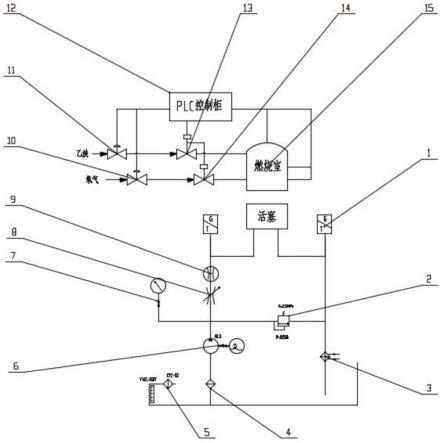
1.本发明涉及的是一种实验台,具体地说是发动机活塞实验台。
背景技术:2.对于车用柴油发动机,提高其功率密度一直是其主要的研究方向,但功率的不断提高和结构尺寸的尽力减少使得柴油机内部的零件的工作条件不断恶劣。柴油机活塞是其内部所有零件中工作条件最为恶劣的几个零件之一,其往复运动的特性不仅使其承受惯性力的影响而承受较大的机械负荷,燃烧室内周期变化的温度和活塞头部与活塞裙部较大的温度差异使其承受巨大的热负荷。
3.一般情况下,活塞的损坏主要由热负荷超过限制参数裂纹等疲劳坏,所以准确检测活塞的温度场进而分析其热负荷的大小是发动机强化过程中必须解决的问题。传统的测试办法是将测温元件装配到发动机中进行实机测试,但燃烧室内复杂的燃烧过程和残余废气总是干扰温度检测,导致结果只能显示出一条与实际温度变化有相同趋势的曲线,但在数值上存在较大的差距。若采用其他实验手段,则无法准确模拟燃烧室内部状态,燃烧温度很难控制,活塞的冷却也难以达到发动机冷却系统的冷却效果,其结果是发动机外部实验测得的参数无法准确反映活塞温度场,而发动机内部实验往往面临传感器难以布置,数据采集干扰大等问题。
4.发动机设计过程中,活塞的设计至关重要,为了验证设计的活塞是否满足高强化指标的要求,需要对活塞进行实验测试。因此,用于活塞温度场测定实验台燃气与冷却系统可以准确地模拟活塞的工作状态,是发动机实验设备开发中的一项关键技术。
技术实现要素:5.本发明的目的在于提供可以保持活塞温度场的稳定,进而准确测得发动机活塞的热力学参数的一种应用于发动机活塞温度场测定的实验台燃气与冷却系统。
6.本发明的目的是这样实现的:
7.本发明一种应用于发动机活塞温度场测定的实验台燃气与冷却系统,其特征是:包括plc控制模块、燃烧室、活塞、油箱,活塞位于燃烧室下方,燃烧室分别连接第一实验台燃气管路和第二实验台燃气管路,第一实验台燃气管路上安装第一电磁阀,第二实验台燃气管路上安装第二电磁阀,乙炔压力容器通过第一流量调节阀连接第一实验台燃气管路,氧气压力容器通过第二流量调节阀连接第二实验台燃气管路,plc控制模块分别连接第一电磁阀、第二电磁阀、第一流量调节阀、第二流量调节阀。
8.本发明还可以包括:
9.1、还包括活塞冷却油路,活塞冷却油路包括活塞进油油路和活塞回油油路,活塞进油油路上安装供油过滤器、油泵、调速阀、节流阀、第一温度传感器,活塞回油油路上安装第二温度传感器、回油冷却器。
10.2、活塞回油油路支出溢流油路,溢流油路上安装定压溢流阀、压力表。
11.本发明的优势在于:
12.1、燃气系统采用乙炔与氧气混合加热的手段,具备大范围的温度调节能力。
13.2、燃气系统的控制阀均采用plc控制,无需手动调节,可以实现燃气供给的稳定,进而维持稳定的燃烧温度,有利于对活塞温度场的精准测量。
14.3、冷却系统包括对活塞冷却腔的油冷与冷却水套的水冷,其冷却原理和真实发动机一致,冷却系统的控制阀同样采用plc控制,具备自动调节的能力。
15.4、冷却系统与燃气系统的控制均采用pid自动控制方法,可以保证实验过程中活塞的受热与散热条件稳定,进而模拟出与真实发动机近乎一致的活塞温度场,依据实验数据,可以准确分析活塞的热力学特性。
附图说明
16.图1为本发明的结构示意图;
17.图2为实验台冷却系统原理图;
18.图3为实验台燃气系统原理图。
具体实施方式
19.下面结合附图举例对本发明做更详细地描述:
20.结合图1-3,本发明一种应用于发动机活塞温度场测定的实验台燃气与冷却系统,主要包括温度传感器1、定压溢流阀2、回油冷却器3、供油过滤器4、油箱冷却器5、2.2kw变频电机6、压力表7、调速阀8、节流阀9、流量调节阀v210、流量调节阀v111、plc控制模块12、电磁阀v313、电磁阀v414、燃烧室15。
21.冷却系统采用缸套水冷,活塞油冷的冷却模式。
22.冷却油的供油量与供油速率受进入活塞的冷却油温度与流出活塞的冷却油温度共同作用,冷却油温度通过温度传感器1获取,反馈的数据用以调节调速阀与8节流阀9的开度,进而调节冷却油流量,实现冷却油温度的闭环控制。
23.冷却系统采用plc控制模块12自动控制,2.2kw变频电机6启动后,冷却油经过供油过滤器4进入实验台冷却管路,多余冷却油经过定压溢流阀2再经过冷却器3回流到油箱,油路压力可通过压力表7查看。
24.由于活塞位置对冷却油的持续加热,冷却油路需要冷却,对于回流进入油箱的冷却油通过冷却器3冷却,为了加强冷却效果,在油箱位置安装了油箱冷却器5。
25.燃气系统采用乙炔与氧气的混合气加热活塞的模式。
26.燃气系统中,乙炔与氧气的流量均由plc控制模块12调节,燃烧室中的温度传感器将实时反馈温度数据,使得燃烧系统实现闭环控制。
27.为了精准控制火焰燃烧的温度,储存在压力容器中的氧气与乙炔分别通过流量调节阀v210、流量调节阀v111进入实验台燃气管路,再由电磁阀v414,流电磁阀v413,对喷入燃烧室15内的燃气进行精准调控。
28.当设备启动,plc控制模块12将首先启动缸套和活塞冷却,在检测正常后,启动燃气系统。在点火完成后,储存在压力容器中的氧气与乙炔分别通过流量调节阀v210、流量调节阀v111进入实验台燃气管路,再由电磁阀v414,流电磁阀v413,对喷入燃烧室15内的燃气
进行精准调控使燃烧室温度达到设定状态。实验台完成启动程序后,将通过pld控制,保持活塞的传热与散热稳定,并开始记录实验数据。
29.1)冷却系统
30.喷流实验台冷却系统的基本原理是:通过冷却油、冷却水对活塞和缸套进行降温,保证活塞进油口、出油口,缸套进水口、出水口的温度和实机相同,且油路与水路的流量均要连续可调。需要说明的是,缸套冷却水路与活塞冷却油路的回路冷使用冷却水塔的冷却水,通过调节流量,保证缸套、活塞出入口温度和实机相同,即可模拟实机冷却的的效果,由于采用plc编程控制,容易通过监控出入口温度信号对流量实现pid控制,提高系统工作的稳定性。
31.技术指标参考实机工作过程中的活塞缸套的工作条件,再结合普通液压系统元器件的要求,做出如下规定:冷却油路流量15l/min;冷却油供油压力2.5mpa;冷却油进口温度45℃;冷却油出口温度55℃;进口及出口加温度传感器;进口加流量传感器;传感器需接入plc,便于实时显示数据。
32.对于工作条件,参考一般冷却系统的使用条件,做出如下要求:室内使用,厂房通风散热良好;海拔:≤200m;工作环境温度:0℃~45℃;存储温度:-20℃~50℃。
33.喷流实验台冷却系统。主要由以下几部分组成:
34.(1)液压源,2套;
35.(2)液压管路,2套;
36.(3)冷却系统,3套;
37.其中活塞冷却的原理图如图2所示。
38.缸套冷却的基本原理是通过油泵将冷却油泵入活塞,油泵的转速可以调整,油泵出口通过泄压阀调定油路压力,再通过节流阀调定流速,活塞入口和出口处都安装了温度传感器,实验过程中,流速和压力可以通过plc系统控制,温度通过传感器采集显示,实验人员通过调整冷却油流量保持出口温度稳定即可。
39.对于液压源,油泵采用变频电机驱动齿轮泵供油,变频电机转速800rpm~2500rpm;额定流量8~25l/min;溢流阀额定压力2.5mpa。
40.液压源为冷却系统提供动力能源,输出压力和流量。此外,油液需要有过滤功能,需要配置吸油过滤器;为了对冷却油加以冷却,油路需要增加回油冷却器。
41.对于缸套冷却,其原理和活塞冷却相同,也需要单独的泵站用于泵水,对回水管路依然需要冷却水塔进行冷却。
42.2)燃气系统
43.燃气系统包括气瓶、燃气管、燃烧仓、控制元件与传感器元件组成。其中气瓶与燃气管路均采用标准件,燃烧仓与控制元件、传感元件的关系如图3所示。燃烧仓的plc控制系统由西门子plc控制器、热电偶模块、扩展模块、流量调节阀测控电路和电子打火电路组成。对于燃气系统的plc控制器,选用西门子s7-200smar小型plc,输入采用直流漏型接法,输出采用直流继电器接法,输出接中间继电器。
44.燃烧仓在点火时,加热启停控制继电器用于控制火焰监测器加电,点火时程控闭合,烧炉运行期间程控保持闭合,点火失败、异常熄火、停炉熄火和超温熄火时程控断开。火焰监测器加电后,按时序给高能点火器加电,控制高能点火枪点火;按时序使控制继电器闭
合,控制燃气电磁阀v3/v4开通,向燃烧仓供燃气;同时根据炉火状态信号,控制着火继电器、熄火继电器相应动作。火焰探测器用于实时检测炉火状态,向火焰监测
45.器提供炉火状态信号。热电偶模块选用em231,plc控制器利用热电偶信号送达的信号测定燃烧仓内温度。
46.其基本原理是,乙炔和氧气在喷嘴位置才混合,并在割炬的作用下,形成内部为乙炔,外部为氧气的火焰核心。在使用过程中,需要手动打开气阀(接入plc后处于常开位置),流量控制均开到最大(流量控制由管路上的电控流量调节阀控制)。在实验台工作完成后,需要手动将其气阀关闭,同时,也可利用其自带的流量控制阀对燃气进行手动调节。