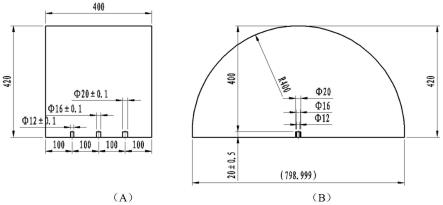
1.本发明属于连铸圆坯检测技术领域,具体涉及一种大规格连铸圆坯的超声波检测进行低倍评估方法。
背景技术:2.目前连铸坯内部宏观质量检验手段通常采用破坏性低倍检测,而低倍抽样检验只能检查一个截面,由于铸坯中心区域宏观缺陷成断续分布,因此低倍抽样检验结果检测比例低、结果偏差大、取样检验周期长,与实物质量往往存在偏差,且有质量损失,经济性差。
3.超声波无损检测方法可对钢材内部百分百检验,并且检验结果可以量化评估。但大规格连铸圆坯由于尺寸大、铸态组织不致密、不均匀、晶粒粗大,且连铸圆表面振痕深、氧化层厚,导致耦合性差、超声波能量穿透性低,粗大铸态组织使超声波的散射与吸收衰减严重,超声波探伤的信噪比差,超声波穿透能量低、缺陷评判困难。故目前,暂无对大钢锭、大连铸圆实现超声波探伤检验,同时缺少对应的检验规范与评判准则。
技术实现要素:4.本发明所要解决的问题是对大连铸圆坯实现超声波检测,得出不同钢种、规格的超声波探伤反射特征与低倍组织、缺陷的对应关系,制定连铸坯超声波探伤的检验规范。
5.对连铸坯表面进行处理去除氧化层,利用大功率探伤设备和低频探头解决了大规格连铸圆坯粗晶、中心疏松导致超声波衰减大、杂波多的问题。探伤时周向扫查面大于等于180
°
,粗糙表面采用喷丸、合适耦合剂、探头移动可采用触点法,沿连铸圆纵向成“w”型扫查,保证声束的有效覆盖,使用dgs底波法来调节灵敏度、平底孔试块验证探伤结果可靠性,当发现存在超记录当量反射时,前后移动探头采用6db法测出缺陷长度尺寸。
6.通过缺陷波与低倍组织结合研究,探索出不同钢种、规格的超声波探伤起始当量、基准当量、缺陷反射当量、底波降低量及反射波型特征与低倍组织、缺陷的对应关系。连铸圆探伤按铸坯规格的不同分为不同的判定等级。按超声波反射特征值分中心疏松、缩孔、中心裂纹三种低倍缺陷,实现对大规格连铸圆坯超声波无损检测。
7.为了实现以上目的,本发明的具体步骤如下:
8.(1)仪器与探头选择:
9.为保证超声波能量穿透性,采用方波功能a型脉冲反射式超声波探伤仪,发射电压最大调制范围400~500v;探头选用带软保护膜探头,晶片直径为ф20~ф34,探头工作频率为0.5mhz~2mhz;
10.(2)探伤前准备:
11.s1.对连铸圆坯表面进行处理,去除连铸圆坯表面的氧化层,连铸圆坯表面氧化层处理后,在其表面涂覆耦合剂;因振痕引起表面粗糙,耦合剂选用融水性化学浆糊与水混合均匀得到的粘稠状混合物,将耦合剂均匀涂在连铸圆坯表面;探头带软保护膜,保证探头激发超声波能量有效透过耦合层穿透铸态组织。
12.s2.可探性测试:验证所选仪器与探头发射声波频率对连铸圆坯具备穿透性好,噪声信号低的要求;第一,选择仪器与探头后,将被探连铸圆坯一次底波调至80%、灵敏度余量不小于10db、噪声信号不超20%;第二,第一次底波与第二次底波灵敏度db差不大于8db;
13.经过可探性测试检测后,满足上述二个条件,说明连铸圆坯可进行超声波探伤;
14.(3)探伤过程;
15.(a)探伤信噪比:探头频率选用以仪器屏幕显示信噪比大于等于6db为原则;
16.(b)零位与声速校准:大规格连铸圆坯组织均匀差、尺寸大,定位与定量误差大;首先进行零位与声速校准,进入超声波探伤仪的校准界面,将被探伤连铸圆坯1倍直径设定为参考值1;2倍直径设定为参考值2,确定后完成零位与声速校准;
17.(c)灵敏度调整:选用的仪器和探头具备距离波幅曲线(dgs)功能,使用dgs曲线法来调节灵敏度;
18.具体操作:使用超声波探伤常用灵敏度调整方法,大平底调整dgs曲线、记录当量为dgs调整值;探头紧贴在连铸圆坯的圆弧面,将超声波探伤仪的闸门移至连铸圆坯一次底波回波上,调整灵敏度,将一次底波高度调整到80%底面回波(bw),在连铸圆坯表面选取三处以上不同位置、取平均值,稳住探头记录dgs参考值,确定后完成dgs曲线制作,即完成灵敏度调整;
19.(d)扫查:在原灵敏度调整的基础上提高2~6db作为扫查灵敏度,二种不同表面氧化层处理方法的扫查要求;
20.s1.采用喷丸清理干净连铸圆坯表面氧化层的扫查要求,探头周向扫查面大于等于180
°
,粗糙表面探头移动可采用触点法,沿连铸圆纵向成“w”型扫查,保证声束的有效覆盖;
21.s2.砂轮打磨连铸圆坯表面要求,打磨区域周向间隔不大于60
°
,打磨宽度大于150mm,保证扫查面180
°
以上覆盖,打磨面不低于50%见亮,即打磨后光面占打磨的总面积不低于50%,沿打磨面移动探头进行扫查;
22.(4)缺陷反射波定量:
23.经步骤(3)的扫查后,当发现连铸圆坯存在缺陷反射时,沿连铸圆坯周向与纵向分别移动探头,测出最大反射回波;通过移动探头获得缺陷波的最大反射回波为缺陷波幅,此位置为缺陷位置;
24.(5)缺陷分类与评判:
25.平面型缺陷指不连续反射周向波幅变化明显、波根窄、底波无明显下降;具体包括不规则小缩孔、线状裂纹类缺陷;
26.非平面型缺陷指不连续反射周向波幅无明显变化、波根成一定宽度、底波明显下降;具体包括孔洞类、放射性心部裂纹、严重疏松、大夹渣类缺陷;
27.对应《大连铸圆坯超声波探伤质量等级规范》对超过评定要求的反射波依据缺陷形状(平面型与非平面型)、底波衰减系数、反射波特征值、缺陷当量值进行分级评判;
28.(6)探伤灵敏度验证:
29.采用对比试块平底孔,验证dgs曲线灵敏度偏差不超
±
2db;对比试块选择与制作:用于验证探伤灵敏度可靠性,验证实践操作过程超声波探伤灵敏度有效性;对比试块的材料牌号以及状态应与被检测材料相同。
30.(7)出具连铸圆坯超声波探伤报告。
31.优选的,步骤(1)中所述方波功能a型脉冲反射式超声波探伤仪的发射电压为450v;所述探头晶片直径推荐使用ф24mm、工作频率1mhz或ф34mm、工作频率0.5hz。
32.优选的,步骤(1)中所述软保护膜的材质包括聚氨酯软性塑料。
33.优选的,步骤(2)的s1中所述去除连铸圆坯表面的氧化层的方式:采用喷丸处理或用砂轮打磨去除连铸圆坯表面氧化层。
34.优选的,步骤(2)的s1中所述融水性化学浆糊与水的质量比为1:4-6。
35.优选的,步骤(2)的s1中所述耦合剂均匀涂在连铸圆坯表面的涂覆厚度为0.1-0.2mm。
36.优选的,步骤(3)的(d)中,所述扫查时,探头的移动速度不超过150mm/s,保证声束有效覆盖10%以上。
37.优选的,步骤(6)中所述对比试块的制作要求如下:
38.(a)材质与状态:选用与被检测材料相近或相同铸态组织,经超声波探伤靠中心三分之一直径处无超过φ8mm的反射;
39.对比试块至少包含3个平底孔,平底孔的孔径按梯度设置,梯度范围φ4-φ28mm,平底孔的深度不得小于20mm;平底孔加工过程中的尺寸误差不超
±
3%。
40.(b)表面:去除表面氧化层、保留连铸圆坯原始振痕;
41.优选的,所述对比试块包含3个平底孔,所述对比试块包含3个平底孔,分别为平底孔1、平底孔2和平底孔3;
42.其中孔径
×
深度参数如下:平底孔1,φ12mm
×
20mm、平底孔2,φ16mm
×
20mm、平底孔3,φ20mm
×
20mm,孔径尺寸误差
±
0.1mm、深度尺寸误差
±
0.5mm。
43.【大连铸圆坯超声波探伤质量等级规范】具体评判要求如下表1。
44.表1连铸圆直探法的质量等级、记录水平和验收准则(适用于铸态组织)
45.46.注:选用探头频率推荐范围350≤d<700、1mhz~2mhz,700≤d<≤1000、0.5mhz~1mhz。
47.大连铸圆坯超声波探伤质量等级规范说明:
48.(1)检测对象:连铸圆坯铸态低倍组织结构,由表向内分细小等轴晶区、柱状晶区、粗大等轴晶区,受粗大铸态组织限制,超声波探伤材料以中、低碳低合金钢为主。
49.(2)检测位置:超声波单值、低频方法,声束扩散大、主要检测沿直接靠中心三分之一位置的缺陷。
50.(3)发现缺陷能力:探头频率限制,连铸圆坯铸态组织探伤主要检测,较严重疏松、缩孔、裂纹类缺陷。
51.(4)借助探伤结果低倍解剖验证,分析反射特征值、底波衰减、波型形貌、反射当量值,与解剖样低倍评级之间关系(疏松、缩孔、裂纹),总结连铸圆坯超声波探伤评判要点。
52.(5)缺陷评判准则:缺陷形状(平面型与非平面型)、底波衰减系数、反射波特征值、缺陷当量值。
53.大连铸圆坯超声波探伤按规格分四个评判等级说明:
54.(1)对应yb/t153-2015中华人民共和国黑色冶金行业标准:附录d(直径350~1000mm连铸圆坯低倍组织缺陷中心疏松、缩孔、裂纹评级);
55.(2)依据连铸圆超声探伤与低倍评级对应数据;
56.表2连铸圆坯探伤与低倍统计
[0057][0058]
本发明的优点和技术效果是:
[0059]
(1)本发明形成了一套专用检测评估方法,可以有效无损检测出大规格连铸圆坯的中心疏松、缩孔、裂纹缺陷,保证连铸圆坯中心低倍质量受控、提高轧材的利用率,创造了可观的经济效益,在行业内实现了连铸坯探伤的实际运用;
[0060]
目前针对材料crmo、s355钢系列,规格φ600mm/φ700mm/φ800mm,连铸圆坯首炉、尾炉轧材超声探伤gb/t4162 b级合格率85%,后经连铸圆坯超声探伤分类管控轧制探伤合格率达99.5%以上。
[0061]
(2)用于风电类连铸圆坯超声波探伤与评判,材料18crnimo7-6、s355nl-z35、42crmo4等,按探伤结果分级管控,质量等级1可直接锻造实心件,质量等级2、3锻造加工工艺优化后、保证锻件探伤合格率;通过本发明的方法,连铸圆坯超声波探伤质量监控与质量分级管控,质量外损比例下降50%以上。
[0062]
(3)本发明增加一种大连铸圆坯低倍质量检验辅助方法,可作为验证连铸工艺改进、质量监控的手段;使用本发明的方法针对连铸圆坯头、尾料超声波探伤,进行分级管控、优化切割长度,提高电炉金属收得率;
[0063]
冶金行业产品竞争越趋激烈,而竞争关键要素无非是质量与成本,借助本发明的
连铸圆坯超声探伤评估方法,可实现连铸圆坯生产成本降低的同时,保证产品质量最优。
附图说明
[0064]
图1为实施例2中42crmo4、直径φ800mm平底孔验证试块的主视图(a)和侧视图(b)。
[0065]
图2为实施例3中18crnimo7-6、直径φ600mm平底孔验证试块的主视图(a)和侧视图(b)。
具体实施方式
[0066]
以下结合实例对本发明进行详细描述,但本发明不局限于这些实施例。
[0067]
实施例1:
[0068]
材质s355nl-z35、φ800mm连铸圆坯超声波探伤;
[0069]
主要用于检测连铸圆坯靠中心三分之一位置的,疏松、缩孔、裂纹类缺陷,依据探伤过程中出现缺陷形状(平面型与非平面型)、底波衰减系数、反射波特征值、缺陷当量值进行分级评判。
[0070]
步骤1:选择仪器与探头:仪器采用a型脉冲反射式超声波探伤仪,具备方波发射功能,发射能量450v,探伤仪工作频率0.25mhz-2mhz;推荐使用ge usn60型号。
[0071]
探头的选择根据连铸圆坯表面状况需要,采用带软保护膜二种类型的探头,具体使用以下二种型号探头。
[0072]
1)0.5mhz/晶片直径34mm直探头(ge型号b0.5sl);
[0073]
2)1mhz/晶片直径24mm直探头(ge型号k1s-c)。
[0074]
步骤2:探伤前准备;
[0075]
1)表面处理:对连铸圆坯表面经喷丸处理,去除连铸圆坯表面的松散氧化层,外观检查合格,符合检测要求;连铸圆坯表面氧化层处理后,在其表面涂覆耦合剂;
[0076]
2)耦合剂:耦合剂应选用融水性化学浆糊、与水按照质量比1:4-6混合均匀得到的粘稠状混合物,用刷子将耦合剂均匀涂在连铸圆表面、涂覆厚度为0.1-0.2mm;
[0077]
3)探性测试:
[0078]
第一,选择仪器与探头后,将被探连铸圆坯一次底波调至80%、灵敏度余量不小于10db、噪声信号不超20%;第二,第一次底倍与第二次底波灵敏度db差不大于8db;
[0079]
经过可探性测试检测后,满足上述二条件,说明连铸圆坯可进行超声波探伤。
[0080]
步骤3:探伤过程;
[0081]
1)零位与声速校准:大规格铸坯组织均匀差、尺寸大,定位与定量误差大。
[0082]
2)灵敏度调整:选用的仪器和探头具备dgs曲线功能,使用dgs曲线法来调节灵敏度;
[0083]
使用仪器dgs功能、将记录当量值设定dgs值,将一次底波高度调整到80%底面回波,选取三处以上不同位置、取平均值,稳住探头记录dgs参考值,确定后完成dgs曲线制作,即完成灵敏度的调整,进行超声探伤检测;
[0084]
3)扫查:在原灵敏度调整基上提高2~6db作为扫查灵敏度,探头在连铸圆坯表面的移动速度不超过150mm/s,保证声束有效覆盖10%以上,当遇到粗糙表面,探头移动可采
用触点法,沿连铸圆纵向成“w”型移动,周向覆盖率大于180
°
。
[0085]
步骤4:缺陷反射波定量:经步骤3)的扫查后,当发现连铸圆坯存在缺陷反射时,沿连铸圆坯周向与纵向分别移动探头,测出最大反射回波;通过移动探头获得缺陷波的最大反射回波为缺陷波幅,此位置为缺陷位置;
[0086]
步骤5:缺陷分类与评判:对应【大连铸圆坯超声波探伤质量等级规范】对超过评定要求的反射波依据缺陷形状(平面型与非平面型)、底波衰减系数、反射波特征值、缺陷当量值进行分级评判。
[0087]
步骤6:探伤灵敏度验证。采用对比试块平底孔,试块的材料牌号以及状态应与被检材料(s355nl-z35、φ800mm)声学特征相同,选用r=400mm对比试块平底孔2、孔径φ16mm,验证dgs曲线灵敏度偏差不超
±
2db,经验证合格、说明探伤结果有效。
[0088]
步骤7:出具连铸圆坯超声探伤报告,评定连铸圆坯超声探伤质量等级。
[0089]
实施例2:
[0090]
针对连铸圆坯材质42crmo4、φ800mm进行超声探伤异常,改轧制棒材控制低倍质量;
[0091]
主要用于检测连铸圆坯开浇头炉、工艺过程异常炉次和尾炉,依据探伤结果进行质量等级分级评判,为轧钢控制圆棒低倍缺陷提供建议。
[0092]
步骤1:按实施例1步骤要求开展对连铸圆坯超声波探伤,区别是探伤灵敏度验证时,采用的对比试块为42crmo4、φ800mm,具体形状与尺寸见图1。
[0093]
步骤2:探伤分级评判。
[0094]
连铸圆坯超声探伤测定,根据铸坯圆截面中心位置存在异常反射波,探伤初步推断沿铸坯心部长度方向存在间断性中心裂纹,严重位置至中心裂纹2级,裂纹长度50mm、宽度60mm,对于典型性反射进行低倍纵剖验证,对应表1《大连铸圆坯超声波探伤质量等级规范》,按连铸圆探伤质量等级3级不合格,4级合格(超出3级规定,但可符合4级要求)。
[0095]
首先按超声探伤表1质量等级进行探伤评定,然后为了进一步验证超声探伤结果,进行低倍解剖,查找表1与表2对应关系;通过表1连铸圆直探法的质量等级、记录水平和验收准则与表2对应yb/t153-2015中华人民共和国黑色冶金行业标准超声探伤与低倍解剖对应关系,即连铸圆坯超声探伤与低倍解剖的对应关联;
[0096]
根据探伤的结果,可相应进行工艺的优化,使其符合要求;
[0097]
步骤3:轧钢加热与轧制工艺优化控制;
[0098]
1)加热工艺:将连铸圆坯加热1230℃,保温时间在原基础上延长1小时;
[0099]
2)轧制工艺:开坯机加大压下量,轧制压缩比大于10、轧制规格
[0100]
3)轧制后冷却工艺:圆棒收集温度大于600℃,采用入坑缓冷。
[0101]
步骤4:轧制圆棒超声波探伤;
[0102]
轧后圆棒按gb/t4162 b级超声波探伤,探伤显示靠材料中心位置存在零星点状反射,探伤合格;圆棒低倍解剖结果为中心疏松1.0级。
[0103]
本发明提供的方法借助探伤结果低倍解剖验证,分析反射特征值、底波衰减、波型形貌、反射当量值,与解剖样低倍评级之间关系(疏松),总结连铸圆坯超声波探伤评判要点。
[0104]
实施例3:
[0105]
风电齿轮用连铸圆坯锻材探伤,材质18crnimo7-6φ600;
[0106]
主要用于检测风电齿轮用高附加值、质量分析高的连铸圆坯,依据探伤结果进行质量等级分级评判,为锻造工艺优化提供建议,可有效规避质量风险,提升品牌效应。
[0107]
步骤1:按实施例1步骤要求开展对风电齿轮用连铸圆坯超声波探伤,区别是探伤灵敏度验证时,采用的对比试块为8crnimo7-6,φ600,具体形状与尺寸见图2。
[0108]
步骤2:探伤分级评判;
[0109]
连铸圆坯超声探伤测定,根据圆截面中心位置存在异常反射波,探伤初步推断沿长度方向存在零星中心缩孔,严重位置缩孔等级1.0,缩孔长度50mm,按连铸圆探伤质量等级2级不合格、3级合格。
[0110]
步骤3:模锻加工工艺;
[0111]
1)连铸圆坯探伤质量等级2级合格,选用正常锻造工艺,铸坯锻轧下料规格毛坯加热镦粗至高度270
±
5mm,模锻反压成型,中心冲孔折算为铸坯心部直径55mm,齿坯最大毛坯尺寸是外圆锻造总压缩比为5.25。
[0112]
2)对连铸圆探伤质量等级2级不合格、3级合格,借助锻造工艺优化,铸坯锻轧下料规格毛坯加热镦粗至高度270
±
5mm,模锻反压成型,采用中心冲孔折算增大为铸坯心部直径70mm,齿坯最大毛坯尺寸是外圆锻造总压缩比为5.25。
[0113]
步骤4:锻后齿坯内圈与辐板按2.0当量判定,对锻造厂2021年四季度探伤情况进行回访跟踪,总探伤齿坯数量1620件,探伤不合格2件,探伤合格率99.88%。
[0114]
连铸圆坯作为后续热加工工件母材,借助对连铸圆坯超声探伤并评级,为后续加工工艺与材料用途提供建议,减少下道工序不合格品产生、保证产品质量。
[0115]
说明:以上实施例仅用以说明本发明而并非限制本发明所描述的技术方案;因此,尽管本说明书参照上述的各个实施例对本发明已进行了详细的说明,但是本领域的普通技术人员应当理解,仍然可以对本发明进行修改或等同替换;而一切不脱离本发明的精神和范围的技术方案及其改进,其均应涵盖在本发明的权利要求范围内。