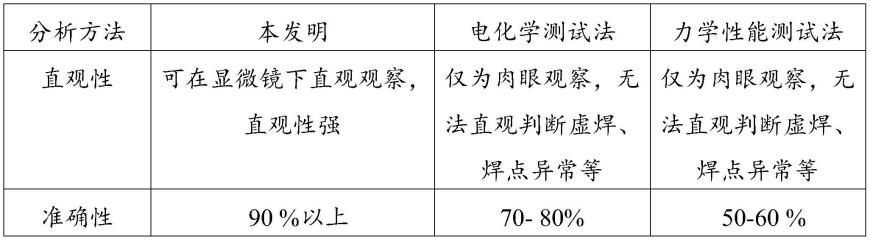
1.本发明属于电池焊点形貌测试技术领域,具体涉及一种电池极耳焊点形貌的分析方法。
背景技术:2.电池作为高能量密度、高功率密度的储能设备,其工艺可靠性与使用安全性直接影响产品的安全性和可靠性。近年来,由于电池载体设备的功率不断增大,使得电池向大电流、高功率、快速充放电方向发展,由于部分电池存在工艺质量问题,导致电池鼓包、热失控等失效事故频发。据统计,在相关可移动电子产品电池失效案例中,30%以上的事故由于极耳工艺缺陷造成,极耳作为连接外部设备与电芯的关键部件,其工艺质量与焊接质量对电池的安全性与可靠性有着非常大的影响。极耳焊接处的工艺质量差会导致电池焊接阻抗大,当电池在大电流下充放电时,容易引起热量积累,造成极耳附近的隔膜、集流体、活性物质长时间过热而损伤,最终引起电池局部内短路、热失控等安全事故。
3.目前,工业上对极耳焊接状况的测试方法主要是用力学的方法评估极耳与集流体之间的焊接强度来间接判断极耳焊接的情况;也有用简单的电化学测试,如测电池的阻抗值是否在规定值范围内来判断焊点的整体情况。这两种极耳焊接情况的判定方法虽然能在一定程度上整体、快速的判断极耳焊接工艺的质量。但都是间接分析焊点的焊接情况,并没有关注到焊点的焊接工艺,不能够深入、直观地判断焊点的虚焊程度、虚焊原因等;也不能直观、形象地表征出焊点与集流体的连接情况。因此,传统的测试方法不能为极耳焊点的深入分析和工艺改进提供依据,形成焊接参数与焊点质量之间的“参数-效果关系”。
技术实现要素:4.本发明提出一种电池极耳焊点形貌的分析方法,以解决现有技术中存在的一个或多个技术问题,至少提供一种有益的选择或创造条件。
5.为克服上述技术问题,本发明通过对电池极耳的焊点区域进行切片样品制备,并采用显微镜对焊点的形貌进行分析,提出了一种电池极耳焊点形貌的分析方法,该方法提供一种直观、准确、可深入分析极耳焊点形貌的方法,为极耳焊接方法及参数的调整提供有效的依据,从而促进产品的可靠性提升。
6.本发明所采取的技术方案是:一种电池极耳焊点形貌的分析方法,包括以下步骤:
7.(1)对电池极耳的焊点区域进行切片处理,得切片样品;
8.(2)采用显微镜观测并测量所述切片样品中所有凹坑的深度,分别记为x1、x2、x3......xn,通过式ⅰ判断所述切片样品中焊点的异常情况:
9.k=(|x
r-xn|/xr)
×
100%
ꢀꢀꢀ
(式ⅰ)
10.其中:k表示每个凹坑深度与平均凹坑深度的差值比;xr表示所有凹坑深度的平均值。
11.具体地,本发明的电池极耳焊点形貌的分析方法,先对电池极耳的焊点区域进行
100mm2内。
29.优选的,所述打磨采用先粗后细的砂纸依次进行打磨。
30.进一步优选的,所述打磨先采用400目的砂纸打磨至透明,然后用400目、1000目、1500目、3000目的砂纸依次进行打磨,打磨至距离标记位置100-500μm处。
31.作为上述方案的进一步改进,步骤(2)中,所述显微镜为光学显微镜、体式显微镜、金相显微镜中的任一种。
32.优选的,步骤(2)中,所述显微镜的倍数为10-100。
33.相对于现有技术,本发明至少具有如下技术效果或优点:
34.本发明通过对电池极耳的焊点区域进行切片样品制备,并采用显微镜对焊点的形貌进行分析,提出了采用每个切片样品中凹坑深度与平均凹坑深度的差值比k,用于判断切片样品中焊点的异常情况的方法。该方法相对于传统的通过电化学或力学等间接分析方法更为直观、有效,准确率可达90%以上。同时,采用本发明的电池极耳焊点形貌的分析方法,还可准确掌握焊点的尺寸,筛查焊点与集流体的焊接工艺情况,为极耳焊接方法及参数的调整提供有效的依据,促进电池产品的可靠性提升。
附图说明
35.图1为实施例1的负极极耳及其焊点的形貌切片图;
36.图2为实施例2的正极极耳及其焊点的形貌切片图。
具体实施方式
37.以下通过实施例对本发明进行具体描述,以便于所属技术领域的人员对本发明的理解,有必要在此特别指出的是,实施例只是用于对本发明做进一步说明,不能理解为对本发明保护范围的限制,所属领域技术人员,根据上述发明内容对本发明作出的非本质性的改进和调整,应仍属于本发明的保护范围,同时,下述所提及的原料未详细说明的,均为市售产品,未详细提及的工艺步骤或制备方法均为本领域技术人员所知晓的工艺步骤或制备方法。
38.实施例1
39.本实施例分析的是锂离子电池,为容量小于2ah的消费类软包电池;负极极耳k大于8%的可视为异常焊点。
40.一种电池极耳焊点形貌的分析方法,包括以下步骤:
41.(1)将待分析的电池在充放电设备下放电至电压为0v,并在惰性气体手套箱中将电池拆解,将待分析极耳连同与其焊连的集流体一同剪下,作为切片对象,待分析极耳包括正极极耳和负极极耳,其中:正极极耳为铝还与铝箔;负极极耳为镍带与铜箔;
42.(2)在光学显微镜下,在10倍数下观察待分析极耳的凸起面和下凹面,寻找极耳处存在下凹面过深、凸起面过于尖锐等情况缺陷的焊点,定位待分析极耳的缺陷焊点对应位置,并记录。
43.(3)将待测极耳先后用丙酮和乙醇洗净,将极耳焊接的集流体基底保留,取待观察焊点周围20mm2的区域范围,用双酚f型环氧树脂和酚醛环氧树脂为固化剂,固化时间为6h;固化后,将表面先用400目的粗砂纸打磨透明,定位要观察的焊点区域,并做标记,再分别用
400、1000、1500目的砂纸依次打磨,待打磨接近标记位置100μm距离时,用光学显微镜在10倍数下进行观测;
44.(4)观测并测量电池负极极耳切片样品中所有凹坑的深度,x1、x2、x3……
x8,分别为10μm、10.6μm、9.6μm、9.5μm、9.8μm、10.2μm、10.5μm、10.3μm,去除一个最高值10.6μm和一个最低值9.5μm,计算凹坑深度平均值xr为10.06μm,计算每个凹坑深度与平均深度的差值比k=(|x
r-xn|/xr)
×
100%为0.6%、4.37%、4.57%、5.57%、2.58%、1.39%、4.37%、2.39%,未存在k值大于8%的焊点,因此结论为未见异常。
45.本实施例的负极极耳及其焊点的形貌切片图如图1所示,其中图1(a)为正常焊点的整体形貌图;图1(b)为图1(a)中指定区域的显微结构放大图。由图1可知,正常电池极耳焊点分布均匀,并可通过显微结构精确测量焊点的深度。
46.上述分析结果与电化学阻抗分析结论相吻合,表明本发明的分析方法是可靠的。
47.实施例2
48.本实施例分析的是锂离子电池,为容量小于2ah的消费类软包电池,正极极耳k大于5%的可视为异常焊点。
49.一种电池极耳焊点形貌的分析方法,包括以下步骤:
50.(1)将待分析的电池在充放电设备下放电至电压为0v,并在惰性气体手套箱中将电池拆解,将待分析极耳连同与其焊连的集流体一同剪下,作为切片对象,待分析极耳包括正极极耳和负极极耳,其中:正极极耳为铝还与铝箔;负极极耳为镍带与铜箔;
51.(2)在体式显微镜下,在25倍数下观察待分析极耳的凸起面和下凹面,寻找极耳处存在下凹面过深、凸起面过于尖锐等情况缺陷的焊点,定位待分析极耳的缺陷焊点对应位置,并记录。
52.(3)将待测极耳先后用碳酸二乙酯、丙酮和乙醇洗净,将极耳焊接的集流体基底保留,取待观察焊点周围60mm2的区域范围,用双酚f型环氧树脂和酚醛环氧树脂为固化剂,固化时间为12h;固化后,将表面先用400目的粗砂纸打磨透明,定位要观察的焊点区域,并做标记,再分别用400、1000、1500目的砂纸依次打磨,待打磨接近标记位置200μm距离时,用金相显微镜在50倍数下进行观测;
53.(4)观测并测量电池负极极耳切片样品中所有凹坑的深度,x1、x2、x3……
x8,分别为6.1μm、6.2μm、5.8μm、5.4μm、5.7μm、6μm、6.3μm、6.1μm,去除一个最高值6.3μm和一个最低值5.4μm,计算凹坑深度平均值xr为5.98μm,计算每个凹坑深度与平均深度的差值比k=(|x
r-xn|/xr)
×
100%为2.00%、3.58%、3.01%、9.70%、4.68%、3.34%、5.35%、2.00%,则x4和x7为异常点,x4可能存在焊接过浅,x7可能存在焊接过深的情况,待进一步观察;同时,观测凹坑另一面,存在开裂现象的为异常焊点。
54.本实施例的正极极耳及其焊点的形貌切片图如图2所示,其中:图2(a)为异常焊点的整体形貌图;图2(b)为图2(a)中指定区域的显微结构放大图。由图2可知,异常电池极耳焊点的分布不均匀,通过显微结构放大图可知,焊点过浅,并存在与集流体焊接不良的现象。
55.上述分析结果与电化学阻抗分析结论相吻合,表明本发明的分析方法是可靠的。
56.实施例3
57.本实施例分析的是锂离子电池,为容量大于2ah的动力锂离子电池;负极极耳k大
于10%的可视为异常焊点。
58.一种电池极耳焊点形貌的分析方法,包括以下步骤:
59.(1)将待分析的电池在充放电设备下放电至电压为0v,并在惰性气体手套箱中将电池拆解,将待分析极耳连同与其焊连的集流体一同剪下,作为切片对象,待分析极耳包括正极极耳和负极极耳,其中:正极极耳为铝还与铝箔;负极极耳为镍带与铜箔;
60.(2)在金相显微镜下,在40倍数下观察待分析极耳的凸起面和下凹面,寻找极耳处存在下凹面过深、凸起面过于尖锐等情况缺陷的焊点,定位待分析极耳的缺陷焊点对应位置,并记录。
61.(3)将待测极耳先后用碳酸二乙酯、乙醇洗净,将极耳焊接的集流体基底保留,取待观察焊点周围100mm2的区域范围,用双酚f型环氧树脂和酚醛环氧树脂为固化剂,固化时间为18h;固化后,将表面先用400目的粗砂纸打磨透明,定位要观察的焊点区域,并做标记,再分别用400、1000、1500目的砂纸依次打磨,待打磨接近标记位置500μm距离时,用体式显微镜在100倍数下进行观测;
62.(4)观测并测量电池负极极耳切片样品中所有凹坑的深度,x1、x2、x3……
x8,分别为14.2μm、14.5μm、14.1μm、14.3μm、14.6μm、13.9μm、14.3μm、14.1μm,去除一个最高值14.6μm和一个最低值13.9μm,计算凹坑深度平均值xr为14.25μm,计算每个凹坑深度与平均深度的差值比k=(|x
r-xn|/xr)
×
100%为0.35%、1.72%、1.06%、3.50%、2.40%、2.52%、3.50%、1.06%,未存在k值大于8%的焊点,因此结论为未见异常。
63.上述分析结果与电化学阻抗分析结论相吻合,表明本发明的分析方法是可靠的。
64.效益对比:
65.将本发明的电池极耳焊点形貌的分析方法与传统的电化学或力学等间接分析方法的优缺点进行对比,结果如表1所示:
66.表1:本发明的电池极耳焊点形貌的分析方法与传统方法对比表
[0067][0068]
由表1可知,传统的电化学或力学测试方法相对于本发明的电池极耳焊点形貌的分析方法,无法实现直观地表征出焊点与集流体的连接情况,更不能为极耳焊点的深入分析和工艺改进提供提供依据,促进产品的可靠性提供。更为重要的是,本发明的电池极耳焊点形貌的分析方法的准确率可达90%以上,远远高于传统的测试方法。
[0069]
显然,上述实施例仅是为清楚地说明所作的举例,而并非对实施方式的限定。对于所属领域的普通技术人员来说,在上述说明的基础上还可以做出其它不同形式的变化或变动。这里无需也无法对所有的实施方式予以穷举。而由此所引伸出的显而易见的变化或变动仍处于本发明的保护范围之中。