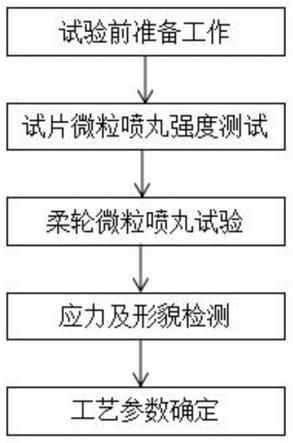
1.本发明涉及机械表面加工技术领域,尤其涉及一种获取微粒喷丸谐波柔轮表面强化加工参数的试验方法。
背景技术:2.谐波柔轮作为高性能精密齿轮的典型代表,广泛应用于航空航天、卫星通信、武器军工、工业机器人、医疗器械等装备。尽管其受力分析、齿面修形、抗磨性能等方面已有研究,但并没有为谐波传动提供长寿命高可靠性的解决方案。如何在保障尺寸精度的前提下,实现材料性能强化并提高其服役寿命一直以来都是工程难题。
3.微粒喷丸作为一种特殊的喷丸工艺,采用直径小于0.1mm弹丸以100m/s 以上的喷射速度不断撞击零件表面。该技术细化了表面晶粒并产生纳米化,表面粗糙度远小于常规喷丸减缓了表面疲劳裂纹的产生,同时也保障了一定的残余应力层,提高了零件的表面硬度,兼顾了表面微观形貌与残余应力,并提高零件疲劳性能,为高性能精密齿轮等零部件表面精细强化提供了可能。
4.尽管有一些企业尝试使用微粒喷丸技术提高零部件的疲劳寿命,但受限于试验设备和丸粒制造工艺以及精密齿轮的加工成本,目前尚无法开展大量工艺试验以确定最优工艺参数。
5.中国专利文献cn 112708853 a公开了一种微粒子喷丸后处理改善alcrn涂层刀具性能的加工方法,它利用微粒喷丸处理了alcrn涂层刀具,降低了涂层表面粗糙度,改善了涂层抗摩擦磨损性能和切削性能。但只证明了微粒喷丸对涂层性能有显著影响变化,没有提供微粒喷丸的最优工艺参数以指导实际生产加工,也没有将其微粒喷丸技术应用至高精密零部件。
技术实现要素:6.本发明的目的是提供一种获取微粒喷丸谐波柔轮表面强化加工参数的试验方法,确定了较佳的加工工艺参数,强化高精密齿轮的表面质量。
7.为解决上述技术问题,本发明采用如下技术方案:
8.本发明一种获取微粒喷丸谐波柔轮表面强化加工参数的试验方法,具体包括以下步骤:
9.步骤一、试验前准备工作:包括喷丸机清理、almen试片夹具制作、谐波柔轮夹具制作、微粒弹丸准备与填充、喷枪定位;
10.步骤二、试片微粒喷丸强度测试,进行n型almen试片微粒喷丸强度测试,绘制弧高度-时间曲线,确认喷丸强度和喷丸时间;
11.步骤三、柔轮微粒喷丸试验,根据确定的气压、喷射距离、流量保持的喷丸强度及饱和强度的试件进行柔轮微粒喷丸试验;
12.步骤四、应力与表面形貌检测,检测微粒喷丸前后的谐波柔轮齿根处残余应力与
表面形貌;
13.步骤五、工艺参数确定,对比步骤四中的检测结果,基于残余应力与表面粗糙度结果,确定较佳的谐波柔轮微粒喷丸工艺参数。
14.进一步的,所述步骤一中,所述微粒弹丸为高速钢丸,平均直径为50μm。
15.进一步的,所述步骤一中,喷丸室内设置有喷丸机,所述喷丸机包括旋转操作台和喷枪,试验前,首先要对喷枪上弹丸储存装置与管道清理干净,消除上面的杂质和灰尘;其次,准备好微粒弹丸、谐波柔轮、柔轮夹具、n型almen 试片及almen试片夹具备用。
16.进一步的,所述步骤二中,首先将almen试片夹具安装到旋转操作台上,再采用弧高仪测量实验前的n型almen试片的弧高值,并将其安装到almen试片夹具上,调整喷枪的位置与喷射角度,使得喷射口中心正对所述almen试片中心;所述步骤三中,首先将柔轮夹具安装到旋转操作台上,再将选好的谐波柔轮连接到柔轮夹具上,调整喷枪的位置与喷射角度,使得喷射口中心正对所述谐波柔轮齿面;
17.试验前,在丸粒储存装置中填充微粒弹丸,两组试验时almen试片与谐波柔轮均随旋转操作台做匀速转动,喷枪垂直于旋转操作台的转轴定位。
18.进一步的,所述喷枪的喷射口与almen试片的受喷表面距离设置为150mm,所述旋转操作台设置为匀速转动。
19.进一步的,所述步骤二中,接通喷丸机电源,调节喷丸流量与喷丸气压,喷射时间分别为4s、8s、16s、32s,微粒喷丸结束后取下almen试片,采用弧高仪测量其弧高值,计算在该喷射气压下的微粒喷丸强度与达到饱和时的微粒喷丸时间。
20.进一步的,所述步骤四中采用表面形貌测量仪器,测量微粒喷丸前后的谐波柔轮的表面微观形貌,同一测量点需经过三次以上重复测量;再使用显微镜视图处理软件截取齿根处的表面微观形貌进行分析,然后去除齿根处的曲率半径并计算表面粗糙度sa与sq,将多次测量结果求平均值。
21.与现有技术相比,本发明的有益技术效果:
22.本发明获取微粒喷丸谐波柔轮表面强化加工参数的试验方法,具体经过试验前准备工作、试片微粒喷丸强度测试、柔轮微粒喷丸试验、应力与表面形貌检测和工艺参数确定五个步骤,为谐波柔轮等小模数精密齿轮强化加工的过程和数据提供提供了一种可行的数据获取试验方法,该试验探究了不同微粒喷丸强度下的表面粗糙度与表面残余应力变化趋势,并指导了谐波柔轮微粒喷丸强化的工艺参数的制定。
附图说明
23.下面结合附图说明对本发明作进一步说明。
24.图1为本发明获取微粒喷丸谐波柔轮表面强化加工参数的试验方法流程图;
25.图2为本发明谐波柔轮示意图;
26.图3为本发明谐波柔轮喷丸试验的示意图;
27.图4为本发明微粒喷丸前后谐波柔轮齿根表面形貌示意图;
28.图5为本发明微粒喷丸前后的表面粗糙度对比曲线图;
29.图6为本发明微粒喷丸前后的表面残余应力对比图;
30.附图标记说明:1、谐波柔轮;2、柔轮夹具;3、旋转操作台;4、喷枪;5、微粒弹丸。
具体实施方式
31.如图1-6所示,一种获取微粒喷丸谐波柔轮表面强化加工参数的试验方法,具体包括以下步骤:
32.步骤一、试验前准备工作:包括喷丸机清理、almen试片夹具制作、谐波柔轮夹具制作、微粒弹丸准备与填充、喷枪定位;
33.步骤二、试片微粒喷丸强度测试,进行n型almen试片微粒喷丸强度测试,绘制弧高度-时间曲线,确认喷丸强度和喷丸时间;
34.步骤三、柔轮微粒喷丸试验,根据确定的气压、喷射距离、流量保持的喷丸强度及饱和强度的试件进行柔轮微粒喷丸试验;
35.步骤四、应力与表面形貌检测,检测微粒喷丸前后的谐波柔轮齿根处残余应力与表面形貌;
36.步骤五、工艺参数确定,对比步骤四中的检测结果,基于残余应力与表面粗糙度结果,确定较佳的谐波柔轮微粒喷丸工艺参数。
37.具体的,所述步骤一中,所述微粒弹丸为高速钢丸,平均直径为50μm。所述步骤一中,喷丸室内设置有喷丸机,所述喷丸机包括旋转操作台3和喷枪4,试验前,首先要对喷枪4上弹丸储存装置与管道清理干净,消除上面的杂质和灰尘;其次,准备好微粒弹丸5、谐波柔轮1、柔轮夹具2、n型almen试片及 almen试片夹具备用。
38.具体的,所述步骤二中,首先将almen试片夹具安装到旋转操作台3上,再采用弧高仪测量实验前的n型almen试片的弧高值,并将其安装到almen试片夹具上,调整喷枪4的位置与喷射角度,使得喷射口中心正对所述almen试片中心;
39.所述步骤三中,首先将柔轮夹具2安装到旋转操作台3上,再将选好的谐波柔轮1连接到柔轮夹具2上,调整喷枪4的位置与喷射角度,使得喷射口中心正对所述谐波柔轮1齿面;
40.试验前,在丸粒储存装置中填充微粒弹丸,两组试验时almen试片与谐波柔轮均随旋转操作台3做匀速转动,喷枪4垂直于旋转操作台3的转轴定位。
41.具体的,所述喷枪4的与almen试片的受喷表面距离设置为150mm,所述旋转操作台3设置为匀速转动。
42.具体的,所述步骤二中,接通喷丸机电源,调节喷丸流量与喷丸气压,喷射时间分别为4s、8s、16s、32s,微粒喷丸结束后取下almen试片,采用弧高仪测量其弧高值,计算在该喷射气压下的微粒喷丸强度与达到饱和时的微粒喷丸时间。
43.具体的,所述步骤四中采用表面形貌测量仪器,测量微粒喷丸前后的谐波柔轮的表面微观形貌,同一测量点需经过三次以上重复测量;再使用显微镜视图处理软件截取齿根处的表面微观形貌进行分析,然后去除齿根处的曲率半径并计算表面粗糙度sa与sq,将多次测量结果求平均值。
44.本发明的具体实施过程如下:
45.首先,本实施例以30crmnsia的谐波双圆弧柔轮为例,试件与齿廓几何如图2所示,其材料参数如下:
46.齿数z=200压力角α0=20
°
制造过程粗加工-热处理-精加工模数m0=0.00315m泊松比v=0.3杨氏模量e=210gpa屈服极限σy=835mpa硬度hv0.1=500
47.步骤一、微粒喷丸试验前准备工作:首先清理喷丸机的丸粒储存装置与管道,避免弹丸中混入杂质与灰尘;然后在丸粒储存装置中填充微粒弹丸,丸粒型号为sbm300,平均直径为50μm;在喷丸机的旋转操作台3的中心固定almen 试片夹具,并安装n型almen试片;喷枪口内径选定为8mm,调节喷枪位置与喷射角度,使喷枪口距离受喷表面150mm,同时使丸粒入射方向垂直于受喷表面,具体的安装位置如图3所示。
48.步骤二、微粒喷丸工艺试验。接通喷丸机电源,调节喷丸流量至25kg/min,先调节喷丸气压至0.6mpa,让旋转操作台3做转速为1.571rad/s的匀速转动,喷射时间分别为4s、8s、16s、32s;微粒喷丸结束后取下almen试片,采用弧高仪测量其弧高值,计算喷射气压为0.6mpa时的微粒喷丸强度与达到饱和时的微粒喷丸时间。然后,按照上述过程依次获得喷射气压分别为0.15mpa、0.3 mpa、0.4mpa时的微粒喷丸强度与达到饱和的微粒喷丸时间。
49.由于达到饱和时的时间相差不大,固定微粒喷丸时间为21s使覆盖率达到 200%。喷射气压分别为0.15mpa、0.3mpa、0.4mpa、0.6mpa时对应的喷射强度分别为0.07mmn、0.09mmn、0.12mmn、0.15mmn。
50.步骤三、谐波柔轮1微粒喷丸工艺试验,取下almen试片夹具更换为柔轮夹具2,根据步骤二中的工艺参数对谐波柔轮样件进行强度分别为0.07mmn、 0.09mmn、0.12mmn、0.15mmn的微粒喷丸处理。喷丸过程如图3所示。
51.步骤四、微粒喷丸前后的表面形貌与表面残余应力检测。
52.测量微粒喷丸前的谐波柔轮的表面微观形貌。采用表面形貌测量仪器,例如白光干涉仪,超景深三维探测仪等测量微粒喷丸前后的谐波柔轮的表面微观形貌,同一测量点经过三次以上重复测量。由于白光干涉仪的测量光斑大小为1 mm*1mm,大于谐波柔轮的齿形轮廓,故使用显微镜视图处理软件截取齿根处的表面微观形貌进行分析。然后去除齿根处的曲率半径并计算表面粗糙度sa与sq,将多次测量结果求平均值。具体测量与数据处理过程如图4、5所示。
53.图5所示为微粒喷丸前后的表面粗糙度对比曲线,可以发现对于谐波柔轮这种硬度较低的材料,微粒喷丸处理也会增大表面粗糙度。当喷丸强度为0.07 mmn时,表面粗糙度sa为0.6μm。随着微粒喷丸强度的增大,表面粗糙度sa 与sq逐渐增大。工程中一般要求柔轮表面粗糙度不超过0.8μm。如果选用较小的喷丸强度,则表面粗糙度仍符合加工要求。
54.图6所示为微粒喷丸前后的表面残余应力对比结果,可以发现经过微粒喷丸处理之后,表面残余压应力有着明显的提升,从未处理的273mpa提升至420 mpa左右,但随着喷丸强度的增大,表面残余压应力并没有随之增大,而是维持在420mpa左右。可见在低喷射强度时,残余压应力已经达到饱和。这种残余应力饱和现象的记载了可参见,“喷丸产生的残余压应力”,s.wang,y.li, m.yao,和r.wang,材料加工工艺学报,第73卷,第64-73页,1998年。
55.对于这种微粒喷丸工艺组合下的谐波柔轮,即使增大喷丸强度也不能进一步提升残余压应力。故建议选择低微粒喷丸强度,可以在保证柔轮残余压应力的同时,将表面粗糙度sa控制在0.6μm以内。
56.以上所述的实施例仅是对本发明的优选方式进行描述,并非对本发明的范围进行限定,在不脱离本发明设计精神的前提下,本领域普通技术人员对本发明的技术方案做出的各种变形和改进,均应落入本发明权利要求书确定的保护范围内。