一端圆形钢板通过螺栓锁固连接;所述的第二驱动电机54为三相电机,第二驱动电机54固定在第二电机支撑盘55中部;第二支撑架53上设有4个架杆,第二电机支撑盘55四角为4个等大的通孔,4个等大的通孔套接第二支撑架53上的4个架杆,架杆与第二电机支撑盘55上的通孔间隙连接,第二电机支撑盘55可在第一支撑架13内滑动;所述的加载部分包括:第一三联齿盘加载装置、第二三联齿盘加载装置;第一三联齿盘加载装置、第二三联齿盘加载装置中局设有相同的压电陶瓷加载机;第一三联齿盘加载装置、第二三联齿盘加载装置对称设置在检测装置底座99上,为三联齿盘施加模拟实时工况的高频动态力;所述的第一三联齿盘加载装置包括:第一加载压电陶瓷31、第一直线电机;所述的第一加载压电陶瓷31为一对压电陶瓷加载杆,能够提供500n-10000n范围内的基值力,0hz-10000hz的高频动态力;所述的第一直线电机包括:第一直线电机底座32,第一直线电机动子33;第一直线电机动子33设在第一直线电机底座32上;第一直线电机底座32通过螺栓固定在检测装置底座99的一侧;所述的第一直线电机动子33前端与第一加载压电陶瓷31连接;第一直线电机动子33带动第一加载压电陶瓷31,同时第一直线电机给第一加载压电陶瓷31提供其工作所需要的预应力;所述的第一直线电机动子33在第一直线电机底座32上的移动带动第一加载压电
陶瓷31移动,实现对第一三联齿盘2的加载与卸载;工作时俩压电陶瓷加载杆加载端同时加载到第一外齿盘23端面;所述的第二三联齿盘加载装置包括:第二加载压电陶瓷34、第二直线电机;所述的第二加载压电陶瓷34与第一加载压电陶瓷31相同;所述的所述的第二直线电机包括:第二直线电机底座35、第二直线电机动子36;第二直线电机动子36设在第二直线电机底座35上;第二直线电机底座35通过螺栓固定在检测装置底座99的另一侧;即第一直线电机底座32与第二直线电机底座35分别设在检测装置底座99的两侧;所述的第二直线电机动子35前端与第二加载压电陶瓷34连接;第二直线电机动子35带动第二加载压电陶瓷34,同时第二直线电机给第二加载压电陶瓷34提供其工作所需要的预应力;所述的第二直线电机动子35在第二直线电机底座34上的移动带动第二加载压电陶瓷34移动,实现对第二三联齿盘4的加载与卸载;工作时俩压电陶瓷加载杆加载端同时加载到第二外齿盘43端面。
27.所述的控制台7分别与第一三联齿盘运转支撑部分,第一三联齿盘,加载部分3,第二三联齿盘,第二三联齿盘运转支撑部分的控制端相连;所述的控制台7分别与第一驱动电机14、第一液压缸12、第一加载压电陶瓷31、第一直线电机、第二加载压电陶瓷34、第二直线电机、第二驱动电机54、第二液压缸52、检测单元9电气连接;所述的检测单元9包括:激光位移传感器91、多面棱镜组件、激光位移传感器底座93、移动平台94、平台驱动组件、检测装置底座99;所述的激光位移传感器91固定在移传感器底座93上;所述的多面棱镜组件包括:多棱体安装轴921、多棱体支撑架922、多棱体镜923、安装轴轴承924;多棱体镜923设在多棱体安装轴921中部;所述的多棱体支撑架922为u字形构件,其两侧为板状支撑结构;多棱体支撑架922两侧的板状支撑上部均设有轴承通孔;所述的安装轴轴承924设有2个,2个安装轴轴承924的内径套接在多棱体镜923两侧的多棱体安装轴921上;2个安装轴轴承924外径装设在多棱体支撑架922的轴承通孔中;即多棱体安装轴921两端轴接在多棱体支撑架922上部;所述的多棱体安装轴921的两端根据试验需求可分别与第一内齿盘22内孔过盈连接或者与二内齿盘42内孔过盈连接,起到传递转动作用;所述的多棱体镜923为一等精度12面棱体;多棱体镜923与激光位移传感器91配套使用;激光位移传感器91为激光三角反射式位移传感器,发射激光到多棱体镜923上,通过反射激光测算多棱体镜923偏角,得到三联齿盘定位精度偏差;所述的激光位移传感器底座93为矩形支撑件,激光位移传感器底座93和多棱体支撑架922固定在移动平台94上;所述的平台驱动组件包括:滑轨951、丝杠952、丝母、联轴器954、平移驱动电机955;所述的滑轨951与丝杠952平行;滑轨951固定在检测装置底座99上;丝杠952与检
测装置底座99轴接;丝母固定在移动平台94底部,丝母套接在丝杠952上;平移驱动电机955通过联轴器954与丝杠952连接;平移驱动电机955驱动移动平台94在滑轨951上移动;所述的平移驱动电机955为三相异步电机;平移驱动电机955与控制台7电气连接。
28.实施例2一种全工况模拟的双三联齿盘可靠性试验方法参见图5至图7所示,一种全工况模拟的双三联齿盘可靠性试验方法,包括如下步骤:试验前准备工作、开启设备、调整试验台至工作位、试验前三联齿盘精度检测、三联齿盘加载、试验后三联齿盘精度检测、调整试验台至非工作位、数据分析、关闭设备;(1)试验前准备工作1)在试验前,检查试验系统的润滑和冷却状况;2)检测各连接件是否有松动现象;3)检测液压站液压是否在正常工作位;4)检测电器元件工作状态;5) 试验过程中,同时监控液压系统温度,防止过热现象发生。
29.(2)开启设备1)打开电源2)打开工控机,开启液压控制软件、电机控制软件、12面棱体(多棱体镜923)检测软件、压电陶瓷控制软件;3)开启液压站。
30.(3)调整试验台至工作位控制台7发送指令,调整三联齿盘运转部分至三联齿盘分离工作位,调整检测单元至两三联齿盘中间位置。
31.(4)试验前三联齿盘精度检测第一三联齿盘定位精度、重复定位精度检测1)控制台7发送指令,控制平移驱动电机955运转通过丝杠螺母副带动检测单元9移动,直至多棱体安装轴921与第一内齿盘22内孔配合上;2)制定齿盘运转方案,这里以12刀位数控刀架的三联齿盘运转方案为例,其他刀位数控刀架运转方案同上;按照12个刀位刀架进行的132次三联齿盘运转试验:一次转位过程可分为间隔0刀位换刀、间隔1刀位换刀、间隔2刀位换刀、间隔3刀位换刀、间隔4刀位换刀、间隔5刀位换刀六种情况,前五种换刀情况都有正转、反转各12种正转换法,间隔5刀位换刀只有12种正转换法,共有132种换法。相对应的三联齿盘运转试验表如下:
3)按照上述三联齿盘运转试验表,控制台发送指令给第一液压缸12控制第一动齿盘21与第一内齿盘22,第一外齿盘23的分离与啮合,控制台7发送指令给第一驱动电机14控制三联齿盘内齿盘运转;每次三联齿盘运转试验都包含上述两个动作,其中第一驱动电机14运转角度由三联齿盘运转试验表决定;4)每次运转试验在12面棱体(多棱体镜923)检测软件记录试验数据,直至全部运转试验结束;5)a三联齿盘试验前精度检测实验结束,控制台7发送指令,控制平移驱动电机955运转通过丝杠螺母副带动检测单元9移动,直至多棱体安装轴921与第一内齿盘22解除配合,和检测单元回到非工作位。
32.第二三联齿盘定位精度、重复定位精度检测1)控制台7发送指令,控制平移驱动电机955运转通过丝杠螺母副带动检测单元9移动,直至多棱体安装轴921与第二内齿盘42内孔配合上;2)制定齿盘运转方案,这里以12刀位数控刀架的三联齿盘运转方案为例,其他刀位数控刀架运转方案同上;按照12个刀位刀架进行的132次三联齿盘运转试验:一次转位过程可分为间隔0刀位换刀、间隔1刀位换刀、间隔2刀位换刀、间隔3刀位换刀、间隔4刀位换刀、间隔5刀位换刀六种情况,前五种换刀情况都有正转、反转各12种正转换法,间隔5刀位换刀只有12种正转换法,共有132种换法。相对应的三联齿盘运转试验表如下:
3)按照上述三联齿盘运转试验表,控制台7发送指令给液压缸:第二液压缸52控制第二动齿盘41与第二内齿盘42,第二外齿盘43的分离与啮合;控制台7发送指令给第二驱动电机54控制三联齿盘内齿盘运转;每次三联齿盘运转试验都包含上述两个动作,其中第一驱动电机14运转角度由三联齿盘运转试验表决定;4)每次运转试验在12面棱体检测软件记录试验数据,直至全部运转试验结束;5)a三联齿盘试验前精度检测实验结束,控制台7发送指令,控制平移驱动电机955运转通过丝杠螺母副带动检测单元9移动,直至多棱体安装轴921与第二内齿盘42解除配合,和检测单元回到非工作位。
33.(5)三联齿盘加载1)三联齿盘运转谱编制:这里采用12刀位数控刀架运转过程对应三联齿盘运转情况为例,其他同上;按照12个刀位刀架进行的132次三联齿盘运转试验:一次转位过程可分为间隔0刀位换刀、间隔1刀位换刀、间隔2刀位换刀、间隔3刀位换刀、间隔4刀位换刀、间隔5刀位换刀六种情况,前五种换刀情况都有正转、反转各12种正转换法,间隔5刀位换刀只有12种正转换法,共有132种换法。相对应的三联齿盘运转试验表如下:
2)三联齿盘载荷谱编制:采用数控刀架在实际切削过程中切削力分析结果,并将其转换为三联齿盘受力情况搭建三联齿盘载荷谱参阅图6、图7三联齿盘载荷谱搭建步骤如下:step1 采集切削力样本数据;step2 选取最小样本;step3 截取信号进行预处理,去除奇异点;step4 采用雨流计数法处理预处理过得信号得到切削力载荷均值、幅值、切削力方向;step5 根据切削力受力分析,计算切削力均值在轴向分力及三联齿盘所受载荷均值;step6 根据算得的三联齿盘载荷力均值、幅值编制三联齿盘载荷谱。
34.参阅图6,所述的雨流计数法又称作“塔顶法”,其过程如同对雨滴从塔顶流下的轨迹进行计数统计,雨流计数的过程主要包括数据压缩和循环数的提取两个步骤。其中数据压缩是去除无效幅值数据,保留载荷数据中有效的峰谷值,将载荷时间历程处理成便于计数的数组;循环数提取的方法常见的有三点法和四点法。由于四点法在统计计数之前不需要进行重新排列,直接利用两个峰值和两个谷值数据就可以进行提取,所以被广泛使用。首先从载荷时间历程中提取出四个连续的极值点,,,,如果满足式1所示的判定依据,则确定一个载荷全循环 ;然后去除掉中间两个数据点,再读取两个新的数据点,继续用式1进行判断;如果不满足,则舍弃第一个数据点,重新读取第五个数据点,继续进行判定,以此类推,直到提取完所有的载荷数据点。对于提取完全循环后剩余的数据点,则可形成残余半循环;(1)参阅图7:所述的切削力受力分析,通过式2将切削力径向力计算出,从而得到三联齿盘加载力均值;
(2)某一实际工况下,由数控刀架实采数据按照上述方法编制的载荷谱如下:3)三联齿盘可靠性试验谱编制所述的三联齿盘可靠性试验谱由三联齿盘运转谱和三联齿盘载荷谱联合构成;这里采用12刀位数控刀架实际工况情况为例;所述的三联齿盘可靠性试验谱为首先按照三联齿盘运载谱间隔0刀位进行运转试验,后按照三联齿盘均幅值表进行加载,加载频率为6hz,后继续按照三联齿盘运转谱进行相隔1刀位运转,以此类推,对应关系为相隔0刀位-6hz,相隔1刀位-15hz,相隔2刀位-21hz,相隔3刀位-28hz,相隔4刀位-41hz,相隔5刀位运转。这里试验时间可以自定,一般选取总时间为2h。
35.(6)试验后三联齿盘精度检测a三联齿盘定位精度、重复定位精度检测1)控制台7发送指令,控制平移驱动电机955运转通过丝杠螺母副带动检测单元9移动,直至多棱体安装轴921与第一内齿盘22内孔配合上;2)制定齿盘运转方案,这里以12刀位数控刀架的三联齿盘运转方案为例,其他刀位数控刀架运转方案同上;按照12个刀位刀架进行的132次三联齿盘运转试验:一次转位过程可分为间隔0刀位换刀、间隔1刀位换刀、间隔2刀位换刀、间隔3刀位换刀、间隔4刀位换刀、间隔5刀位换刀六种情况,前五种换刀情况都有正转、反转各12种正转换法,间隔5刀位换刀只有12种正转换法,共有132种换法。相对应的三联齿盘运转试验表如下:
3)按照上述三联齿盘运转试验表,控制台发送指令给第一液压缸12控制第一动齿盘21与第一内齿盘22,第一外齿盘23的分离与啮合,控制台7发送指令给第一驱动电机14控制三联齿盘内齿盘运转;每次三联齿盘运转试验都包含上述两个动作,其中第一驱动电机14运转角度由三联齿盘运转试验表决定;4)每次运转试验在12面棱体检测软件记录试验数据,直至全部运转试验结束;5)a三联齿盘试验前精度检测实验结束,控制台7发送指令,控制平移驱动电机955运转通过丝杠螺母副带动检测单元9移动,直至多棱体安装轴921与第一内齿盘22解除配合,和检测单元回到非工作位。
36.b三联齿盘定位精度、重复定位精度检测1)控制台7发送指令,控制平移驱动电机955运转通过丝杠螺母副带动检测单元9移动,直至1多棱体安装轴921与第一内齿盘22内孔配合上;2)制定齿盘运转方案,这里以12刀位数控刀架的三联齿盘运转方案为例,其他刀位数控刀架运转方案同上;按照12个刀位刀架进行的132次三联齿盘运转试验:一次转位过程可分为间隔0刀位换刀、间隔1刀位换刀、间隔2刀位换刀、间隔3刀位换刀、间隔4刀位换刀、间隔5刀位换刀六种情况,前五种换刀情况都有正转、反转各12种正转换法,间隔5刀位换刀只有12种正转换法,共有132种换法;相对应的三联齿盘运转试验表如下:
3)按照上述三联齿盘运转试验表,控制台发送指令给第二液压缸52控制第二动齿盘41与第二内齿盘42,第二外齿盘43的分离与啮合,控制台7发送指令给第二驱动电机54控制三联齿盘内齿盘运转;每次三联齿盘运转试验都包含上述两个动作,其中第二驱动电机54运转角度由三联齿盘运转试验表决定;4)每次运转试验在12面棱体检测软件记录试验数据,直至全部运转试验结束;5)a三联齿盘试验前精度检测实验结束,控制台7发送指令,控制平移驱动电机955运转通过丝杠螺母副带动检测单元9移动,直至多棱体安装轴921与第二内齿盘42解除配合,和检测单元回到非工作位;(7)调整试验台至非工作位控制台7发送指令,调整三联齿盘运转部分至三联齿盘分离工作位,调整检测单元至两三联齿盘中间位置。
37.(8)数据分析将采集到的精度指标以向量的形式存放入控制台7,进行长时间多次了靠性试验后,以时间为横坐标,每次三联齿盘可靠性试验的到的试验后检测数据为变量代入可靠性模型分析,得到对应的可靠性指标;所述的可靠性模型包括维纳过程、逆高斯过程、伽马模型等退化模型。
38.(9)关闭设备1)关闭液压站。
39.2)关闭液压控制软件、电机控制软件、12面棱体检测软件、压电陶瓷控制软件,关闭工控机3)关闭电源,结束实验。
40.本发明中所述的实施例是为了便于该技术领域的技术人员能够理解和应用本发明,本发明只是一种优化的实施例,或者说是一种较佳的具体的技术方案,它只适用于一定范围内的不同型号,外齿盘外径一致的动力刀架的三联齿盘的可靠性试验,范围之外的不同型号,不同尺寸的动力伺服刀架的可靠性试验,基本的技术方案不变,但其所用零部件的规格型号将随之改变,如箱体通孔内径,12面棱体安装轴两端直径等,故本发明不限于实施
这一种比较具体技术方案的描述。本发明中所提出的可靠性试验方法不仅适用于本发明中所提出的试验装置才能进行,同样适用于所有三联齿盘可靠性实验装置,针对于不同类型的可靠性试验装置,都可在本可靠性试验方法中选取不同的运转谱、加载谱、可靠性试验模型等。如果相关的技术人员在坚持本发明基本技术方案的情况下做出不需要经过创造性劳动的等效结构变化或各种修改都在本发明的保护范围内。